Измерение расхода и количества (сложно)
В промышленности учет расхода жидкостей, пара и газа ведут с помощью двух групп приборов: расходомеров, измеряющих расход вещества, т. е. его количество, протекающее по трубопроводу в единицу времени, и счетчиков количества, измеряющих суммарный объем или массу вещества, протекающего по трубопроводу.
Часть расходомеров оборудована счетными устройствами, служащими как для измерения расхода, так и для определения суммарного расхода за определенный промежуток времени. Наиболее широко применяют расходомеры переменного и постоянного перепада. Расход вязких жидкостей, например мазута, измеряют ультразвуковыми расходомерами. Однако они сложны и дороги, поэтому их применяют сравнительно редко (в данной книге они не рассматриваются). Расходомеры, основанные на других принципах действия, пока еще не получили широкого распространения.
Расходомеры переменного перепада. Принцип действия расходомеров переменного перепада основан на измерении давления по перепаду, который создается в трубопроводе установленным внутри него сужающим устройством. В суженном сечении увеличиваются скорость, а следовательно, и кинетическая энергия потока, что вызывает уменьшения его потенциальной энергии. Соответственно статическое давление потока после сужающего устройства будет меньше, чем перед ним. Разность между статическими давлениями потока, взятыми на некоторых расстояниях до и после сужающего устройства, называют перепадом давления.
|
|
Простейшая схема измерения расхода по методу переменного перепада давления (рис. 1.7) включает в себя сужающее устройство (диафрагму) 2, установленное в трубопроводе 1, соединительные трубки 3 для отбора давления до сужающего устройства и после него и передачи этого давления к U-образному манометру 4.
Рис. 1.7. Принципиальная схема измерения расхода по методу переменного перепада давления: 1 - трубопровод; 2 - сужающее устройство (диафрагма); 3 - соединительные трубки; 4 - U-образный манометр
Перепад давления р будет тем больше, чем больше скорость потока, т. е. чем больше расход. Следовательно, перепад давления на сужающем устройстве является мерой расхода жидкости, газа или пара, протекающих через трубопровод.
К достоинствам расходомеров переменного перепада относится возможность использования их при различных температурах и давлениях измеряемой среды, а к недостаткам — потеря давления потока и относительная трудность промышленного применения расходомеров при малых расходах.
Для измерения расхода по методу переменного перепада давления в качестве сужающих устройств применяют стандартные диафрагмы и сопла, изготовленные в соответствии с требованиями специальных правил.
|
|
В качестве стандартных сужающих устройств используются:
· трубки Вентури;
· трубки Пито;
· расходомерные сопла;
· диафрагмы.
Наиболее часто в качестве сужающего устройства используются диафрагмы.
Расходомерная диафрагма представляет собой диск с отверстием. Диафрагмы бывают бескамерные и камерные. Бескамерная диафрагма 2 (ГОСТ 26969—86) представляет собой стальной диск, имеющий концентрическое (симметричное оси) отверстие с острой кромкой со стороны входа потока и коническую часть со стороны выхода. Толщина диска не должна превышать 0,05 внутреннего диаметра трубопровода. Бескамерные диафрагмы применяют в трубопроводах диаметром более 400 мм. Отбор давления производится непосредственно перед диафрагмой и после нее по ходу потока в трубопроводе. При этом отборное устройство, установленное перед диафрагмой, обозначают знаком «+», а расположенное за диафрагмой —знаком «—».
