Структура и расчет основных параметров поточной линии
Под структурой поточной линии в общем виде следует понимать состав входящих в нее рабочих мест (технологических участков), транспортных средств, управляющих и других устройств (систем) и производственные взаимосвязи между ними. Наиболее сложной является структура поточного производства на уровне цеха (предприятия), под которой понимается состав поточных линий различного назначения, робототехнических комплексов, гибких автоматизированных модулей, транспортно-накопительных, управляющих и других систем и формы производственных взаимосвязей между ними.
Выбору структуры поточного производства и его комплектованию должен предшествовать анализ конструкционно-технологических особенностей изделий и определение уровня их технологичности с учетом формы, габаритов, массы, марок и видов материалов, их свойств, характера технологии и состава входящих в нее операций, методов их выполнения и затрат времени, необходимого оборудования, инструментов, приспособлений, средств механизации и автоматизации, приборов (аппаратов) для предупреждения дефектов и выявления брака, а также с учетом технических и эксплуатационных требований к изделиям, предусмотренных ГОСТами, ОСТами, техническими условиями заказчика потребителя.
Выбор типа оборудования для поточной линии предопределяется характером технологического процесса, составом, сложностью и назначением входящих в него операций; габаритами, массой изготовляемого изделия и требованиями, предъявляемыми к его качеству. При комплектовании поточных линий желательно добиться прямолинейного расположения оборудования, если позволяют производственные мощности и тип выбранных транспортных средств.
|
|
Выбор рациональной структуры и компоновка являются важной предпосылкой разработки оптимальных планировок поточных линий (рис. 3.4).
Рис. 3.4. Схемы компоновки и планировок поточных линий
Оценка оптимальности варианта планировки линии производится по таким технико-экономическим показателям, как доля площади, занятой непосредственно технологическим оборудованием, выпуск продукции на 1 кв.м производственной площади, длина пути, проходимого за смену рабочим при обслуживании им нескольких единиц оборудования, и др.
Важным организующим структурным элементом поточного производства является транспорт. Учитывая многообразие различных факторов, в поточном производстве применяют средства периодического транспорта (краны, электрокары, тельферы и др.), бесприводные средства непрерывного транспорта (рольганги, скаты), приводные средства непрерывного транспорта (ленточные, пластинчатые, цепные и другие транспортеры), роботизированные транспортные средств (промышленные роботы, различные транспортно-накопительные автоматизированные системы).
|
|
Выбор организационных форм поточных линий определяется тактом работы линии, степенью синхронизации операций технологического процесса, уровнем загрузки рабочих мест на линии.
Под тактом поточной линии г понимается календарный период времени между запуском (выпуском) на линию данного объекта (деталь, сборочная единица, изделие) и следующего за ним. Такт является функцией заданной программы выпуска, существенно влияет на выбор технологического процесса, оборудования, оснастки, транспортных средств. В общем виде величина такта определяется:
r = F д / N з
где Fд - действительный фонд времени за плановый период (смена, сутки, месяц);
Nз - количество запускаемых на поточную линию объектов производства за тот же период.
В тех случаях, когда передача с операции на операцию осуществляется транспортными партиями (небольшие детали, малая величина такта, измеряемая секундами), рассчитывается ритм поточной линии:
r р = r n тр ,
где nтр - величина транспортной (передаточной) партии.
|
|
По способу поддержания ритма различают линии с регламентированным и свободным ритмом. Линии с регламентированным ритмом характерны для непрерывно-поточного производства. Здесь ритм поддерживается с помощью конвейеров или сигнализации. Линии со свободным ритмом не имеют технических средств, строго регламентирующих ритм работы. Эти линии применяются при любых формах потока, и соблюдение ритма в этом случае возлагается непосредственно на работников данной линии.
Чтобы обеспечить единый такт или ритм поточной линии, при организации поточного производства осуществляется синхронизация, т. е. производительность выравнивается по всем операциям технологического процесса. Синхронизация означает достижение равенства или кратности времени выполнения операций технологического процесса установленному такту их работы и является важной предпосылкой непрерывного функционирования линий. К наиболее распространенным способам синхронизации относятся: расчленение операции на переходы и комбинирование различных вариантов порядка их выполнения или группирование переходов нескольких операций, концентрация операций, введение параллельных рабочих мест на операциях, длительность которых кратна такту, интенсификация режимов работы, совмещение времени выполнения нескольких переходов, рационализация рабочих приемов, совмещение времени машинной и ручной работы и др.
|
|
Рассматривают предварительную синхронизацию с отклонением от такта (ритма) в пределах примерно ± 10 %, которая осуществляется при проектировании поточных линий, и окончательную, более точную, синхронизацию - при отладке линии.
Предварительная синхронизация достигается подбором метода выполнения операций, оборудования и технологической оснастки, режимов обработки и структуры операции. В операциях с большим удельным весом ручного времени, например на сборке, синхронизация достигается в результате перекомпоновки переходов.
