Особенности расчета конических колес
В конической передаче (рис. 4.2) оси валов обычно пересекаются под углом 900. В этом случае передаточное число равно [16, 17]:
u = n 1 / n 2 = z 2 / z 1 = tgδ 2 = ctgδ 1,
где δ1 и δ2 – половины углов при вершинах начальных конусов, δ 1 + δ 2 =900.
Максимальное передаточное число конической передачи равно 6,3., рекомендуемое – (2…3).
Для конических передач основным расчетным параметром является внешний делительный диаметр колеса de 2:
где ψ Re = b 2 / Re– коэффициент длины зуба, КП – коэффициент, учитывающий повышение нагрузочной способности косозубых передач по сравнению с прямозубыми.
Рекомендуется [16, 17] выбирать ψ Re =0,25-0,3, а также b 2 <0,3 Re и b 2 <10 me .
Для прямозубых колес КП = 1, для колес с наклонными и круговыми зубьями КП = 1,15-1,35. Поскольку как минимум шестерня в конической передаче расположена консольно, принимают KF = 1,5.
Расчетные значения внешнего делительного диаметра колеса должны округляться в большую сторону по ряду чисел [13]: 50, 63, 80, 100, 125, 160, 200, 250, 280, 315, 355, 400, 450, 500, 560, 630, 710, 800, 900, 1000, 1250, 1400, 1600.
Для обеспечения выполнения геометрических и технологических условий изготовления конических передач количество зубьев шестерни вычисляется по следующей формуле [8], которая носит рекомендательный характер:
.
В случае прямозубых конических передач полученная расчетом величина z1 не должна быть меньше 20. В противном случае принимают z1 = 20.
Расчеты конических передач проводятся по размерам, связанным с большими основаниями конусов.
|
|
Основными параметрами конической передачи являются: внешние делительные диаметры de 1 и de 2, внешний окружной модуль me , длина образующей делительного конуса Re (внешнее конусное расстояние).
de1 = me z1, de2 = = me z2
Re1
![]() |
de1 δ1
![]() | |||
![]() | |||
δ2 b
![]() |
da1
![]() | ![]() |
d2
![]() |
da2
Рис. 4.2 Элементы конической передачи
Диаметры окружностей конусов вершин зубьев:
da 1 = de 1 + 2 meCos δ 1
da 2 = de 2 + 2 meCos δ 2
Диаметры окружностей конусов впадин:
df1 = de1 – 2,5meCos δ1
df2 = de2 – 2,5meCos δ2
Средние делительные диаметры:
d 1 = 2( Re -0,5 b ) Sin δ 1
d2 = 2(Re-0,5b)Sin δ2
Модуль в среднем сечении (средний окружной модуль) равен: m = d 1 / z 1 = d 2 / z 2
Проверка контактной прочности зубьев конических колес проводится по соотношению [16, 17]:
Напряжения изгиба в зубьях конических косозубых колес должны удовлетворять условию [8]:
|
|
В этом выражении у – коэффициент формы зуба конического колеса, определяемый по приведенному значению числа зубьев, которое определяется из выражений [8]:
При прямых зубьях znp 1 = z 1 / Cosδ 1 и znp 2 = z 2 / Cosδ 2
При наклонных и круговых зубьях znp 1 = z 1 / Cosδ 1 Cos 3 β и znp 2 = z 2 / Cosδ 2 Cos 3 β.
По найденному значению znp находят по табл. 4.10 величину y .
Таблица 4.10 Коэффициент формы зуба у [8]
z , znp | 22 | 24 | 26 | 28 | 30 | 33 | 36 | 39 | 42 | 45 | 50 | 65 | 80 | 100 | 300 |
у | 0,384 | 0,395 | 0,404 | 0,412 | 0,417 | 0,426 | 0,435 | 0,442 | 0,446 | 0,452 | 0,458 | 0,471 | 0,48 | 0,482 | 0,496 |
Таблица 4.11 Ширина зубчатых венцов конических колес b 2 [8]
de2 мм | Ширина зубчатого венца b 2 в зависимости от передаточного числа u | |||||||||||||
1,4 | 1,6 | 1,8 | 2,0 | 2,24 | 2,5 | 2,8 | 3,15 | 3,55 | 4,0 | 4,5 | 5,0 | 5,6 | 6,3 | |
1 | 2 | 3 | 4 | 5 | 6 | 7 | 8 | 9 | 10 | 11 | 12 | 13 | 14 | 15 |
50 | 9 | 8,5 | - | - | - | - | - | - | - | - | - | - | - | - |
56 | 10 | 9,5 | - | - | - | - | - | - | - | - | - | - | - | - |
63 | 11 | 10,5 | 10 | 10 | - | - | - | - | - | - | - | - | - | - |
71 | 12 | 12 | 11,5 | 11,5 | - | - | - | - | - | - | - | - | - | - |
80 | 14 | 13 | 13 | 13 | 12 | 12 | - | - | - | - | - | - | - | - |
