Определение стоимости отливки
Базовой маркой для отливки из стали принимаем сталь 20 ГОСТ 1050-88.
По таблице 2.4 прейскуранта [8] определяем оптовую цену 1т отливки шестой группы сложности (по таблице 1 [9]) массой М0 = 0,92 кг: М1 = 1,1 кг, Ц1 = 1053 руб./т, М2 =1,4 кг, Ц2 =1031 руб./т.
По таблице 2.5 прейскуранта [8] определяем величину коэффициента расчёта оптовых цен Кц, так как значение Кц для отливок из стали 20 отсутствует, тогда значение Кц принимаем для наиболее близкой по своим физико-механическим свойствам стали 20 ГОСТ 1050-88 (Кц= 3,3). Определяем оптовую цену 1 т отливок:
Цопт= Цх ∙ Кц = 1045,67∙3,3= 3450,7 руб./т. (23)
По таблице 1.1 прейскуранта [8] базовые значения точностных характеристик отливки шестой группы сложности с наибольшим габаритным размером до 160 мм включительно: класс точности размеров - 12, класс точности массы -12. Для отливки «Муфта» принимаем класс размерной точности 8, класс точности массы 8. По таблице 1.1 прейскуранта [8] определяем величину доплат к оптовой цене за точность размеров и точность массы:
Ктр = +0,39, Ктм = + 0,13.
По таблице 1.2 прейскуранта [8] для отливки из стали 20 толщина стенок не учитывается, т.е. Кs = 0. По таблице 1.7 прейскуранта [8] определяем группу серийности отливки массой 0,92 кг при Nгод =1000 шт./год: имеем седьмую группу. По таблице 1.8 прейскуранта [8] определяем величину доплат для седьмой группы серийности:
Кс = +0,02.
По таблице 1.10 прейскуранта [8] определяем величину доплат за нормализацию и очистку отливок до металлического блеска абразивным способом
|
|
Цто = 28+55=83 руб./т.
Определяем оптовую цену 1т отливок массой М0 = 0,92 кг заданных потребительских свойств
Сопт= Цопт(1 ± Ктр ± Ктм ± Кs ± Кс) + Цто + Цо (24)
Сопт = 3450,7 ∙ (1 + 0,39 + 0,13+ 0 + 0,02) + 83 =5397,1 руб./т
Определяем стоимость отливки
Определяем фактическую стоимость отливки
Сотл. факт. = Сотл.∙ Кинфл. = 8,1 ∙70 =567 руб. (25)
где, Кинфл.=70 руб. к курсу одного EURO.
2.5.3.5 Определение методов обработки поверхностей. Оптимальный способ обработки поверхностей детали означает, что удалось отыскать технологический переход. Таким образом, это является началом поиска структуры технологической операции, а затем и всего технологического процесса.
Применяют табличный, расчётный и таблично-расчётный методы выбора способа обработки поверхностей.
Табличным методом пользуются для быстрых ориентировочных решений, а также для выбора способов обработки поверхностей с невысокими технологическими требованиями.
Для более точных поверхностей рекомендуется использовать таблично-расчётный метод, основанный на определении уточнения. Задача решается в три этапа. На первом этапе отыскивают способы обработки, обеспечивающие требуемую точность размера поверхности. На втором этапе проверяют, обеспечивается ли заданное качество поверхностного слоя данной поверхности посредством способа обработки, выбранного на первом этапе. Если нет, то добавляют дополнительно такие способы обработки, которые позволяют решить задачу обеспечения качества поверхностного слоя либо заменяют часть способов, выбранных на втором этапе, на иные. На третьем этапе проверяют, обеспечиваются ли технические требования по точности формы и точности расположения поверхностей (если они оговорены в рабочем чертеже особо). Если нет, то также добавляют дополнительно такие способы обработки, которые позволяют решить и эту задачу.
|
|
ПРИМЕР: Рассчитаем общее уточнение для 1 наиболее точной (трудоемкой) поверхности.
1. ø50 Н9, Тдет=0,046. Находим общее уточнение
, (26)
где - допуск заготовки,
- допуск детали.
