ТЕХНОЛОГИИ ИСПОЛЬЗОВАНИЯ ШАХТНЫХ ВОД 11 страница
3) флотация с подачей воздуха через пористые материалы;
4) электрофлотация;
5) биологическая и химическая флотация.
Флотация с выделением воздуха из раствора применяется для очистки вод, содержащих очень мелкие частицы, поскольку позволяет получать самые мелкие пузырьки воздуха. Суть метода заключается в создании перенасыщенного раствора воздуха в жидкости, а затем уменьшении давления, благодаря чему начинается бурное выделение из раствора микропузырьков газа. Количество воздуха, которое выделилось из перенасыщенного раствора, должна составлять при эффективной флотации 1...5% объема обрабатываемой воды. Для повышения эффективности работы установок флотаций целесообразно предварительно удалять из воды наиболее крупные и тяжелые частицы.
По способу перенасыщение различают три вида флотации с выделением воздуха из раствора: вакуумная, напорная и эрлифтная.
При вакуумной флотации сточную воду воздухом при атмосферном давлении в аэрационной камере. Потом ее в камеру флотации, где вакуумом в течение 20 минут. поддерживают разрежение (200...300 мм.рт.ст.). Преимуществом вакуумной флотации является то, что образование пузырьков газа, их слипание с частицами и всплывания комплексов “частица-пузырек” происходит в спокойной воде, а потому вероятность их разрушения минимальна; минимальны также энергозатраты на насыщение жидкости воздухом, образование и измельчение воздушных пузырьков. К недостаткам способа относятся незначительная степень насыщения стоков пузырьками воздуха, а следовательно, нецелесообразности применения метода при высокой концентрации взвешенных веществ (более 250 мг/л); необходимость сооружения герметически закрытых флотаторов.
|
|
Напорная флотация имеет большую область применения. Все шире ее начинают использовать для очистки от взвешенных веществ шахтных вод. Она позволяет очищать воды с концентрацией взвешенных веществ до 5000 мг/л и более. Она используется как в безреагентных, так и реагентных режимах.
Процесс напорной флотации имеет две стадии: насыщение воды воздухом в течение 15 мин. под давлением 0,15..0,4 МПа в напорной камере (сатураторовые); выделение воздушных пузырьков из раствора под атмосферным давлением.
При использовании данной схемы воздухом, а затем очищается весь объем сточной воды. При большом содержании взвешенных веществ в исходной воде, такая схема малоэффективна.
Эрлифтная флотация требует в 2...4 раза меньше затрат энергии, но требует значительного перепада отметок по высоте между приемной емкостью и аэратором, а также между аэратором и флотатором (разность отметок составляет 20...35 м).
|
|
Флотация с диспергированием воздуха. Диспергирование воздуха в воде достигается механическими и пневматическими методами.
Механическое диспергирование воздуха осуществляется с помощью импеллерных установок флотации. Импеллер – это турбина (диск) насосного типа диаметром 600...700 мм с радиальными лопатками, обращенных вверх. При его вращении возникает множество мелких вихревых потоков, которые разбиваются на пузырьки воздуха определенной величины. Степень измельчения пузырьков и эффективность очистки зависят от скорости вращения импеллера. С увеличением скорости размеры пузырьков уменьшаются, и возрастает эффективность флотации. Но возникает турбулентность потока, которая способствует разрушению комплексов, а, следовательно, снижает эффективность очистки.
Применение импеллерних установок целесообразно при очистке сточных вод с высокой концентрацией взвешенных веществ (более 2...3 г/л).
Пневматическое диспергирование воздуха отличается простотой и экономичностью. Обычно в пневматических установках флотации измельчение пузырьков воздуха достигается пропусканием его через специальные сопла, устанавливаемые на распределительных трубках. Диаметр одного сопла примерно 1 мм; давление воздуха перед ним 0,3...0,5 МПа; скорость выхода струи из сопла 100...200 м/сек.
|
|
Как аэраторы могут применяться не только сопла, но также пористые керамические пластины, колпачки, резиновые трубки с наколотыми отверстиями и др. В этих случаях имеет место флотация с подачей воздуха через пористые материалы. Недостатком этого метода является возможность засорения и зарастания пор, а также трудность набора мелкопористых материалов, обеспечивающих выход мелких пузырьков воздуха, близких по своим размерам.
