Способы обработки фасонных поверхностей.
Обрабатываемые поверхности деталей относят к фасонным, если они образованы криволинейной образующей, комбинацией прямолинейных образующих, расположенных под различными углами к оси детали, или комбинацией криволинейных и прямолинейных образующих.
Фасонные поверхности могут быть получены на токарных станках различными способами: сочетаниями поперечной и продольной подач резца относительно заготовки фасонными резцами, профиль которых соответствует профилю готовой детали; поперечной и продольной подачами резца относительно заготовки с использованием приспособлений и копирных устройств, позволяющих обработать поверхность детали по заданному профилю, позволяющим использовать достоинства различных способов для повышения точности и производительности токарной обработки фасонных поверхностей. Обрабатываемые фасонных поверхности могут быть наружным! и внутренними.
![]() |
Рис. 4.41. Обработка фасонных поверхностей по копиру:
1 — резец; 2 — рукоятка; 3 — тяга; 4 — палец; 5 — копир
Фасонные поверхности, в том числе hi длинных деталях, обрабатывают остроко- нечными быстрорежущими и твердосплавными проходными резцами в том случае, если заданный профиль получает ся с помощью шаблона, копира, приспособлений и т. п. При обработке галтеле и канавок радиусом 20мм на стальных и чугунных деталях применяют резцы, режущая часть которых выполнен! по профилю обрабатываемой галтел или канавки . При обработке галтелей и канавок 20 мм режущую часть резцов выполняют с радиусом скругления, равным (1,5—2) R. Обработку в этом случае ведут продольной и поперечной подачами.
|
|
Для повышения производительное?! обработки фасонных поверхностей сложного профиля применяют фасонные резцы , рабочая част которых может быть выполнена из быстро режущей стали или твердого сплава а державка из конструкционной стали которая соединяется с режущей частью
Фасонные резцы: а — цельный, б — с механическим креплением режущей части, в — дисковый
Обработка проходными резцами.
Обработка фасонной поверхности детали может быть выполнена при одновременной продольной поперечной подаче остроконечного проходного резца. При выборе резца следует обратить внимание на то, чтобыформа его вершины и расположение режущих кромок позволяли обработать фасонную поверхность детали с заданными углами наклона и радиусами.Для приобретения навыка перемещения вручную резца по заданной траектории при одновременной продольной и поперечной подаче следует предварительно (перед обработкой фасонной детали) выполнить несколько упражнений, что позволит освоиться с особенностями управления станком при фасонной обработке. Для этого в патроне или в центрах закрепляют готовую деталь с фасонной поверхностью сложного профиля. Перемещая суппорт координированным вращением
|
|
Обработка фасонными резцами.
Для обработки галтелей, резьбы и других фасонных поверхностей применяют фасонные резцы (рис. 9.6). Профиль режущей кромки этих резцов полностью совпадает с профилем обрабатываемой поверхности и поэтому передняя поверхность резца должна устанавливаться точно на линии центров станка. Для сохранения обрабатываемого профиля фасонные резцы затачивают по передней поверхности. Это нужно учитывать при установке резцов. В горизонтальной плоскости резец должен быть перпендикулярен к линии центров станка, правильность установки проверяют угольником, который одним катетом прикладывают к цилиндрической поверхности детали, а другим — к боковой поверхности резца. При этом между угольником и резцом должен быть равномерный просвет.
Применение призматических и круглых фасонных резцов позволяет обрабатывать фасонные поверхности сложного профиля. Передней поверхностью призматического фасонного резца служит торец призмы, а задний угол а образуется наклонным положением резца в державке.
|
|
Для сохранения обрабатываемого профиля фасонные резцы затачивают по передней поверхности. Это нужно учитывать при установке резцов. В горизонтальной плоскости резец должен быть перпендикулярен к линии центров станка, правильность установки проверяют угольником, который одним катетом прикладывают к цилиндрической поверхности детали, а другим — к боковой поверхности резца. При этом между угольником и резцом должен быть равномерный просвет.
4.Контроль фасонных поверхностей.
Контроль фасонных поверхностей выполняют шаблоном или совмещением увеличенного профиля фасонной поверхности детали с ее проецируемым чертежным брожением на экране. Причины отклонения фактического профиля детали: внешность профиля резца или погрешность установки, а также деформации заготовки, которые вызваны чрезмерно большие подачами.
8Íàðåçàíèå ðåçüáû.
1.Общие сведения о резьбе.
![]() |
Вершина резца при перемещении с постоянной скоростью подачи вдоль вращающейся заготовки, врезаясь, оставляет на ее поверхности винтовую линию (рис. 4.42).
|
|
Рис. 4.42. Схема нарезания наружной резьбы:
а — схема движения инструмента и заготовки; б — нарезание однозаходной резьбы резцом
Нарезание на резьбы резцами.
На токарно-винторезных станках наиболее широко применяют метод нарезания наружной и внутренней резьб резцами (рис. 4.45). Резьбонарезные резцы бывают стержневые, призматические и круглые; их геометрические параметры не отличаются от геометрических параметров фасонных резцов.
