ИСПЫТАНИЯ НА УДАРНУЮ ВЯЗКОСТЬ. АНАЛИЗ И ОЦЕНКА СКЛОННОСТИ К ХРУПКОМУ РАЗРУШЕНИЮ КОНСТРУКЦИОННЫХ СТАЛЕЙ И ИХ СВАРНЫХ СОЕДИНЕНИЙ
Цель работы: изучение механических свойств материалов при испытаниях образцов с концентратором напряжений; освоение методик испытаний на ударный изгиб и определения критической температуры хрупкости.
Оборудование и материалы: маятниковый копер типа МК-30, испытательная машина с жесткой системой нагружения и электронной системой регистрации, криостат для охлаждения образцов, лабораторные электропечи СНОЛ для нагрева образцов, стереомикроскоп МБС-9, инструментальный микроскоп, токарный и фрезерный станки, заготовки для изготовления образцов, образцы и половинки испытанных в интервале температур образцов, штангенциркуль, миллиметровая бумага, персональный компьютер и оборудование для просмотра и фотографирования изломов образцов.
Задания: 1. Изучить роль концентраторов напряжений при оценке механических свойств, характера деформации и вида излома металлических материалов в интервале температур. 2. Изучить методологию температурных испытаний при растяжении. 3. Изучить устройство и работу маятникового копра. 4. Изучить методологию температурных испытаний при ударном изгибе. 5. Изучить изменение характера деформации и вида излома образцов для ударного изгиба в интервале температур ВХП. 6. Освоить методики определения и подтверждения критической температуры хрупкости конструкционных сталей.
Основные сведения
Конструктивная прочность и склонность к хрупкому разрушению.
|
|
Приведенные в лабораторной работе 11 данные нашли широкое применение при оценке стандартных механических свойств металлических материалов, характеризующих металлургические и технологическое качество материала. Эти характеристики используют при проведении расчетов на прочность слабо- или умеренно нагруженных изделий, работающих кратковременных статических нагрузках.
Однако, изменение условий нагружения (характер приложения нагрузки, температуры эксплуатации, внешней среды и т.д.), увеличение размеров эксплуатируемого оборудования, появление концентраторов напряжений, часто приводит к тому, что стандартных характеристик прочности и пластичности становится недостаточно для описания поведения материалов в реальных конструкциях. Более того, сконструированные без учета вышеуказанных факторов изделия могут неожиданно и самопроизвольно разрушаться, приводя к большим, а иногда и катастрофическим авариям с человеческими жертвами.
Совокупность механических свойств, обеспечивающих надежную и длительную работу материалов изделий в условиях эксплуатации называется конструктивной прочностью. Как правило, это комплексная характеристика, включающая сочетание критериев прочности, жесткости, надежности и долговечности, наиболее полно отражающих прочность изделий в заданных условиях эксплуатации. Оценка и расчет этих параметров с точки зрения «сопротивления материалов» рассмотрены в курсе «Детали машин и основы конструирования».
|
|
Рассмотрим более подробно вопросы надежности работы конструкций, которые в вышеупомянутом курсе
практически не рассматриваются. Надежность конструкции обеспечивается, если последняя сохраняет прочность, жесткость и устойчивость при гарантированной долговечности. На рис.12.1 показано, в каких случаях надежность конструкции не обеспечивается. Потеря прочности – это разрушение (разделение на части) изделия в процессе эксплуатации (Рис.12.1а). Недостаточная жесткость (Рис.12.1б) обусловлена появлением остаточных деформаций при эксплуатации изделия. Потеря устойчивости (Рис.12.1в) означает, что конструкция теряет свою форму, выходя из устойчивого состояния по какой-либо причине, и не возвращается в это первоначальное состояние. Если расчеты на прочность в соответствии с существующими нормами гарантируют работоспособность во всех вышеприведенных случаях, конструкция должна надежно работать в процессе длительной эксплуатации.
|
|
Однако, есть материалы, которые в определенных условиях в процессе эксплуатации могут разрушаться, даже если расчеты гарантируют надежную работу конструкции. Это материалы, склонные к хрупкому разрушению. В результате получается, что фактически надежность – это способность материалов конструкций противостоять хрупким разрушениям, так как такое разрушение – наиболее опасная причина внезапного отказа деталей в условиях эксплуатации. Хрупкое разрушение происходит неожиданно и протекает с большой скоростью при номинальных напряжениях ниже расчетных. Факторы, увеличивающие опасность хрупкого разрушения, - это наличие или появление в процессе эксплуатации концентраторов напряжений, понижение температуры, динамические нагрузки, большие размеры деталей.
