Объекты, входящие в состав Томинского ГОКа
Проектный замысел разработки Томинского месторождения выполнен по модели, применяемой для всех крупномасштабных медно‐порфировых проектов, где экономия добычи меди достигается за счет масштаба горных работ.
В составе Томинского горно-обогатительного комбината планируется три основных производственных комплекса:
1. Комплекс по добыче медно-порфировых руд Томинского месторождения и Калиновского участка - «Открытый рудник»;
2. Комплекс по получению медного концентрата и меди из руд месторождения:
a. Обогатительная фабрика производительностью 14 млн. т в год по исходной руде с хвостовым хозяйством и оборотным водоснабжением;
b. Гидрометаллургический завод по переработке окисленных руд (1,74 млн. т в год по исходной окисленной руде);
3. Комплекс инженерного обеспечения производства и санитарно-бытового обслуживания персонала комбината - «Производственная площадка предприятия с объектами инфраструктуры».
Для обустройства и эксплуатации Томинского ГОКа предполагается построить:
· автомобильную дорогу от Челябинской объездной дороги;
· железнодорожную ветку от станции «Клубника» ОАО «РЖД», расположенную в п. Первомайский;
· линии электропередач и подстанции ПС 220\10 кВ (мощностью 142 МВА) и ПС 110\10 кВ (мощностью 10 МВА);
· систему производственного технического водоснабжения для забора и подачи воды из поверхностных источников (с использованием стоков очистных сооружений пос. Новосинеглазово, г. Коркино, дренажных вод шахты «Коркинская» и угольного разреза «Коркинский);
|
|
· систему хозяйственно-питьевого водоснабжения;
· газопровод высокого давления и ГРП (от ГРП ОАО «Челябинскгазком»);
· телефонную и оптиковолоконную линии связи.
Проектом не предусмотрено строительство собственных складских помещений и объектов подготовки взрывчатых материалов и средств взрывания – данные виды работ будут выполняться по договору подряда сторонней организацией.
Более подробно характеристики объектов Томинского ГОКа даны в разделах ниже. Схема внутриплощадного размещения объектов комбината представлена в Приложении 1.
Основные объекты Томинского ГОКа
Открытые рудники
Томинское и Калиновское месторождения медно-порфировых руд находятся на расстоянии друг от друга в 4,7 км. Месторождения будут разрабатываться открытым способом.
Срок эксплуатации Томинского карьера с учетом развития и затухания горных работ составляет 18 лет, Калиновского – 10 лет. С 2025 по 2031 годы идет совместная отработка двух участков.
В условиях одновременной отработки и переработки запасов Томинский карьер определен как основной (около 75% годовых объемов руды перерабатываемой на ОФ методом флотации), а Калиновский карьер со статусом подчиненного значения.
|
|
В пределах рудника будут выполняться следующие основные процессы:
· Снятие поверхностного слоя почвы и ее размещение на хранение, склад почвенно-растительного слоя (ПРС);
· Выемка вскрыши;
· Добыча окисленной руды и ее переработка;
· Добыча сульфидной (первичной) и рыхлой руды и ее переработка.
Приняты следующие технические решения для проектирования рудных карьеров:
· Оптимизация количества окисленной и вторичной руды на рудных складах;
· Размещение дробильного комплекса в Томинском карьере, с целью естественного его заглубления, посадки фундаментов дробильного оборудования на скальный грунт и использования пространства карьера;
· Подшихтовка вторичных руд с рудного склада производится непосредственно в приёмный бункер, к первичным рудам на основной конвейер;
· Переработка окисленных руд методом кучного выщелачивания и гидрометаллургию;
· Использование скальных пород при строительстве объектов комбината и внутренних нужд.
