Р АСЧЁТ СИЛОВЫХ Ш ПИЛЕК ГОЛОВКИ БЛОКА
ВВЕДЕНИЕ
Надѐжность современных автотракторных двигателей внут-реннего сгорания во многом зависит от прочности его основных деталей, которые испытывают значительные динамические и тепло-вые нагрузки. Динамические нагрузки на некоторые детали носят циклический характер с различной частотой и амплитудой, в ре-зультате действия нагрузок в деталях могут возникать одновремен-но крутильные, изгибные, растяжения - сжатия напряжения. Тепло-вые нагрузки, связанные с градиентами температур вызывающих тепловые напряжения, а также всевозможные концентраторы на-пряжений в деталях сложной формы создают дополнительные на-пряжения, которые необходимо учитывать при расчѐтах деталей. Многие детали, совершая возвратно-поступательное и вращатель-ное движения, подвержены износу в процессе эксплуатации. Всѐ это в сочетании с другими факторами снижает прочность деталей двигателей.
Существующие методы расчѐта деталей двигателя на проч-ность позволяют определить с достаточной степенью точности, возникающие в них напряжения и рассчитать запасы прочности с учѐтом влияния факторов снижающих прочность деталей.
Целью создания практикума является ознакомление студен-тов с существующими методами расчѐта деталей двигателя на прочность и решение ими практических задач связанных с опреде-лением прочности деталей. Практикум закрепляет теоретический знания по дисциплине «Конструирование и расчѐт двигателей», прививает навыки расчѐта деталей двигателя с учѐтом теплового и напряжѐнно-деформированного состояния, при действии перемен-ных нагрузок.
|
|
Практикум включает в себя методы и исходные данные для расчѐта деталей кривошипно-шатунного и газораспределительного механизмов двигателя на прочность с анализом результатов расчѐ-та.
Практикум состоит из трѐх частей: часть 1 – «Расчѐт деталей цилиндропоршневой и шатунной групп», часть 2 – «Расчѐт деталей группы коленчатого вала», часть 3 – «Расчѐт деталей газораспреде-лительного механизма».
3
|
|
|
|
|
|
П рактическаяработа№1
Р АСЧЁТ Г ИЛЬЗЫ Ц ИЛИНДРА ДВИГАТЕЛЯ
Ц е л ь работы: ознакомится с методом расчѐта гильзы ци-линдра двигателя с жидкостным охлаждением, произвести расчѐт еѐ на прочность.
Метод расчёта
Основные конструктивные размеры гильз выбираются с учѐтом обеспечения необходимой их прочности и жѐсткости, ис-ключающей появление овализации цилиндра при сборке двигателя и во время его работы. Толщину чугунной стенки гильзы обычно принимают по экспериментальным данным.
|
|
Мокрые гильзы выполняют из легированных чугунов, серых перлитных чугунов СЧ 20, СЧ 35 или из сталей типа 38ХМЮА.
Толщину стенки гильзы в первом приближении определяют по формуле, используемой для расчѐта цилиндрических сосудов:
d = 0,5×D׿ è
sz +0,4× p z ö sz -1,3× p z ø
(1.1)
где p z - максимальное давление газов в цилиндре двигателя в конце процесса сгорания топлива, МПа; D - диаметр цилиндра, мм; σz - допускаемое напряжение на растяжение (для стальных гильз sz =80-100МП а, для чугунных гильз sz =50-60М П а).
При расчѐте гильзы цилиндров на прочность определяют напряжения только от основных нагрузок: максимального давления газов, бокового давления поршня и перепада температур в стенке гильзы.
Для двигателей с жидкостным охлаждением в качестве опасной нагрузки принимается максимальное давление в процессе
4
|

|
|
|
|
Растягивающее напряжение sp от действия сил газов опре-
|
|
деляют по приближѐнной зависимости, которая не учитывает не-равномерность распределения напряжений по толщине гильзы:
|
где p zmax - максимальное давление газов в цилиндре двигателя, условно отнесенное к положению поршня в НМТ, МПа.
