Технологические параметры процесса
Неоднократными исследованиями установлено, что качество метанола-сырца находится в прямой зависимости от технологических параметров процесса: отношение в циркуляционном газе, объемной скорости и температуры. Повышение температуры синтеза как на цинк - хромовом , так и на медь содержащихся катализаторах всегда ухудшает качество метанола-сырца: увеличивается содержание спиртов
, альдегидов, некоторых эфиров и др. Увеличение соотношения
в циркуляционном газе всегда сопровождается снижение содержания примесей в метанол-сырце (эфиров, альдегидов, кислот),что видно по изменению перманганатного числа. Этот показатель , хотя и не даст полной характеристики качества продукта (оценивает только содержание примесей, которые способны окисляться
) , позволяет предсказать концентрацию основных органических примесей в метанол-сырце.
Влияние параметров процесса на содержание примесей в метаноле – сырце при низкотемпературном синтезе под давлением 5 МПа изучалось на опытно-промышленном агрегате (объем катализатора 1.7 ) и на опытной установке с однорядным изотермическом реактором ( объем катализатора 20
. Данные получены для периода работы катализатора, характеризующегося наименьшей скоростью снижения активности. Сырьем служил газ, получаемый парокислородной конверсией природного пара после моноэтаноламиновой очистки. Состав газа корректировали введением в него диоксида углерода и технического водорода. Увеличение соотношения
способствует снижению содержания в метаноле-сырце всех рассматриваемых примесей.( рис 3.24 давление 5 МПа, температура 260 °С, содержание
7 %, инертных компонентов 20 % об.)
|
|
Значительное влияние на содержание примесей оказывает температура. При ее повышении резко увеличивается содержание в метанол-сырце пропанола-1, пентанола -3,2- метилпропанола.
При повышении температуры и давления всегда снижается содержание основного продукта – метанола, а при повышении соотношения в циркуляционном газе, напротив, улучшается качество метанола- сырца и уменьшается общее содержание примесей.
Такая же закономерность отмечается и для индивидуальных компонентов, например высших спиртов и других кислородсодержащих примесей.
Функциональная схема
Технологический процесс получения метанола из оксида углерода и водорода включает ряд операций, обязательных для любой технологической схемы синтеза. Газ предварительно очищается от карбинола железа, сернистых соединений, подогревается до температуры начала реакции и поступает в реактор синтеза метанола. По выходе из зоны катализа из газов выделяется образовавшийся метанол, что достигается охлаждением смеси, которая затем сжимается до давления синтеза и возвращается в процесс.
|
|
Технологические схемы различают аппаратурным оформлением главным образом стадии синтеза, включающей основной аппарат- колонну синтеза и теплообменник.
Расчетная схема
Для расчета материального баланса ХТС надо привести технологическую схему производства к расчетной схеме. Это делается в два этапа.
1)Не все элементы изменяют состав потока и его величину, например, теплообменник, насос и др. Для расчета материального баланса ХТС такие элементы можно исключить и будет получен сокращенный вариант ХТС, предназначенный для расчета материального баланса. На рис представлена сокращенная технологическая схема.
2) Технологические аппараты представим в виде расчетных элементов ХТС. Четыре типа расчетных элементов позволяют рассчитать материальный баланс любой ХТС.
Смеситель СМ смешивает два потока. Это происходит при соединении трубопроводов, в смесителях, в аппаратах для приготовления растворов, в адсорберах при полном поглощении компонентов одного из потоков. Смеситель имеет два входа и один выход.
|
|
Делитель из одного потока образует два потока. Это происходит при разветвлении трубопровода, в ректификационных колоннах, экстракторах, кристаллизаторах, фильтрах, сепараторах, и т.д. Делитель имеет один вход и два выхода. Различают два вида делителей – простые и линейные.
Делитель простой ДП производит разветвление потока на два, при этом составы поток не изменяются. Один из выходящих из делителя потоков составляет долю α от входного потока, другой, соответственно, долю (1- α) .
Делитель линейный ДЛ делит поток на два, но для него определен коэффициент разделения каждого компонента – доля количества i-го вещества, выходящего с одним из потоков. Например, ректификационная колонна производит разделение компонентов сложной смеси и поэтому ее можно представить как линейный делитель.
Реактор Р изменяет химический состав потока за счет протекания химической реакции. Элемент (реактор) имеет один вход и один выход. Для реактора задаются стехиометрическое уравнение реакции и степень превращения ключевого (которое в недостатке) вещества. В нашем случае реактор разделяем на два по числу протекающих реакций.
![]() |
|
|
Также расчетная схема ХТС может быть представлена в виде таблицы. Для этого пронумеруем все расчетные элементы. Для каждого расчетного элемента укажем номера элементов, из которых потоки входят в данный расчетный элемент, и номера элементов, в которые направляются потоки, выходящие из данного расчетного элемента. В каждой строчке таблицы укажем номер и наименование элемента и его связи.