Далее методом подбора определяем необходимое количество способов обработки из известного соотношения
, (27)
где - уточнение на
-ом переходе.
|
|
Должно выполняться условие
а) Точение черновое
;
,
.
б) Точение чистовое
;
,
.
в) Шлифование предварительное
;
,
.
г) Шлифование окончательное
;
,
.
По формуле (15) определяем
- условие выполняется, следовательно, методы обработки поверхности выбраны верно.
Остальные методы обработки поверхностей выбираем табличным методом. Методы обработки поверхностей детали представлены в таблице 7:
Таблица 7
Методы обработки поверхностей детали
Номера поверхностей | Методы обработки | Квалитет точности | Допуск обработки, мкм | Шероховатость обработанной поверхности, мкм | Твердость поверхности |
1 | 2 | 3 | 4 | 5 | 6 |
1 | 1.Обтачивание черновое | 14 | 390 | 25-1,6 | HRC41…45 |
2 | Обтачивание черновое | 14 | 740 | 50-6,3 | HRC41…45 |
3 | 1.Обтачивание черновое | 14 | 390 | 25-1,6 | HRC41…45 |
4 | Обтачивание черновое | 13 | 270 | 12,5-6,3 | HRC41…45 |
5 | 1.Обтачивание черновое 2. Обтачивание чистовое | 13 11 | 390 160 | 25-1,6 25-1,6 | HRC41…45 |
6 | 1.Обтачивание черновое | 13 | 390 | 25-1,6 | HRC41…45 |
7 | 1.Обтачивание черновое | 13 | 390 | 25-1,6 | HRC41…45 |
8 | 1.Обтачивание черновое 2. Обтачивание чистовое 3. Шлифование предварительное 4. Шлифование окончательное | 13 11 9 7 | 390 160 62 25 | 25-1,6 25-1,6 6,3-0,4 3,2-0,4 | HRC41…45 |
9 | Обтачивание черновое | 13 | 270 | 12,5-6,3 | HRC41…45 |
10 | Обтачивание черновое Обтачивание чистовое Шлифование предварительное Шлифование окончательное | 13 11 9 7 | 390 160 62 25 | 25-1,6 25-1,6 6,3-0,4 3,2-0,4 | HRC41…45 |
11 | Фрезерование черновое | 13 | 270 | 25-0,8 | HRC41…45 |
12 | Фрезерование черновое | 13 | 270 | 25-0,8 | HRC41…45 |
13 | Сверление черновое | 13 | 270 | 25-0,8 | HRC41…45 |
14 | Сверление черновое | 13 | 270 | 25-0,8 | HRC41…45 |
15 | Сверление черновое | 13 | 270 | 25-0,8 | HRC41…45 |
16 | Сверление черновое | 13 | 270 | 25-0,8 | HRC41…45 |
17 | Сверление черновое | 13 | 270 | 25-0,8 | HRC41…45 |
18 | Сверление черновое | 13 | 270 | 25-0,8 | HRC41…45 |
19 | Нарезание резьбы | 7 | HRC41…45 | ||
20 | Нарезание резьбы | 7 | HRC41…45 | ||
21 | Нарезание резьбы | 7 | HRC41…45 | ||
22 | Нарезание резьбы | 7 | HRC41…45 | ||
23 | Нарезание резьбы | 7 | HRC41…45 | ||
24 | Нарезание резьбы | 7 | HRC41…45 | ||
25 | Протяжная | 9 | HRC41…45 | ||
26 | Протяжная | 9 | HRC41…45 | ||
27 | Протяжная | 9 | HRC41…45 | ||
28 | Протяжная | 9 | HRC41…45 | ||
29 | Протяжная | 9 | HRC41…45 | ||
30 | Протяжная | 9 | HRC41…45 | ||
31 | Протяжная | 9 | HRC41…45 | ||
32 | Протяжная | 9 | HRC41…45 |
|
|
2.5.3.6 Определение (расчет) припусков аналитическим методом. Величина припуска влияет на себестоимость изготовления детали. При увеличенном припуске повышаются затраты труда, расход материала и другие производственные расходы, а при уменьшенном приходится повышать точность заготовки, что также увеличивает стоимость изготовления детали.