Открытый карьер предусматривает строительство капитальных автомобильных съездов и последующую отработку горизонтов.
|
|
Основные технологические решения предусматривают цикличную технологию ведения горных работ – экскаватор в комплексе с автомобильным транспортом. В связи с различными физико-механическими свойствами выделенных промышленно-технологических типов руд и вмещающих пород на Томинском месторождении и Калиновском участке планируется различная технология их отработки:
· окисленные и вторичные руды Томинского месторождения и окисленные руды Калиновского участка будут отрабатываться без предварительного рыхления - с помощью экскавации с дальнейшей транспортировкой автосамосвалами к месту переработки или складирования;
· скальные первичные сульфидные руды будут добываться с предварительным рыхлением буро-взрывными работами (БВР) с последующей экскавацией и транспортировкой автосамосвалами до участка крупного дробления (производительностью 5248 т/ч), и далее конвейером на склад обогатительной фабрики.
Открытые горные работы ведутся по цикличной технологии с буровзрывной подготовкой горной массы к выемке. Для обеспечения высоких темпов ведения горных работ, предусматривается применение импортного горнотранспортного оборудования большой единичной мощности с дизельным приводом.
|
|
Вскрышные породы и грунт почвенно-растительного слоя транспортируются автотранспортом к местам складирования.
Согласно расчетам, общий объем вскрышных пород из двух карьеров составит около 370 млн. м3.
На основании принятой технологии отработки запасов окисленных и первичных сульфидных руд Томинского месторождения медно-порфировых руд, вскрышные породы, удаляемые из карьеров, складируются и используются в следующих направлениях:
• складирование ПРС на специализированный склад – 4 639 тыс. м3;
• складирование во внешний отвал скальной вскрыши – 84 629 тыс. м3;
• складирование во внешний отвал рыхлой вскрыши – 92 393 тыс. м3;
• формирование площадки склада окисленных руд – 5 000 тыс. м3;
• формирование промышленной площадки – 35,4 тыс. м3;
• формирование монтажной площадки – 15 тыс. м3;
• формирование ограждающего вала (дамбы) накопителя рудничных вод – 1 816,1 тыс. м3;
• отсыпке земляного полотна технологических автодорог – 250,0 тыс. м3.
Также планируется использования вскрышных пород на устройство противофильтрационных экранов хвостохранилища.
Отработка окисленных руд планируется с первого года, а отработка первичных сульфидных руд – со второго года проектного периода. На полную мощность по руде, составляющую 14 млн. т. руды в год, предприятие выходит с 5 года ведения работ. Часть окисленной и рыхлой руды будет размещаться на складах временного хранения, для того, чтобы как можно раньше начать разработку первичных сульфидных руд.
Для подготовки скальной горной массы к выемке принят буровзрывной способ рыхления. Буровые работы заключаются в бурении взрывных скважин в скальном массиве с использованием буровых установок.
В качестве взрывчатых материалов на руднике было принято использовать водно-гелевое взрывчатое вещество Rioflex 7000 производства компании Maxam.
Взрывные работы заключаются в производстве эмульсионных взрывчатых веществ (ВВ) на заводе, доставке ингредиентов для приготовления ВВ до скважины, заряжании скважины, монтаже взрывной сети на взрываемом блоке и организации взрыва. Данные работы планируется проводить с использование подрядной организации. Максимальная масса взрывчатки при одном цикле взрыва составит до 2 т.
Для обеспечения нужд карьера предполагается строительство участка по изготовлению компонентов водно-гелевого взрывчатого вещества и по мере увеличения объемов взрывных работ использовать необходимое количество смесительно‐зарядных машин (СЗМ).
Гидрометаллургия
Настоящим проектом предусматривается строительство гидрометаллургического завода по переработке продуктивных растворов кучного выщелачивания меди из окисленных руд. Переработка окисленных медных руд будет производиться методом кучного выщелачивания слабыми сернокислыми растворами. Извлечение меди из медьсодержащих продуктивных растворов будет производиться с помощью экстракционной технологии (технология SX) с последующей реэкстракцией и электролизом меди (технология EW) с получение высококачественных медных катодов (с содержанием меди – 99,99%).
