Назначение припусков на механическую обработку.
ФГБОУ ВО Уфимский государственный авиационный технический университет Кафедра машин и технологии литейного производства ОТЧЕТ
По учебной практике в ПАО «УМПО»
(обозначение документа) |
Группа | Фамилия, И., О. | Подпись | Дата | Оценка | ||
МА-198п | ||||||
Студент | Аджибае Д.А | |||||
Консультант | ||||||
Принял |
Уфа 2018 г.
Введение
Целью прохождения учебной практики является реализация полученных теоретических знаний, умений и навыков, а также получение представления о практической деятельности предприятия. Для достижения поставленных целей при прохождении практики в первую очередь ставилась задача изучения структуры, порядка, планировки и организации ПАО «ОДК-УМПО».
ПАО «Уфимское моторостроительное производственное объединение» (УМПО) — российское предприятие, производитель авиационных двигателей. Основано в 1925 году. В объединении работают более 22 тысяч человек.
Основными видами деятельности предприятия являются производство, сервисное обслуживание и ремонт турбореактивных авиационных двигателей, производство и ремонт узлов вертолетной техники, выпуск оборудования для нефтегазовой промышленности. Серийно выпускает турбореактивные двигатели для самолетов семейства Су-35С, Су-27 ,семейства Су-30 , семейства Су-25, узлы вертолетной техники на вертолеты «Ка» и «Ми».
|
|
Входит в состав «Объединённой двигателестроительной корпорации» — 100 % специализированной дочерней компании ОАО ОПК «Оборонпром» по управлению двигателестроительными активами.
Прессование.
Получение изделий прессованием.
Прямое прессование — это процесс прессования негранулированных порошков. Из технологической схемы получения таблеток, видно, что прямое прессование позволяет исключить 3—4 технологические операции из производственного процесса.
Способ прямого прессования обладает рядом преимуществ, к ним относятся:
- сокращение времени производственного цикла за счет упразднения ряда операций и стадий;
- использование меньшего количества оборудования;
- уменьшение производственных площадей;
- снижение энерго- и трудозатрат;
- получение таблеток из влаго-, термолабильных материалов и несовместимых веществ.
К недостаткам способа прямого прессования относятся:
- возможность расслаивания таблеточной массы;
- изменение дозировки при прессовании с незначительным количеством действующих веществ;
- необходимость использования высокого давления.
Некоторые из указанных недостатков сводятся к минимуму при таблетировании путем принудительной подачи прессуемых веществ в матрицу.
Однако, несмотря на целый ряд преимуществ, прямое прессование медленно внедряется в производство. Это объясняется тем, что для производительной работы таблеточных машин прессуемый материал должен обладать оптимальными технологическими характеристиками, а именно: изодиаметрической формой кристаллов, хорошей сыпучестью (не менее 5—6 г/с), высокой прессуемостью (не менее 0,4—0,5 г/мл) и низкой адгезионной способностью к пресс-инструменту таблеточной машины.
|
|
При обратном прессовании заготовку закладывают в глухой контейнер, и она при прессовании остается неподвижной, а истечение металла из отверстия матрицы, которая крепится на конце полого пуансона, происходит в направлении, обратном движению пуансона с матрицей. Обратное прессование требует меньших усилий, пресс-остаток составляет 5…6 %. Однако меньшая деформация приводит к тому, что прессованный пруток сохраняет следы структуры литого металла. Конструктивная схема более сложная.
Процесс прессования характеризуется следующими основными параметрами: коэффициентом вытяжки, степенью деформации и скоростью истечения металла из очка матрицы.
|
|
Коэффициент вытяжки λ определяют как отношение площади сечения контейнера Fк к площади сечения всех отверстий матрицы Fм.
Степень деформации:
Скорость истечения металла из очка матрицы пропорциональна коэффициенту вытяжки и определяется по формуле:
Vп– скорость прессования (скорость движения пуансона)
При прессовании металл подвергается всестороннему неравномерному сжатию и имеет очень высокую пластичность.
К основным преимуществам прессования относятся:
- возможность обработки металлов, которые из-за низкой пластичности другими методами обработать невозможно;
- возможность получения практически любого профиля поперечного сечения;
- получение широкого сортамента изделий на одном и том же прессовом оборудовании с заменой только матрицы;
- высокая производительность, до 2…3 м/мин.
Недостатки прессования:
- повышенный расход металла на единицу изделия из-за потерь в виде пресс-остатка;
- появление в некоторых случаях заметной неравномерности механических свойств по длине и поперечному сечению изделия;
- высокая стоимость и низкая стойкость прессового инструмента;
- высокая энергоемкость.
Назначение припусков на механическую обработку.
|
|
Создание эскиза заготовки.
Припуском называется слой металла, предназначенный для снятия в процессе механической обработки. Величина припуска должна быть такой, чтобы после механической обработки поверхность детали отвечала требованиям по качеству металла, механическим свойствам и шероховатости. Величина припуска регламентируется государственным стандартом ГОСТ Р 53464-2009 «Отливки из металлов и сплавов. Допуски размеров, массы и припуски на механическую обработку».
Класс точности отливок определяется в зависимости от типа производства (серийности), материала и состояния модельного комплекта и оснастки, а также других факторов. К первому классу точности относятся отливки, получаемые в крупносерийном и массовом производстве при машинной формовке с использованием, как правило, металлического модельного комплекта. Второй класс точности достигается при машинной формовке по деревянным моделям (среднесерийное производство). Отливки, получаемые в единичном и мелкосерийном производстве с использованием ручной формовки и деревянного модельного комплекта могут относиться как ко второму, так и к третьему классу точности в зависимости от состояния технологической оснастки и квалификации формовщика. Примем, что в рассматриваемом случае отливка относится ко второму классу точности.
В соответствии с ГОСТ 2.423-73 припуски на механическую обработку на чертежах изображаются сплошной основной линией поверх контура детали. Величина припуска учитывается в линейных размерах отливки. Отверстия, впадины и другие особенности конфигурации детали, не выполняемые литьем, зачеркиваются сплошной линией. Слой металла, оставляемый на месте не выполняемых литьем элементов детали, называется напуском.
Все поверхности модели, перпендикулярные разъему, должны иметь формовочные уклоны, облегчающие извлечение модели из формы. Следовательно, формовочные уклоны будут иметь место и на отливке, т.к. последняя повторяет наружную конфигурацию модели. На обрабатываемых поверхностях формовочный уклон назначается сверх припуска на механическую обработку. Значения формовочных уклонов для наружных поверхностей моделей регламентируются ГОСТом 3212-92.
Рис. 1. Эскиз детали
Рис. 2. Эскиз заготовки
Деталь изготавливается из стали 45.
C | Si | Mn | Ni | S | P | Cr | Cu | As | Fe |
0,42-0,5 | 0,17-0,37 | 0,5-0,8 | до 0,25 | до 0,04 | до 0,035 | до 0,25 | до 0,25 | до 0,08 | 97 |
Табл. 1. Химический состав в % стали 45
Дата добавления: 2018-08-06; просмотров: 374; Мы поможем в написании вашей работы! |
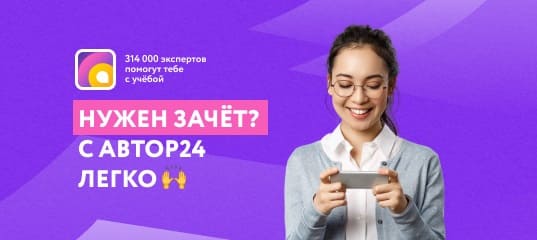
Мы поможем в написании ваших работ!