Аппарат | Главный вход | Побочный вход | Первый выход | Второй выход |
1. Смеситель | 0 | 5 | 2 | - |
2. Реактор линейный | 1 | - | 3 | - |
3. Реактор линейный | 2 | - | 4 | - |
4. Делитель линейный | 3 | - | 5 | 6 |
5. Делитель простой | 4 | - | 1 | 0 |
6. Делитель линейный | 4 | - | 0 | 0 |
В реакторе 2 проходит реакцияCO2 + 3H2 = CH3OH + H20.
В реакторе 3 проходит реакция CO + H20 = CO2 + H2.
Расчет
Пересчитаем мощность по метанолу из т/год в кг/час. Получим:
Пм = 1000 т/сут = 41’666,67 кг/час.
Попробуем приблизительно оценить расход свежих газов. Для этого найдем мольный расход метанола:
Nм = Пм/M,
где Nм-мольный расход, Пм – мощность по метанолу, M – молярная масса метанола.
Nм = 41’666,67/32 = 1’302,08 кмоль/ч.
Принимаем долю метанола в метаноле-сырце 84% масс. Тогда массовый расход по метанолу-сырцу будет равен:
Gм.с = Пм/ω = 41’666,67/0,84 = 49’603,2 кг/ч.
Доля воды ω = 16%, значит расход воды в метаноле-сырце:
GН2О = Gм.сЧω = 49’603,2Ч0,16 = 7’936,5 кг/ч или N = 440,92 кмоль/ч.
В делитель 6 поступает только 80% воды, поступившей в делитель 4. Тогда в делитель 4 поступило:
NД4 = 440,92/0,8 = 551,15 кмоль/ч.
В реакторе 3 степень превращения воды принята равной 0,9. Значит в реактор 3 поступило:
NP3 = 551,15/(1-0,9) = 5’511.5 кмоль/ч воды.
В реакторе 2 степень превращения CO2 X= 0,85. Поскольку из 1 моля углекислого газа образуется 1 моль воды, следовательно можем найти число моль CO2, поступившее в реактор 2:
NP2 = 5’511,5/0,85 = 6’484.12 кмоль/ч CO2.
Не учитывая приход рециркуляционных газов, рассчитываем общую сумму молей всех газов в смесителе 1, при ССО2 = 7,52 или 0,0752:
No = 6’484,12/0,0752 = 86’225 kмоль/ч или No = 86’225’000 моль/ч.
Затем, по закону Менделеева-Клапейрона пересчитываем мольный расход в объемный расход (принимаем температуру, равной 300 оС, давление 7*106 Па).
PVO = NORT , где P = 7*106 Па, T = 573,15 K, R = 8,31 Дж/(моль•К)
VO = NORT/P = (86,225*106*8,31*573,15)/(7*106) = 58’668,4 м3/ч.
Получаем примерную оценку Vо = 58,67 тыс м3/час.
Примерный расчет:
Используя программу для расчета ХТС, проводим следующие манипуляции:
1) Вводим все присутствующие в системе вещества из базы данных: азот, метанол, вода, метан, оксид углерода, диоксид углерода, водород.
2) Вводим реакции в том же виде, в котором они написаны выше.
3) Входим во вкладку «схема». Набираем аппараты, указанные в таблице выше. Заполняем связи аппаратов так, как указано в таблице. Выбираем масштаб производства промышленный.
4) Входим во вкладку «аппараты». Корректируем все аппараты, вводя требуемые данные, большая часть которых была получена в задании. Другую часть (Vo) мы примерно оценили. Стоит уточнить только несколько вводимых величин:
Для смесителя: P = 70 ата. Vo = 58.7 тыс м3/час.
Для реактора 2: принята степень превращения 0.85
Для реактора 3: принята степень превращения 0.90
Для делителя простого: доля сдувки 0,02 (позже ее будем варьировать)
Рассчитываем систему. Получаем следующие данные (для удобства приведен только важный аппарат):
Как видно из таблицы, мы довольно сильно ошиблись в оценке Vo, поскольку выданная производительность по метанолу (17.811 т/ч) явно меньше, чем требуется (требуется 41.667 т/ч).
Приближения Vo будем выполнять позже, определив сначала оптимальную величину сдувки, просчитав схему при величине сдувки 0.3, 0.2, 0.05, 0.02, 0.01.
