Суппорт, фартук, задняя бабка и система смазывания станка
Суппорт. Он (рис.6) предназначен для перемещения во время обработки режущего инструмента, закрепленною в резцедержателе. Он состоит из нижних салазок / (продольного суппорта), которые перемещаются по направляющим станины с помощью рукоятки 15 и обеспечивают перемещение резца вдоль заготовки. На нижних салазках по направляющим 12 перемещаются поперечное салазки (поперечный суппорт), которые обеспечивают перемещение резца перпендикулярно оси вращения заготовки (детали). На поперечных салазках 3 расположена поворотная плита 4, которая закрепляется гайкой 10. По направляющим 5 поворотной плиты 4 перемещаются с помощью рукоятки 13 верхние салазки //, которые вместе с плитой 4 могут поворачиваться в горизонтальной плоскости относительно поперечных салазок и обеспечивать перемещение резца под углом к оси вращения заготовки (детали). Резцедержатель 6 (резцовая головка) с болтами 8 крепится к верхним салазкам с помощью рукоятки 9, которая, перемещаясь по винту 7, зажимает резец. Привод перемещения суппорта производится от ходового винта 2 и ходового вала, расположенного под ходовым винтом. Включение автоматических подач производится рукояткой 14. Устройство поперечного суппорта показано на рис. 2.7. По направляющим продольного суппорта / ходовым винтом 12, оснащенным рукояткой 10, перемещаются салазки поперечного суппорта. Ходовой винт 12 закреплен одним концом в продольном суппорте /, а другим — связан с гайкой, состоящей из двух частей 15 и 13 и клина 14, которая крепится к поперечным салазкам'9. Затягивая винт 16, раздвигают клином 14 обе части 15 и 13 гайки, в результате чего выбирается зазор между ходовым винтом 12 и гайкой. Величину перемещения поперечного суппорта определяют по лимбу //. К поперечному суппорту крепится гайками 7 поворотная плита 8, вместе с которой поворачиваются верхние салазки 6 и резцедержатель 5.
|
|
|
На некоторых станках на поперечных салазках 9 устанавливается задний резцедержатель 2 для проточки канавок, отрезки и других работ, которые могут быть выполнены перемещением поперечного суппорта, а также кронштейн 3 с щитком 4, защищающим рабочего от попадания стружки и брызг смазочно-охлаждающей жидкости.
Рис. Суппорт токарного станка
Устройство резцедержател я показано на рис. 2.8. В центрирующей- расточке верхних салазок 5 установлена коническая оправка 3 с резьбовым концом. На конусе оправки установлена четырехсторонняя резцовая головка 6. При вращении рукоятки 4 головка 2 перемещается вниз по резьбе конической оправки 3 и через шайбу / и упорный подшипник обеспечивает жесткую посадку резцовой головки 6 на конической поверхности оправки 3. От проворота при закреплении резцовая головка удерживается шариком, который заклинивается между поверхностями, образованными пазом на основании конической оправки 3 и отверстием в резцовой головке 6.
|
|
|
Рис Поперечный суппорт
Фартук. Продольное и поперечное перемещение салазок суппорта производится через фартук .2 (рис. 2.9), который крепится к нижней поверхности продольного суппорта /. Ручная продольная подачапроизводится маховиком 15 (см. рис. 2.6), который через зубчатую передачу сообщает вращение зубчатому колесу 4 (см. рис. 2.9), катящемуся по рейке 3, закрепленной на станине 5 станка, и перемещает продольный суппорт / вместе с поперечным суппортом 6 и фартуком 2.
Продольная подача суппорта / от ходового винта 2 производится включением разъемной гайки рукояткой/4 (см. рис. 2.6). Разъемная гайка (рис. 2.10) состоит из двух частей (/ и 2), которые перемещаются по направляющим
Рис. 2.9. Фартук
А при повороте рукоятки 5. При этом диск 4 посредством прорезей В, расположенных эксцентрично, перемещает пальцы 3, в результате чего обе части гайки сдвигаются или раздвигаются. Если обе части гайки охватывают ходовой винт, то производится продольная подача (перемещение) суппорта; если они раздвинуты, то подача отключается.
|
|
Задняя бабка. Устройство задней бабки показано на рис. 2.11. В корпусе / (при вращении винта 5 маховиком 7) перемещается пиноль 4, закрепляемая рукояткой 3. В пиноли устанавливается центр 2 с коническим хвостовиком (или инструмент). Задняя бабка перемещается по направляющим станка вручную или с помощью продольного суппорта. В рабочем неподвижном положении задняя бабка фиксируется рукояткой 6, которая соединена с тягой 8 и рычагом 9: Сила прижима рычага 9 тягой 8 к станине регулируется гайкой // и винтом 12, Более жесткое крепление задней бабки производится с помощью гайки 13 и винта 14, который прижимает к станине рычаг 10.
