Деформации и напряжения при сварке и меры их предупреждения
Основными причинами образования деформаций и напряжений при сварке являются неравномерный нагрев сварной конструкции и усадка наплавленного металла.
Для уменьшения деформаций и напряжений при сварке необходимо руководствоваться следующими правилами:
· применять марки электродов, повышающих пластичность металла шва;
· выполнять швы с меньшим количеством наплавленного металла;
· ограничивать применение накладок и косынок;
· применять по возможности стыковые швы, так как они обеспечивают наименьшую концентрацию напряжений;
· использовать методы секционного изготовления конструкций;
· правильно выбирать тепловой режим при сварке; при сварке закаливающихся сталей применять предварительный, сопутствующий и послесварочный подогрев;
· применять методы обратных деформаций и предварительного смещения;
· с целью уменьшения коробления листов, швы длиной более 600 мм выполнять в обратно-ступенчатом порядке;
· соблюдать правильную последовательность наложения швов;
· предусмотреть свободную усадку шва;
· сваривать длинные швы от середины к его концам;
· при сварке листовых заготовок для предотвращения деформаций применять метод предварительных прихватов или ребер жесткости;
· использовать метод жесткого закрепления заготовок перед сваркой;
· для снятия внутренних напряжений применять общий отжиг
сварного изделия, проковку шва и околошовной зоны; для устранения деформаций можно применять также механическую правку в холодном или горячем состоянии.
|
|
Контроль качества сварных соединений осуществляется наружным осмотром, проверкой размеров швов, механическими испытаниями прочности сварных соединений, испытаниями плотности шва, металлографическими исследованиями и контролем внутренних дефектов.
Запись сварочной операции (приваривание трубки к обойме) в технологической документации производится следующим образом:
7 1 080 9041 Сварочная
1. Приварить трубку поз. 1 к обойме поз. 3 швом № 6 по замкнутому контуру с катетом 1 мм. (См. лист 1 гл. вида сварочного чертежа)
Или (приваривание заглушки в сквозном отверстии корпуса):
7 1 045 9041 Сварочная
А. Установить заглушку в гнездо
1. Приварить заглушку согласно чертежу в один слой, заподлицо с поверхностью корпуса, перекрывая начало шва.
Допускаются вогнутости шва глубиной до 0,4 мм.
После проведения сварочной операции необходимо произвести зачистку шва применением слесарно-сварочной операции:
7 1 050 6310–0107 Слесарно–сварочная
А. Установить корпус на верстак
|
|
1. Зачистить сварочные швы от шлаков и брызг металла с плавным переходом к основному металлу, а также места потемневшие от сварки, не нарушая размеров и параметров корпуса, выполненных по чертежу до сварки
Щетка металлическая из углеродистой проволоки; шабер; надфиль плоский 80 № 2; шкурка шлиф. 2С 1000х50 П6 25А 20-НМА ГОСТ 6456-82; Плита поверочная, кл. 1; Щуп, набор № 1.
При необходимости проводят операцию отжига для снятия остаточных напряжений. Далее следуют операции: промывочная и контрольная.
Пайка
Пайкой называется процесс получения неразъемного соединения заготовок с нагревом ниже температуры их автономного расплавления путем смачивания, растекания и заполнения зазора между ними расплавленным припоем и сцепления их при кристаллизации шва
(рис. 1.16).
![]() |
Припой – материал для пайки и лужения с температурой плавления ниже температуры плавления паяемых материалов. Припой должен обладать хорошей смачивающей способностью, обеспечивать достаточно высокие сцепляемость, прочность, пластичность и герметичность паяного соединения, иметь коэффициент линейного расширения, близкий к коэффициенту линейного расширения паяемого материала, быть дешевым и недефицитным. Припои представляют собой сплавы цветных металлов сложного состава. Все припои по температуре плавления подразделяются на особолегкоплавкие (температура плавления ≤ 145 °С), легкоплавкие (температура плавления 145 ≤ 450 °С), среднеплавкие (температура плавления 450 ≤ 1100 °С) и тугоплавкие (температура плавления более 1100 °С). Припой выбирают в зависимости от паяемого материала. Припои изготавливают в виде прутков, проволок, листов, полос, спиралей, дисков, колец, зерен и т.д., укладываемых в место соединения [58]. Пайка производится обычно в среде флюса.
|
|
Флюс – вещество или смесь различных веществ (в жидком, пастообразном или твердом состоянии), способствующих очистке поверхности паяемого металла, снижающих поверхностное натяжение, улучшающих растекание и смачиваемость жидкого припоя. Температура плавления флюса всегда ниже температуры плавления припоя. При ультразвуковой пайке флюс не применяется.