Влияние концентрации напряжений на характер деформации и разрушения. Если сравнить выполненные в одинаковых условиях кривые растяжения гладкого цилиндрического образца и образца с кольцевой выточкой (надрезом), диаметр которой равен диаметру гладкого цилиндрического образца (Рис.12.2), можно обнаружить существенные различия (Рис.12.4). Во-первых, образец с выточкой значительно жестче, так как деформация в нем сосредоточена в области концентратора напряжений, но ограничена в области с диаметром D, так как номинальные напряжения там (из-за большего диаметра) значительно ниже предела текучести. В гладком образце ограничений для пластической деформации нет, линии скольжения свободно выходят на боковые поверхности образца; в результате, деформация равномерна по всей рабочей длине образца (L0). Во-вторых, напряжения по сечению образцов распределены по-разному. В гладком образце напряженное состояние – одноосное: номинальное напряжение (Ϭн) одинаково по всему сечению (Рис.12.3а). В надрезанном образце действует объемное трехосное напряжение растяжения, причем Ϭmax в направлении растяжения сосредоточено в области концентратора напряжений, а его величина больше, чем Ϭн (Рис.12.3б). При объемном напряженном состоянии, в-третьих, течение стеснено по сравнению с одноосным и возникает при более высокой внешней нагрузке.
|
|
Действие всех этих факторов мы и наблюдаем на кривой деформации надрезанного образца (Рис.12.4). Модуль упругости образца с надрезом больше, что хорошо видно из сравнения начальных участков кривых (Рис. 12.4 слева), так как на упругом участке кривая деформации надрезанного образца круче. Предел текучести и предел прочности надрезанного образца существенно больше, т.е. деформация и разрушение в нем происходит при больших напряжениях. Однако, относительное удлинение надрезанного образца намного (в несколько раз) меньше, в то время, как пластическое течение гладкого образца осуществляется легко из-за релаксации напряжений при выходе полос скольжения на боковую поверхность образца в процессе равномерной деформация (до появления шейки). Соответственно, механическая вязкость надрезанного образца (площадь под кривой растяжения в координатах Р - ∆ℓ), т.е. способность необратимо поглощать энергию в процессе пластической деформации, упрочнения и разрушения, - значительно меньше.
Таким образом, в образцах с концентратором напряжений деформация существенно затрудняется и локализуется в области концентратора, где наибольшая величина напряжений (Ϭmax). Здесь процессы упрочнения и разрушение начинаются значительно раньше. Чем больше острота концентратора напряжений и глубина надреза, тем сильнее выражен этот эффект. Выявленные закономерности характерны для любых металлических материалов. Практически
все реальные конструкции имеют какие-либо конструктивные концентраторы напряжений. Концентраторами напряжений являются также внутренние или внешние дефекты макроструктуры, появляющиеся в процессе изготовления или эксплуатации изделия. Все они оказывают влияние на поведение материала, усиливая неоднородность деформации.
Для материалов, испытывающих вязко-хрупкий переход (ВХП) при понижении температуры (а это все ОЦК- и часть ГПУ-металлов), концентраторы напряжений резко усиливают эффект охрупчивания. При этом интервал температур ВХП резко (на десятки и даже сотни градусов) повышается по сравнению с результатами, полученными на гладких цилиндрических образцах. При испытаниях в интервале температур охрупчивания (на жестких разрывных машинах с температурной камерой) машинные кривые растяжения в координатах Р – Δ l при разных температурах будут существенно отличаться (Рис.12.5). При высоких температурах (выше точки ТА) кривые растяжения будут иметь колоколообразный вид (Рис.12.5о), а излом полностью вязкий – ямочный (Рис.12.6а). Упругая энергия в процессе растяжения расходуется на процессы деформации, упрочнения и продвижения вязкой трещины из вершины надреза. При очень низких температурах (ниже точки ТВ) кривые растяже-
ния будут иметь вид треугольника (Рис.12.5в). Разрушение происходит в точке 1 на прямолинейном восходящем участке кривой растяжения – в упругой области. Здесь при нагружении вся потенциальная энергия деформации представляет собой упругую энергию, накопленную при упругом искажении кристаллической решетки металла (Рис.11.1). В момент разрушения вся эта упругая энергия, равная площади треугольника 0-1-2, высвобождается с резким звуковым эффектом. Излом здесь полностью хрупкий, макроскопически плоский и совпадает с плоскостью надреза; разрушение осуществляется путем скола по плоскостям спайности (Рис.12.6б). После хрупкого разрушения упругие искажения кристаллической решетки исчезают (Рис.11.1а).