Рис. 2.II. Задняя бабка
Система смазывания станка. Масла, введенные между контактирующим и взаимно перемещающимися поверхностями станка, образуют на них защитную пленку, которая уменьшает коэффициент трения. В результате этого уменьшаются износ деталей и затраты мощности привода на преодоление сил трения, повышается коэффициент полезного действия станка. Одновременно масла охлаждают контактирующие поверхности деталей при трении.
|
|
Детали станков смазывают двумя способами — индивидуальным и централизованным. Индивидуальная смазка бывает периодического и непрерывного действия. Периодическая смазка производится вручную (из пресс-масленки) или одноплунжерным насосом, непрерывная — разбрызгивающими кольцами, капельными масленками, масляной ванной или насосами. Наиболее распространена централизованная смазка.
|
4Îáðàáîòêà íàðóæíûõ öèëèíäðè÷åñêèõ и торцовых ïîâåðõíîñòåé. Îáðàáîòêà êàíàâîê и отрезание заготовок
1.Обработка резцами с пластинками из твердых сплавов. Черновая обработка цилиндрических поверхностей.
Особенности обработки твердосплавными резцами. Для наружного продольного чернового и чистового точения применяют проходные резцы. В настоящее время конструкция резцов с напаянными твердосплавными пластинами устарела. За рубежом около 80 % применяемых проходных твердосплавных резцов имеют сборную конструкцию, у нас в стране — только 20 % (рис. 4.18). По сравнению с напаянными резцами сборные имеют следующие преимущества: сокращение расходов на переточку; уменьшение вспомогательного времени на смену и подналадку резцов; экономия твердого сплава.
![]() | ![]() | ||
Прямые проходные резцы изготовляют с главным углом в плане



Рис.. Проходные резцы сборной конструкции (а) и типовые резцовые вставки с механическим креплением многогранных и цилиндрических твердосплавных пластин (б):
1 - подкладка; 2 - пластина; 3 - штифт; 4 - винт; 5 - державка; 6 - шарик
2.Обработка быстрорежущими резцами. Чистовая обработка.
Особенности обработки резцами из быстрорежущих сталей. Резцы из быстрорежущих сталей имеют такую же форму передней поверхности, как у сборных резцов с пластинками твердого сплава того же назначения, но имеют отличные от них углы резания и размеры элементов головки
Чистовая обработка. Для получения поверхности с малой шероховатостью, точной по форме и размерам заготовку подвергают чистовой обработке.
![]() |
Рис. 4.20. Проходные отогнутые (а и б) и упорные (в) резцы
Если требуемую шероховатость поверхности нельзя получить обычным проходным резцом, то применяют специальные (чистовые) резцы, предназначенные только для чистовой обработки.
Особенности обработки торцовых поверхностей. Торцы и уступы обрабатывают подрезными, проходными отогнутыми или проходными упорными резцами.
Подрезной резец предназначен для обработки наружных торцовых поверхностей. При подрезании торца движение подачи резца осуществляется перпендикулярно к оси обрабатываемой заготовки. Подрезной резец позволяет обрабатывать различные торцовые и другие поверхности с продольным и поперечным движениями подачи.
Рис. 4.23. Подрезные резцы: а — для обработки наружных торцов; б — для работы с продольной Vs2 и поперечной Vs1 подачами |
![]() |
Подрезные резцы изготовляют с пластинами из быстрорежущих сталей и сборные, с пластинами из твердых сплавов. Главный задний угол a = 10... 15°, передний угол

Прорезание канавок и отрезание заготовок.
Обработка канавок и отрезка. Узкие канавки обрабатывают прорезными резцами. Форма режущей кромки резца соответствует форме обрабатываемой канавки. Прорезные резцы (рис. 4.24) бывают прямые и отогнутые, которые, в свою очередь, делятся на правые и левые. Чаще применяют правые прямые и левые отогнутые прорезные резцы.