Допускаемые напряжения sp для гильз цилиндров, выпол-
ненных из чугунов, изменяются в пределах 30 – 60 МПа, а для стальных – 80 – 120 МПа.
Во время работы двигателя между внутренней и наружной поверхностями гильзы возникает значительный перепад темпера-тур, вызывающий тепловые напряжения:
E×a ×DT t [2× 1- m)]
(1.3)
где E - модуль упругости материала гильзы, МПа (для стали E = 2,2×105 , для чугуна E =1,0×105 ); aц - коэффициент линейно-
го расширения, 1/К (для стали aц =10×10-6 , для чугуна aц =11×10-6 ); DT - перепад температур, К (на основании опытных данных DT =100–150 К); m - коэффициент Пуассона (для стали m =0,25-0,33, для чугуна m =0,23-0,27).
Напряжениям растяжения на наружной поверхности гильзы
соответствует знак плюс, а напряжениям сжатия на внутренней по-верхности – знак минус.
|
|
Суммарные напряжения от давления газов и перепада темпе-ратур:
5
на наружной поверхности цилиндра
såa =sp +st ; (1.4)
на внутренней поверхности
såi =sp -st . (1.5)
Суммарное напряжение в чугунной гильзе не должно превы-шать 100 – 130 МПа, а в стальной – 180 – 200 МПа.
Для двигателей с воздушным охлаждением с несущими ци-линдрами
- напряжения разрыва s’ Р по кольцевому сечению гильзы
s 'р =0,25× p zmax ×D dг ; (1.6)
- напряжения изгиба от боковой силы N
|
|
|
|
где D 0 – наружный диаметр цилиндра.
Суммарное напряжение от растяжения и изгиба в стенках не-сущего цилиндра
sS =s 'р +sи , (1.9)
6
в чугунных гильзах напряжения не должны превышать 60 МПа, в стальных – 110МПа.
П араметры д ля расчёта
В табл. 8 Приложения, для соответствующего варианта, выби-раются числовые значения следующих параметров для расчѐта гильзы цилиндра: D, p zmax .
7
П рактическаяработа№2
Р АСЧЁТ СИЛОВЫХ Ш ПИЛЕК ГОЛОВКИ БЛОКА
Ц е л ь работы: ознакомится с методом расчѐта силовых шпилек головки блока двигателя с жидкостным охлаждением, про-извести расчѐт еѐ на прочность.
Метод расчёта
Расчѐт силовых шпилек головки блока строится на допуще-нии, что в процессе сгорания топлива силу давления газов воспри-нимают ближайшие к цилиндру шпильки (четыре – шесть), а дейст-вие силы их затяжки распространяется только на ближайший к ци-линдру участок головки и блока.
Материалом для изготовления шпилек в бензиновых и ди-зельных двигателях служат углеродистые стали с высоким преде-лом упругости 30, 35, 40, 45, 30Х, 35Х, 40Х, 45Х и высоколегиро-ванные стали 18ХНВА, 20ХН3А.
При нерабочем состоянии в холодном двигателе силовые
|
по опытным данным определяют в виде следующей приближѐнной зависимости:
|
|
|
|
где b – коэффициент затяжки шпильки (изменяется в пределах 1,5 – 2,0, для соединения с прокладками достигает 5 и более); c -
|
|
сила давления газов при сгорании, приходящаяся на одну шпильку, МН.
Сила давления газов при сгорании, приходящаяся на одну шпильку:
8
|
|
|
|

|
|
|
ш п
(2.2)
где p zmax - максимальное давление сгорания, МПа; F k - пло-щадь проекции поверхности камеры сгорания на плоскость, пер-пендикулярную оси цилиндра, м2; z ш п - число шпилек на один ци-линдр.
|
где F п - площадь поршня, м2.
|
|
|
|
Растягивающая шпильку сила:
aголD голlгол -aш пD шпlшп t Kгол + Kшп
, (2.3)
|
|
|
|
м; l шп - расчѐтная длина шпильки, м; K г о л и K ш п - податливость головки и шпильки, м/Н.