При растяжении в интервале температур ВХП на кривой растяжения при нагрузках выше предела упругости появляется нелинейный участок 1-3. Здесь осуществляется пластическая деформация, упрочнение, потеря сплошности и медленное вязкое продвижение трещины в области концентратора напряжений (Рис.12.7). Во всем этом интервале температур развитие вязкой трещины неожиданно прерывается хрупким разрушением. При этом площадь под кривой растяжения состоит из двух частей (Рис.12.5 а,б):
1/ Площадь, ограниченная справа отрезком 3-4, параллельном линии нагружения на упругом участке. Эта площадь представляет собой необратимые потери энергии, связанные с пластической деформацией, упрочнением и подрастанием вязкой трещины. Эти потери представляют собой механическую вязкость материала, имеющего концентратор напряжений (Ан).
2/ Площадь треугольника 3-5-4, представляющая собой упругую энергию, высвобождающуюся при хрупком разрушении (Аупр). Эта энергия не может быть отнесена к вязкости, так как не связана с необратимыми потерями при пластической деформации и упрочнении образца. Выделяющаяся при хрупком разрушении упругая энергия переходит, в основном, в кинетическую энергию движения разделившихся половинок образца, упругие колебания, распространяющиеся в элементах нагружающей системы, ударную волну в воздухе (резкий звуковой эффект), колебания атомов на вновь образовавшейся поверхности разрушения сколом. В конечном итоге, все эти динамические эффекты в соответствии с первым законом термодинамики приводят к увеличению теплоты.
Трещина хрупкого разрушения возникает в плоскости кольцевого надреза на некотором расстоянии от его вершины. Очаг трещины связан, как правило, с наиболее крупным скоплением неметаллических включений или другим микроскопическим дефектом вблизи кольцевого надреза. Место расположения этого очага довольно легко выявляется при макрофрактографическом анализе излома в виде концентрически расходящихся от него лучей. Ниже некоторой температуры Тθ вязкое разрушение ограничено кольцевой зоной среза, расположенного под углом 450 к плоскости надреза. Кривая растяжения здесь ограничена восходящим участком (Рис.12.5б). Выше этой температуры на кривой растяжения появляется нисходящий участок (Рис.12.5в), протяженность которого определяется неожиданным проявлением хрупкого разрушения. На изломе разрушенного образца выявляется зона подрастания вязкой трещины ℓ c (Рис.12.7), ограниченная изнутри зоной макроскопически хрупкого разрушения. Последняя представляет собой эллипс, площадь которого легко рассчитывается.
Площадь макроскопически хрупкого разрушения (S хр) прямо пропорциональна упругой энергии (Аупр), высвобождающейся при хрупком разрушении этого образца (Рис.12.8). Коэффициент пропорциональности (G) представляет собой трещиностойкость при хрупком (квазихрупком) разрушении. Трещиностойкость характеризует критический уровень упругой энергии, при котором может возникнуть хрупкое разрушение.
При трехточечном изгибе призматического образца с боковым надрезом (Рис.12.9) закономерности разрушения в интервале ВХП сходны с рассмотренными выше для растяжения цилиндрического образца с кольцевым надрезом. Кривая нагрузка-деформация при изгибе (Р – f, где f - стрела прогиба), характерная при разрушении в интервале ВХП, приведена на рис.12.8. Левая часть кривой аналогична с приведенной, например, на рис.12.5в. Однако, в правой части диаграммы появляются новые участки, связанные с наличием напряжений сжатия, характерных для изгиба (Рис.12.10).
