Краткое описание объекта производства и технологических процессов
В этом разделе работы должно быть краткое описание объектов производства и их назначение, указаны материал, из которого изготавливаются детали, вес заготовок и чистый вес деталей каждого типоразмера (наименования), оптовая цена материала и реализуемых отходов, а также количество деталей на изделие. Исходные данные по типоразмерам обрабатываемых деталей сводят в таблицу 3.1.
Описание технологического процесса изготовления детали каждого типоразмера производится исходя из задания, выдаваемого руководителем курсовой работы. В задании по каждой операции должны быть указаны используемое технологическое оборудование, его технико-экономические характеристики, разряд работы по операциям и нормы времени по базовому и проектируемому вариантам (таблица 3.2). Время на операцию включает в себя основное (машинное) время ( ), вспомогательное (ручное или роботизированное) время (
) и время на переналадку оборудования (
), необходимое для перехода от одного типоразмера (номенклатуры) деталей к другому (для упрощения расчетов в него можно включить подготовительно-заключительное время, время, затрачиваемое на изготовление пробных деталей (как правило, 2–3 шт.), время на коррекцию ЧПУ и настройку инструмента).
Продолжительность переналадки оборудования зависит от номенклатуры изготавливаемых типоразмеров деталей и количества партий дета-
Таблица 3.1 – Исходные данные (условные) для расчета
|
|
Наименование детали | Вид заготовки | Материал (марка) | Норма расхода материала на одну деталь, кг. | Чистый вес детали, кг. | Оптовая цена 1 кг. материала, руб. | Оптовая цена 1 кг. отходов, руб. |
Таблица 3.2 – Технологические процессы изготовления детали и модели оборудования
Наименование операции | Разряд рабочего | № детали | Базовый вариант | Проектируемый вариант | ||||||||
модель оборудования или марка | затраты времени, мин. | модель оборудования или марка | затраты времени, мин. | |||||||||
![]() | ![]() | ![]() | ![]() | ![]() | ![]() | ![]() | ![]() | |||||
лей по каждому типоразмеру, запускаемых в производство в течение планового периода.
Расчет календарно-плановых нормативов
Прежде всего необходимо определить календарный фонд времени ( = 365 (366) дней, затем — номинальный фонд времени работы оборудования
, (3.1)
где – количество выходных и праздничных дней.
|
|
Номинальный годовой фонд времени работы оборудования в часах при работе в одну смену рассчитывают по формуле
, (3.2)
где – количество полных рабочих дней;
– продолжительность рабочей смены, ч. (
= 8 ч);
– количество предпраздничных, сокращенных на один час дней;
– продолжительность предпраздничной рабочей смены, ч. (
= 7 ч).
Годовой эффективный фонд времени работы оборудования в часах определяют по формуле
, (3.3)
где – коэффициент, учитывающий время простоя оборудования в плановом ремонте (для уникальных станков и станков свыше 30-й категории сложности
= 0,90, для станков с ЧПУ
= 0,80, для обрабатывающих центров
= 0,75).
Годовой эффективный фонд времени в днях с учетом простоев оборудования в плановых ремонтах исчисляют по формуле
. (3.4)
Количество партий деталей зависит от номенклатуры обрабатываемых деталей ( ) и количества дней (смен) работы оборудования (
), если запуск (выпуск) всех видов деталей осуществляется ежедневно (ежесменно). Для базового варианта
= 2. В связи с тем что при гибком автоматизированном производстве не требуется большого количества рабочих-операторов и участок оснащен весьма дорогостоящим оборудованием, производственный процесс целесообразно осуществлять в три смены (
= 3). При ежесменном запуске деталей количество партий определяют по формуле
|
|
, (3.5)
где – число рабочих смен в сутки.
Количество переналадок оборудования на каждой операции ( ) будет равно количеству партий деталей
. (3.6)
Годовой фонд времени, затрачиваемый на переналадку оборудования, определяют по формуле
(ч.), (3.7)
где – время на переналадку оборудования на соответствующей операции, устанавливаемое для партии деталей, мин;
– количество переналадок оборудования на соответствующей операции в течение планового периода.
Для расчета фонда времени, затрачиваемого на переналадку оборудования, используют таблицу (таблица 3.3).
Таблица 3.3 – Расчет фонда времени, затрачиваемого на переналадку оборудования
Наименование операции | Базовый вариант | Проектируемый вариант | ||||
![]() | ![]() | ![]() | ![]() | ![]() | ![]() | |
Гибкие производственные участки обычно создают для обработки деталей различных типоразмеров (наименований), используемых для изготовления изделия. Следовательно, программы выпуска по каждому типоразмеру или равны, или кратны между собой.
|
|
Если программы по типоразмерам равны, т. е. , то их величину можно определить исходя из следующего уравнения
, (3.8)
где – программа выпуска деталей
-го типоразмера на плановый (годовой) период, шт.;
,
, …
– оперативное время по каждому типоразмеру деталей по ведущей группе оборудования проектируемого варианта, по которой определяется мощность участка по отдельной операции технологического процесса, мин.