Камерная диафрагма (рис. 1.8) состоит из диска 1 и двух кольцевых камер 2 и для отбора давления до диафрагмы и после нее. Камеры соединяются с внутренним пространством трубопровода через кольцеобразные щели А и Б, расположенные непосредственно у торцовой поверхности диафрагмы. Таким образом, отбор давления в камерных диафрагмах производится по периметру трубопровода для измерения среднего давления в трубопроводе. К камерам присоединяют трубки 5 и 6, передающие перепад давления от диафрагм к дифманометру.
|
|
Рис. 1.8. Камерная диафрагма: 1 - диск; 2, 3 - кольцевые камеры; 4, 7 - фланцы; 5, 6 - соединительные трубки; 8 - прокладки; 9 -болты
Камерные диафрагмы применяют в трубопроводах с внутренним диаметром от 50 до 400 мм. Диафрагму и кольцевые камеры изготовляют из материалов, устойчивых к длительным воздействиям измеряемой среды. Чаще всего диск делают из нержавеющей, а камеры—из углеродистой стали. К качеству механической обработки поверхностей камерных диафрагм и других сужающих устройств предъявляют повышенные требования. Отверстие диска со стороны входа потока цилиндрическое на длине по оси не более 0,02 внутреннего диаметра трубопровода, а далее расточено на конус под углом 45° у выхода потока. Кромка отверстия диска у входа потока острая, без закруглений, вмятин и заусенцев. Угол между торцовой поверхностью диафрагмы и цилиндрической частью отверстия 90°.
|
|
Камерные диафрагмы устанавливают на прямолинейных участках трубопроводов между двумя фланцами 4 и 7, стягиваемыми болтами 9. Для уплотнения соединения между фланцами и кольцевыми камерами, а также между камерами и диском ставят прокладки 8. Материал для прокладок выбирают в зависимости от химических свойств и давления измеряемой среды.
Расходомерное сопло (рис. 1.9) состоит из плавно сужающейся части на входе и цилиндрической — на выходе.
Кромка цилиндрической части острая, без фасок, закруглений и заусенцев. Очертание профильного отверстия сопла подобно очертанию струи при входе ее в сужающее устройство, поэтому в нем образуется значительно меньше завихрений, приводящих к безвозвратной потере давления потока, чем в диафрагме. Кроме того, сопла более стойки к истиранию и менее подвержены загрязнению. Но из-за сложности изготовления их применяют редко.
Рис. 1.9. Расходомерное сопло
Давление отбирают до начала сужения потока и в начале цилиндрической части сопла. На рисунке показаны два варианта отбора давления через кольцевые камеры (вверху) и через отдельные отверстия непосредственно у сужающего устройства (внизу).
Достоинства метода переменного перепада давления
1. Универсальность. Данный метод применяется для измерения расход практически любых сред: жидкостей, газа, пара. Для вязких жидкостей применяются сужающие устройства специальной формы.
2. Низкая первоначальная стоимость. Стоимость расходомера, основанного на методе переменного перепада давления, складывается, исходя из стоимости сужающего устройства, импульсных линий и датчика дифференциального давления.
3. Беспроливная методика поверки. Для периодической поверки расходомеров на СУ требуется измерить геометрические размеры сужающего устройства и поверить датчик дифференциального давления.
4. Отсутствие движущихся частей.
5. Измерение расхода в условиях высокого давления. Давление в трубопроводе может достигать 40МПа.
6. Измерение расхода в условиях высоких и низких температур. Диапазон температуры измеряемой среды лежит в пределах от -200 до +1000°С.
7. Широкий диапазон типоразмеров. Метод переменного перепада давления используется как на трубопроводах с малым диаметром условного прохода (Ду = 15 мм), так и на больших трубопроводах (Ду = 2000 мм).
Недостатки метода переменного перепада давления
1. Узкий динамический диапазон. Стандартный динамический диапазон сужающих устройств приблизительно 1:3. Такое ограничение связано, в первую очередь, с квадратичной зависимостью между расходом и перепадом давления на СУ. Использование высокоточных датчиков дифференциального давления позволяет увеличить динамический диапазон.
2. Высокая стоимость эксплуатации. Расходомеры на сужающих устройствах требуют периодического обслуживания: измерение геометрических размеров сужающего устройства, прочистка импульсных линий, прогрев импульсных линий, установка нуля на датчике дифференциального давления.