Рассмотрим подробнее появление этих участков. При изгибе образца под концентратором напряжений появляются упругие, а затем и пластические деформации, упрочнение и разрушение (все как описано для растяжения образца с концентратором напряжений). Наиболее интенсивно этот процесс развивается в средней части зоны надреза, где действует объемное напряженное состояние. Поэтому здесь и появляется вязкая трещина, распространяющаяся в плоскости надреза вглубь образца. У боковых поверхностей изгибаемого образца полосы деформации могут выходить на эти поверхности, уменьшая уровень напряжений, и разрушение здесь
тормозится. При накоплении критического уровня упругой энергии, характеризуемого величиной трещиностойкости G, происходит неожиданное хрупкое разрушение. Однако, разделения образца на две части не происходит, так как запаса упругой энергии становится недостаточно для продвижения хрупкой трещины внутри образца в зону сжатия, характерную для изгиба (Рис.12.10). Разрушение может возобновиться в точке 5 (Рис.12.9), если подвод упругой энергии продолжится. При этом требуется значительно меньшая действующая нагрузка, соответствующая линии 5-6 (Рис.12.9), так как фактическая глубина надреза уже увеличилась на линейный размер трещины хрупкого разрушения. Вначале вновь осуществляется подрастание вязкой трещины, а за
тем хрупкое разрушение (точка 6 на рис.12.9). Наличие всех этих участков отражается на кривой деформации при изгибе; можно, например, выявить участки, соответствующие упругой энергии, высвободившейся при хрупком разрушении (3-4-5-5') и (6-7-9-8) (Рис.12.9). Исключив эти участки из площади под кривой деформации, можно получить механическую вязкость при статическом изгибе. На изломах можно выявить зоны вязкого подрастания трещины и хрупкого излома
(Рис.12.11) и связать их с характером кривой нагрузка – прогиб.
Так как на образцах, как правило, присутствует только один концентратор напряжений – боковой надрез, в процессе пластической деформации полосы скольжения могут свободно выходить на гладкие боковые поверхности, параллельные плоскости изгиба. Это приводит к релаксации напряжений в зонах, прилегающих к этим поверхностям. Упругие напряжения концентрируются в центральной зоне под надрезом. При хрупком разрушении трещина проскакивает в зоне максимальных напряжений, а на боковых участках, где напряжения по вышеуказанной причине меньше, происходит вязкое разрушение путем среза оставшегося сечения под углом около 450 к плоскости излома (рис.12.11). Эти зоны получили наименование «Губы среза».
При испытаниях на статический изгиб достаточно легко моделировать влияние увеличения остроты и глубины надреза, размера образца и скорости нагружения на параметры и характеристики разрушения. Все эти изменения увеличивают жесткость нагружения, так как приводят к созданию условий, при которых достигается увеличение запаса упругой энергии, а следовательно, и более благоприятных условий для возникновения неожиданного хрупкого разрушения. Все испытания необходимо проводить на жесткой испытательной машине с электронной регистрацией нагрузок и деформаций.
Испытания на ударную вязкость.
В инженерной практике металлургических и машиностроительных заводов, на предприятиях, эксплуатирующих такие опасные объекты, как сосуды под давлением, трубопроводы и т.д., очень широкое применение получили испытания на ударный изгиб призматических образцов с боковым надрезом. В России такие испытания регламентированы ГОСТ 9454-78 и получили наименование испытаний на ударную вязкость. В основном, такие испытания проводятся для оценки склонности материалов к хрупкому разрушению.
Особенности деформации и разрушения при испытаниях на ударную вязкость аналогичны рассмотренным чуть выше испытаниям на статический трехточечный изгиб. Однако последние медленны и трудоемки и не применимы в текущем контроле металлопродукции на металлургических и сталепрокатных заводах и крупных энергомашиностроительных предприятиях. Не все данные, которые можно получить из анализа диаграмм нагрузка-прогиб, необходимы для экспресс-оценки склонности к хрупкому разрушению. Более того, эту оценку желательно проводить в наиболее жестких условиях, которые обеспечивают испытания на ударный изгиб.
Для испытаний используют так называемые маятниковые копры (Рис.12.12) с жестким массивным П-образным основанием, вмонтированным в фундамент. На выступы поперек основания устанавливается призматический образец с надрезом
Испытания на ударную вязкость. Испытания на ударный изгиб для чёрных, цветных металлов и сплавов регламентируется ГОСТ 9454-78 (Приложение 2). Испытания проводятся в диапазоне температур о т минус 10 0С до плюс 30 0С. Метод основан на разрушении образца с концентратором посередине одним ударом маятникового копра (Рис.10.1). В результате испытания определяют полную работу, затраченную при ударе или ударную вязкость.
