Классификация стали по содержанию примесей
Государственное профессиональное училище №81 Дипломная работа на тему: "Дуговая сварка неповоротных стыков стальных труб диаметром до 300 мм." Подготовил: Учащийся группы СВ-01 Курбангалеев Максим План 1. Введение. 2. Материал изделия-углеродистая сталь, расшифровка стали, ее свариваемость. Классификация сталей. 3. Сборка изделия, порядок сборки труб для водопроводов. 4. Сварка трубы. Выбор способа сварки и оборудования, обоснование их выбора. 5. Материал для сварки, обоснование их выбора. 6. Режим сварки, обоснвание показателей режима сварки. 7. Контроль качества сварных швов. 8. Техника безопасности при электросварке. 9. Список используемой литературы. Введение История развития сварки С электрическими явлениями в природе человек познакомился очень давно. Такими явлениями были: гроза; способность янтаря, натёртого шерстью, притягивать мелкие частички различных веществ; с древних времён были известны людям и некоторые свойства природных магнитов и т. д. В России интерес к электричеству постоянно возрастал со времён Ломоносова. И как только стало известно о создании итальянским физиком А. Вольта нового источника, способного давать электрическую энергию в результате химических реакций, русские исследователи начали работать с электрическим током. В начале 1802 года профессор Петербургской медико-химической академии В.В. Петров построил самый крупный для того времени источник тока - батарею из 4200 пар медных и цинковых кружков. Именно этой батареи и было суждено стать исторической: на ней была впервые в мире получена электрическая дуга. Её назвали вольтовой, по названию источника тока - вольтова столба. Но современники не сумели по достоинству оценить открытие учёного. От открытия В.В. Петрова до технического применения дугового разряда с целью соединения (сварки) и разъединения (резки) металлов прошло около 80 лет. Открытие В.В. Петрова значительно опередило свой век. Надо было появиться на свет новому русскому умельцу-самородку Николаю Николаевичу Бенардосу, который на основании дуги Петрова и достижений мировой электротехники создал принципиально новый способ сварки и резки металлов - электродуговой. Николай Николаевич Бенардос родился 26 июля (7 августа) 1842 года через восемь лет после смерти профессора В.В. Петрова, в деревне Бенардосовка на Херсонщине (ныне село Мостовое Николаевской области). С ранних лет он проявил интерес к различным ремёслам, особенно к технике. И хотя по настоянию отца, полковника в отставке, ему пришлось поступить на медицинский факультет Киевского университета, до конца он там не доучился и перешёл в Московскую земледельческую и лесную академию (ныне Тимирязевская сельскохозяйственная академия). В 1869 году Н.Н. Бенардос поселился в заштатном городке Лух Юрьевского уезда Костромской губернии. Он построил в имении матери механические мастерские и занялся воплощением своих изобретений, испытаниями и усовершенствованием их. Более 120 оригинальных изобретений сделал Н.Н. Бенардос, многие его идеи не потеряли своего значения и сейчас. Диапазон изобретений поразителен: железные бороны и углубители, скороварки и молотильные машины, паровые ножницы и пневматическая поливалка, пароходные колёса с поворотными лопастями и охотничьи лодки, замки и краны, турбины для гидроэлектростанций и пушка для метания канатов на терпящий бедствие пароход, летательные аппараты и станки для обработки металла и дерева, пневматические и вагонные тормоза и ветряной двигатель. Большое количество изобретений сделал он в области электротехники. И самым важным из них, принесших ему мировую славу, явился разработанный им в 1882 г. способ электродуговой сварки, названный электрогефестом. Металл расплавлялся дугой, горящей между угольным электродом, закреплённым в специальном держателе, и изделием, подключённым к полюсам источника тока. В 1886 году в столице России было организовано первое в мире специализированное научно-производственное объединение по электросварке -"Электрогефест". Сам Н.Н. Бенардос был здесь одновременно и учёным-исследователем, и конструктором аппаратуры, и рабочим-сварщиком. С 1886 года началось практическое применение дуговой сварки в мастерских железных дорог и на других предприятиях не только для ремонта, но и для изготовления различных металлических изделий. Создателем нового направления в производстве металлических конструкций стал русский инженер Н.Г. Славянов. Способ электросварки угольным электродом Н.