Оборудование с ЧПУ, рекомендуемое к применению.
Комитет по образованию Государственное бюджетное профессиональное образовательное учреждение «Санкт-Петербургский технический колледж» УТВЕРЖДАЮ Директор ГБПОУ СПбТК _______А.В. Бурасовский « » 2017 г.
Методические указания
По подготовке
Курсового проекта
По ПМ.01. «Разработка технологических процессов изготовления деталей машин»
для студентов 4 курса очной формы обучения
по специальности 151901
«Технология машиностроения»
(базовая подготовка)
Согласовано на заседании Методического совета: Протокол № ___от «____»______2017 г. | Рассмотрено на заседании ПЦК «Технология машиностроения» Протокол №_____от «____»___________2017 г. Председатель ПЦК__________/Тимофеева Н.О./ | |
|
Санкт-Петербург, 2017
СОДЕРЖАНИЕ
1. ОБЩИЕ ПОЛОЖЕНИЯ………………………………………………………..…………3
1.1. Место курсового проекта в
учебном плане подготовки специалистов………………………………………………3
|
|
1.2. Цель и задачи курсового проекта ……………………………………………..…...3
2. МЕТОДИЧЕСКИЕ УКАЗАНИЯ К ВЫПОЛНЕНИЮ ОСНОВНЫХ РАЗДЕЛОВ КУРСОВОГО ПРОЕКТА ……………………………………………………………..9
2.1. Общая часть………………………………………………………………………….10
2.2. Технологическая часть……………………………………………………………...14
2.3 Техника безопасности и охрана окружающей среды…………………………......24
3. БИБЛИОГРАФИЧЕСКИЙ СПИСОК ………………………………………………….25
4. ПРИЛОЖЕНИЯ…………………………………………………………………………..26
Приложение 1…………………………………………………………………………….26
Приложение 2…………………………………………………………………………….29
Приложение 3…………………………………………………………………………….30
Приложение 4…………………………………………………………………………….32
1. ОБЩИЕ ПОЛОЖЕНИЯ
Методические указания разработаны в соответствии с требованиями Федерального государственного образовательного стандарта среднего профессионального образования (ФГОС СПО), требованиями рабочих учебных планов ГБПОУ СПбТК по специальности 151901 «Технология машиностроения» (базовая подготовка).
Целью методических указаний является ознакомление студентов:
|
|
- с последовательностью работы над курсовым проектом
- с требованиями, предъявляемыми к содержанию курсового проекта
- с требованиями, предъявляемыми к оформлению пояснительной записки, графической части, комплекта технологической документации.
В методических указаниях изложены состав и последовательность этапов выполнения основных разделов выпускной квалификационной работы.
1.1. Место курсового проекта в учебном плане подготовки специалистов
Курсовой проект представляет собой самостоятельную и логически завершенную работу, связанную с решением задач тех видов деятельности, к которым готовится выпускник:
- разработка технологических процессов изготовления деталей машин;
- участие во внедрении технологических процессов изготовления деталей машин и осуществление технического контроля;
- выполнение работ по одной или нескольким профессиям рабочих, должностям служащих;
и является заключительным этапом обучения студентов по специальности «Технология машиностроения».
Выполнение курсового проекта является комплексной проверкой подготовки студентов к работе на предприятиях машиностроительного комплекса. Защита курсового проекта проводится с целью выявления соответствия уровня и качества подготовки выпускников ФГОС СПО в части государственных требований к минимуму содержания и уровню подготовки выпускников и дополнительным требованиям колледжа по специальности «Технология машиностроения» и готовности выпускника к профессиональной деятельности.
|
|
1.2. Цель и задачи курсового проекта
Целью выполнения курсового проекта является:
- систематизация, закрепление, расширение теоретических знаний и практических умений, использование их при решении профессиональных задач;
- приобретение навыков самостоятельной творческой работы, связанной с решением конкретной производственной задачи, обусловленной темой дипломного проектирования;
- определение уровня сформированности профессиональных и общих компетенций.
- комплексная проверка подготовки выпускников колледжа к работе на предприятиях машиностроительного комплекса.
В процессе подготовки курсового проекта студент должен решить следующие задачи:
- обосновать актуальность выбранной темы, ее соответствие современным требованиям науки и производства с учетом реальных задач предприятия, работающего в условиях рыночной экономики, где быстрота реализации принятых решений играет главенствующую роль;
|
|
- практическое решение вопросов по рассматриваемой в курсовом проекте проблематике, с использованием ЭВМ становится возможным решение проблемы автоматизации разработки технологических процессов и проектирования средств технологического оснащения;
- оформить курсовой проект в соответствии с указанными требованиями.
2. МЕТОДИЧЕСКИЕ УКАЗАНИЯ К ВЫПОЛНЕНИЮ ОСНОВНЫХ РАЗДЕЛОВ КУРСОВОГО ПРОЕКТА.
Порядок формирования папки курсового проекта:
1. Титульный лист (не нумеруется)
2. Задание на курсовой проект.
3. Аннотация (не нумеруется)
4. Оглавление (начинается нумерация с 3 листа), включает в себя содержание пояснительной записки по теме дипломного проекта.
Для выполнения пояснительной записки по технологической тематике курсового проекта может быть предложено следующее содержание:
ВВЕДЕНИЕ
1. ОБЩАЯ ЧАСТЬ
1.1. Описание конструкции и условий эксплуатации детали.
1.2. Анализ технологичности детали.
2. ТЕХНОЛОГИЧЕСКАЯ ЧАСТЬ
2.1. Обоснование заданного типа производства.