Вязкость твёрдого тела – свойство необратимо поглощать энергию при пластическом деформировании и разрушении разрушения.
4.1. Типовая схема испытания:
- измерить размеры образца;
- проверить совпадение стрелочного указателя (Рис.10.1, поз.3) с нулевым делением круговой шкалы при свободно висящем маятнике;
Рис. 10.1. Маятниковый копёр для испытания материалов на ударную вязкость:
1 - маятник; 2 - образец; 3 - стрелка; 4 - шкала.
- установить образец на опоры надрезом в противоположную сторону
от маятника копра (Рис.10.2);
- поднять маятник на исходную высоту и зафиксировать на защёлку;
- настроить автоматизированную систему обработки результатов;
- произвести испытание, освободив маятник от защёлки;
- зафиксировать угол взлёта маятника после разрушения образца;
Рис. 10.2. Расположение образца перед началом испытания.
- сохранить результаты и вывести протокол испытаний.
Работа, затраченная на разрушение образца, будет равна разности энергии маятника до и после удара.
4.2. Силовое оборудование для испытаний.
Рисунок 10.3. Маятниковые копры для ударных испытаний: а) МК-15; б) МК-30.
Копёр состоит из чугунной станины в виде массивной плиты 2 с двумя вертикальными колоннами 3. В верхней части колонн на горизонтальной оси подвешен укреплённый в шарикоподшипниковых опорах маятник с грузом в виде стального плоского диска с вырезом 5, в котором закреплён стальной закалённый нож, служащий бойком при испытании (Рис 10.3).Внизу на уровне вертикально висящего маятника к колоннам станины прикреплены две стальные закалённые опоры 10, на которые помещают образец 11. Под опорами между колоннами проходит тормозной ремень 12, который, прижимаясь к маятнику, качающемуся после удара, вызывает его торможение. Тормозной ремень приводится в действие вручную рукояткой 1 (МК-15) или автоматической рукояткой 1(МК-30).
4.3. Образцы.
ГОСТом 9454-78 предусмотрено использование 20 типов образцов, различающихся как собственными размерами, так и размерами концентраторов при трёх видах надрезов, Рис. 4.7.
Рис. 10.7. Образцы с концентраторами:
а) U -образный; б) Т-образный с усталостной
трещиной; в) V-образный.
4.4. Характеристики материала получаемые из испытаний.
1. Работа удара - обозначается буквами KU, KV, KT и цифрами. Первая буква К обозначает символ работы удара, вторая буква U, V, T- вид концентратора. Последующие цифры обозначают: максимальная энергия удара маятника, глубину концентратора, ширину образца. Например: KV-40 50/2/2 – работа удара, определённая на образце с концентратором вида V при температуре минус 40 0С. Максимальная энергия копра 50Дж, глубина концентратора 2 мм, ширина образца 2 мм. Если испытания проводятся при Т = 20 ± 10 0С, то температура в обозначениях не проставляется.
Величина работы К, затраченной на излом образца, определяется как разность потенциальной энергии маятника в его положениях до и после удара (Рис. 4.8) и вычисляется по формуле:
К = Q∙(H1–H2),
где Q – вес маятника, Н;
H1 – высота подъёма маятника до удара, м;
H2 - высота подъёма маятника после удара, м.
Рис. 10.8. Схема определения энергии копра до и после удара.
Вводя соответствующие обозначения, получаем:
H1 = R - R× sin (a-900) = R (1-cosa),
H2 = R - R× cosb = R (1-cosb),
где R – длина маятника (расстояние от центра тяжести маятника до его оси вращения). Следовательно, работа маятника:
К = Q× R× cosb = R(cosb-cosa).
2. Ударная вязкость ( K С) – отношение работы К, затраченной на разрушение образца, к площади поперечного сечения А0 в месте надреза:
КС = К / А0, А0 = H1×В,
где А0-площадь поперечного сечения образца в плоскости надреза, м2;
H1- начальная высота рабочей части образца, м;
В - начальная ширина образца, м.
4.4. Определение хладноломкости материалов с помощью испытаний на ударный изгиб.
