Общие сведения о термической обработке.
Термическая обработка заключается в нагреве детали до определенных температур, выдержке при этой температуре и охлаждении с той или иной скоростью. При этом происходит изменение структуры, а следовательно, механических и технологических свойств обрабатываемой детали.
При нагревании и охлаждении в железоуглеродистых сплавах происходят превращения при определенных температурах, называемых критическими точками. При нагревании их принято условно обозначать А1 Аз, Аст (рис. 1). Превращения в сталях при нагревании носят кристаллизационный характер, т. е. при этом происходит образование центров зародышей и последовательный их рост. Исходная структура всех сталей представляет собой смесь двух фаз — феррита и цементита.
При медленном нагревании до температуры A0 (723°C) никаких превращений в стали не происходит. При достижении критической точки А з перлит переходит в аустенит. При дальнейшем нагреве в доэвтектоидных сталях происходит постепенное растворение феррита в аустените. При температуре выше линии GSE стали будут иметь однородную структуру — аустенит.
При медленном охлаждении эвтектоидной стали, аустенит превращается в перлит (смесь феррита и цементита). Превращение аустенита в перлит происходит диффузионно; углерод, выделяясь из аустенита, образует зародыши цементитовых включений, число которых и последовательный рост зависят от степени переохлаждения.
|
|
Регулируя степень охлаждения аустенита, можно получить следующие продукты его распада: перлит — крупнозерную смесь феррита и цементита; троостит — мелкозерную (высокодисперсную) смесь феррита и цементита.
Рис. 1. Оптимальный интервал закалочных температур стали
При больших степенях переохлаждения аустенита диффузионное перераспределение углерода практически прекращается, и образование цементита становится невозможным. Образуется структура мартенсит — перенасыщенный твердый раствор углерода в Feά.
Наименьшая скорость охлаждения, при которой аустенит превращается в мартенсит, называется критической скоростью закалки. Мартенсит имеет игольчатое строение и высокую твердость (НВ 500— 650). Мартенситное превращение происходит в интервале температур Мн — Мк (где Мн — начало мартенситных превращений; Мк — конец мартенситных превращений), которые определяются содержанием углерода в стали.
Виды термической обработки стали:
1) отжиг первого рода или рекристаллизация;
2) отжиг второго рода;
3) нормализация;
4) закалка;
5) отпуск.
Отжиг первого рода (рекристаллизационный отжиг) — нагрев детали до температуры ниже фазовых превращений, выдержка при этой температуре и медленное охлаждение. Такой вид отжига применяют для снятия внутренних напряжений у деталей, полученных методом холодной деформации (холодная прокатка, холодная штамповка, волочение и др.)» а также для уничтожения нагартовки (наклепа) металла.
|
|
Температура рекристаллизационного отжига любого металла должна быть выше температуры рекристаллизации данного металла. Температура рекристаллизационного отжига для разных металлов и сплавов различная. Например, для стали температура рекристаллизационного отжига на 150—250° С выше температуры рекристаллизации, обычно 680—700° С.
Рекристаллизация заключается в том, что, начиная с некоторой температуры при нагревании, происходит интенсивное перемещение атомов в металле, что влечет за собой изменение формы и величины деформированных кристаллических зерен. При этом происходят превращения, подобные происходящим при первичной кристаллизации и вторичной перекристаллизации (зарождаются новые центры кристаллов и одновременно происходит их рост). Взамен вытянутых расплющенных зерен образуются мелкие, сфероидальные зерна; металлу возвращаются исходные свойства, т. е. понижается твердость, повышается пластичность.
|
|
Отжиг второго рода (отжиг с фазовыми превращениями) — нагрев детали до температуры несколько выше критической, выдержка при этой температуре и медленное охлаждение вместе с печью.
Цель отжига — выровнять химический состав детали, получить мелкозернистую равновесную структуру, снять внутренние напряжения, повысить пластичность и понизить твердость, улучшить условия обрабатываемости резанием. Отжиг второго рода подразделяется на полный, неполный, изотермический ступенчатый и диффузионный.
Полный отжиг производят путем нагрева стали на 30—50°С, выше критической температуры А3, выдержки при этой температуре и медленном охлаждении. Полному отжигу подвергают и горячедеформируемые стали (поковки, штамповки, прокат, а также слитки и фасонные отливки из углеродистой и легированной стали).