Н. Бенардоса ещё только начинал своё триумфальное шествие по миру, когда на одном из заводов промышленного Урала электрическая дуга загорелась между изделием и стальным стержнем-электродом. Николай Гаврилович Славянов родился 23 апреля (5 мая) 1854 года в Задонском уезде Воронежской губернии. Окончив с золотой медалью гимназию в Воронеже, он в 1872 году поступил в Петербургский Горный институт. Получив специальность инженера-металлурга в 1877 году, Н.Г. Славянов уехал работать на казённый Воткинский горный завод смотрителем механических фабрик. В 1883 году он был назначен управителем орудийных и механических фабрик Пермских пушечных заводов в Мотовилихе. С 1888 года стал там горным начальником, а с 1891 года и до конца жизни занимал должность горного начальника (директора) Пермских пушечных заводов. Н.Г. Славянов заменил неплавящийся угольный электрод металлическим плавящимся электродом-стержнем, сходным по химическому составу со свариваемым изделием. Но самое главное то, что сварочная ванна была защищена слоем шлака - расплавленного металлургического флюса. Такой процесс повышал качество наплавленного металла при сварке. Н.Г. Славянов разработал специальный сварочный генератор на 1000 А, заменивший аккумуляторную батарею Бенардоса. В 1891 году Н.Г. Славянов запатентовал своё изобретение во Франции, Германии, Великобритании, Австро-Венгрии, Бельгии, а в 1897 году - в США. В России дальнейшее развитие нового технологического процесса электродуговой сварки столкнулось с существенными трудностями: электротехническая промышленность страны была очень слабой. Применение электросварки постепенно сокращалось, а со смертью её создателя практически прекратилось вовсе. Первые крупные сварочные работы в России возобновились и были выполнены под руководством В.П. Вологдина. На Дальзаводе (судоремонтный завод) он организовал в 1920 году сварочный участок, на котором ремонтировали детали и узлы судов, изготавливали паровые котлы, буксирные катера. На станции Большой Невер по проекту Вологдина впервые был построен сварной резервуар для хранения нефтепродуктов, начали строить сварные суда (первым было судно "Седов"), крупные доки, морские траулеры и т.п. С началом индустриализации советской России роль электросварки проявилась в полном объёме. Без неё не удалось бы невиданными темпами построить Магнитку, Кузнецк, Днепрогэс. В эти годы учёный, специалист в области мостостроения академик Евгений Оскарович Патон сумел оценить всё, что может дать сварка. Он организовал в Киеве при Академии наук УССР лабораторию, поставившую перед собой ясную и чёткую цель широкого применения электросварки вместо клёпки в самых различных отраслях промышленности. В январе 1934 года на базе этой электросварочной лаборатории был создан Институт электросварки, который в настоящее время носит имя его организатора - Е.О. Патона. В период с 1934 по 1941 год под руководством Е.О. Патона и при его непосредственном участии был выполнен цикл исследований в области проблем прочности сварных конструкций, их расчёта и надёжности. В результате систематических работ по изучению металлургических и электротехнических процессов дуговой сварки был разработан способ сварки под флюсом. Дальнейшие работы по сварке, выполненные в Институте электросварки им. Е.О. Патона, принесли институту всемирную известность. Материал изделия-углеродистая сталь, расшифровка стали, ее свариваемость. Классификация сталей.
|
|
|
|
|
|
|
|
Марка стали: 08кп.
Заменитель: 08
Классификация: сталь конструкционная углеродистая качественная.
Применение: для шайб, вилок, труб, а также деталей, подвергаемых химико-термической обработке-втулок, проушин, тяг.
Свариваемость: без ограничений. Сварка производится без подогрева и без последующей термообработки.
Ограниченно свариваемая: сварка возможна при подогреве до 100-200 град. и последующей термообработке.
Трудносвариваемая: для получения качественных сварных соединений требуются дополнительные операции: подогрев до 200-300 град. при сварке, термообработка после сварки-отжиг.
Углеродистой сталью называется сплав железа с углеродом (содержание углерода до 2%) с примесями кремния, серы и фосфора, причем главной составляющей, определяющей свойства, является углерод.К недостаткам углеродистой стали относятся:
отсутствия сочетания прочности и твердости с пластичностью;
потеря твердости и режущей способности при нагревании до 200°C и потери прочности при высокой температуре;
низкая коррозионная устойчивость в среде электролита, в агрессивных средах, в атмосфере и при высоких температурах;
низкие электротехнические свойства;
высокий коэффициент теплового расширения;
увеличение веса изделий, удорожание их стоимости, усложнение проектирования вследствие невысокой прочности этой стали.
