Порядок выполнения работы на приборе Роквелла
Выбрав образцы для измерения твердости на приборе ТК (например, отожженные стали 45, У8А, У12А; закаленные стали 45, У8А, У12А), произвести испытания твердости в соответствии с вышеуказанными рекомендациями. Результаты испытания занести в протокол:
Протокол № 2
Испытания на твердость твердомером типа ТК
(прибором Роквелла)
Показания твердости образцов стали, полученных на различных приборах, записать в таблицу по форме:
№ образца | Материал образца | Условия испытания | Измерения | |||||
нагрузка Р, Н | вид наконечника | обозначение шкалы | первое | второе | третье | среднее значение | ||
1 | ||||||||
2 | ||||||||
3 |
При составлении отчета необходимо указать:
Ø цель;
Ø задание лабораторной работы;
Ø применяемое оборудование;
Ø используемую литературу;
Ø указать теоретические данные и основные определения испытуемых показаний;
Ø записать основные данные по устройству приборов Бринелля и Роквелла;
Ø составить схему приборов, с указанием основных деталей;
Ø изложить последовательность выполнения работы по определению твердости выбранных образцов на соответствующих приборах;
Ø сделать вывод о возможностях, достоинствах и недостатках методов испытаний и применяемых при исследовании материалов.
ОТЧЕТ
По лабораторной работе № 1.
|
|
Тема: ИЗУЧЕНИЕ МЕТОДОВ ОПРЕДЕЛЕНИЯ ТВЕРДОСТИ
СПОСОБАМИ БРИНЕЛЛЯ И РОКВЕЛЛА
Цель работы: Приобрести навыки в определении твердости металлов на твердомерах
типа ТШ (прибор Бринелля) и типа ТК (прибор Роквелла).
Задание: 1) изучить устройство и работу твердомеров типа ТШ и ТК;
2) определить твердость отожженных и закаленных стальных образцов;
3) определить твердость образцов из цветных сплавов (бронза, латунь,
дюралюминий).
Оборудование и материалы: твердомер шариковый ТШ (прибор Бринелля); твердомер ТК (прибор Роквелла); лупа для измерения отпечатков, два комплекта отожженных образцов из стали марок (10), 20, 45, У8А, У12А, (У10А) размером 50X50X80 мм каждый; два комплекта закаленных и отпущенных образцов из стали марок 45, У8А, У12А; комплект образцов цветных сплавов: бронза, латунь, дюралюминий (марки сплавов подбирают в зависимости от практических возможностей лаборатории техникума).
Литература:
Основные источники:
1. Черепахин А.А. Материаловедение, 8-е издание, переработанное. – М. «Академия», 2014. – 256 с.
|
|
Дополнительные источники:
1.Никифоров В.М. Технология металлов и конструкционные материалы. –Л., Машиностроение, 1987-З6Зс.
2.Кузьмин Б.А. и др. Металлургия, металловедение и конструкционные материалы,- М., Высшая школа, 1977
3.Кузьмин Б.А. и др. Технология металлов и конструкционные материалы- М., Машиностроение,1989-4960.
4. Чернов Н.Н. Металлорежущие станки-М., Машиностроение, 1988-41бс.
5. Гурин Ф.В. ,Гурин М.Ф. Технология автомобилестроения- М: Машиностроение, 1986- 296с.
6. Мотовилин Г.В., Масино У.А., Суворов О.М. Автомобильные материалы: Справочник. М:Транспорт ,1989-464с.
1. Составить принципиальную схему твердомеров типа ТШ и ТК:
2. Определение твердости образцов
2.1. Испытания на твердость твердомером типа ТШ /прибором Бринелля/
№ образца
| Материал образца (марка) | № отпечатка | Условия испытания | Диаметр отпечатка | Твердость | Погрешность в % | |||||
нагрузка на образец Р,Н | диаметр шарика, мм | время выдержки под нагрузкой, с | первое измерение, мм | второе измерение, мм | среднее измерение, мм | НВ (теоретическое) | по таблице | ||||
1 | Сталь 1________ | 3000 | 10 | 10 | 4.3 | ||||||
2 | Сталь 3_______ | 3000 | |||||||||
3 | Сталь 2_______ |
|
|
Теоретическая твердость НВ по Бринеллю:
НВ = | 2 Р | Н/мм2 |
πD (D- ![]() |
1) НВ =
2) НВ =
3) НВ =
2.2. Испытания на твердость твердомером типа ТК /прибором Роквелла/
№ образца | Материал образца | Условия испытания | Измерения | |||||
нагрузка Р, Н | вид наконечника | обозначение шкалы | первое | второе | третье | среднее значение | ||
1 | ||||||||
2 | ||||||||
3 |
Результаты вдавливания наконечника на приборе Роквелла:
Н = K—(H—h)/c,
1)Н =
2)Н =
3)Н =
Вывод (об возможностях определении твердости металлов на твердомерах типа ТШ (прибор Бринелля) и типа ТК (прибор Роквелла).