Электрофлотация. Суть очистки сточных вод методом электрофлотации заключается в подъеме взвешенных веществ из объема жидкости на ее поверхность с помощью пузырьков газа, образующихся при электролизе воды. В процессе электролиза сточной воды на аноде выделяются пузырьки кислорода, хлора и других газов, а на катоде - водорода. Основную роль в процессе флотации частиц играют пузырьки водорода. Их размер значительно меньше размеров пузырьков воздуха при других методах флотации (от 20 до 100 мкм).
Размер пузырьков водорода зависит от материала катода, диаметра катода и плотности тока. Материал катода определяет угол смачивания: чем менее гидрофобный материал катода, тем легче отрываются мелкие пузырьки водорода от поверхности катода и, выделяясь в раствор, насыщая его. Из пересыщенного раствора мельчайшие пузырьки газа выделяются на поверхности взвешенных веществ и флотируют их. Чем больше кривизна катода (то есть меньше его диаметр), тем более мелкие пузырьки водорода выделяются в раствор. Рекомендуется применять не пластинчатые, а проволочные катоды.
|
|
Электрофлотация является перспективным направлением очистки шахтных вод. Это обусловлено, во-первых, высокой эффективностью и скоростью процесса очистки; во-вторых, минимальным расходом реагентов-собирателей при применении растворимых анодов; в-третьих, наличием электрокинетических явлений в приэлектродного зонах.
ЛЕКЦИЯ 16
УДАЛЕНИЕ ВЗВЕШЕННЫХ ВЕЩЕСТВ ИЗ ШАХТНЫХ ВОД ФИЛЬТРОВАНИЕМ
1 Принцип действия и типы фильтров
Фильтрование является наиболее распространенным методом очистки природных и многих сточных вод.
Фильтрация – это гидромеханический (при процеживании) или физико-химический (при объемном фильтровании) процесс удаления примесей, что протекает в фильтрующем элементе за счет разницы давления до и после фильтрующего элемента. В переводе с латыни filtrum - войлок.
В качестве фильтрующих элементов могут быть тонкие перегородки с порами или объемные элементы с пористыми наполнителями. В зависимости от этого различают два принципа действия фильтров.
Если фильтрующий элемент тонкой пористой перегородкой, то он работает по принципу процеживания. При процеживании в фильтрующем элементе (типа сетки, ткани) содержатся поры с поперечным сечением меньшим, чем размеры частиц взвешенных веществ, изымаются. В этом случае действует сугубо гидромеханический механизм удаления примесей из воды. Схематично процесс процеживания изображен на рис. 7.1.
Рис. 7.1. Удаление взвешенных веществ процеживанием
При пропускании суспензии через перфорированную перегородку вначале задерживаются частицы, размер которых больше размера пор. При закупорке пор увеличивается гидравлическое сопротивление перегородки и уменьшается размер пор. В дальнейшем в более мелких порах, образовавшиеся мелкие частицы заклиниваются, и постепенно при перегородке образуется слой осадка, через который собственно и фильтруется суспензия. Процеженная вода называется фильтратом. Объем фильтрата, получаемого в единицу времени с единицы поверхности фильтра, называется скоростью фильтрации (VФ).
В объемных фильтрах размер пор гораздо больше размеры зависших (и коллоидных) примесей воды, а их задержание протекает за счет контактной коагуляции (см. 5.1.4). Как правило, вода перед фильтрованием обрабатывается коагулянтами или флокулянтами для астабилизации частиц примесей в фильтрующем элементе прилипают к контактных поверхностей (волокон или зерен). Так вот в данном случае действует не гидромеханический, а физико-химический механизм удаления примесей из
воды. В поровом среде объемных фильтров накапливаются загрязнения и продукты гидролиза коагулянтов, которые уменьшают объем пор и вызывают рост гидравлического сопротивления фильтра.
