Факторы, определяющие расход материала
На единицу продукции в швейной промышленности
Главной задачей нормирования материалов является установление прогрессивных технических норм их расхода, так как себестоимость швейных изделий в значительной степени (85-90 %) определяется стоимостью расходуемых на их изготовление материалов. Причем стоимость ткани в этих затратах составляет порядка 50 %.
Норма расхода – предельно допустимое количество материалов для изготовления изделия. Нормы должны быть максимально экономичными, устанавливаться на основании передовых методов работы и быть ориентированы на прогрессивную технологию и новую технику.
На предприятиях действуют отраслевые, оперативные и средневзвешенные нормы расхода материала.
Отраслевые – это средние нормы расхода материалов на единицу каждого вида изделия по группам моделей. Отраслевые нормы в зависимости от способа производства разрабатываются и утверждаются министерствами легкой промышленности или службы сервиса на основе обобщения опыта работы по экономии сырья нескольких десятков передовых предприятий отрасли. На предприятия поступают в виде инструкций, в которых сформулированы основные принципы размещения лекал в раскладке, рекомендованы типовые схемы раскладок лекал, установлены нормативы межлекальных выпадов для ряда основных видов изделий с учетом объективных (не зависящих от квалификации раскладчика) факторов, влияющих на величину межлекальных выпадов в раскладке. Действуют такие нормы несколько лет и подлежат пересмотру при изменении модных силуэтов. По отраслевым нормам контролируют определение закройщиком количества материала, необходимого для изготовления изделия; отраслевые нормы не могут быть превышены при выполнении раскладок.
|
|
Оперативные – это нормы расхода материалов на единицу каждого вида изделия, установленные на предприятиях с учетом разнообразных модельных особенностей, специфики раскройного производства на данном предприятии, шкалы заказов и т. д. Оперативные нормы разрабатывают на все изделия, виды материалов и услуг, не предусмотренные отраслевыми нормами. Такие нормы утверждает руководство предприятия. Они подлежат пересмотру не реже одного раза в год и служат контрольными показателями для закройщиков данного предприятия.
Средневзвешенные групповые (заявочные) – это нормы расхода материалов на единицу укрупненного вида изделия, рассчитывают на основе отраслевых норм с учетом разнообразия групп моделей и процентного соотношения размеров и ростов. Предназначаются такие нормы для определения количества материалов, необходимых для выполнения запланированных объемов и услуг, оказываемых предприятиями.
|
|
На расход материала на единицу швейного изделия оказывают влияние факторы, зависящие и не зависящие от производства.
К факторам, зависящим от производства, относятся:
1. Экономичность конструкции, то есть:
§ соотношение больших и малых деталей в комплекте;
§ форма контуров отдельных деталей (кривизна, наклон линий срезов к линии основы);
§ наличие деталей, раскраиваемых под углом к нитям основы или из другого материала;
§ величина суммарной площади деталей. Размер полезной площади деталей зависит от принятой методики конструирования, размера технологических прибавок на обработку изделия в процессе пошива, размера конструктивных прибавок на свободное облегание, внешнего оформления силуэта, взаимной сопряженности деталей, количества и величины дополнительных деталей и декоративных элементов, величины припусков на образование складок, шлиц и др.
2. Метод нормирования:
· методы определения величины внутренних выпадов;
· точность измерения площади лекал;
· степень обоснованности нормативов потерь материалов при раскрое;
· вид раскладки (лицом вниз, лицом к лицу);
· методы комбинирования и количество комплектов лекал в раскладке.
|
|
3. Техника и организация подготовительно-раскройного и швейного производства:
□ точность измерения ширины и длины, площади материала (применяемые методы и оборудование);
□ квалификация нормировщиков и раскладчиков;
□ условия хранения материала;
□ подбор материалов в настил (в комплект кроя);
□ способ нанесения контуров лекал;
□ величина зазоров между лекалами.
К факторам, не зависящим от производства, относятся:
1. Количество входных материалов:
* длина и ширина кусков ткани;
* вид поверхности материала;
* наличие рисунка, его рапорт;
* наличие дефектов (сортность).
2. Ассортимент продукции:
◊ шкала размеров и ростов;
◊ экономичность моделей;
◊ размер заказа торговой организации.
