Подобрать подшипники качения для ведомого вала цилиндрической косозубой передачи
|
Таблица 24. Исходные данные
Нагрузки, действующие на подшипники; Н | Диаметр вала под подшипник; dП, мм | Частота вращения ведомого вала; n2, об/мин | ||||
Fa | RБх | RБу | RГх | RГу | ||
Выбор типа подшипников
5.1.1. По условиям компоновки и работы подшипниковых узлов и с учетом небольшой величины осевой нагрузки назначаем для обеих опор шариковый радиальный однорядный подшипник (табл. 25). По таблице 25 в соответствии с посадочным диаметром на вал, где d = dп, выбираем подшипник и выписываем его характеристики: | ![]()
![]() ![]() ![]() ![]() |
№___; d = dп = мм; D = мм; В = мм; r = мм; Cr = кН; Cor = кН.
В соответствии с условиями работы и типом подшипника принимаем коэффициенты для расчета: V = 1; КБ =1,3; КТ =1; Х=1; Y =0; а1 =1;а23 =0,7.
Таблица 25. Основные параметры подшипников по ГОСТ 8338-75 (выборка)
Обоз-на-чение | Размеры, мм
| Грузоподъемность, кН | Обоз-на- чение | Размеры, мм | Грузоподъемность, кН | ||||||||||
d п | D | В | r | Cr | Cor | d п | D | В | r | Cr | Cor | ||||
204 | 20 | 47 | 14 | 1,5 | 12,7 | 6,2 | 213 | 65 | 120 | 23 | 2,5 | 56,0 | 34,0 | ||
205 | 25 | 52 | 15 | 1,5 | 14,0 | 6,95 | 214 | 70 | 125 | 24 | 2,5 | 61,8 | 37,5 | ||
206 | 30 | 62 | 16 | 1,5 | 19,5 | 10,0 | 215 | 75 | 130 | 25 | 2,5 | 66,3 | 41,0 | ||
207 | 35 | 72 | 17 | 2 | 25,5 | 13,7 | 216 | 80 | 140 | 26 | 3 | 70,2 | 45,0 | ||
208 | 40 | 80 | 18 | 2 | 32,0 | 17,8 | 217 | 85 | 150 | 28 | 3 | 83,2 | 53,0 | ||
209 | 45 | 85 | 19 | 2 | 33,2 | 18,6 | 218 | 90 | 160 | 30 | 3 | 95,6 | 62,0 | ||
210 | 50 | 90 | 20 | 2 | 35,1 | 19,8 | 219 | 95 | 170 | 32 | 3,5 | 108,0 | 69,5 | ||
211 | 55 | 100 | 21 | 2,5 | 43,6 | 25,0 | 220 | 100 | 180 | 34 | 3,5 | 124,0 | 79,0 | ||
212 | 60 | 110 | 22 | 2,5 | 52,0 | 31,0 |
|
|
|
5.1.2. Определяем суммарные реакции опор вала, Ri , (см. п. 4):
Далее расчет ведем по наиболее нагруженной опоре, Ri max = Н.
5.1.3. Определяем эквивалентную динамическую нагрузку на подшипник, Pr:
Pr = (V ∙ X ∙ Ri max +Y ∙ Fa)∙КБ ∙КТ = (1∙1∙+0∙)∙1,3∙1 = ≈ Н.
5.1.4. Определяем скорректированную расчетную долговечность подшипника, L 10 ah:
5.1.5. Оцениваем пригодность выбранного подшипника по соотношению
L 10 ah ≥ [L10h ] и делаем вывод:
час > 12000час, – условие соблюдается.
Конструирование подшипникового узла (рис. 18)
Схема установки подшипников – «враспор» – вал зафиксирован в двух опорах, причем в каждой опоре в одном направлении.
В конструкции редуктора применены закладные крышки, регулирование радиальных подшипников выполнено установкой компенсаторного кольца, установленного между торцами наружного кольца подшипника и крышки. Для удобства сборки компенсаторное кольцо нужно устанавливать со стороны глухой крышки подшипника.
а |
L |
Схема «враспор» |
Фиксирующая опора |
Рис.18. Схема осевого фиксирования вала |

