Основные задачи автоматизации
Лекция № 38
Глава 8. АВТОМАТИЗАЦИЯ ПРОЦЕССОВ ВАРКИ СТЕКЛА
Основные задачи автоматизации. Функциональная схема автоматизации стекловаренной печи
План
1 Стадии стекловарения
2 Ванная стекловаренная печь
3 Основные задачи автоматизации
4 Функциональная схема системы автоматического регулирования расхода газа с коррекцией по его температуре
5 Функциональная схема системы автоматического регулирования разрежения с коррекцией по давлению в печи
6 Функциональная схема системы автоматического регулирования уровня стекломассы
7 Функциональная схема системы регулирования соотношения газ — воздух
Стадии процесса стекловарения в ванных печах
Процесс стекловарения является основным технологическим процессом производства листового стекла и стеклоизделий. Прежде чем сформулировать задачи автоматизации, кратко рассмотрим основные стадии процесса стекловарения в ванных печах и особенности технологического агрегата — ванной стекловаренной печи.
Обычно рассматривают следующие стадии процесса стекловарения.
Стадия силикатообразования характеризуется тем, что к концу ее основные химические реакции в твердом состоянии между компонентами шихты закончены. В шихте не остается отдельных составляющих ее компонентов, большинство газообразных включений улетучивается. Для обычных натрий-кальциевых стекол эта стадия завершается при температуре 800 — 900 °С и характеризуется плавлением, кипением шихты и постепенным уменьшением объема куч шихты от загрузки в глубину варочной части.
|
|
Стадия стеклообразования характеризуется тем, что к концу ее стекломасса становится прозрачной, в ней отсутствуют непроваренные частицы шихты, однако она пронизана большим количеством пузырей и свилей. Эта стадия завершается при температуре 1150 — 1200 °С.
Стадия дегазации (осветления) характеризуется тем, что в конце ее стекломасса освобождается от видимых газовых включений, устанавливается равновесное состояние между стекломассой (жидкой фазой) и газами, остающимися в самой стекломассе (газовая среда). Внешним характерным признаком является наличие варочной пены. Отсутствие пены свидетельствует о завершении процесса осветления.
Стадия гомогенизации характеризуется однородностью и освобождением стекломассы от свилей. Визуально для процесса характерно чистое зеркало стекломассы при более низких температурах.
Стадия студки характеризуется снижением температуры на 200 — 300 °С, необходимым для достижения рабочей вязкости стекломассы. После прохождения стадии студки стекломасса при определенной температуре и вязкости поступает на формование, где из нее вырабатывается лента стекла или стеклоизделия.
|
|
В настоящее время процесс стекловарения на промышленных предприятиях осуществляют в ванных стекловаренных печах, где догрузка шихты, варка стекла и выработка ленты стекла (или стеклоизделий) происходят в течение всей кампании печи непрерывно и одновременно.
Ванная стекловаренная печь
Ванная стекловаренная печь состоит из бассейна, пламенного пространства, регенераторов, переводных клапанов и загрузчиков шихты. Бассейн представляет собой ванну, выложенную из огнеупорных брусьев и расположенную на самостоятельном основании. Стены бассейна, испытывающие гидростатическое давление стекломассы, обвязывают металлическими креплениями, а варочную часть снабжают дополнительно искусственным охлаждением. Пламенное пространство ограничено стенами и сводом, подвешенными на металлических опорах. Между стенами и бассейном печи оставляют закладываемый огнеупорным кирпичом промежуток (заклинок) высотой до 120 мм для наблюдения за печью и ее обслуживания. Стены и свод выкладывают из динаса и изолируют материалами, стойкими при высоких температурах. Бассейн печи выкладывают из огнеупорных брусьев, например, «Бакор-33», «Бакор-41».
|
|
Регенераторы представляют собой камеру прямоугольного сечения, внутри которой расположена насадка, выложенная из шамотного кирпича. Регенераторы служат для использования тепла отходящих газов и нагрева воздуха, подаваемого в горелки ванных печей с поперечным направлением пламени. Они могут быть вертикальными и горизонтальными. Чаще применяют вертикальные регенераторы.