Заготовки и детали отрезают отрезными резцами (рис. 4.25). Ширина режущей кромки отрезного резца зависит от диаметра отрезаемой заготовки и может быть равна 3; 4; 5; 6; 8 и 10 мм. Длина l головки отрезного резца должна быть несколько больше половины диаметра d прутка, от которого отрезают заготовку.
Отрезные резцы изготовляют цельными, а также с пластинами из быстрорежущей стали или твердого сплава. Для уменьшения трения между резцом и разрезаемым материалом головка резца сужается к стержню под углом 1...2° (с каждой стороны резца), угол = 0°, задний угол a = 12°.
Для уменьшения шероховатости поверхности, полученной после отрезки, на задних вспомогательных поверхностях резца делают фаски шириной 1...2 мм (рис. 4.25, б). Поперечная подача при обработке канавок — 0,05 ...0,3 мм/об (для стальных деталей диаметром до 100 мм).
![]() |
Скорость резания при обработке канавок и отрезке заготовок — 25...30 м/мин для резцов из быстрорежущих сталей и 125... ... 150 м/мин для твердосплавных резцов.
![]() |
Рис. 4.25. Отрезные резцы: а — для получения ровного торца у отрезаемой детали; б — для уменьшения шероховатости поверхности, полученной после отрезки |
Рис. 4.24. Прорезные резцы: а — прямой левый; б — прямой правый; в — отогнутый левый; г — отогнутый правый |
|
7.Контроль деталей.
Контроль деталей. Наиболее распространенным инструментом для измерения размеров деталей, полученных после черновой и получистовой обработки, является штангенциркуль (рис. 4.26).
![]() | ![]() | ||
Рис. 4.26. Измерения штангенциркулем:
![]() |
а — правильное измерение небольшого диаметра; б — неправильное измерение; в — правильное измерение большого диаметра; г — штангенциркуль с цифровой индикацией; Аи В — губки для измерения внутренних поверхностей; С и D — губки для измерения наружных поверхностей; 1 — винт; 2 — каретка нониуса; 3 — линейка; 4 — ножка для измерения уступов и углублений
Рис. 4.27. Предельная скоба регулируемая (а) и нерегулируемая (б):
1, 2 и 3 — винты; 4, 5 — измерительные головки; 6 — опорная поверхность; ПР и НЕ — соответственно проходной и непроходной размеры
Наиболее удобным для определения размеров является штангенциркуль с цифровой индикацией (рис. 4.26, г).
В условиях серийного производства детали измеряют предельными регулируемыми (рис. 4.27, а) и нерегулируемыми (рис. 4.27, б) скобами. Особенностью скоб различных конструкций является то, что с их помощью оценивают два размера обработанной детали: первый — с наибольшим отклонением, а второй — с наименьшим. Размер с наибольшим отклонением обозначается ПР (проходной), а размер с наименьшим отклонением — НЕ (непроходной). В регулируемых скобах размеры НЕ и ПР настраивают перемещением измерительных головок.
Контроль наружных уступов, торцов и канавок. Глубину канавок на наружной поверхности детали измеряют линейкой, штангенциркулем, штангенглубиномером и шаблоном-уступомером (рис. 4.28).
Рис. 4.28. Измерение глубины канавки:
а — линейкой; 6 — штангенциркулем; в — штангенглубиномером; г — шаблоном-уступомером
Ширину обработанного участка до уступа измеряют линейкой в том случае, если не требуется большой точности измерения. При более высоких требованиях к точности измерения лучше использовать штангенциркуль, а при серийном производстве деталей — шаблон-уступомер. Проходная сторона шаблона (ПР) при измерении должна упираться в обработанную цилиндрическую поверхность детали, а непроходная сторона (НЕ) — в наружную цилиндрическую поверхность детали.
5Îáðàáîòêà цилиндрических îòâåðñòèé
Сверление и рассверливание.
