ОСОБЕННОСТИ РЕМОНТА ЭЛЕКТРООБОРУДОВАНИЯ С РАЗЛИЧНЫМИ ВИДАМИ ВЗРЫВОЗАЩИТЫ
7.1. Особенности конструкций электрооборудования во взрывозащищенном исполнении.
7.1.1. К взрывозащищенному электрооборудованию всех трех уровней взрывозащиты относятся:
а) электрооборудование повышенной надежности против взрыва;
б) взрывобезопасное электрооборудование;
в) особовзрывобезопасное электрооборудование.
7.1.2. Наиболее распространенный вид взрывозащиты по всем уровням -«взрывонепроницаемая оболочка», которая создается в результате обеспечения высокой прочности корпуса и подшипниковых узлов, крепления деталей и узлов, с соблюдением регламентированных параметров взрывозащиты.
Взрывозащита электрооборудования этого вида обеспечивается за счет:
а) высокой механической прочности составных частей оболочки;
б) соблюдение параметров взрывонепроницаемых соединений оболочки;
в) уплотнения вводов проводов или кабеля эластичными уплотнительными кольцами или затвердевающей массой;
г) применения пружинных шайб и других специальных устройств для предупреждения самоотвинчивания деталей крепления оболочки или частей, токоведущих и заземляющих зажимов;
д) применение охранных колец или углублений для головок болтов и гаек, скрепляющих части оболочки, что обеспечивает невозможность разборки электрооборудования без помощи специального инструмента;
е) применения специальных зажимов заземления и блокировок;
|
|
ж) ограничения допустимой температуры нагрева наружных частей оболочки;
з) применения коррозионностойких смазок для покрытия взрывозащитных поверхностей, что обеспечивает длительную сохранность их от разрушения коррозией и, как следствие, сохранение взрывонепроницаемых соединений;
и) нормированных значений параметра шероховатости взрывозащитных поверхностей;
к) применение трекингостойких электроизоляционных материалов для электрооборудования группы I;
л) выполнение других требований, оговоренных в ремонтной и эксплуатационной документации на конкретное электрооборудование.
7.1.3. Детали и сборочные единицы взрывонепроницаемой оболочки независимо от их состояния (отремонтированные, не подвергавшиеся ремонту, вновь изготовленные, полученные по кооперации и т.п.) должны быть подвергнуты гидравлическим испытаниям.
Допускается не проводить эти испытания в том случае, если детали или сборочные единицы поступают на ремонтные предприятия как запасные части и имеют сопроводительную документацию, удостоверяющую их соответствие документации на изготовление электрооборудования или ремонтной документации.
Если за эксплуатацию электрооборудования и его ремонт отвечает одно и то же должностное лицо, то необходимость проведения гидравлических испытаний деталей и сборочных единиц, не подвергавшихся ремонту и не имеющих следов повреждений (вмятин, трещин, цветов побежалости и т.п.), определяет это лицо и оно же несет ответственность за взрывобезопасность электрооборудования после ремонта.
|
|
Допускается по усмотрению руководителя предприятия или должностного лица, ответственного за ремонт электрооборудования, не проводить гидравлические испытания деталей и сборочных единиц электрооборудования, не подвергавшихся ремонту и не имеющих следов повреждений, изготовленных из стали, в том числе методом сварки, с толщиной оболочки 6 мм и выше.
7.1.4. Гидравлические испытания проводятся по методике, приведенной в ГОСТ 22782.6 по нормам и схемам, указанным в ремонтной документации и РД 16.209-84 «Испытания гидравлические».
7.1.5. После гидравлических испытаний допускается производить дополнительную механическую обработку частей оболочки с сохранением нормируемых размеров деталей без последующих повторных гидроиспытаний.
7.1.6. Параметры взрывонепроницаемых соединений оболочек электрооборудования должны соответствовать ремонтной документации.
|
|
7.1.7. Шероховатость взрывозащитных поверхностей отдельных частей взрывонепроницаемой оболочки должна соответствовать ремонтным чертежам и должна быть не ниже указанной в таблице 1.
Таблица 1
Неподвижные соединения | Подвижные соединения типа | |
вал | втулка | |
6,3 мкм | 6,3 мкм | 6,3 мкм |
Примечание: Для доведения плоских и цилиндрических поверхностей пластмассовых деталей после их изготовления методом прямого прессования или литься до требуемых размеров, обеспечивающих взрывозащиту взрывонепроницаемой оболочки, допускается механическая обработка этих деталей.
7.1.8. Диаметр резьбы и материал крепежных элементов должны соответствовать ремонтной документации.
Допускается замена материала только материалом с повышенными, по сравнению с указанными в ремонтной документации, прочностными характеристиками (временное сопротивление на разрыв, предел текучести, относительное удлинение и т.п.) при полном сохранении чертежных размеров и форм.
7.1.9. Суммарная неплоскостность взрывозащитных поверхностей плоского взрывонепроницаемого соединения не должна превышать нормированной ширины взрывонепроницаемой щели.
7.1.10. Раковины, забоины, вмятины, ржавчина, чернота, наличие краски и другие дефекты на взрывозащитных поверхностях не допускаются.
|
|
7.1.11. Допускается на взрывозащитных поверхностях частей взрывонепроницаемой оболочки после их обработки наличие пор диаметром не более 1 мм, беспорядочно расположенных, числом не более 20 на 1 см2, из них не более 6 пор диаметров свыше 0,5 до 1 мм.
Незначительные по размерам пороки литья (раковины, чернота и т.п.), незначительные сварочные раковины, обнаруженные на взрывозащищенных поверхностях после окончательной обработки, а также следы механических повреждений (забоины, вмятины и т.п.) на этих поверхностях допускается устранять путем запайки мягкими припоями, медью или латунью - для стальных деталей; медью или латунью - для чугунных.
Устранение указанных дефектов может также осуществляться заделкой пластическими материалами.
Технические требования к материалам, исправляющим дефекты в соответствии с приложением 9.
7.1.12. При устранении дефектов в соответствии с п. 7.1.10 необходимо руководствоваться черт. 1, табл. 2 и следующими требованиями:
а) должна быть произведена разделка поверхностей дефектов до неповрежденного металла;
б) кратчайший неповрежденный путь между двумя любыми разделками должен быть не менее значений, приведенных в табл. 2;
в) поверхность разделанного литьевого дефекта, находящегося в зоне Вн, вписывается в окружность диаметром d, при этом если часть разделки выходит за пределы зоны Вн, то размеры этой части не нормируются;
г) проекция разделки следов механических повреждений, находящихся в зоне Вн, на размерную линию, по которой определяется длина Вн, должны быть не более размера d с глубиной разделки не более h (табл. 2), при этом, если часть разделки выходит за пределы зоны Вн, то размеры этой части не нормируются;
д) допускается заделка дефектов вокруг отверстия для винта или других деталей крепления в кольцевой зоне Н = аф - ан, т.е. в зоне превышения фактического взрывонепроницаемого пути от кромки отверстия до внутренней кромки оболочки (аф) или до ближайшей разделки над нормированным (ан) по действовавшей в период изготовления электрооборудования нормативно-технической документации;
е) в пределах зоны aн заделка дефектов не допускается;
ж) размеры и расположение разделок в зоне Н и на поверхности вне Вн не нормируются;
з) материал заделки должен иметь хорошую адгезию;
и) поверхность заделки должна быть расположена заподлицо с основной поверхностью и иметь тот же параметр шероховатости;
к) не допускаются местные забоины или выступы, увеличивающие зазор между сопрягающимися поверхностями.
7.1.13. Устранение дефектов, не удовлетворяющих требованиям пп. 7.1.10 - 7.1.11, а также устранение любых дефектов на взрывозащитных поверхностях с нормированной длиной взрывонепроницаемого соединения Вн = 5 мм должно производиться только путем заварки. Не допускается заливка дефектов свинцом.
7.1.14. Заделка любых повреждений в расточках втулок для валиков управления или валов электродвигателей не допускается Детали с такими повреждениями должны растачиваться с последующей установкой в процессе ремонта втулок. Поврежденные втулки подлежат замене.
7.1.15. Раковины в глухом или сквозном отверстии в стенке оболочки или на поверхности фланцев допускается исправлять рассверливанием или расточкой отверстия и запрессовкой в него глухой пробки или втулки по посадке Н8/u8 (черт. 2).
Толщина втулок или пробок в каждом отдельном случае выбирается в зависимости от конструкции оболочки.
Для особо нагруженных болтов пробки должны устанавливаться по резьбе.
Пробки и втулки должны завариваться с одного или двух торцов. После сварки необходимо произвести обработку взрывозащитных поверхностей с соблюдением требуемой шероховатости.
7.1.16. Если исправления по пп. 7.1.12, 7.1.14 были произведены после испытаний деталей взрывонепроницаемой оболочки электрооборудования в соответствии с пп. 7.1.2 и 7.1.3 настоящих РД, то необходимо такие детали вновь подвергнуть испытаниям.
Детали взрывонепроницаемой оболочки, исправленные в соответствии с пп. 7.1.10 и 7.1.11 после испытаний по пп. 7.1.2 и 7.1.3 повторным испытаниям не подвергаются.
7.1.17. Втулки, устанавливаемые на вал или в подшипниковый щит, могут изготовляться из чугуна, меди, бронзы, латуни с запрессовкой по посадке Н8/u8.
Крепление втулки осуществляется либо ее развальцовкой с обеих сторон, либо упорным буртом и развальцовкой другой стороны втулки (черт. 3), либо винтом (черт. 4).
Упорный бурт или винты должны располагаться, как правило, с внутренней стороны взрывонепроницаемой оболочки.
7.1.18. Ремонт взрывозащитных поверхностей взрывонепроницаемой оболочки может осуществляться методом гальваническогоосталивания или другими методами, обеспечивающими прочность и надежность восстановленных взрывозащитных поверхностей.
В каждом случае ремонтное предприятие должно гарантировать надежность принятого метода восстановления взрывозащитных поверхностей в течение срока эксплуатации изделия до очередного ремонта.
Рекомендуется, при необходимости, технологический процесс заделки дефектов согласовывать с предприятием (организацией), головной по данному виду технологического процесса.
Таблица 2
Параметры | Длина взрывонепроницаемого сопряжения (щели), мм | ||
15 и 12,5 | |||
Допустимая по действовавшей в период изготовления электрооборудования нормативно-технической документации длина щели между поверхностями прилегания от кромки отверстий под болт до кромки оболочки, ан, мм, не менее | 9,0 | 8,0 | 5,0 |
Диаметр окружности, описанной вокруг разделки, для литьевого порока или проекция разделки на линию, по которой определяется Вн, d, мм, не более | 5,0 | 3,0 | 2,0 |
Кратчайший путь по неповрежденной поверхности между разделками (в пределах Вн), l, мм, не менее | 9,0 | 8,0 | 5,0 |
Ширина разделки при механическом повреждении, b, мм, не более | 2,0 | 1,5 | 1,0 |
Глубина разделки при механическом повреждении, h, мм, не более | 4,0 | 3,0 | 2,0 |
Вк - конструктивный размер части взрывонепроницаемого сопряжения (щели);
Вс - фактическая длина взрывонепроницаемого сопряжения (щели);
Вн - длина взрывонепроницаемого сопряжения (щели) по действовавшей в период изготовления электрооборудования нормативно-технической документации;
Черт. 1
Электротехника
Существует множество понятий, которые нельзя увидеть собственными глазами и потрогать руками. Наиболее ярким примером служит электротехника, состоящая из сложных схем и малопонятной терминологии. Поэтому очень многие просто отступают перед трудностями предстоящего изучения этой научно-технической дисциплины. Получить знания в этой области помогут основы электротехники для начинающих, изложенные доступным языком. Подкрепленные историческими фактами и наглядными примерами, они становятся увлекательными и понятными даже для тех, кто впервые столкнулся с незнакомыми понятиями. Постепенно продвигаясь от простого к сложному, вполне возможно изучить представленные материалы и использовать их в практической деятельности. Понятия и свойства электрического тока Электрические законы и формулы требуются не только для проведения каких-либо расчетов. Они нужны и тем, кто на практике выполняет операции, связанные с электричеством. Зная основы электротехники можно логическим путем установить причину неисправности и очень быстро ее устранить. Суть электрического тока заключается в движении заряженных частиц, переносящих электрический заряд от одной до другой точки. Однако при беспорядочном тепловом движении заряженных частиц, по примеру свободных электронов в металлах, переноса заряда не происходит. Перемещение электрического заряда через поперечное сечение проводника происходит лишь при условии участия ионов или электронов в упорядоченном движении. Электрический ток всегда протекает в определенном направлении. О его наличии свидетельствуют специфические признаки: Нагревание проводника, по которому протекает ток. Изменение химического состава проводника под действием тока. Оказание силового воздействия на соседние токи, намагниченные тела и соседние токи. Электрический ток может быть постоянным и переменным. В первом случае все его параметры остаются неизменными, а во втором – периодически происходит изменение полярности от положительной к отрицательной. В каждом полупериоде изменяется направление потока электронов. Скорость таких периодических изменений представляет собой частоту, измеряемую в герцах Основные токовые величины При возникновении в цепи электрического тока, происходит постоянный перенос заряда через поперечное сечение проводника. Величина заряда, перенесенная за определенную единицу времени, называется силой тока, измеряемой в амперах. Для того чтобы создать и поддерживать движение заряженных частиц, необходимо воздействие силы, приложенной к ним в определенном направлении. В случае прекращения такого действия, прекращается и течение электрического тока. Такая сила получила название электрического поля, еще она известна как напряженность электрического поля. Именно она вызывает разность потенциалов или напряжение на концах проводника и дает толчок движению заряженных частиц. Для измерения этой величины применяется специальная единица – вольт. Существует определенная зависимость между основными величинами, отраженная в законе Ома, который будет рассмотрен подробно. Важнейшей характеристикой проводника, непосредственно связанной с электрическим током, является сопротивление, измеряемое в омах. Данная величина является своеобразным противодействием проводника течению в нем электрического тока. В результате воздействия сопротивления происходит нагрев проводника. С увеличением длины проводника и уменьшением его сечения, значение сопротивления увеличивается. Величина в 1 Ом возникает, когда разность потенциалов в проводнике составляет 1 В, а сила тока – 1 А. Закон Ома Данный закон относится к основным положениям и понятиям электротехники. Он наиболее точно отражает зависимость между такими величинами, как сила тока, напряжение, сопротивление и мощность. Определения этих величин уже были рассмотрены, теперь нужно установить степень их взаимодействия и влияния друг на друга. Для того чтобы вычислить ту или иную величину, необходимо воспользоваться следующими формулами: Сила тока: I = U/R (ампер). Напряжение: U = I x R (вольт). Сопротивление: R = U/I (ом). Зависимость этих величин, для лучшего понимания сути процессов, часто сравнивается с гидравлическими характеристиками. Например, внизу бака, наполненного водой, устанавливается клапан с примыкающей к нему трубой. При открытии клапана вода начинает течь, поскольку существует разница между высоким давлением в начале трубы и низким – на ее конце. Точно такая же ситуация возникает на концах проводника в виде разности потенциалов – напряжения, под действием которого электроны двигаются по проводнику. Таким образом, по аналогии, напряжение представляет собой своеобразное электрическое давление. Силу тока можно сравнить с расходом воды, то есть ее количеством, протекающим через сечение трубы за установленный период времени. При уменьшении диаметра трубы уменьшится и поток воды в связи с увеличением сопротивления. Этот ограниченный поток можно сравнить с электрическим сопротивлением проводника, удерживающим поток электронов в определенных рамках. Взаимодействие тока, напряжения и сопротивления аналогично гидравлическим характеристикам: с изменением одного параметра, происходит изменение всех остальных. Энергия и мощность в электротехнике В электротехнике существуют еще и такие понятия, как энергия и мощность, связанные с законом Ома. Сама энергия существует в механической, тепловой, ядерной и электрической форме. В соответствии с законом сохранения энергии, ее невозможно уничтожить или создать. Она может лишь преобразовываться из одной формы в другую. Например, в аудиосистемах осуществляется преобразование электроэнергии в звук и теплоту. Любые электрические приборы потребляют определенное количество энергии на протяжении установленного промежутка времени. Эта величина индивидуальна для каждого прибора и представляет собой мощность, то есть объем энергии, который может потребить тот или иной прибор. Этот параметр вычисляется по формуле P = I x U, единицей измерения служит ватт. Он означает перемещение одного ампера одним вольтом через сопротивление в один ом. Таким образом, основы электротехники для начинающих помогут на первых порах разобраться с основными понятиями и терминами. После этого будет значительно легче использовать полученные знания на практике.
Основы слесарных работ
Основные виды слесарных работ
Далее: Понятие о допусках и посадках
Разметка
]
Рис. 30. Разметочная плита
Разметкой называется нанесение на поверхность заготовки границ в виде линий и точек, соответствующих размерам детали по чертежу, а также осевых линий и центров для сверления отверстий.
Если разметка производится только в одной плоскости, например на листовом материале, то она называется плоскостной. Разметка поверхностей заготовки, расположенных под разными углами друг к другу, называется пространственной. Заготовки размечают на специальной чугунной плите (рис. 30), называемой разметочной, устанавливаемой на деревянном столе так, чтобы ее верхняя плоскость была строго горизонтальной.
Инструменты для размет-к и. При разметке пользуются различными разметочными инструментами.
Чертилка (рис. 31) представляет собой стальной стержень с острыми закаленными концами. Чертилкой наносят тонкие линии на поверхности заготовки при помощи линейки, шаблона или угольника.