2.2. Выбор и обоснование метода получения заготовки и расчет заготовки с чертежом заготовки.
2.3. Разработка проектируемого технологического процесса.
2.3.1. Технические условия на изготовление детали и методы их обеспечения.
2.3.2. Выбор технологического оборудования и технологической оснастки.
2.3.3. Разработка маршрутного технологического процесса.
2.4. Разработка операционного технологического процесса.
2.4.1. Определение операционных припусков и межоперационных размеров.
2.4.2. Обоснование выбора баз.
2.4.3. Расчет режимов резания и норм времени.
3. ТЕХНИКА БЕЗОПАСНОСТИ И ОХРАНА ОКРУЖАЮЩЕЙ СРЕДЫ.
4. БИБЛИОГРАФИЧЕСКИЙ СПИСОК.
ВВЕДЕНИЕ
Введение обязательно должно быть увязано с темой дипломного проекта, содержать краткое изложение дипломного задания, обоснование важности и актуальности выбранной темы. Во введении отмечаются основные цели и мероприятия, связанные с дальнейшим повышением технического уровня производства, экономией использования основных материалов, механизацией и автоматизацией производства, разработкой прогрессивных технологических процессов, улучшением качества продукции и влиянием этих факторов на технико-экономические показатели проекта. Введение не должно превышать двух страниц текста.
1. ОБЩАЯ ЧАСТЬ.
1.1. Описание конструкции и условий эксплуатации детали.
1.1.1. Назначение и конструкция детали.
Описываются: наименование детали, ее номер, в какой узел входит, назначение в узле, каким подвергается нагрузкам.
1.1.2. Технические требования.
К ним относятся требования к детали, записанные на чертеже, описании изделия или непосредственно вытекающие из взаимной связи ее поверхностей точности размеров и формы. Например, если на чертеже или в технических условиях не указаны:
- допускаемые отклонения от формы детали, то они принимаются в пределах допуска на размер соответствующих поверхностей;
- несоосность отверстий, лежащих на одной оси – принимается в пределах допуска на меньший диаметр и т.п.
Технические требования наряду с конструкцией детали, определяют порядок и методы механической обработки.
Пример. Технические требования.
Несоосность отверстия диаметром 80мм и диаметром 50мм допускается в пределах половины допуска на отверстие диаметром 50мм.
Биение торца диаметром 200/120мм относительно оси – не более 0.05мм.
Твердость поверхностей детали – НВ 170…229.
1.1.3. Материал детали.
В пояснительной записке следует дать характеристику материала, показать его химический состав, физико-механические свойства, технологические свойства. Этот анализ необходим для выбора метода получения заготовки, материала режущей части инструментов и определения режимов резания.
Таблица 1 Химический состав, в %
Углерод С | Кремний Si | Марганец Mn | Фосфор Р | Хром Cr | Никель Ni | Сера S |
Таблица 2 Механические свойства
Твердость по Бринелю НВ | Предел прочности при растяжении sв в МПа | Предел прочности при изгибе sизг в МПа | Предел текучести sТ в МПа | Относительное удлинение
![]() | Относительное сужение
![]() |
1.2. Анализ технологичности детали.
Технологичная конструкция позволяет экономить затраты труда, повышать точность, использовать высокопроизводительное оборудование, оснастку и инструменты, экономить энергию. Чем более технологичной оказывается конструкция, тем совершеннее и дешевле будет ее производство.
Согласно стандартам ЕСТПП 14.201-83 и др. технологичность детали оценивается следующими коэффициентами:
1. Коэффициент унификации конструкции элементов детали
Куэ = Qуэ/Qэ (1.1)
где Qуэ – число унифицированных типоразмеров и конструктивных элементов
(резьбы, отверстия, фаски, шлицы, зубья и т.п.)
Qэ – общее число типоразмеров конструктивных элементов в изделии.
При Куэ > 0.6 деталь относится к технологичным.
2. Коэффициент точности Кт.
Кт = 1- 1/Аср (1.2)
где Аср – средний квалитет точности обработки
При Кт < 0.8 деталь относится к весьма точным изделиям.
3. Коэффициент шероховатости Кш.
![]() |
Кш = 1/Бср (1.9)
где Бср – средний класс шероховатости (ГОСТ 2789-73) -
n1, n2, …. ni – число поверхностей соответствующего класса шероховатости.
При Кш < 0,16 изделие относится к труднообрабатываемым.
Данные для расчета коэффициентов технологичности сведены в таблице №3.
Таблица 3 Таблица для расчета коэффициентов технологичности детали «Корпус»
№ | Наименование поверхности | Квалитет | Параметр шероховатости Ra | Вид обработки | Степень унификации |
1 | Наружная цилиндрическая поверхность Æ 50h9 | 9 | 2,5 | точение черновое чистовое | унифицир. |
2. ТЕХНОЛОГИЧЕСКАЯ ЧАСТЬ.
2.1. Обоснование заданного типа производства.
В машиностроении различают три типа производства: массовое, серийное, единичное (ГОСТ 14.004-83).
Тип производства характеризуется коэффициентом закрепления операций:
Кзо=О/Р (2.1)
где О – число различных технологических операций, выполняемых в течении
месяца,
Р – число рабочих мест.
В массовом и крупносерийном производстве 1<Кзо<10, в серийном 10<Кзо<20, в мелкосерийном 20<Кзо<40.
Тип производства оказывает влияние на выбор оборудования, приспособлений, режущего и мерительного инструментов. В массовом производстве, где оборудование полностью загружено изготовлением однотипных деталей и Кзо=1, используются автоматические линии и станки, специальные приспособления, измерительные и режущие инструменты и т.п.