Наиболее распространенным методом получения отверстий и сплошном материале является сверление. Движение резания при сверлении — вращательное, движение подачи поступательное. Перед началом работы проверяют совпадение вершин переднего и заднего центров станка. Заготовку устанавливают в патрон и проверяют, чтобы ее биение (эксцентричность) относительно оси вращения не превышала припуска, снимаемого при наружном обтачивании. Проверяют также биение торца заготовки, в котором будет обрабатываться отверстие, и выверяют заготовку по торцу. Перпендикулярность торца к оси вращения можно обеспечить подрезкой, при этом в центре заготовки можно выполнить углубление для нужного направления сверла и предотвращения его увода и поломки.
|
Для обработки штучных заготовок устанавливают трехкулачковый патрон и производят расточку сырых кулачков, а для обработки деталей из прутка зажимную цангу и соответствующие размеру прутка вкладыши, подающую цангу и направляющую втулку. Сверла с коническими хвостовиками устанавливают непосредственно в конусное отверстие пиноли задней бабки. Если размеры конусов не совпадают, то сверла устанавливают посредством переходных втулок .
Спиральные сверла изготовляют из сталей: углеродистой марки У12А, легированной марки 9ХС, быстрорежущей марки Р6М5, а также из твердых сплавов марок ВК6М, ВК8 и ВК15 и др.
Для сверл из быстрорежущей стали скорость резания и=25ч-35 м/мин. Причем большие значения принимают при увеличении диаметра сверла и уменьшении подачи.
При ручной подаче сверла трудно обеспечить ее постоянное (стабильное) значение. Для стабилизации подачи используют различные устройства. Механическую подачу сверла осуществляют суппортом токарного станка.
В резцедержателе станка устанавливают сверло с помощью прокладок 2 и 3 так, чтобы ось сверла находилась на линии центров. Если сверло с коническим хвостовиком , то применяют державку 2 с соответствующим коническим отверстием (гнездом). После выверки осей сверла и центров сверло подводят вручную к торцу заготовки и начинают сверление, а затем после зацентровки включают механическую подачу суппорта. Перед выходом сверла из заготовки механическую подачу значительно уменьшают или отключают и заканчиваю! сверление ручной подачей.
Зенкерование и развертывание отверстий.
Зенкером обрабатывают отверстия, предварительно штампованные, литые или просверленные. Зенкерование может быть как предварительной (перед развертыванием), так и окончательной обработкой. Кроме обработки отверстий, зенкеры применяются иногда для обработки торцовых поверхностей заготовок.
Зенкеры, как и сверла, устанавливают на токарных станках чаще всего в задней бабке или револьверной головке.
Развертывание. Для получения на токарных станках отверстий высокой точности и заданного качества обрабатываемой поверхности применяют развертывание.
При работе чистовыми развертками на токарных и токарно-револьверных станках применяют качающиеся оправки, которые компенсируют несовпадение оси отверстия с осью развертки. Для того чтобы обеспечить высокое качество обработки, сверление, зенкерование (или растачивание) и развертывание отверстия производят за одну установку заготовки в патроне станка.
Растачивание отверстий.
Если диаметр отверстия превышает диаметр стандартных сверл или зенкеров, то такое отверстие растачивают. Растачивание применяют также при обработке отверстий с неравномерным припуском или с непрямолинейной образующей.
На токарно-револьверных станках применяют расточные резцы круглого сечения, которые крепятся в специальных оправках-державках (рис. ).
![]() |
Расточный резец по сравнению с токарным имеет меньшую площадь сечения державки и больший вылет, что обусловливает отжим резца и способствует возникновению вибраций; поэтому при растачивании, как правило, снимается стружка меньшего размера и снижается скорость резания.
Рис. 4.30. Расточный резец, применяемый на токарно - револьверных станках:
1 — резец; 2 — винт крепления резца; 3 — державка
При черновом растачивании стали глубина резания достигает 3 мм; продольная подача 0,08—0,2 мм/об, а скорость реза ния 25 м/мин для быстрорежущих резцов и 50—100 м/мин для твердосплавных резцов. При чистовом растачивании стали глубина резания не превышает 1 мм, продольная подача — 0,05—0,1 мм/об, а скорость резания — 40—80 м/мин для быстрорежущих резцов и 150—200 м/мин для твердосплавных резцов.
6 Îáðàáîòêà êîíè÷åñêèõ ïîâåðõíîñòåé.
Способы обработки наружных конических поверхностей.
Общие сведения о конусах. Коническая поверхность характеризуется следующими параметрами (рис. 4.31): меньшим й и большим D диаметрами и расстоянием / между плоскостями, в которых расположены окружности диаметрами D и d. Угол а называется углом наклона конуса, а угол 2а — углом конуса.
