Технологическая схема процесса
Nbsp;
КУРСОВАЯ РАБОТА
по теме: «Расчет материального баланса отделения синтеза метанола под давлением 5-8 МПа»
Содержание
Задание
Технологическая схема
Технологические параметры процесса
Функциональная схема
Расчетная схема
Расчеты
Рекомендации по экологии
Литература
Задание
Рассчитать материальный баланс ХТС отделения синтеза метанола при следующих условиях:
1. | Мощность по метанолу, 100% CH3OH т/сут | 1000 |
2. | Состав свежего газа, ci0, % об. H2 CO CO2 CH4 N2 | 73.02 14.28 7.52 4.67 0.51 |
3. | Состав метанола сырца, % масс. CH3OH H2O | 84.0 16.0 |
4. | Объем рециркуляции, Vц, тыс. нм3/ч | 10-2000 |
5. | Количество продувочных газов, Vп, тыс. нм3/ч | 6-120 |
6. | Доля сдувки α | 0.02-0.05 |
7. | Степень превращения в реакторе, CO2 H2O | 0.75-0.85 0.85-0.90 |
8. | Коэффициенты разделения сепаратора в рециркуляционный поток, αi H2 CO CO2 CH3OH H2O N2 CH4 | 0.999 0.999 0.997 0.250 0.200 0.999 0.999 |
9. | Содержание в циркуляционном газе, % об. CH3OH H2O | 0.4-0.6 0.08-0.10 |
10. | Функционал в свежем газе, f | 3.0 |
Нарисовать технологическую схему отделения синтеза метанола под давлением 5-8 МПа, дать ее функциональную, структурную, операторную и расчетную формы. Описать функционирование схемы и ее технологические параметры с учетом рассчитанного материального баланса.
Задание:
1). Оценить теоретически, а затем уточнить расчетом на компьютере количество свежего газа Vo, для обеспечения заданной мощности по метанолу с точностью 0.5 %.
|
|
2). По найденной величине Vo рассчитать материальный баланс ХТС и построить зависимости мощности по метанолу Gм, количества продувочных газов Vп и объема рециркуляции Vц от доли сдувки α, значения которой проварьировать 0.3 0.2 0.05 0.02 0.01
3). Определить целесообразную величину сдувки и обсудить данные с преподавателем.
4). Для найденных Vо и выбранном α определить величины и составы всех потоков в любой точке ХТС.
5). Определить кратность циркуляции, расходный коэффициент по свежему газу, выбросы газа в сдувке ( м3/т CH3OH).
Введение
Исторически известно несколько способов получения метанола:
1) сухая перегонка древесины и лигнина;
2) термическое разложение формиатов;
3) синтез из метана через хлористый метил с последующим омылением;
4) неполное окисление метана на катализаторах или без таковых под давлением. синтез газ метанол циркуляция выброс
С этапами изучения химии метанола связаны имена величайших химиков. Впервые метанол был обнаружен еще в середине XVII века Робертом Бойлем при изучении продуктов перегонки дерева, однако в чистом виде метиловый спирт, или древесный, получаемый этим способом, был выделен только через 200 лет: тогда впервые удалось очистить его от примесей сопутствующих веществ, прежде всего уксусной кислоты и ацетона. В 1857 году Марселен Бертло получил метанол омылением хлористого метила. Процесс сухой перегонки древесины долгое время оставался, пожалуй, единственным способом производства метанола. Сейчас он полностью вытеснен каталитическим синтезом из оксида углерода и водорода. Получение метанола из синтез-газа впервые было осуществлено в Германии в 1923 году фирмой BASF. Процесс проводился под давлением 100-300 атм на оксидных цинк-хромовых катализаторах (ZnO-Cr2O3) в интервале температур 320-400єС, производительность первой промышленной установки доходила до 20 т/сут. Интересно, что в 1927 году в США был реализован промышленный синтез метанола, основанный не только на монооксиде, но и на диоксиде углерода. В настоящее время в результате развития и усовершенствования процесса получения метанола из синтез-газа используются реакторы большой мощности с производительностью до 2000 т метанола в сутки.В настоящее время основное количество метанола производится из синтез-газа, сырьем для которого главным образом является метан. Также известны схемы использования с этой целью отходов нефтепереработки, коксующихся углей.
|
|
|
|
Производство исходного газа для синтеза метанола. Сырьё для производства метанола
Технологический исходный газ для синтеза метанола получается в результате конверсии (превращения) углеводородного сырья: природного газа, синтез газа после производства ацетилена, коксового газа, жидких углеводородов (нефти, мазута, легкого каталитического крекинга) и твердого топлива (угля, сланцев).