В крупносерийном производстве должны преобладать полуавтоматические и автоматизированные станки и приспособления.
В среднесерийном производстве и мелкосерийном производстве преобладают универсальные станки, оснащенные специализированными приспособлениями. Используются станки с программным управлением и промышленные роботы, а также специализированные станки.
Выполняя этот пункт пояснительной записки, дипломник должен указать значение Кзо и дать характеристику используемого оборудования, кроме того, указать величину партии деталей и характер организации производства. Количество деталей партии, одновременно запускаемых в производство, устанавливается с таким расчетом, чтобы оправдать расходы по переналадке оборудования и обеспечить выпуск деталей равными частями в течении года. Формула для расчета и размер партии приводятся в организационно-экономической части проекта.
2.2. Выбор и обоснование метода получения заготовки.
В машиностроении основными видами заготовок для деталей являются стальные и чугунные отливки, а также заготовки из цветных металлов и сплавов, штамповки и всевозможные профили проката.
Вид заготовки оказывает значительное влияние на характер технологического процесса, трудоемкость и экономичность ее обработки.
Содержание и последовательность действий при выборе метода получения заготовки:
2.2.1. Рассматривают два метода получения заготовок. При этом исходят из опыта завода, где изготовляется заданная деталь, кроме того, следует учесть тип производства, марку материала и конфигурацию детали и другие технические требования на изготовление детали.
2.2.2. Назначают припуски на обрабатываемые поверхности детали согласно выбранному методу получения заготовок по нормативным таблицам. Выбор припусков на механическую обработку штампованных заготовок осуществляется по ГОСТ 7505-89, литых по ГОСТ 2665-85.
2.2.3. Рассчитывают размеры заготовок. Для расчета размеров заготовки табличные значения припусков на механическую обработку прибавляют к наружным размерам готовой детали подлежащим обработке. Для определения внутренних размеров заготовки – припуски вычитают.
2.2.4. Выбирают отклонения размеров заготовок и определяют размеры и отклонения заготовок. Отклонения на размеры заготовок приводятся в соответствующих таблицах выше указанных ГОСТов «Припуски на механическую обработку».
2.2.5. Выполняют эскизы заготовок с указанием размеров и отклонений.
2.2.6. Производят расчет массы заготовок. Масса заготовки (детали) сложной конфигурации устанавливается путем определения массы отдельных простейших геометрических фигур, из которых состоит заготовка (деталь).
2.2.7. Определяют коэффициент использования материала Км.
2.2.8. Определяют себестоимость изготовления заготовки выбранных вариантов для сопоставления и определения экономического эффекта получения заготовки.
В этом же разделе устанавливается конструкторский и технологический код детали по классификатору ЕСКД (класс 71, 72, 73) и технологическому классификатору.
Пояснения и результаты анализа представлены в таблице № 4.
Таблица 4 Конструкторско-технологический код детали «Втулка»
Код | Пояснения и результаты анализа |
Конструкторский код детали СПТК 71. 3443.016 | |
СПТК 71 3 4 4 3 016 | Код организации - разработчика Класс деталей – тела вращения Подкласс деталей с отношением 0.5<L/D<2 Группа деталей без закрытых уступов, ступенчатая односторонняя без наружной резьбы С центральным сквозным отверстием круглым в поперечном сечении Вид: без кольцевыми пазами на торцах, с пазами и шлицами на наружной поверх, с отверстиями вне оси детали Порядковый номер |
Технологический код детали 690044 32414116 | |
6.9.0 04 4 32 4 1 4 1 1 6 | Максимальный наружный диаметр 28 Максимальная длина L=40, центрального отверстия Сталь 45, сталь углеродистая с содержанием С=45% Вид детали по методу изготовления обрабатываемая резаньем Пруток круг не калиброванный Наименьший наружный квалитет Ø20к7 Наименьший внутренний квалитет Ø10h12 Наименьшая шероховатость по наружной поверхности Ra=0.8 Отклонения форм и расположения поверхностей отсутствуют Без термобработки, с покрытием Масса детали 0.001 |
Конструкторско-технологический код детали СПТК. 71. 3443.016 690044 32414116 |
2.3. Разработка проектируемого технологического процесса.
На этом этапе изготовления изделия особое внимание обращают на качество и его важнейший показатель – точность. В 21 веке точность деталей машин выросла почти в 2000 раз. Такого увеличения не наблюдается ни по одному из показателей служебных характеристик. Понятие «точность» относится не только к размеру, но и к форме, взаимному расположению поверхностей, физико-механическим характеристикам деталей и среды, в которой их изготовляют. Важнейшим показателем качества является точность всех параметров изготовления детали. С использованием ЭВМ становится возможным решить проблему автоматизации разработки ТП, обеспечив выполнение всех требований чертежа детали с минимальными затратами труда и издержками производства, используя при этом высокопроизводительное оборудование с ЧПУ
2.3.1. Технические условия на изготовление детали записаны в пункте 1.1.2. В данном разделе необходимо описать методы обеспечения перечисленных в пункте 1.1.2 требований.
2.3.2. Выбор технологического оборудования и оснастки.
2.3.2.1. Выбор оборудования.
Выбор станков производится исходя из следующих соображений:
- выбранный станок должен обеспечивать выполнение технических требований, предъявляемых к изготовлению детали;
- размеры рабочей зоны станка должны соответствовать габаритным размерам обрабатываемой детали;
- производительность станка должна соответствовать заданной программе выпуска деталей;
- мощность, жесткость и кинематические возможности станка должны позволять вести обработку на оптимальных режимах резания с наименьшей затратой времени и наименьшей себестоимостью.