3. Небольшой межповерочный интервал. Стандартный межповерочный интервал расходомера на СУ составляет – 1 год.
4. Низкая точность измерений. Погрешность измерений обычно менее 3,0-3,5 %.
Камерный метод измерения расхода. Камерные расходомеры измеряют объемный расход напрямую путем повторяющегося захвата порции жидкости. Общий объем жидкости, проходящей через расходомер в заданный промежуток времени, – это произведение объема порции на количество порций. Камерные расходомеры часто суммируют расход напрямую на встроенный счетчик, но они также могут генерировать импульсный выход, который может быть прочитан на местном ЖКИ или передан в комнату управления. Так как каждый импульс представляет дискретный объем жидкости, они хорошо подходят для автоматического дозирования и учета. Снижение точности камерных расходомеров связано с просачиванием через внутреннюю изолированную поверхность. Три основных типа таких расходомеров: поршневые счетчики, счетчики с овальными шестернями и дисковые счетчики.
Достоинства камерного метода измерения расхода
1. Невысокая стоимость. Простота метода измерения определяет невысокую себестоимость камерных расходомеров.
2. Возможность измерения малых расходов.
Недостатки камерного метода измерения расхода
1. Наличие движущихся частей. Износ движущихся механизмов приводит к снижению точности измерений или к возможному выходу из строя расходомера.
2. Сложность ремонта. Обычно ремонт камерных расходомеров возможен только в заводских условиях.
Вихревые расходомеры. При определенных условиях движения потока среды, часть кинетической энергии потока может преобразовываться в пульсации (завихрения). Частота следования этих пульсаций пропорциональна скорости потока.
Общие характеристики для большей части вихревых расходомеров:
1. Стандартный выходной частотный сигнал.
2. Широкий динамический диапазон (от 1:10 до 1:40).
3. Достаточно высокая точность измерений.
4. Независимость точности измерения расхода от изменений температуры, давления и плотности измеряемой среды.
5. Высокая повторяемость и стабильность показаний.
6. Простота конструкции, легкость в монтаже, низкая стоимость обслуживания.
7. Универсальность принципа – измерение жидкостей, газа и пара.
Существует несколько основных типов вихревых расходомеров, отличающихся по способу образования вихрей. Наиболее распространенный тип, у которого поперек потока измеряемой среды установлено плохообтекаемое тело (тело обтекания, вихревое тело, вихреобразователь), за которым поочередно с разных сторон образуются вихри.
Принцип действия. При обтекания потоком неподвижного препятствия (тела обтекания) образуются вихри. Образование вихрей и их отрыв от тела обтекания происходит поочередно с разных его сторон.
Рис. 1.10. Принцип работы вихревых расходомеров
Развитие вихря с одной стороны препятствует его образованию с противоположной стороны. За телом обтекания образуется двойная дорожка из вихрей, называемая «дорожкой Кармана».
Частота вихреобразования (частота отрыва вихрей) пропорциональна скорости потока, а значит и расходу. Зависимость между частотой вихреобразования и скоростью (расходом) определяется критерием Струхаля:
St = f*d/W,
где f – частота вихреобразования,
d – характерный размер тела обтекания,
W – средняя скорость потока.
Частота вихреобразования определеяется формулой:
f = St*W/d.
Для характеристики вихревых расходомеров вместо числа Струхаля используется К-фактор. Производители под К-фактором подразумевают либо:
- число вихрей, приходящихся на единицу объема среды:
Кф = n/V
- объем среды, приходящийся на один вихрь:
Кф = V/n,
где n – число вихрей за время t;
V – объем среды за время t.
Основное уравнение вихревого расходомера:
f = Kф*W/d.
К-фактор условно постоянен в определенном диапазоне чисел Re и не зависит от плотности, вязкости, скорости потока и др. свойств среды. Диапазон чисел Рейнольдса, при которых К-фактор постоянен называется рабочей областью (областью измерений) вихревых расходомеров.