Расход ткани на единицу изделия по индивидуальным заказам складывается из площади лекал, межлекальных выпадов и припусков на подгонку изделия. Расход материала на единицу изделия, раскраиваемого настилами (серийное и массовое производство), складывается из площади лекал, межлекальных выпадов и припусков по длине настила (на потери при настилании на концах настила). Пример оформления нормировочной карты приведен в прил. 10.
|
|
По данным ведущей в мире фирмы по производству САПР для швейной промышленности Lectra (Франция) [21], суммарные технологические потери (отходы) ткани при производстве швейных изделий составляют в среднем 31 % (от всей используемой ткани).
Из них:
17 % – межлекальные отходы;
2 % – потери по ширине;
2 % – потери при настилании;
3 % – потери при расчете кусков ткани в настилы;
2 % – бракованная ткань;
5 % – потери, обусловленные необходимостью закупки избыточной ткани.
Экономия материалов даже на 1 % в условиях среднего по объему выпуска продукции предприятия (объем выпуска швейных изделий около 30 млн руб. – переработка ткани в год на сумму около 110 млн руб.) эквивалентна экономии порядка 1 млн рублей, т. е. свыше 30 тыс. долларов [20, 28].
При любом производстве основным резервом улучшения использования ткани является сокращение межлекальных (внутренних) выпадов в раскладках лекал, составляющих около 55 % всех технологических потерь ткани. Межлекальные отходы (выпады) – это нежелательные зазоры между лекалами в раскладке, которые возникают вследствие того, что детали швейных изделий имеют сложную форму.
Процент межлекальных потерь определяют по формуле:
,
где Sp – площадь раскладки; Sл – площадь лекал с учетом припусков на швы; р – процент межлекальных выпадов.
Процент межлекальных отходов зависит от многих факторов:
• ширины и вида материала,
• формы, размера и числа деталей в раскладке. Лекала с прямыми контурами, приближающимися по форме к прямоугольнику, трапеции и т. п., располагаются в раскладке с наименьшими зазорами (отходами), чем лекала со сложными контурами. Наличие в комплекте лекал одновременно крупных и мелких деталей позволяет в зазорах между крупными деталями разместить мелкие, полнее использовать площадь раскладки;
• вида лицевой поверхности материала. Раскладки лекал на гладких материалах дают наименьшие расходы по сравнению с раскладками на материалах с ворсом, рисунком в крупную клетку и др., так как раскладки на ворсистых материалах и материалах с крупным рисунком требуют дополнительных припусков на подгонку рисунка, соблюдения направления рисунка, ворса, начеса;
• вида раскладки по числу комплектов лекал. Многокомплектная раскладка выгоднее, чем однокомплектная, так как в ней увеличивается возможность поиска наиболее удачного расположения лекал (больше вариантов размещения);
• сочетания размероростов в раскладке. Опыт показал, что сочетания смежных или одинаковых размероростов в раскладке дают лучшие показатели расхода материала;
• расположение лекал в раскладке в наибольшей степени при равных условиях оказывает влияние на размеры межлекальных отходов. Решающее значение в этом имеет опыт и навыки раскладчика.
Возможны следующие пути снижения расхода материала на единицу изделия без ущерба для его эстетического оформления:
Ø уменьшение прибавок на образование складок, рельефов, отделочных швов;
Ø уменьшение технологических прибавок (за счет допущенных излишеств) на сутюживание, усадку при стачивании швов, обработку срезов;
Ø анализ конфигурации деталей, определение мест в срезах деталей, мешающих лучшей укладываемости их в раскладке, нахождение путей их совершенствования, используя для этого возможность перевода швов, образование надставок, срезание углов;
Ø рациональное проектирование форм мелких деталей и возможности их усовершенствования;
Ø изменение направления нити основы в деталях, направления ворса и т. д.;
Ø соединение в одной раскладке лекал деталей двух разных моделей.
Наряду с положением швов, размером и формой лекал для расхода материала большое значение имеет количество швов. Чем меньше отдельные детали, тем экономичнее их можно комбинировать в одной раскладке, но с другой стороны каждый дополнительный шов вызывает увеличение расхода материала на величину припуска на швы и дополнительное время на обработку.