По типу фильтрующих элементов различают следующие фильтры:
• сетчатые
• тканевые
• мембранные
• намывные
• волокнистые
• зернистые.
Первыми четырьмя типами являются пористые перегородки, последние два, - объемные элементы.
Наиболее широко применяются объемные зернистые фильтры, поэтому они представлены наиболее полно (подраздел 7.5). Остальные типы фильтров описаны обзорно. При этом надо иметь в виду, что тканевые фильтры используются для очистки воды, для обезвоживания осадков.
2 Сетчатые фильтры
Для изготовления сеток применяют металлы, не коррозируют: латунь, бронзу, нержавеющую и оцинкованную сталь. По способу изготовления различают сетки колосниковые (щелевые) и тканые. В технологии очистки воды применяются исключительно последние.
Наиболее распространенными типами сетчатых фильтров является микрофильтры и барабанные сетки.
Микрофильтры применяют для удаления из природной воды планктона и водорослей при их содержании свыше 1000 клеток/мл, а также для доочистки сточных вод от биоценозов микроорганизмов. Задерживают они также до 25% взвешенных примесей взвесей. Основным их рабочим элементом является горизонтальный барабан с поверхностью из двух слоев сетки: рабочего микросетки с ячейками 40 мкм и поддерживающей сетки с ячейками 2...5 мм. Сетки галунового плетения изготавливаются из нержавеющей стали. Барабан погружен в воду на 3/5 диаметра и в рабочем состоянии неподвижен. Вода фильтруется изнутри наружу, примеси остаются на внутренней поверхности барабана. По мере загрязнения сетки ее сопротивление и при потерях напора 0,2 м требуется ее чистка.
Для чистки включается вращение барабана от привода (через шестеренку и большое зубчатое колесо на торце барабана) и подводится промывочная (фильтрованная или процеженная) вода с давлением не менее 0,15 Мпа. Струи промывной воды смывают загрязнения в желоба, откуда они по центральной трубе сливаются в канализацию. Расход воды на промывку составляет 1,5% от процеженной количества. Промывка системы микрофильтрации может быть автоматизирована.
Барабанные сетки применяются как входные устройства, предназначенные для удаления грубых взвешенных примесей. Конструктивно они аналогичны микрофильтрами, отличаются от них величиной ячеек рабочей сетки, что составляет 0,2...0,5 мм.
3 Намывные фильтры
Принцип действия намывных фильтров состоит в том, что на пористые перегородки (в виде цилиндров с поверхностью из металлических сеток, проволочных навивок или капроновых сеток на перфорированных каркасах, пористой керамики) наносится фильтрующий порошок (диатомит, перлит, целлюлоза, бентонит, древесная бы), что создает мелкие поры, через которые и фильтруется вода. Применяются намывные фильтры для очистки маломутных вод в напорных схемах очистки. Кроме того, они удаляют из воды органические вещества, масла. Конструкция намывного патронного фильтра приведена на рис. 7.2.
Работают эти фильтры под давлением в следующем режиме: сначала в течение 5...10 минут проводится намыв суспензии порошка на фильтрующие элементы (суспензия вводится в исходную воду) со скоростью 3 м/ч из расчета 300...400 г/м2.. После намыва на протяжении 36...60 часов идет рабочий фильтроцикл: - вода фильтруется внутрь патронов сквозь слои осадка, намывного порошка и перегородки. Осадок и порошок содержатся при этом на вертикальных поверхностях за счет разницы давления 0,15.0,20 МПа. В состав порошков может включаться активированный уголь.
Рис. 7.2. Схема работы намывного фильтра: 1 - бункер с фильтрующим порошком, 2 – гидроэлеватор,3 - намывной фильтр, 4 - патрон, 5 - намывной слой.