Если программы по типоразмерам не равны, но кратны, то их величину можно определить исходя из выражения
, (3.8)
;
; …;
.
В качестве ведущей группы оборудования обычно выбирают наиболее дорогостоящее, однако это зачастую приводит к низкой загрузке оборудования на других операциях. Поэтому, если спрос на продукцию предприятия достаточно велик, для повышения загрузки оборудования на всех операциях за ведущую группу можно принимать оборудование, используемое на операции с наименьшим суммарным оперативным временем по всей номенклатуре деталей.
Размер партии деталей -го типоразмера (наименования) определяют по формуле
, (3.9)
где – количество партий деталей -гo типоразмера.
Необходимое количество единиц оборудования рассчитывают по формуле
, (3.10)
где – время, затрачиваемое на переналадку оборудования на каждой
-й операции, ч. (см. таблицу 3.3);
– программа деталей
-го типоразмера (наименования), шт.;
– оперативное время на
-й операции деталей
-го типоразмера (наименования), мин;
– номенклатура обрабатываемых деталей;
– коэффициент выполнения норм времени (в пределах 1,0–1,1).
Расчет количества единиц оборудования по операциям технологического процесса производится в табличной форме (таблица 3.4).
В курсовой работе данную таблицу (см. таблицу 3.4) следует продолжить по данным проектируемого варианта.
Коэффициент загрузки оборудования в идеале должен быть равен единице, но на практике он только стремится к ней. Необходимо также понимать, что коэффициент загрузки оборудования не должен быть больше единицы.
Для достижения максимального значения коэффициента загрузки оборудования могут быть использованы различные методы. Например, можно в указанных пределах варьировать коэффициент выполнения норм времени, в случае низкой трудоемкости сократить количество смен.
Организация производственного процесса партиями предусматривает использование последовательно-параллельного вида движений предметов труда. При механизации и автоматизации производства чаще всего применяют последовательно-параллельный вид движений, так как он обеспечивает такое частичное совмещение времени выполнения смежных операций, при котором вся изготавливаемая партия деталей проходит через каждую опера-
Таблица 3.4 – Расчет необходимого количества единиц оборудования и коэффициента его загрузки
Расчетные показатели | Программа выпуска, шт. | Вид операции, модель оборудования | ||||
… | … | и т. д. | ||||
![]() | ![]() | ![]() | ![]() | … | ||
Базовый вариант | ||||||
Валик 16×172 | … | |||||
И. т. д. | … | |||||
Итого |
|
| … | |||
Годовой эффективный фонд времени работы оборудования ( |
|
| … | |||
Коэффициент выполнения норм времени ( |
|
| … | |||
Расчетное количество единиц оборудования ( |
|
| … | |||
Принятое количество единиц оборудования ( |
|
| … | |||
Коэффициент загрузки оборудования ( |
|
| … |
цию без каких-либо перерывов. Детали с операции на операцию передаются поштучно или небольшими транспортными партиями. Оборудование работает непрерывно, может работать в автоматическом режиме.
Длительность производственного цикла при использовании последовательно-параллельного вида движений партий деталей определяют по формуле
, (3.11)
где – величина партии деталей
-го типоразмера (наименования), шт.;
– оперативное время на
-й операции
-го типоразмера деталей, мин;
– минимальное оперативное время на каждой паре смежных операций (если на операции установлено несколько станков, то
делится на количество станков), мин;
– количество операций технологического процесса изготовления деталей.
Пример 3.1. Проведем расчет длительности производственного цикла ( ) по проектируемому варианту, представленному в табл. 3.2. Исходные данные для расчета представлены в таблице 1.
Итак, технологический процесс изготовления деталей предполагает выполнение пяти операций ( = 5); номенклатура обрабатываемых деталей (
) равна 4; размер партии деталей по каждому типоразмеру (
) — 33; продолжительность выполнения каждой операции приведена в таблице 1; на
Таблица 1 – Затраты времени на выполнение каждой операции технологического процесса по всей номенклатуре обрабатываемых деталей, мин.
Наименование операций | Номенклатура деталей | |||
![]() | ![]() | ![]() | ![]() | |
1. … | 3,5 | 3,5 | 3,5 | 3,7 |
2. … | 2,9 | 2,9 | 2,9 | 3,0 |
3. … | 3,5 | 3,5 | 3,5 | 3,7 |
4. … | 6,1 | 6,4 | 6,4 | 6,4 |
5. … | 6,6 | 7,0 | 7,0 | 7,1 |
первых трех операциях используется по одному станку, на третьей и четвертой операциях — по два станка ( 1,
2).