-------------------------------------------------------------------------------------------------------------------
-------------------------------------------------------------------------------------------------------------------
-------------------------------------------------------------------------------------------------------------------
-------------------------------------------------------------------------------------------------------------------
-------------------------------------------------------------------------------------------------------------------
|
|
-------------------------------------------------------------------------------------------------------------------
-------------------------------------------------------------------------------------------------------------------
-------------------------------------------------------------------------------------------------------------------
-------------------------------------------------------------------------------------------------------------------
-------------------------------------------------------------------------------------------------------------------
-------------------------------------------------------------------------------------------------------------------
-------------------------------------------------------------------------------------------------------------------
-------------------------------------------------------------------------------------------------------------------
-------------------------------------------------------------------------------------------------------------------
-------------------------------------------------------------------------------------------------------------------
-------------------------------------------------------------------------------------------------------------------
-------------------------------------------------------------------------------------------------------------------
-------------------------------------------------------------------------------------------------------------------
-------------------------------------------------------------------------------------------------------------------
-------------------------------------------------------------------------------------------------------------------
-------------------------------------------------------------------------------------------------------------------
-------------------------------------------------------------------------------------------------------------------
Лабораторная работа 2.
Тема: ИЗУЧЕНИЕ И ЗАРИСОВКА МИКРОСТРУКТУРЫ
ЖЕЛЕЗОУГЛЕРОДИСТЫХ СПЛАВОВ
Цель работы: Изучить строение углеродистых сталей и чугунов, приобрести навыки в работе с металломикроскопом.
Задание: 1) Ознакомиться с устройством и работой металломикроскопа;
2) Изучить методику изготовления микрошлифов;
3) Дать характеристику структурных составляющих и сделать зарисовки;
4) Сделать вывод о влиянии структуры сплава на их свойства.
Оборудование и материалы: металлографические микроскопы МИМ-7; комплект микрошлифов сталей и чугунов; альбом фотографий микроструктур сталей и чугунов.
Методические указания
Металлографический метод испытаний применяют для изучения внутреннего строения металлов и сплавов при помощи анализов микроскопического и макроскопического. Макроанализ применяют при выборе места взятия пробы для макроанализа, при выявлении пористости, раковин, трещин, включений, неоднородностей по химическому составу и пр. Микроанализ — это исследование металлов и сплавов на специальных образцах (микрошлифах) с помощью металломикроскопов при увеличениях до 2000 раз. Микроанализ применяют в основном для выявления состава структурных составляющих и изменений внутреннего строения сплавов, происходящих под влиянием различных режимов термической и химико-термической обработки, а также после внешнего механического воздействия на сплав.
Приготовление микрошлифов. Образцы для микроанализа вырезают из того места, которое является наиболее важным в эксплуатационных условиях исследуемого металла или детали.
Образцы изготовляют цилиндрической (D = 10 и 15 мм) или прямоугольной формы (10Х 10 X 15 мм) пилой или карборундовыми дисками или электроискровым способом, в зависимости от твердости материала. Одну из плоскостей образца обрабатывают напильником или на абразивном круге; затем эту же плоскость шлифуют до выведения рисок шлифовальными шкурками различных номеров с постепенно уменьшающимися размерами зерен абразива или на вращающихся кругах специальными пластами.
После тщательного шлифования образец полируют до зеркального блеска на быстровращающихся дисках, обтянутых замшей, фетром или сукном с применением полирующей смеси (взмученные в воде оксиды алюминия, хрома, железа или паста ГОИ). В настоящее время широко применяют электрополирование.
Полированный шлиф подвергают травлению определенными химическими реактивами для выявления микроструктуры сплава. Реактивы для травления выбирают в зависимости от состава, структурного состояния сплавов и цели исследования.
