ТЕХНОЛОГИИ ИСПОЛЬЗОВАНИЯ ШАХТНЫХ ВОД 10 страница
Рис. 6.3. Принципиальная схема (сечение и план) радиального отстойника
Рис. 6.4. Схема тонкослойного канала
Для уменьшения глубины осаждения основной поток разбивают на ряд мелких потоков, отделенных друг от друга твердыми поверхностями: пластинами, стенками труб и так далее. Форма сечения ячеек, которые образуются, не имеет существенного значения для характера течения жидкости.
Конструктивно образуется тонкослойная камера, которую называют модулем или блоком. Наиболее распространены пластинчатые и трубчатые конструкции модулей. На практике диаметр трубок принимают 20-50 мм, а расстояние между параллельными пластинами 10-20 мм (иногда 50-100 мм, если очищаются суспензии с грубыми примесями; снижены требования к эффекту освещения и др.). Малый диаметр трубок, малое расстояние между пластинами обеспечивают не только малую высоту падения частицы в сравнении с условиями в обычном отстойнике (горизонтальном, вертикальном, радиальном), но и ламинарность движения жидкости.
Для изготовления модулей применяют различные материалы, из которых наиболее распространены синтетические полимерные пленки, имеющие малый коэффициент трения.
Благоприятные условия для седиментации взвесей в каждом канале модуля и малые размеры каналов к их быстрого заиливания (зашламирования), что грозит выходу из строя модуля. Для предотвращения этого явления необходимо удалять осадок из каналов. Последнее достигается самоочисткой каналов путем установки модулей в наклонном положении. Угол наклона должен быть большим, чем угол естественного откоса. Обычно он составляет 45-600. В таком положении преодолеваются силы сцепления осадка поверхностью пластины и под действием гравитационных сил он сползает вниз (в зону накопления осадка).
|
|
По соотношению направлений движения в канале воды и осадка модули классифицируют на три основных вида: прямоточные наклонные модули, в которых направление движения воды и осадка совпадают; противоточные - вода и осадок движутся навстречу друг другу; перекрестные - вода движется перпендикулярно движению осадка. Наиболее распространены отстойники с протиточными модулями.
За простоту конструкции модулей, их изготовление возможно не только в заводских условиях, но также силами шахтных мастерских.
Практический опыт работы тонкослойных отстойников показывает, что они работают непрерывно, устойчиво и не требуют значительных энерго - и трудозатрат. Благодаря этому эффективность осветления воды с помощью таких сооружений примерно в 2...5 раз выше, чем в обычных (горизонтальных и др.) и достигает в ряде случаев 80%. За счет малой глубины осаждения процесс осветления протекает в течение короткого времени (в среднем 10 мин), что увеличивает производительность отстаивания в 50-100 раз, позволяет уменьшить объем отстойных сооружений в 10-12 раз, значительно затраты на их строительство.
|
|
Таким образом, использование тонкослойных отстойников позволяют увеличить эффективность очистки сточных вод и повышает компактность очистных станций, что особенно важно при остром дефиците свободных площадей. Предварительные расчеты показывают, что капитальные затраты при этом в 2-3 раза ниже.
Перечисленные преимущества (в частности возможность использования тонкослойных модулей как уплотнителей) привели к использованию тонкослойных отстойников в стесненных условиях подземных горных выработок шахт.
С помощью тонкослойных модулей, устанавливаемых на выходе перед сборными лотками, достигается повышение эффективности работы обычных горизонтальных, вертикальных и радиальных отстойников.
2 Осветлители с взвешенным слоем осадка
Радиальные отстойники - это аппараты или сооружения, применяемые для усиления процесса осветления сточных (шахтных) вод. Действие осветлителей основано на контактной коагуляции, протекающей на поверхности хлопьев осадка.
|
|
Принцип работы осветлителей заключается в пропускании воды в направлении снизу вверх через слой шлама, что раньше образовался, с такой скоростью, при которой взвешенные вещества не уносятся из зоны взвешенного осадка (рис. 6.5.). При этом образуется взвешенный слой осадка (ОШ), который и очищает воду. Чрезмерный осадок отводится с поверхности ОШ непрерывно.