Податливость шпильки с постоянной площадью поперечно-го сечения:
|
9
|
внутреннему диаметру резьбы, м2
|
|
|
d в =d -1,4×t, (2.6)
где d в – внутренний диаметр резьбы, d и t – наружный диаметр и шаг резьбы.
Податливость головки блока цилиндров:
|
|
головки, приходящаяся на одну шпильку, м2.
С учѐтом всех действующих сил максимальная сила, растя-гивающая шпильку:
|
|
|
|
Минимальная растягивающая сила
|
|
|
Максимальные и минимальные напряжения в шпильке оп-ределяют по внутреннему диаметру резьбы:
|
|
10
Параметры цикла нагружения шпильки и запас прочности определяют по известным уравнениям, с учѐтом концентрации на-пряжений и свойств материала.
Допускаемые запасы прочности изменяются в пределах: 2,5 – 4,0 – по пределу выносливости и 1,5 – 2,5 – по пределу текучести.
П араметры д л я расчёта
В табл. 8 Приложения, для соответствующего варианта, вы-бираются числовые значения следующих параметров для расчѐта гильзы цилиндра для двигателя с жидкостным охлаждением: p zmax ,
z ш п , l г о л , l ш п .
11
П рактическаяработа№3 РАСЧЁТ ПОРШНЯ
Ц е л ь работы: ознакомится с методом расчѐта поршня и его элементов, произвести расчѐт их на прочность.
Метод расчёта
Поршни изготавливают из алюминиевых сплавов методом литья из АЛ25 или ковкой из АК4.
Для плоских и близких по конфигурации днищ поршня, их рассчитывают на изгиб от действия максимальных газовых сил
p zmax . Днище рассматривают как круглую плиту, свободно опи-рающуюся на цилиндр. Для бензиновых двигателей наибольшее давление газов достигается при работе на режиме максимального крутящего момента. Для дизелей максимальное давление газов обычно достигается при работе на режиме максимальной мощно-сти.
Напряжение от изгиба в днище поршня:
sИ =0,25×pzmax ×(dB /dД ), (3.1)
где dВ - внутренний диаметр поршня у днища, м; dД - толщина
днища, м.
Если днище поршня без рѐбер жѐсткости, допускаемое на-пряжение для поршней из алюминиевых сплавов составляет 20 – 25 МПа, при наличии рѐбер жѐсткости, допускаемое напряжение – 50 – 150 МПа.
Головка поршня рассчитывается на сжатие. Напряжение сжатия рассматривается в сечении, ослабленном отверстиями для отвода масла:
|
12
|
днище поршня, МН; F A-A - площадь сечения головки поршня, ос-лабленном отверстиями для отвода масла, м2 .
Площадь сечения поршня, ослабленного масляными отвер-стиями:
|
|
|
|
|
|
|
|
|
Допускаемые напряжения на сжатие для поршней из алю-миниевых сплавов 30 – 40 МПа.
Стенку в указанном сечении поршня рассчитывают также на разрыв:
|
|
кольцами, расположенная выше сечения А-А, МН;
m Г » (0,4-0,6)×mПГ - масса поршневой головки с кольцами, рас-
положенная выше сечения А-А, кг; m ПГ - масса поршневой груп-пы, кг; R - радиус кривошипа, м; wХ -Хmax =p ×n Х -Хmax /30 - мак-
симальная угловая скорость холостого хода двигателя, рад/с. Допускаемые напряжения на разрыв для поршней из алю-
миниевых сплавов 4 – 10 МПа.
13
Толщина верхней межкольцевой перемычки форсированных двигателей с высокой степенью сжатия рассчитывается на срез и изгиб от действия максимального давления газов p zmax .
Межкольцевая перемычка рассматривается как кольцевая пластина, защемлѐнная по окружности основания канавки и нагру-женная по всей площади давления газов.