![]() |
Резьбы треугольного профиля нарезают резцами с углом в плане при вершине е = 60° ± 10' для метрической резьбы и е = 55° ± 10' для дюймовой резьбы. Учитывая погрешности перемещения суппорта, которые могут привести к увеличению угла резьбы, иногда применяют резцы с углом е = 59°30'. Вершина резца может быть скругленной или с фаской (в соответствии с формой впадины нарезаемой резьбы).
Рис. 4.45. Упрощенная кинематическая схема нарезания резьбы на токарно-винторезном станке:
1 — заготовка; 2 — суппорт; 3 — ходовой винт; М — электродвигатель; d\, d2 — диаметры шкивов; Р — шаг ходового винта; z1..., z10 — шестерни; п — частота вращения заготовки; Ds — направление движения подачи
Резьбонарезные резцы оснащают пластинами из быстрорежущей стали и твердых сплавов. Предварительно деталь обтачивают таким образом, чтобы ее наружный диаметр был меньше наружного диаметра нарезаемой резьбы. Для метрической резьбы диаметром до 30 мм эта разница ориентировочно составляет 0,14... 0,28 мм, диаметром до 48 мм — 0,17...0,34 мм, диаметром до 80 мм — 0,2...0,4 мм. Уменьшение диаметра заготовки обусловлено тем, что при нарезании резьбы материал заготовки деформируется и в результате этого наружный диаметр резьбы увеличивается.
На токарно-винторезных станках резьбу нарезают резцами за несколько проходов. После каждого прохода резец отводят в исходное положение. По нониусу ходового винта поперечного движения подачи суппорта устанавливают требуемую глубину резания и повторяют проход. При нарезании резьбы с шагом до 2 мм подача составляет 0,05...0,2 мм на один проход. Если резьбу нарезать одновременно двумя режущими кромками, то образующаяся при этом стружка спутывается и ухудшает качество поверхности резьбы. Поэтому перед рабочим проходом резец следует смещать на 0,1 ...0,15 мм поочередно вправо или влево, используя перемещение верхнего суппорта, в результате чего обработка ведется только одной режущей кромкой. Число черновых проходов — 3... 6, а чистовых — 3.
Нарезание плашками и метчиками.
Для нарезания наружной резьбы на винтах, болтах, шпильках и других деталях применяют плашки. Участок детали, на котором необходимо нарезать резьбу плашкой, предварительно обрабатывают. Диаметр обработанной поверхности должен быть несколько меньше наружного диаметра резьбы. Для метрической резьбы диаметром 6... 10 мм эта разница составляет 0,1...0,2 мм, диаметром 11... ... 18 мм — 0,12...0,24 мм, диаметром 20...30 мм — 0,14...0,28 мм. Для образования захода резьбы на торце детали необходимо снять фаску, соответствующую высоте профиля резьбы.
Плашку устанавливают в плашкодержатель (патрон), который закрепляют в пиноли задней бабки или гнезде револьверной головки. Скорость резания v при нарезании резьбы плашками для стальных заготовок 3...4 м/мин, для чугунных — 2...3 м/мин и для латунных — 10... 15 м/мин.
Накатывание резьбы.
Обработка резьбы накатыванием осуществляется копированием профиля накатного инструмента за счет его вдавливания в металл заготовки. На токарных, токарно-револьверных станках и автоматах производят накатывание резьбы диаметром от 5 до 25 мм одним роликом. Резьбу накатывают при вращении заготовки / в патроне или цанге с поступательным перемещением суппорта станка вместе с накатником 3, в который вмонтирован ролик 2. При этом необходимо следить за деформацией заготовки под действием односторонней радиальной силы.
Резьбонакатные головки по принципу работы не отличаются от резьбонарезных головок. Накатывание резьбы производится, как правило, при самозатягивании головки, поэтому осевая подача инструмента на заготовку необходима только в начальный период, пока ролики не захватят заготовку. При накатывании поверхность резьбы получается с уплотненными слоями и без микронеровностей, характерных для обработки резанием, что повышает прочность резьбы детали. Резьбы можно накатывать на заготовках из различных материалов, относительное удлинение которых 6^12%. При накатывании резьб рекомендуется применять смазочноохлаждающие жидкости (эмульсию или масло).
Рис. 10.25. Схема накатывания резьбы роликом
Для получения резьбы способом пластической деформации на внутренней Поверхности применяют раскатники (рис. 10.27). Раскатчик имеет заборную часть с конической резьбой длиной /,=ЗР для глухих и /1=(10-ь20)Р для сквозных отверстий. Калибрующая часть выполнена с цилиндрической резьбой длиной /г = (5ч-~8)Р- По всей рабочей части раскатника выполнена огранка К = 0,2-=-0,6 мм для уменьшения сил трения. В процессе работы раскатник вращается относительно детали с принудительной подачей вдоль оси.
![]() |
Контроль резьбы.
Контроль резьбы. Шаг резьбы измеряют резьбовым шаблоном, представляющим собой пластину 2 (рис. 4.46), на которой нанесены зубцы с шагом резьбы, обозначаемым на плоскости шаблона. Набор шаблонов для метрической или дюймовой резьбы скрепляется в кассету /. Резьбовыми шаблонами определяют только шаг резьбы.