Конструкции осветлителей разнообразны и отличаются: по форме рабочей камеры; по наличию или отсутствию дырчатого днища под слоем взвешенного осадка; по способу удаления избыточного осадка; по конструкции и месту расположения осадоущільнювачів.
В практике очистки шахтных вод нашли применение трехсекционные осветлители коридорного типа с вертикальным осадоущільнювачем.
Угол между наклонными стенками нижней части рабочих камер принимают равным 60-700, а между наклонными стенками осадоущільнювача - 700.
Рис. 6.5. Принципиальная схема осветлителя с взвешенным слоем осадка
Воду с коагулянтом подают в нижнюю часть рабочих камер осветлителя. Хлопья коагулянта и захватываемые им частицы суспензии пи восходящим потоком воды до тех пор, пока скорость выпадения их не станет равной скорости восходящего потока (колеблется от 0,6 до 1,2 м/с). В результате образуется слой взвешенного осадка, через который дренирует вода. При этом наблюдается прилипания частиц взвеси к хлопьям коагулянта. Высота взвешенного (псевдозрідженого) слоя осадка составляет 1,8...2,5 м, а высота зоны осветления более 2 м. Постоянный уровень слоя осадка поддерживается за счет того, что его излишки постоянно стекают в осадоущільнювач через окно.
|
|
Удаление осадка происходит либо естественным образом (под действием разности плотностей осветленной воды и взвешенного слоя), или принудительно (отсосом вследствие разницы уровней отбора воды из рабочей камеры и уплотнителя).
3 Очистка шахтных вод в поле центробежных сил
Прогрессивным направлением осветления сточных вод, в том числе шахтных, является разделение суспензий в поле центробежных сил. В этом случае сепарация частиц твердой фазы происходит в потоке жидкости, что оборачивается. На частицы, удаляются, в центробежных устройствах действуют силы значительно больше (в сотни раз) за силы притяжения, действующие в отстойниках, а потому их эффективность и производительность во много раз выше.
Гидросепарация примесей с центробежным принципом осуществляется с помощью гидроциклонов и центрифуг. В гидроциклонах центробежные силы создаются вращением жидкости в неподвижном корпусе, а в центрифугах – самого корпуса (ротора). Для осветления сточных вод широко распространены гидроциклоны (напорные и ненапорные). Центрифуги в большей степени используются для обезвоживания осадков.
3.1 Напорные гидроциклоны (НГЦ)
К достоинствам напорных гидроциклонов перед обычными отстойниками относятся высокая удельная производительность, низкие капитальные и эксплуатационные расходы, достаточно высокий эффект осветления воды, возможность создания компактных автоматизированных установок с регулированием количественных и качественных показателей процесса. Схема НГЦ приведена на рис. 6.6.
Рис. 6.6.Схема напорного гидроциклона
Начальная сточная вода подается под давлением 0,05...0,3 МПа питающим патрубком по касательной (т. е. тангенциально) к цилиндрической части с тангенциальной скоростью 4...15 м/с и получает вместе с примесями вращательное движение с большой угловой скоростью. При этом образуются две характерные потоки жидкости: внешний и внутренний. Направления вращения потоков в гидроциклоне совпадают, а направления их поступательного движения противоположные. Внешний загрязненный поток движется у стенок цилиндрической и конической частей по винтовой спирали вниз к шламового патрубка. Под действием возникающей центробежной силы (где m - масса частицы; V - окружная скорость потока на входе в аппарат) твердые грубодисперсные примеси преодолевают сопротивление жидкости, отжимаются к цилиндрической поверхности гидроциклона, оседают на ней, опускаются вниз и выводятся (разгружаются) через песочный (шламовий) насадок вместе с некоторой частью воды в форме струи, который имеет вращательное движение. Осветленная часть жидкости возвращает (образуя внутренний поток) и движется вверх по оси гидроциклона к сливному насадку. Это обусловлено тем, что вблизи вершины конуса образуется воздушная пробка, давление в котором меньше атмосферного.