Хладноломкость – способность материалов хрупко разрушаться при низких температурах.
Хрупкое разрушение – разрушение, не сопровождающееся макроскопически выраженной остаточной деформацией и происходящее по механизму отрыва.
Хладноломкость материалов характеризуется критической температурой хрупкости (Тк0). Под Тк0 понимается температура, принимаемая за температурную границу изменения характера разрушения материала от хрупкого к вязкому. Она определяется:
v по энергии, затрачиваемой на разрушение, в качестве показателя которой принимается ударная вязкость;по виду излома образцов, в качестве показателя которого принимается доля вязкой составляющей в изломе или (значительно реже) значение поперечного расширения образца в зоне излома.
Для определения критической температуры хрупкости проводят испытания образцов с надрезом типа V на ударный изгиб в выбранном интервале температур. На основании полученных результатов испытаний строят зависимости ударной вязкости и/или вязкой составляющей в изломе (Рис. 4.9) от температуры испытаний. Значения критической температуры хрупкости определяют по заданным критериальным значениям ударной вязкости и/или вязкой составляющей в изломе. На Рис.10.9 для стали с содержанием углерода С = 0,09% пороговая температура Тк0 = 0 0С, т.е. ниже этой температуры материал при ударном нагружении будет разрушаться хрупко и при низких энергетических затратах (Рис.10.9,а).
КС V , Дж/м2
-80 -40 0 40 80
Температура испытаний, 0С
Рис. 10.9. Сериальные диаграммы ударной вязкости образцов с V-надрезом
(а) и доля волокна (В, %) в изломе (б). Низкоуглеродистая сталь с 0,09 % С [2 ].
·ЗАДАНИЕ И ТРЕБОВАНИЯ К СОДЕРЖАНИЮ ОТЧЁТА·
1.Изучить характеристики вязкости материалов и метод их определения в ГОСТ 9454-78 (Приложение 2) при нагружении образцов по схеме ударного изгиба.
2.Составить краткий отчёт, который должен содержать:
- наименование практической работы;
- цель работы;
- краткая схема испытания;
- ответы на контрольные вопросы.
·КОНТРОЛЬНЫЕ ВОПРОСЫ·
1. В чём заключается отличие вязкости твёрдого материала от вязкости жидкостей и газов?
2. Чем вызвана необходимость проведения испытаний на ударный изгиб?
3. Что больше – KCU или KCV одного и того же материала? Почему?
4. У каких материалов будет больше ударная вязкость:
с sВ = 300МПа и d = 32% или с sВ = 800МПа и d = 1,5%.
5. Возможна ли запись диаграммы нагружения при ударном изгибе?
6. Что характеризует критическая температура хрупкости?
7. Может ли Тк0 быть выше комнатной температуры? Ответ обосновать.
Список использованной литературы
1. Золотаревский В.С. Механические свойства металлов. М. МИСИС. 1998. 400с.
2. Ю.А. Геллер, А.Г. Рахштадт. Материаловедение. Методы анализа, лабораторные
работы и задачи. М. Металлургия. 1989. 456с.
3. А.И. Самохоцкий, М.Н. Кунявский. Лабораторные работы по металловедению и
термической обработке металлов. М. Машиностроение. 1981. 174с.
4.ГОСТ 9454-78. Металлы. Метод испытания на ударный изгиб при пониженных,
комнатной и повышенных температурах. М. Изд. стандартов. 1998. 31с.
5. В.Ю. Гольцев. Методы механических испытаний и механические свойства
материалов. М. НИЯУ МИФИ. 2012. 227с.
6. Я.Б. Фридман. Механические свойства металлов. Том 2. Механические испытания.
Конструктивная прочность. М. Машиностроение. 1974. 368с.
Приложение № 1
Дата добавления: 2019-01-14; просмотров: 790; Мы поможем в написании вашей работы! |
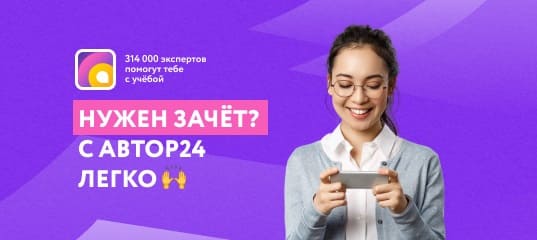
Мы поможем в написании ваших работ!