При выборе оборудования предпочтение следует отдавать тем моделям станков, которые оснащены контрольно-измерительными головками для измерения деталей и настройки инструментов непосредственно на станке и адаптивными системами управления.
Для обоснования применения дорогих, но высокопроизводительных агрегатных, специализированных, многошпиндельных станков должны быть сделаны соответствующие экономические расчеты.
2.3.2.2. Выбор технологической оснастки.
Выбор приспособлений производится в зависимости от вида обработки, типа станка и типа производства.
Для крупносерийного и массового производства характерно применение высокопроизводительных специальных приспособлений, снабженных быстродействующим зажимным устройством.
В серийном и единичном производстве применяются, в основном, универсальные и универсально-наладочные приспособления.
Выбранные приспособления должны обеспечивать:
- правильную установку детали,
- повышение производительности труда,
- надежность и безопасность работы,
- расширение технологических возможностей станка,
- автоматическое получение заданной точности,
- экономичность обработки.
В условиях мелкосерийного и серийного производства следует применять стандартные универсальные приспособления: патроны, машинные тиски, поворотные столы, кондукторные приспособления, предусматривая для них дополнительные наладки для заданного изделия.
При проектировании приспособления желательно применять пневматические или гидравлические приводы зажимов, предусматривать возможность обработки заготовки одновременно на двух позициях или по несколько штук (многоместные) Приступая к проектированию, необходимо проанализировать имеющиеся конструкции приспособлений, наметить пути их усовершенствования или замены новыми приспособлениями, принципиально отличающимися от старых.
2.3.2.3. Выбор режущего инструмента.
Выбор режущего инструмента зависит от вида станка, метода обработки, материала обрабатываемой детали, требуемой точности и шероховатости поверхностей, типа производства.
В единичном и мелкосерийном производстве в основном используются универсальные инструменты.
В крупносерийном и массовом производстве широко используются специальные инструменты. Особое значение имеет применение комбинированного инструмента, дающего возможность обрабатывать несколько поверхностей за один проход, модульного инструмента, позволяющего осуществлять автоматическую смену, увеличить технологическую жесткость.
В соответствии с дипломным заданием для одной из операций проектируемого технологического процесса конструируется специальный рабочий режущий инструмент. Выбор конструкции должен быть обоснован технической и экономической целесообразностью. Такими инструментами могут быть фасонные резцы, набор фрез, протяжки для фасонных поверхностей, многоступенчатые зенкеры и развертки, комбинированный инструмент, инструменты новейшей конструкции для станков с программным управлением и оснащенных сверхтвердыми режущими материалами.
2.3.2.4. Выбор измерительного инструмента.
Измерительный инструмент выбирается в зависимости от вида измеряемой поверхности, размеров поверхности, точности механической обработки, типа производства.
В единичном, мелкосерийном производстве применяются универсальные измерительные инструменты: штангенциркули, микрометры и другие.
В крупносерийном и массовом производстве применяются калибры, шаблоны, автоматические устройства для активного контроля.
Завершить выполнение данного раздела следует заполнением таблицы 5.
Таблица 5 Оборудование и технологическая оснастка по операциям
Операция | Наименование станка, тип (модель), основные размеры, мощность | Приспособления | Режущий инструмент | Измерительный инструмент |
2.3.3. Разработка маршрутного технологического процесса.
Разработка маршрутного технологического процесса заключается в выборе последовательности операций, выполнение которых обеспечивает получение из заготовки готовой детали.
В пояснительной записке необходимо заполнить таблицу маршрута обработки заданной детали.
Таблица 6 Маршрут обработки
№ операции | Операция | Оборудование | ||
Код | Наименование | Код | Наименование оборудования, модель | |
2.4. Разработка операционного технологического процесса.
2.4.1. Расчет припусков.
Припуск на обработку поверхности детали может быть назначен по соответствующим справочным таблицам, ГОСТам или на основе расчетно-аналитического метода определения припусков (РАМОП).
Применение РАМОП сокращает отход металла в стружку по сравнению с табличным значением, создает единую систему определения припусков на обработку и размеров детали по технологическим переходам заготовок, способствует повышению культуры производства.
Согласно дипломному заданию, припуски на все операции и переходы определяются справочным методом по справочникам. Расчет припусков для одной-двух поверхностей дипломник должен произвести аналитическим методом.
Данные по расчету припусков статистическим методом могут быть сведены в табл. 7
Форма для расчета припусков, допусков и промежуточных размеров по технологическим переходам при справочном методе расчета.
Таблица 7
Поверхность, операция, технологический переход | Припуск, мм | Расчетный размер, мм | Допуск, мм |
1 | 2 | 3 | 4 |
Поверхность Æ 25е8 Заготовка Точение черновое Точение чистовое Шлифование |
Результаты расчета заносятся в таблицу № 8.
Форма для расчета припусков, допусков и промежуточных размеров по технологическим переходам при аналитическом методе расчета.
Таблица 8
Расчетная поверхность, вид обработки | Элементы припуска | Расчетный припуск | Расчетный размер | Допуск | Пред. размеры | Пред. значения припуска | |||||
Rzi-1 | hi-1 | D | Ei-1 | max | min | max | min | ||||
мкм | мкм | мкм | мкм | мкм | мм | мкм | мм | мм | мкм | мкм | |
1 | 2 | 3 | 4 | 5 | 6 | 7 | 8 | 9 | 10 | 11 | 12 |
Поверхность Æ25е8 Заготовка 1.точение черновое 2.точение чистовое 3.шлифование | |||||||||||
2.4.2. Обоснование выбора баз.