Одной из важных особенностей напорных гидроциклонов является сильная корреляция
производительности и эффективности разделения суспензий с основными конструктивными и технологическими параметрами аппаратов. К ним относятся скорость движения воды на входе, масса и плотность частиц, их концентрация на входе, физические свойства воды, конструктивные параметры (диаметры гидроциклона, насадок, впускных и сливных патрубков). Эффективность удаления грубодисперсных взвешенных веществ в гидроциклонах составляет в среднем 70-80%, достигая в отдельных случаях 95%.
В большинстве случаев напорные гидроциклоны работают без протиску со стороны сливного и шламового патрубков, т. е. давление на выходе из сливного и шламового патрубков соответствует атмосферному.
Основные размеры напорного гидроциклона подбираются по данным заводов-изготовителей. Размеры патрубков и насадок принимаются с учетом взаимных соотношений их диаметров, а также соотношение с диаметром циклона.
Напорные гидроциклоны разделяются на одиночные и батарейные. Разновидностью последних является мультигидроциклоны.
В зависимости от физико-механических и химических свойств обрабатываемых сточных вод гидроциклоны изготавливаются из нержавеющей стали, полиэтилена, полиуретана или чугуна. Для уменьшения абразивного износа внутренних поверхностей стальных гидроциклонов их футеруют в отдельных случаях каменным литьем, резиной, покрывают эмалью и др.
3.2 Открытые гидроциклоны (ВГЦ)
Они служат в отличие от напорных аппаратов для удаления примесей, как оседающих, так и всплывающих, гидравлическая крупность которых более 0,2 мм/сек. Эти устройства имеют большую производительность и меньший, чем напорные гидроциклоны, гидравлическое сопротивление. Диаметр их цилиндрической части составляет 2-6м, иногда 10 м, в то время к диаметр напорных гидроцилиндров обычно не превышает 0,7 м. Схема простого ВГЦ приведена на рис. 6.7.
Рис. 6.7. Схема открытого гидроциклона
3.3 Центрифуги (ЦФ)
В центрифугах в отличие от гидроциклонов поле центробежных сил создается за счет вращения корпуса аппарата (ротора). По принципу действия ЦФ разделяются на такие, которые фильтруют (для удаления грубодисперсных суспензий) и осветительные (удаляют тонкодисперсные суспензии, а ультрацентрифуги - даже микробы).
ЦФ применяют в технологиях очистки воды в основном для обработки осадков очистных сооружений.
Частота вращения ротора ЦФ достигает 1000...1500 оборотов в минуту, поэтому для них характерны высокие значения фактора разделения (до сотен тысяч единиц).
По конструкции различают два вида осветительных центрифуг: периодического и непрерывного действия.
В ЦФ периодического действия (рис. 6.8) порция очищаемой воды, ротор с вертикальной осью вращения, открытый сверху. При вращении ротора частицы примесей отбрасываются к стенкам и накапливаются на них, а очищенная вода (фугат) выбрасывается через горловину и перехватывается кожухом (на схеме не показан). Для выгрузки осадка, который накопился ротор периодически останавливается и опрокидывается.
Рис. 6.8. Центрифуга периодического действия
В ЦФ непрерывного действия (рис. 6.9) ротор вращается вокруг горизонтальной оси, на которой располагается частично полый неподвижный вал со спиральным шнеком. Отброшенные к стенкам ротора частицы лопастями шнека непрерывно подаются к отверстиям для выгрузки шлама, а фугат отводится через кольцевые зазоры в торцевой стенке ротора. В вода внутрь ротора попадает по полой части вала. Фугат и шлам перехватываются элементами кожуха, на схеме не показанным.