Исходный газ для синтеза метанола можно получить почти из всех видов сырья, которые используют при получении водорода, например в процессах синтеза аммиака и гидрирования жиров. Поэтому производство метанола может базироваться на тех же сырьевых ресурсах, что и производство аммиака. Использование ого или иного вида сырья для синтеза метанола определяется ядом факторов, но прежде всего его запасами и себестоимостью в выбранной точке строительства. - В соответствии с реакцией образования метанола
СО + 2Н2↔ CH3OH
В исходном газе отношение водорода к окиси углерода должно составлять 2:1, то есть теоретически необходимо, чтобы газ содержал 66,66 объемн. % H2 и 33,34 объемн. % СО. В производственных условиях синтез метанола осуществляют по циркуляционной схеме при отношении H2 : СО в цикле выше стехиометрического. Поэтому необходимо иметь избыток водорода в исходном газе, т. е. отношение H2: CO в нем обычно поддерживают в пределах 1,5—2,25.
|
|
При содержании значительных количеств двуокиси углерода в исходном газе отношение реагирующих компонентов целесообразно выражать соотношением (H2—CO2) : (CO+CO2). Это соотношение учитывает расход водорода на реакции восстановления окиси и двуокиси углерода. В исходном газе оно должно быть несколько выше стехиометрического для обеих реакций и равно 2,15—2,25. Величина соотношения (H2—CO2) : (СО+СО2) не определяет концентрации двуокиси углерода в исходном газе. Количество СО2 может быть различным в зависимости от метода получения газа, также условий синтеза (давление, температура, состав катализатора синтеза метанола) и изменяется от 1,0 до 15,0 объемн %. Природный и попутный газы представляют наибольший интерес как с экономической точки зрения, так и с точки зрения конструктивного оформления процесса подготовки исходного газа (конверсия, очистка и компримирование). Кроме того, они содержат меньше нежелательных примесей, чем газы, полученные газификацией твердого топлива.
Состав природного газа в зависимости от месторождения различен. Основным компонентом природного газа является метан; наиболее значительно меняется содержание гомологов метана (этан, пропан, бутан) и инертных газов.
Большинство крупных производств метанола базируется на использовании природного газа. Для получения исходного газа, S углеводородное сырье подвергают конверсии различными окислителями — кислородом, водяным паром, двуокисью углерода и их смесями. В зависимости от используемых видов окислителей или их смесей различают следующие способы конверсии: паро-углекислотная при атмосферном или повышенном давлениях, паро-углекислотная с применением кислорода, высокотемпературная и паро-углекислородная газификация жидких или твердых топлив. Выбор окислителя или их комбинации определяется назначением получаемого исходного газа (для синтеза метанола на цинк-хромовом или медьсодержащем катализаторах) и технико-экономическими факторами.
В качестве сырья для производства метанола используют также синтез-газ после производства ацетилена методом окислительного пиролиза (на 1 т ацетилена обычно образуется до 10000 м3 газа). Этот газ содержит водород и окись углерода в соотношениях, близких к стехиометрическому для реакции синтеза метанола. Остаточный, метан является нежелательной примесью, поэтому до поступления в отделение синтеза газ проходит и каталитическую конверсию.
При использовании в качестве сырья для получения исходного газа твердого топлива (кокса и полукокса) последнее подвергают с газификации водяным паром. Кроме кокса, газификации могут подвергаться антрацит, сланцы, бурые угли, мазут и нефть. Процессы газификации проводят при атмосферном или при повышенном давлении. По технологическим принципам процессы газификации разделяют на циклические и непрерывные. Получение исходного газа таким способом в настоящее время устарело. Отметим лишь, что практически при любом режиме газификации отношение Н2: СО в конвертированном газе меньше теоретического. Поэтому часть газа после очистки от примесей направляют на конверсию окиси углерода водяным паром.
Коксовый газ, получаемый в процессе коксования каменных углей, содержит значительное количество метана (до 19—25%), У непредельных соединений и большое количество различных прим сей. От некоторых из них (смолы, аммиак, бензол, нафталин и др.) газ очищают на коксохимических заводах.
Технологическая схема процесса
Функциональная форма.
Основным аппаратом в синтезе метанола служит реактор — контактный аппарат, конструкция которого зависит, главным образом, от способа отвода тепла и принципа осуществления процесса синтеза. В современных технологических схемах используются реакторы трех типов:
- трубчатые реакторы, в которых катализатор размещен в трубах, через которые проходит реакционная масса, охлаждаемая водным конденсатом, кипящим в межтрубном пространстве;
- адиабатические реакторы, с несколькими слоями катализатора, в которых съем тепла и регулирование температуры обеспечивается подачей холодного газа между слоями катализатора;
- реакторы, для синтеза в трехфазной системе, в которых тепло отводится за счет циркуляции жидкости через котел-утилизатор или с помощью встроенных в реактор теплообменников.