В зависимости от сложности изготавливаемой детали возможны несколько вариантов базирования.
1. Заготовку базируют на черновые (необработанные) поверхности и при одной установке за одну операцию выполняют ее полную обработку (обработка на станках-автоматах, агрегатных, на станках с ЧПУ типа «обрабатывающий центр»).
2. Заготовку базируют на черновые поверхности, производя обработку поверхностей, которые далее используются как чистовые несменяемые базы. Обработку заготовок выполняют за несколько установов.
3. Вариант аналогичен предыдущему за исключением того, что перед последним этапом ТП принятые чистовые технологические базы подвергают повторной (отделочной) обработке. Вариант характерен для деталей повышенной точности.
4. Выполнение некоторых операций возможно с одновременным базированием на черновые и чистовые поверхности. Этот случай (нежелательный) может встретиться при изготовлении деталей с особыми требованиями.
5. Заготовку базируют на несколько сменяемых баз, которые повторно обрабатываются. Например: предварительное и окончательное шлифование планки на магнитной плите с последовательным перевертыванием для обработки каждой ее стороны.
Студенту рекомендуется рассмотреть варианты базирования и обосновать выбранный вариант.
При выборе технологических баз стремятся к более полному соблюдению принципа совмещения баз. Соблюдение принципа постоянства баз содействует повышению точности взаимного расположения обрабатываемых поверхностей заготовки. При вынужденной смене баз нужно переходить от менее точной базы по размерам, форме и расположению к более точной. К выбранным базам должны быть сформулированы требования точности и шероховатости. Условное обозначение опор, зажимов, установочных элементов выполняются согласно ГОСТ 3.1107-81.
2.4.3. Расчет режимов резания и норм времени.
Исходными данными для выбора режима резания являются: данные об изготовляемой детали и ее заготовке, а также данные о применяемом оборудовании и инструменте.
Режимные параметры выбирают таким образом, чтобы была обеспечена наибольшая производительность труда при наименьшей себестоимости данной технологической операции. Эти условия удается выполнить при работе инструментом рациональной конфигурации с максимальным использованием всех эксплуатационных возможностей станка.
Аналитический расчет режимов резания по эмпирическим формулам с учетом всех поправочных коэффициентов производят по указанию руководителя проекта только для двух-трех переходов или разнохарактерных операций, например точения, сверления, шлифования. Для остальных операций режимы резания устанавливают по таблицам нормативных справочников с использованием поправочных коэффициентов, учитывающих изменение условий обработки.
Нормы вспомогательного и подготовительно-заключительного времени берут по таблицам нормативных справочников.
Данные для расчета Твсп. заносят в таблицу № 9.
Данные для расчета вспомогательного времени на операцию.
Таблица 9
№ пер | tуст | tпер | tn | ts | tсм | tвсп | tок.пр. |
А | |||||||
1 | |||||||
2 | |||||||
3 | |||||||
4 | |||||||
Б |
Штучное время определяют по формуле:
Тшт = (То + Твсп)(1+ К/100) (2.2)
где То - основное технологическое время, которое может быть машинным, машинно-ручным и ручным. На станках определяем машинное время.
Твсп - затрачивается на выполнение рабочим ряда действий, необходимых для того, чтобы обеспечить проведение основной работы. Твсп затрачивается на:
tуст. и закр. - время на установку и закрепление заготовки;
tперех. - время, связанное с переходом;
tсмен. - время на смену инструмента;
tn - время на смену частоты вращения;
ts - время на смену подач;
tок.пр. - время на окончательный промер;
(То + Твсп) - оперативное время;
Тобсл.р.м. - время на обслуживание рабочего места;
Тотд - время на отдых;
Тобсл.р.м. + Тотд. - прибавочное время, определяется в % от оперативного времени;
К = 5-12 %
Норма выработки определяется по формуле:
Nвыр = (480 – Тп.з)/Тшт (2.3)
Особенности нормирования на станке с ЧПУ рассмотрены в методических рекомендациях по выполнению расчетно-лабораторных работ на станках с ЧПУ.
6.Техника безопасности и охрана окружающей среды.
В этом разделе следует кратко осветить общие правила техники безопасности на предприятии, указать номера ИОТ для различных операций, обратить внимание на мероприятия, проводимые администрацией предприятия по улучшению условий труда работников.
БИБЛИОГРАФИЧЕСКИЙ СПИСОК
Основные источники:
1.Ермолаев В. В.
Технологическая оснастка: учебник для студ.учреждений сред. проф.образования/ В.В. Ермолаев.- 2-е изд.-М.: Издательский центр «Академия», 2013- 320с.
2. Новиков В.Ю.
Технология машиностроения: в 2 ч. – Ч. 1: учебник для студ. учреждений сред. проф. образования-/В.Ю.Новиков, А.И. Ильянков. – 3-е изд., стер. – М. : Издательский центр «Академия», 2014-420 c.
3. Новиков В.Ю.
Технология машиностроения: в 2 ч. – Ч. 2: учебник для студ. Учреждений сред. Проф. образования-/В.Ю.Новиков, А.И. Ильянков. – 3-е изд., стер. – М. : Издательский центр «Академия», 2014-432 c.
4. Черпаков Б.И.
Технологическое оборудование машиностроительного производства: учебник для студ. учреждений сред. проф. образования-/Б.И.Черпаков, Л.И.Вереина.-5-е изд. стер.- М.: Издательский центр «Академия», 2013- 448с.