Обычно в заготовках, полученных методом литья, могут содержаться раковины, песочные включения, а в штампованных заготовках имеются обезуглероженный слой, микротрещины и другие дефекты.
Дефектный слой чугунных отливок по деревянным моделям составляет 1-6 мм, у поковок - 0,5-1,5 мм и у горячекатаного проката - 0,5-1,0 мм. Для более точного определения припуска на обработку и предотвращения перерасхода материала применяют аналитический метод для каждого конкретного случая с учётом всех требований выполнения заготовок и промежуточных операций.
Для получения деталей более высокого качества необходимо при каждом технологическом переходе механической обработки заготовки предусматривать производственные погрешности, характеризующие отклонения размеров, геометрические отклонения формы поверхности, микронеровности, отклонения расположения поверхностей. Все эти отклонения должны находиться в пределах поля допуска на размер поверхности заготовки.
Аналитический метод определения припусков базируется на анализе производственных погрешностей, возникающих при конкретных условиях обработки заготовки.
Величина промежуточного припуска [3; 5; 15] для плоских поверхностей заготовки
(28)
для поверхностей типа тел вращения (наружных и внутренних)
(29)
где Rz – высота микронеровностей поверхности, оставшихся при выполнении предшествующего технологического перехода, мкм;
h – глубина дефектного поверхностного слоя, оставшегося при выполнении предшествующего технологического перехода, мкм;
D o – суммарные отклонения расположения, возникшие на предшествующем технологическом переходе, мкм;
y – величина погрешностей установки заготовки при выполняемом технологическом переходе, мкм.
Отклонения при чистовой обработке обычно исключают при расчётах из-за их малой величины. Отклонения и погрешности в установке определяют в каждом конкретном случае, в зависимости от метода получения заготовки.
Максимальный припуск на обработку поверхности заготовки:
- для плоских поверхностей:
; (30)
- для поверхностей типа тел вращения:
, (31)
где и
- допуск на размер на предшествующем переходе, мм;
и
- допуск на размер на выполняемом переходе, мм.
Допуски и шероховатость поверхности на окончательных технологических переходах (операциях) принимают по рабочему чертежу.
Для удобства распределения промежуточных припусков перед их расчётом исходные и расчётные данные по каждой операции на конкретную обрабатываемую поверхность в технологической последовательности заносят в таблицу [3; 5] (см. таблицу 8).
Таблицу рекомендуется заполнять в такой последовательности:
8. В графу «Заготовка и технологическая операция» записывают вид заготовки и операции, установленные на данную обрабатываемую поверхность в технологической последовательности.
9. В графу «Точность заготовки и обрабатываемых поверхностей» записывают степень точности выбранной заготовки и квалитет на промежуточные размеры без предельных отклонений.
10. В графу «Элементы припусков» заносят величину микронеровностей Rz и глубину дефектного поверхностного слоя Т на заготовку и на все операции в технологической последовательности, в зависимости от метода обработки, а величину погрешностей установки заготовки на выполняемой операции определяют по таблице или производят расчёт по формуле.
11. Суммарное значение отклонений рассчитывают аналитическим методом, и значения расчёта заносят в графу таблицы.
12. В графу «Допуски на размер» заносят значения допуска на заготовку и промежуточные размеры, в соответствии со степенью точности заготовки и квалитетом, установленным на размер по каждой операции.
Остальные значения промежуточных припусков и размеров вносят в таблицу после расчётов.
Графы промежуточных размеров Dmin и Dmax определяют и заполняют от окончательных промежуточных размеров до размеров заготовки.
Дата добавления: 2018-11-24; просмотров: 1455; Мы поможем в написании вашей работы! |
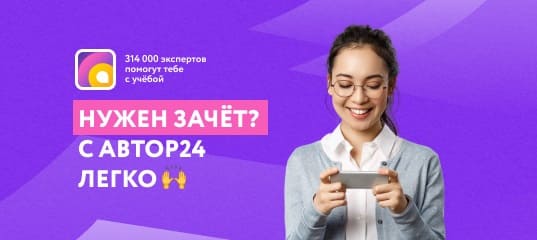
Мы поможем в написании ваших работ!