Правильность выполненной на детали внутренней и наружной резьбы комплексно оценивают с помощью резьбовых калибров (рис. 4.47). Резьбовые калибры разделяют на проходные, имеющие полный профиль резьбы и являющиеся как бы прототипом детали резьбового соединения, и непроходные, контролирующие только средний диаметр резьбы и имеющие укороченный профиль.
![]() |
Рис. 4.46. Резьбовой шаблон: 1 — кассета; 2 — пластина
Для измерения наружного, среднего, внутреннего диаметров и шага резьбы применяют резьбовые микрометры (рис. 4.48). Резьбовой микрометр имеет в шпинделе и пятке посадочные отверстия, в которые устанавливают комплекты сменных вставок, соответствующие измеряемым элементам резьбы. Для удобства измерений резьбовой микрометр закрепляют в стойке, а затем настраивают по шаблону или эталону.
Перед контролем проверяемые детали необходимо очистить от стружки и грязи. В процессе контроля следует осторожно обращаться с калибрами, чтобы на их рабочей резьбовой поверхности не появились забоины и царапины.
9 Îçíàêîìëåíèå ñ óñòðîéñòâîì ôðåçåðíûõ ñòàíêîâ.
1. Понятие фрезерования. Виды работ, выполняемые на фрезерных станках
Фрезерование- это процесс обрапботки деталей путем снятия стружки с помощью инструмента (фрез) на фрезерных станках
2.Основные типы фрезерных станков и их обозначение.
На машиностроительных предприятиях фрезерные работы выполняют на консольно-фрезерных, вертикально-фрезерных с кресловым столом, фрезерных непрерывного действия, копировально-фрезерных, шпоночнофрезерных специальных и специализированных станках. Наиболее универсальными и широко распространенными учебных мастерских техникумов являются консольно-фрезерные станки, которые в зависимости от расположен шпинделя делятся на: горизонталь; фрезерные (с неповоротным столе моделей 6М80Г, 6Р81Г, 6Р82Г; горизонтально-фрезерные поворотным столом (универсальны. 6Н81, 6Р82, 6Р830; вертикально-фрезерные 6М10, 6Р12, 6Р13 ,широкоуниверсальные 6П80Ш, 6Р810. -6Р82Ш.
3.Устройство и основные узлы фрезерных станков.
Станина установленная на основании станка, служит для крепления узлов и механизмов станка. Некоторые узлы станка, такие, как коробка скоростей, шпиндель, механизм подачи движения коробке подач, расположены внутри станины, другие узлы станка — консоль, стол, хобот (у горизонтально-фрезерных станков), насос ля подачи охлаждающей жидкости — находятся на наружных поверхностях станины. На передней стенке станины имеются вертикальные направляющие ля консоли, выполненные в виде ласточкина хвоста, а наверху — горизонтальные направляющие для хобота. Консольно-фрезерные станки имеют отдельные двигатели для привода коробки скоростей и коробки подач. Хобот 7 имеется у горизонтально- и вертикально-фрезерных станков и служит для правильной установки и поддержки фрезерной оправки. Хобот установлен в горизонтальных направляющих на верхней части станины и может быть закреплен с различным вылетом. Для увеличения жесткости при обработке тяжелых заготовок и при больших сечениях стружки применяют поддержки, которые связывают хобот с консолью.
Консоль 3 представляет собой жесткую чугунную отливку, установленную на вертикальных направляющих станины. Снизу она поддерживается стойкой, в которую вставлен телескопический винт подъема и опускания консоли.
Салазки 4 являются промежуточным звеном между консолью и столом станка..
Стол 5 по направляющим салазок перемещается в продольном направлении. На столе укрепляют заготовки, зажимные, делительные и другие приспособления. Для этой цели рабочая поверхность стола имеет продольные Т-образные пазы..
Шпиндель 6, получающий движение от коробки скоростей, служит для вращения режущего инструмента. Передний конец шпинделя имеет внутренний конус, в который вставляется фрезерная оправка с фрезой или непосредственно хвостовик торцовой фрезы.
Коробка скоростей, расположенная в станине 2 станка, предназначена для передачи вращения от электродвигателя шпинделю станка и изменения частоты вращения последнего в соответствии с требуемой скоростью главного движения резания. Частота вращения шпинделя изменяется путем переключения подвижных зубчатых колес и блоков, расположенных на нескольких валах коробки скоростей и шпинделе, а также упругих муфт, включающих ту или иную пару зубчатых колес.
![]() |
Хобот 7 с серьгами 8 служит для поддержания оправки с закрепленной на ней фрезой. Вылет хобота на требуемую длину осуществляют поворотом рукоятки торцового ключа. Для установки в шпиндель станка оправки с фрезой серьгу снимают с направляющих хобота.
Вертикальный консольно-фрезерный станок в отличие от горизонтального имеет вертикально расположенный шпиндель с поворотной головкой 9, которая может поворачиваться в вертикальной плоскости на угол 45с в обе стороны. Назначение узлов и органов управления такое как и у горизонтально-фрезерных ста ков. Основной отличительной особенностью этих станков является отсутствие хобота.