Напряжение среза межкольцевой перемычки:
t = 0,0314× p zmax ×D/h М П , (3.5)
где h М П - высота верхней межкольцевой перемычки, м. Напряжение изгиба межкольцевой перемычки:
sИ = 0,0045× p zmax ×(D/h М П )2 (3.6)
Сложное напряжение по третьей теории прочности:
|
Допускаемые напряжения в верхней межкольцевой пере-мычки с учѐтом значительных температурных нагрузок не должны превышать 30 – 40 МПа для поршней из алюминиевых сплавов.
Максимальное удельное давление юбки поршня на стенку цилиндра, при работе двигателя на режиме максимальной мощно-сти, определяется из уравнения:
p ю = Nmax /(h ю ×D) , (3.8)
где Nmax - наибольшая нормальная сила, действующая на стенку цилиндра (определяется по данным динамического расчѐта), МН;
h ю - высота юбки, м.
Для современных автотракторных двигателей максимальное удельное давление не должно превышать 0,3 – 1,0 МПа.
14
|
|
|
|
|
|
Dé1+aц ×(t ц -t0)ù -D/Ю Ю 1+aп ×(t Ю -t0)
, (3.10)
где t ц =383-388, t Г = 473-723, t Ю = 403- 473 - темпера-туры соответственно стенок цилиндра, головки поршня и юбки в их
рабочем состоянии, для двигателей с жидкостным охлаждением, К; t0 = 293 - начальная температура цилиндра и поршня, К; aц и aп
- коэффициенты линейного расширения материалов цилиндра и поршня соответственно, 1/К (для чугуна aц =11×10-6 , для алюми-ниевых сплавов aгол = 22×10-6 ).
П араметры д ля расчёта
Согласно варианту по табл. 8-9 Приложения принимаются значения следующих параметров для расчѐта поршня: dВ , dД ,
|
15
П рактическаяработа№4 РАСЧЁТ ПОРШНЕВОГО КОЛЬЦА
Ц е л ь работы: ознакомится с методом расчѐта поршневого кольца и произвести расчѐт его на прочность.
Метод расчёта
Расчѐт колец заключается: а) в определении среднего давле-ния кольца на стенку цилиндра, которое должно обеспечивать дос-таточную герметичность камеры сгорания и не должно резко уве-личивать потери мощности двигателя на трение колец о стенки ци-линдра; б) в построении эпюры давления кольца по окружности; в) в определении напряжений изгиба, возникающих в сечении, проти-воположном замку, при надевании кольца на поршень и в рабочем состоянии; г) в установлении монтажных зазоров в прямом замке кольца.
Для изготовления поршневых колец используются серые и модифицированные чугуны типа СЧ 15, СЧ 20, СЧ 25 и высоко-прочные чугуны с шаровидным графитом типа ВЧ 45, ВЧ 50, ВЧ 60.
Среднее давление кольца на стенку цилиндра:
|
где Ж - разность зазоров в замке кольца в свободном состоянии и минимально допустимого во время работы двигателя, м; dп.к -толщина поршневого кольца, м; E - модуль упругости материала кольца, МПа (для серого чугуна E =1,0×105 , для легированного
чугуна E =1,2×105 ).
Допустимое среднее радиальное давление: для компресси-онных колец – 0,1 – 0,37 МПа; для маслосъѐмных колец – 0,2 – 0,4 МПа.
16
|
|
|
|
|

|
|
|
|
|
|
p = p с р ×mк , (4.2)
где mк - переменный коэффициент, определяемый изготовителем в соответствии с принятой формой эпюры давления кольца на зер-кало цилиндра.
Для бензиновых двигателей принимается грушевидная фор-ма эпюры давления кольца со следующими параметрами:
Угол Y, град Коэффициент mк
0 30 60 90 1.05 1.04 1.02 1.0
120 150 180 1.02 1.27 1.50
Для дизельных двигателей принимается каплевидная форма эпюры давления кольца со следующими параметрами:
Угол Y, град Коэффициент mк
0 30 60 1.05 1.05 1.14
90 120 0.90 0.45
150 180 0.67 2.85
Максимальные напряжения при изгибе кольца в рабочем состоянии, возникающие в его поперечном сечении напротив замка:
0,382×E× Ж max
|
|
(4.3)
Максимальные напряжения, возникающие при разведении замка в процессе надевания кольца на поршень:
4×E×(dпк -0,114× Ж) max
|
|
(4.4)
17
где k - коэффициент, зависящий от способа приложения уси-лий к кольцу при надевании его на поршень (в расчетах принимает-ся k =1,57 ).