Рейсмас применяют для нанесения на заготовке горизонтальных линий, параллельных поверхности разметочной плиты. Рейсмас (рис. 32) состоит из основания и укрепленной в его центре стойки, на которой имеется подвижный хомутик с чертилкой, поворачивающейся вокруг своей оси. Подвижный хомутик может перемещаться по стойке и закрепляться на ней в любом положении зажимным винтом.
Рис. 31. Чертилка
Разметочный циркуль (рис. 33) служит для вычерчивания окружностей и закруглений на размечаемой заготовке.
Рис. 32. Рейсмас
Рис. 33. Разметочный циркуль
Для точной разметки пользуются штангенрейсмасом (рис. 34). На массивном основании прочно укреплена штанга, имеющая миллиметровую шкалу. По штанге перемещается рамка с нониусом и вторая рамка микрометрической подачи. Обе рамки закрепляются на штанге винтами в любом нужном положении. К рамке крепится хомутиком сменная ножка чертилки.
Разметочный штангенциркуль применяют для вычерчивания окружностей больших диаметров с непосредственной установкой размеров. Разметочный штангенциркуль (рис. 35) состоит из штанги с нанесенной на ней миллиметровой шкалой и двух ножек, из которых ножка неподвижно укреплена на штанге, а ножка подвижная и может перемещаться на штанге. Подвижная ножка имеет нониус. В обе ножки вставляются закаленные стальные иглы. Игла подвижной ножки может перемещаться вверх и вниз и в нужном положении зажиматься винтом.
Рис. 34. Штангенрейсмас
Рис. 35. Разметочный штангенциркуль
Рис. 36. Центроискатель
Центроискатель предназначен для определения центра торца цилиндрической заготовки (рис. 36). Центроискатель состоит из угольника с полками, расположенными под углом 90° друг к другу, и ножки, внутренняя сторона которой делит прямой угол угольника пополам. Для определения центра центроискатель устанавливают так, чтобы полки угольника касались цилиндрической поверхности заготовки. Чертилкой ведут по внутренней стороне ножки, нанося таким образом линию диаметра, затем поворачивают центро-искатель на 90° и наносят вторую диаметральную линию. Точка пересечения этих линий и будет являться центром торца цилиндрической заготовки.
Масштабный высотомер (рис. 37) применяют для разметки в тех случаях, когда нужно установить острие чертилки на определенной высоте. Он состоит из неподвижной масштабной линейки, прикрепленной к чугунному угольнику, подвижной линейки, перемещающейся по направляющим основаниям, визирного движка с тонкой чертой. При разметке визирный движок устанавливают так, чтобы тонкая черта его совпадала с главной осью заготовки, и в этом положении закрепляют. После этого нулевое деление подвижной линейки ставят против тонкой черты визирного движка и расстояние (высоту) от главной оси заготовки до других осей читают на подвижной линейке.
Кернер служит для нанесения небольших углублений на разметочных линиях заготовки, для того чтобы линии эти были хорошо видимы и не стерлись в процессе обработки заготовки. Кернер (рис. 38) изготовляется из инструментальной стали в виде стержня, средняя часть которого имеет насечку. Рабочая часть нижнего конца кернера затачивается под углом 45—60° и закаливается, а верхний конец является бойком, по которому при на-кернивании ударяют молотком.
Приспособления для разметки. В целях предохранения поверхности разме точной плиты от царапин, забоин, а также для создания устойчивого положения при разметке деталей, не имеющих плоского основания, и облегчения процесса разметки применяются чугунные по д-кладки (рис. 39, а), домкратики (рис. 39, б) и разметочные ящики (рис. 39, в) различной формы. Применяют также угольники, струбцинки и регулируемые клинья.
Процесс разметки осуществляется следующим образом. Поверхности размечаемых заготовок очищают от грязи, пыли и жиров. Затем покрывают тонким слоем мела, разведенного в воде с добавлением льняного масла и сиккатива или столярного клея. Хорошо обработанные поверхности покрываются иногда раствором медного купороса или скоросохнущими красками и лаками. Когда нанесенный слой мела или краски высохнет, можно начать разметку. Разметка может производиться по чертежу или шаблону.
Рис. 37. Масштабный высотомер
Рис. 38. Кернер
Процесс разметки заготовки по чертежу выполняют в такой последовательности:
– подготовленную заготовку устанавливают на разметочную плиту;
– наносят на поверхности заготовки основные линии, по которым можно определить положение других линий или центров отверстий;
– наносят горизонтальные и вертикальные линии в соответствии с размерами чертежа, затем находят центры и вычерчивают окружности, дуги и наклонные линии;
– по нанесенным линиям кернером выбивают небольшие углубления, расстояние между которыми в зависимости от состояния поверхности и размера заготовки может быть от 5 до 150 мм.
Рис. 39. Приспособления для разметки:
а — подкладки, б — доыкратики, в — разметочные ящики
При плоскостной разметке одинаковых деталей целесообразнее пользоваться шаблоном. Такой способ разметки заключается в том, что стальной шаблон накладывают на заготовку и чертилкой обводят на заготовке его контуры.
Рубка металла
Слесарная рубка применяется для снятия лишнего металла в тех случаях, когда не требуется большой точности обработки, а также для грубого выравнивания шероховатых поверхностей, для разрубания металла, срубания заклепок, для вырубания шпоночных пазов и т. п.
Инструменты для рубки. Инструментами для рубки металла являются зубила и крейцмейсели» а ударным инструментом — молоток.
Зубило (рис. 40, а) изготовляется из инструментальной стали У7А и, как исключение, У7, У8 и У8А. Ширина лезвия зубила от 5 до 25 мм. Угол заточки лезвия выбирается в зависимости от твердости обрабатываемого металла. Например, для рубки чугуна и бронзы угол заточки должен быть 70°, для рубки стали 60°, для рубки латуни и меди 45°, для рубки алюминия и цинка 35°. Лезвие зубила затачивают на наждачном круге так, чтобы фаски имели одинаковую ширину и одинаковый угол наклона к оси зубила. Угол заточки проверяют шаблоном или угломером.
Рис. 40. Инструменты для рубки металла:
а — зубило, б — крейцмейсель, в — слесарный молоток
Крейцмейсель (рис. 40, б) применяют для прорубания шпоночных канавок, срубания заклепок, предварительного прорубания канавок для последующей рубки широким зубилом.
Для предотвращения заклинивания крейцмейселя при прорубании узких канавок его лезвие должно быть шире оттянутой части. Углы заточки лезвия крейцмейселя те же, что и у зубила. Длина крейцмейселя от 150 до 200 мм.
Слесарный молоток (рис. 40,б). При рубке обычно используют молотки весом 0,5—0,6 кГ. Молоток изготовляют из инструментальной стали У7 и У8, а рабочую часть его подвергают термической обработке (закалке с последующим отпуском). Молотки бывают с круглым и квадратным бойком. Рукоятки молотков делают из дерева твердой породы (дуб, береза, клен и др.). Длина рукояток молотков среднего веса от 300 до 350 мм.
Для повышения производительности труда в последнее время начали осуществлять механизацию рубки путем применения пневматических молотков, работающих под действием сжатого воздуха, поступающего от компрессорной установки.
Процесс ручной рубки заключается в следующем. Обрубаемую заготовку или деталь зажимают в тисках так, чтобы разметочная линия рубки находилась на уровне губок. Рубку осуществляют в стуловых тисках (рис. 41, а) или, в крайнем случае, в тяжелых параллельных тисках (рис. 41,6). Зубило при рубке должно находиться в наклонном положении к обрубаемой поверхности заготовки под углом 30—35°. Молотком ударяют с таким расчетом, что бы центр бойка молотка попадал’ в центр головки зубила, причем нужно внимательно смотреть только на лезвие зубила, которое следует перемещать точно по разметочной линии рубки заготовки.
Рис. 41. Тиски:
а — стуловые, 6 — параллельные
При рубке толстый слой металла срубают за несколько проходов зубила. Для снятия металла зубилом с широкой поверхности предварительно крейцмейселем вырубают бороздки, затем образовавшиеся выступы срубают зубилом.
Для облегчения работы и получения гладкой поверхности при рубке меди, алюминия и других вязких металлов периодически смачивают лезвие зубила мыльной водой или маслом. При рубке чугуна, бронзы и других хрупких металлов на ребрах заготовки часто происходит выкрашивание. Для предотвращения выкрашивания перед рубкой на ребрах делают фаски.
Листовой материал рубят на наковальне или на плите зубилом с закругленным лезвием, причем сначала делаю? надрубку легкими ударами по разметочной линии, а затем разрубают металл сильными ударами.
Основным оборудованием рабочего места слесаря является верстак (рис. 42,а, б), представляющий собой прочный, устойчивый стол высотой 0,75 и шириной 0,85 м. Крышка верстака должна быть изготовлена из досок толщиной не менее 50 мм. Сверху и с боков верстак обивают листовой сталью. На верстаке устанавливают стуловые или тяжелые параллельные тиски. Стол имеет выдвижные ящики для хранения слесарного инструмента, чертежей и обрабатываемых заготовок и деталей.
Перед началом работы слесарь обязательно должен проверить слесарные инструменты. Обнаруженные у инструментов дефекты устраняют или заменяют непригодный к работе инструмент исправным. Категорически запрещается работать молотком с косой или сбитой поверхностью бойка, работать зубилом с косой или сбитой головкой.
Рис. 42. Рабочее место слесаря:
а — одноместный верстак, б — двухмесгный верстак
Для защиты глаз от осколков слесарь должен работать обязательно в очках. Для защиты окружающих от отлетающих осколков на верстаке устанавливают металлическую сетку. Верстак должен быть прочно установлен на полу, а тиски хорошо закреплены на верстаке. Работать на плохо установленных верстаках, а также на слабо закрепленных тисках нельзя, так как это может привести к ранению руки, кроме того, быстро утомляет.
Правка и гибка металла
Слесарная правка применяется обычно для выравнивания искривленной формы заготовок и деталей. Правку выполняют вручную или на правильных валках, прессами, на листоправйльных и углоправйльных станках и т. д.
Правку вручную осуществляют на правйльной чугунной плите или на кузнечной наковальне слесарными деревянными или металлическими молотками. Тонкий листовой материал правят на правильных плитах. При правке листового материала толщиной менее 1 мм применяют деревянные или стальные бруски, которыми приглаживают листы на правйльной плите. При правке листов толщиной более 1 мм применяют деревянные или металлические молотки.
При ручной правке листового материала вначале выявляют все выпуклости и отмечают их мелом, затем лист укладывают на правильную плиту так, чтобы выпуклости находились сверху. После этого начинают наносить удары молотком с одного края листа в направлении выпуклости, а затем с другого края. Удары молотка должны быть не очень сильными, но частыми. Молоток следует держать крепко и наносить удары по листу центральной частью бойка, не допуская никаких перекосов, так как при неправильных ударах на листе могут появиться вмятины или другие дефекты.
Полосовой материал правят на правйльных плитах ударами молотка; прутковый материал круглого сечения правят на специальном правйльно-калибровочном станке.
Вмятины на крыльях, капоте и кузове автомобиля выправляют сначала при помощи фигурных рычажков, затем под вмятину устанавливают болванку или оправку и ударами металлического или деревянного молотка выправляют вмятину.
Гибка металла применяется для получения необходимой формы изделий из листового, пруткового материала, а также из труб. Гибку осуществляют ручным или механическим способом.
При гибке ручным способом предварительно размеченный металлический лист устанавливают в приспособление и зажимают в тисках, после чего наносят удары по выступающей из приспособления части деревянным молотком.
Трубы гнут ручным или механическим способом. Трубы больших размеров (например, трубу глушителя) обычно гнут с предварительным подогревом в местах изгиба. Трубы небольших размеров (трубки систем питания и тормозной) гнут в холодном состоянии. Для того чтобы при гибке не сплющивались стенки трубы, а в местах изгиба не изменялось сечение, трубу предварительно заполняют мелким сухим песком, канифолью или свинцом. Чтобы получить нормальное закругление, а ь месте изгиба труба была круглой (без складок и вмятин), нужно правильно выбрать радиус изгиба (большему диаметру трубы соответствует больший радиус). Для гибки в холодном состоянии трубы должны быть предварительно отожжены. Температура отжига зависит от материала трубы. Например, медные и латунные трубы отжигают при температуре 600—700 °Сс последующим охлаждением в воде, алюминиевые при температуре 400—580 °С с последующим охлаждением на воздухе, стальные при 850—900 °С с последующим охлаждением на возухе.
Рис. 43. Роликовое приспособление для гибки труб
Гибку труб производят при помощи различных приспособлений. На рис. 43 показано роликовое приспособление Механическуюгибку труб осуществляют на трубогибочных, кромкогнбочных станках, универсально-гибочных прессах.
Резка металла
При резке металла пользуются различными инструментами: кусачками, ножницами, ножовками, труборезами. Применение того или иного инструмента зависит от материала, профиля и размеров обрабатываемой заготовки или детали. Например, для резки проволоки применяют кусачки (рис, 44,а), которые изготовляют из инструментальной стали марки У7 или У8. Губки кусачек подвергаются закалке с последующим низким (нагрев до 200° С и медленное охлаждение) отпуском.
Рис. 44. Инструменты для резки металла: а — кусачки, б — стуловые ножницы, в — рычажные ножницы
Для резки листового материала используют ручные, стуловые, рычажные, электрические, пневматические, гильотинные, дисковые ножницы. Тонкий листовой материал (до 3 мм) обычно режут ручными или стуловыми ножницами (рис. 44, б), а толстый (от 3 до 6 мм) — рычажными (рис. 44, в). Такие ножницы изготовляют из углеродистой инструментальной стали У8, У10. Режущие кромки ножниц закаливают. Угол заострения режущих кромок ножниц обычно не превышает 20—30°.
При резке ножницами предварительно размеченный металлический лист располагают между лезвиями ножниц с таким расчетом, чтобы разметочная линия совпадала с верхним лезвием ножниц.
Все более широкое применение находят электрические и пневматические ножницы. В корпусе электрических ножниц имеется электродвигатель (рис. 45), ротор которого при помощи червячной передачи приводит во вращение эксцентриковый валик, с которым связан шатун, приводящий в движение подвижный нож. Нижний неподвижный нож жестко связан с корпусом ножниц.
Рис. 45. Электрические ножницы И-31
Пневматические ножницы работают под действием сжатого воздуха.
Гильотинными ножницами с механическим приводом разрезают стальные листы толщиной до 40 мм. Дисковыми ножницами разрезают листовой материал толщиной до 25 мм по прямой или кривой линиям.
Для резки небольших заготовок или деталей применяют ручные и электромеханические ножовки.
Ручная ножовка (рис. 46) представляет собой стальную раздвижную рамку, называемую станком, в которой укреплено стальное ножовочное полотно. Ножовочное полотно имеет форму пластины длиной до 300 мм, шириной от 3 до 16 мм и толщиной от 0,65 до 0,8 мм. Зубья ножовочного полотна разводятся в разные стороны с таким расчетом, чтобы ширина пропила, образующегося при резке, получалась на 0,25—0,5 мм больше толщины ножовочного полотна.
Ножовочные полотна бывают с мелкими и крупными зубьями. При разрезании деталей с тонкими стенками, тонкостенных труб и тонкого профильного проката применяют полотна с мелкими зубьями, а для резки мягких металлов и чугуна — с крупными зубьями.
Ножовочное полотно устанавливают в станке зубьями вперед и натягивают так, чтобы оно во время работы не перекашивалось. Перед началом работы разрезаемую заготовку или деталь устанавливают и зажимают в тисках так, чтобы разметочная линия (линия разреза) была расположена как можно ближе к губкам тисков.
Во время работы слесарь должен держать ножовку за рукоятку правой рукой, а левая рука должна лежать на переднем конце станка. При перемещении ножовки от себя совершается рабочий ход. При этом ходе нужно делать нажим, а при обратном перемещении ножовки, т. е. при перемещении на себя, происходит холостой ход, при котором нажима не следует делать.
Работа ручной ножовкой малопроизводительная и утомительна для рабочего. Применение электромеханических ножовок резко повышает производительность труда. Устройство электромеханической ножовки показано на рис. 47. В корпусе ножовки имеется электродвигатель, приводящий во вращение вал, на котором насажен барабан.
Рис. 47. Электромеханическая ножовка
На барабане имеется спиральный паз, по которому перемещается палец, закрепленный в ползуне. К ползуну прикреплено ножовочное полотно. При работе электродвигателя барабан вращается, а ножовочное полотно, прикрепленное к ползуну, совершая возвратно-поступательное движение, режет металл. Планка предназначена для упора инструмента при работе.
Полотно ножовки.
Рис. 46. Ножовка:
1 — станок, 2 — неподвижная серьга, 3 — рукоятка, 4 — ножовочное полотно, 5 — лупа, 6 — барашек, 7 — подвижная серьга
Рис. 48. Труборез
Для резки труб применяется труборез. Он состоит из скобы (рис. 48) с тремя дисковыми резцами, из которых резцы неподвижны, а резец подвижный, и рукоятки, установленной на резьбе. При работе труборез надевают на трубу, поворотом рукоятки придвигают подвижный диск до соприкосновения с поверхностью трубы, затем, вращая труборез вокруг трубы, разрезают ее.