После проведения специальных исследований была рекомендована схема переработки окисленных руд, предусматривающая основные процессы:
· трехстадийное дробление руды;
· окомкование руды с добавлением серной кислоты;
· транспортировка окомкованной руды системой транспортеров до полигона выщелачивания;
· укладка руды в штабель на специально подготовленную площадку;
· выщелачивание руды путем орошения кучи слабым раствором серной кислоты;
· сбор продуктивных растворов выщелачивания по системе дренажей и подача их в пруд-накопитель, где раствор отделяется от примесей;
· экстракция меди из продуктивных растворов и получение богатого медьсодержащего реэкстрагента;
· перевод меди из органического раствора в электролит;
· электролиз электролита с получением катодной меди содержанием 99,99 %;
На рис. 2.4-1 показана технологическая схема кучного выщелачивания меди из окисленных руд с переработкой продуктивных растворов и получением катодной меди.
Рис. 2.4-1. Технологическая схема кучного выщелачивания меди
Переработка окисленных руд месторождения Томинское и участка Калиновский, а также производство товарной продукции (катодной меди) будет осуществляться на гидрометаллургическом комплексе ЗАО «Томинский ГОК», в состав которого входят:
· полигон кучного выщелачивания;
· смеситель для приготовления выщелачивающих растворов;
· прудок-отстойник медьсодержащих продуктивных растворов;
· прудок-отстойник обезметалленных растворов;
· аварийный пруд;
· цех по производству катодной меди с установкой по извлечению меди из продуктивных растворов;
· склад серной кислоты с емкостями;
· насосная станция;
· вспомогательные сооружения (трансформаторная подстанция и т. д.).
Производительность проектируемого гидрометаллургического комплекса по руде составит 1740 тыс. т./год.
Продолжительность цикла отработки одной секции рудного штабеля составляет 100 суток. Под нужды полигона кучного выщелачивания будет необходимо около 64 га площади земель.
Годовая производительность гидрометаллургического комплекса переработки окисленных руд по товарной продукции (катодной меди) составит 5660 т. Период работы гидрометаллургического комплекса составит 15 лет.
Для снижения негативного воздействия в процессе строительства и эксплуатации гидрометаллургического завода по переработке окисленных руд предусмотрены следующие меры:
· Площадка кучного выщелачивания будет иметь надежную гидроизоляцию и высокую механическую прочность;
· Конструкция основания рудного штабеля будет обеспечивать полный сбор раствора из кучи и исключать утечку растворов в неконтролируемую зону;
· Для сбора, осветления и временного хранения продуктивных (медьсодержащих) и обезметалленных растворов технологической схемой предусматривается строительство следующих технологических емкостей:
o прудок медьсодержащих продуктивных растворов объемом 7 тыс. м3;
o прудок обезметалленных растворов объемом 7 тыс. м3.
· В период межсезонья и простоя оборудования предусмотрено использование аварийного прудка, в который будет производится сбор дождевых и талых вод
· Для предотвращения случайной гибели водоплавающих птиц, поверхность прудов технологических растворов перекрывают капроновой сеткой закрепленной на стальных тросах;
· Электролизные ванны будут снабжены вентиляционным колпаком со скрубберной очисткой отходящих газов.
Обогатительная фабрика
На основании проведенных исследований и технологических испытаний для сульфидных руд месторождения Томинское и Калиновского участка была рекомендована технология переработки методом прямой селективной двухстадиальной флотации с получением медного концентрата марки КМ-5. Технология переработки включает следующие операции:
· Крупное дробление руды и складирование дробленой руды;
· Измельчение дробленой руды в специальной мельнице, разделение продукта дробления на фракции, часть из которых направляется либо на многостадийную флотацию, либо на додрабливание в конусной дробилке;
· Флотационное обогащение концентрата предполагает многократное применение последовательных стадий флотации, измельчения, разделение продуктов флотации на пенный концентрат сульфидов меди и минералы пустой породы (хвосты).
В процессе флотационного обогащения используют основные реагенты (известь, собиратели, пенообразователи), которые будут автоматически дозироваться в зависимости от количества перерабатываемой руды.
На рис. 2.4-2 показана технологическая схема получения медного концентрата из сульфидных руд методом прямой селективной двухстадиальной флотации.
