Портландцемент (страница 1 из 4)
Общие сведения
Портландцемент – гидравлическое вяжущее вещество, получаемое совместным тонким измельчением портландцементного клинкера, в составе которого преобладают силикаты кальция – 70…80%, с добавкой природного гипса (3…5%). По внешнему виду портландцемент представляет собой тонкодисперсный порошок темно-серого или зеленовато-серого цвета.
Портландцементный клинкер – это зернистый материал (размер гранул 10…40 мм), получаемый обжигом до спекания (при температуре до 1450°С) тщательно подобранной сырьевой смеси. Добавка гипса вводится для регулирования сроков схватывания портландцемента.
Изобретение портландцемента связано с именами английского каменщика Джозефа Аспдина, получившего 21.10.1824 г. патент на портландцемент, и русского строителя Егора Герасимовича Челиева, который изобрел цемент, наиболее схожий с современным портландцементом, и описал его в своей книге, изданной в 1825 г.
Название портландцемента происходит от англ. Portland – название полуострова на юге Великобритании, где добывалось сырье для производства портландцемента.
Сырьем для производства портландцемента служат:
известняки с высоким содержанием кальцита СаСО3 (мел, плотный известняк и др.);
глинистые породы (глины, глинистые сланцы), основной составляющей которых являются водные алюмосиликаты с общей формулой Al2O3·nSiO2·mH2O;
мергели – горные породы, представляющие собой природную смесь известняков и глин;
|
|
отходы промышленности, сходные по составу с природным сырьем (вскрышные породы, доменные шлаки, нефелиновый шлам, золы ТЭС и проч.);
корректирующие добавки, используемые для обеспечения требуемого химического состава сырьевой смеси (пиритные огарки, трепел, опока и др.).
Соотношение между карбонатной и глинистой составляющими сырьевой смеси 3:1 (75% известняка и 25% глины).
Производство портландцемента – технологически сложный и энергоемкий процесс, который можно разделить на две основные стадии: первая – производство клинкера, вторая – помол клинкера совместно с гипсом, а в ряде случаев и со специальными добавками.
Производство клинкера может осуществляться сухим, мокрым и комбинированным способом. Сухой способ заключается в приготовлении сырьевой муки (в виде порошка) из сухих или предварительно высушенных компонентов с остаточной влажностью 1…2%. Сухой способ в 1,5…2 раза менее энергоемок, чем мокрый. При мокром способе сырьевые материалы измельчаются и смешиваются в присутствии воды, поэтому смесь получается в виде вязкотекучей массы – шлама (от нем. schlamm – грязь) с влажностью 35…45%. Это наиболее энергоемкий способ. Комбинированный способ заключается в том, что приготовленный шлам до поступления в печь обезвоживается на фильтрах до влажности 16…18%. Энергоемкость производства в целом остается высокой, однако, данный способ позволяет на 20…30% снизить расход топлива по сравнению с мокрым способом.
|
|
Обжиг сырьевой смеси осуществляется во вращающихся печах, работающих по принципу противотока (сырье движется навстречу раскаленным продуктам сгорания топлива). Печь диаметром 5…7 м имеет небольшой наклон (3-5°) и вращается со скоростью 1–2 об/мин. При мокром способе производства длина печи достигает 185-230 м. Двигаясь от верхнего конца печи (холодного) к нижнему (горячему, со стороны которого подается топливо), сырье проходит различные температурные зоны, в каждой из которых происходят физико-химические превращения, в результате чего и получается цементный клинкер.
После испарения свободной воды, выгорания органических примесей и удаления химически связанной воды из глинистых минералов происходит декарбонизация углекислого кальция (900…1100°С) с образованием большого количества СаО и одновременно разложение дегидратированных глинистых минералов на оксиды Al2O3, SiO2, Fe2O3. Образовавшиеся оксиды вступают в химическое взаимодействие с образованием новых минералов 3СаО·Al2O3, СаО·Al2O3 и частично 2СаО·SiO2.
|
|
При температуре 1100…1250°С происходят твердофазовые реакции образования минералов 3СаО·Al2O3, 4СаО·Al2O3·Fe2O3 и 2СаО·SiO2. Наивысшего значения (1300–1450°С) температура обжига достигает в зоне спекания, где происходит частичное плавление сырья и образуется главный минерал клинкера – алит 3СаО·SiO2. В последней зоне печи клинкер охлаждается до 1000°С путем вдувания холодного воздуха, а при выходе из печи поступает в холодильник, где интенсивно охлаждается холодным воздухом.