Трубы и профильный материал режут также ленточными или дисковыми пилами. Устройство ленточной пилы ЛС-80 показано на рис. 49. На станине пилы имеется стол с прорезью, предназначенной для прохода (ленты) полотна пилы. В нижней части станины находятся электродвигатель и ведущий шкив пилы, а в верхней части станины — ведомый шкив. При помощи маховичка натягивают полотно пилы.
В дисковых пилах вместо режущей ленты имеется режущий диск. Особенностью дисковых пил является возможность резки профильного металла под любым углом.
Для резки закаленной стали и твердых сплавов применяют также тонкие шлифовальные круги.
Опиливание металла
Опиливание является одним из видов слесарной обработки, заключающимся в снятии с заготовки или детали слоя металла для получения заданных форм, размеров и чистоты поверхности.
Этот вид обработки выполняют специальным слесарным инструментом, называемым напильником. Напильники изготовляют из инструментальных сталей У12, У12А, У13 или У13А, ШХ6, ШХ9, ШХ15 с обязательной закалкой. По форме поперечного сечения напильники разделяются на плоские (рис. 50, а), полукруглые (рис. 50,6), квадратные (рис. 50,в), трехгранные (рис. 50,г), круглые (рис. 50, д) и др.
По видам насечки напильники бывают с одинарной и с двойной насечкой (рис. 51,а, б). Напильники с одинарной насечкой применяют для опиливания мягких металлов (свинец, алюминий, медь, баббит, пластмассы), напильники с двойной насечкой — для обработки твердых металлов. В зависимости от числа насечек, приходящегося на 1 пог. см, напильники делятся на шесть номеров. К № 1 относятся напильники крупной насечки с числом зубьев от 5 до 12, так называемые «драчевые». Напильники с насечкой № 2 имеют число зубьев от 13 до 24, они называются «личными». Так называемые «бархатные» напильники имеют мелкую насечку — № 3, 4, 5, 6, изготовляются с числом зубьев от 25 до 80.
Рис. 49. Ленточная пила ЛС-80
Рис. 50. Напильники и их применение (слева):
а — плоский, о — полукруглый, в — квадратный, г — трехгранный, д — круглый
Для грубого опиливания, когда требуется снять слой металла от 0,5 до 1 мм, применяют драчевые напильники, которыми за один рабочий ход можно снять слой металла толщиной 0,08—0,15 мм.
В тех случаях, когда после предварительного грубого опиливания драчевыми напильниками требуется чистая и точная обработка заготовки или детали, применяют личные напильники, которыми можно снимать за один ход слой металла толщиной 0,02—0,03 мм.
Рис. 51. Насечка напильников:
а — одинарная, б — двойная
Бархатные напильники применяют для самой точной обработки и придания обрабатываемой поверхности высокой чистоты. Для доводочных и других специальных работ применяют напильники, называемые «надфилями». Они имеют самую мелкую насечку. Для опиливания мягких материалов (дерева, кожи, рога и др.) применяют напильники, которые называются рашпилями.
Выбор напильника зависит от твердости обрабатываемой поверхности и формы заготовки или детали. Для увеличения срока службы напильников необходимо принимать меры, предохраняющие от попадания на них воды, масла, грязи. После работы насечку напильников следует очистить металлической щеткой от грязи и опилок, застрявших между зубьями насечки. На хранение напильники укладывают в инструментальные ящики в один ряд, не допуская прикасания их друг к другу. Для предотвращения замасливания напильника во время работы насечку натирают маслом или сухим древесным углем.
Приемы опиливания. Производительность и точность опиливания зависят в основном от того, насколько согласованы движения правой и левой рук, а также от силы нажима на напильник и положения корпуса слесаря. При опиливании слесарь стоит сбоку тисков на расстоянии приблизительно 200 мм от края верстака для того, чтобы движение его рук было свободным. Положение корпуса слесаря прямое и повернуто на 45° по отношению к продольной оси тисков.
Напильник берут за ручку правой рукой так, чтобы большой палец располагался сверху вдоль ручки, а остальные пальцы обхватывали ее снизу. Левая рука должна лежать ладонью поперек верхней поверхности переднего конца напильника.
Движение напильника должно быть строго горизонтальным, а сила нажима рук должна регулироваться в зависимости от точки опоры напильника на обрабатываемой поверхности. Если точка опоры находится посередине напильника, то сила нажима обеими руками должна быть одинаковой. При движении напильника вперед нужно нажим правой руки увеличивать, а левой, наоборот, уменьшать. Движение напильника назад должно происходить без нажима.
При опиливании на обрабатываемой поверхности остаются следы зубьев напильника, называемые штрихами. Штрихи в зависимости от направления движения напильника могут быть продольными или перекрестными. Качество опиливания определяется тем, насколько равномерно располагаются штрихи. Для получения пра-аильной опиленной поверхности, равномерно покрытой штрихами, Применяют перекрестное опиливание, заключающееся в том, что сначала опиливают параллельными штрихами справа налево, а затем слева направо (рис. 52,а).
После грубого опиливания проверяют качество работы на просвет поверочной линейкой, которую прикладывают вдоль, поперек и по диагонали обработанной плоскости. Если просвет одинаковый или его совсем нет, качество опиливания считается хорошим.
Более точным способом является проверка «на краску», заключающаяся в том, что на поверхность проверочной плиты наносят тонкий слой краски (обычно синьки или сажи, разведенной на масле) и накладывают на нее деталь обработанной поверхностью, а затем, легко нажимая на деталь, передвигают ее по всей плите и снимают. Если следы краски равномерно располагаются по всей поверхности детали, считается, что опиливание выполнено правильно.
Тонкие круглые детали опиливают следующим образом. В тиски зажимают деревянный брусок с трехгранным вырезом, в который укладывают опиливаемую деталь, а конец ее зажимают в ручные тисочки (рис. 52, б). При опиливании ручные тисочки вместе с закрепленной в них деталью постепенно повертывают левой рукой.
При опиливании нескольких плоскостей, расположенных относительно друг друга под углом 90°, поступают следующим образом. Вначале перекрестным опиливанием обрабатывают широкие противоположные плоскости и проверяют их на параллельность. После этого опиливают одну из узких плоскостей продольными штрихами. Качество обработки ее проверяют линейкой на просвет, углы, образованные с широкой плоскостью,— угольником. Затем опиливают остальные плоскости. Узкие плоскости на взаимную перпендикулярность проверяют угольником.
При опиливании деталей, изготовленных из тонкого листового металла, вначале обрабатывают широкие плоскости на плоскошлифовальных станках, затем детали соединяют в пачки и опиливают их ребра обычными приемами.
Распиливание прямолинейных фасонных пройм начинается обычно с изготовления вкладышей и только после этого приступают к проймам. Вначале опиливают наружные ребра проймы, затем обозначают центр и контуры проймы, после разметки просверливают круглое отверстие с таким расчетом, чтобы края отверстия отстояли от разметочных линий не менее чем на I—2 мм. После этого производят предварительное опиливание отверстия (проймы) и в его углах делают подрезки надфилем
Рис. 52. Опиливание поверхностей:
а — широкой плоской, б — цилиндрической
Затем приступают к окончательной обработке, опиливая вначале две взаимно параллельные стороны проймы, после чего по шаблону опиливают рядом расположенную сторону, а затем следующую противоположную, параллельную ей. Размечают пройму на несколько сотых миллиметра меньше размеров вкладыша. Когда пройма готова, делают припасовку (точную пригонку деталей друг к другу) по вкладышу.
После припасовки вкладыш должен входить в пройму и в местах соприкосновения с ней не иметь просветов.
Одинаковые детали изготовляют опиливанием по копиру-кондуктору. Копир-кондуктор является приспособлением, контур рабочих поверхностей которого соответствует контуру изготовляемой детали.
Для опиливания по копиру-кондуктору заготовку зажимают вместе с копиром в тиски (рис. 53) и опиливают выступающие за контур копира части заготовки. Такой способ обработки повышает производительность труда при опиливании деталей из тонкого листового материала, которые зажимают в тиски сразу по нескольку штук.
Механизация процесса опиливания. На ремонтных предприятиях ручное опиливание заменяется механизированным, выполняемым на опиловочных. станках при помощи специальных приспособлений, электрическими и пневматическими шлифовальными машинками. К легким переносным машинкам относятся очень удобная электрическая шлифовальная машинка И-82 (рис. 54, а) и пневматическая шлифовальная машинка ШР-06 (рис. 54,6), на шпинделе которых имеется абразивный круг. Шпиндель приводится в действие пневматическим роторным двигателем.
Для опиливания поверхностей в труднодоступных местах применяют механический напильник (рис. 54,в), работающий от электрического привода с гибким валом, который вращает наконечник /. Вращение наконечника передается через валик и червячную передачу эксцентрику 2. Эксцентрик при вращении сообщает плунжеру 3 и прикрепленному к нему напильнику возвратно-поступательное движение.
Техника безопасности при опиливании. Опиливаемая заготовка должна быть надежно зажата в тисках, чтобы в процессе работы она не могла изменять своего положения или выскочить из тисков. Напильники обязательно должны быть с деревянными ручками, на которые насажены металлические кольца. Ручки прочно насаживаются на хвостовики напильников.
Стружку, образующуюся при опиливании, убирают волосяной щеткой. Категорически запрещается слесарю убирать стружку голыми руками или сдувать ее, так как это может привести к ранению рук и глаз.
Рис. 53. Опиливание по копиру:
1 — копирная планка, 2 — снимаемый слой
Рис. 54. Инструменты для механизированного опиливания:
а — электрическая шлифовальная машинка И-82, 6 — пневматическая шлифовальная машинка ШР-06, в — механический напильник
При работе с переносными электрическими инструментами необходимо предварительно проверить надежность их заземления.
Шабрение
Шабрением называется процесс снятия очень тонкого слоя металла с недостаточно ровной поверхности специальным инструментом — шабером. Шабрение является окончательной (точной) отделкой поверхностей сопряженных деталей станков, вкладышей подшипников скольжения, валов, поверочных и разметочных плит и т. п. для обеспечения плотного прилегания частей соединения.
Шаберы изготовляют из высокоуглеродистой инструментальной стали У12А или У12. Часто шаберы делают из старых напильников, удалив с них насечку наждачным кругом. Режущую часть шабера закаливают без последующего отпуска с целью придания ей высокой твердости.
Шабер затачивают на наждачном круге так, чтобы штрихи от заточки располагались поперек лезвия. Во избежание сильного нагрева лезвия при заточке шабер периодически охлаждают в воде. После заточки лезвие шабера доводят на точильных брусках-оселках или на абразивных кругах, поверхность которых покрыта машинным маслом.
Шаберы бывают с одним или двумя режущими концами, первые называются односторонними, вторые — двусторонними. По форме режущего конца шаберы разделяют на плоские (рис. 55, а), трехгранные (рис. 55, б) и фасонные.
Плоские односторонние шаберы бывают с прямым или отогнутым вниз концом, применяются для шабрения плоских поверхностей пазов, канавок. Для шабрения кривых поверхностей (при обработке втулок, подшипников и т. п.) применяют трехгранные шаберы.
Фасонные шаберы предназначены для шабрения фасонных поверхностей, сложных по профилю канавок, желобков, пазов и т. п. Фасонный шабер представляет собой набор стальных пластинок, форма которого соответствует форме обрабатываемой поверхности. Пластинки насаживаются на металлическую державку.шабера и закрепляются на ней гайкой.
Качество обработки поверхности шабрением проверяют на поверочной плите.
В зависимости от длины и ширины обрабатываемой плоской поверхности величина припуска на шабрение должна быть от 0,1 до 0,4 мм.
Поверхность детали или заготовки перед шабрением обрабатывают на металлорежущих станках или опиливанием.
После предварительной обработки начинают шабрение. Поверхность поверочной плиты покрывают тонким слоем краски (сурик, синька или сажа, разведенные в масле). Обрабатываемую поверхность тщательно протирают тряпкой, аккуратно накладывают на поверочную плиту и медленно перемещают по ней круговыми движениями, после чего осторожно снимают.
В результате такой операции все выступающие на поверхности участки окрашиваются и отчетливо выделяются пятнами. Окрашенные участки (пятна) вместе с металлом удаляют шабером. Затем обрабатываемую поверхность и поверочную плиту очищают и плиту вновь покрывают слоем краски, а заготовку или деталь снова накладывают на нее.
Рис. 55. Шаберы ручные:
а — прямой плоский односторонний и плоский односторонний с отогнутым концом, б — трехгранные
Вновь образующиеся пятна на поверхности опять удаляют шабером. Пятна при повторных операциях будут делаться меньшего размера, а число их будет увеличиваться. Шабрят до тех пор, пока пятна не будут равномерно расположены по всей обрабатываемой поверхности, а количество их будет соответствовать техническим условиям.
При шабрении кривых поверхностей (например, вкладыша подшипника) вместо поверочной плиты пользуются шейкой вала, которая должна находиться в сопряжении с обрабатываемой поверхностью вкладыша. В этом случае вкладыш подшипника накладывают на шейку вала, покрытую тонким слоем краски, осторожно поворачивают его вокруг нее, затем снимают, зажимают в тиски и шабрят по пятнам.
При шабрении шабер устанавливают по отношению к обрабатываемой поверхности под углом 25—30° и держат его правой рукой за ручку, прижав локоть к туловищу, а левой рукой нажимают на шабер. Шабрение производится короткими движениями шабера, причем если шабер плоский прямой, то движение его должно быть направлено вперед (от себя), плоским шабером с отогнутым вниз концом движение производят назад (к себе), а трехгранным шабером — вбок.
В конце каждого хода (движения) шабера его отрывают от обрабатываемой поверхности, чтобы не получились заусенцы и уступы. Для получения ровной и точной обрабатываемой поверхности направление шабрения каждый раз после проверки по краске меняют так, чтобы штрихи пересекались.
Точность шабрения определяют по количеству равномерно расположенных пятен на площади размером 25X25 мм2 обработанной поверхности путем наложения на нее контрольной рамки. Среднее количество пятен определяется проверкой нескольких участков обрабатываемой поверхности.
Шабрение вручную является очень трудоемким и поэтому оно на крупных предприятиях заменяется шлифованием, точением или его осуществляют механизированными шаберами, применение которых облегчает труд и резко повышает его производительность.
Рис. 56. Механизированный шабер
Механизированный шабер приводится в действие электродвигателем (рис. 56) через гибкий вал, присоединенный одним концом к редуктору, а другим к кривошипу. При включении электродвигателя кривошип начинает вращаться, сообщая шатуну и прикрепленному к нему шаберу возвратно-поступательное движение. Кроме электрического шабера, применяют пневматические шаберы.
Притирка
Притирка является одним из самых точных способов окончательной доводки обрабатываемой поверхности, обеспечивающим высокую точность обработки — до 0,001—0,002 мм. Процесс притирки заключается в снятии тончайших слоев металла абразивными порошками, специальными пастами. Для притирки применяют абразивные порошки из корунда, электрокорунда, карбида кремния, карбида бора и др. Притирочные порошки по зернистости разделяются на шлифпорошки и микропорошки. Первые применяются для грубой притирки, вторые — для предварительной и окончательной доводки.
Для притирки поверхностей сопряженных деталей, например клапанов к седлам в двигателях, ниппелей к гнездам кранов и т. п., применяют преимущественно пасты ГОИ (Государственного оптического института). Пастами ГОИ притирают любые металлы, как твердые, так и мягкие. Эти пасты выпускаются трех видов: грубые, средние и тонкие.
Грубая паста ГОИ имеет темно-зеленый цвет (почти черный), средняя — темно-зеленый, а тонкая — светло-зеленый. Инструменты— притиры изготовляются из серого мелкозернистого чугуна, меди, бронзы, латуни, свинца. Форма притира должна соответствовать форме притираемой поверхности.
Притирка может осуществляться двумя способами: при помощи притира и без него. Обработку несопрягаемых между собой поверхностей, например калибров, шаблонов, угольников, плиток и т. п., осуществляют при помощи притира. Сопрягаемые поверхности обычно притирают друг к другу без применения притира.
Притиры представляют собой подвижные вращающиеся диски, кольца, стержни или неподвижные плиты.
Процесс притирки несопрягаемых плоскостей производится следующим образом. На поверхность плоского притира насыпают тонкий слой абразивного порошка или наносят слой пасты, который затем вдавливают в поверхность стальным бруском или катающимся роликом.
При подготовке притира цилиндрической формы абразивный порошок насыпают ровным тонким слоем на стальную закаленную плиту, после чего притир катают по шщте до тех пор, пока абразивный порошок не вдавится в его поверхность. Подготовленный притир вставляют в обрабатываемую деталь и с легким нажимом перемещают вдоль ее поверхности или, наоборот, обрабатываемую деталь перемещают вдоль поверхности притира. Абразивные зерна порошка, вдавленные в притир, срезают с притираемой поверхности детали слой металла толщиной 0,001—0,002 мм.
Обрабатываемая деталь должна иметь припуск на притирку не более 0,01—0,02 мм. Для повышения качества притирки применяются смазывающие вещества: машинное масло, бензин, керосин и др.
Сопрягаемые детали притирают без притиров. На подготовленные к притирке поверхности деталей наносят тонкий слой соответствующей пасты, после чего детали начинают перемещать одну по другой круговыми движениями то в одну, то в другую сторону.
Процесс притирки ручным способом часто заменяется механизированным.
В ремонтных мастерских автомобильных хозяйств для притирки клапанов к седлам применяются коловороты, электрические дрели и пневматические машинки.