Для уменьшения искажения образующей конической поверхности и уменьшения отклонения угла наклона конуса необходимо устанавливать режущую кромку резца по оси вращения обрабатываемой детали.
Рис. 4.31. Геометрия конуса:
d и D — меньший и больший диаметры; l — расстояние между плоскостями; а — угол наклона конуса; 2а — угол конуса
При обработке валов часто встречаются переходы между обрабатываемыми поверхностями, которые имеют коническую форму. Если длина конуса не превышает 50 мм, то его обрабатывают широким: резцом. При этом режущая! кромка резца должна быть установлена в плане относительно оси центров на угол, соответствующий углу наклона конуса на обрабатываемой детали. Резцу сообщают подачу в поперечном или продольном направлении. Чтобы уменьшить искажение образующей конической поверхности и угла наклона конуса, режущую кромку резца устанавливают по оси вращения детали.
![]() |
Следует учитывать, что при обработке конуса резцом с режущей кромкой длиной более 15 мм могут возникнуть вибрации, уровень которых тем выше, чем больше длина обрабатываемой детали, меньше ее диаметр, меньше угол наклона конуса, чем ближе расположен конус к середине детали, чем больше вылет резца и меньше прочность его закрепления. В результате вибраций на обрабатываемой поверхности появляются следы и ухудшается ее качество.
Рис. 4.32. Обработка конической поверхности путем поворота верхних салазок суппорта:
2а — угол конуса; а — угол наклона конуса
Конические поверхности с большими уклонами можно обрабатывать при повороте верхних салазок суппорта с резцедержателем (рис. 4.32) на угол а, равный углу наклона обрабатываемого конуса. Подача резца производится вручную (рукояткой перемещения верхних салазок), что является недостатком этого метода, поскольку неравномерность ручной подачи приводит к увеличению шероховатости обработанной поверхности. Указанным способом обрабатывают конические поверхности, длина которых соизмерима с длиной хода верхних салазок.
1. Обработка внутренних конических поверхностей
Обработку внутренней конической поверхности 4 заготовки (рис. 4.34, б) производят по копиру 2, установленному в пиноли задней бабки или в револьверной головке станка. В резцедержателе поперечного суппорта устанавливают приспособление с копирным роликом 3 и остроконечным проходным резцом. При поперечном перемещении суппорта копирный ролик 3 в соответствии с профилем копира 2 получает продольное перемещение, которое через приспособление передается резцу. Внутренние конические поверхности обрабатывают расточными резцами.
![]() | ![]() | ||
Рис. 4.34. Обработка конической поверхности с применением копирных устройств:
а — при продольном перемещении суппорта: / — суппорт; 2 — тяга; 3 — зажим; 4 — ползун; 5 — ось; 6 — копирная линейка; 7 — плита; 8 — болт; б — при поперечном перемещении суппорта: 1 — приспособление; 2 — копир; 3 — копирный ролик; 4 — внутренняя коническая поверхность; а — угол поворота копирной линейки
Для получения конического отверстия в сплошном материале заготовку сначала обрабатывают предварительно (сверлят, растачивают), а затем окончательно (развертывают). Развертывание выполняют последовательно комплектом конических разверток. Диаметр предварительно просверленного отверстия на 0,5... 1 мм меньше заходного диаметра развертки.
Если требуется коническое отверстие высокой точности, то его перед развертыванием обрабатывают коническим зенкером, для чего в сплошном материале сверлят отверстие диаметром на 0,5 мм меньше, чем диаметр конуса, а затем применяют зенкер. Для уменьшения припуска под зенкерование иногда применяют ступенчатые сверла разного диаметра.
12Îáðàáîòêà ôàñîííûõ ïîâåðõíîñòåé.
Дата добавления: 2018-10-25; просмотров: 1473; Мы поможем в написании вашей работы! |
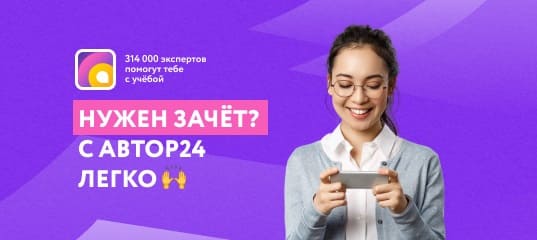
Мы поможем в написании ваших работ!