Òåìà 10: Ôðåçåðîâàíèå ïëîñêèõ ïîâåðõíîñòåé.
1. Инструмент и оборудование, применяемое при фрезеровании плоских поверхностей.
Большинство деталей имеют поверхности в форме плоскостей, например направляющие станины станка, поверхность основания тисков, контрольные и разметочные плиты, поверхности установочных угольников, грани болтов и гаек, квадраты хвостовиков инструментов. Фрезерование плоских поверхностей можно производить главным образом цилиндрическими фрезами на горизонтально-фрезерных станках, а торцовыми и концевыми фрезами как на горизонтально, так и вертикально-фрезерных станках .
Фрезерование плоскостей производят в такой последовательности: подводят заготовку под вращающуюся фрезу до легкого касания, затем отводят из-под фрезы, выключают шпиндель станка, устанавливают лимб вертикальной подачи (при фрезеровании плоской поверхности) или поперечной подачи (при фрезеровании плоской торцовой поверхности) на глубину фрезерования, включают шпиндель станка и перемещают вручную стол с заготовкой до касания с фрезой, после чего включают продольную подачу стола.
При обработке цилиндрическими фрезами длина фрезы должна на 10...15 мм перекрывать требуемую ширину обработки. Диаметр фрезы выбирают в зависимости от ширины фрезерования и глубины резания / (мм).
|
Рис.Фезерование плоских поверхностей торцовой фрезой
Наклонной плоской поверхностьюназывается плоская поверхность, расположенная под углом к горизонтали. Скосом называют короткую наклонную плоскость. Различные способы фрезерования наклонных плоскостей и скосов показаны на рис.
Фрезерование наклонной плоской поверхности с поворотом заготовки можно выполнять как на горизонтально, так и на вертикально-фрезерных станках, применяя универсальные машинные тиски, угловые плиты или специальные приспособления и прихваты.
Схемы фрезерования наклонных поверхностей и скосов:
а, б—на горизонтально-фрезерном; в—на вертикально-фрезерном станке с поворотом заготовки; г, д—, на вертикально-фрезерном станке с поворотом" шпинделя; е—на горизонтально-фрезерном станке угловой фрезой.
Òåìà 11: Ôðåçåðîâàíèå óñòóïîâ, ïàçîâ, êàíàâîê.
1.Особенности фрезерования уступов и канавок
В деталях машин и приборов встречаются поверхности, называемые уступами и пазами. Пазы могут быть прямоугольными и фасонными, сквозными и замкнутыми. Для обработки прямоугольных, фасонных и сквозных пазов и уступов на горизонтально-фрезерных станках применяют различные фрезы. Для обработки замкнутых пазов, шпоночных канавок и других малодоступных поверхностей на горизонтально- и вертикально-фрезерных станках применяют концевые..фрезы.
На рис. показаны наиболее часто встречающиеся дисковые фрезы. Эти фрезы крепят на оправки фрезерных станков аналогично цилиндрическим. Дисковые фреза больших размеров в целях экономя быстрорежущей стали изготовляются сборными со вставными ножами. Фрезерование уступовдисковым фрезами можно выполнить различий ми приемами: каждый уступ фрезеруется одной трехсторонней фрезой; оба уступа одновременно фрезеруют набором из двум дисковых фрез точно одинакового диаметра . В этом случае чтобы получить заданный размер между уступами, на оправку между фреза, ми устанавливают соответствуют» промежуточные кольца или фрезеруют в двухпозиционном приспособлении, вращающемся на 180° . После фрезерования первого уступа (1-я позиция) приспособление с закрепленной в нем заготовкой поворачивают и ставят во 2-ю позицию для фрезерования второго уступа.
Сквозные прямоугольные пазы чаще всего фрезеруют дисковыми трехсторонними фрезами (рис. 5.23, а), дисковыми пазовыми или концевыми фрезами (рис. 5.23, б). При фрезеровании точных пазов ширина дисковой фрезы (диаметр концевой фрезы) должна быть меньше ширины паза, а фрезерование на заданный размер производят за несколько проходов. Обработка пазов концевыми фрезами требует правильного выбора направления вращения шпинделя станка относительно винтовых канавок фрез. Оно должно быть взаимно противоположным.
Фрезерование замкнутых пазов производят на вертикально-фрезерных станках концевыми фрезами (рис. 5.23, г). Диаметр фрез следует принимать на 1... 2 мм меньше ширины паза. Врезание на заданную глубину резания осуществляют перемещением стола с заготовкой в продольном и вертикальном направлениях, затем включают продольное движение подачи стола и фрезеруют паз на необходимую длину с последующими чистовыми проходами по боковым сторонам паза.
Криволинейные пазы фрезеруют за один рабочий ход на полную их глубину. Соответственно этому условию назначают результирующее движение подачи, равное сумме векторов поперечного и продольного движения подач. Для уменьшения врезания в местах изменений направлений пазов необходимо вести обработку фрезами с минимальными вылетами и уменьшать скорости подачи.