Прочность сцепления припоя с соединяемыми поверхностями заготовок зависит от физико-химических и диффузионных процессов, протекающих между припоем и основным металлом.
По прочности паяные соединения уступают сварным. Паять можно стали всех марок, твердые сплавы, цветные металлы, чугуны.
|
|
К преимуществам пайки относятся отсутствие плавления и незначительный нагрев основного материала, что позволяет сохранить неизменным его состав, структуру и механические свойства.
Порошковая металлургия
Методами порошковой металлургии получают разнообразные материалы и изделия (рис. 1.17). Преимущества заготовок, полученных методом порошковой металлургии:
· резкое сокращение расхода материалов и энергии при производстве изделий; коэффициент использования материала 0,95…0,97, против 0,4…0,6 при механообработке;
· композиционная гибкость при разработке различных материалов;
· постоянство состава и свойств изделий;
· однородность микроструктуры;
· исходные материалы для порошковых изделий могут быть получены как из руд, так и из любых отходов металлургической и машиностроительной промышленности (стружки, окалины, облоя);
· создание материалов с особыми свойствами (пористых материалов, твердых сплавов, материалов защитных покрытий, композиционных материалов и др.), которые невозможно получить традиционными методами.
![]() |

Существующие методы получения порошков (в зависимости от основных принципов производства) могут быть разделены на механические и физико-химические. К механическим методам относятся измельчение металлов резанием, с дальнейшим размолом в шаровых мельницах, измельчение в вихревых мельницах, в вибромельницах (рис.1.18), дробление в инерционных дробилках, а также распыление струи жидкого металла паром, водой, сжатым газом.
Под физико-химическими методами получения порошков понимают такие технологические процессы, при которых вследствие глубинных физико-химических превращений металл или сплав переходит в порошкообразное состояние. При этом полученный порошок может отличаться по химическому составу от исходных продуктов. К физико-химическим методам относятся: восстановление оксидов твердыми восстановителями и газами, электролиз расплавленных сред или водных растворов, диссоциация карбонилов, метод испарения и конденсации.
Получение металлических порошков восстановлением из оксидов является наиболее распространенным, высокопроизводительным и экономичным методом.
В качестве исходных материалов используются недорогие рудные концентраты, оксиды, отходы металлургического производства. Частицы порошков получаются губчатыми в виде многогранников с сильно развитой поверхностью, которые благодаря большой пористости хорошо прессуются. Получаются порошки Cu, Ni, Co, Fe, W, Mo, Cr, Mn, V, Al.
![]() |
Электролитическим осаждением металлов из водных растворов солей получают порошки олова, серебра, меди, железа. Из расплавленных сред получают редкие металлы: тантал, ниобий, уран. Достоинством метода является возможность получения порошков высокой чистоты. Недостаток – высокая стоимость метода и большие затраты энергии. Размеры частиц 10…100 мкм.
В карбонильном методе реализуются реакции:
Во время реакций можно легко отделить частицы посторонних примесей и получить очень чистый металл в виде частиц сфероидальной формы размером 1…10 мкм. Наиболее часто этим способом получают порошки Fe, Co, Ni, реже Cr, Mo, W и др.
При получении, хранении, транспортировке порошков необходимо учитывать:
· некоторые порошки могут самовозгораться, например, порошки железа, кобальта и др.;
· почти все порошковые материалы токсичны, например, порошок никеля вызывает резкие болезненные изменения крови.
Порошки обозначаются по ГОСТ 9849-86. Например, ПЖ2М3 – порошок железный, 2 – чистота порошка, М – мелкий, 3 – подгруппа плотности.
Технологический процесс изготовления деталей из порошков:
1. Подготовка порошков.