Клапан к его седлу притирают следующим образом. Клапан устанавливают в направляющую втулку блока цилиндров, предварительно надев на стержень клапана слабую пружину и фетровое кольцо, которое предохраняет направляющую втулку от попадания в нее притирочной пасты. После этого рабочую фаску клапана смазывают пастой ГОИ и начинают вращать клапан ручной или электрической дрелью, делая одну треть оборота влево, а затем два-три оборота вправо. При изменении направления вращения необходимо ослаблять нажим на дрель, чтобы клапан под действием пружины, надетой на его стержень, приподнимался над седлом.
Притирают клапан обычно вначале грубой пастой, а затем средней и тонкой. Когда на рабочей фаске клапана и седла образуется матово-серая полоса в виде кольца без пятен, притирка считается законченной. После притирки клапан и седло тщательно промывают, чтобы удалить оставшиеся частицы притирочной пасты.
Сверление применяется для получения в заготовках или деталях круглых отверстий. Сверление осуществляют на сверлильных станках или механической (ручной), электрической или пневматической дрелью. Режущим иструментом является сверло. Сверла по конструкции разделяются на перовые, спиральные, центровые, сверла для сверления глубоких отверстий и комбинированные. В слесарном деле применяют преимущественно спиральные сверла. Сверла изготовляют из инструментальных углеродистых сталей У10А, У12А, а также из легированных хромистых сталей 9ХС, 9Х и быстрорежущих Р9 и Р18.
Спиральное сверло (рис. 57) имеет форму цилиндрического стержня с конусообразным рабочим концом, у которого по сторонам имеются две винтовые канавки с наклоном к продольной оси сверла в 25—30°. По этим канавкам стружка отводится наружу. Хвостовая часть сверла делается цилиндрической или конической. Угол заточки при вершине сверла может быть разным и зависит от обрабатываемого материала. Например, для обработки мягких материалов он должен быть от 80 до 90°, для стали и чугуна 116—118°, для очень твердых металлов 130—140°.
Сверлильные станки. В ремонтных мастерских наибольшее применение имеют одношпиндельные вертикально-сверлильные станки (рис. 58). Обрабатываемая заготовка или деталь помещается на столе, который можно поднимать и опускать при помощи винта. Рукояткой стол закрепляют на станине на необходимой высоте. Сверло устанавливают и закрепляют в шпинделе. Шпиндель приводится во вращение электродвигателем через коробку скоростей, автоматическая подача осуществляется коробкой подач. Вертикальное перемещение шпинделя осуществляется вручную маховиком.
Ручная дрель (рис. 59) состоит из шпинделя, на котором находится патрон, конической зубчатой передачи (состоящей из большого и малого зубчатых колес), неподвижной ручки, подвижной ручки и нагрудника. Сверло вставляют в патрон и закрепляют. При сверлении слесарь удерживает дрель левой рукой за неподвижную ручку, а правой вращает подвижную ручку, опираясь грудью на нагрудник.
Рис. 57. Спиральное сверло:
1 — рабочая часть сверла, 2 —шейка, 3 — хвостовик, 4 — лапка, л — канавка, 6 — перо, 7 — направляющая фаска (ленточка), 8 — поверхность задней заточки, 9 — режущие кромгки, 10 — перемычка, 11 — режущая часть
Рис. 58. Одношпиндельный вертикально-сверлильный станок 2135
Пневматическая дрель (рис. 60, а) работает под действием сжатого воздуха. Она удобна в работе, так как имеет небольшие габариты и вес.
Электрическая дрель (рис. 60, б) состоит из электродвигателя, зубчатой передачи и шпинделя. На конец шпинделя навинчивается патрон, в котором зажимается сверло. На кожухе имеются рукоятки, в верхней части корпуса — нагрудник для упора при работе.
Сверление производят или по разметке, или по кондуктору. При сверлении по разметке сначала размечают отверстие, затем его накернивают по окружности и по центру. После этого закрепляют обрабатываемую заготовку в тисках или другом приспособлении и приступают к сверлению. Сверление по разметке обычно осуществляют в два приема. Сначала просверливают отверстие на глубину четверти диаметра. Если полученное отверстие (несквозное) совпадает с размеченным, то продолжают сверление, в противном случае исправляют установку сверла и только после этого продолжают сверление. Такой способ имеет наибольшее применение.
Рис. 59. Ручная дрель
Рис. 60. Пневматическая (а) и электрическая (б) дрели:
1 — ротор, 2 — статор, 3 — патрон, 4 — шпиндель, 5 — редуктор, 6 — курок
Сверление большого количества одинаковых деталей с высокой точностью осуществляется по кондуктору (шаблону, имеющему точно выполненные отверстия). Кондуктор накладывают на обрабатываемую заготовку или деталь и через отверстия в кондукторе производят сверление. Кондуктор не дает возможности сверлу отклоняться, благодаря чему отверстия получаются точными и расположенными на нужном расстоянии. При сверлении отверстия под резьбу необходимо пользоваться справочными пособиями для выбора величины диаметра сверла в соответствии с видом резьбы, а также с учетом механических свойств обрабатываемого материала.
Причины поломок сверл. Основными причинами поломок сверл при сверлении являются: отклонение сверла в сторону, наличие в обрабатываемой заготовке или детали раковин, закупорка канавок на сверле стружкой, неправильная заточка сверла, плохая термическая обработка сверла, тупое сверло.
Заточка сверл. На производительность работы и качество сверления большое влияние оказывает заточка сверла. Сверла затачивают на специальных станках. В небольших мастерских сверла затачивают вручную на наждачных точилах. Контроль заточки сверла осуществляют специальным шаблоном, имеющим три поверхности а, б, в, (рис. 61).
Зенкование отверстий — последующая (после сверления) обработка отверстий, заключающаяся в удалении заусенцев, снятии фасок и получении конусного или цилиндрического углубления у входной части отверстия. Зенкование осуществляют специальными режущими инструментами — зенковками. По форме режущей части зенковки делят на цилиндрические и конические (рис. 62, а, б). Конические зенковки применяют для получения в отверстиях конусных углублений под головки заклепок, потайных винтов и болтов. Конические зенковки могут быть с углом при вершине 30, 60 и 120°.
Цилиндрическими зенковками обрабатывают плоскости бобышек, углубления под головки шурупов, болтов, винтов, шайб. Цилиндрическая зенковка имеет направляющую цапфу, которая входит в обрабатываемое отверстие и обеспечивает правильное направление зенковки. Зенковки изготовляют из углеродистых инструментальных сталей У10, У11, У12.
Зенкерование представляет собой последующую обработку отверстий перед развертыванием специальным инструментом — зенкером, режущая часть которого имеет больше режущих кромок, чем сверло.
По форме режущей части зенкеры бывают спиральные и прямые, по конструкции их разделяют на цельные, насадные и со вставными ножами (рис. 63, а, б, в). По числу режущих кромок зенкеры бывают трех- и четырехзубые. Цельные зенкеры имеют три или четыре режущие кромки, насадные — четыре режущие кромки. Зенкерование выполняют на сверлильных станках, а также пневматическими и электрическими дрелями. Зенкеры крепят так же, как и сверла.
Развертывание является чистовой обработкой отверстия, выполняемой специальным режущим инструментом, называемым разверткой.
При сверлении отверстия оставляют припуск на диаметр под черновое развертывание не более 0,2—0,3 мм, а под чистовое — 0,05—0,1 мм. После развертывания точность размера отверстия повышается до 2—3-го класса.
Рис. 61. Шаблон для контроля заточки сверл
Рис. 62. Зенковки:
а — цилиндрическая, б — коническая
Развертки по способу приведения в действие делятся на машинные и ручные, по форме обрабатываемого отверстия — на цилиндрические и конические, по устройству — на цельные и сборные. Развертки изготовляют из инструментальных сталей.
Цилиндрические цельные развертки бывают с прямым или винтовым (спиральным) зубом, а следовательно, и такими же канавками. Цилиндрические развертки со спиральным зубом могут быть с правыми или левыми канавками (рис. 64, а, б). Развертка состоит из рабочей части, шейки и хвостовика (рис. 64, в).
Рис. 63. Зенкеры:
а — цельный, б —насадной, я —со вставными ножами
Рис. 64. Цилиндрические развертки:
а — с правой винтовой канавкой, б — с левой винтовой канавкой, в — основные части развертки
Режущая, или заборная, часть делается конусной, она выполняет основную работу резания по снятию припуска. Каждая режущая кромка образует с осью развертки главный угол в плане Ф (рис. 64, в), который у ручных разверток обычно составляет 0,5—1,5°, а у машинных 3—5° — для обработки твердых металлов и 12—15° — для обработки мягких и вязких металлов. .
Режущие кромки заборной части образуют с осью резвертки угол при вершине 2 ср. На конце режущей части снимается фаска под углом 45°. Это необходимо для предохранения вершин режущих кромок от забоин и выкрашивания при работе.
Калибрующая часть развертки резания почти не производит, она состоит из двух участков: цилиндрического, который служит для калибрования отверстия, направления развертки, и участка с обратной конусностью, предназначенного для уменьшения трения развертки о поверхность отверстия и предохранения отверстия от разработки.
Шейкой называется участок развертки между рабочей частью и хвостовиком. Диаметр шейки на 0,5—1 мм меньше диаметра калибрующей части. У машинных разверток хвостовики конической формы, у ручных — квадратные. Развертки бывают с равномерным и неравномерным шагом зубьев. Машинные развертки закрепляют в шпинделе станка при помощи конических гильз и патронов, ручные развертки — в воротке, при помощи которого и производится развертывание.
Конические развертки применяют для развертывания конических отверстий под конус Морзе, под конус метрический, под штифты с конусностью 1 :50. Конические развертки изготовляют комплектами из двух или трех штук. Комплект из трех разверток состоит из черновой, промежуточной и чистовой (рис. 65, а, б, в). В комплекте из двух разверток одна является переходной, а другая чистовой. Конические развертки изготовляют с режущей частью по всей длине зуба, которая у чистовых разверток является и калибрующей частью.
Развертывание вручную и на станках. Ручное развертывание осуществляют при помощи воротка, в котором закрепляют развертку. При ручном развертывании мелкие заготовки или детали закрепляют в тисках, а большие обрабатывают без, закрепления.
После закрепления заготовки или детали режущую часть развертки вводят в отверстие с таким расчетом, чтобы оси развертки и отверстия совпадали. После этого медленно вращают развертку по часовой стрелке; вращать развертку в обратном направлении нельзя, так как могут получиться задиры. При машинном развертывании на станках поступают так же, как при сверлении.
Рис. 65. Конические развертки:
а — черновая, б — промежуточная, в — чистовая
При развертывании отверстий в стальных заготовках или деталях в качестве смазки применяют минеральные масла; в медных, алюминиевых, латунных деталях — мыльную эмульсию. В чугунных и бронзовых заготовках отверствия развертывают всухую.
Выбор диаметра развертки имеет большое значение для получения необходимых размера отверстия и чистоты его поверхности. При этом учитывают толщину стружки, снимаемой инструментом (табл. 2).
Пользуясь данной таблицей -‘можно выбрать диаметр развертки и зенкера.
Пример. Необходимо развернуть ручным способом отверстие диаметром 50 мм. Для этого берут чистовую развертку диаметром 50 мм, а черновую развертку 50—0,07=49,93 мм.
При выборе машинной чистовой развертки следует учитывать величину разработки, т. е. увеличение диаметра отверстия при машинном развертывании.
При обработке отверстий сверлом, зенкером и разверткой необходимо соблюдать следующие основные правила техники безопасности:
выполнять работу только на исправных станках, имеющих необходимые ограждения;
перед началом работы привести в порядок одежду и головной убор. При работе одежда должна облегать тело без развевающихся пол, рукавов, поясов, лент и т. п., она должна быть наглухо застегнута.
Длинные волосы должны быть подобраны под головной убор:
– сверло, зенкер, развертку или приспособление точно устанавливают в шпиндель станка и прочно закрепляют;
– стружку из получаемого отверстия удалять пальцами или сдувать категорически запрещается. Удалять стружку разрешается только крючком или щеткой после остановки станка или при отводе сверла;
– обрабатываемая заготовка или деталь должна быть установлена неподвижно на столе или плите станка в приспособлении; нельзя удерживать ее руками во время обработки;
– нельзя устанавливать инструмент во время вращения шпинделя или проверять рукой остроту вращающегося сверла;
– при работе электродрелью ее корпус должен быть заземлен, рабочий должен находиться на изолированном полу.
Нарезание резьбы
Нарезание резьбы представляет собой процесс получения на цилиндрических и конических поверхностях винтовых канавок. Совокупность витков, расположенных по винтовой линии на изделии, называется резьбой.
Резьба бывает наружная и внутренняя. Основными элементами всякой резьбы являются профиль, шаг, высота, наружный, средний и внутренний диаметры.
Рис. 66. Элементы резьбы
Профилем резьбы называется форма сечения витка, проходящего через ось болта или гайки (рис. 66). Ниткой (витком) называется часть резьбы, образуемая при одном полном обороте профиля.
Шагом резьбы называется расстояние между двумя одноименными точками соседних витков, измеряемое параллельно оси резьбы, оси болта или гайки.
Высота резьбы определяется как расстояние от вершины резьбы до основания.
Вершиной резьбы называется участок профиля резьбы, находящийся на наибольшем расстоянии от оси резьбы (оси болта или гайки).
Основанием резьбы (впадиной) называется участок профиля резьбы, находящийся на наименьшем расстоянии от оси резьбы.
Углом профиля резьбы называется угол между двумя боковыми сторонами профиля резьбы.
Наружный диаметр резьбы — наибольший диаметр, измеряемый по вершине резьбы в плоскости, перпендикулярной к оси резьбы.
Рис. 67. Системы резьб:
а — метрическая; б — дюймовая, в — трубная
Средний диаметр резьбы—это расстояние между двумя линиями, параллельными оси болта, из которых каждая находится на разных расстояниях от вершины нитки и дна впадины. Ширина витков наружной и внутренней резьбы, измеренная по окружности среднего диаметра, одинакова.
Внутренний диаметр резьбы — наименьшее расстояние между противоположными основаниями резьбы, измеренное в направлении, перпендикулярном оси резьбы.
Профили и системы резьб. В деталях машин применяются различные профили резьбы. Наиболее распространенными являются треугольный, трапецеидальный и прямоугольный профили. По назначению резьбы разделяются на крепежные и специальные. Треугольная резьба применяется для скрепления деталей между собой (нарезки на болтах, шпильках, гайках и т. п.), ее часто называют крепежной. Трапецеидальную и прямоугольную резьбы применяют на деталях механизмов передачи движения (винты слесарных дисков, ходовые винты токарно-винторезных станков, подъемники, домкраты и т. п.).р. Существуют три системы резьбы: метрическая, дюймовая и трубная. Основной является метрическая резьба, которая имеет профиль в виде равностороннего треугольника с углом при вершине 60° (рис. 67, а). Во избежание заедания при сборке вершины резьбы у болтов и гаек срезаются. Размеры метрических резьб даются в миллиметрах.
Трубная резьба представляет собой мелкую дюймовую резьбу. Она имеет такой же профиль, как и дюймовая, с углом при вершине 55° (рис. 67, в). Трубная резьба применяется главным образом для газовых, водопроводных труб и муфт, соединяющих эти трубы.
Инструменты для нарезания наружныхрезьб. Для нарезания наружной резьбы применяют плашку, представляющую собой дельное или разрезное кольцо с резьбой на внутренней поверхности (рис. 68, а, б). Стружечные канавки плашки служат для образования режущих кромок, а также для выхода стружки.
По конструкции плашки разделяются на круглые (лерки), раздвижные и специальные для нарезания труб. Круглые плашки бывают цельные и разрезные. Цельные круглые плашки обладают большой жесткостью, чают чистую резьбу. Разрезные плашки применяются для нарезания резьбы невысокой точности.
Раздвижные плашки состоят из двух половинок, которые называются полуплашками. На наружных сторонах полуплашек имеются пазы с углом 120° для закрепления полуплашек в клуппе. На каждой полуплашке проставлен диаметр резьбы и номера 1 и 2, которыми руководствуются при установке их в клупп. Плашки, изготовляются из инструментальной стали У£2»
Нарезание резьбы вручную плашками осуществляют при помощи воротков и клуппов. При работе круглыми плашками применяют специальные воротки (рис. 68, в). Рамка такого зоротка имеет форму круглой плашки. В отверстие рамки устанавливают круглую плашку и закрепляют тремя стопорными винтами, имеющими конические концы, которые входят в специальные углубления на плашке. Четвертым винтом, входящим в разрез регулируемой плашки, устанавливают наружный размер резьбы.
Рис. 68. Инструменты для нарезания наружных резьб:
а — плашка разрезная, б — плашка раздвижная, в — вороток, г г- клупп с косой рамкой
Раздвижные плашки устанавливают в клупп с косой рамкой (рис. 68, г), у которой имеются две рукоятки. Обе полуплашки устанавливают в рамку. Регулировочным винтом сближают полуплашки и устанавливают их для получения резьбы нужного размера. Между крайней полуплашкой и регулировочным винтом вставляется сухарь, обеспечивающий равномерное распределение давления винта на полуплашки.
Резьбу нарезают вручную и на станках. В слесарном деле чаще пользуются ручным инструментом. Нарезание наружной резьбы раздвижными плашками заключается в следующем. Заготовку болта или другой детали зажимают в тисках и смазывают маслом. Затем на конец заготовки накладывают клупп с плашками и регулировочным винтом сближают плашки так, чтобы они врезались в заготовку на 0,2—0,5 мм.