Подачу горючего газа и воздуха, а также отвод отходящих газов в регенеративных печах производят с помощью переводных клапанов.
Топливо (газ, мазут) подают в печь обычно через водоохлаждаемые фурмы или форсунки, которые вставлены в щечки горелок. Снизу в горелки подается предварительно подогретый в регенераторах воздух. Топливо поступает по раздельным трубопроводам для каждой стороны печи и разводится по горелкам. Подача воздуха на современных стекольных заводах осуществляется принудительно с помощью вентиляторов под насадки регенераторов.
В настоящее время применяют следующие схемы подачи воздуха: от одного вентилятора в боров; индивидуально в каждую секцию регенератора от общего ветилятора; индивидуально в каждую секцию регенератора от отдельных вентиляторов; отдельно в каждую секцию регенераторов при количестве индивидуальных вентиляторов, уменьшенном вдвое.
|
|
Для охлаждения огнеупоров стены стекловаренной печи охлаждают сжатым воздухом.
Автоматизация технологического процесса стекловарения является сложной проблемой. Основной технологический агрегат стекольного производства — ванная стекловаренная регенеративная печь с поперечным направлением пламени представляет собой многозвенный объект с распределенными параметрами, значительной инерционностью и свойством самовыравнивания, подверженный случайным и детерминированным возмущениям, воздействующим как на входные, так и выходные параметры.
В качестве входных параметров объекта регулирования могут быть приняты: расход газа по горелкам, расход воздуха на горение, химический состав шихты, давление в печи, а также ряд дополнительных факторов (температура окружающей среды, атмосферное давление, теплотворная способность газа и пр.).
В качестве выходных параметров могут быть приняты: объем отбираемой из печи стекломассы, ее выработочная характеристика — вязкость, зависящая от химического состава и температуры расплава стекломассы.
Схематически стекловаренная печь представляет собой ванну с расплавом стекла, поверхность которого частично покрыта шихтой и варочной пеной. Сверху к поверхности стекломассы примыкает газовое пространство, в котором расположены газовые горелки, направляющие поток тепла в стекломассу.
Для полного математического описания стекловаренной печи необходимо одновременно моделировать процессы, происходящие в газовом пространстве, факелах горелок, шихте и стекломассе. Это сложная и трудоемкая задача. При моделировании процессов, происходящих в стекломассе, последнюю считают однородной несжимаемой ньютоновской жидкостью. Каждый элемент объема характеризуют следующими параметрами: плотностью ρ, давлением Р, температурой Т и скоростью υ .
Основные задачи автоматизации
Основными задачами автоматизации процессов стекловарения являются:
— стабилизация основных технологических параметров стекловарения с целью получения стекломассы заданного качества и количества;
— оптимизация технологического процесса стекловарения по технико-экономическому критерию.
В настоящее время ванные стекловаренные печи в той или иной степени оборудованы локальными системами автоматического регулирования отдельных технологических параметров, в задачу которых входит поддержание значений этих параметров, найденных при первоначальной настройке режима печи и корректируемых по мере надобности обслуживающим персоналом. К локальным системам относятся системы автоматического регулирования уровня стекломассы, расхода газа по горелкам, давления в пламенном пространстве печи, соотношения топливо — воздух, загрязнения и др. В данном случае выбор режимных значений, которые должны поддерживаться в заданных пределах с помощью локальных систем автоматического регулирования (САР), производится эмпирическим путем, т.е. подстройкой значений технологических параметров до первого устойчивого состояния. Рассматриваемые системы автоматического регулирования могут быть реализованы как на базе технических средств локальной автоматики (серийной контрольной, регулирующей аппаратуры), так и с применением управляющих вычислительных машин (УВМ), например в режиме непосредственного цифрового управления (НЦУ).