2. Смешивание, введение добавок
3. Прессование. (Холодное прессование не обеспечивает механической прочности изделий, и они могут разрушаться даже при незначительных усилиях).
4. Спекание.
(Спекание порошковых материалов – это тепловая обработка свободно насыпанного порошка или прессованных заготовок при 0,7…0,9 абсолютной температуры плавления металла. Это важнейшая операция порошковой металлургии, при которой в результате диффузионных, рекристаллизационных и других процессов при термической обработке из уплотненного конгломерата частиц порошка создается единое тело, обладающее определенной структурой и свойствами).
5. Дополнительная обработка (механическая, термическая, химико-термическая, пропитка, гальваническая, нанесение покрытий и др.).
В зависимости от плотности и назначения порошковые сплавы подразделяются на две группы:
· плотные – сплавы с минимальной пористостью, изготовленные на основе порошков железа, меди, никеля, бронзы, латуни, титана, специальных сплавов;
· пористые, в которых после окончательной обработки сохраняется 10…15% пор по объему, что обеспечивает приобретение специальных свойств и позволяет применять их для изготовления антифрикционных изделий, фильтров и др.
Для обозначения конструкционных порошковых сталей в России принята следующая маркировка. Первая буква в обозначении характеризует класс материала: С – сталь; вторая буква – П – изделие получено методом порошковой металлургии, следующее потом число показывает содержание углерода в процентах; все последующие буквы обозначают легирующие элементы, цифры – содержание легирующих элементов в процентах. Материал СП45Х2Н3Д2 получен методом порошковой металлургии, содержит 0,45% углерода, 2% хрома, 3% никеля, 2% меди.
Достоинства порошковых сталей – малый процент отходов при изготовлении деталей, возможность получения деталей с заданными свойствами. Недостатки: малая прочность на изгиб, быстрее подвергаются коррозии, поэтому должны иметь специальное покрытие. Порошки токсичны.
Дополнительная обработка резанием производится в том случае, когда полученная точность исходного изделия бывает недостаточна. При обработке пористых заготовок нельзя применять охлаждающие жидкости, так как впитавшаяся жидкость вызывает коррозию. При обработке резанием применяют твердосплавный или алмазный инструмент.
Применение методов порошковой металлургии: производство антифрикционных материалов (железо-графитовых, бронзо-графитовых и т.п.) для подшипников скольжения, изготовление фильтров из пористых материалов, производство перетачиваемых и неперетачиваемых пластин для оснащения режущего инструмента, изготовление алмазосодержащих инструментов.
Нанопорошки
Нанопорошковая индустрия начала развиваться совсем недавно, однако изделия, создаваемые ею, имеют существенно более высокие параметры, чем изделия, полученные обычными методами порошковой металлургии.
Нанопорошки – это порошки, размеры частиц которых составляют 10-9…10-7 м (0,001…0,1 мкм). Превращение в нанодисперсную систему исходного органического или неорганического материала рождает, по сути, новый вид вещества с совершенно уникальными свойствами. Распыленное до такого состояния твердое тело, уже и не твердое тело и не жидкость, хотя ведет себя в отдельных моментах как жидкость.
Спектр разрабатываемых практических применений нанотехнологии уже сейчас очень широк:
· создаются материалы с заранее заданными свойствами;
· интегральные схемы, созданные с помощью нанотехнологии, будут на 3…6 порядков меньше и быстрее существующих сегодня;
· нанокомпозиционные керамики и сплавы покажут рекордные свойства по отношению к существующим;
· твердость металлов с наноструктурой ожидается в 7 раз выше по отношению к изготовленным традиционными способами;
· создаются адсорбенты нового типа для очистки воды и воздуха;
· создаются лекарства широкого применения и т.д.
По оценкам международного научного сообщества, волшебный «карлик», так называют нанопорошки, в состоянии поднять мировые технологии на качественно новый уровень развития, произвести такую же революцию, какую в свое время произвело открытие микроэлектроники. По результатам конкурса 2000 года, нанопорошки, получаемые в Инновационно-технологическом центре г. Томска, вошли в число 100 лучших высокотехнологичных товаров, представленных на рынке США в 2000 году.