Фрезерование пазов специальных профилей — Т-образных, типа «ласточкин хвост» — осуществляют на вертикально- или продольно-фрезерных станках за три (Т-образные пазы) или два (пазы типа «ласточкин хвост») перехода. Учитывая неблагоприятные условия работы Т-образных и одноугловых фрез, используемых при выполнении указанных операций, подача на зуб S. не должна превышать 0,03 мм/зуб; скорость резания — 20...25 м/мин.
Рис. 5.23. Схемы фрезерования прямоугольных и фасонных пазов:
а — дисковые трехсторонние фрезы; б — дисковые пазовые или концевые фрезы; г — концевые фрезы; Д. — направление вращения фрезы
Отрезание заготовок
Для отрезания или разрезания заготовок на части применяют тонкие дисковые фрезы, которые называются отрезными. Зубья этих фрез расположены только по цилиндрической части. Для уменьшения трения фрезы о стенки прореза (пропила) диски фрез имеют утонение к центру на угол Фрезы могут быть с мелкими, средними (нормальными) и крупными) зубьями. Фрезы с мелкими и средними зубьями применяют для резания тонких заготовок, труб, прорезания шлицев; фрезы с крупными зубьями — для прорезания глубоких и узких пазов и для отрезных работ.
|
|
|
Заготовку закрепляют в машинных тисках, расположенных параллельно оси шпинделя станка, так чтобы зажимные губки были направлены вдоль фрезерной оправки. Чтобы заготовку не выр из тисков, часто применяют вращение фрезы по подаче (рис. 4.40, а). В этом случае сила фрезерования прижимает заготовку к тискам. Если фрезерный станок изношен и механизм продольного движения подачи стола имеет мертвый ход (люфт), лучше применять фрезерование против подачи.
Òåìà 12: Ôðåçåðîâàíèå ôàñîííûõ ïîâåðõíîñòåé.
1.Способы фрезерования профильных пазов и канавок.
Многие детали машин имеют не только прямолинейные и плоские поверхности, но и различные криволинейные контуры, состоящие из отрезков прямых, дуг окружностей различного диаметра и других кривых. Криволинейные контуры можно фрезеровать на вертикально-фрезерных станках: по разметке комбинированием продольной и поперечной ручной подач; по разметке с помощью поворотного круглого стола; по копиру в специальных приспособлениях.
2.Фрезерование по разметке комбинированием продольной и поперечной ручной подач
Фрезерование комбинированием ручных подач заключается в том, что предварительно размеченную заготовку, а при необходимости с просверленными отверстиями для крепления и ввода инструмента закрепляют одним из разобранных на предыдущих занятиях методов на столе фрезерного станка. Перемещая ручной подачей стол одновременно в продольном и поперечном направлениях, подводят заготовку под вращающуюся концевую фрезу так, чтобы фреза снимала слой металла в соответствии с размеченным криволинейным контуром. Заготовку перед фрезерованием предварительно разметить и просверлить отверстия — центральное диаметром 30 мм для крепления ее на круглом столе и четыре вспомогательных диаметром 32 мм для ввода концевой фрезы. Обработку проводят на вертикально-фрезерном станке с применением поворотного круглого стола, при этом выполняют приемы, рассмотренные на занятиях 35...38.
Процесс обработки состоит из двух самостоятельных операций: фрезерования наружных прямолинейных и криволинейных (радиусных) участков и фрезерования внутренних замкнутых криволинейных пазов. Выбрать концевую фрезу.
13 Фрезерования профильных пазов и канавок
1.Инструмент для фрезерования
Шпоночные пазы фрезеруют пазовыми дисковыми фрезами, пазовыми затылованными (ГОСТ 8543—71), шпоночными (ГОСТ 9140—78) и насадными фрезами. Пазовая или шпоночная фреза должна быть установлена в диаметральной плоскости заготовки.
Фрезерование открытых шпоночных пазов с выходом канавки по окружности, радиус которой равен радиусу фрезы, производят дисковыми фрезами. Пазы, в которых не допускается выход канавки по радиусу окружности, фрезеруют концевыми или шпоночными фрезами.
Гнезда под сегментные шпонки фрезеруют хвостовыми и насадными фрезами на горизонтально- и вертикально-фрезерных станках. Направление движения подачи — только к центру вала (рис. 5.25, а).
![]() |
Для получения точных по ширине пазов обработку ведут на специальных шпоночно-фрезерных станках с маятниковой подачей (рис. 5.25, б). При этом способе фреза врезается на 0,2...0,4 мм и фрезерует паз по всей длине, затем опять врезается на ту же глубину и фрезерует паз на всю длину, но в другом направлении.
Рис. 5.25. Фрезерование шпоночных пазов:
а — дисковыми фрезами с вертикальным или поперечным движением подачи; б — шпоночными фрезами с маятниковым движением подачи; Д. — направление движения резания; h — глубина фрезерования; /)ф — диаметр концевой фрезы; / — припуск, снимаемый за один проход инструмента
Для фрезерования шпоночных пазов рекомендуется применять шпоночные фрезы с 51= 0,02...0,04 мм/зуб при скорости резания v = 15... 20 м/мин; дисковые пазовые фрезы с S: = 0,03...0,06 мм/зуб при скорости резания v = 25...40 м/мин.