Углеродистые стали
На долю углеродистых сталей приходится 80 % от общего объема. Это объясняется тем, что углеродистые стали дешевы и сочетают удовлетворительные механические свойства с хорошей обрабатываемостью резанием и давлением. При одинаковом содержании углерода по обрабатываемости резанием и давлением они значительно превосходят легированные стали. Однако углеродистые стали менее технологичны при термической обработке. Из-за высокой критической скорости закалки углеродистые стали охлаждают в воде, что вызывает значительные деформации и коробление деталей. Кроме того, для получения одинаковой прочности с легированными сталями их следует подвергать отпуску при более низкой температуре, поэтому они сохраняют более высокие закалочные напряжения, снижающие конструкционную прочность.
По статистической прочности стали относятся преимущественно к сталям нормальной прочности.
Расшифровка сталей
ОБОЗНАЧЕНИЕ И ПРАВИЛЬНАЯ РАСШИФРОВКА СТАЛЕЙ.
По химическому составу сталь расшифровывается:
цифровые обозначения стали.
буквенные обозначения стали.
Первыми цифрами марки обозначают содержание углерода (в десятых долях для инструментальных и нержавеющих сталей, в сотых долях для конструкционных сталей). Буквой указаны легирующий элементы. Следующими за буквой цифры обозначают среднее содержание в целых единицах, если содержании легирующею элемента менее чем 1,5% то за буквой цифровое обозначение не прописывается.
Основные буквенные обозначения применяемые в Российской промышленности:
Азот — А
Бор — Р
Ниобий — Б
Ванадий -Ф
Никель — Н
Вольфрам -В
Кобальт — К
Кремний — С
Марганец — Г
Молибден — М
Титан — Т
Углерод — У
Фосфор — П
Хром – Х
Алюминий — Ю
Медь — Д
Расшифровка марок сталей и химические элементы:
15х1м1ф – сталь жаропрочная низколегированная
20Х-сталь конструкционная легированная
12Х1МФ-сталь жаропрочная низколегированная
15Х5М-сталь жаропрочная низколегированная
Сталь 15Х5М флокеночувствительна и не склонна к отпускной хрупкости
40Х-сталь конструкционная легированная
30ХГСА-сталь конструкционная легированная
Сталь 15ХСНД-конструкционная низколегированная для сварных конструкций
Сталь 09Г2С -низколегированная конструкционная
Общими для всех обозначениями являются буквенные обозначения легирующих элементов:
Н — никель,
Х — хром,
К — кобальт,
М — молибден,
В — вольфрам,
Т — титан,
Д — медь,
Г — марганец,
С — кремний.
Конструкционные нелегированные качественные стали (например, Ст.10; Ст.20; Ст.30; Ст.45), обозначают двузначным числом, указывающим на среднее содержание углерода в стали 0,10%; 0,20%; и т.д.
Конструкционная низколегированная 09Г2С расшифровывается как сталь, углерода в которой около 0,09% и содержание легирующих компонентов марганца, кремния и других, составляет в сумме менее 2,5%.
Стали 10ХСНД и 15ХСНД отличаются разницей углерода, в таких сталях среднее содержание каждого элемента содержится менее 1% процента, поэтому цифры за буквой не ставятся.
Сталь 13ХФА
Заменитель: Сталь 15ХФА, Сталь 20ХФА, Сталь 09СФА
Классификация: Сталь конструкционная легированная
Применение: трубные заготовки и трубы бесшовных горячедеформированных нефтегазопроводных повышенной коррозионной стойкости и хладостойкости, предназначенные для использования в системах, транспортирующих газ, нефтегазопроводов, технологических промысловых трубопроводов, а также в системах поддержания пластового давления в условиях севера при температуре окружающей среды от -60°С до +40°С, температурой транспортируемых сред от +5°С до +40°С и рабочим давлением до 7,4 МПа; бесшовные горячедеформированные трубы повышенной коррозионной стойкости и хладостойкости, с наружным диаметром от 89 до 426 мм класса прочности не менее К52
Конструкционные легированные стали, такие как 20Х; 30Х; 40Х обозначают буквами и цифрами, в данном случае марка показывает содержание углерода и основного легирующего элемента хрома. Цифры после каждой буквы обозначают примерное содержание соответствующего элемента, однако при содержании легирующего элемента менее 1,5% цифра после соответствующей буквы не ставится.
30ХГСА хромокремнемарганцевая сталь, обладает большой прочностью и повышенным сопротивлением к ударным нагрузкам. В состав марки входит углерод 0,30%, кроме углерода содержит марганец, кремний и хром, примерно в равных долях по 0,8— 1,1%
Классификация стали
Сталь - деформируемый (ковкий) сплав железа с углеродом (до 2,14%) и другими элементами. Получают, главным образом, из смеси чугуна со стальным ломом в кислородных конвертерах, мартеновских печах и электропечах. Сплав железа с углеродом, содержащий более 2,14% углерода, называют чугуном.