Неполный отжиг производят, нагревая детали до температуры выше критической точки Ac на 30—50°С, выдержки при этой температуре и последующего медленного охлаждения. Неполный отжиг необходим для перекристаллизации перлита, снятия внутренних напряжений, улучшения обрабатываемости резанием. Применяется для заэвтектоидных сталей.
Нормализация — промежуточный процесс термической обработки между отжигом и закалкой. В зависимости от химического состава стали нормализацию применяют иногда вместо отжига или закалки. Нормализация отличается от отжига повышенной скоростью охлаждения (на стойком или движущемся воздухе). Процесс нормализации заключается в нагреве стали выше критических температур Аз, Аст на 30—50°С, выдержке при этой температуре и охлаждении на воздухе. Нормализацией достигают измельчения и однородности структуры, устранения внутренних напряжений и уничтожения сетки вторичного цементита в заэвтектоидных сталях. Нормализации подвергают фасонные отливки, поковки, штамповки и прокатные материалы.
|
|
Закалка — это процесс, который заключается в нагреве стали выше критических температур А3, Ac на 30—50°С, выдержке при этой температуре и последующем быстром охлаждении в воде, масле или других охлаждающих средах.
Основная цель закалки — получение высокой твердости и прочности.
Резкое увеличение твердости и прочности в процессе закалки происходит за счет изменения структуры в процессе нагрева и охлаждения, за счет образования неравновесных твердых структур — мартенсита, троостита и сорбита.
Температура нагрева под закалку зависит от химического состава стали. Доэвтектоидную углеродистую сталь нагревают выше критической температуры А3 на 30—50°С, а заэвтектоидную и эвтектоидную стали нагревают выше Ac на 30—50°С. Температура под закалку доэвтектоидной стали изменяется с изменением содержания в стали углерода, температура нагрева заэвтектоидных сталей постоянная и равна 770—780°С.
Нагрев деталей должен быть медленным, чтобы не возникали напряжения и трещины. Время нагрева зависит от химического состава стали, от формы и размеров детали. Время выдержки должно быть достаточным, чтобы весь процесс превращения феррито-цементной смеси в аустенит полностью завершился. Продолжительность выдержки обычно 25% общего времени нагрева. Скорость охлаждения должна быть такой, чтобы обеспечить получение нужной структуры — мартенсита, троостита или сорбита, т. е. обеспечить необходимые механические свойства обрабатываемой детали.
Для успешного проведения термической обработки правильный выбор закалочной среды имеет большое значение. Закалку среднеуглеродистых сталей производят в воде при температуре 18°С, а большинства остальных сталей — в масле. Объемная закалка в зависимости от способа охлаждения разделяется на следующие виды.
Закалка в одном охладителе углеродистых сталей (охлаждение в воде) и легированных сталей (охлаждение в масле) заключается в том, что нагретую до температуры закалки деталь погружают в закалочную среду и держат до ее полного охлаждения. Недостаток этого способа — возникновение больших термических напряжений из-за резкой разности температур нагретого металла и охлаждающей среды.
Ступенчатую закалку производят быстрым охлаждением последовательно в двух различных охлаждающих средах. Первой охлаждающей средой служат расплавленные соли или масло с температурой на 20—30°С выше точки начала мартенситного превращения М для данной стали. В горячей среде деталям дают кратковременную выдержку, цель которой — выравнивание температур по сечению детали. Структура металла — аустенит. Второй охлаждающей средой является воздух; при этом аустенит переходит в мартенсит.
Достоинство такого метода закалки — уменьшение термических напряжений, а следовательно, невозможность появления трещин, поводки и коробления, а также хорошее сочетание высокой вязкости с прочностью. Ступенчатую закалку применяют для мелких деталей из углеродистой стали с сечением 8—10 мм и для деталей из легированной стали с сечением до 30 мм.
Изотермическая закалка, так же как и ступенчатая закалка, производится в двух охлаждающих средах. Температура горячей среды (соляные, селитровые и щелочные ванны) зависит от химического состава стали. Время выдержки должно быть достаточным для полного превращения аустенита в игольчатый троостит. Окончательное охлаждение до комнатной температуры производится на воздухе.
Изотермическую закалку широко применяют для деталей из высоколегированных сталей. После изотермической закалки сталь приобретает высокие прочностные свойства.