Для травления поверхности шлифов существует много различных реактивов. Например, для образцов, изготовленных из стали и чугунов:
а) 5%-ный раствор азотной кислоты HNO3 в этиловом спирте;
б) 4%-ный раствор' пикриновой - кислоты (NО) С6Н6ОН в спирте;
в) пикрат натрия (NO)3C6H2Na — стандартный реактив, применяется для того, чтобы отличить цементит от феррита;
г) реактив, составленный из трех объемных частей соляной кислоты
НСl и одной части азотной кислоты HNO3. Реактив применяют для
травления нержавеющих сталей, пользуются им через 24 ч после приготовления.
Для образцов, изготовленных из медных сплавов:
а) 8%-ный раствор хлорида меди СuСl2;
б) 3%-ный раствор хлорида железа FеСl3 в 10%-ном растворе
соляной кислоты (НСl).
Для баббитов и магниевых сплавов:
а) 2—4%-ный раствор азотной кислоты HNO3 в спирте;
б) уксусный гликоль состава: 20% уксусной кислоты СН3СООН,
60% этиленгликоля С2Н4(ОН)2, 1% концентрированной азотной кисло
ты HNO3 и 19% воды. Уксусный гликоль применяют только для
магниевых сплавов: через 5—30 с после того, когда травитель будет
нанесен на поверхность микрошлифа, его стирают ватой, затем шлиф
промывают в горячей воде и высушивают.
Для алюминиевых сплавов:
а) 0,5%-ный раствор плавиковой кислоты в воде;
б) смесь кислот: 1% HF, 2,5% HNO3, 1,5% НСl и 95% воды.
Травление поверхности производится до ее потускнения, т. е. до тех пор, пока поверхность не примет ровный, слегка матовый оттенок без каких-либо пятен. Травление осуществляется методом погружения либо протирания. В первом случае микрошлиф с полированной поверхностью погружают на 3—8 с в реактив, во втором протирают ватой, смоченной в реактиве. После травления поверхность промывают в спирте и просушивают фильтровальной бумагой. При рассмотрении под микроскопом такой поверхности элементы структуры четко заметны. Если структура выявлена не отчетливо, шлиф травят дополнительно.
На этом приготовление шлифа заканчивается.
Металломикроскопы.
Для исследования микроструктуры металлов и сплавов применяют металлографические микроскопы, которые в отличие от биологических позволяют рассматривать при увеличении непрозрачные тела в отраженном свете.
По устройству различают микроскопы вертикальные и горизонтальные.
Рис. 4 Металлографический микроскоп МИМ-6:
1-фотокамера, 2-иллюминаторный тубус, 3- визуальный тубус с окуляром, 4- предметный столик, 5- микрометрический винт грубой наводки, 6- микрометрический винт тонкой наводки, 7- осветительное устройство Промышленность выпускает вертикальные металлографические микроскопы МИМ-6, МИМ-7 и горизонтальные МИМ-3, МИМ-8 и др. Одним из наиболее распространенных металломикроскопов в учебных заведениях является МИМ-6 (рис. 4). При визуальном наблюдении этот микроскоп обеспечивает увеличение до 590 раз и до 1416 раз — при фотографировании.
Лучи от источника света 2 (рис. 5), пройдя через коллектор 3, светофильтры 4, полуматовую пластинку 7, диаграмму 17, линзы 6, 8, 9 и полевую диафрагму 18, отражаются от пластины 10 и через объектив 12 попадают на шлиф 1.
Отразившись от поверхности шлифа, лучи света вновь проходят через объектив 12 и с помощью отражательной призмы 11 направляются в окуляр 16, попадая таким образом в глаз наблюдателя. Для перевода изображения на фотокамеру нужно с помощью рычага отодвинуть отражательную призму 11 и открыть фотозатвор, при этом лучи проходят через фотоокуляр 13 и, отражаясь от зеркала 14, попадают на матовое стекло фотокамеры 15, вместо которого можно вставить подготовленную к съемке кассету.
При работе с микроскопом следует отрегулировать интенсивность освещения при помощи винтов колпачка 7 (см. рис. 4) и коллектора 3 (рис. 5). Для удаления или приближения объектива 12 к шлифу пользуются микрометрическим винтом 5 грубой наводки (см. рис. 4), а затем микрометрическим винтом 6 тонкой наводки. Шлиф перемещается при помощи винтов предметного столика 4, который движется во взаимно перпендикулярных направлениях. Используя перечисленные подвижные части микроскопа, можно добиться четкого изображения структуры металла.
Общее увеличение микроскопа находим по формуле:
NH = N об N ок,
где N об — увеличение объектива; NOK — увеличение окуляра.