Вследствие большого объема производства и весьма крупных капитальных затрат в производстве метанола сейчас используют все три типа технологических процессов.
В последние годы получают широкое распространение технологической схемы синтеза метанола на низкотемпературных катализаторах для понижения давления. Процесс проводят под давлением 5-10 МПа в основном на трехкомпонентных медьсодержащих катализаторах с циркуляцией газов турбоциркуляционными машинами. Для привода компрессора от паровой турбины используют пар, получаемый непосредственно на установке. Процесс производства метанола при низком давлении включает практически те же стадии, что и производство его при высоких давлениях. Однако имеются и некоторые особенности.
Исходный газ для синтеза метанола на низкотемпературных медьсодержащих катализаторах должен быть тщательно очищен от каталитических ядов (сера, хлор). В природном газе содержится 10- 300 мг/м3 сернистых соединений, а содержание их в газе для синтеза не должно превышать 0,5 мг/м3. Содержание серы при этом в свежем газе должно быть не более 0.15 мг/м3. В связи с этим представляет большой интерес схема синтеза метанола из синтез газа, отходящего из производства ацетилена, так как сернистые соединения природного газа адсорбируются растворителем ацетилена. Схема производства метанола из синтез газа компактна и высокоэффективна. Мощность производства определяется ресурсом газа и обычно составляет 100 -110 тыс. т. в год.
Синтез – газ сжимается турбокомпрессором 1, проходит тонкую очистку от паров растворителя ацетилена в угольном фильтре 2 и смешивается с циркуляционным газом. Для регулирования соотношения реагирующих компонентов в синтез газе добавляется газ с высоким содержанием водорода (12-16 % отн.), например продувочный газ из производства метанола под высоким давлением. Циркуляция газа обеспечивается центробежным компрессором 5. Циркуляционный газ через теплообменник 6 и электроподогреватель 8 поступает в шахтный реактор синтеза 9. Отвод тепла реакции производится подачей в слой катализатора холодного газа, который распределяется с помощью специально сконструированных камер смешения.
Температура газа на входе в реактор 205-225 °С, максимальная температура в слое катализатора 290 °С. Выходящий из реактора циркуляционный газ отдает тепло газу, поступающему в реактор в рекуперационных теплообменниках 6 и направляется в воздушные холодильники - конденсаторы 7. Сконденсировавшийся метанол, вода и другие побочные продукты определяются в сепараторе 3. Метанол- сырец из сборника 4 направляется на ректификацию. Циркуляционный газ из сепаратора возвращается на всасывающую линию циркуляционного компрессора 5.
Данную схему можно использовать для получения метанола и из природного газа, предварительно тщательно очистив газ от серы и подвергнув его конверсии метана. Недостатком схемы является применение турбокомпрессоров с электроприводами, что приводит к расходованию электроэнергии до 800- 900 кВт*ч/т.
Вследствие снижения температуры синтеза при низком давлении процесс осуществляется в условиях, близких к равновесию, что позволяет увеличить производительность агрегата.
Конструкция и изготовление реакторов для проведения процесса при низком давлении проще благодаря более мягким условиям синтеза. При этом применяют реакторы как шахтные, так и трубчатые. В реакторах для синтеза при низком давлении особое внимание уделяют теплосъему, так как медьсодержащие катализаторы по сравнению с цинк-хромовыми значительно более чувствительны к колебаниям температуры. В шахтных реакторах температурный режим регулируют с помощью байпасов, холодный газ вводят через специальные распределительные устройства. В трубчатых реакторах катализатор находится в трубках, охлаждаемых кипящей водой. Температуру катализатора поддерживают постоянной по всей длине реактора с помощью регуляторов давления, причем перегревы катализатора практически исключены. Выгрузка отработанного катализатора протекает тоже достаточно просто – путем снятия колосниковых решеток. Диаметр реакторов достигает 6 м при длине 8- 16 м.
Дата добавления: 2018-10-26; просмотров: 236; Мы поможем в написании вашей работы! |
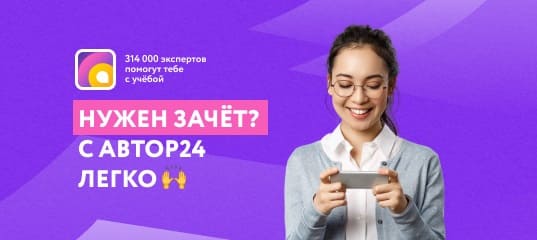
Мы поможем в написании ваших работ!