1 | 2 | 3 | 4 | 5 | 6 | 7 | 8 | 9 | 10 | 11 | 12 | 13 | 14 | 15 |
90 | 16 | 15 | 15 | 14 | 14 | 14 | - | - | - | - | - | - | - | - |
100 | 18 | 17 | 16 | 16 | 16 | 15 | 15 | 15 | - | - | - | - | - | - |
112 | 20 | 19 | 18 | 18 | 17 | 17 | 17 | 17 | - | - | - | - | - | - |
125 | 22 | 21 | 20 | 20 | 19 | 19 | 19 | 19 | 19 | 18 | - | - | - | - |
140 | 24 | 24 | 22 | 22 | 22 | 21 | 21 | 21 | 21 | 21 | 20 | - | - | - |
160 | 28 | 28 | 26 | 25 | 25 | 25 | 24 | 24 | 24 | 24 | 24 | 24 | 24 | 24 |
180 | 32 | 30 | 30 | 28 | 28 | 28 | 28 | 26 | 26 | 26 | 26 | 26 | 26 | 26 |
200 | 34 | 34 | 32 | 32 | 32 | 30 | 30 | 30 | 30 | 30 | 30 | 30 | 28 | 28 |
225 | 40 | 38 | 36 | 36 | 36 | 34 | 34 | 34 | 34 | 32 | 32 | 32 | 32 | 32 |
250 | 45 | 42 | 40 | 40 | 40 | 38 | 38 | 38 | 38 | 36 | 36 | 36 | 36 | 36 |
280 | 50 | 48 | 45 | 45 | 45 | 42 | 42 | 42 | 42 | 42 | 40 | 40 | 40 | 40 |
315 | 55 | 52 | 52 | 50 | 50 | 48 | 48 | 48 | 48 | 45 | 45 | 45 | 45 | 45 |
355 | 63 | 60 | 60 | 55 | 55 | 55 | 55 | 55 | 52 | 52 | 52 | 52 | 52 | 52 |
400 | 70 | 70 | 65 | 63 | 63 | 60 | 60 | 60 | 60 | 60 | 60 | 60 | 60 | 60 |
450 | 80 | 75 | 75 | 70 | 70 | 70 | 70 | 65 | 65 | 65 | 65 | 65 | 65 | 65 |
500 | 90 | 85 | 80 | 80 | 80 | 75 | 75 | 75 | 75 | 75 | 75 | 75 | 70 | 70 |
|
|
Особенности расчета червячной передачи
Червячные или зубчато-винтовые передачи применяют для вращения валов со скрещивающимися осями. Движение осуществляется по типу винтовой передачи, когда винтом служит червяк, а колесо представляет собой гайку, изогнутую по окружности резьбой наружу.
|
|
Некоторые важные для расчетов и функционирования элементы червяка показаны на рис. 4.3.
Исходными данными для расчета червячной передачи являются: крутящий момент на выходе передачи (на валу червячного колеса) Т2, частота вращения выходного вала n 2, передаточное число u ред.
Время безотказной работы передачи обычно принимают равным t = 30000 часов, температуру окружающей среды to = 20°С.
р α=20о
![]() |
df 1 d 1 da 1
![]() | ![]() | ||
V 2 Виток червяка
Зуб колеса γ
V 1 VS
b1
Рис. 4.3 Цилиндрический архимедов червяк
Материал червячного колеса:
1) Венец – оловянистая (при больших скоростях скольжения), безоловянная бронза или латунь (при скорости скольжения VCK < 8 м/с) и чугун СЧ12-28, СЧ15-32 (при скорости скольжения VCK < 2 м/с);
2) Ступица и диск - СЧ12-28, СЧ15-32 или сталь 45.
Если червячное колесо имеет небольшие габаритные размеры, то оно целиком выполняется из бронзы.
Материал червяка: углеродистые или легированные термообработанные стали 45, 50, 12ХН3А, 20, 40Х, 40ХН, 38ХМЮА. При работе с венцом из безоловянной бронзы зубья червяка должны иметь твердость не ниже HRC 45.
В качестве параметров исходного контура инструмента можно принять:
h*а = 1 – коэффициент высоты головки зуба;
c* = 0,2 – коэффициент радиального зазора;
α = 20°– угол профиля рейки.
При проверке червячных передач на статическую прочность при пиковых нагрузках предельные допускаемые напряжения принимают из следующих условий.
Таблица 4.12 Предельные допускаемые напряжения в червячной передаче [8]
Материал | [σ]Н пред | [σ]И пред |
Оловянные бронзы | 4 σТ | - |
Безоловянные бронзы | 2 σТ | 0,8 σТ |
Чугуны | 260-300 Н/мм2 | 0,6 σпч.р |
Пределы текучести и прочности бронз должны выбираться соответственно принятой марке материала по справочникам. Однако, для решения задач учебного проектирования можно принять следующие средние значения:
Для оловянистых бронз σТ = 150-160 Н/мм2; σв = 240-250 Н/мм2
Для безоловянных бронз σТ = 260-300 Н/мм2 ; σв = 560-580 Н/мм2
Дата добавления: 2018-11-24; просмотров: 312; Мы поможем в написании вашей работы! |
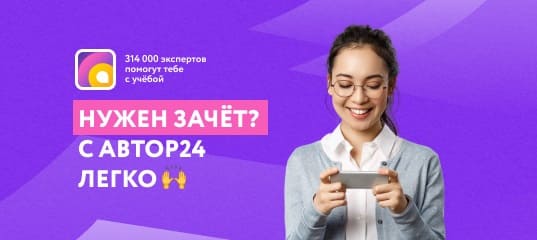
Мы поможем в написании ваших работ!