Использование различных объективов и окуляров, состоящих из набора оптических линз, позволяет получить различные увеличения. Аналогично работает микроскоп МИМ-7.
Характеристика структурных составляющих сталей в равновесном состоянии.
Под равновесным состоянием сплава понимается такое его состояние, при котором все фазовые превращения в сплаве полностью закончились. Основой для определения фаз и структурных составляющих железоуглеродистых сплавов в равновесном состоянии является диаграмма железо—цементит (рис. 7).
Структурные составляющие углеродистой стали после ее полного отжига следующие:
Феррит — твердый раствор углерода в ά-железе, продукт диффузионного превращения аустенита при охлаждении его ниже температур, соответствующих линии GS.
Зерна феррита образуются первыми, и их размер в значительной степени зависит от скорости охлаждения аустенита. При рассмотрении в микроскопе феррит наблюдается в виде светлых зерен неодинаковой яркости. Растворимость углерода в феррите достигает 0,025% и изменяется с изменением температуры.
Феррит является пластичной составляющей структуры; его относительное удлинение δ=50%. Твердость феррита (НВ6—160) зависит от концентрации в нем углерода и других растворенных элементов, от величины зерен, убывая с возрастанием последних.
Цементит — химическое соединение углерода с железом, или карбид железа (FезС). При рассмотрении под микроскопом он наблюдается в различных геометрических формах в виде пластин, мелких зерен и других структурных составляющих — перлита или феррита. Цементит травится реактивами медленнее, чем феррит, поэтому он как бы возвышается над последним и при рассмотрении под микроскопом кажется более светлым. Отличить цементит от феррита в сомнительных случаях можно путем травления шлифа пикритом натрия, который окрашивает цементит в темный цвет.
Цементит — самая твердая составляющая (НВ>800). Пластичность его ничтожно мала и практически равна нулю. Поэтому с возрастанием цементита в структуре стали, что наблюдается при увеличении в ней углерода, твердость стали повышается, а пластичность падает.
Перлит — эвтектоид, т. е. механическая смесь из цементита и феррита, образовавшаяся при распаде аустенита в результате медленного охлаждения последнего.
При изготовлении шлифа пластинки цементита, более твердого, чем феррит, сошлифовываются меньше и поэтому выступают из основной массы перлита. Феррит как мягкая составляющая сошлифовывается больше, что усиливается при травлении. Поэтому, рассматривая перлит под микроскопом при косом освещении, можно заметить чередующиеся между собой темные и светлые полоски. В зависимости от формы цементита различают: а) пластинчатый перлит, в котором цементит и феррит, имеют форму пластин; б) зернистый перлит, в котором цементит имеет форму зерен, расположенных в феррите. Границы зерен и пластин наблюдаются в виде темных линий, которые образуются тенью от выступающих цементитных частиц.
Форма и размеры цементитных частиц в перлите существенно влияют на свойства стали. Так, например, зернистый перлит более пластичен, но имеет большую твердость, чем пластинчатый. Твердость зернистого перлита НВ 160—220, а пластинчатого НВ 300—250. Если размер цементитных частиц очень мал, то перлит в обычном металломикроскопе наблюдается в виде темных зерен, на которых нельзя заметить ни пластин, ни зерен цементита.
Структура углеродистой стали после ее полного отжига представляет собой совокупность рассмотренных выше структурных составляющих и должна соответствовать диаграмме железо—цементит.
Структура в отожженных доэвтектоидных сталях (содержание углерода до 0,8%) представляет собой феррит и перлит. При рассмотрении под микроскопом зерна феррита кажутся светлыми, а зерна перлита — темными. С увеличением содержания углерода количество зерен перлита увеличивается. С возрастанием перлитной составляющей в структуре доэвтектоидной стали повышаются ее твердость и предел прочности, а пластичность уменьшается.
Отожженные эвтектоидные стали (содержание углерода 0,8%) полностью состоят из одной структурной составляющей — перлита (пластинчатого или зернистого). Твердость и предел прочности эвтектоидной стали выше, чем доэвтектоидной, пластичность ниже. Структура отожженных заэвтектоидных сталей представляет собой перлит + вторичный цементит. Последний в зависимости от режима термической обработки наблюдается в виде светлых, небольших по величине зерен либо в виде светлой сетки по границам зерен перлита. Строение и свойство перлита в заэвтектоидной стали аналогичны эвтектоидной стали.