После этого начинают вращать клупп, поворачивая его на 1—2 оборота вправо, затем на пол-оборота влево и т. д. Так делают до тех пор, пока не будет нарезана резьба на необходимую длину детали.
Затем клупп свертывают по резьбе в исходное положение, регулировочным винтом плашки сближают еще больше и повторяют процесс нарезания до получения полного профиля резьбы. После каждого прохода необходимо смазывать нарезаемую часть заготовки. Нарезание резьбы цельными плашками производится за один проход.
Рис. 69. Слесарные метчики:
а — основные части метчика, б — комплект метчиков: 1 — черновой, 2 — средний, 3 — чистовой
Инструменты для нарезания внутреннихрезьб. Внутреннюю резьбу нарезают метчиком как на станках, так и вручную. В слесарном деле преимущественно пользуются ручным способом.
Метчик (рис. 69, а) представляет собой стальной винт с продольными и винтовыми канавками, которые образуют режущие кромки. Метчик состоит из рабочей части и хвостовика. Рабочая часть разделяется на заборную и калибрующую части.
Заборной частью метчика называется передняя конусная часть, выполняющая основную работу резания. Калибрующая часть служит для направления метчика в отверстии при нарезании и калибровке резьбы. Зубья резьбовой части метчика называются режущими перьями. Хвостовик служит для закрепления метчика в патроне или в воротке. Хвостовик заканчивается квадратом. По назначению метчики делят на слесарные, гаечные, машинные и др.
Метчики применяют для нарезания резьбы вручную, они выпускаются комплектами из двух или трех штук. Комплект метчиков”“’ для нарезания метрической и дюймовой резьб состоит из трех штук: чернового, среднего и чистового (рис. 69, б). Заборная часть чернового метчика имеет 6—8 витков, среднего метчика — 3—4 витка и чистового—1,5—2 витка. Черновым метчиком производят предварительное нарезание, средним делают резьбу более точной, а чистовым осуществляют окончательное нарезание и калибруют резьбу.
По конструкции режущей части метчики бывают цилиндрические и конические. При цилиндрической конструкции все три метчика комплекта имеют разные диаметры. Только чистовой метчик имеет полный профиль резьбы, наружный диаметр среднего метчика меньше чистового на 0,6 высоты резьбы, а диаметр чернового метчика меньше диаметра чистового на полную высоту резьбы. Метчики с цилиндрической конструкцией режущей части применяются главным образом для нарезания резьбы в глухих отверстиях.
При конической конструкции все три метчика имеют одинаковый диаметр, полный профиль резьбы с различной длиной заборных частей. Такие метчики применяют для нарезания резьбы в сквозных отверстиях. Метчики изготовляют из инструментальных углеродистых сталей У10, У12. Вручную резьбы нарезают при помощи воротка, имеющего квадратное отверстие.
Заготовку или деталь закрепляют в тисках, а метчик — в воротке. Процесс нарезания резьбы состоит в следующем. Черновой метчик устанавливают вертикально в подготовленное отверстие и при помощи воротка начинают его вращать по часовой стрелке с легким нажимом. После того как метчик врежется в металл, нажим прекращают и продолжают вращение.
Периодически нужно проверять угольником положение метчика по отношению к верхней плоскости заготовки. Метчик следует повернуть на 1—2 оборота по часовой стрелке, а затем на пол-оборота против часовой стрелки. Это следует делать для
того, чтобы получающаяся при нарезании стружка дробилась и тем самым облегчалась работа.
После чернового метчика нарезание производят средним, а затем чистовым. Для получения чистой резьбы и охлаждения метчика при нарезании применяют смазку. При нарезании резьбы в стальных заготовках в качестве смазывающих и охлаждающих жидкостей применяют минеральное масло, олифу или эмульсию, в алюминиевых — керосин, в медных — скипидар. В чугунных и бронзовых заготовках резьбы нарезают всухую.
При нарезании резьбы в заготовках, изготовленных из мягких и вязких металлов (баббит, медь, алюминий), метчик периодически вывертывают из отверстия и очищают канавки от стружки.
При работе метчиком возможны различные дефекты, например поломка метчика, рваная резьба, срыв резьбы и др. Причинами этих дефектов являются: тупой метчик, забивание канавок метчика стружкой, недостаточная смазка, неправильные установка метчика в отверстие и выбор диаметра отверстия, а также невнимательное отношение работающего.
Клепка
При ремонте машин и их сборке слесарю приходится иметь дело с различными соединениями деталей. В зависимости от способа сборки соединения могут быть разъемными и неразъемными. Одним из способов сборки деталей в неразъемное соединение является клепка.
Клепка производится при помощи заклепок ручным или машинным способом. Клепка бывает холодной и горячей.
Заклепка представляет собой стержень цилиндрической формы с головкой на конце, которая называется закладной. В процессе расклепывания стержня образуется вторая головка, называемая замыкающей.
Рис. 70. Основные типы заклепок и заклепочных швов:
головки: а — полукруглая, 6 —потайная, в — полупотайная, г —шаг заклепочного соединения; швы; д — внахлестку, е — встык с одной накладкой, ж — встык с двумя накладками
По форме закладной головки заклепки бывают с полукруглой головкой, с полупотайной головкой, с потайной головкой (рис. 70, а, б, в) и др.
Соединение деталей, выполненное заклепками, называется заклепочным швом.
В зависимости от расположения заклепок в шве в один, в два и более рядов заклепочные швы разделяются на однорядные, двухрядные, многорядные.
Расстояние t между центрами заклепок одного ряда называется шагом заклепочного соединения (рис. 70, г). Для однорядных швов шаг должен быть равным трем диаметрам заклепки, расстояние а от центра заклепки до края склепываемых деталей должно быть равно 1,5 диаметра заклепки при просверленных отверстиях и 2,5 диаметра при пробитых отверстиях. В двухрядных швах шаг берут равным четырем диаметрам заклепки, расстояние от центра заклепок до края склепываемых деталей — 1,5 диаметра, а расстояние между рядами заклепок должно равняться двум диаметрам заклепки.
Заклепочные соединения выполняют тремя основными способами: внахлестку, встык с одной накладкой и встык с двумя накладками (рис. 70, д, е, ж). По назначению заклепочные швы разделяют на прочные, плотные и прочно-плотные.
Качество заклепочного шва в большой степени зависит от того, правильно ли выбрана заклепка.
Оборудование и инструменты, применяемые при ручной и механизированной клепке. Ручную клепку осуществляют при помощи слесарного молотка с квадратным бойком, поддержки, натяжки и обжимки (рис. 71). Молотки бывают весом от 150 до 1000 Г. Вес молотка выбирается в соответствии с диаметром стержня заклепки,
Поддержка служит опорой для закладной головки заклепки при расклепывании, натяжка — для более плотного сближения склепываемых деталей, обжимка применяется для придания правильной формы замыкающей головке заклепки.
Механизированную клепку осуществляют пневматическими конструкций. Пневматический клепальный молоток (рис. 72) работает под действием сжатого воздуха и приводится в действие пусковым курком. При нажиме на пусковой курок открывается клапан 9 и сжатый воздух, поступая по каналам в левую часть камеры ствола, приводит в действие ударник, который ударяет по обжимке.
Рис. 71. Вспомогательные инструменты, применяемые при клепке:
1 — обжимка, 2 — поддержка, 3 — натяжка
После удара золотник перекрывает поступление воздуха в канал 3, соединяя его с атмосферой, а сжатый воздух направляется по каналу 4 в правую часть камеры ствола, при этом ударник отбрасывается канал 4 перекрываетсязолот-в действие и т. д. Работу пнев-выполняют два человека, один производит клепку молотком, а другой является подручным.
Рис. 72. Пневматический клепальный молоток П-72
Процесс клепки заключается в следующем. В отверстие вставляют заклепку и устанавливают закладной головкой на зажатую в тисках поддержку. После этого на стержень заклепки устанавливают натяжку. По головке натяжки ударяют молотком, в результате чего происходит сближение склепываемых деталей.
Затем начинают ударами молотка расклепывать стержень заклепки, нанося поочередно прямые и косые удары непосредственно по стержню. В результате расклепывания получается замыкающая головка заклепки. Для придания правильной формы замыкающей головке на нее надевают обжимку и ударами молотка по обжимке производят окончательную обработку головки, придавая ей правильную форму.
Под заклепки с потайной головкой отверстие предварительно обрабатывают зенковкой на конус. Расклепывают потайную головку прямыми ударами молотка, направленными точно вдоль оси заклепки.
Наиболее часто встречающимися дефектами клепки являются следующие: изгиб стержня заклепки в отверстии, получившийся потому, что диаметр отверстия был очень велик; прогиб материала вследствие того, что диаметр отверстия был мал; смещение закладной головки (косо просверлено отверстие), изгиб замыкающей головки, образовавшийся в результате того, что стержень заклепки был очень длинный или поддержка была установлена не по оси заклепки; подсечка детали (листа) из-за того, что лунка обжимки была больше головки заклепки, трещины на головках заклепок, появляющиеся при недостаточной пластичности материала заклепок.
Техника безопасности. При выполнении клепальных работ необходимо соблюдать следующие правила техники безопасности: молоток должен быть надежно насажен на рукоятку; бойки молотков, обжимки не должны иметь выбоин, трещин, так как они могут в процессе клепки расколоться и осколками ранить как производящего клепку рабочего, так и находящихся вблизи рабочих; при работе пневматическим молотком его необходимо регулировать. При регулировании нельзя пробовать молоток, придерживая обжимку руками, так как это может повести к серьезному ранению руки.
Электротехнические материалы
Электротехнические материалы представляют собой совокупность проводниковых, электроизоляционных, магнитных и полупроводниковых материалов, предназначенных для работы в электрических и магнитных полях. Сюда же можно отнести основные электротехнические изделия: изоляторы, конденсаторы, провода и некоторые полупроводниковые элементы. Электротехнические материалы в современной электротехнике занимают одно из главных мест. Всем известно, что надежность работы электрических машин, аппаратов и электрических установок в основном зависит от качества и правильного выбора соответствующих электротехнических материалов. Анализ аварий электрических машин и аппаратов показывает, что большинство из них происходит вследствие выхода из строя электроизоляции, состоящей из электроизоляционных материалов.
Не менее важное значение для электротехники имеют магнитные материалы. Потери энергии и габариты электрических машин и трансформаторов определяются свойствами магнитных материалов. Довольно значительное место занимают в электротехнике полупроводниковые материалы, или полупроводники. В результате разработки и изучения данной группы материалов были созданы различные новые приборы, позволяющие успешно решать некоторые проблемы электротехники.
При рациональном выборе электроизоляционных, магнитных и других материалов можно создать надежное в эксплуатации электрооборудование при малых габаритах и весе. Но для реализации этих качеств необходимы знания свойств всех групп электротехнических материалов.
Проводниковые материалы
К этой группе материалов относятся металлы и их сплавы. Чистые металлы имеют малое удельное сопротивление. Исключением является ртуть, у которой удельное сопротивление довольно высокое. Сплавы также обладают высоким удельным сопротивлением. Чистые металлы применяются при изготовлении обмоточных и монтажных проводов, кабелей и пр. Проводниковые сплавы в виде проволоки и лент используются в реостатах, потенциометрах, добавочных сопротивлениях и т. д.
В подгруппе сплавов с высоким удельным сопротивлением выделяют группу жароупорных проводниковых материалов, стойких к окислению при высоких температурах. Жароупорные, или жаростойкие, проводниковые сплавы применяются в электронагревательных приборах и реостатах. Кроме малого удельного сопротивления, чистые металлы обладают хорошей пластичностью, т. е. могут вытягиваться в тонкую проволоку, в ленты и прокатываться в фольгу толщиной менее 0,01 мм. Сплавы металлов имеют меньшую пластичность, но более упруги и устойчивы механически. Характерной особенностью всех металлических проводниковых материалов является их электронная электропроводность. Удельное сопротивление всех металлических проводников увеличивается с ростом температуры, а также в результате механической обработки, вызывающей остаточную деформацию в металле.
Прокатку или волочение используют в том случае, когда нужно получить проводниковые материалы с повышенной механической прочностью, например при изготовлении проводов воздушных линий, троллейных проводов и пр. Чтобы вернуть деформированным металлическим проводникам прежнюю величину удельного сопротивления, их подвергают термической обработке — отжигу без доступа кислорода.
Электроизоляционные материалы
Электроизоляционными материалами, или диэлектриками, называют такие материалы, с помощью которых осуществляют изоляцию, т. е. препятствуют утечке электрического тока между какими-либо токопроводящими частями, находящимися под разными электрическими потенциалами. Диэлектрики имеют очень большое электрическое сопротивление. По химическому составу диэлектрики делят на органические и неорганические. Основным элементов в молекулах всех органических диэлектриков является углерод. В неорганических диэлектриках углерода нет. Наибольшейнагревостойкостью обладают неорганические диэлектрики (слюда, керамика и др.).
По способу получения различают естественные (природные) и синтетические диэлектрики. Синтетические диэлектрики могут быть созданы с заданным комплексом электрических и физико-химических свойств, поэтому они широко применяются в электротехнике.
По строению молекул диэлектрики делят на неполярные (нейтральные) и полярные. Нейтральные диэлектрики состоят из электрически нейтральных атомов и молекул, которые до воздействия на них электрического поля не обладают электрическими свойствами. Нейтральными диэлектриками являются: полиэтилен, фторопласт-4 и др. Среди нейтральных выделяют ионные кристаллические диэлектрики (слюда, кварц и др.), в которых каждая пара ионов составляет электрически нейтральную частицу. Ионы располагаются в узлах кристаллической решетки. Каждый ион находится в колебательном тепловом движении около центра равновесия — узла кристаллической решетки. Полярные, или дипольные, диэлектрики состоят из полярных молекул-диполей. Последние вследствие асимметрии своего строения обладают начальным электрическим моментом еще до воздействия на них силы электрического поля. К полярным диэлектрикам относятся бакелит, поливинилхлорид и др. По сравнению с нейтральными диэлектриками полярные имеют более высокие значения диэлектрической проницаемости, а также немного повышенную проводимость.
По агрегатному состоянию диэлектрики бывают газообразными, жидкими и твердыми. Самой большой является группа твердых диэлектриков. Электрические свойства электроизоляционных материалов оценивают с помощью величин, называемых электрическими характеристиками. К ним относятся: удельное объемное сопротивление, удельное поверхностное сопротивление, диэлектрическая проницаемость, температурный коэффициент диэлектрической проницаемости, тангенс угла диэлектрических потерь и электрическая прочность материала.
Удельное объемное сопротивление — величина, дающая возможность оценить электрическое сопротивление материала при протекании через него постоянного тока. Величина, обратная удельному объемному сопротивлению, называется удельной объемной проводимостью. Удельное поверхностное сопротивление — величина, позволяющая оценить электрическое сопротивление материала при протекании постоянного тока по его поверхности между электродами. Величина, обратная удельному поверхностному сопротивлению, называется удельной поверхностной проводимостью.
Температурный коэффициент удельного электрического сопротивления — величина, определяющая изменение удельного сопротивления материала с изменением его температуры. С повышением температуры у всех диэлектриков электрическое сопротивление уменьшается, следовательно, их температурный коэффициент удельного сопротивления имеет отрицательный знак. Диэлектрическая проницаемость — величина, позволяющая оценить способность материала создавать электрическую емкость. Относительная диэлектрическая проницаемость входит в величину абсолютной диэлектрической проницаемости. Температурный коэффициент диэлектрической проницаемости — величина, дающая возможность оценить характер изменения диэлектрической проницаемости, а следовательно, и емкости изоляции с изменением температуры. Тангенс угла диэлектрических потерь — величина, определяющая потери мощности в диэлектрике, работающем при переменном напряжении.
Электрическая прочность — величина, позволяющая оценить способность диэлектрика противостоять разрушению его электрическим напряжением. Механическая прочность электроизоляционных и других материалов оценивается при помощи следующих характеристик: предел прочности материала при растяжении, относительное удлинение при растяжении, предел прочности материала при сжатии, предел прочности материала при статическом изгибе, удельная ударная вязкость, сопротивление раскалыванию.
К физико-химическим характеристикам диэлектриков относятся: кислотное число, вязкость, водопоглощаемость. Кислотное число — это количество миллиграммов едкого калия, необходимое для нейтрализации свободных кислот, содержащихся в 1 г диэлектрика. Кислотное число определяется у жидких диэлектриков, компаундов и лаков. Эта величина позволяет оценить количество свободных кислот в диэлектрике, а значит, степень их воздействия на органические материалы. Наличие свободных кислот ухудшает электроизоляционные свойства диэлектриков. Вязкость, или коэффициент внутреннего трения, дает возможность оценить текучесть электроизоляционных жидкостей (масел, лаков и др.). Вязкость бывает кинематической и условной. Водопоглощаемость — это количество воды, поглощенной диэлектриком после пребывания его в дистиллированной воде в течение суток при температуре 20° С и выше. Величина водопоглощаемости указывает на пористость материала и наличие в нем водорастворимых веществ. С увеличением этого показателя электроизоляционные свойства диэлектриков ухудшаются.
К тепловым характеристикам диэлектриков относятся: температура плавления, температура размягчения, температура каплепадения, температура вспышки паров, теплостойкость пластмасс, термоэластичность (теплостойкость) лаков, нагревостойкость, морозостойкость, тропикостойкость.