Помол клинкера с добавкой гипса осуществляется в многокамерных шаровых мельницах при помощи загруженных в барабан мелющих тел – шаров (при грубом помоле) или цилиндров (при мелком помоле).
Химический составклинкера выражают содержанием оксидов в % по массе (таблица 6.6).
Таблица 6.6
Химический состав клинкера портландцемента
Оксид | Содержание, % | Оксид | Содержание, % |
СаО | 63…66 | Al2O3 | 4…8 |
SiO2 | 21…24 | Fe2O3 | 2…4 |
В небольших количествах в клинкере содержатся MgO, SO3, Na2O, K2O, TiO2, Cr2O3, P2O5 .
Содержание в клинкере MgО и свободного (не связанного в основные клинкерные минералы) СаО ограничивается, так как они могут стать причиной неравномерного изменения объема цемента при твердении. Свободного СаО в клинкере должно быть не более 1%, MgО – не более 5%.
|
|
Суммарное содержание щелочных оксидов (Na2O и К2О) не должно превышать 0,6%, так как они могут явиться причиной коррозии бетона и существенно замедлять схватывание портландцемента.
Минеральный состав клинкера:
Трехкальциевый силикат (алит) – 3СаО·SiO2 (С3S) – 45…60% – основной минерал клинкера, определяет скорость твердения, прочность и другие свойства портландцемента;
Двухкальциевый силикат (белит) – 2СаО·SiO2 (С2S) – 20…30% – медленно твердеет, но достигает высокой прочности при длительных сроках твердения;
Трехкальциевый алюминат 3СаО·Al2O3 (С3А) – 4…12% – быстро гидратируется и твердеет, но конечная прочность его небольшая; является причиной сульфатной коррозии цементного камня;
Четырехкальциевый алюмоферрит 4СаО·Al2O3·Fe2O3 (С4АF) – 10…20% – по скорости твердения занимает промежуточное положение между С3S и С2S.
Фазовый состав клинкера представлен кристаллической фазой в виде клинкерных минералов (85…95%) и аморфной фазой в виде клинкерного стекла (5…15%).
Вещественный состав портландцемента характеризуется процентным содержанием клинкера, гипса, видом и количеством вводимых добавок.
Введение в цемент при помоле минеральных и органических добавок позволяет направленно изменять свойства вяжущего, экономить клинкер, уменьшать расход цемента в бетоне. Добавки обладают разным механизмом действия: при твердении цемента могут вступать в химическое взаимодействие с продуктами гидратации цемента (активные минеральные добавки), влиять на пластичность бетонных и растворных смесей (добавки поверхностно-активных веществ), выступать в роли наполнителей, снижающих активность цемента и т.п.
Добавки–наполнители (тонкомолотые магматические горные породы, известняк, кварцевый песок, топливные шлаки и золы) вводятся для снижения активности вяжущего, способствуют снижению тепловыделения цемента при твердении.
Активные минеральные добавки (АМД) – природные (осадочного происхождения – диатомиты, трепелы, опоки, глиежи; вулканического происхождения – вулканический пепел, вулканический туф, пемза, трасс, витрофир) или искусственные (зола-унос, микрокремнезем, топливные шлаки) вещества, которые вводятся в цемент для связывания водорастворимого портландита – Ca(OH)2, являющегося одним из продуктов гидратации алита и белита, в малорастворимые соединения, повышая стойкость бетона к коррозии выщелачивания (вымыванию портландита из цементного камня), его водостойкость, сульфатостойкость и эксплуатационные свойства.
Твердение портландцемента происходит благодаря сложным физико-химическим процессам взаимодействия клинкерных минералов и гипса с водой. Сразу после затворения начинаются химические реакции. В результате физико-химических процессов на поверхности твёрдых частиц и в жидкой фазе формируются продукты гидратации в виде новообразований различной закристаллизованности. На их смачивание затрачивается вода, поэтому система постепенно теряет подвижность, загустевает, переходит в твёрдое состояние, наступает начало схватывания и дальнейшее твердение. Традиционно процессы твердения портландцемента принято описывать теорией Байкова А.А.