Материалы, поступающие на производство, состоят из отрезов и кусков разной длины. При проверке качества возникают условные разрезы кусков в местах расположения распространенных дефектов материалов. Длина отрезов и кусков может быть различна и редко бывает равной или кратной длине раскладки лекал или настила. Вследствие этого при раскрое возникают остатки материала от кусков (концевые остатки). Остатки могут быть рациональными и нерациональными.
Рациональными являются те остатки, которые можно использовать по прямому назначению на данном предприятии, нерациональными – остатки, которые не могут быть использованы по прямому назначению. Задачей рационального использования кусков материалов является сокращение всех видов остатков.
При раскрое изделий по индивидуальным заказам максимальное использование куска материала может быть достигнуто раскроем каждого изделия от куска без предварительного отрезания полотна. Если остаток от куска является нерациональным, то его используют вместе с последним полотном на заказ большего размера и длины. При раскрое материалов настилами применяют безостатковый способ раскроя, при котором от кусков после настилания могут оставаться маломерные остатки не более 10–15 см.
Если кусок не используется полностью в одном настиле, то его предварительно рассчитывают на два настила и более.
Предварительный расчет кусков на несколько настилов выполняют аналитическим методом ручным или механизированным способом.
Ручной способ расчета кусков осуществляют с помощью вспомогательных таблиц, в которых указаны возможные длины настилов и соответственно потребная длина куска материала при разном числе полотен в настиле. Путем сравнения заданной длины куска материала с длинами кусков в таблице по определенным настилам находят вариант использования куска с допустимым остатком или без него. Для ускорения процесса подбора вариантов используют настольные калькуляторы.
Механизированный способ расчета кусков материала осуществляют с помощью специализированных электронно-вычислительных машин и машин общего назначения. В настоящее время в современных САПР («Комтенс», «Грация», «Ассоль», «Реликт» и др.) действует подсистема расчет куска, в которых осуществляется расчет кусков ткани в настилы в соответствии с планом выпуска, учет кусков на складе, подбор и расчет фурнитуры [29]. Использование таких систем позволяет установить полный контроль за расходом ткани и сэкономить 7–10 % ткани при производстве изделий.
5.2. Виды раскладок, способы и условия их выполнения
Раскладка – определенная рамка, в которой положены лекала в соответствии с техническими условиями.
Технические условия (требования) на раскладку лекал – это правила, соблюдение которых закладывает основы высокого качества готовой одежды и экономичного расходования материала.
Основные требования при выполнении раскладки:
ü соблюдение направления долевой нити и допускаемых отклонений;
ü соблюдение направления рисунка, ворса, начеса и т.д.;
ü учет допускаемых надставок в деталях;
ü соблюдение комплектности деталей и их принадлежности к правой или левой стороне изделия;
ü линии обводки лекал должны быть хорошо видны, с толщиной линии для карандаша – не более 1 мм, для мела – не более 2 мм.
По способу расположения полотен в настиле существуют следующие виды раскладок:
* в сгиб;
* в разворот «лицом» вниз;
* в разворот «лицом к лицу».
Настиланиев сгиб(рис. 28)применяют при раскрое изделий одежды по индивидуальным заказам. Преимущество этого способа состоит в отсутствии перекосов, уменьшении затрат времени на раскладку и в удобстве выполнения раскладки. Недостаток – увеличение расхода ткани на единицу изделия и сложность раскроя изделий больших размеров.
Рис. 28. Однокомплектная раскладка в сгиб
Настилание тканив разворот «лицом» вниз применяется при раскрое изделий из ткани в клетку или полоску, с несимметричным рисунком, где требуется подгонка рисунка, а также при раскрое изделий с цельнокроеными рукавами и крупными несимметричными деталями.
Настилание ткани в разворот «лицом к лицу» применяется при раскрое изделий, имеющих симметричные детали. Этот способ является наиболее экономичным при расходе ткани, применяется в массовом производстве.
При выполнении настилов должны выполняться следующие требования:
• равнение по кромке с отклонением не более ±3 мм;
• ошибка отрезания полотен должна быть не более ±5 мм от длины настила;
• не допускается растяжение и слабина ткани при настилании, а также подтягивание полотен;
• ширина и длина настила должны соответствовать ширине и длине раскладки лекал.