При охлаждении в процессе закалки в стали возникают термические и структурные внутренние напряжения. Термические напряжения возникают в результате неравномерного охлаждения, а структурные - при превращении аустенита в мартенсит, что сопровождается значительным увеличением объема. В результате создания таких напряжений при закалке может возникнуть брак — коробление, трещины и изменение объема.
Поверхностная закалка применяется для придания ответственным деталям (валам, зубчатым колесам и др.), работающим на трение и одновременно подвергающимся действию ударных нагрузок, твердости поверхностного слоя, высокого сопротивления изнашиванию и вязкости сердцевины, обеспечивающей сопротивление удару. В зависимости от способа нагрева деталей поверхностная закалка разделяется на индукционную (токами высокой частоты), контактную, газопламенную, закалку в электролите.
Индукционная закалка основана на том, что электрический ток высокой частоты, проходя по проводнику — индуктору, создает вокруг него электрическое поле. На поверхности детали, помещенной в этом поле, индуцируются вихревые токи, вызывая нагрев детали до высоких температур. Это обеспечивает возможность протекания фазовых превращений, т. е. превращение ферритоцементитной смеси в аустенит. После охлаждения поверхность детали имеет структуру мартенсита.
Отпуск — это завершающая операция термической обработки, формирующая структуру, а, следовательно, и свойства стали. Назначение отпуска — снять внутренние напряжения, возникшие в процессе закалки, и получить необходимую структуру. Процесс отпуска заключается в нагревании стали до температуры ниже Аз выдержке при температуре и охлаждении. В зависимости от температуры нагрева закаленной детали различают три вида отпуска: низкий, средний и высокий.
Низкий отпуск производится при температуре 150—250°С с целью уменьшения закалочных напряжений при сохранении мартенситной структуры. Твердость детали после низкого отпуска почти не изменяется. Низкий отпуск применяется для углеродистых сталей, для которых необходимы высокая твердость и износоустойчивость.
Средний отпуск производится при температурах нагрева 350—500°С и применяется для пружинных и рессорных сталей, а также для сталей, идущих на изготовление штампов.
Рис. 2. Диаграмма влияния температуры отпуска на механические свойства стали
Высокий отпуск производится при температурах нагрева 500—650°С и применяется для конструкционных сталей.
Кроме температуры нагрева при отпуске весьма важно время выдержки, скорость же охлаждения в большинстве случаев значения не имеет (рис. 2).
Нагрев образцов стали для термообработки в лабораторных условиях проводят в муфельных электропечах (рис. 3), которые состоят из металлического корпуса, внутри которого выложен муфель 2 из четырех плит с вмонтированными в них нагревательными спиралями 3. Рабочая камера закрывается дверцей 4. Регулирование температуры в печи осуществляется реостатом с помощью ручки 5. Для измерения температуры применяют термоэлектрические пирометры, термопары, которые вставляют в отверстия печи, имеющиеся в задней стенке. Печь до начала работы хорошо прогревают, для чего ее выдерживают до трех часов при температуре 700°С.
Рис. 3. Муфельная печь.
РЕШЕНИЕ ПРАКТИЧЕСКИХ ЗАДАЧ.
Практическое применение работы предусматривает обосновать выбор металла для изготовления заданной детали и выбор вида и режима термической и химико-термической обработки, которая обеспечит надежность детали в условиях эксплуатации, указанных в каждой задаче.
Для решения задач необходимо, прежде всего, определить материал, обладающий свойствами, близкими к требуемым. Для этой цели рекомендуется ознакомиться с классификацией, составам и назначением основных материалов, используемых в технике.
Если для улучшения свойств выбранного материала нужны термическая или химико-термическая обработка, то необходимо указать их режимы, получаемую структуру и свойства. При рекомендации режимов обработки необходимо также указать наиболее экономичные и производительные способы. Например, для деталей, изготовляемых в больших количествах, — обработку с индукционным нагревом, газовую цементацию и др.; для деталей, работающих в условиях переменных нагрузок, например для валов, зубчатых колес многих типов, необходимо рекомендовать обработку, повышающую предел выносливости (в зависимости от рекомендуемой стали к ним относятся цементация, цианирование, азотирование, закалка с индукционным нагревом, обработка дробью).
При решении задач рекомендуется использовать учебные пособия, ГОСТы, справочники.