Рис. 6.9.Центрифуга непрерывного действия
4 Удаление примесей воды флотацией
4.1 Принцип действия флотации
Пенная флотация применяется для удаления из воды нерастворимых коллоидно - и грубодисперсных примесей (оптимальная крупность частиц составляет 10-3...10-1 см), а также (в отдельных случаях) истинно растворенных примесей и (попутно) снижение значений БПК, ХПК, удаление летучих компонентов. После удаления основной массы загрязнений флотацией нужна доочистка воды (фильтрованием и др.).
Удаление примесей методом флотации происходит в результате молекулярного прилипания (адсорбции) частиц в газовых (чаще воздушных) пузырьков, вводимых в жидкость или образующихся в последний, и флотируют (всплывают) в виде комплексов “частицы-пузырьки” под действием сил Архимеда на поверхность воды. При этом на поверхности образуется пенный слой с более высокой концентрацией примесей, чем в исходной жидкости, которую необходимо очищать.
Явление адсорбции обусловлено избытком свободной энергии поверхностных пограничных слоев раздела двух фаз и поверхностными явлениями смачивания.
К числу основных факторов, влияющих на процесс флотации относятся минералогический состав частиц (что определяют их гидрофобность или гидрофильность), гранулометрическая характеристика твердой фазы (размеры и плотность), состав воды, ее температура, плотность, реагентный режим, конструкция установки флотации и др.
Элементарным актом флотации является прилипание одной частицы в пузырьки газа. Прилипание (или неприлипания) зависит от “игры” трех сил: Ван-дер-ваальса (межмолекулярное притяжение); электростатического отталкивания при перекрытии двойных электрических слоев частиц, образующихся вокруг, в водном растворе; силы гидратации гидрофильных групп на поверхности частицы. Последние два вида сил расклинивающего давления. Наиболее уязвимой стадией элементарного акта, определяющего слипание, является преодоление расклинивающего давления в тонкой пленке (особенно с учетом краткости времени возможного контакта частицы и пузырьки газа, равного всего 0,001...0,002 с). Установлено, что преодоление расклинивающего давления и осуществления элементарного акта флотации возможно тогда, когда наблюдается несмачиваемость или плохое смачивание частицы жидкостью. Степень смачиваемости водой твердых частиц, взвешенных в воде, характеризуется величиной краевого угла смачивания. Чем больше угол , тем более гидрофобная поверхность частицы, т. е. увеличивается вероятность прилипания к ней и прочность удержания на ее поверхности воздушных пузырьков. Поэтому интенсификация процесса флотации достигается зачастую искусственно гидрофобизацией поверхности частиц с помощью флотореагентов, что именуются реагентами - собирателями, или коллекторами. Они избирательно сорбируются на частицах и ухудшают их смачиваемость.
При флотации используют также реагенты-пенообразователи и реагенты-регуляторы. Первые адсорбируются и концентрируются на поверхности раздела вода-воздух и способствуют сохранению воздушных пузырьков в диспергованому состоянии путем стабилизации пленки воды между пузырьками.
Реагенты-регуляторы повышают избирательность (селективность) флотации. В их присутствии реагент-собиратель гидрофобизирует в основном, те минералы, которые должны переходить в пену.
Как собиратели и пенообразователи используют органические вещества типа СПАР, а как регуляторы - различные неорганические вещества.
Увеличение температуры жидкости обычно повышает эффективность флотации. Большое значение при флотации имеют размер, количество и равномерность распределения воздушных пузырьков в обрабатываемой сточной воде. Оптимальные размеры воздушных пузырьков 15...30 мкм, а максимальные - 100...200 мкм.
Появление газовых (воздушных) пузырьков в обрабатываемой воде обеспечивается двумя путями: искусственным введением газа в водный раствор; возникновением в водном объеме в результате химических, биологических и других процессов, которые также стимулируются искусственно.