Для чистки патронов давление снимается (перекрывается подвод исходной воды), давление снаружи и внутри патронов выравнивается, осадок с порошком под действием силы тяжести отделяется от подложки и выпадает в конусную часть корпуса, откуда сбрасывается за пределы аппарата. Возможна регенерация и повторное использование порошка из осадка. В некоторых аппаратах для улучшения чистки патронов от порошка и осадка в обратном направлении подводится сжатый воздух или даже пара.
Основные расчетные параметры намывных фильтров:
• скорость фильтрации 1...50 м/ч
• продолжительность промывки 15 мин
• -потери воды при промывке 0,5...0,7 %.
4 Волокнистые фильтры
Традиционное применение волокнистых фильтров для очистки газов. Только в последнее время они стали использоваться в современных водоочистительных аппаратах.
В качестве фильтрующих элементов используются минеральные (стеклянные, базальтовые) и органические волокна. Последние преобладают и делятся на три класса: природные (шерсть, хлопок), искусственные (вискоза, целлюлоза), синтетические (полимерные). Наибольшие перспективы имеют синтетические волокна, они делятся на две группы:
* карбоцепочные (содержащих в основном полимерном цепочке только молекулы углерода)
* гетероцепочные (молекулы кислорода, азота и другие, содержащиеся в основной цепи).
Карбоцепочные волокна позволяют прививать к основной цепи сополимеры, которые обеспечивают специфические свойства. Изменяя привитые сополимеры, можно получить волокна специального назначения: ионообменные, сорбенты, антимикробные.
Для удаления взвешенных веществ используют гетероцепочные волокна, в основном полиамидные (капрон) и полиэфирные (лавсан). Достоинствами синтетических волокон является химическая стойкость, малая плотность, высокая удельная поверхность.
Среда волокнистых фильтров может формироваться из неурегулированных (перепутанных) волокон или из структурированных волокон (например, в форме ершей).
Волокнистые фильтры применяются в бытовых водоочистительных фильтрах, для очистки промышленных сточных вод. На рис. 7.3 приведена принципиальная схема волокнистого фильтра, разработанного в ДонНТУ и Донбасской национальной академии строительства и архитектуры. Такие фильтры нашли применение для грубого освещения шахтных вод.
Основным элементом фильтра является волокнистая среда (насадка) из синтетических волокон в форме ершей. Вода, обработанная коагулянтами или флокулянтами, движется снизу вверх через насадку, при этом астабилизированные доли примесей за счет действия контактной коагуляции прилипают к волокнам и изымаются из воды. Для чистки насадки от загрязнений она продувается сжатым воздухом (при отключенном фильтре), при этом пузырьки воздуха отрывают задержанные примеси от волокон и последние очищаются. Загрязненная вода в то же время сбрасывается с корпуса фильтра снизу.
Рис. 7.3. Волокнистый фильтр конструкции ДонНАСа: 1 - подвод исходной воды в рабочем режиме и сброс загрязненной воды при регенерации, 2 - призматическая часть, 3 - волокняна насадка, 4 - отвод осветленной воды, 6 - коллектор сжатого воздуха, 7 - боковые ответвления для распределения сжатого воздуха по площади фильтра
Волокнистые фильтры имеют очень большую поруватість (до 99 и более процентов), развитую поверхность насадки, незначительное гидравлическое сопротивление.
5 Скорые фильтры
Так называются наиболее распространенные на практике зернистые фильтры.
Быстрые фильтры предложенные американским инженером Хайятом в 1884 г. и назывались раньше американскими. Они работают по принципу объемного фильтрования, при котором примеси задерживаются во всем объеме фильтрующей среды в порах на поверхности зерен. Это возможно при предварительной обработке воды коагулянтами.
Быстрые фильтры применяются как сооружения финишной очистки воды, мутность фильтрата не должна превышать 1,5 мг/л.
5.1 Основные виды зернистых фильтрующих материалов
Наиболее распространенным и традиционным зернистым материалом для скорых фильтров является кварцевый песок. Этот материал должен содержать не менее 96% кремнезема и иметь большие зерна. Это дефицитный материал, месторождения содержат обычно не более 20-30% пригодного песка. Ближайшее к Донбассу месторождением кварцевого песка является Просянский карьер (Днепропетровская обл.).