|
|
При установке радиальных шарикоподшипников между торцом наружного кольца подшипника и торцом крышки подшипника оставляют зазор а = 0,2…0,5 мм для компенсации тепловых деформаций.
Зазор оставляют со стороны крышки, имеющей отверстие для выходного конца вала. Этот зазор на чертежах сборочных единиц не показывают.
|
Для предупреждения вытекания смазочного масла, а также для защиты от загрязнения извне, подшипниковые узлы снабжают уплотнительными устройствами — манжетами.
Таблица 26.
Контактное напряжение σН =[σ H ], МПа | Рекомендуемая кинематическая вязкость масла, мм2 /с; при окружной скорости колес, м/с | ||
До 2 | 2…5 | Свыше 5 | |
Для зубчатых передач работающих при 40 ºС | |||
До 600 | 34 | 28 | 22 |
600…1000 | 60 | 50 | 40 |
|
|
Таблица 27.
Марка масла | Кинематическая вязкость, мм2 /с (см. табл. 18) |
Для зубчатых передач работающих при 40 ºС | |
И-Л-А-22 | 19…25 |
И-Г-А-32 | 29…35 |
И-Г-А-46 | 41…51 |
И-Г-А-68 | 61…75 |
Для смазывания выбираем индустриальное масло по таблицам 26 и 27.
Окружная скорость колес 𝓋 = ______ м/с.
Кинематическая вязкость масла – _____мм2/с; марка масла – ________.
(Дать характеристику выбранного масла)
|

Рис. 19. Редуктор цилиндрический одноступенчатый:
1 — корпус; 2 — крышка корпуса; 3 — крышка смотрового люка с отдушиной, окантованная с двух сторон вулканизированной резиной; 4 — фильтр из тонкой проволоки; 5 — установочный штифт конический; 6 — пробка маслослива; 7 — уплотняющая прокладка (кольцо); 8 — маслоуказатель; 9 — крышка подшипника закладная; 10 — компенсаторное кольцо (пружинное); 11 — манжетное уплотнение.
|
Шпоночное соединение –
Предохранительная муфта –
Расчет шпоночных соединений
|
Исходные данные берем из табл.5 и табл.23 и заносим в табл.28:
Таблица 28. Исходные данные
Диаметр посадочного места под зубчатое колесо; d К, мм | Диаметр выходного конца вал; d В, мм | Вращающий момент на ведомом валу: М2, Н·м | Допускаемое напряжение смятия, [σ]см, МПа. |
150 |
b |
d |

l |
A |
A |
Рис. 20. Соединение призматической шпонкой |



При конструировании нескольких шпоночных пазов на одном валу их располагают на одной образующей. Для разных ступеней одного и того же вала назначать одинаковые по сечению шпонки, исходя из ступени меньшего диаметра. Для соединений принимаем призматические шпонки (рис.20, табл. 29).
Таблица 29. Шпонки призматические ГОСТ 23360-78 (выборка)
Диаметр вала, d, мм | Сечение шпонки, мм | Глубина паза, мм | Диаметр вала, d, мм | Сечение шпонки, мм | Глубина паза, мм | ||||
b | h | вала, t1 | ступицы, t2 | b | h | вала, t1 | ступицы, t2 | ||
От 12 до 17 | 5 | 5 | 3 | 2,3 | От 50 до 58 | 16 | 10 | 6 | 4,3 |
От 17 до 22 | 6 | 6 | 3,5 | 2,8 | От 58 до 65 | 18 | 11 | 7 | 4,4 |
От 22 до 30 | 8 | 7 | 4 | 3,3 | От 65 до 75 | 20 | 12 | 7,5 | 4,9 |
От 30 до 38 | 10 | 8 | 5 | 3,3 | От 75 до 85 | 22 | 14 | 9 | 5,4 |
От 38 до 44 | 12 | 8 | 5 | 3,3 | От 85 до 95 | 22 | 14 | 9 | 5,4 |
От 44 до 50 | 14 | 9 | 5,5 | 3,8 |
Параметры выбранной шпонки: b = мм; h = мм; t1 = мм; t2 = мм.
Все полученные значения параметров, без указаний, округляем до ближайшего большего стандартного числа по ГОСТ 6636-69 (целого четного или кратного 5):
|
6.1.2. Определяем длину шпонки для соединения вала со звездочкой, lз:
с учетом конструктивного исполнения шпонки принимаем lз = мм.
6.1.3. Определяем длину шпонки для соединения вала с зубчатым колесом, lк:
с учетом конструктивного исполнения шпонки принимаем lк = мм.
Расчет штифта предохранительной муфты (рис. 21)
2 |
3 |
4 |
1 |
Рис. 21. Предохранительная дисковая муфта со срезным штифтом: 1, 2 – полумуфты; 3 – срезной штифт; 4 – втулки |