Автоматические системы стабилизации технологических режимов процессов стекловарения (первая задача) дают возможность стабилизировать теплотехнические и технологические параметры, обеспечивая тем самым стабильную работу стекловаренных печей и стеклоформующих машин и других агрегатов формования ленты стекла или стеклоизделий.
Применение локальных систем автоматического регулирования повышает качество выпускаемой продукции, уменьшает брак, технологические отходы и улучшает условия труда обслуживающего персонала. Нарушение технологических процессов варки стекла в ванных печах в значительной мере зависит от соблюдения технологической дисциплины в дозировочно-смесительном цехе и главным образом от стабилизации технологических режимов процесса варки стекла.
Другая задача автоматизации технологических процессов является весьма сложной проблемой, так как предусматривает создание автоматической системы управления, способной автоматически находить и поддерживать оптимальные технологические режимы в условиях непрерывного изменения внешних факторов. Создание подобной системы автоматического управления технологическими процессами стекловарения позволит выявить резервы повышения производительности стекловаренных агрегатов, а также экономических и качественных показателей.
Создание таких систем автоматического регулирования требует построения общей математической модели объекта, охватывающей множественные взаимозависимости всех основных технологических параметров, разработки технологических критериев процессов и применения средств вычислительной техники.
Математическая модель процессов стекловарения в общем виде может быть представлена как система, связывающая отмеченные параметры процесса. Для того или иного процесса математическая модель создается на основании теоретических и экспериментальных исследований, и на базе такой модели разрабатываются алгоритмы контроля и управления технологическими процессами стекловарения. Следует отметить, что не всегда представляется возможным непосредственно контролировать ряд технологических величин, поэтому на основании экспериментального изучения технологического процесса выявляют косвенные параметры, которые поддаются автоматическому контролю и характеризуют ход протекания технологического процесса. В качестве таких параметров могут быть названы: температура стекломассы на выходе из стекловаренной печи, положение границы варочной пены, форма границы раздела чистой стекломассы и пены, содержание кислорода в отходящих газах и др. Контроль некоторых косвенных параметров будет более подробно рассмотрен ниже.
В связи с тем, что общая функциональная схема автоматизации стекловаренного агрегата состоит из ряда схем автоматического управления и контроля технологическими параметрами процесса стекловарения и значительно насыщена унифицированной контрольно-измерительной регулирующей аппаратурой, она представлена раздельно на рис. 3.5 — 115. Рассмотрепные функциональные схемы построены на базе унифицированной аппаратуры «Каскад» системы ГСП.
В системах автоматического управления использованы следующие унифицированные блоки: преобразователь ферродинамический токовый ПФТ; преобразователь нормирующий НЛ-ТЛ1-М; блок суммирования А04; блок измерительный И04; блок регулирующий релейной группы 2Р21; блок регулирующий аналоговой группы АР12; устройство задающее токовое ЗУ05; устройство задающее ЗУ 11; блок управления аналогового регулятора БУ12; блок управления релейного регулятора БУ21; блок усилителей БУ2; блок указателей В12; амперметр узкопрофильный М1731С; дифманометр - тягонапоромер ДКОФМ-То4; дифманометр - расходомер мембранный ДМ-ЭР; пускатель бесконтактный ПБР-2-3; механизм электрический исполнительный с блоком токового датчика МЭО.
Дата добавления: 2018-10-27; просмотров: 352; Мы поможем в написании вашей работы! |
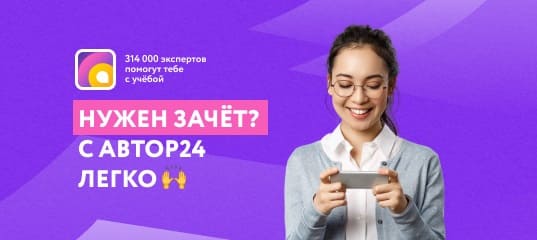
Мы поможем в написании ваших работ!