Приведем только таблицу со значениями производительности метанола Gм, его потерь Vп и объема рециркуляции Vц в зависимости от величины сдувки α:
Величина сдувки α | Количество продувочных газов Vп, тыс.м3/ч | Производительность метанола Gм, т/ч | Объем рециркуляции Vц, тыс.м3/ч |
0.3 | 70.926 | 29.094 | 165.493 |
0.2 | 60.969 | 33.175 | 242.783 |
0.05 | 43.046 | 40.134 | 817.883 |
0.02 | 38.309 | 41.661 | 1877.135 |
0.01 | 35.434 | 42.180 | 3507.946 |
Заметно, что большая доля сдувки приводит к значительным потерям (что следственно, выбросам) и низкой производительности метанола. Однако, выбор невысокой доли сдувки приводит к накоплению газов в системе Объем рециркуляции при малых значениях сдувки меняется очень сильно. Изобразим данные на графике:
Из графика, составленного по данным из выше указанной таблицы
Критической долей сдувки (как видно из графика) является доля 0,2, после которой начинается резкий рост объема рециркуляции. Примем долю сдувки равную 0,02 (минимальная возможная по заданию) и будем подбирать Vo.
Методом подбора, получаем вводимое значение Vo = 137.3 тыс.м3/ч.
Все величины и составы потоков, рассчитанные программой на компьютере:
Расход продувочных газов и объем рециркуляции получился, маловат, но увеличить его не удается, даже принимая минимально возможные степени превращения в реакторах. Поэтому оставляем все как есть.
Как видно из таблицы материального баланса, заданное нами Vo верно и дает результат с необходимой точностью:
Требуется 41.667 т/ч метанола, получаем 41.661 т/ч. Погрешность составляет:
Δ = {(41.667-41.661)/41.667}*100=0.014% < 0.5% (заданная погрешность в задании)
Расходный коэффициент по свежему газу:
ηг =
Или
ηг =
Кратность рециркуляции:
Выбросы газа в сдувке:
Или:
Рекомендации по экологии
Метанол является сильнейшим ЯДОМ. И представляет собой летучую бесцветную жидкость с температурой кипения 65 градусов Цельсия, с запахом подобным запаху обычного питьевого спирта. Легко воспламеняется. Пары его образуют взрывоопасные смеси. Смешивается во всех соотношениях с водой в любых пропорциях и многими органическими жидкостями. По запаху, цвету и вкусу метанол имеет сходство с этиловым спиртом, что увеличивает опасность этого яда. 30 мл выпитого метанола смертельны, известны случаи отравления с тяжелыми последствиями всего лишь 5-10 мл. метанола. Метанол является сильным и опасным для человека ядом. Он может проникнуть в организм через воду, при вздыхании воздуха, насыщенного его парами, через кожу, при мытье рук и смачивании одежды.Газовые выбросы в производстве метанола подразделяют на постоянные и периодические. К постоянным относятся отходящие газы и пары, выделяющиеся из метанола-сырца на стадии дистилляции, а так же продувочные газы из емкостей. Основными выбросами в атмосферу являются периодические, которые возникаю при остановках агрегатов, отдельных машин, аппаратов, узлов технологической линии. Из оставленных систем выбрасываются при продувке оставшиеся в них пары и газы. Основным направлением уменьшения периодических выбросов газов в окружающий бассейн является повышение надежности всех узлов системы, сведение количества остановок и пусков агрегатов до минимума, удлинение пробегов между ремонтами.Источником загрязнения биосферы в производстве метанола являются сточные воды. В них содержится до 0,3 % метанола и других кислородосодержащих соединений углерода. В основном это воды от промывки шламов и емкостей вместе с отходами со стадии очистки метанола. Практически полная очистка сточных вод достигается только при их биологической обработке. Биологическое окисление проводят в аэростенках с активным илом. Предельно допустимая концентрация метанола в сточных водах, поступающих на биохимическую очистку, до 200 мг/л. Как правило, до поступления на биологические очистные сооружения сточные воды производства метанола многократно разбавляются сточными водами других производств и хозяйственно-бытовыми водами.
Литература
1. М.М. Караваев, В.Е. Леонов, И.Г. Попов, Е.Т. Шепелев, «Производство синтетического метанола», 1984.
2. А.М. Кутепов, Т.И.Бондарев, М.Г. Беренгартен, «Общая химическая технология», 1990.
3. Методическое пособие №4604 : В.С. Бесков, В.И. Ванчурин. –М. : РХТУ им. Д. И. Менделеева, « Рекомендации по оформлению самостоятельных работ по ОХТ», 2009.
Размещено на Allbest.ru
Дата добавления: 2018-10-26; просмотров: 195; Мы поможем в написании вашей работы! |
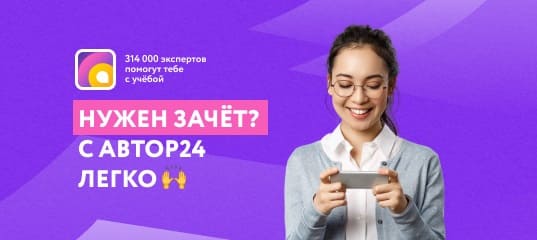
Мы поможем в написании ваших работ!