В помощь студентам при выполнении практического занятия приведено подробное решение одной типовой задачи.
Примерные задачи по выбору сплавов и режимов термической обработки в зависимости от условий работы деталей и конструкций:
1. Завод изготовляет коленчатые валы диаметром 35 мм; сталь в готовом изделии должна иметь предел прочности не ниже 750 МПа и ударную вязкость не ниже 50 МПа. Кроме того, вал должен обладать повышенной износостойкостью не по всей поверхности, а только в
шейках, т. е. в участках, сопряженных с подшипниками и работающих на истирание.
Подберите марку стали, рекомендуйте режим термической обработки всего вала для получения заданных свойств и режим последующей термической обработки, повышающей твердость только в отдельных участках поверхности вала.
Приведите структуру и твердость стали в поверхностном слое шейки вала и структуру и механические свойства в остальных участках.
2. Стаканы цилиндров мощных двигателей внутреннего сгорания должны обладать высоким сопротивлением износу на поверхности. Для повышения износостойкости применяют азотирование.
Подберите сталь, пригодную для азотирования, приведите химический состав, рекомендуйте режим термической обработки и режим азотирования. Укажите твердость поверхностного слоя и механические свойства низлежащих слоев в готовом изделии.
3. Станкостроительный завод изготовляет шпиндели токарных станков. Шпиндели работают с большой скоростью в условиях повышенного износа, поэтому твердость в поверхностном слое должна быть HRC 58—62.
Подберите сталь для изготовления шпинделя, рекомендуйте режим термообработки, обеспечивающий получение заданной твердости в поверхностном слое. Укажите структуру стали в поверхностных слоях и в сердцевине шпинделя, механические свойства сердцевины после окончательной термической обработки.
4. Червяк редукторов диаметром 35 мм можно изготовить из цементируемой и нецементируемой стали. Предел прочности в сердцевине -детали должен быть 580—686 МПа.
Выберите марку цементируемой и нецементируемой углеродистой качественной стали. Обоснуйте, в каких случаях целесообразно применять цементируемую и в каких случаях — нецементируемую сталь.
Укажите химический состав, рекомендуемый режим химико-термической и термической обработки и сопоставьте механические свойства стали обоих типов в готовом изделии.
5. Палец шарнира диаметром 30 мм работает на изгиб и срез и должен обладать высокой износостойкостью на поверхности и высокой вязкостью в сердцевине.
Подберите углеродистую сталь, укажите ее состав и марку, рекомендуйте режим химико-термической и термической обработки, укажите структуру, механические свойства в сердцевине и твердость на поверхности после окончательной обработки. Укажите желаемую толщину твердого поверхностного слоя.
6. Выберите марку стали для изготовления топоров. Лезвие топора не должно сминаться или выкрашиваться в процессе работы; поэтому оно должно иметь твердость в пределах HRC 50—55 на высоту не более 30—40 мм; остальная часть топора не подвергается закалке и
имеет более низкую твердость.
Укажите химический состав стали, режим термической обработки, обеспечивающий указанную твердость, а также способ закалки, позволяющий получить эту твердость только на лезвии топора.
7. Выберите марку стали для изготовления продольных пил по дереву и укажите режим термической обработки, микроструктуру и твердость готовой пилы.
Режимы термической обработки выберите таким образом, чтобы предупредить деформацию пилы при закалке и отпуске, а также обеспечить получение в стали высоких упругих свойств после отпуска (пила должна «пружинить»).
8. Автосцепки вагонов на железнодорожном транспорте изготавливаются литыми. Для повышения механических свойств отливки подвергают термической обработке.
Выберите марку стали и обоснуйте термическую обработку, если предел прочности должен быть не ниже 343 МПа.
Укажите структуру и механические свойства стали после литья и после термической обработки.
9. Завод изготовляет зубчатые колеса диаметром 60 мм и высотой
80 мм. Предел текучести должен быть не ниже 530—540 МПа.
Выберите сталь для изготовления зубчатых колес и приведите состав и марку, учитывая технологические особенности термической обработки и необходимость предотвратить деформацию и образование трещин при закалке.
Рекомендуйте режим термической обработки и укажите механические свойства в готовом состоянии.