На первом этапе не всегда удается обеспечить полную синхронизацию процесса; в этот период допускается отклонение в загрузке рабочих мест на 8 – 10 %. Эта перегрузка должна быть ликвидирована при отладке линии путем внедрения организационно-технических мероприятий, повышающих производительность труда на перегруженных рабочих местах, т.е. при окончательной синхронизации процесса. В числе подобных мероприятий можно назвать применение средств малой механизации, форсирование технологических режимов, внедрение высокопроизводительной оснастки, рациональную планировку рабочего места и улучшение его обслуживания, индивидуальный подбор рабочих для перегруженных операций, а также материальное стимулирование повышения производительности труда на этих операциях.
Полная синхронизация операций обеспечивается при достижении равенства
t1 / c1 = t2 / c2 = t3 / c3 = … = t m/ cm = rпл
где t1, t2, t3, tm - норма времени по операциям, мин.;
с1, с2, с3, сm - число рабочих мест на операции, шт.;
rпл – такт поточной линии, мин.
На следующем этапе определяем необходимое число рабочих мест (единиц оборудования) для каждой операции:
с i расч = ti / r пл
где ti – норма времени на i-ю операцию.
При полной синхронизации потока величина сi расч всегда целое число, загрузка рабочих мест полная и одинаковая на всех операциях. При неполной синхронизации на несинхронных операциях сi расч не равно целому числу. Экономически целесообразно округлять сi расч до ближайшего меньшего числа, предусмотрев при этом использование рациональной оснастки, более рационального режима работы оборудования и т.д. При этом допустимая перегрузка рабочего места в расчетах должна быть не более 10 – 12 % со снятием ее при отладке линии.
Коэффициент загрузки рабочих мест на каждой операции, %,
С
Кз = -----
Спрi
Средний коэффициент загрузки рабочих мест на поточной линии, %,
M
S С pi
i =1
К з ср ----------
M
S C пр i
i =1
Коэффициенты kз оi и kз о ср являются показателями целесообразности применения поточного производства. Желательно иметь в массово-поточном производстве нижний предел загрузки рабочих мест 80 – 85 %, а в серийно-поточном – 70 – 75 %.
Далее осуществляем планировку поточной линии, начиная ее с разработки схем рабочих мест по всем операциям и выбора рациональных транспортных средств. В результате общей компоновки поточной линии определяется ее внешний контур, способ расстановки оборудования, расположение транспортных средств, средств промежуточного и окончательного контроля, мест для заделов. Планировка поточных линий (см. рис. 3.5) должна обеспечивать прямоточность и наиболее короткий путь движения изделия, рациональное использование производственных площадей, удобство транспортировки заготовок и деталей к рабочим местам, к местам обслуживания и выполнения ремонтов.
Рис.3.5. Схема планировки поточной линии с распределительным конвейером
(под цифрой 1 - пример расположения объектов производства
и разметочных знаков на конвейере)
1 - ленточный транспортер, 2 - места для складирования,
3 - приводная и стяжная станция, 4 - стеллаж
После расчета такта, количества рабочих мест для последующей планировки конвейера рассчитывается его шаг lш , т. е. расстояние между осями симметрии двух рядом расположенных объектов на конвейере.
Длина деления, или шаг конвейера, выбирается из соотношения
1ш min< lш<lш min. l ш min определяется габаритами объекта и средним расстоянием между двумя рядом находящимися на конвейере объектами (lср= 200 - 300 мм), а 1ш max определяется допустимой скоростью движения конвейера.
Скорость движения конвейера должна соответствовать такту потока. Это соответствие достигается, если путь, равный шагу, конвейер проходит за такт:
vk = l ш / r .
Чаще всего применяют распределительные конвейеры со скоростями в пределах 0,5 + 2 м/мин. Период распределительного конвейера П – это комплект знаков, предназначенных для его разметки.
Длина рабочей части конвейера:
И и
lр.k = l ш ( S wpi + S wki )
i=1 i=1
wpi и wki - количество рабочих мест, где выполняются производственные и контрольные операции;
и - число всех операций в технологическом процессе.
Длина рабочей линии конвейера l р к согласовывается с его периодом.
Рабочий конвейер оснащен механическим транспортером, который перемещает обрабатываемый объект вдоль линии, регламентирует ритм работы и служит местом выполнения операций. Поскольку объекты не снимаются с конвейера, линии рабочим конвейером применяют главным образом для сборки сварки изделий, заливки в формы (в литейных цехах), окраски узлов и агрегатов в специальных окрасочно-сушильных автоматических камерах.
Шаг рабочего конвейера lш при сборке небольших изделий часто принимают равным 1 - 1,2 м, а при сборке крупногабаритных изделий руководствуются такими же соображениями, как и для распределительного конвейера, т. е. учитываются габариты объекта и расстояние между ними. Максимально допустимый шаг лимитируется также допустимой скоростью движения конвейера. Рациональными скоростями рабочего конвейера считаются 0,5 - 2,5 м/мин при сборке относительно небольших объектов или при повышенных требованиях к ее точности.