Рассчитываем длительность производственного цикла по изготовлению деталей ,
,
,
:
= 155,1 мин. = 2,58 ч.;
= 157 мин. = 2,62 ч.;
= 157 мин. = 2,62 ч.;
= 168,7 мин. =2,81 ч.
Однако длительность производственного цикла всей номенклатуры изделий не соответствует сумме циклов изделий ,
,
,
. Поправку к расчету позволит внести построение графика движения изделий по операциям и время на переналадку оборудования таблица 2.
Таблица 2 – Затраты времени на выполнение каждой операции технологического процесса по всей номенклатуре обрабатываемых деталей с учетом станков и партий деталей, мин.
Наименование операций | Номенклатура деталей | |||
![]() | ![]() | ![]() | ![]() | |
1. … | 115,2 | 115,2 | 115,2 | 121,8 |
2. … | 95,4 | 95,4 | 95,4 | 98,7 |
3. … | 115,2 | 115,2 | 115,2 | 121,8 |
4. … | 100,4 | 105,3 | 105,3 | 105,3 |
5. … | 108,6 | 115,2 | 115,2 | 116,8 |
Среднее количество деталей -гo типоразмера (наименования) в незавершенном производстве определяют по формуле
, (3.12)
где – годовая программа запуска изделия
-го типоразмера (наименования).
Внутри цехов заготовки, детали, сборочные единицы в процессе изготовления перевозят между кладовыми (складами) и участками, с одного участка на другой, а на участках — между рабочими местами (технологическим оборудованием). При этом широко используется транспортное оборудование различного типа, в частности ручные тележки, электрокары, транспортеры различных типов, робоэлектрокары, промышленные роботы, манипуляторы.
Одним из основных факторов при выборе транспортного средства для межцеховой транспортировки является грузоподъемность. Поэтому необходимо учитывать размеры партий и вес обрабатываемых деталей.
Количество транспортных средств прерывного (циклического) действия (тележки, робоэлектрокары и др.) определяют по формуле
, (3.13)
где – количество транспортных операций по каждой детали (перевоз материалов на заготовительную операцию, заготовок на участок механической обработки, готовых деталей на склад и др.);
– программа запуска деталей
-гo наименования (сборочных единиц), шт.;
– вес одной детали
-го типоразмера (из исходных данных — норма расхода материала на одно изделие), кг.;
– грузоподъемность транспортных единиц, кг.;
– коэффициент использования грузоподъемности транспортных средств (в пределах 0,6–0,75);
– число рабочих смен в сутки;
– среднее расстояние между пунктами, м. (в пределах 80–150 м);
– средняя скорость движения транспортного средства, м./мин. (в пределах 50–100 м./мин.);
– время на загрузку транспортного средства за каждую операцию,
мин (в пределах 5–10 мин);
– время на разгрузку транспортного средства за каждую операцию,
мин (в пределах 5–10 мин).
Чтобы определить необходимое количество промышленных роботов для обслуживания станков с ЧПУ, необходимо сначала определить, сколько таких станков может обслужить один промышленный робот. Для этого используют формулу
, (3.14)
где – основное (машинное) время, затрачиваемое при обработке одной детали
-го типоразмера (наименования), мин;
– вспомогательное время, затрачиваемое непосредственно промышленным роботом при обслуживании оборудования, мин;
– номенклатура обрабатываемых деталей на данном оборудовании.
Вспомогательное время включает в себя время на выбор детали (заготовки) из общей их совокупности, время перемещения детали в рабочую зону, время соединения детали с рабочим органом станка, время закрепления детали в рабочем органе станка, время удаления готовой детали из рабочей зоны, время возврата промышленного робота в исходное положение.
Если получается дробное число станков, можно изменить скорость передвижения промышленного робота. В результате исключаются простои станков и промышленных роботов. Исходя из количества станков, обслуживаемых одним промышленным роботом, и необходимого количества станков с ЧПУ для выполнения производственной программы (см. таблицу 3.4) определяют необходимое количество промышленных роботов для обеспечения гибкого автоматизированного производства по формуле
, (3.15)
где – принято е количество единиц оборудования;
– количество операций технологического процесса изготовления деталей на данном оборудовании.
Дата добавления: 2018-08-06; просмотров: 318; Мы поможем в написании вашей работы! |
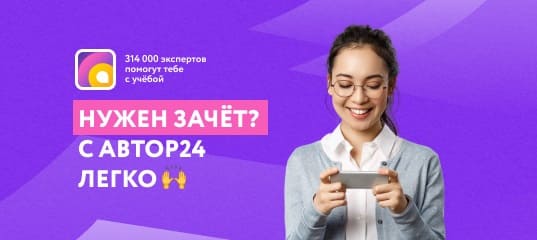
Мы поможем в написании ваших работ!