10.Многие измерительные инструменты плоской формы (шаблоны, линейки, штангенциркули) изготовляют из листовой стали; они должны обладать высокой износостойкостью в рабочих кромках. Приведите режимы обработки, обеспечивающей получение этих свойств, если инструменты изготовляют большими партиями из сталей 15 и 20.
ОБРАЗЕЦ РЕШЕНИЯ:
Задача. Завод имеет сталь двух марок: 45 и 20ХНЗА, из которых можно изготовить вал диаметром 70 мм для работы с большими нагрузками.
Какую из сталей следует применить для изготовления вала, если сталь должна иметь предел текучести не ниже 740 МПа?
Сталь 45 согласно ГОСТу в состоянии поставки (после прокатки и отжига) имеет твердость не более НВ 207. При твердости НВ 190—200 сталь имеет предел прочности не выше 588—608 МПа. Предел текучести стали 45 не превышает 265—314 МПа.
Сталь 20ХНЗА согласно ГОСТу в состоянии поставки (после прокатки и отжига) имеет твердость не более НВ 250. Предел прочности не превышает 735 МПа и может быть ниже 588 МПа для плавок с более низкой твердостью. Предел текучести стали не превышает 343— 392 МПа.
Таким образом, для получения заданного предела текучести вал необходимо подвергнуть термической обработке.
Для такого ответственного изделия, как вал двигателя, поломки которого нарушают работу машины, необходимо применить сталь качественную. Сталь 45 относится к классу качественной углеродистой, а сталь 20ХНЗА — к классу высококачественной легированной. Они содержат соответственно 0,42—0,50 и 0,17—0,23% углерода и принимают закалку. Для повышения прочности можно принимать нормализацию или закалку с высоким отпуском.
Так как вал двигателя воспринимает в работе динамические нагрузки, а также вибрацию, более целесообразно применить закалку и отпуск.
После закалки в воде углеродистая сталь 45 получает структуру мартенсита. Однако вследствие небольшой прокаливаемости углеродистой стали эта структура в изделиях диаметром более 20—25 мм образуется только в сравнительно тонком поверхностном слое толщиной 2—4 мм. Последующий отпуск вызовет превращение мартенсита и троостита в сорбит только в поверхностном слое, но не влияет на структуру и свойства перлита и феррита в основной массе изделия. Сорбит отпуска обладает более высокими механическими свойствами, чем феррит и перлит.
Наибольшие напряжения от изгиба, кручения и повторно переменных нагрузок воспринимают наружные слои. Однако в сопротивлении динамическим нагрузкам, которые воспринимает вал, участвуют не только поверхностные, но и нижележащие слои металла.
Сталь 20ХНЗА легирована никелем и хромом для повышения прокаливаемости и закаливаемости. Она получает после закалки однородную структуру и механические свойства в сечении диаметром до 75 мм.
Таким образом, свойствами, которые обеспечат требования для изготовления вала диаметром 70 мм для работы с большими нагрузками, обладает сталь 20ХНЗА, которую необходимо применить для изготовления валов с соответствующей термодинамической обработкой (закалка с 820—835°С в масле и отпуск 520—530°С в масле).
Порядок выполнения работы
1. Ознакомившись с целью работы, заданием и внимательно изучив теоретические основы различных видов термической обработки, к работе приступают в такой последовательности.
2. Получив четыре образца стали, назначить для них режим обработки по диаграмме железо—цементит (сверив с данными по табл. 4, 5, 6): температуру нагрева, время выдержки и охлаждающую среду.
3. Измерить твердость образца на твердомерах ТШ или ТК.
4. Провести нагрев, выдержку и охлаждение в соответствии с назначенными режимами для нормализации, закалки и отпуска.
5. Измерить твердость образцов после их термической обработки.
6. Все данные занести в соответствующий протокол.
В отчете должны быть отражены:
Ø цель работы,
Ø задание,
Ø последовательность выполнения закалки и отпуска,
Ø характеристика изменения твердости исследуемых образцов.
ОТЧЕТ
По лабораторной работе № 3.
Тема: ПРОВЕДЕНИЕ ЗАКАЛКИ И ОТПУСКА УГЛЕРОДИСТЫХ СТАЛЕЙ
Цель работы: изучить влияние термической обработки на механические свойства сталей. Приобрести навыки проведения операций термической обработки: нормализации, закалки и отпуска углеродистых сталей.