При таких скоростях вполне допустимо непрерывное движение конвейера. Если требуется скорость больше, чем 2,5 м/мин, применяют конвейер пульсирующего типа. Однако при высокой технологической оснащенности сборочных работ, бригадной организации труда и в условиях непрерывного движения скорость υк может быть значительно выше 2,5 м/мин. (см. метод. указания "Поточное производство").
Прямоточные линии
Прямоточные (прерывно-поточные) линии чаще всего используют для механической обработки деталей (заготовок) при недогрузке оборудования из-за несинхронности процесса. Поэтому прямоточные линии экономически оправдывают себя, если достигнута синхронизация большей части операций, включенных в технологическую цепочку линии, и возможна комбинированная загрузка рабочих, работающих на недогруженном оборудовании, путем закрепления за ними двух-трех операций.
Для прямоточных линий устанавливается наиболее целесообразный для данных условий производства период обслуживания рабочими-совместителями закрепленных за ними рабочих мест с выполнением на каждом из них определенного задания. Он зависит от уровня ритмичности, грузоподъемности транспортных средств и других факторов.
На прерывно-поточных (прямоточных) линиях с характерной для них различной производительностью на отдельных операциях непрерывность отсутствует, однако ритмичность выпуска здесь соблюдается. Ритм линии в этом случае укрупненный и определяется интервалом времени, в течение которого на линии формируется выработка установленной величины, например часовая, полусменная, сменная.
По способу поддержания ритма различают линии с регламентированным и свободным ритмом. Линии с регламентированным ритмом характерны для непрерывно-поточного производства. Здесь ритм поддерживается с помощью конвейеров или сигнализации. Линии со свободным ритмом не имеют технических средств, строго регламентирующих ритм работы. Эти линии применяются при любых формах потока, и соблюдение ритма в этом случае возлагается непосредственно на работников данной линии.
В связи с отсутствием синхронности процесса на прямоточной линии возникает из-за разной производительности на смежных рабочих местах межоперационные оборотные заделы. Изменение межоперационного оборотного задела определяется по формуле:
где Zоб i,i+1 – изменение межоперационного оборотного задела между операциями за период времени Т';
Т' – период времени, в течение которого смежные операции находятся в неизменных условиях по производительности, мин.;
Спр i, Спр i+1 – количество работающих станков на предшествующей и последующей операциях за период Т';
t'шт i, t'шт i+1 – откорректированное штучное время соответственно предшествующей и последующей операций, мин.
Значение Т', Спр i, Спр i+1 определяются на основании графика-регламента работы оборудования (рис. 3.6).
1
2
3
4 5
6
7
8
| 1 2 3 4 5 6 7 8 |
|
|
№№ ПП |
Операция | Количество рабочих мест | Загрузка рабочих мест | Табельный номер рабочего | Графики работы оборудования и межоперационных оборотных заделов R н = 1 смена (480 мин.) | |||||||||||||
Сpi | Cnpi | Номер станка | % загрузки | 60 | 120 | 180 | 240 | 300 | 360 | 420 | 480 | |||||||
1 | 2 | 3 | 4 | 5 | 6 | 7 | 8 | 9 | 10 | 11 | 12 | 13 | 14 | 15 | ||||
![]() ![]() ![]() ![]() ![]() 1 | Фрезерование | 3,84 | 4 | 1 2 3 4 | 100 100 86 86 | 01 01 02 02 | ||||||||||||
![]() ![]() ![]() ![]() ![]() | ||||||||||||||||||
![]() ![]() ![]() | Растачивание | 1,44 | 2 | 1 2 | 100 44 | 03 04 | ||||||||||||
![]() ![]() ![]() ![]() | ||||||||||||||||||
![]() ![]() ![]() | Обтачивание | 2,50 | 3 | 1 2 3 | 100 100 50 | 05 06 04 |
|
Схема планировки прямоточных линий должна предусматривать территориальное сближение рабочих мест, обслуживаемых рабочими-совместителями. Наиболее приемлемыми транспортными средствами для прямоточных линий являются рольганги, тельферы, электрокары.
Дата добавления: 2018-09-22; просмотров: 770; Мы поможем в написании вашей работы! |
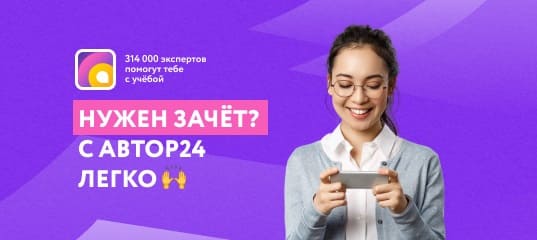
Мы поможем в написании ваших работ!