Угловые фрезы также используют при фрезеровании угловых канавок на конической поверхности. Устанавливают фрезы относительно диаметральной плоскости заготовки так же, как и при фрезеровании угловых канавок на цилиндрической поверхности.
![]() |
Рис. 5.26. Схема установок фрез при фрезеровании канавок режущих
инструментов:а, б, в, г — переходы при наладке станка; D — диаметр заготовки; И — глубина фрезерования; х — смещение торца фрезы относительно осевой плоскости заготовки
На вертикально-фрезерных станках концевыми фрезами обрабатывают различные уступы, плоскости, а также сквозные и закрытые пазы. Концевые фрезы в отличие от торцовых, цилиндрических и дисковых имеют цилиндрические или конические хвостовики. Для фрезерования шпоночных пазов на валах машин применяют концевые фрезы, которые имеют точный диаметр, равный ширине паза, и два три зуба, сходящиеся к центру в одну точку (без центрового отверстия). Концевые фрезы крепят на шпинделе станка, в патроне, или непосредственно в шпиндель.
Òåìà 14: Ôðåçåðîâàíèå ñ ïîìîùüþ äåëèòåëüíîé ãîëîâêè.
1.Виды делительных головок и их устройства.
Делительные головки являются важнейшими принадлежностями консольно-фрезерных станков, которые расширяют их технологические возможности. Делительные головки используют при изготовлении различных инструментов (фрез, разверток, метчиков, зенкеров), фрезеровании зубчатых колес, пазов и шлицев, зубьев на торцах (зубчатых муфт), нормализованных деталей машин (головок болтов, граней гаек) и других деталей.
Различают делительные головки для непосредственного деления (делительные приспособления), оптические делительные головки и универсальные делительные головки. Универсальные делительные головки делятся на лимбовые и безлимбовые. Наиболее распространены, в том числе и в учебных мастерских техникумов, лимбовые головки, которые пригодны для выполнения всех видов деления.Делительная головка устроена следующим образом на чугунном основании 20 со стяжными дугами 9 установлен поворотный корпус 10, который можно поворачивать вокруг своей оси на угол в пределах 7...10° вниз и О...1ОО0 вверх. Угол поворота устанавливают по шкале с нониусом 12. В корпусе расположен шпиндель со сквозным отверстием, на переднем конце которого можно закрепить центр 21, либо поводковый или кулачковый патрон и диск 8 (лимб) для непосредственного деления.
![]() |
Некоторые конструкции делительных головок на диске непосредственного деления имеют три делительных круга с 24, 30 и 36 отверстиями, что позволяет производить непосредственное деление на 2, 3, 4, 6, 8, 10, 12, 15, 18, 24, 30 и 36 частей. На заднем конце шпинделя устанавливают оправку для сменных зубчатых колес. В средней части шпинделя расположено червячное колесо, которое при необходимости стопорится зажимом .
Òåìà 15: Îçíàêîìëåíèå ñ ðàáîòîé øëèôîâàëüíûõ ñòàíêîâ.
1.Процесс шлифования. Виды шлифования.
Шлифование — один из окончательных видов обработки металлов как в сыром, так и в закаленном состоянии. Шлифованием можно обрабатывать как простые цилиндрические валики и отверстия, плоские поверхности, а также сложные профильные поверхности, например зубчатые колеса, шлицевые валы, резьбы, червяки, направляющие станин и т. п.
При круглом наружном шлифовании с продольным движением подачи необходимы следующие движения: вращение 1 шлифовального круга — главное движение резания; вращение 2 обрабатываемой заготовки вокруг своей оси — круговая подача заготовки; продольное возвратно-поступательное движение 3 заготовки (или в некоторых моделях станков—шлифовального круга) вдоль своей оси — продольное движение подачи;
![]() |
Поперечное перемещение 4 шлифовального круга к заготовке (или заготовки к шлифовальному кругу) — поперечное движение подачи или подача на глубину шлифования. При шлифовании с продольным движением подачи поперечную подачу 4 осуществляют периодически в конце каждого двойного или одинарного хода стола станка. В настоящее время получил большое распространение способ глубинного шлифования или способ шлифования установленным кругом, когда весь припуск удаляют за один проход при небольшой продольной подаче. При глубинном шлифовании подачу осуществляют только в одну сторону. После того как очередная заготовка прошлифована, стол возвращают в исходное положение для установки следующей заготовки. При этом способе положение шлифовальной бабки остается неизменным (до очередной правки шлифовального круга) и обеспечивается постоянство размеров
Работы, выполняемые шлифовщиком.