Рис.2.4-2. Схема получения медного концентрата методом прямой селективной двухстадиальной флотации.
Крупное дробление и складирование дробленой руды
Исходную руду максимальной крупностью 1000 мм доставляют автосамосвалами и разгружают в приемное отверстие гирационной дробилки. Для удаления негабаритных кусков руды дробилка оснащена гидравлическим молотом (бутобоем). Дробление осуществляется в одну стадию на гирационной дробилке до крупности 200-250 мм.
Дробленую руду разгружают в промежуточный бункер, откуда пластинчатым питателем и магистральным ленточным конвейером руда транспортируется на промежуточный склад дробленой руды, расчитанный на суточную производительность. Укладку руды на складе осуществляют при помощи конвейера.
Для руд Томинского меторождения и участка Калиновский планируются отдельные дробилки и склады крупнодробленой руды.
Со склада дробленой руды через промежуточные бункера посредством пластинчатых питателей и конвейера руду направляют в главный корпус обогатительной фабрики.
Смешивание руд Томинского месторождения и Калиновского участка, а также извести, подаваемой для регулирования среды обогащения, производится на магистральном конвейере.
Измельчение и предварительная песковая флотация
Руда конвейером подается в мельницу полусамоизмельчения. Измельчение руды осуществляется в двух параллельно установленных мельницах полусамоизмельчения и трех шаровых мельницах. Конечная крупность измельчения составляет 80 % минус 0,1 мм.
С целью выделения материала «критической» крупности, после мельницы полусамоимельчения установлен грохот с ситом 9 мм. Додрабливание надрешетного продукта грохота разгрузки мельниц полусамоизмельчения производится в конусной дробилке. Разгрузка конусной дробилки возвращается в питание мельницы полусамоизмельчения. Подрешетный продукт грохота направляется на классификацию на гидроциклонах.
Планируется, что пески гидроциклонов периодически, при подходящем вещественном составе отдельных участков месторождения, будут направляться на песковую флотацию с целью выделения раскрытых минералов меди, что позволит выделить черновой концентрат, тем самым снизить переизмельчение материала и, как следствие, снизить потери меди с шламами. Пенный продукт песковой флотации, минуя основную и контрольную операции флотации, направляется на перечистные операции. Камерный продукт песковой флотации, либо пески гидроциклона направляются на измельчение в шаровых мельницах. Измельченный продукт шаровых мельниц возвращается на классификацию гидроциклонами.
Слив гидроциклона направляется на основную флотацию.
Флотация
Флотация включает основную, контрольную и две перечистных операции.
Флотационное отделение состоит из четырёх веток основной и контрольной флотации, каждая из которых состоит из контактного чана объемом 300 м3 и четырех флотационных камер основной флотации объемом 300 м3 каждая и четырех флотационных камер контрольной флотации объемом 300 м3 каждая. Две секции перечистной флотации представляют собой пять флотационных камер первой перечистки объемом 100 м3 каждая, а также четыре камеры второй перечистки объемом 30 м3 каждая.
Слив гидроциклонов отделения измельчения самотеком поступает в агитационный чан, где осуществляется перемешивание пульпы с флотационными реагентами перед основной флотацией. В качестве основных реагентов флотационного обогащения планируется использование извести как регулятора среды , собирателя Aerophine 3418А, пенообразователя оксаль Т-92. Приготовление растворов реагентов на фабрике проводят в реагентном отделении. Для подачи реагентов предусматривается система автоматического дозирования по количеству перерабатываемой руды. Проливы реагентов, а также смывы полов и оборудования реагентных отделений собирают в дренажных канавах и дренажными насосами направляют либо в хвостохранилище, либо возвращают в соответствующую емкость приготовления раствора.
Из чана пульпа поступает во флотомашины основной операции. Пенный продукт основной флотации через зумпф направляется на классификацию в гидроциклоны.
Камерный продукт основной флотации поступает во флотомашины контрольной операции. Пенный продукт контрольной флотации объединяется с концентратом основной операции. Хвосты контрольной флотации, являющиеся отвальным продуктом фабрики, разгружаются в зумпф и далее насосом перекачиваются в хвостохранилище.