Рис.1.11. К-фактор
Конструкция вихревых расходомеров. В общем виде, вихревой расходомер состоит из двух частей: первичного преобразователя и вторичного преобразователя (электронного блока или конвертера).
Рис.1.12. Общие элементы конструкции вихревых расходомеров
Первичный преобразователь включает в себя вихреобразователь (тело обтекания) и устройство детектирования вихрей (сенсор). Электронный блок состоит из фильтра, усилителя, АЦП и схемы выходных сигналов. С развитием микропроцессорной электроники появились интеллектуальные вихревые расходомеры, в которых сигнал с АЦП проходит обработку. Помимо улучшения точности измерения и сведения к минимуму влияний факторов температуры, давления, нелинейности К-фактора, неравномерности потока и др., появилась возможность использования цифровой коммуникации и добавления дополнительной функциональности (например, функции вычислителя-счетчика) в расходомере.
Вихреобразователь или вихревое тело – это один из главных компонентов первичного преобразователя, во многом определяющий метрологические характеристики расходомера (линейность и повторяемость, пределы измерения) и потери давления. В целом, при выборе оптимального вихреобразователя, производители расходомеров руководствуются следующими требованиями:
1. вихри не должны пересекатья для их однозначного детектирования;
2. генерация вихрей должна быть стабильна (постоянство числа Струхале) в широком диапазоне чисел Рейнольдса;
3. вихри должны быть достаточно сильными для детектирования, должно быть высокое соотношение сигнал-шум;
4. форма и структура тела обтекания должна быть достаточно простой и технологичной;
5. геометрия и материал исполнения тела обтекания должны исключать влияние коррозии и температуры на метрологические характеристики прибора;
6. спектр частот вихрей как жидкостей так и газов не должен перекрываться со спектром естественных и промышленных частот (вибрация трубопровода, частота самовозбуждения сенсора и др.).
Существует достаточно большое число разновидностей вихреобразователей, которые можно разделить на две группы: состоящие из одной части и состоящие из двух и более частей.
Наиболее распространенными являются вихревые тела, состоящие из одной части, такие, как цилиндрическое, прямоугольное, треугольное и трапециевидное тела.
Рис.1.13. Простые тела обтекания
Некоторые производители используют более сложные многосоставные тела обтекания.
Рис.1.14. Сложные составные тела обтекания
Методы детектирования вихрей, получивших наибольшее распространение:
1. Детектирование пульсации вихрей (вихревые расходомеры пульсаций давления и вихревые расходомеры изгибных напряжений).
2. Детектирование вихрей с помощью изменения электрической емкости чувствительного элемента (вихревые емкостные расходомеры).
3. Детектирование вихрей с помощью ультразвуковых волн (вихреакустические расходомеры).
4. Терморезистивный и термоанемометрический метод детектирования (термальные вихревые расходомеры).
5. Электромагнитное детектирование вихрей (вихревые электромагнитные расходомеры).
Вихревые расходомеры изгибных напряжений. Для детектирования вихрей за телом обтекания (или внутри него) устанавливается подвижное тело (крыло или трубка), на которое поочередно с разных сторон воздействуют вихри потока. Под действием давления вихрей выступающее тело изгибается и передает воздействие на чувствительный элемент. В качестве чувствительного элемента преимущественно используются пьезокерамические элементы, преобразующие механическое воздействие в электрический сигнал, который в дальнейшем усиливается и фильтруется.
Сенсоры на основе пьезоэлементов отличаются быстродействием, хорошим уровнем сигнала, высокой технологичностью, низкой стоимостью изготовления, отсутствием контакта с измеряемой средой и высокой повторяемостью.
Вихревые расходомеры изгибных напряжений отличаются широким температурным диапазоном, универсальностью, высокой стабильностью и надежностью, что сделало их наиболее распространненым типом вихревых расходомеров.