Шлифовщик должен уметь шлифовать наружные поверхности простых устойчивых заготовок из высококачественных марок сталей круглого профиля по 11-му квалитету (4-й класс точности), с параметрами шероховатости поверхности в пределах от Rz = 2Q мкм до Ra = 0,8 мкм на плоскошлифовальных, круглошлифовальных и бесцентровошлифовальных станках с соблюдением последовательности обработки и режимов резания по технологической карте с правкой шлифовальных кругов; шлифовать и доводить заготовки из высококачественных сталей круглого профиля по 8...9-му квалитетам (3-й класс точности) с параметрами шероховатости в пределах Rа = 1,25...0,4 мкм на специализированных автоматических и полуавтоматических станках, налаженных для обработки определенных заготовок; выполнять установку и выверку заготовок на станке и в приспособлении;
ТБ при работе на шлифовальных станках
При работе на шлифовальном станке кроме общих правил техники безопасности, необходимо соблюдать следующие меры предосторожности;
Не устанавливать на станок неиспытанный круг. Все круги диаметром более 150 мм испытывают на прочность путем вращения на специальной установке при скорости, в 1,5 раза превышающей установленную окружную рабочую скорость. После испытания на прочность на круг наносят специальную отметку (маркировку). Круг, установленный на станок, должен быть подвергнут кратковременному (не менее 5 мин) вращению вхолостую с рабочей скоростью, при этом в опасной зоне не должны находиться люди. Наличие защитного кожуха дл( круга обязательно.
Òåìà 16: Îçíàêîìëåíèå ñ ðàáîòîé ñòðîãàëüíûõ ñòàíêîâ.
1.Назначения строгания.
Строгание применяют для обработки плоских и несложных фасонных поверхностей с прямолинейными образующими в единичном, опытном и мелкосерийном производстве. Некоторые примеры работ, выполняемых на строгальных станках: строгание горизонтальной плоской поверхности при поперечной подаче стола; строгание вертикальной плоской поверхности при вертикальной подаче суппорта ; строгание пазов и канавок (широкие пазы выполняют последовательно за несколько проходов резца); строгание Т-образных пазов за три приема: обработка средней части паза, обработка левой части, обработка правой части паза; строгание наклонных плоских поверхностей при установке суппорта под углом 45°; строгание фасонных поверхностей. Строгание производят на поперечно-продольно-строгальных станках.
2. Строгальные станки
На поперечно-строгальных станках, предназначенных для обработки заготовок длиной до 1 м, движение резания сообщается резцу. Резание производят при прямолинейном поступательном движении резца, закрепленного в ползуне станка, а возвратное! движение является холостым ходом. Обрабатываемую заготовку закрепляют на столе станка и сообщают движение подачи (в конце холостого хода) в направлении, перпендикулярном направлению движения резания.
В учебных мастерских используют главным образом поперечно-строгальные станки, как выпускаемые в настоящее время заводами, так и снятые с производства, с кривошипно-кулисном; механизмами (моделей 736, 7А35, 7E35 и др.) и гидрофицированные, с бесступенчатым регулированием скорости ползуна (моделей 7М36, 7ДЯ и др.).
На рис. показан общий вид одного из наиболее распространенных поперечно-строгальных станков модели 736. Основной узел станка — станина 9, по горизонтальным направляющим 8 которой перемещается ползун/ с суппортом 5. По вертикальным направляющим 3 станины передвигается поперечина W, а по направляющим поперечины — стол 2, который дли большей устойчивости поддерживается стойкой. Неподвижный упор б, установленный на станине, с помощью храпового механизма осуществляет автоматическую подачу резца. Обрабатываемую заготовку или приспособление для ее крепления устанавливают на столе, для чего на горизонтальной и вертикальной опорных поверхностях стола предусмотрены Т-образные пазы. Резец 4 закреплен в резцедержателе, установленном на суппорте 5. Главное рабочее движение (прямолинейное возвратно-поступательное) сообщают ползуну с резцом.
На рис.показана кинематическая схема станка с кривошипно-кулисным механизмом. От электродвигателя вращение через коробку скоростей передается зубчатому колесу г = 25, сцепляющемуся с кулисным колесом z= 120 (на схеме повернуто на 90°), которое сообщает движение кулисе. На кулисном колесе, несущем кривошипный палец, насажен кулисный камень, входящий в прорезь кулисы. Верхний конец кулисы шарнирно связан с полушкой, закрепленной в ползуне станка. При вращении кулисного колеса кулиса под действием кулисного камня совершает возвратно-поступательное касательное движение.
![]() |
Длина хода ползуна регулируется путем изменения радиуса окружности, которую описывает центр кривошипного пальца. На рис. изображен механизм регулирования радиуса кривошипа. Кривошипный палец 4, вставленный в кулисный камень 6, выполнен заодно с ползушкой, которая может передвигаться в радиально расположенных направляющих кулисного колеса. Перемещение пальца с ползушкой, т. е. изменение радиуса окружности вращения пальца, осуществляется при вращении винта 5. Этот винт приводится во вращение вручную с помощью рукоятки / и конических зубчатых колес 2 и 3 (г = 17). С увеличением радиуса окружности вращения пальца 4 возрастает угол качания кулисы у, а следовательно, и длина хода ползуна. При кривошипно-кулисном приводе ползун имеет неравномерную скорость движения. В конце хода происходит спад скорости до нуля и реверсирование, а в середине хода при вертикальном положении кулисы скорости рабочего и холостого ходов имеют максимальные значения. Средняя скорость рабочего хода (скорость
Òåìà 17: Îçíàêîìëåíèå ñ ðàáîòîé ñòàíêîâ ñ ×ÏÓ è ïðîãðàììíûìè óñòðîéñòâàìè.