Задание: 1) ознакомиться с устройством печи и прибором для измерения температуры;
2) измерить твердость на образцах конструкционной и инструментальной стали; 3) назначить режимы обработки, нормализации, закалки и отпуска;
4) произвести закалку и отпуск различных марок углеродистой стали;
5) охарактеризовать структуры, полученные в образцах после каждого вида термической обработки, с указанием их на диаграмме сплавов железо—цементит.
6) измерить твердость после термической обработки.
7) установить влияние термической обработки на механические свойства сталей.
Оборудование и материалы: электропечи для нагрева; образцы углеродистой стали марок 35, 45, 50, 60, У8, У12; приборы для измерения твердости — твердомеры типа ТШ и ТК; полировально-шлифовальная установка; реактивы для травления и паста ГОИ; клещи.
Литература:
Основные источники:
1. Черепахин А.А. Материаловедение, 8-е издание, переработанное. – М. «Академия», 2014. – 256 с.
Дополнительные источники:
1.Никифоров В.М. Технология металлов и конструкционные материалы. –Л., Машиностроение, 1987-З6Зс.
2.Кузьмин Б.А. и др. Металлургия, металловедение и конструкционные материалы,- М., Высшая школа, 1977
3.Кузьмин Б.А. и др. Технология металлов и конструкционные материалы- М., Машиностроение,1989-4960.
4. Чернов Н.Н. Металлорежущие станки-М., Машиностроение, 1988-41бс.
5. Гурин Ф.В. ,Гурин М.Ф. Технология автомобилестроения- М: Машиностроение, 1986- 296с.
6. Мотовилин Г.В., Масино У.А., Суворов О.М. Автомобильные материалы: Справочник. М:Транспорт ,1989-464с.
ход ВЫПОЛНЕНИя РАБОТЫ
1. Обосновать выбор металла для изготовления заданной детали и выбор вида и режима термической и химико-термической обработки, которая обеспечит надежность детали в условиях эксплуатации, указанных в каждой задаче. (Условия задачи в методической карте работы, вариант определяет преподаватель).
____________________________________________________________________________________________________________________________________________________________________________________________________________________________________________________________________________________________________________________________________________________________________________________________________________________________________________________________________________________________________________________________________________________________________________________________________________________________________________________________________________________________________________________________________________________________________________________________________________________________________________________________________________________________________________________________________________________________________________________________________________________________________________________________________________________________________________________________________________________________________________________________________________________________________________________________________________________________________________________________________________________________________________________________________________________________________________________________________________________________________________________________________________________________________________________________________________________________________________________________________________________________________________________________________________________________________________________________________________________________________________________________________________________________________________________________________________________________________________________________________________________________________________________________________________________________________________________________________________________________________________________________________________________________________________________________________________________________________________________________________________________________________________________________________________
4. Вывод (характеристика изменения твердости исследуемых образцов до и после термообработки):
____________________________________________________________________________
____________________________________________________________________________
____________________________________________________________________________
____________________________________________________________________________
____________________________________________________________________________
____________________________________________________________________________
___________________________________________________________________________
____________________________________________________________________________
____________________________________________________________________________
____________________________________________________________________________
____________________________________________________________________________
Лабораторная работа 4.
Тема: ИзмеРение основных углов токарного резца.
Цель работы: 1) Углубление знаний конструкции и геометрических параметров основных токарных резцов
2)Ознакомиться со средствами и техникой измерения геометрических параметров токарных резцов
3)Определить влияние углов токарных резцов на процесс обработки металлов резанием
Задание: Практически провести измерения геометрических параметров токарных резцов.
Оборудование и материалы: набор основных видов резцов, универсальный настольный угломер ЛМТ, радиусомер, измерительная линейка или штангенциркуль.
Методические указания
Дата добавления: 2020-04-25; просмотров: 1441; Мы поможем в написании вашей работы! |
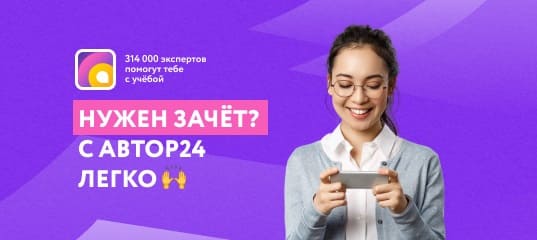
Мы поможем в написании ваших работ!