Тем не менее, такие приборы весьма чувствительны к вибрациям трубопровода, что является их главным недостатком последние несколько лет. Несмотря на разработки некоторых производителей в направлении улучшения структуры сенсора и последующей интеллектуальной обработки сигнала, в условиях сильной вибрации расходомер может не работать.
Емкостные вихревые расходомеры.Пульсации давления вихрей воздействуют на емкостные ячейки сенсора, деформируя их поверхность, и, соответственно, изменяя емкость ячеек. Дифференциальная схема обработки сигнала позволяет существенно снизить влияние внешних источников вибрации за счет взаимоподавления шумов, приходящих с разных емкостей. Несмотря на невозможность изготовления абсолютно идентичных конденсационных ячеек, способных полностью исключить влияние вибрации, виброустойчивать вихревых расходомеров с емкостным способом съема сигнала достаточно высокая (порядка 1g).
Другим преимуществом таких расходомеров является возможность работы на высоких температурах до 400ºС. С ростом температуры изменяются диэлектрическая проницаемость и геометрия электродов, а также растут токи утечки за счет температурной эмиссии электронов. Однако эксперименты показывают, что описанные эффекты практически не влияют на работу приборов.
Вихреакустические расходомеры
Принцип действия вихреакустических расходомеров показан на рис.1.15.
Рис.1.15. Принцип действия вихреакустического расходомера
Для детектирования вихрей используются пары излучатель-приемник (одна или две), установленные в стенки корпуса прибора. При этом излучатели постоянно излучают высокочастотные акустические сигналы, пересекающиеся в центре проточной части.
Каждый из чередующихся вихрей отличается направлением вращения от предыдущего. При пересечении с вихрем, происходит модуляция ультразвуковой волны по фазе, которая фиксируется приемниками сигнала, преобразовывается в электрический сигнал и обрабатывается.
Приборы отличаются высокой чувствительностью, что позволяет их использовать для измерений на низких расходах. При этом зависимость точности измерений от температуры среды (особенно для газов) и влияние механических и газовых включений на процесс измерений, ограничили область использования вихреакустических расходомеров, сузив ее до чистых жидкостей и небольшого числа разновидностей газов.
Вихревые электромагнитные расходомеры. Особенности конструкции вихревых расходомеров с электромагнитным съемом сигнала представлен на рис.1.16. При движении электропроводной жидкости (проводника) в поле постоянного магнита наводится ЭДС. Вихри создают возмущение или пульсации ЭДС, которые фиксируются электродом, установленным за телом обтекания. Частота пульсаций ЭДС соответствует частоте вихреобразования. Такие расходомеры отличаются простой конструкции, возможностью автономного батарейного питания, низкой стоимостью, возможностью проведения имитационной поверки.
Рис. 1.16. Принцип действия вихревого электромагнитного расходомера
При этом приборы склонны к образованию отложений в проточной части вблизи магнита, имеют нестабильные метрологические характеристика и могут работать только в электропроводных средах.
Счетчики количества(сложно)
Счетчики количества жидкости по принципу действия подразделяют на скоростные, объемные и весовые. Скоростные бывают со спиральной горизонтальной (для измерения больших расходов) и с вертикальной (малых расходов) вертушкой. Счетчики с вертикальной вертушкой, а также весовые не получили широкого распространения в промышленности, поэтому их рассматривать не будем.
Скоростные счетчики со спиральной горизонтальной вертушкой устанавливают в закрытых трубопроводах таким образом, чтобы через них проходил весь поток измеряемой жидкости. Протекающий через счетчик поток измеряемой жидкости воздействует на вертушку: чем больше средняя скорость протекающей жидкости, а, следовательно, и ее количество, тем быстрее вращается вертушка. Вертушка механически связана со счетным механизмом, шкала которого отградуирована в единицах количества (как правило, в м3 ).
Счетный механизм прибора может быть помещен непосредственно в измеряемой жидкости или защищен от нее сальником. В приборах, счетный механизм которых находится в измеряемой жидкости, показания отсчитывают через защитное стекло, отделяющее камеру расходомера от наружной среды. Такие приборы по своей конструкции более просты, однако их детали быстро изнашиваются от воздействия жидкости.