99% всей стали - материал конструкционный в широком смысле слова: включая стали для строительных сооружений, деталей машин, упругих элементов, инструмента и для особых условий работы - теплостойкие, нержавеющие, и т.п. Его главные качества - прочность (способность выдерживать при работе достаточные напряжения), пластичность (способность выдерживать достаточные деформации без разрушения как при производстве конструкций, так в местах перегрузок при их эксплуатации), вязкость (способность поглощать работу внешних сил, препятствуя распространению трещин), упругость, твердость, усталость, трещиностойкость, хладостойкость, жаропрочность.
Высокопрочные стали имеют высокую прочность при достаточной пластичности (среднеуглеродистая легированная сталь 40ХН2МА), высокой конструктивной прочностью, малой чувствительностью к надрезам, высоким сопротивлением хрупкому разрушению, низким порогом хладноломкости, хорошей свариваемостью.
Классификация сталей и сплавов производится:
· по химическому составу;
· по структурному составу;
· по качеству (по способу производства и содержанию вредных примесей);
· по степени раскисления и характеру затвердевания металла в изложнице;
· по назначению.
Химический состав
По химическому составу углеродистые стали делят в зависимости от содержания углерода на следующие группы:
· малоуглеродистые - менее 0,3% С;
· среднеуглеродистые - 0,3...0,7% С;
· высокоуглеродистые - более 0,7 %С.
Для улучшения технологических свойств стали легируют. Легированной называется сталь, в которой, кроме обычных примесей, содержатся специально вводимые в определенных сочетаниях легирующие элементы (Сr, Ni, Мо, Wo, V, Аl, В, Тl и др.), а также Mn и Si в количествах, превышающих их обычное содержание как технологических примесей (1% и выше). Как правило, лучшие свойства обеспечивает комплексное легирование.
В легированных сталях их классификация по химическому составу определяется суммарным процентом содержания легирующих элементов:
· низколегированные - менее 2,5%;
· среднелегированные - 2,5...10%;
· высоколегированные - более 10%.
Структурный состав
Легированные стали и сплавы делятся также на классы по структурному составу:
· в отожженном состоянии - доэвтектоидный, заэвтектоидный, ледебуритный (карбидный), ферритный, аустенитный;
· в нормализованном состоянии - перлитный, мартенситный и аутенитный.
К перлитному классу относят углеродистые и легированные стали с низким содержанием легирующих элементов, к мартенситному - с более высоким и к аустенитному - с высоким содержанием легирующих элементов.
Классификация стали по содержанию примесей
По качеству, то есть по способу производства и содё примесей, стали и сплавы делятся на четыре группы
Стали обыкновенного качества
Стали обыкновенного качества (рядовые) по химическому составу -углеродистые стали, содержащие до 0,6% С. Эти стали выплавляются в конвертерах с применением кислорода или в больших мартеновских печах. Примером данных сталей могут служить стали СтО, СтЗсп, Ст5кп.
Стали обыкновенного качества, являясь наиболее дешевыми, уступают по механическим свойствам сталям других классов.
Стали качественные
Стали качественные по химическому составу бывают углеродистые или легированные (08кп, 10пс, 20). Они также выплавляются в конвертерах или в основных мартеновских печах, но с соблюдением более стро-гих требований к составу шихты, процессам плавки и разливки.
Углеродистые стали обыкновенного качества и качественные по степени раскисления и характеру затвердевания металла в изложнице делятся на спокойные, полуспокойные и кипящие. Каждый из этих сортов отличается содержанием кислорода, азота и водорода. Так в кипящих сталях содержится наибольшее количество этих элементов.
Стали высококачественные
Стали высококачественные выплавляются преимущественно в электропечах, а особо высококачественные - в электропечах с электрошлаковым переплавом (ЭШП) или другими совершенными методами, что гарантирует повышенную чистоту по неметаллическим включениям (содержание серы и фосфора менее 0,03%) и содержанию газов, а следовательно, улучшение механических свойств. Это такие стали как 20А, 15Х2МА.
Дата добавления: 2018-10-25; просмотров: 184; Мы поможем в написании вашей работы! |
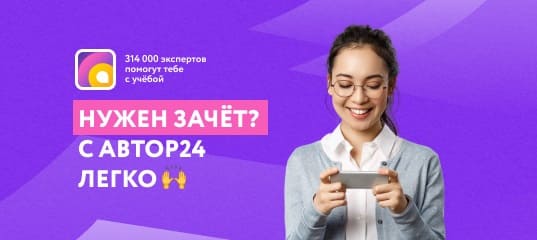
Мы поможем в написании ваших работ!