Склеивание
![]() |
Склеивание часто применяют в машиностроении. Склеивание применяют как самостоятельный процесс, так и альтернативный сварке. Вместо сварки заготовки склеивают том случае, когда должны быть исключены перераспределение напряжений в заготовках или нагрев заготовок. Склеивание применяют даже вместо лазерной сварки и электронно-лучевой, дающих минимальное изменение поверхностного слоя свариваемых заготовок. Склеивают металлы (рис. 1.19 – 1.20), пластмассы, керамику, ферриты, стекло, резину в различных сочетаниях. В качестве клеящего вещества используют смесь смол марок СЭДМ-2, Э-181, Л-20 и др. в определенном сочетании. В зависимости от величины зазора между склеиваемыми заготовками, в полученную смесь могут добавляться наполнители: молотый кварцевый песок, алюминиевая пудра, карбонильное железо, нитрид бора, двуокись титана и др. При очень малых зазорах (до 0,015 мм) смесь применяют в разбавленном состоянии и без наполнителя. Клей с наполнителем используется в диапазоне зазоров 0,07…0,15 мм. Клей с наполнителем может применяться и при больших величинах зазора (до 0,6 мм), но при отсутствии требований по герметичности. Свежеприготовленный клей должен быть использован в течение 2-х часов.
Склеиваемые поверхности металлических изделий не должны иметь следов коррозии, окалины, окисных пленок покрытий, лакокрасочных покрытий. Не подлежат склеиванию и поверхности, имеющие гальванические покрытия с промасливанием и пропиткой гидрофобизирующей жидкостью. На склеиваемых поверхностях не допускаются зазубрины, заусенцы, острые кромки. Параметр шероховатости склеиваемых метал-лических поверхностей должен быть в пределах Ra = 3,2…0,050 мкм.
Склеивание может выполняться как в специально оборудованных помещениях, так и на слесарно-сборочных участках. В первом случае необходимы три отдельные операции: перед операцией склеивания не- обходима промывочная операция, затем выполняется операция склеивания и заканчивается операцией сушки, в которой происходит отверде-
вание клея. Во втором случае все три операции выполняются как переходы одной операции.
В зависимости от необходимых требований к клеевому соединению отвердевание клея может производиться как на воздухе, так и в печи при температуре до 100…150 градусов (для металлических изделий). При этом время сушки уменьшается с 24…48 часов до 3…6 часов.
Часто операцию склеивания используют как технологический прием (рис. 1.21), если необходимо получить глухое отверстие в труднодоступном месте изделия: сначала получают сквозные отверстия, а потом нарезают резьбу и ставят резьбовую заглушку на клею (или используют сварку) в одном из отверстий.
Запись операции склеивания (склеивание резьбовой заглушки с корпусом по рис. 1.20), как отдельной операцией, в технологической документации производится следующим образом:
39 2 110 8846–0102 Склеивание
1. Склеить детали поз. 1 и поз. 2 согласно чертежу
или (второй случай):
44 3 090 8864–0031 Слесарно–сборочная
1. Промыть заглушку и заглушаемое отверстие смесью хладона с бензином в соотношении 2:1. Просушить в течение 15 мин
2. Покрыть заглушку клеем
3. Заглушить отверстие заглушкой заподлицо с плоскостью основания. Щели не допускаются
4. Сушить в течение 48 часов на воздухе при температуре 25± 10°С
После операции склеивания допускается проводить операции обработки резанием или отделочные операции. При этом силы резания должны быть небольшими, чтобы не повредить клеевое соединение.
Дата добавления: 2019-02-12; просмотров: 935; Мы поможем в написании вашей работы! |
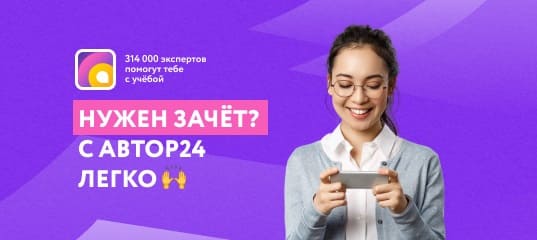
Мы поможем в написании ваших работ!