Дополнительные источники:
1. Учебники и учебные пособия
1. Анухин В.И.
Допуски и посадки. Учебное пособие 5-е.изд. - СПб.: Питер, 2012- 256 с
2. Ермолаев В. В.
Технологическая оснастка. Лабораторно – практические работы и курсовое проектирование : учеб. пособие для студентов. учреждений сред. проф.образования/ В.В. Ермолаев.- 2-е изд.-М.: Издательский центр «Академия», 2014-432 с.
3.Ильянков А.И.
Технология машиностроения: Практикум и курсовое проектирование: учеб.пособие для студ. учреждений сред. проф. образования-/А.И.Ильянков, В.Ю.Новиков -2-е изд.,стер.- .- М.: Издательский центр «Академия», 2013-412 c
4.Проектирование технологических схем и оснастки: учеб. Пособие для студентов. Высш. Учеб. Заведений/ [ Л.В. Лебедев, А.А. Погонин, И.В. Шрубченко и др.]- М.:Издательский центр «Академия», 2009- 420с.
5. Технология машиностроения. Часть III: Правила оформления технологической документации: Учеб. Пособие/ Э.Л. Жуков. И.И. Козарь, Б.Я. Розовский, В.В. Дегтярев, А.М. Соловейчик; Под ред. С.Л. Мурашкина. СПб.: Изд-во Политехн. Ун-та, 2008-58c
2.Справочники
1.Гузеев В.И., Батуев В.А., Сурков А.И
Режимы резания для токарных и сверлильно-фрезерно-расточных станков с ЧПУ/ Справочник / Под ред. В.И. Гузеева М.: Машиностроение, 2007 г-
2. Справочник технолога-машиностроителя под ред. Косиловой А.Г. Том 1. М.: Машиностроение, 2007 г – 656 c.
3.Справочник технолога-машиностроителя под ред. Косиловой А.Г. Том 2. М.: Машиностроение, 2007 г – 652 c.
4.Станочные приспособления. Справочник в 2-х томах. Ред. совет Г.Н. Вардашкин (пред.) и др. М.: Машиностроение, 1984- 645 c.
3.Электронные ресурсы:
1. Информационный сайт по по технологии машиностроения. [Электронный ресурс] / - Режим доступа: http :// revolution . allbest . ru свободный. – Загл. с экрана. – Яз. рус.
2. Сайт СТАНКО инструмент [Электронный ресурс] / - Режим доступа:
http://www.gig-ant.com/machinery/63/1232.htm свободный. – Загл. с экрана. – Яз. рус.
Приложение 1
Класс шероховатости по ГОСТ 2789-73 | Параметры шероховатости | |
Ra, мкм | Rz, мкм | |
1 | 80, 63, 50, 40 | 320, 250, 200, 160 |
2 | 40, 32, 25, 20 | 160, 125, 100, 80 |
3 | 20.0, 16.0, 12.5, 10.0 | 80, 63, 50, 40 |
4 | 10.0, 8.0, 6.3, 5.0 | 40, 32, 25, 20 |
5 | 5.0, 4.0, 3.2, 2.5 | 20.0, 16.0, 12.5, 10.0 |
6 | 2.5, 2.0, 1.6, 1.25 | 10.0, 8.0, 6.3 |
7 | 1.25, 1.00, 0.80, 0.63 | 6.3, 5.0, 4.0, 3.2 |
8 | 0.63, 0.50, 0.40, 0.32 | 3.2, 2.5, 2.0, 1.6 |
9 | 0.32, 0.25, 0.20, 0.16 | 1.60, 1.25, 1.00, 0.80 |
10 | 0.160, 0.125, 0.100, 0.080 | 0.80, 0.63, 0.50, 0.40 |
11 | 0.080, 0.063, 0.050, 0.040 | 0.40, 0.32, 0.25, 0.20 |
12 | 0.040, 0.032, 0.025, 0.020 | 0.20, 0.16, 0.125, 0.100 |
13 | 0.020, 0.016, 0.012, 0.010 | 0.100, 0.080, 0.063, 0.050 |
14 | 0.010, 0.008 | 0.050, 0.040, 0.032, 0.025 |
Параметры, выделенные являются предпочтительными.
Приложение 2
Оборудование с ЧПУ, рекомендуемое к применению.