Большое применение в электротехнике получили пленочные электроизоляционные материалы, изготавливаемые из полимеров. К ним относятся пленки и ленты. Пленки выпускают толщиной 5—250 мкм, а ленты — 0,2—3,0 мм. Высокополимерные пленки и ленты отличаются большой гибкостью, механической прочностью и хорошими электроизоляционными свойствами. Полистирольные пленки выпускают толщиной 20—100 мкм и шириной 8—250 мм. Толщина полиэтиленовых пленок обычно составляет 30—200 мкм, а ширина 230—1500 мм. Пленки из фторопласта-4 изготавливают толщиной 5—40 мкм и шириной 10—200 мм. Также из этого материала выпускают неориентированные и ориентированные пленки. Наиболее высокими механическими и электрическими характеристиками обладают ориентированные фторопластовые пленки.
Полиэтилентерефталатные (лавсановые) пленки выпускают толщиной 25—100 мкм и шириной 50—650 мм. Полихлорвиниловые пленки изготавливают из винипласта и из пластифицированного полихлорвинила. Большей механической прочностью, но меньшей гибкостью обладают пленки из винипласта. Пленки из винипласта имеют толщину 100 мкм и более, а пленки из пластифицированного полихлорвинила — 20—200 мкм. Триацетатцеллюлозные (триацетатные) пленки изготавливают непластифицированными (жесткими), окрашенными в голубой цвет, слабопластифицированными (бесцветными) и пластифицированными (окрашенными в синий цвет). Последние обладают значительной гибкостью. Триацетатные пленки выпускают толщиной 25, 40 и 70 мкм и шириной 500 мм. Пленкоэлектрокартон — гибкий электроизоляционный материал, состоящий из изоляционного картона, оклеенного с одной стороны лавсановой пленкой. Пленкоэлектрокартон на лавсановой пленке имеет толщину 0,27 и 0,32 мм. Его выпускают в рулонах шириной 500 мм. Пленкоасбестокартон — гибкий электроизоляционный материал, состоящий из лавсановой пленки толщиной 50 мкм, оклеенной с двух сторон асбестовой бумагой толщиной 0,12 мм. Пленкоасбестокартон выпускают в листах 400 х 400 мм (не менее) толщиной 0,3 мм.
Электроизоляционные лаки и эмали
Лаки — это растворы пленкообразующих веществ: смол, битумов, высыхающих масел, эфиров целлюлозы или композиций этих материалов в органических растворителях. В процессе сушки лака из него испаряются растворители, а в лаковой основе происходят физико-химические процессы, приводящие к образованию лаковой пленки. По своему назначению электроизоляционные лаки делят на пропиточные, покровные и клеящие.
Пропиточные лаки применяются для пропитки обмоток электрических машин и аппаратов с целью закрепления их витков, увеличения коэффициента теплопроводности обмоток и повышения их влагостойкости. Покровные лаки позволяют создать защитные влагостойкие, маслостойкие и другие покрытия на поверхности обмоток или пластмассовых и других изоляционных деталей. Клеящие лаки предназначаются для склеивания листочков слюды друг с другом или с бумагой и тканями с целью получения слюдяных электроизоляционных материалов (миканиты, микалента и др.).
Эмали представляют собой лаки с введенными в них пигментами — неорганическими наполнителями (окись цинка, двуокись титана, железный сурик и др.). Пигменты вводятся с целью повышения твердости, механической прочности, влагостойкости, дутостойкости и других свойств эмалевых пленок. Эмали относятся к покровным материалам.
По способу сушки различают лаки и эмали горячей (печной) и холодной (воздушной) сушки. Первые требуют для своего отверждения высокой температуры — от 80 до 200° С, а вторые высыхают при комнатной температуре. Лаки и эмали горячей сушки, как правило, обладают более высокими диэлектрическими, механическими и другими свойствами. С целью улучшения характеристик лаков и эмалей воздушной сушки, а также для ускорения отверждения их сушку иногда производят при повышенных температурах — от 40 до 80° С.
Основные группы лаков имеют следующие особенности. Масляные лаки образуют после высыхания гибкие эластичные пленки желтого цвета, стойкие к влаге и к нагретому минеральному маслу. По нагревостойкости пленки этих лаков относятся к классу А. В масляных лаках используют дефицитные льняное и тунговое масла, поэтому они заменяются лаками на синтетических смолах, более стойкими к тепловому старению.
Масляно-битумные лаки образуют гибкие пленки черного цвета, стойкие к влаге, но легко растворяющиеся в минеральных маслах (трансформаторное и смазочное). По нагревостойкости эти лаки относятся к классу А (105° С). Глифталевые и масляно-глифталевые лаки и эмали отличаются хорошей клеящей способностью по отношению к слюде, бумагам, тканям и пластмассам. Пленки этих лаков обладают повышенной нагревостойкостью (класс В). Они устойчивы к нагретому минеральному маслу, но требуют горячей сушки при температурах 120—130° С. Чисто глифталевые лаки на основе немодифицированных глифталевых смол образуют твердые негибкие пленки, применяемые в производстве твердой слюдяной изоляции (твердые миканиты). Масляно-глифталевые лаки после высыхания дают гибкие эластичные пленки желтого цвета.
Кремнийорганические лаки и эмали отличаются высокой нагревостойкостью и могут длительно работать при 180—200° С, поэтому они применяются в сочетании со стекловолокнистой и слюдяной изоляцией. Кроме этого, пленки обладают высокой влагостойкостью и стойкостью к электрическим искрам.
Лаки и эмали на основе полихлорвиниловых и перхлорвиниловых смол отличаются стойкостью к воде, нагретым маслам, кислым и щелочным химическим реагентам, поэтому они применяются в качестве покровных лаков и эмалей для защиты обмоток, а также металлических деталей от коррозии. Следует обратить внимание на слабое прилипание полихлорвиниловых и перхлорвиниловых лаков и эмалей к металлам. Последние вначале покрывают слоем грунта, а затем лаком или эмалью на основе полихлорвиниловых смол. Сушка этих лаков и эмалей производится при 20, а также при 50—60° С. К недостаткам такого рода покрытий относится их невысокая рабочая температура, составляющая 60—70° С.
Лаки и эмали на основе эпоксидных смол отличаются высокой клеящей способностью и несколько повышенной нагревостойкостью (до 130° С). Лаки на основе алкидных и фенольных смол (фенолоалкидные лаки) имеют хорошую высыхаемость в толстых слоях и образуют эластичные пленки, могущие длительно работать при температурах 120—130° С. Пленки этих лаков обладают влаго- и маслостойкостью.
Водно-эмульсионные лаки — это устойчивые эмульсии лаковых основ в водопроводной воде. Лаковые основы производят из синтетических смол, а также из высыхающих масел и их смесей. Водно-эмульсионные лаки пожаро- и взрывобезопасны, потому что в их составе нет легковоспламеняющихся органических растворителей. Из-за малой вязкости такие лаки имеют хорошую пропитывающую способность. Их применяют для пропитки неподвижных и подвижных обмоток электрических машин и аппаратов, длительно работающих при температурах до 105° С.
Электроизоляционные компаунды
Компаунды представляют собой изоляционные составы, которые в момент использования бывают жидкими, а затем отвердевают. Компаунды не имеют в своем составе растворителей. По своему назначению данные составы делятся на пропиточные и заливочные. Первые из них применяют для пропитки обмоток электрических машин и аппаратов, вторые — для заливки полостей в кабельных муфтах, а также в электромашинах и приборах с целью герметизации.
Компаунды бывают термореактивными (не размягчающимися после отвердевания) и термопластичными (размягчающимися при последующих нагревах). К термореактивным можно отнести компаунды на основе эпоксидных, полиэфирных и некоторых других смол. К термопластичным относятся компаунды на основе битумов, воскообразных диэлектриков и термопластичных полимеров (полистирол, полиизобутилен и др.). Пропиточные и заливочные компаунды на основе битумов по нагревостойкости относятся к классу А (105° С), а некоторые к классу Y (до 90° С). Наибольшейнагревостойкостыо обладают компаунды эпоксидные и кремнийорганические.
Компаунды МБК изготовляют на основе метакриловых эфиров и применяют как пропиточные и заливочные. Они после отвердевания при 70—100° С (а со специальными отвердителями при 20° С) являются термореактивными веществами, которые могут использоваться в интервале температур от —55 до +105° С.
Непропитанные волокнистые электроизоляционные материалы
К этой группе относятся листовые и рулонные материалы, состоящие из волокон органического и неорганического происхождения. Волокнистые материалы органического происхождения (бумага, картон, фибра и ткань) получают из растительных волокон древесины, хлопка и натурального шелка. Нормальная влажность электроизоляционных картонов, бумаги и фибры колеблется от 6 до 10%. Волокнистые органические материалы на основе синтетических волокон (капрон) обладают влажностью от 3 до 5%. Такая же примерно влажность наблюдается у материалов, получаемых на основе неорганических волокон (асбест, стекловолокно). Характерными особенностями неорганических волокнистых материалов являются их негорючесть и высокая нагревостойкость (класс С). Эти ценные свойства в большинстве случаев снижаются при пропитке этих материалов лаками.
Электроизоляционную бумагу изготавливают обычно из древесной целлюлозы. Наибольшую пористость имеет микалентная бумага, применяемая в производстве слюдяных лент. Электрокартон изготавливают из древесной целлюлозы или из смеси хлопчатобумажных волокон и волокон древесной (сульфатной) целлюлозы, взятых в различных соотношениях. Увеличение содержания хлопчатобумажных волокон снижает гигроскопичность и усадку картона. Электрокартон, предназначенный для работы в воздушной среде, имеет более плотную структуру по сравнению с картоном, предназначенным для работы в масле. Картон толщиной 0,1—0,8 мм выпускают в рулонах, а картон толщиной от 1 мм и выше — в листах различных размеров.
Фибра представляет собой монолитный материал, получаемый в результате прессования листов бумаги, предварительно обработанных нагретым раствором хлористого цинка и отмытых в воде. Фибра поддается всем видам механической обработки и формованию после размачивания ее заготовок в горячей воде.
Летероид — тонкая листовая и рулонная фибра, используемая для изготовления различного вида электроизоляционных прокладок, шайб и фасонных изделий.
Асбестовые бумаги, картоны и ленты изготавливаются из волокон хризотилового асбеста, обладающего наибольшей эластичностью и способностью скручиваться в нити. Все асбестовые материалы стойки к щелочам, но легко разрушаются кислотами.
Электроизоляционные стеклянные ленты и ткани производят из стеклянных нитей, получаемых из бесщелочных или малощелочных стекол. Преимущество стеклянных волокон перед растительными и асбестовыми состоит в их гладкой поверхности, понижающей поглощение влаги из воздуха. Нагревостойкость стеклянных тканей и лент выше асбестовых.
Электроизоляционные лакированные ткани (лакоткани)
Лакированные ткани представляют собой гибкие материалы, состоящие из ткани, пропитанной лаком или каким-либо электроизоляционным составом. Пропиточный лак или состав после отвердевания образует гибкую пленку, которая обеспечивает хорошие электроизоляционные свойства лакоткани. В зависимости от тканевой основы лакоткани делятся на хлопчатобумажные, шелковые, капроновые и стеклянные (стеклоткани).
В качестве пропиточных составов для лакотканей применяют масляные, масляно-битумные, эскапоновые и кремнийорганические лаки, а также кремнийорганические эмали, растворы кремнийорганических каучуков и др. Наибольшей растяжимостью и гибкостью обладают шелковые и капроновые лакоткани. Они могут работать при нагреве не выше 105° С (класс А). К этому же классу нагревостойкости относятся все хлопчатобумажные лакоткани.
Основными областями применения лакотканей являются: электрические машины, аппараты и приборы низкого напряжения. Лакоткани используют для гибкой витковой и пазовой изоляции, а также в качестве различных электроизоляционных прокладок.
Пластические массы
Пластическими массами (пластмассами) называются твердые материалы, которые на определенной стадии изготовления приобретают пластические свойства и в этом состоянии из них могут быть получены изделия заданной формы. Данные материалы представляют собой композиционные вещества, состоящие из связующего вещества, наполнителей, красителей, пластифицирующих и других компонентов. Исходными материалами для получения пластмассовых изделий являются прессовочные порошки и прессовочные материалы. По нагревостойкости пластмассы бывают термореактивные и термопластичные.
Слоистые электроизоляционные пластмассы
Слоистые пластмассы — материалы, состоящие из чередующихся слоев листового наполнителя (бумага или ткань) и связующего. Важнейшими из слоистых электроизоляционных пластмасс являются гетинакс, текстолит и стеклотекстолит. Они состоят из листовых наполнителей, располагающихся слоями, а в качестве связующего вещества использованы бакелитовые, эпоксидные, кремнийорганические смолы и их композиции.
В качестве наполнителей применяют специальные сорта пропиточной бумаги (в гетинаксе), хлопчатобумажные ткани (в текстолите) и бесщелочные стеклянные ткани (в стеклотекстолите). Перечисленные наполнители сначала пропитывают бакелитовыми или кремнийорганическими лаками, сушат и режут на листы определенного размера. Подготовленные листовые наполнители собирают в пакеты заданной толщины и подвергают горячему прессованию, в процессе которого отдельные листы при помощи смол прочно соединяются друг с другом.
Гетинакс и текстолит устойчивы к минеральным маслам, поэтому широко используются в маслонаполненных электроаппаратах и трансформаторах. Наиболее дешевым слоистым материалом является древесно-слоистая пластмасса (дельта-древесина). Она получается горячим прессованием тонких листов березового шпона, предварительно пропитанных бакелитовыми смолами. Дельта-древесина применяется для изготовления силовых конструкционных и электроизоляционных деталей, работающих в масле. Для работы на открытом воздухе этот материал нуждается в тщательной защите от влаги.
Асбестотекстолит представляет собой слоистую электроизоляционную пластмассу, получаемую горячим прессованием листов асбестовой ткани, предварительно пропитанных бакелитовой смолой. Его выпускают в виде фасонных изделий, а также в виде листов и плит толщиной от 6 до 60 мм. Асбогетинакс — слоистая пластмасса, получаемая горячим прессованием листов асбестовой бумаги, содержащей 20% сульфатной целлюлозы или асбестовой бумаги без целлюлозы, пропитанных эпоксидно-фенолоформальдегидным связующим.
Из рассмотренных слоистых электроизоляционных материалов наибольшей нагревостойкостью, лучшими электрическими и механическими характеристиками, повышенной влагостойкостью и стойкостью к грибковой плесени обладают стеклотекстолиты на кремнийорганических и эпоксидных связующих.
Намотанные электроизоляционные изделия
Намотанные электроизоляционные изделия представляют собой твердые трубки и цилиндры, изготовленные методом намотки на металлические круглые стержни каких-либо волокнистых материалов, предварительно пропитанных связующим веществом. В качестве волокнистых материалов применяют специальные сорта намоточных или пропиточных бумаг, а также хлопчатобумажные ткани и стеклоткани. Связующими веществами являются бакелитовые, эпоксидные, кремнийорганические и другие смолы.
Намотанные электроизоляционные изделия вместе с металлическими стержнями, на которые они намотаны, сушат при высокой температуре. С целью гигроскопичности намотанных изделий их лакируют. Каждый слой лака сушат в печи. К намотанным изделиям можно отнести и сплошные текстолитовые стержни, потому что их тоже получают путем намотки заготовок из текстильного наполнителя, пропитанного бакелитовым лаком. После этого заготовки подвергают горячему прессованию в стальных пресс-формах. Намотанные электроизоляционные изделия применяют в трансформаторах с воздушной и масляной изоляцией, в воздушных и масляных выключателях, различных электроаппаратах и узлах электрооборудования.
Минеральные электроизоляционные материалы
К минеральным электроизоляционным материалам относятся горные породы: слюда, мрамор, шифер, талькохлорит и базальт. Также к этой группе относятся материалы, получаемые из портландцемента и асбеста (асбестоцемент и асбопласт). Вся эта группа неорганических диэлектриков отличается высокой стойкостью к электрической дуге и обладает достаточно высокими механическими характеристиками. Минеральные диэлектрики (кроме слюды и базальта) поддаются механической обработке, за исключением нарезания резьбы.
Электроизоляционные изделия из мрамора, шифера и талькохлорита получают в виде досок для панелей и электроизоляционных оснований для рубильников и переключателей низкого напряжения. Точно такие же изделия из плавленого базальта можно получить только методом литья в формы. Чтобы базальтовые изделия обладали необходимыми механическими и электрическими характеристиками, их подвергают термической обработке с целью образования в материале кристаллической фазы.
Электроизоляционные изделия из асбестоцемента и асбопласта представляют собой доски, основания, перегородки и дугогасительные камеры. Для изготовления такого рода изделий используют смесь, состоящую из портландцемента и асбестового волокна. Изделия из асбопласта получают холодным прессованием из массы, в которую добавлено 15% пластичного вещества (каолина или формовочной глины). Этим достигается большая текучесть исходной прессовочной массы, что позволяет получать из асбопласта электроизоляционные изделия сложного профиля.
Основным недостатком многих минеральных диэлектриков (за исключением слюды) является невысокий уровень их электрических характеристик, вызванный большим количеством имеющихся пор и наличием оксидов железа. Такое явление позволяет использовать минеральные диэлектрики только в устройствах низкого напряжения.
В большинстве случаев все минеральные диэлектрики, кроме слюды и базальта, перед применением пропитывают парафином, битумом, стиролом, бакелитовыми смолами и др. Наибольший эффект достигается при пропитке уже механически обработанных минеральных диэлектриков (панели, перегородки, камеры и др.).