При взаимодействии с водой минералов – силикатов происходит одновременно их гидролиз (разложение водой) и гидратация (присоединение воды) с образованием гидросиликата и гидроксида кальция (портландита):
2(3СаО·SiO2) + 6H2O → 3СаО·2SiO2·3H2O + 3Са(ОН)2;
2(2СаО·SiO2) + 4H2O → 3СаО·2SiO2·3H2O + Са(ОН)2.
Гидросиликаты кальция – основной продукт твердения портландцемента – практически нерастворимы в воде. Они выделяются из раствора в виде геля, который со временем кристаллизуется. Этот гель пронизывают, укрепляя его, кристаллы Са(ОН)2. Содержание портландита в продуктах гидратации портландцемента может составлять до 15…20%. Другие продукты взаимодействия клинкера с водой также участвуют в формировании структуры цементного камня и влияют на его свойства.
Гидратация трехкальциевого алюмината протекает крайне быстро с образованием крупных кристаллов гидроалюмината кальция и приводит к утрате пластичности цементного теста:
3СаО·Al2O3 + 6H2O → 3СаО·Al2O3·6H2O.
Для замедления схватывания портландцемента при помоле клинкера добавляют 3…5% двуводного гипса. Гипс реагирует с трехкальциевым алюминатом и связывает его в практически нерастворимый гидросульфоалюминат кальция (эттрингит) в начале гидратации портландцемента:
3СаО·Al2O3+3(CaSO4·2H2O)+26H2O → 3СаО·Al2O3·3CaSO4·32 H2O.
Эттрингит выделяется в виде пленок на поверхности частиц С3А, затрудняет доступ к ним воды и, соответственно, замедляет их гидратацию и отодвигает начало схватывания цемента. Кроме того, роль добавки гипса состоит в улучшение свойств цементного камня (прочности, морозостойкости) за счет уплотнения структуры, связанного с увеличением объема эттрингита (в 2…2,5 раза больший объем по сравнению с объемом исходных реагирующих веществ) в еще не затвердевшей системе.
Четырехкальциевый алюмоферрит при взаимодействии с водой образует гидроалюминат и гидроферрит кальция:
4СаО·Al2O3·Fe2O3 + mH2O → 3СаО·Al2O3·6H2O + СаО·Fe2O3·nH2O.
Гидроалюминат связывается добавкой природного гипса, а гидроферрит входит в состав цементного геля.
Реакции гидратации клинкерных минералов экзотермические. По интенсивности тепловыделения минералы можно расположить в следующей последовательности: C3A > C3S > C4AF > C2S. Интенсивность тепловыделения портландцемента зависит от минерального состава и тонкости помола.
Тепловыделение играет положительную роль при бетонировании конструкций в зимних условиях, т.к. позволяет применять метод термоса (твердение бетона в утепленной опалубке), и отрицательную – при бетонировании в жаркую, сухую погоду, особенно при бетонировании массивных конструкций. Вследствие саморазогрева бетона возможно образование в конструкции усадочных трещин.
Выделяющийся при гидратации портландцемента портландит – Са(ОН)2 создает в твердеющем цементе щелочную среду (pH = 12…12,5), что предотвращает коррозию стальнойарматуры в бетоне (порог коррозии арматурной стали pH = 11,8). В то же время водорастворимый Са(ОН)2 является «слабым звеном» с точки зрения коррозии цементного камня в бетоне.
При затворении портландцемента избыток воды нежелателен. Цемент в состоянии химически связать строго определенное количество воды – максимально 25…30% массы цемента, фактически к возрасту 28 суток это значение составляет 15%. Лишняя вода образует в цементном камне капиллярные поры, что ведет к снижению его прочности. Поэтому в современной технологии бетона практически всегда используют пластификаторы – поверхностно-активные вещества, позволяющие при сохранении заданной подвижности бетонной смеси снизить её водопотребность на 25…40%.
Дата добавления: 2018-11-24; просмотров: 1188; Мы поможем в написании вашей работы! |
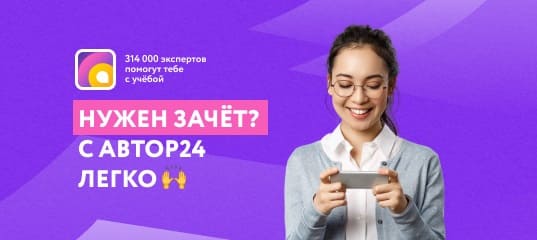
Мы поможем в написании ваших работ!