1.Общие сведения о станках с ЧПУ и ПУ.
Общие сведения о станках с программным управлением и их классификация. При ручном управлении станком необходимую последовательность приемов и команд задает рабочий, который, предварительно изучив чертеж детали. и другую техническую документацию, составляет программу работ, обрабатывает деталь, измеряет ее и, при необходимости, устраняет допущенные неточности.
При автоматическом управлении станком необходимая последовательность команд задается программоносителем, который может быть изготовлен в виде материального аналога отдельных поверхностей обрабатываемой детали (копиров, шаблонов, кулачков, упоров и др.); или все команды записываются на перфоленту, магнитную ленту, магнитный диск.
Наибольшей быстротой и гибкостью переналадки обладают станки с программным управлением.
Станки с ЧПУ имеют устройства для считывания перфоленты. На перфоленте нанесены отверстия, которые в процессе движения ленты создают соответствующие электрические сигналы, задающие в кодированном виде управляющую программу различным органам станка. Эта программа запоминается в памяти устройства ЧПУ. Структурная схема устройства ЧПУ станком показана на рис.
Классификация (обозначение) моделей станков с ЧПУ
По принципу смены инструмента станки с ЧПУ делятся на три группы: с ручной сменой; с автоматической сменой в револьверной головке; с автоматической сменой в магазине.
По принципу смены заготовок станки с ЧПУ подразделяются на станки с ручной и автоматической, посредством манипуляторов или роботов, сменой заготовок. При наличии пристаночных накопителей заготовок станки могут эксплуатироваться в течение длительного времени без участия оператора.
2.Устройство станков с ЧПУ и ПУ. Инструменты и приспособления.
При составлении технологом-программистом технологического процесса обработки детали, описании и программировании движений отдельных органов станков с ЧПУ принята стандартная система осей координат, относительно которых указывают направления и величины перемещений рабочих органов. Исходной осью (ось Z) является ось рабочего шпинделя и направление, параллельное ей. Положительным (со знаком «плюс») принято считать направление перемещения элемента станка, при котором инструмент или заготовка отходят друг от друга. Ось X всегда горизонтальная и перпендикулярна оси Z. Ось Y перпендикулярна плоскости XZ. Схема осей координат токарного станка приведена на рис.
По числу программируемых движений или координат станки с ЧПУ могут быть: 2-координатные, например токарные — с продольной и поперечной подачами суппорта или сверлильные — с движением шпинделя на глубину сверления и перемещением стола для обработки следующего отверстия; 3-ко-ординатные, например фрезерные — с перемещением стола в трех направлениях; 4-координатные — токарные двухсуппортные или фрезерные с дополнительным движением инструмента или заготовки. На станках со сложной траекторией движения инструмента применяют 5-координатные устройства ЧПУ. Некоторые устройства позволяют одновременно осуществлять движет только по одной из координат станка.
![]() |
Станки с ЧПУ нормального и повышенного классов точности устанавливают в общих помещениях механических цехов, а станки высокого класса точности — в изолированных помещениях. Нормальная температура воздуха в помещении должна быть 20°С. Легкие и средние станки монтируют на виброопоры или резиновые прокладки непосредственно на бетонном полу, а крупные и тяжелые станки — на бетонные фундаменты без виброизоляции.
Технология обработки на сверлильных станках
и оснастка
На сверлильных станках можно выполнять не только сверление, но и другие технологические операции дальнейшей обработки отверстий. На современных сверлильных станках осуществляют следующие работы:
|
ж |
• сверление сквозных и глухих отверстий (рис. 6.9, а);
• рассверливание отверстий на больший диаметр (рис. 6.9, б);
• зенкерование, выполняемое для получения отверстия с высокими квалитетом и параметром шероховатости поверхности(рис. 6.9, в);
• зенкование, выполняемое для образования в основании просверленного отверстия гнезд с плоским дном под головки винтов и болтов (рис. 6.9, г);
Рис. 6.9. Работы, выполняемые на сверлильных станках:
а — сверление; б — рассверливание; в — зенкерование; г — зенкование; д — развертывание; е — раскатывание; ж — нарезание внутренней резьбы; з — подрезание (цекование) торцов
Дата добавления: 2018-10-25; просмотров: 3783; Мы поможем в написании вашей работы! |
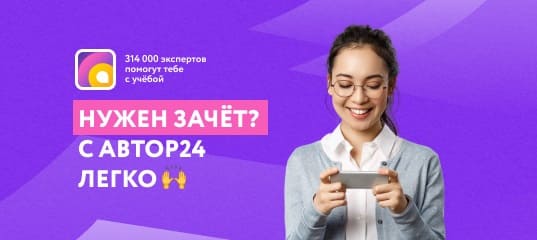
Мы поможем в написании ваших работ!