Объединенный пенный продукт основной и контрольной флотации направляется на тонкое измельчение с предварительной классификацией в гидроциклонах. Слив гидроциклонов, готовый по крупности продукт, направляется в питание первой перечистной флотации, а пески гидроциклонов вновь направляются в шаровую мельницу. Камерный продукт первой перечистки направляется в хвосты, а пенный продукт поступает на вторую перечистную флотацию. Пенный продукт второй перечистки является кондиционным товарным концентратом меди, который направляется в отделение сгущения и фильтрации концентрата.
Обезвоживание продуктов флотации
Медный концентрат подвергают обезвоживанию в радиальных сгусителях при постоянном добавлении флокулянта. Слив сгустителя направляется на оборотное водоснабжение. Пески сгустителя направляются в питание фильтр-пресса. Оборотный фильтрат направляется в питание радиального сгустителя. Кек фильтра (обезвоженный медный концентрат) разгружают на ленточный конвейер, далее конвейером направляют на склад медного концентрата.
Хвосты флотационного обогащения без специальной обработки направляют в хвостохранилище.
Конечная продукция
Конечным товарным продуктом обогащения сульфидных рудявляется медный концентрат марки КМ-5 с массовой долей влаги не более 13 %. Характеристика концентрата КМ-5 приведена в Таблице 2.4-1. Отвальным продуктом переработки являются хвосты флотации с содержанием меди менее 0,07 %. Характеристика насыпного и удельного веса продуктов обогатительной фабрики приведена в таблице 2.4-1.
Таблица 2.4-1. Сводные данные переработки руд на обогатительной фабрике Томинского ГОКа
Показатель | Ед. изм. | Значение |
Исходное питание | ||
Производительность по сульфидной руде | тыс.т./год | 14 000 |
Содержание в руде Cu | % | 0,44 |
Всего металл | т./год | 61 600 |
Продолжительность эксплуатации месторождения | лет | 20 |
Суммарная добыча меди в руде за весь период эксплуатации месторождения | т. | 1 232 000 |
Технологические показатели извлечения меди | ||
Извлечение металла | % | 85 |
т./год | 52 360 | |
Выход концентрата | % | 1,88 |
Выход концентрата | т./год | 261 800 |
Содержание меди в концентрате | % | 20 |
Суммарный выход концентрата за весь период эксплуатации месторождения | тыс.т. | 5 236 |
Суммарный выход меди в концентрате за весь период эксплуатации месторождения | тыс.т. | 1 047 |
Потери | ||
Выход отвальных хвостов | тыс.т./год | 13 737 |
Содержание меди в отвальных хвостах | % | 0,07 |
Потери меди с отвальными хвостами | т./год | 9 240 |
Суммарный выход отвальных хвостов за весь период эксплуатации месторождения | тыс.т. | 274 740 |
Суммарные потери меди в отвальных хвостах за весь период эксплуатации месторождения | тыс.т. | 184,8 |
Средний годовой выход товарного концентрата марки КМ-5 составит 261 800т, в пересчете на металл 52,3 тыс.т. За весь период эксплуатации месторождения планируется получить 5 236 тыс. т. товарного концентрата КМ-5, либо, в пересчете на чистую медь 1 047 тыс. т. Содержание меди в отвальных хвостах составит 0,07 %. За весь период отработки месторождения выход отвального продукта составит около 274 740 тыс. т.
Хвостохранилище
Для размещения хвостов от обогатительной фабрики к юго-западу от карьеров планируется построить хвостохранилище.
В состав проектируемых гидротехнических сооружений хвостохранилища будут входить:
1. Сооружения хвостового хозяйства:
· площадка хвостохранилища для складирования отвальных хвостов;
· магистральные и распределительные пульповоды для гидравлического транспорта хвостов.
2. Сооружения оборотного водоснабжения:
· водосбросные сооружения хвостохранилища;
· насосная станция оборотного водоснабжения;
· водоводы оборотной воды.