Мрамор и изделия из него не переносят резких изменений температуры и растрескиваются. Шифер, базальт, талькохлорит, слюда и асбестоцемент более устойчивы к резким сменам температур.
Слюдяные электроизоляционные материалы
Данные материалы состоят из листочков слюды, склеенных при помощи какой-либо смолы или клеящего лака. К клееным слюдяным материалам относятся миканиты, микафолий и микаленты. Клееные слюдяные материалы используют в основном для изоляции обмоток электрических машин высокого напряжения (генераторы, электродвигатели), а также изоляции машин низкого напряжения и машин, работающих в тяжелых условиях.
Миканиты представляют собой твердые или гибкие листовые материалы, получаемые склеиванием листочков щипаной слюды с помощью шеллачной, глифталевых, кремнийорганических и других смол или лаков на основе этих смол.
Основные виды миканитов — коллекторный, прокладочный, формовочный и гибкий. Коллекторный и прокладочный миканиты относятся к группе твердых миканитов, которые после клейки слюды подвергаются прессованию при повышенных удельных давлениях и нагреве. Эти миканиты обладают меньшей усадкой по толщине и большей плотностью. Формовочный и гибкий миканиты имеют более рыхлую структуру и меньшую плотность.
Коллекторный миканит — это твердый листовой материал, изготовляемый из листочков слюды, склеенных при помощи шеллачной или глифталевой смол или лаков на основе этих смол. Для обеспечения механической прочности при работе в коллекторах электрических машин в данные миканиты вводят не более 4% клеящего вещества.
Прокладочный миканит представляет собой твердый листовой материал, изготовляемый из листочков щипаной слюды, склеенных с помощью шеллачной или глифталевой смол или лаков на их основе. После склеивания листы прокладочного миканита подвергают прессованию. В данном материале 75—95% слюды и 25—5% клеящего вещества.
Формовочный миканит — твердый листовой материал, изготовляемый из листочков щипаной слюды, склеенных с помощью шеллачной, глифталевой или кремнийорганических смол или лаков на их основе. После склеивания листы формовочного миканита прессуют при температуре 140—150° С.
Гибкий миканит представляет собой листовой материал, обладающий гибкостью при комнатной температуре. Он изготовляется из листочков щипаной слюды, склеенных масляно-битумным, масляно-глифталевым или кремнийорганическим лаком (без сиккатива), образующим гибкие пленки.
Отдельные виды гибкого миканита оклеивают с двух сторон микалентной бумагой для увеличения механической прочности. Гибкий стекломиканит — листовой материал, гибкий при комнатной температуре. Это разновидность гибкого миканита, отличается повышенной механической прочностью и повышенной устойчивостью к нагреву. Данный материал изготовляется из листочков щипаной слюды, склеенных друг с другом кремнийорганическими или масляно-глифталевыми лаками, образующими гибкие нагревостойкие пленки. Листы гибкогостекломиканита оклеиваются с двух или с одной стороны бесщелочной стеклотканью.
Микафолий — это рулонный или листовой электроизоляционный материал, формуемый в нагретом состоянии. Он состоит из одного или нескольких, чаще двух-трех, слоев листочков слюды, склеенных между собой и с полотном бумаги толщиной 0,05 мм, или со стеклотканью, или со стеклосеткой. В качестве клеящих лаков применяют шеллачный, глифталевый, полиэфирный или кремнийорганический.
Микалента представляет собой рулонный электроизоляционный материал, гибкий при комнатной температуре. Состоит из одного слоя листочков щипаной слюды, склеенных между собой и оклеенных с одной или двух сторон тонкой микалентной бумагой, стеклотканью или стеклосеткой. В качестве клеящих лаков используют масляно-битумные, масляно-глифталевые, кремнийорганические и растворы каучуков.
Микашелк — рулонный электроизоляционный материал, гибкий при комнатной температуре. Микашелк представляет собой одну из разновидностей микаленты, но с повышенной механической прочностью на разрыв. Он состоит из одного слоя листочков щипаной слюды, склеенных между собой и оклеенных с одной стороны полотном из натурального шелка, а с другой — микалентной бумагой. В качестве клеящих лаков использованы масляно-глифталевые или масляно-битумные лаки, образующие гибкие пленки.
Микаполотно — рулонный или листовой электроизоляционный материал, гибкий при комнатной температуре. Микаполотно состоит из нескольких слоев щипаной слюды, склеенных между собой и оклеенных с двух сторон хлопчатобумажной тканью (перкаль) или микалентной бумагой с одной стороны и тканью — с другой.
Микалекс представляет собой слюдяную пластмассу, изготовляемую прессованием из смеси порошкообразной слюды и стекла. После прессования изделия подвергают термической обработке (сушке). Микалекс выпускают в виде пластин и стержней, а также в виде электроизоляционных изделий (панели, основания для переключателей, воздушных конденсаторов и пр.). При прессовании микалексовых изделий в них могут быть добавлены металлические части. Данные изделия поддаются всем видам механической обработки.
Слюдинитовые электроизоляционные материалы
При разработке природной слюды и при изготовлении электроизоляционных материалов на основе щипаной слюды остается большое количество отходов. Их утилизация дает возможность получить новые электроизоляционные материалы — слюдиниты. Такого рода материалы изготовляют из слюдинитовой бумаги, предварительно обработанной каким-либо клеящим составом (смолы, лаки). Из слюдяной бумаги путем склеивания с помощью клеящих лаков или смол и последующего горячего прессования получают твердые или гибкие слюдинитовые электроизоляционные материалы. Клеящие смолы могут быть введены непосредственно в жидкую слюдяную массу — слюдяную суспензию. Среди наиболее важных слюдинитовых материалов нужно сказать о следующих.
Слюдинит коллекторный — твердый листовой материал, калиброванный по толщине. Получается горячим прессованием листов слюдинитовой бумаги, обработанной шеллачным лаком. Коллекторный слюдинит выпускается в листах размером от 215 х 400 мм до 400 х 600 мм.
Слюдинит прокладочный — твердый листовой материал, получаемый горячим прессованием листов слюдинитовой бумаги, пропитанных клеящими лаками. Прокладочный слюдинит выпускается в листах размером 200 х 400 мм. Из него изготовляют твердые прокладки и шайбы для электрических машин и аппаратов с нормальным и повышенным перегревом.
Стеклослюдинит формовочный — твердый листовой материал в холодном состоянии и гибкий — в нагретом. Получается при склеивании слюдинитовой бумаги с подложками из стеклоткани. Формовочный нагревостойкийстеклослюдинит — твердый листовой материал, формуемый в нагретом состоянии. Его изготовляют путем склеивания листов слюдинитовой бумаги со стеклотканью при помощи нагревостойкого кремнийорганического лака. Он выпускается в листах размером 250 х 350 мм и более. Данный материал имеет повышенную механическую прочность при растяжении.
Слюдинит гибкий — листовой материал, гибкий при комнатной температуре. Его получают путем склеивания листов слюдинитовой бумаги с последующим горячим прессованием. В качестве связующего применяется полиэфирный или кремнийорганический лак. Большинство видов гибкого слюдинита оклеивается стеклотканью с одной или двух сторон. Стеклослюдинит гибкий (нагревостойкий) — листовой материал, гибкий при комнатной температуре. Производится в результате склеивания одного или нескольких листов слюдинитовой бумаги со стеклотканью или стеклосеткой при помощи кремнийорганических лаков. После склеивания материал подвергается горячему прессованию. Он оклеен стеклотканью с одной или двух сторон с целью повышения механической прочности.
Слюдинитофолий — рулонный или листовой материал, гибкий в нагретом состоянии, получаемый склеиванием одного или нескольких листов слюдинитовой бумаги с телефонной бумагой толщиной 0,05 мм, применяемой в качестве гибкой подложки. Область применения этого материала та же, что и микафолия на основе щипаной слюды. Слюдинитофолий выпускается в рулонах шириной 320—400 мм.
Слюдинитовая лента — рулонный нагревостойкий материал, гибкий при комнатной температуре, состоящий из слюдинитовой бумаги, оклеенной с одной или обеих сторон стеклосеткой или стеклотканью. Слюдинитовые ленты выпускают преимущественно в роликах шириной 15, 20, 23, 25, 30 и 35 мм, реже — в рулонах.
Стеклобумослюдинитовая лента — рулонный, гибкий в холодном состоянии материал, состоящий из слюдинитовой бумаги, стеклосетки и микалентной бумаги, склеенных и пропитанных эпоксидно-полиэфирным лаком. С поверхности ленту покрывают липким слоем компаунда. Выпускают ее в роликах шириной 15, 20, 23, 30, 35 мм.
Стеклослюдинитоэлектрокартон — листовой материал, гибкий при комнатной температуре. Он получается в результате склеивания слюдинитовой бумаги, электрокартона и стеклоткани при помощи лака. Выпускается в листах размером 500 х 650 мм.
Слюдопластовые электроизоляционные материалы
Все слюдопластовые материалы изготовляются путем склеивания и прессования листов слюдопластовой бумаги. Последнюю получают из непромышленных отходов слюды в результате механического дробления частиц упругой волной. По сравнению со слюдинитами слюдопластовые материалы обладают большей механической прочностью, но менее однородны, т. к. состоят из частиц большей величины, чем слюдиниты. Важнейшими слюдопластовыми электроизоляционными материалами являются следующие.
Слюдопласт коллекторный — твердый листовой материал, калиброванный по толщине. Получается горячим прессованием листов слюдопластовой бумаги, предварительно покрытых слоем клеящего состава. Выпускается в листах размером 215 х 465 мм.
Слюдопласт прокладочный — твердый листовой материал, изготавливаемый горячим прессованием листов слюдопластовой бумаги, покрытых слоем связующего вещества. Выпускается в листах размером 520 х 850 мм.
Слюдопласт формовочный — прессованный листовой материал, твердый в холодном состоянии и способный формоваться в нагретом. Выпускается в листах размером от 200 х 400 мм до 520 х 820 мм.
Слюдопласт гибкий — прессованный листовой материал, гибкий при комнатной температуре. Выпускается в листах размером от 200 х 400 мм до 520 х 820 мм. Стеклослюдопласт гибкий — прессованный листовой материал, гибкий при комнатной температуре, состоящий из нескольких слоев слюдопластовой бумаги, оклеенных с одной стороны стеклотканью, а с другой — стеклосеткой или с обеих сторон стеклосеткой. Выпускается в листах размером от 250 х 500 мм до 500 х 850 мм.
Слюдопластофолий — рулонный или листовой материал, гибкий и формуемый в нагретом состоянии, получаемый склеиванием нескольких листов слюдопластовой бумаги и оклеенный с одной стороны телефонной бумагой или без нее.
Слюдопластолента — гибкий при комнатной температуре рулонный материал, состоящий из слюдопластовой бумаги, оклеенной микалентной бумагой с обеих сторон. Этот материал выпускается в роликах шириной 12, 15, 17, 24, 30 и 34 мм.
Стеклослюдопластолентанагревостойкая — гибкий при комнатной температуре материал, состоящий из одного слоя слюдопластовой бумаги, оклеенной с одной или с двух сторон стеклотканью или стеклосеткой с помощью кремнийорганического лака. Материал выпускается в роликах шириной 15, 20, 25, 30 и 35 мм.
Электрокерамические материалы и стекла
Электрокерамические материалы представляют собой искусственные твердые тела, получаемые в результате термической обработки (обжига) исходных керамических масс, состоящих из различных минералов (глины, талька и др.) и других веществ, взятых в определенном соотношении. Из керамических масс получают различные электрокерамические изделия: изоляторы, конденсаторы и др.
В процессе высокотемпературного обжига данных изделий между частицами исходных веществ происходят сложные физико-химические процессы с образованием новых веществ кристаллического и стеклообразного строения.
Электрокерамические материалы делят на 3 группы: материалы, из которых изготовляют изоляторы (изоляторная керамика), материалы, из которых изготовляют конденсаторы (конденсаторная керамика), и сегнетокерамические материалы, обладающие аномально большими значениями диэлектрической проницаемости и пьезоэффектом. Последние получили применение в радиотехнике. Все электрокерамические материалы отличаются высокой нагревостойкостыо, атмосферостойкостью, стойкостью к электрическим искрам и дугам и обладают хорошими электроизоляционными свойствами и достаточно высокой механической прочностью.
Наряду с электрокерамическими материалами, многие типы изоляторов изготовляют из стекла. Для производства изоляторов применяют малощелочное и щелочное стекла. Большинство типов изоляторов высокого напряжения изготовляют из закаленного стекла. Закаленные стеклянные изоляторы по своей механической прочности превосходят фарфоровые изоляторы.
Магнитные материалы
Величины, с помощью которых оцениваются магнитные свойства материалов, называются магнитными характеристиками. К ним относятся: абсолютная магнитная проницаемость, относительная магнитная проницаемость, температурный коэффициент магнитной проницаемости, максимальная энергия магнитного поля и пр. Все магнитные материалы делятся на две основные группы: магнитно-мягкие и магнитно-твердые.
Магнитно-мягкие материалы отличаются малыми потерями на гистерезис (магнитный гистерезис — отставание намагниченности тела от внешнего намагничивающего поля). Они имеют относительно большие значения магнитной проницаемости, малую коэрцитивную силу и относительно большую индукцию насыщения. Данные материалы применяются для изготовления магнитопроводов трансформаторов, электрических машин и аппаратов, магнитных экранов и прочих устройств, где требуется намагничивание с малыми потерями энергии.
Магнитно-твердые материалы отличаются большими потерями на гистерезис, т. е. обладают большой коэрцитивной силой и большой остаточной индукцией. Эти материалы, будучи намагниченными, могут длительное время сохранять полученную магнитную энергию, т. е. становятся источниками постоянного магнитного поля. Магнитно-твердые материалы применяются для изготовления постоянных магнитов.
Согласно своей основе, магнитные материалы подразделяются на металлические, неметаллические и магнитодиэлектрики. К металлическим магнитно-мягким материалам относятся: чистое (электролитическое) железо, листовая электротехническая сталь, железо-армко, пермаллой (железо-никелевые сплавы) и др. К металлическим магнитно-твердым материалам относятся: легированные стали, специальные сплавы на основе железа, алюминия и никеля и легирующих компонентов (кобальт, кремний и пр.). К неметаллическим магнитным материалам относятся ферриты. Это материалы, получаемые из порошкообразной смеси окислов некоторых металлов и окиси железа. Отпрессованные ферритовые изделия (сердечники, кольца и др.) подвергают обжигу при температуре 1300—1500° С. Ферриты бывают магнитно-мягкие и магнитно-твердые.
Магнитодиэлектрики — это композиционные материалы, состоящие из 70—80% порошкообразного магнитного материала и 30—20% органического высокополимерного диэлектрика. Ферриты и магнитодиэлектрики отличаются от металлических магнитных материалов большими значениями удельного объемного сопротивления, что резко снижает потери на вихревые токи. Это позволяет использовать эти материалы в технике высоких частот. Кроме этого, ферриты обладают стабильностью своих магнитных характеристик в широком диапазоне частот.
Электротехническая листовая сталь
Электротехническая сталь является магнитно-мягким материалом. Для улучшения магнитных характеристик в нее добавляют кремний, который повышает величину удельного сопротивления стали, что приводит к уменьшению потерь на вихревые токи. Такая сталь выпускается в виде листов толщиной 0,1; 0,2; 0,35; 0,5; 1,0 мм, шириной от 240 до 1000 мм и длиной от 720 до 2000 мм.
Пермаллои
Данные материалы представляют собой железо-никелевые сплавы с содержанием никеля от 36 до 80%. Для улучшения тех или иных характеристик пермаллоев в их состав добавляют хром, молибден, медь и др. Характерными особенностями всех пермаллоев являются их легкая намагничиваемость в слабых магнитных полях и повышенные значения удельного электрического сопротивления.
Пермаллои — пластичные сплавы, легко прокатываемые в листы и ленты толщиной до 0,02 мм и менее. Благодаря повышенным значениям удельного сопротивления и стабильности магнитных характеристик пермаллои могут применяться до частот 200—500 кГц. Пермаллои очень чувствительны к деформациям, которые вызывают ухудшение их первоначальных магнитных характеристик. Восстановление первоначального уровня магнитных характеристик деформированных пермаллойных деталей достигается термической обработкой их по строго разработанному режиму.
Магнитно-твердые материалы
Магнитно-твердые материалы обладают большими значениями коэрцитивной силы и большой остаточной индукцией, а следовательно, большими значениями магнитной энергии. К магнитно-твердым материалам относятся:
- сплавы, закаливаемые на мартенсит (стали, легированные хромом, вольфрамом или кобальтом);
- железо-никель-алюминиевые нековкие сплавы дисперсионного твердения (альни, альнико и др.);
- ковкие сплавы на основе железа, кобальта и ванадия (виккалой) или на основе железа, кобальта, молибдена (комоль);
- сплавы с очень большой коэрцитивной силой на основе благородных металлов (платина — железо; серебро — марганец — алюминий и др.);
- металлокерамические нековкие материалы, получаемые прессованием порошкообразных компонентов с последующим обжигом отпрессованных изделий (магнитов);
- магнитно-твердые ферриты;
- металлопластические нековкие материалы, получаемые из прессовочных порошков, состоящих из частиц магнитно-твердого материала и связующего вещества (синтетическая смола);
- магнитоэластические материалы (магнитоэласты), состоящие из порошка магнито-твердого материала и эластичного связующего (каучук, резина).
Остаточная индукция у металлопластических и магнитоэластических магнитов на 20—30% меньше по сравнению с литыми магнитами из тех же магнито-твердых материалов (альни, альнико и др.).