Характеристика структурных составляющих чугунов. Чугун представляет собой сплав железа с углеродом и некоторыми другими элементами.
Углерода в чугуне содержится 2—6,67%, в структуре он наблюдается в виде графита и цементита. Структура чугуна зависит от скорости его охлаждения и химического состава. По структуре, наблюдаемой в микроскопе, чугуны делятся на белые, серые, высокопрочные и ковкие.
Белые чугуны образуются при ускоренном охлаждении и имеют матово-белый цвет в изломе. В белом чугуне почти весь углерод находится в связанном соединении с железом в виде цементита Fe3C.
В зависимости от содержания углерода различают три класса белых чугунов:
Ø доэвтектический (содержание углерода меньше 4,3%),
Ø эктектический (углерода 4,3%) и
Ø заэвтектический (углерода больше 4,3%).
Микроструктура доэвтектического чугуна включает три структурные составляющие:
Ø перлит,
Ø ледебурит и
Ø вторичный цементит.
Перлит наблюдается в виде темных зерен, а ледебурит — в виде отдельных участков. Каждый такой участок представляет собой смесь мелких округленных или вытянутых зерен перлита, равномерно расположенных в белой цементитной основе.
С увеличением концентрации углерода в доэвтектическом чугуне доля ледебурита в структуре увеличивается за счет уменьшения участков структуры, занимаемых перлитом и вторичным цементитом. Вторичный цементит наблюдается в виде светлых зерен.
Эвтектический чугун состоит из одной структурной составляющей — ледебурита, представляющего собой равномерную механическую смесь перлита с цементитом.
Заэвтектический чугун характеризуется двумя структурными составляющими — первичным цементитом и ледебуритом. С увеличением углерода количество первичного цементита в структуре возрастает. Характерная особенность структуры белого чугуна — наличие весьма твердых и малопластичных составляющих: цементита и ледебурита. Поэтому белый чугун имеет высокую твердость, мало пластичен и плохо обрабатывается резцом. По указанным причинам его применение в машиностроении ограничено.
Серый чугун имеет в изломе серый цвет, что объясняется присутствием в его структуре графита. Структура серого чугуна представляет собой металлическую основу, пронизанную графитовыми включениями.
Металлическая основа серого чугуна может быть
Ø ферритной,
Ø ферритно-перлитной и
Ø перлитной.
Ферритный чугун имеет структуру:
Ø феррит (светлая основа),
Ø перлит (серая основа) и
Ø пластинчатый графит (темные пластинчатые включения).
Перлитный серый чугун — перлит (серая основа), пластинчатый графит (темные пластинчатые включения).
Прочность графита в сером чугуне по сравнению с металлической основой ничтожно мала. Присутствие графита в чугуне равносильно надрезу — пустоте. Поэтому чем равномернее расположены графитовые включения в металлической основе, чем они мельче и их форма ближе к округленной, тем меньше разобщена металлическая основа чугуна и, следовательно, его прочность выше. Наличие графита, с одной стороны, снижает механические свойства чугуна, а с другой — повышает его износостойкость и способность поглощать вибрацию.
Высокопрочный чугун при рассмотрении в металломикроскоп имеет следующую структуру: металлическую основу (перлит и феррит, цементит и перлит или феррит) и графитовые включения в виде округленного (глобулярного) графита. Такой чугун получается модифицированным с помощью магния или церия. Высокая прочность чугуна обеспечивается указанной формой графита и структурой металлической основы.
Ковкий чугун получается в результате отжига отливок, изготовленных из белого чугуна. В процессе отжига цементит, входящий в структуру белого чугуна, распадается на железо и графит. Образующийся при этом графит имеет хлопьевидную форму (темные включения), что и обеспечивает хорошие пластические формы чугуна. В зависимости от строения металлической основы различают перлитный, перлитно-ферритный и ферритный ковкие чугуны.
Дата добавления: 2020-04-25; просмотров: 129345; Мы поможем в написании вашей работы! |
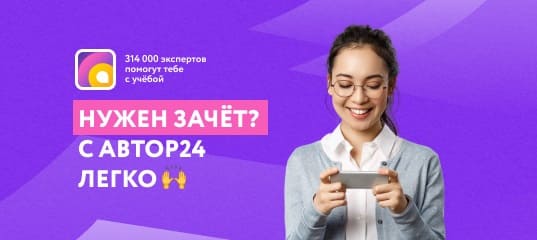
Мы поможем в написании ваших работ!