Поток поступающей жидкости выравнивается струевыпрямителем 2 (рис. 1.17) и направляется на лопатки вертушки 3, которая выполнена в виде многозаходного винта. Вращение вертушки через червячную пару и передаточный механизм 4 передается счетном механизму 5.
.17. Скоростной счетчик со спиральной горизонтальной вертушкой: 1 - корпус; 2 - струевыпрямитель; 3 -вертушка; 4 - передаточный механизм; 5 - счетный механизм
Объемные счетчики делятся на приборы с овальными шестернями, поршневые и дисковые. Рассмотрим принцип действия наиболее распространенного в промышленности счетчика с овальными шестернями (рис. 10.18). Его действие основано на вытеснении из измерительной камеры 1 прибора определенных объемов жидкости вращающимися овальными шестернями 2.
Обе шестерни находятся в непрерывном зацеплении и обкатывают друг друга. При этом на них действует разность давлений: между большим со стороны входа жидкости и меньшим со стороны выхода. В результате перепада давлений в трубопроводе (до и после счетчика) образуется сила, заставляющая шестерни вращаться. При этом каждая из шестерен при полном обороте проталкивает половину объема жидкости, поступающей в камеру, а обе шестерни за один оборот пропускают количество жидкости, равное полному объему камеры прибора.
Рис. 1.18. Схемы ( I- III) работы объемного счетчика с овальными шестернями: 1 - камера; 2 - шестерни
Частота вращения овальных шестерен неравномерна и зависит в каждый момент времени от их взаимного расположения. Но это не влияет на процесс измерения, так как счетчик подсчитывает только число оборотов шестерен.
Вращение шестерен передается посредством магнитной муфты и передаточного механизма стрелочному указателю и счетному механизму. Магнитная муфта отделяет внутренние полости камеры от внешней среды, что дало возможность отказаться от сальниковых уплотнений, которые увеличивают трение.
Счетчики количества газа делятся на барабанные (для лабораторных измерений), клапанные (в основном используют в быту) и ротационные (для измерения больших количеств газа). Последние широко применяют в промышленности.
Механизм вращения лопастей ротационного газового счетчика аналогичен механизму вращения овальных шестерен для счетчиков количества жидкости. Валы каждой из лопастей вне корпуса имеют на конце шестерни, находящиеся в зацеплении, благодаря чему движение одной лопасти передается другой.
Благодаря тщательной обработке внутренней поверхности корпуса и трущихся поверхностей лопастей, а также точной их подгонке утечки газа в таких счетчиках минимальны. По сравнению с остальными газовыми счетчиками ротационные имеют меньшие габариты при одних и тех же пределах измерения.
Электромагнитные расходомеры (ЭМР). В основу работы ЭМР положен закон электромагнитной индукции Майкла Фарадея, согласно которому изменение полного магнитного потока Ф порождает в проводнике пропорциональную ему
индукционную электродвижущую силу (э.д.с.Е)
При этом э.д.с. возникает независимо от причины изменения магнитного потока – как от изменения самого поля, так и от движения проводника. Поэтому при движении проводящей жидкости в магнитном поле на ней наводится э.д.с. пропорциональная скорости изменения магнитного потока, а значит скорости движения жидкости.
Конструкции первичных преобразователей. Конструктивно первичный преобразователь расхода (ППР) электромагнитного типа состоит из проточной части – трубы из немагнитной стали, имеющей изоляционное покрытие, электродного узла, включающего два или более электродов и индуктора, состоящего из двух катушек и создающего магнитное поле.
Кроме трубы с футеровкой существуют конструкции с трубой из непроводящего материала и даже из металлической трубы без изолирующего покрытия. В последнем случае ППР, кроме изолированных от трубы измерительных электродов, имеет также две пары токовых и потенциальных электродов, с помощью которых сервоусилители, задают ток в трубе, пропорциональный расходу, поддерживая потенциал проводящей трубы равный потенциалу измерительного электрода.
