ТЕХНОЛОГИЯ ИЗГОТОВЛЕНИЯ ЖЕЛЕЗОБЕТОННЫХ СТАНИН МЕТАЛЛОРЕЖУЩИХ СТАНКОВ
Рассмотрена и проанализирована технология изготовления станин металлорежущих станков.
Железобетон – это сочетание бетона и стальной арматуры, при котором эти материалы работают совместно (рисунок 1).
Рис. 1. Схема работы железобетона под изгибающей нагрузкой
В верхней части балки при изгибе возникают сжимающие напряжения, в нижней – растягивающие. Предел прочности бетона на растяжение значительно (в 10-15 раз) меньше, чем при сжатии. Для увеличения сопротивления бетона растягивающим напряжениям целесообразно добавлять в опасные зоны стальную арматуру. Для лучшего сцепления бетона и арматуры используют специальные сгибы или анкеры на концах прутков, или используют прутки переменного сечения.
Изготовление железобетонных станин металлорежущих станков выполняется в следующем порядке:
1) Для жесткой фиксации основных рабочих компонентов станка используются закладные детали, которые непосредственно заливаются бетоном. Закладные детали как правило представляют собой: стальные плиты, швеллеры, бруски, двутавры и т.д. При проектировании схемы армирования необходимо предусмотреть правильную фиксацию закладных деталей в бетоне, что достигается следующими способами: в закладные вставляются анкерные болты, загнутые на конце; закладные можно внахлестку приваривать к стержням арматурного каркаса.
2) Далее производится подготовка арматурного каркаса. В верхней части станины располагаются основные продольные (рабочие) арматуры, для которых расходуется сталь повышенной прочности, они, как правило, имеют наибольший диаметр сечения. В нижней части располагается монтажная арматура, которая принимает на себя растягивающую нагрузку при монтаже и в ходе затвердевания бетона, а также сжимающую нагрузку непосредственно при эксплуатации. К рабочей и монтажной арматуре приваривают продольную арматуру, предварительно согнутую в хомут, она имеет наименьший диаметр - от 6 до 10 мм.
|
|
3) На ровную поверхность ставится основание опалубки, к которому жестко крепится стальная коробка, определяющая форму станины. На основании располагаются закладные и устанавливается арматурный каркас.
4) Собирается опалубка и производится бетонирование с уплотнением бетона.
5) Спустя несколько дней снимается опалубка, производится необходимая механическая обработка, грунтовочные и покрасочные работы.
Замена чугунного литья железобетоном позволяет значительно снизить трудоемкость изготовления станины и затраты средств на материалы. Полный цикл изготовления железобетонной станины, в сравнении с технологией чугунного литья, сокращается более чем в 10 раз. Это положительно сказывается на таком важном для каждого производства факторе, как ускорение оборачиваемости оборотных средств предприятия [1].
|
|
Материал поступил в редколлегию 24.02.2017
УДК 005.007
Протченко И.В.
Научный руководитель: доцент кафедры «Компьютерные технологии и системы», к.т.н. Терехов М.В.
ПЛАЗМЕННАЯ НАПЛАВКА ИЗНОСОУСТОЙЧИВЫХ ПОКРЫТИЙ, ЕЕ ПРИЕМУЩЕСТ И НЕДОСТАТКОВ
Рассмотрена и проанализирована технология плазменной наплавки, ее применение, а также преимущества и недостатки технологии.
Плазменная наплавка на данный момент один из современнейших способов наращивания различных металлов или сплавов. Плазменная наплавка используется для наложения на изделие различных износоустойчивых покрытий (жароустойчивых, кислотоупорных, антифрикционных, устойчивых к коррозии и износу) при восстановлении или изготовлении. Это очень экономит средства ведь изделия из высоко прочных материалов стоят очень дорого, но, если мы будем делать изделия из обычных твердых сплавов, а потом наращивать износа стойкое покрытие, это сэкономить большое количество денег и ресурсов. Плазмой называется высокотемпературный сильно ионизированный газ, состоящий из молекул, атомов, ионов, и др. При дуговой ионизации газ пропускают через канал и создают дуговой разряд, тепловое влияние которого ионизирует газ, а электрическое поле создает направленную плазменную струю.
|
|
Теперь разберемся как это работает, для наплавки используются металлы в виде проволоки или порошка. В таком состоянии металл попадает под луч плазмы где плавится и попадает на поверхность детали. Одновременно с этим процессом непрерывно нагревают и саму деталь (рис.1).
Рис. 1. Плазменная наплавка
Преимущества технологии: возможность покрыть деталь разными покрытиями с индивидуальными защитными особенностями; широкие границы регулирования энергетических возможностей плазменной дуги, поскольку она является наиболее гибким источником тепла; отсутствие ограничений по размерам наплавляемых зон и толщине напалки; плазменный поток имеет очень высокую температуру, из-за чего позволяет плавить тугоплавкие материалы; возможность многократного повторения процесса, в следствии чего повышение ремонтоспособности детали.
Недостатки технологии: возможность изменения свойств наплавленного покрытия из-за переходов в него элементов основного метала; возникновение деформации в изделиях за счет значительного термического воздействия; обязательное использование в отдельных случаях предварительного нагрева и медленного остывания наплавляемого изделия, что увеличивает время процесса; преимущественное расположение наплавляемого изделия в горизонтальном положении; трудоемкость наплавки мелких изделий сложной формы.
|
|
Материал поступил в редколлегию 24.02.2017
УДК 004.925.84
А.С. Силютина
Научный руководитель: доцент кафедры «Компьютерные технологии и системы», к.т.н. Терехов М.В.
silyutik@gmail.com
Дата добавления: 2018-10-27; просмотров: 593; Мы поможем в написании вашей работы! |
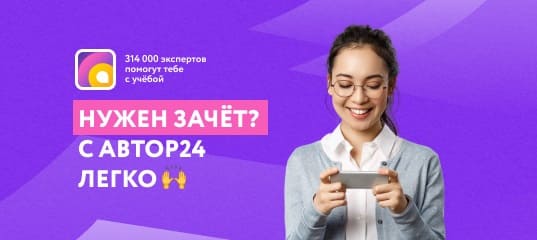
Мы поможем в написании ваших работ!