В зависимости от числа комплектов лекал раскладки делятся на одиночные (рис. 29) и комбинированные (рис. 30).
Рис. 29. Однокомплектная раскладка лицом вниз
Рис. 30. Комбинированная раскладка лицом к лицу
Одиночные раскладки бывают из одного комплекта лекал при раскладке их на материале в разворот, из одного полукомплекта лекал при раскладке их на материале, сложенном вдвое по длине (в сгиб), и из двух полукомплектов лекал разных или одинаковых размеров и ростов (одиночная комбинированная раскладка) при комплекте деталей изделия из двух полотен, укладываемых «лицом к лицу».
Комбинированные раскладки имеют более одного комплекта лекал (1,5; 2; 2,5; 3 и т. д.). Они могут быть использованы при комплекте деталей изделия из одного полотна и из двух, укладываемых «лицом к лицу».
В швейной промышленности для выполнения раскладок используют методы на основе эвристических правил. Базовыми эвристиками являются методы одиночно-последовательного размещения и секционно-полосовой.
Суть секционно-полосового метода заключается в том, что порядок размещения новых деталей в рамке раскладки задается в виде поперечных полос по длине ткани. Как правило, в каждой из полос детали размещаются в порядке убывания площадей лекал. Таким образом, оптимизация размещения производится локально, в пределах одной полосы. В процессе размещения сначала выбирается крупное лекало и укладывается в полосу, затем – поменьше, и, наконец, оставшийся межлекальный выпад заполняется мелкими деталями. В секционно-полосовом методе, особенно в многокомплектных раскладках, в одной полосе могут совмещаться одноименные крупные детали, например две спинки или два рукава (рис. 30). Ширина полосы определяется размером первой крупной детали. Однако применение данного метода не всегда обеспечивает требуемый по нормативам процент межлекальных выпадов.
Для выполнения раскладок швейных изделий с большим числом деталей был предложен метод последовательно-одиночного размещения. Метод действует следующим образом. Сначала выбирают по определенному критерию одно из лекал, как правило, самое крупное, и размещают его в рамке раскладки. Следующий шаг – выбор второго лекала и размещение его в рамке раскладки. Обычно выбирается самое крупное из оставшихся лекал и размещается оно так, чтобы площадь, занимаемая обеими деталями, была минимальна, разумеется, с учетом долевого направления нити основы и других условий раскладки. Третий и последующие шаги аналогичны второму, они выполняются, пока не будут исчерпаны все лекала. Достоинство метода – высокая скорость работы. Недостаток – высокий процент межлекальных выпадов (порядка 20–30 %).
Для получения на материале качественной обмелки необходимо соблюдать следующие условия:
§ ширина рамки раскладки должна быть меньше ширины ткани без кромки на 10 мм;
§ касание лекал деталей по криволинейным участкам не допускается;
§ соприкасающиеся прямолинейные участки деталей необходимо обозначать одной линией;
§ детали раскладывать строго по долевому направлению;
§ расстояние между надсечками на зарисовке детали не должно иметь отклонение более ±1 мм от соответствующего расстояния на лекалах-эталонах;
§ расстояние между надсечками в парных деталях должно быть одинаковым;
§ к деталям, раскраиваемым методом вырубки, добавляют припуск не менее 8 мм по всему периметру;
§ толщина линий обводки должна быть не более 0,1 см
§ внутренняя часть линий обводки должна совпадать с контуром лекал;
§ между срезами деталей, у которых при выкраивании допустимые отклонения в срезах составляют не более 0,2 см, должно оставаться расстояние не менее 0,1–0,15 см.
В настоящее время на большинстве предприятий отрасли процесс выполнения раскладок автоматизирован.