Футеровка является самым практичным и применяемым элементом конструкции ППР. Материал футеровки определяет как технические параметры (стабильность геометрических размеров и формы), так и технологические (диапазон допустимых температур и давлений рабочей среды), и, кроме того, эксплутационные характеристики (надежность, долговечность). В качестве изоляционного покрытия используются: твердая резина, полиэтилены, полипропилены, эмаль, стекловолокно, фторопласты, в том числе армированные сеткой из нержавеющей стали для повышения прочности, керамика и т.п.
Для ППР больших диаметров при измерении водных растворов используется также твердые и обычные резины на базе фторкаучуков и бутиленовых каучуков.
Электродная система – весьма ответственный узел ЭМР, определяющий возможность утечек рабочей среды по электродам вследствие термоударов, вакуумирования и других причин. Электроды выполняются из различных металлов, обладающих высокой коррозионной стойкостью к измеряемой среде: никельсодержащие аустенитные стали (316L, 12Х18Н10Т), сплавы Ni-Mo (HastelloyÔ B, C, F), Ni-Cu (MonelÔ) Pt, Ti, Ta, Zr. Для компенсации термического и усталостного расширения применяют пружинные компенсаторы, а для контроля утечек – контрольные контакты. Поскольку наличие уплотнений имеет теоретическую возможность утечек, предпринимаются попытки исключить этот элемент, например, изготовлением цельной конструкции электрод-труба. 99,9%) к керамической трубе с помощью припоя на основе сплава Au-Ti.
ППР оснащают также дополнительными конструктивными элементами, например заземляющими кольцами или фланцами, которые выполняют как функцию центрирования ППР относительно трубопровода, так и обеспечивают электрическую связь с рабочей средой. При отсутствии заземляющих колец или фланцев, в трубу ППР вводится дополнительный (третий) электрод, который, кстати, может использоваться также для целей диагностики состояния процесса, неполного заполнения или опустошения канала.
Радикальное решение проблем утечек это отказ от контакта со средой и переход к бесконтактному (емкостному) принципу съема сигнала, позволяющий не только избежать утечки по электродам, но и исключить коррозию электродов, какое-либо искажение потока, позволяет измерять расходы жидкости с крайне низкой проводимостью. Недостатком такой конструкции следует считать несколько большую погрешность измерений, менее устойчивый измерительный сигнал и ограниченный ряд Ду используемых первичных преобразователей с проточной частью, выполненной из керамики.
Значительное потребление электроэнергии ЭМР по сравнению с другими принципами измерения расхода является, пожалуй, одним из главных недостатков метода. Самодиагностика узлов ЭМР и линий связи, предполагалась как одна из опций повышающая потребительские свойства ЭМР, но не более того. Диагностика работоспособного состояния ЭМР, включая метрологическую достоверность измерений, имеет крайне важное значение при учетных операциях (custody transfer), так как является основой для взаимных расчетов и предъявления претензий. Система диагностики новейших ЭМР серии Optiflux фирмы Krohne de facto задает новый стандарт для ЭМР нового поколения. Она охватывает не только практически все внутренние устройства ЭМР, но и состояние процесса и смежных устройств.
Дата добавления: 2018-09-20; просмотров: 685; Мы поможем в написании вашей работы! |
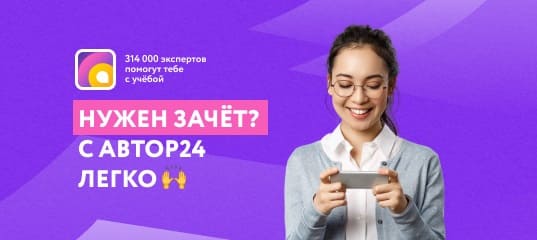
Мы поможем в написании ваших работ!