Таблица 30. Исходные данные
Передаваемый муфтой вращающий момент, МБ, Н·м, | Число штифтов, z | Радиус расположения оси штифта, R , мм |
1 | 45 |
Материал штифта – сталь 45; τв = 390 МПа.
6.2.1. Определяем предельный вращающий момент, передаваемый при нормальной работе муфты, Мпред:
Мпред = 1,25·МБ = 1,25∙ = Н×м.
6.2.2. Определяем диаметр штифта из расчета на срез, d ш:
По ГОСТ 3128-70 диаметры штифтов: 4, 5, 6, 8, 10, 12, 16, 20, 25, 30, 32, 40, 50 мм.
Принимаем штифт диаметром d ш = ____ мм.
ЗАКЛЮЧЕНИЕ
(Это образец, надо сделать свой текст в соответствии со своим проектом.)
При работе над курсовым проектом были закреплены знания методик расчетов типовых деталей машин общего назначения, получены навыки принятия решений при компоновке редуктора и конструировании его деталей.
Был выбран электродвигатель. При разбивке передаточного отношения редуктора были учтены рекомендации (4, 5, 6). Передаточные числа отдельных передач приняты согласно ГОСТ 2885-76 и 12289-76.
Проектный расчет зубчатых передач выполнен по критерию контактной прочности активной поверхности зубьев. После определения размеров передач проведены проверочные расчеты по критерию контактной и изгибной выносливости, а также при действии пиковых нагрузок. Все условия прочности выполняются. При компоновке механизма проработан вопрос оптимального размещения зубчатых передач в корпусе редуктора, определены схемы установки опор валов, способы осевой фиксации зубчатых колес, подшипников на валах. Были определены способ изготовления и размеры конструктивных элементов зубчатых колес, форма и размеры элементов корпуса редуктора.
Выбранные подшипники проверены на пригодность по их долговечности из расчета по динамической грузоподъемности.
Шпоночные соединения проверены на прочность по напряжениям смятия.
Определены опасные сечения валов по действующим нагрузкам, наличию и форме концентраторов напряжений. Проведен расчет на усталостную прочность (выносливость) для наиболее опасных сечений валов.
Решены вопросы смазки передач редуктора и подшипников. Для смазки подшипников быстроходного вала применена раздельная от передач смазка пластичным материалом (Литол-24).
Для соединения валов редуктора с электродвигателем и валом конвейера были выбраны муфты с упругими элементами, компенсирующие погрешности монтажа агрегатов.
Полученная конструкция привода в полной мере отвечает современным требованиям, предъявляемым к механизмам данного типа.
|
Литература
|
1. Анурьев В.И. «Справочник конструктора - машиностроителя». Издание
7-е в 3-х томах – М.: Машиностроение, 1982.
2. Боков В.Н. и др. Детали машин: Атлас конструкций. – М., 1983.
3. Вереина Л.И., Краснов М.М. Техническая механика: учебник для студентов учреждений среднего профессионального образования. – М.: Издательский центр «Академия», 2018.
4. Дунаев П.Ф., Леликов О.П. «Конструирование узлов и деталей машин», Москва: Издательский центр «Академия», 2003.
5. Иванов М.Н. «Детали машин» - М.: Высшая школа, 2003.
6. Указания к выполнению курсового проекта по дисциплине ОП.02 «Механика» раздел «Детали машин» для студентов специальности 26.02.05 «Эксплуатация судовых энергетических установок». Методическое пособие/ Сост. Е.В.Павлова – Ростов-на-Дону, 2018.
7. Решетов Д.Н. Детали машин: Атлас конструкций. – М., 1979.
8. Чернавский С. А., Боков К. Н., Чернин И. М. Курсовое проектирование деталей машин: Учебное пособие. – Издательство: ИНФРА-М, 2018 г.
9. Шейнблит А.Е. «Курсовое проектирование деталей машин» М., 2005.
10. Эрдеди А.А., Эрдеди Н.А. Детали машин. - М.: Высшая школа, Академия, 2017.
Дата добавления: 2019-01-14; просмотров: 449; Мы поможем в написании вашей работы! |
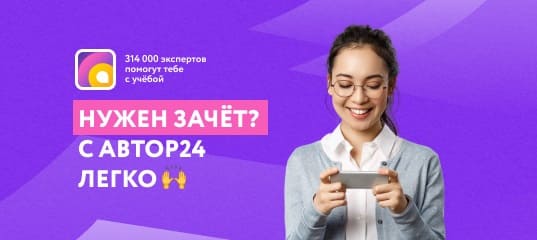
Мы поможем в написании ваших работ!