№ | Наименование станка | модель | Устройство ЧПУ | Размеры раб.пов-ти стола, мм | Наибольший диаметр обрабатываемого изделия, мм | Наибольшая масса обрабатываемого изделия, кг | Наибольшая масса обрабатываемого изделия, кг | Мощность электро-двигателя главного движения, кВт | Габарит, мм | Масса, кг | Кол-во инструментов в магазине рев. головки, шт |
1 | 2 | 3 | 4 | 5 | 6 | 7 | 8 | 9 | 10 | 11 | 12 |
1 | Центр токарный продольного точения с ЧПУ | 11Б16ВФ4 | 2У32 | - | 16 | - | 150 | 5.5 | 2200х2600 1000х 1800х | 12 | |
2 | Автомат токарный продольного точения многооперационный с ЧПУ | 11Б25ВФ4 | 2Р32 | - | 25 | - | 250 | 7,6 | 2270х 1400х3200 1950х | 12 | |
3 | Токарно-карусельный одностоечный с ЧПУ | 1612Ф3 | - | 11250 | - | 1000 | 5,5 | 2875х 3220х15500 4080х | |||
4 | Токарно-винторезный станок с ЧПУ | 16К20Ф3 | Электроника НЦ-31 | - | 630 | - | 1500 | 30 | 5290х7850 3470х | 4 | |
5 | Токарный станок с ЧПУ | 16А20ФС33 | 2Р22 | - | 400 | - | 1000 | 11 | 3505х 1700х3800 | 8 | |
6 | Токарный патронно-центровой полуавтомат с ЧПУ | 1716ПФ3 | 2Р22 | - | 320 | - | 760 | 11 | 3020х2830 | 4500 | 8 |
7 | Полуавтомат токарно-многоцелевой двухсуппортный | 17А20ПФ40-4 | СМ2101 | - | 400 | - | 7500 | 25 | 3850х1600 х1775 | 6100 | 12 |
![]() | |||||||||||
| |||||||||||
1 | 2 | 3 | 4 | 5 | 6 | 7 | 8 | 9 | 10 | 11 | 12 |
8 | Токарно-винторезный с ЧПУ | ИТ42 | Маяк 223 | - | 125 | - | 500 | 4 | 2970х2310 | 2400 | 12 |
9 | Многоцелевой токарно-револьверный прутково-патронный полуавтомат с ЧПУ | 1П420ПФ40 | НЦ80-31 | - | 200 (50 диаметр прутка) | - | - | 30 | 3150х3260 х2300 | 6700 | 12 |
10 | Многоцелевой токарно- патронноцентровой полуавтомат с ЧПУ | РТ-72Ф4 | - | 630 | - | 750 | 30 | 4820х2750 | 11200 | 8 | |
11 | Многоцелевой токарный станок | ИРТ180ПМФ4 | - | 200 | - | - | 18.5 | 2751х2170 х1650 | 4500 | 24 | |
12 | Многоцелевой токарно-револьверный автомат с ЧПУ | 11Д25 | - | 25 | - | 100 | 15 | 2630х1700 | 3600 | ||
13 | Многоцелевой токарно-револьверный прутково-патронный автомат с ЧПУ | 11540ПФ4 | - | 40 (диаметр патрона 125) | - | 125 | 15 | 3250х2400 х2150 | 5000 | ||
14 | Многоцелевой токарный патронно-центровой полуавтомат с ЧПУ | 1716ПФ4 | - | 320 | - | - | 11 | 3020х2830 | 500 | 12 | |
1 | 2 | 3 | 4 | 5 | 6 | 7 | 8 | 9 | 10 | 11 | ![]() |
15 | Многоинструментальный горизонтально-расточной станок с ЧПУ | ИР200ПМ1Ф4 | С С «Фанук» и др. | 200х200 | - | 30 | - | 5,5 | 5813х2400 х2400 | 6000 | 24 |
16 | Многоцелевой станок | ИС500ПФМ4 | С С «Фанук» и др. | 500х500 | - | 800 | - | 22 | 5813х1750 х3560 | 1400 | 40/62/100 |
17 | Многоцелевой станок | ИС800ПМФ4 | С С «Фанук» и др. | 800х800 | - | - | - | - | 5813х1750 х3560 | 16900 | 40/64/100 |
18 | Обрабатывающий центр | Модуль ИР320ПМФ4 | С С «Фанук» и др. | 320х320 | - | 150 | - | 7,5 | 3840х2300 х2507 | 1000 | 36 |
19 | Модуль сверлильно-фрезерно-расточной | ЛП395ПМФ4М | Типа С С | 1250 х1250 | - | 4000 | - | 25 | 8720х7960 х4500 | 35000 | 50 |
20 | Обрабатывающий центр | ОЦ1И22 | С С «Маяк» | 1250 х400 | - | 200 | - | 14 | 4770х2300 х3000 | 5800 | 15 |
Приложение 2
Аналитический расчет
Деталь – фланец. Сталь 45 ГОСТ 1050-88.
Заготовка – штамповка, масса заготовки – 1.5 кг.
![]() |
Ø25е8
dmax=24,960 мм
dmin=24,927 мм
РАСЧЕТНАЯ КАРТА
Расчетная поверхность, вид обработки | Элементы припуска | Расчетный припуск | Расчетный размер | Допуск | Пред. размер
| Пред. значение припуска | |||||
Rzi-1 | hi-1 | ![]() | Ei-1 | max | min | max | min | ||||
мкм | мкм | мкм | мкм | мкм | мм | мкм | мм | мм | мкм | мкм | |
Пов-ть Ø25е8 | |||||||||||
Заготовка | 27,666 | 1800 | 29,47 | 27,67 | |||||||
Черновое точение | 160 | 200 | 640 | 450 | 2285 | 25,381 | 210 | 25,59 | 25,38 | 3880 | 2290 |
Чистовое точение | 50 | 50 | 38,4 | 27 | 294 | 25,087 | 130 | 25,22 | 25,09 | 370 | 290 |
Шлифование | 25 | 25 | - | 30 | 160 | 24,927 | 33 | 24,96 | 24,927 | 260 | 163 |
Расчет промежуточных припусков и допусков ступенчатой заготовки, полученной методом горячей объемной штамповки на молотах, прессах и горизонтально-ковочных машинах ведут по ступени, к которой предъявляют высокие требования по точности, качеству поверхности, отклонению расположения.
Маршрут обработки поверхности Ø25е8:
1. точение черновое
2. точение чистовое
3. шлифование
1. Расчет припусков на черновое точение.
При обработке цилиндрических заготовок минимальную величину припуска определяют на диаметр по формуле:
3.1. Элементы припуска Rzi-1 и hi-1 для поковок, изготовляемых штамповкой определяют по массе заготовки.