Раздроблен антрацит получают измельчением угля марок АП, АК, АС, материал не должен содержать зерна слоистой строения. Применяется редко, в основном для двухслойных фильтров.
Раздробленный керамзит получают из керамзитового гравия - искусственного строительного материала (применяется как утеплитель и легкий заполнитель бетонов). При дроблении керамзита получаются зерна с развитой поверхностью, внутренними и наружными порами. В начале эксплуатации материал подвергается повышенному истиранию, в дальнейшем процесс износа тормозится. Этот материал, есть во всех регионах, и может широко использоваться для фильтров.
Дробленые горелые породы - это измельченные горные породы шахтных отвалов, подвергшихся естественному обжигу при с угольными отходами в терриконах. Этот материал еще недостаточно опробован и не может применяться при подготовке качественной воды.
Гранулированный пенополистирол получают вспениванием гранул полистирола в кипящей воде. При этом получаются шаровые зерна с плотностью, меньшей, чем у воды. Этот материал применяют в специальных фильтрах с плавающей загрузкой.
Керамический песок - искусственный материал нового поколения. Получают сушкой и обжигом капель глинистой суспензии с добавками. Изменяя добавки (известняк, магнетит, торф, древесная мука, гидрофобизаторы, полимеры), можно получать материалы по заказу, с необходимыми свойствами. Технология получения керамического песка еще отрабатывается.
Местные материалы используются при дефиците традиционного кварцевого песка. В горных районах используют вулканические шлаки и туфы (цеолит), в промышленных регионах - отходы промышленности (шлаки), отсев каменных карьеров (гранодиорит), искусственные пористые материалы (аглопорит, вермикулит, шунгизит). Для новых материалов нужно проводить испытания механической прочности и химической устойчивости.
Физико-механические свойства основных фильтрующих материалов сведены в табл.7.1.
Таблица 7.1 - Физико-механические свойства основных фильтрующих материалов
Материал | Насып-ная объемная масса, кг/м3 | Плотность , г/см3 | Парува-тость % | Коэффициент формы | Потенциал протекания |, мВ| |
Кварцевый песок | 1400 | 2,6 | 34-47 | 1,2-1,5 | -41 |
Раздробленный антрацит | 700-900 | 1,7 | 52-58 | 1,5-2,5 | -17 |
Раздробленный керамзит | 400-600 | 1,6-2,1 | 60-74 | 3,2-4,4 | -30 |
Горелые породы | 1250 | 2,4 | 60 | 2,1 | -20 |
Вулканические шлаки | 900 | 2,0 | 55 | 2,7 | -13 |
Шунгизит | 650 | 2,2 | 65 | 2,1 | |
Гранодиорит | 1300 | 2,65 | 50 | 1,7 | |
Граншлак никелевый | 1650 | 3,2 | 48 | 1,75 | |
Пинополисты-ролл | 100-150 | 0,01-0,7 | 45 | ~1 |
Фильтрующий материал, помещенный в корпус фильтра, называется загрузкой, засыпкой, насадкой. В осветительных фильтрах, предназначенных для удаления из воды взвешенных веществ, используются инертные материалы, не вступающие в химические взаимодействия с фильтрованной водой. Активные материалы (ионообменные, сорбенты) рассмотрены далее в главах 11...13.
Дата добавления: 2018-11-24; просмотров: 300; Мы поможем в написании вашей работы! |
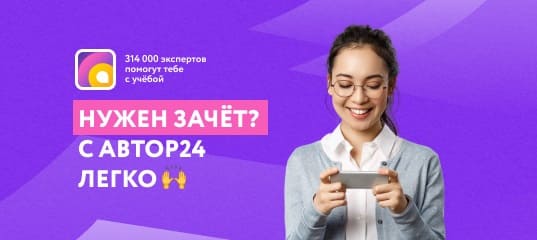
Мы поможем в написании ваших работ!