Раскладка лекал в САПР может выполняться как в автоматизированном, так и в полуавтоматизированном режиме, то есть раскладка выполняется вручную на экране дисплея или автоматически по заданному алгоритму с выводом на экран дисплея результата о минимальном проценте межлекальных выпадов. Как правило, выполнение раскладок осуществляется в соответствии с заданными технологическими ограничениями: шириной материала, видом настилания материала, направления долевой, припуском-зазором между деталями, рапортом рисунка [29]. В системах имеются возможности объединения деталей в группы, разъединения (разрезания) деталей в раскладке с автоматическим добавлением припуска на шов. Так как конечным продуктом таких САПР является зарисованная на бумаге раскладка лекал, по которой в дальнейшем происходит раскрой настила ткани, то системы имеют подпрограммы, поддерживающие широкий спектр периферийных устройств различных производителей, и обеспечивающие вывод раскладок на плоттер или каттер. Есть системы («Силуэт», «Комтенс», «Investronica»), когда вместо плоттера совместно с САПР используется система автоматизированного раскроя. В этом случае в САПР входит подсистема оптимизации процесса раскроя раскладки на автоматической раскройной установке («Спутник», «Invescu» фирмы Investronica, «Texcut» фирмы Kuris-Wastema), включающая задание последовательности и направления раскроя, некроеных деталей и отдельных участков, точек врезки, выездов в кромку.
Раскладки, используемые для составления программы автоматизированного раскроя, должны выполняться со следующими правилами: без зазора могут располагаться прямолинейные параллельные срезы деталей без надсечек; прямолинейные параллельные срезы деталей, имеющие надсечки, совпадающие со срезами других деталей. Зазоры 4 мм должны соблюдаться между криволинейными срезами деталей и прямолинейными срезами деталей, имеющих надсечки (кроме вышеперечисленных). Не рекомендуется располагать мелкие детали (обтачки, планки, листочки, клапаны и т. д.) в области проймы спинки, полочки, у кромки; допускать большого скопления мелких деталей в одном месте. Длину раскладки выбирают с учетом длин настилочного и раскройного столов.
Готовую раскладку лекал для автоматизированного раскроя воспроизводят на графопостроителе (принтере) в уменьшенном масштабе для последующего контроля раскроя и маркировки пачек деталей.
Как показывает опыт внедрения традиционных САПР на сотнях предприятий, их применение обеспечивает экономию сырья до 3 %. Экономия получается за счет нормирования межлекальных отходов, уплотнения раскладок, устранения потерь, связанных с обмеловкой лекал, и других факторов.
Вопросы для повторения и самоконтроля
1. Как осуществляется нормирование материалов?
2. Какая группа специалистов занимается нормированием?
3. Какие виды потери материалов вы знаете?
4. Какие факторы влияют на расход материала?
5. Какие пути снижения расхода ткани на единицу изделия существуют?
6. Как определяется процент межлекальных потерь?
7. Что такое концевые остатки? Как они используются?
8. Назовите виды раскладок.
9. В чем преимущество многокомплектных раскладок?
10. Какие эвристики используются при раскладке лекал?
11. Перечислите требования при выполнении настилов.
12. Какие требования нужно соблюдать при обмеловке лекал?
13. Какие правила должны выполняться при составлении раскладки для автоматизированного раскроя лекал?
ЗАКЛЮЧЕНИЕ
Одежда относится к предметам потребления и служит для удовлетворения различных потребностей: эстетических, утилитарных, культурных, социальных и др.
Процесс удовлетворения потребностей порожден и определяется спросом. Весь цикл процесса состоит из следующих элементов: потребление (эксплуатация); изучение спроса; прогнозирование потребностей; проектирование; материальное производство (конструкторско-технологическая подготовка производства и изготовление); потребление (эксплуатация).
Таким образом, цикл процесса удовлетворения потребностей является беспрерывным, циклическим и повторяющимся, но уже в другом времени и на другом уровне.
Процесс проектирования составляет значительную часть процесса удовлетворения потребностей и представляет абстрактную мыслительную и познавательную деятельность проектировщика, направленную на разработку проектно-конструкторской документации. Таким образом, проект состоит из комплекса проектно-конструкторской документации на новое изделие и содержит обоснование проектирования, цель, требования к качеству объекта, конструкцию изделия в виде чертежей, образец – эталон изделия, техническое описание, комплект лекал и др. Проект позволяет изготовить одно и то же изделие на различных предприятиях в различное время и достаточно в большом количестве.