3. Дренажные сооружения.
4. Контрольно-измерительная аппаратура.
Хвостохранилище проектируется на складирование отвальных хвостов обогатительной фабрики в течение 20 лет эксплуатации. С учетом производительности фабрики до 14 млн. т руды в год и календарным планом переработки руды, общий объем отвальных хвостов составит 274, 740 млн. т.
При объемной плотности намывных хвостовых отложений 1,4 т/м3, и с учетом коэффициента заполнения 0,85, необходимая емкость хвостохранилища составит 231 млн. м3.
Общая площадь хвостохранилища составит 760 га.
Предполагается, что первичные дамбы будут возведены по всему периметру до первоначальной высоты от 6 до 10 м в зависимости от топографии отдельных участков. В дальнейшем, по мере заполнения, планируется нарастить 6 ярусов для первого хвостохранилища и один ярус для второго хвостохранилища с приращением высоты по ~4,0 м с каждым ярусом.
При организации площадки хвостохранилища какого-либо экранирования (из привозных материалов) днища хвостохранилища не предусматривается в связи с низкой эффективностью таких сооружений. Экранирование ложа хвостохранилища предлагается осуществлять намывом малофильтрующих хвостов с использованием вскрышных пород, а перехват фильтрационных вод осуществлять дренажными сооружениями. Дренажные сооружения располагаются вдоль одной стороны хвостохранилища и состоят из дренажных канав и дренажных насосных установок. Дренажные канавы целесообразно заглубить на 4-5 метров ниже отметок рельефа местности с тем чтобы перехватывать часть грунтового потока, уровень которого в естественном состоянии, по данным изысканий, располагается на глубине 3,5-4,0 м. Дренажные воды перекачиваются в хвостохранилище и будут использованы для подпитки системы оборотного водоснабжения.
Транспортировка хвостов с обогатительной фабрики будет организована с использованием пульповодов.
Проектируемая система гидротранспорта хвостов состоит из следующих сооружений:
· пульпонасосная станция, располагающаяся на обогатительной фабрике;
· магистральные пульповоды;
· распределительные пульповоды.
Предлагается, что система гидротранспорта хвостов будет включать две основные ветки магистрального пульповода и одну резервную.
Прокладка пульповодов будет осуществляться наземным способом по железобетонным подкладкам без теплоизоляции. Вдоль трассы будет проложена инспекторская автодорога.
Для сбора пульпы при опорожнении трубопроводов будет организована аварийная емкость.
Распределительные пульповоды будут работать в две нитки (длина каждой 4,0 км). Общая длина всех распределительных пульповодов составит 8,0 км.
Система оборотного водоснабжения
В состав системы оборотного водоснабжения входят: два водосборных коллектора, насосная станция оборотной воды и водоводы.
Работа хвостохранилища предусматривается в замкнутом цикле без сброса технологических вод в естественные водоемы. Отстойный пруд хвостохранилища является основным источником водоснабжения для обогатительной фабрики.
Осветленные воды собранные водосборным колодцем будут поступать в насосную станцию оборотной воды в которой устанавливаются три насоса, из них два насоса рабочих, один - в резерве.
От насосной станции оборотной воды до обогатительной фабрики, предусматривается прокладка двух водоводов: один рабочий и один в резерве. Длина трассы ~1 200 м. Прокладка водоводов подземная, в засыпке. Вдоль трассы водоводов необходимо проложить инспекторскую автодорогу.
Дата добавления: 2018-10-26; просмотров: 766; Мы поможем в написании вашей работы! |
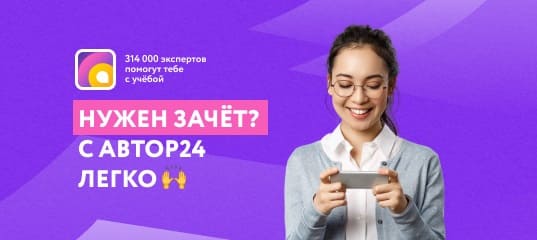
Мы поможем в написании ваших работ!