С учетом их особенностей различают два механизма прикрепления пузырька газа к поверхности частицы: соприкосновением (при искусственном введении газа) и возникновением пузырьков непосредственно на поверхности частицы (напорная флотация).
Возникновение пузырьков газа непосредственно на поверхности частицы вызывается десорбцией его молекул при понижении давления в жидкости и их объединением в пузырек под действием сил Ван-дер-ваальса. Пузырь во времени и его размер стабилизируется, когда лапласовый давление внутри пузырька сравняется с разностью начального и конечного внешнего давления.
Устойчивость пузыря (сохранится ли она закрепленной на частице, или оторвется, лопнет) зависит от двух причин: во-первых, от гидродинамической силы подъема Архимеда, во-вторых, от дополнительной силы отрыва.
В реальных условиях в жидкости возникают дополнительно различные силы, которые стремятся оторвать частицу от пузырька. Это силы инерции, тяжести и трения. Наибольшее значение имеют силы инерции, которые появляются из-за движения частиц по траекториям кривых.
4.2 Преимущества и недостатки метода флотации
Флотация является перспективным методом водоочистки, в частности шахтных вод. Это обусловлено его достоинствами, к которым относятся:
- высокий общий степень очистки (95...98%), высшее (в 1,5..2 раза) эффективность извлечения тонкодисперсных частиц нефтепродуктов СПАВ, микроорганизмов и микроэлементов;
- высокая скорость разделения твердой и жидкой фаз, которая в среднем составляет 2...3 мм/с (при отстаивании некоагулированных взвешенных веществ - 0,1...0,2 мм/с; скоагулированных взвешенных веществ - 0,3...0,6 мм/с; при осветлении в слое взвешенного осадка - 0,6...1,0 мм/с);
- небольшая продолжительность процесса очистки - 15...20 мин. (в тонкослойных отстойниках - 30...60 мин; в осветлителях - 90...120 мин);
- высокое гидравлическое нагрузка на флотатор - 4...8 м /ч (4...6 м /ч на тонкослойные отстойники; 2,5...3 м/ч на осветители);
- меньший объем флотатора по сравнению с тонкослойными отстойниками и осветителей (в 2 ...5 раз);
- меньший объем пенного продукта в сравнении с осадком при отстаивании и при осветлении в слое взвешенного осадка (в 2 ...4 раза);
- выше содержание твердой фазы в пенном продукте и меньше его влажность;
- меньший объем сооружений для обработки пенного продукта (в 2...4 раза);
- небольшие капитальные и эксплуатационные затраты и простота аппаратурного оформления;
- универсальность метода (флотация одновременно сопровождается аэрацией сточных вод, снижением концентрации ПАВ, микроорганизмов, нефтепродуктов, отдельных ионов и даже радиоактивных веществ);
- экономия производственных площадей, которые занимают очистные сооружения.
К недостаткам флотации относится отсутствие четких научных критериев оптимизации процесса флотации мелких (тонких) частиц, таких характерных для производственных сточных вод (в том числе шахтных).
4.3 Методы флотации
По способу насыщения (аэрации) жидкости различают следующие виды обработки флотацией производственных сточных вод:
1) флотация с выделением воздуха из раствора (вакуумные, напорные и эрлифтные установки флотации);
2) флотация с механическим диспергированием воздуха (импеллерные, безнапорные и пневматические установки флотации);
Дата добавления: 2018-11-24; просмотров: 382; Мы поможем в написании вашей работы! |
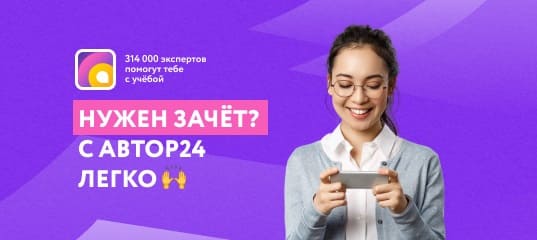
Мы поможем в написании ваших работ!