Чем выше организационно-технический уровень процесса проектирования и полнее процесс удовлетворения потребностей, тем большее количество специалистов самого различного профиля могут быть в нем задействованы: менеджер, психолог, технолог, художник-модельер, конструктор, экономист и другие специалисты. Первостепенная роль при проектировании одежды, то есть на этапе формирования материально-пространственной структуры производственных объектов, отводится конструктору и дизайнеру. Однако этапы изучения спроса и прогнозирования потребностей также предполагают участие конструктора, так как в противном случае он не сможет сформировать достоверную информацию о проектируемых моделях одежды.
Цель изучения дисциплины «Конструкторская и технологическая подготовка производства» – приобретение теоретических знаний и практических навыков в области проектирования новых моделей одежды различных видов и покроев. Программа курса позволяет ознакомиться с новейшими достижениями и направлениями в области современного проектирования одежды: разработкой технологичных конструкций плечевых и поясных швейных изделий; унификацией и стандартизацией деталей и узлов; построением основных, производных и вспомогательных лекал; их градацией; нормированием.
В настоящее время в век электронной техники рутинный труд конструктора заменяют компьютеры. Разработаны и действуют различные автоматизированные системы проектирования (САПР), позволяющие рассчитывать и строить чертежи деталей базовых конструкций одежды, выполнять градацию деталей. Кроме того, решаются задачи компьютерного конструктивного моделирования с использованием базовых конструкций. Однако применение САПР не снижает требований к квалификации конструктора, который должен уметь рассчитывать и строить чертежи конструкций различных видов и покроев одежды, вычерчивая при этом красивые линии модного кроя вручную, знать основы расчета схем градаций лекал без использования современных технических средств.
БИБЛИОГРАФИЧЕСКИЙ СПИСОК
1. Коблякова, Е. Б. Конструирование одежды с элементами САПР : учебник для вузов / Е. Б. Коблякова, Г. С. Ивлева, В. Е. Романов и др. – 4-е изд., перераб. и доп.; под ред. Е. Б. Кобляковой. – М. : Легпромбытиздат, 1988. – 464 с.
2. Куренова, С. В. Конструирование одежды : учебное пособие / С. В. Куренова, Н. Ю. Савельева. – Ростов н/Д : Феникс, 2003. – 480 с.
3. Беркетова, Н. П. Основы конструкторской подготовки производства одежды : конспект лекций / Н. П. Беркетова. – Омск : ОГИС, 1999. – 56 с.
4. Котлер, Ф. Основы маркетинга / Ф. Котлер, Г. Армстронг, Дж. Содерс и др. – 2-е европейское изд., пер. с англ. – М., СПб., Киев : Издательский дом «Вильямс», 1999. – 369 с.
5. Проектирование промышленных коллекций с учетом прогноза потребительских предпочтений. Мода 2006 : учебное пособие в 2-х частях. / И. В. Виниченко, О. А. Рашева, Е. В. Франк; под общ. ред. И. В. Лашиной. Ч. 2 – Омск : ОГИС, 2005. – 101 с.
6. Багиев, Г. Л. Основы маркетинговых исследований : учебное пособие / Г. Л. Багиев, И. А. Аренкова. – СПб. : СПбУЭФ, 1996. – 267 с.
7. Ждановская, Г. А. Потребительское поведение и факторы, определяющие колебание спроса на те или иные виды товаров и услуг / Г. А. Ждановская, Е. А. Васина // Маркетинг и маркетинговые исследования в России. – 1996. – № 2. – С. 4-9.
8. Герчинкова, И. Н. Методика проведения маркетинговых исследований // Маркетинг. – 1995. – № 3. – С. 31-42.
9. Медведева, Т. В. Художественное конструирование одежды : учебное пособие / Т. В. Медведева. – М. : ФОРУМ:ИНФРА-М, 2003. – 480 с.
10. Воронкова, Т. Ю. Проектирование швейных предприятий. Технологические процессы пошива одежды на предприятиях сервиса : учебное пособие / Т. Ю. Воронкова. – М. : ФОРУМ: ИНФРА-М, 2006. – 128 с.
11. Межгосударственный стандарт. Единая система конструкторской документации. Основные положения. – М. : Издательство стандартов, 1984. – 343 с.