Допускаемые напряжения при изгибе кольца 220 – 450 МПа. Монтажный зазор в прямом замке холодного кольца после
заведения последнего в цилиндр двигателя:
|
|
|
|
енты линейного расширения материалов цилиндра и кольца; t к ,t ц ,t о – температура соответственно кольца, стенок цилиндра в рабочем состоянии двигателя и начальная температура, К (при жид-костном охлаждении t к = 473 – 573, t ц = 383 – 388, t0 = 293).
П араметры д ля расчёта
Согласно варианту по табл. 9 Приложения принимаются значения следующих параметров для расчѐта поршневого кольца:
D, dп.к .
18
|
|
|

|
|
|
Ц е л ь работы: ознакомится с методом расчѐта поршневого пальца и произвести расчѐт его на прочность.
Метод расчёта
Во время работы двигателя поршневой палец подвергается действию переменных нагрузок. Расчѐт поршневого пальца вклю-чает определение удельных давлений пальца на втулку поршневой головки шатуна и на бобышки, а также напряжений от изгиба, среза и овализации.
Поршневые пальцы изготавливают из сталей 15Х, 20Х, 12ХН2, 12ХН3А, 20ХН3А, 40ХН, 18Х2Н4МА, которые подверга-ются цементации, закалке и низкотемпературному отпуску.
Давление, приходящееся на единицу площади проекции опорной поверхности:
- в бобышках поршня:
p zmax × п +k× jпг б d н ×(L п г -L п )
(5.1)
|
|
расстояние между бобышками поршня, м; L пг - длина поршневой головки шатуна, м.
- во втулке поршневой головки шатуна:
p zmax × п + j п г ш d н ×L п г
(5.2)
Для современных автотракторных двигателей p б =15-50М П а, p ш =20-60М П а .
19
|
|
|

|
|
P×(L п + 2×L б п -1,5×L п г ) и 1,2×d3 ×(1-g4 )
(5.3)
|
|
Для автотракторных двигателей допускаемые напряжения при изгибе 200 - 250 МПа.
Максимальные напряжения при срезе пальца возникают в сечениях, расположенных в зазорах между торцами бобышек и поршневой головки шатуна:
0,85×P×(1+g +g2) (1-g4)×d2
. (5.4)
|
горизонтального диаметра Ddmax ) наблюдается в средней части пальца на длине около 0,2L п в направлении, перпендикулярном к плоскости действия нагрузки:
|
|
|
|
|
Диаметральная деформация Ddmax не должна превышать
допустимое значение 0,001d н .
Напряжения, возникающие при овализации пальца:
20
- на внешней поверхности пальца в горизонтальной плоско-сти в соответствии с рисунком (точка 1):
|
|
|
|
|
|
|
|
|
|
|
|
|
|
|
|
|
|
|
|
|
|
|
|
|
|
|
|
|
|
|
|
|
|
|
Наибольшее напряжение имеет место на внутренней по-верхности пальца в горизонтальной плоскости. Эти напряжения не должны превышать 300 – 350 МПа.
П араметры д ля расчёта
Согласно варианту по табл. 9 Приложения принимаются значения следующих параметров для расчѐта поршневого пальца:
|
21
Дата добавления: 2018-09-22; просмотров: 402; Мы поможем в написании вашей работы! |
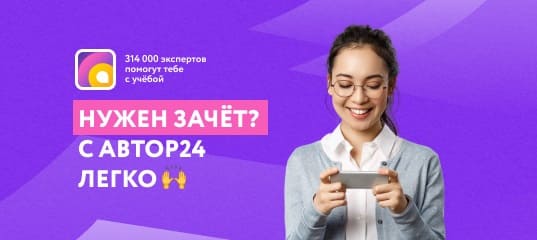
Мы поможем в написании ваших работ!