Rzi-1=Rz=160мкм hi-1=200мкм (1, табл.12 стр.186)
(если заготовка получена литьем см.табл.6-10 с.182-185) данные заносят в графу 2,3
![]() |
1.2. Суммарное отклонение расположения поверхностей, возникшее на предыдущей операции при обработке заготовки в патроне для наружной поверхности определяют по формуле(1, форм.31,стр.187):
где: - изогнутость оси (кривизна стержня)
- смещение оси фланца относительно оси стержня
При консольном креплении кривизна стержня:
,
где: - величина предельного отклонения относительно оси детали, приходящаяся на 1мм длины стержня,
L – расстояние от сечения, для которого определяют величину отклонения до места крепления заготовки, мм.
При консольной обработке заготовки L<Lз, при обработке в центрах L<0.5Lзаг,
где: Lзаг – общая длина заготовки, мм: Δк = 8мкм/мм (т.19,стр.187)
Смещение оси фланца относительно оси стержня:
=0.5мм=500мкм (1, т.20, стр.187)
![]() |
Суммарное отклонение:
Данные заносят в графу 4.
1.3. Погрешности установки при черновом точении:
где: Еб – погрешность базирования
Езак – погрешность закрепления
Епр – погрешность приспособления
Епр в расчетах можно не учитывать в виду ее малой величины. Еб зависит от схемы базирования (см. Вардашкин. Станочные приспособления).
![]() |
Заготовка устанавливается в патроне и имеет место погрешность центрирования:
Где: Tdi-1- допуск на диаметральный размер базы заготовки, мм
![]() |
При Tdi-1>1, величину погрешности центрирования рассчитывают по формуле:
Базой заготовки служит фланец 100мм.
Величина допуска на диаметральный размер заготовки для поковки нормальной точности, масса заготовки 1.5кг, группа стали М1 (углеродистая сталь с содержанием углерода до 0.45% и до 2% легирующих элементов), степень сложности С1.
![]() |
1.4. Минимальный расчетный припуск на черновое точение:
4. Расчет припуска на чистовое точение.
2.1.Элементы припуска Rzi-1 и hi-1 штампованных поковок после механической обработки (черновое точение h12)
Rzi-1=50мкм hi-1=50мкм (1, табл.25, стр.188)
![]() |
2.2. Суммарное отклонение расположения заготовки после чернового точения:
где: Ку – коэффициент уточнения
- кривизна заготовки
Ку=0.06 (табл.29, стр.190)
![]() |
2.3. Остаточная погрешность установки при чистовом точении:
Е2=Ку*Е1+Еб2
Т.к. черновое точение и чистовое производятся в одной установке, то Еб2=0
Е2=0.06*450=27мкм
2.4. Минимальный припуск на чистовое точение:
![]() |
3. Расчет припуска на шлифование
3.1. Элементы припуска Rzi-1 и hi-1 после чистового точения
Rzi-1=25мкм hi-1=25мкм (1, табл.25, стр.188)
Примечание: если деталь подвергается термообработке, то поверхностный слой должен быть сохранен. В этом случае значение hi-1=25мкм в графу 3 не заносят.
3.2.
Суммарное отклонение расположения поверхности определяется как остаточное отклонение расположения заготовки после чистового точения.
Ку=0.04 (табл.29, стр.190)
3.3.Погрешность установки при шлифовании:
Еу=30мкм (табл.12,стр.41)
![]() |
3.4. Минимальный припуск на шлифование:
4. Расчетный минимальный размер по переходам:
- шлифование dр3=24,927мм
- чистовое точение dр2=24,927+0,160=25,087мм
- черновое точение dр1=25,087+0,294=25,381мм
- заготовка dрзаг=25,381+2,285=27,666мм
5. Принятый (округленный) минимальный размер:
- шлифование dр3=24,927мм
- чистовое точение dр2=25,09мм
- черновое точение dр1=25,38мм
- заготовка dрзаг=27,67мм
6. Принятый максимальный размер по переходам:
- шлифование dр3=24,927+0,033=24,96мм
- чистовое точение dр2=25,09+0,13=25,22мм
- черновое точение dр1=25,38+0,21=25,59мм
- заготовка dрзаг=27,67+1,8=29,47мм
7. Предельный минимальный припуск по переходам:
- шлифование 25,09-24,927=0,163мм
- чистовое точение 25,38-25,09=0,29мм
- черновое точение 27,67-25,38=2,29мм
2,743мм
8. Предельный максимальный припуск по переходам:
- шлифование 25,22-24,96=0,26мм
- чистовое точение 25,59-25,22=0,37мм
- черновое точение 29,47-25,59=3,88мм
4,51мм
9. Проверка:
1800-33=1767мкм
4.51-2.743=1.767мм=1767мкм
АНАЛИТИЧЕСКИЙ РАСЧЕТ
1. Определение массы детали
Отливка 1 класса точности q=3.5 кг
2. Разработка технологического маршрута обработки заданной поверхности детали. Ø50 Н9
растачивание черновое Н11(+0,160)
растачивание чистовое H9(+0, 062)
Дата добавления: 2018-09-20; просмотров: 265; Мы поможем в написании вашей работы! |
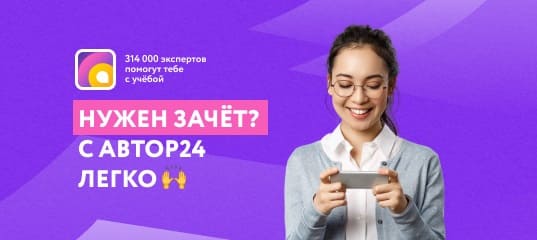
Мы поможем в написании ваших работ!