12. Коблякова, Е. Б. Основы проектирования рациональных размеров и формы одежды. – М. : Легкая и пищевая пром-сть, 1984. – 208 с.
13. Шершнева, Л. П. Совершенствование проектирования одежды на основе комплексной оценки качества и учета спроса населения. – М. : Легпромбытиздат, 1988. – 165 с.
14. Сухарев, М. И. Принципы инженерного проектирования одежды / М. И. Сухарев, А. М. Бойцова. – М. : Легкая и пищевая промышленность, 1981. – 272 с.
15. Рисуют все! // Индустрия моды. – 2006. – № 3 (22). – С. 66-69.
16. Бахмат, Е. И. Конструктивное моделирование одежды. Конструктивный анализ внешней формы моделей и их деталей : учебное пособие / Е. И. Бахмат. – Омск : ОмТИ, 1996. – 30 с.
17. Мартынова, А. И. Конструктивное моделирование одежды : учебное пособие для вузов / А. И. Мартынова, Е. Г. Андреева. – М. : МГАЛП, 1999. – 216 с.
18. Янчевская, Е. А. Конструирование одежды : учебник для вузов / Е. Я. Янчевская. – М. : Издательский центр «Академия», 2005. – 384 с.
19. Чижик, М. А. Конструктивное моделирование одежды : учебное пособие / М. А. Чижик. – Омск : ОГИС, 2000. – 104 с.
20. Зак, И. С. Hi Tech-технологии обеспечивают экономию сырья до 6 % / И.С. Зак, Р.И. Сизова, Б.А. Козлов // Швейная промышленность. – 2002. – № 1. – С. 38.
21. Козлов, Б. А. Плотные многокомплектные раскладки деталей швейных изделий. – М.: Легпромбытиздат, 1985. – 152 с.
22. Андрианов, В. С. Ресурсосберегающие технологии раскройного производства / В. С. Андрианов, С. К. Лопадина // Швейная промышленность. – 1996. – № 5. – С. 27-30.
23. Кириллова, Л. И. О совершенствовании нормативной базы швейной отрасли / Б. А. Кириллова, Л. Ф. Ветошина // Швейная промышленность. – 2000. – № 5. – С. 43-44.
24. Парыгина, М. М. Технология получения точного кроя деталей швейных изделий. / М. М. Парыгина // Швейная промышленность. – 2000. – № 5. – С. 31-33.
25. ОСТ 17–326–86 Изделия швейные, трикотажные, меховые. Типовые фигуры женщин. Размерные признаки для проектирования одежды. – М. : ЦНИИТЭИлегпром, 1986.
26. ОСТ 17–325–86 Изделия швейные, трикотажные, меховые. Типовые фигуры мужчин. Размерные признаки для проектирования одежды. – М. : ЦНИИТЭИлегпром, 1986.
27. Андреева, М. В. Работа с лекалами и градация по нормам в САПР «Ассоль». / М. В. Андреева, Т. Ю. Холина, А. М. Павлов // Швейная промышленность. – 2001. – № 3. – С.27-302.
28. Мурашов, Л. В. Надо ли нормировать плотность раскладок в современных условиях? / Л. В. Мурашов, И. С. Зак, Р. И. Сизова // Швейная промышленность. – 2004. – № 1. – С.18-19.
29. Андреева, М. В. САПР «Ассоль» – оптимальное планирование раскройного производства. / М. В. Андреева // Швейная промышленность. – 2003. – № 1. – С.14-16.
ПРИЛОЖЕНИЕ 1
Дата добавления: 2018-08-06; просмотров: 2075; Мы поможем в написании вашей работы! |
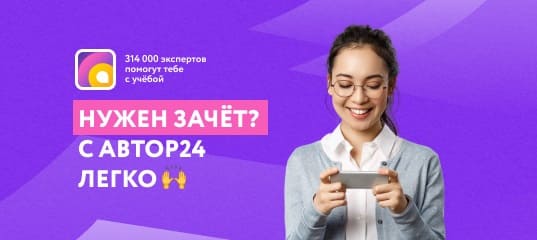
Мы поможем в написании ваших работ!