Ферриты
Ферриты представляют собой неметаллические магнитные материалы, изготовленные из смеси специально подобранных окислов металлов с окисью железа. Название феррита определяется названием двухвалентного металла, окисел которого входит в состав феррита. Так, если в состав феррита входит окись цинка, то феррит называется цинковым; если в состав материала добавлена окись марганца — марганцевым.
В технике находят применение сложные (смешанные) ферриты, имеющие более высокие значения магнитных характеристик и большее удельное сопротивление по сравнению с простыми ферритами. Примерами сложных ферритов являются никель-цинковый, марганцево-цинковый и др.
Все ферриты — вещества поликристаллического строения, получаемые из окислов металлов в результате спекания порошков различных окислов при температурах 1100-1300° С. Ферриты могут обрабатываться только абразивным инструментом. Они являются магнитными полупроводниками. Это позволяет применять их в магнитных полях высокой частоты, т. к. потери у них на вихревые токи незначительны.
Полупроводниковые материалы и изделия
К полупроводникам относится большое количество материалов, отличающихся друг от друга внутренней структурой, химическим составом и электрическими свойствами. Согласно химическому составу, кристаллические полупроводниковые материалы делят на 4 группы:
1. материалы, состоящие из атомов одного элемента: германий, кремний, селен, фосфор, бор, индий, галлий и др.;
2. материалы, состоящие из окислов металлов: закись меди, окись цинка, окись кадмия, двуокись титана и пр.;
3. материалы на основе соединений атомов третьей и пятой групп системы элементов Менделеева, обозначаемые общей формулой и называемые антимонидами. К этой группе относятся соединения сурьмы с индием, с галлием и др., соединения атомов второй и шестой групп, а также соединения атомов четвертой группы;
4. полупроводниковые материалы органического происхождения, например полициклические ароматические соединения: антрацен, нафталин и др.
Согласно кристаллической структуре, полупроводниковые материалы делят на 2 группы: монокристаллические и поликристаллические полупроводники. К первой группе относятся материалы, получаемые в виде больших одиночных кристаллов (монокристаллы). Среди них можно назвать германий, кремний, из которых вырезают пластинки для выпрямителей и других полупроводниковых приборов.
Вторая группа материалов — это полупроводники, состоящие из множества небольших кристаллов, спаянных друг с другом. Поликристаллическими полупроводниками являются: селен, карбид кремния и пр.
По величине удельного объемного сопротивления полупроводники занимают промежуточное положение между проводниками и диэлектриками. Некоторые из них резко уменьшают электрическое сопротивление при воздействии на них высокого напряжения. Это явление нашло применение в вентильных разрядниках для защиты линий электропередачи. Другие полупроводники резко уменьшают свое сопротивление под действием света. Это используется в фотоэлементах и фоторезисторах. Общим свойством для полупроводников является то, что они обладают электронной и дырочной проводимостью.
Электроугольные изделия (щетки для электрических машин)
Кданного рода изделиям относятся щетки для электрических машин, электроды для дуговых печей, контактные детали и др. Электроугольные изделия изготовляют методом прессования из исходных порошкообразных масс с последующим обжигом.
Исходные порошкообразные массы составляют из смеси углеродистых материалов (графит, сажа, кокс, антрацит и пр.), связующих и пластифицирующих веществ (каменноугольные и синтетические смолы, пеки и пр.). В некоторых порошкообразных массах связующего нет.
Щетки для электрических машин бывают графитными, угольно-графитными, электрографитированными, металло-графитными. Графитные щетки изготовляют из натурального графита без связующего (мягкие сорта) и с применением связующего (твердые сорта). Графитные щетки отличаются мягкостью и при работе вызывают незначительный шум. Угольно-графитные щетки производят из графита с добавлением других углеродистых материалов (кокс, сажа), с введением связующих веществ. Полученные после термической обработки щетки покрывают тонким слоем меди (в электролитической ванне). Угольно-графитные щетки обладают повышенной механической прочностью, твердостью и малым износом при работе.
Электрографитированные щетки изготовляют из графита и других углеродистых материалов (кокс, сажа), с введением связующих веществ. После первого обжига щетки подвергают графитизации, т. е. отжигу при температуре 2500—2800° С. Электрографитированные щетки обладают повышенной механической прочностью, стойкостью к толчкообразному изменению нагрузки и применяются при больших окружных скоростях. Металло-графитные щетки производят из смеси порошков графита и меди. В некоторые из них вводят порошки свинца, олова или серебра. Эти щетки отличаются малыми значениями удельного сопротивления, допускают большие плотности тока и имеют малые переходные падения напряжения.
Устройство электроборудования
Работа электрика по обслуживанию электрооборудования сводится к поддержанию работоспособного и безопасного состояния электрических машин, пуско-защитных аппаратов, устройств освещения, сигнализации и автоматики, что все и называется электрооборудованием, а также проводов, кабелей, разъемов, зажимов, электромонтажных изделий и т. д.
В состав устройств могут входить различные элементы, например, резисторы, конденсаторы, полупроводниковые приборы. Электрик должен быть знаком со всеми этими элементами, аппаратами и устройствами, но при работе он встречает много вопросов и затруднений, особенно в молодом возрасте, когда мало опыта. Полезно все эти вопросы и затруднения не спеша проанализировать с книгой, но таких книг пока недостаточно.
Целью данного раздела суперэнциклопедии является знакомство электрика с электрооборудованием и другими составляющими электроустановок в части их безопасности, безотказности, увеличения срока службы.
Раздел 1.
Раздел 1.
Электрическая энергия является неотъемлемым благом цивилизации. Обладая легкой делимостью, транспортабельностью, универсальностью, она проникла во все сферы нашей жизни и обеспечивает комфорт в жилище, приготовление пищи, такие блага цивилизации, как связь, телевидение, радио и т. д.
В быту, на даче, на подсобных участках нам приходится соприкасаться и пользоваться сотнями электрических помощников, облегчающих труд и создающих комфорт. Грамотная их эксплуатация, элементарные работы по включению и подключению, замене отдельных элементов, ремонту — вот основные задачи, с которыми приходится сталкиваться практически каждому человеку. Часто неспециалисту сложно объяснить, что же он хочет от электроустановки, какие могут быть последствия несанкционированного вмешательства в ее работу, как уберечься от поражения электрическим током. Авторы осознавали объемность задач и поэтому ограничились наиболее общими и прикладными вопросами применения электрической энергии дома и на даче. Для удобства читателя сведения сгруппированы по тематике, а информация представлена в виде вопросов и ответов, что позволяет ее конкретизировать.
Электричество - Друг и Враг
Электричество - Друг и Враг
Электричество является не только источником благ, но и основой для многочисленных забот по его рациональному и безопасному использованию. Ответом на эти общие вопросы и посвящена настоящая глава.
Каков порядок допуска в эксплуатацию производственных потребителей?
Сложившаяся монополия государственных энергосистем определяет единство требований к порядку допуска в эксплуатацию потребителей. Основным правовым документом, регулирующим взаимоотношения энергоснабжающей организации и потребителя (абонента), является договор. В договоре указываются количество, сроки и качество подлежащей отпуску электроэнергии; категория потребителей; порядок определения цены отпускаемой электроэнергии; способ и условия контроля потребления электроэнергии с указанием приборов, по которым он будет производиться; формы расчета; обязательство обеспечить установленный договором режим потребления; обязательство потребителя допускать представителей электроснабжающей организации и органов Государственного энергонадзора для проверки технических средств коммерческого учета электроэнергии, состояния электрооборудования и электроустановок потребителей. Договоры на снабжение электроэнергией заключаются в письменной форме по инициативе абонента не позднее чем за три месяца до начала потребления. Договор не реже чем через каждые три года подлежит обновлению и корректировке. При сдаче собственности в аренду потребитель письменно сообщает энергоснабжающей организации наименование арендатора, характер деятельности и сроки аренды, заключает договор о взаимоотношениях с организацией-арендатором и продолжает расчеты за потребленную электроэнергию с электроснабжающей организацией по установленным тарифам.
Обязательным условием заключения договора на снабжение электроэнергией является наличие у потребителя: технических условий на присоединение к электрическим сетям энергоснабжающей организации; акта границ балансовой принадлежности и ответственности сторон; установленных и готовых к эксплуатации технических средств учета потребления электроэнергии; согласованной с энергоснабжающей организацией годовой потребности в электроэнергии и мощности, подтвержденной соответствующими документами.
Подача напряжения на новые электроустановки производится при наличии акта допуска их в эксплуатацию, заключения органа Госэнергонадзора о соответствии объекта утвержденной проектно-сметной документации после заключения договора на пользование электроэнергией, проверки и установки приборов учета и при наличии наряда Энергонадзора на включение электроустановки.
До пуска электроустановок в эксплуатацию они должны пройти приемосдаточные испытания и быть приняты потребителем от монтажной или пусконаладочной организации по акту в соответствии с действующими правилами. Электроустановки с сезонным характером работы (дома, зоны отдыха и т. п.) должны ежегодно перед включением предъявляться для осмотра инспектору Госэнергонадзора. В договоре между абонентом и энергоснабжающей организацией указываются данные о присоединенных к сети абонента субабонентах (наименование, мощность, электропотребление, расчетные счетчики, тарифы и т. д.).
Абоненты рассчитываются за электрическую энергию, потребленную ими и субабонентами, по тарифам, установленным для соответствующих групп потребителей, к которым они относятся (жилой сектор, электроплиты, производственные потребители и т. д.).
Kак и кого получить разрешение на подключение жилого дома?
После завершения монтажа электроустановок потребитель (владелец дома) должен подготовить документацию:
• согласованный проект электроснабжения (или подробную схему);
• протокол измерения сопротивления тока заземляющего устройства и повторного заземления;
• протокол проверки цепи между заземлителями и заземляющими элементами токоприемников;
• акт на скрытые работы по монтажу кабелей проводок и заземляющих устройств;
• технические паспорта на силовое электрооборудование и приборы учета с отметкой торгового предприятия или справку о приобретении;
• технические условия и справку владельца электрических сетей, ведавших технические условия, об их выполнении.
При наличии указанной документации потребитель подает заявление на отпуск электроэнергии и вызов представителя предприятия Энергонадзор. Представитель должен:
• осмотреть выполненный монтаж электроустановок на соответствие проекту и Правилам устройства электроустановок;
• проверить соответствие результатов проведенных испытаний нормам;
• провести инструктаж владельца электроустановок по основным мерам безопасности при эксплуатации, о чем делается соответствующая запись в заявлении-обязательстве владельца.
Право пользования электроэнергией потребителю предоставляется после допуска электроустановок к эксплуатации и выдачи абонентской книжки или абонентской карточки. Присоединение электроустановок к электросети производится персоналом предприятия, выдавшего технические условия, по наряду предприятия Энергонадзор.
Что делать если вы хотите использовать электрическую энергию для нагрева?
Для получения разрешения на применение электроэнергии для нагрева потребитель представляет материалы, обосновывающие целесообразность данного решения: технико-экономическое обоснование выбора электронагрева; перечень видов электротермической технологии; перечень электронагревательных устройств, предполагаемых к установке, с указанием их паспортных данных; перечень мероприятий по снижению потребляемой мощности в часы максимума нагрузки энергосистемы; перечень приборов и устройств, контролирующих включение нагрузки.
К технологическим процессам с использованием в тепловых процессах электрической энергии относят местный обогрев животных и птицы (коврики, брудеры, электрообогреваемые полы и т. п.):
нагрев воды и получение пара для запаривания кормов, пропаривания молочной посуды, промывки молокопроводов, пастеризации молока:
подогрев воды для поения скота; поддержание необходимого температурного режима в хранилищах фруктов, овощей и семенного зерна.
При применении электроводонагревателей мощностью более 10 кВт они должны быть оборудованы аккумуляторами нагретой воды.
Применение электронагревательных устройств для целей отопления и горячего водоснабжения в организациях, в помещении контор, клубов и т. д., где имеются источники центрального или местного теплоснабжения, а также в помещениях гаражей для личного автотранспорта запрещается.
Надо ли получать разрешение на установку стационарных электроплит и каков его порядок ?
Не требуется разрешение на установку стационарных плит для приготовления пищи:
- при установке бытовых кухонных плит в жилых домах высотой 9 и более этажей независимо от места их строительства и ведомственной принадлежности;
- при установке бытовых кухонных электроплит и электротитанов в общежитиях независимо от этажности;
- при установке электротермического оборудования в детских яслях-садах, общеобразовательных школах, школах-интернатах, техникумах, институтах, профтехучилищах, больницах и поликлиниках, в буфетах и кафе театров и кинотеатров.
Во всех прочих случаях разрешение должно быть выдано в соответствии с общими правилами получения разрешений на подключение электроэнергии для нагрева.
Как организуется учет электроэнергии?
Для коммерческого учета используют только технические средства, включенные в реестр Госстандарта. При питании от одного источника электроснабжения нескольких потребителей различных тарификационных групп приборы учета должны быть установлены для каждой тарификационной группы. Это требование касается как абонентов, так и субабонентов. В жилых домах расчетные электросчетчики устанавливают на каждую квартиру (абонента), а также для учета электроэнергии, расходуемой для общедомовых нужд (освещение подъездов, работа лифтов и т. п.).
Технические средства коммерческого учета (электросчетчики, сумматоры и т. п.) после согласования проекта с электроснабжающей организацией приобретаются и устанавливаются потребителями (абонентами) или организациями-застройщиками. Техническое обслуживание данных средств учета производит энергоснабжающая организация, она же проводит проверку и плановую их замену.
Технические средства коммерческого учета должны иметь на креплении кожухов пломбы Госстандарта, а также пломбы энергоснабжающей организации на крышках других средств, защищающих схемы учета от вмешательства извне.
При применении электрической энергии для нагрева должны предусматриваться электрические счетчики для расчета за потребленную электроэнергию по двум зонам суток (дневной, ночной). Данные приборы приобретаются, устанавливаются и эксплуатируются потребителем. Планируемые к установке приборы учета и устройства управления должны быть согласованы с электроснабжающей организацией на стадии проектирования.
При электроснабжении индивидуальных жилых домов и строений число и тип счетчиков определяются проектом и зависят от вида тарифа на потребляемую электроэнергию. Проект обязательно должен быть согласован с энергоснабжающей организацией и предприятиями Энергонадзора. Перед трехфазным счетчиком обязательно устанавливают отключающий аппарат (рубильник, автоматический или пакетный выключатель и т. п.). Счетчики должны быть непосредственного включения и иметь пломбу с клеймом госповерителя давностью на момент установки не более: трехфазные — 12 месяцев; однофазные — 2 года.
Приборы учета, отключающие аппараты и при необходимости другие устройства должны быть опломбированы. После счетчика, включенного непосредственно в питающую сеть, должен быть установлен аппарат защиты. Он должен устанавливаться возможно ближе к счетчику, но не далее чем на 10 м по длине электропроводки. Если после счетчика каждая линия снабжена аппаратами защиты, установка общего аппарата защиты не требуется.
Перед счетчиком должно быть установлено отключающее устройство в виде рубильника или двухполюсного выключателя для безопасной замены счетчика с приспособлением для пломбирования.
Кто имеет право обслуживать и эксплуатировать электрооборудование?
Эксплуатация электрооборудования бывает производственная и техническая. Производственная эксплуатация предполагает использование оборудования с целью получения технологического эффекта и производится технологическим персоналом или пользователем (электросоковыжималка — для получения сока, электроплита — для приготовления пищи и т. п.). В условиях производства этот персонал относится к 1-й группе по технике безопасности и периодически инструктируется.
Техническая эксплуатация направлена на обеспечение надежной и безопасной работы оборудования или восстановление его работоспособности и должна осуществляться квалифицированным электротехническим персоналом. Квалифицированным электротехническим персоналом считаются специально подготовленные лица, прошедшие проверку знаний в объеме, обязательном для данной работы, и имеющие квалификационную группу по технике безопасности. Групп по технике безопасности 5. Чем выше квалификационная группа, тем больше возможности электротехнического персонала. Лица со второй квалификационной группой могут выполнять работы в недействующих электроустановках, с третьей и выше — в действующих электроустановках.
В зависимости от вида помещений, условий окружающей среды, наличия или отсутствия токопроводящих предметов предъявляются различные требования по эксплуатации и устройству электрооборудования. Несоблюдение этих требований может привести к нарушениям в работе электроустановок, электротравмам, пожарам или взрывам.
Что такое категория по надежности электоснабжения и она обеспечивается?
Все потребители электрической энергии при питании от государственной энергосистемы различаются по надежности электроснабжения, иначе — по категориям.
Электроприемники I категории — это такие электроприемники, перерыв в электроснабжении которых может повлечь за собой опасность для жизни людей, значительный ущерб народному хозяйству, повреждение дорогостоящего основного оборудования, массовый брак продукции, расстройство сложного технологического процесса, нарушение функционирования особо важных элементов коммунального хозяйства.
Электроприемники II категории — электроприемники, перерыв электроснабжения которых приводит к массовому недоотпуску продукции, массовым простоям рабочих, механизмов и промышленного транспорта, нарушению нормальной деятельности значительного количества городских и сельских жителей.
Электроприемники III категории — все остальные электроприемники, не подходящие под определения I и II категории.
Электроприемники I категории должны обеспечиваться электроэнергией от двух независимых взаимно резервирующих источников питания, и перерыв их электроснабжения может быть допущен лишь на время автоматического восстановления питания. Для электроснабжения особой группы электроприемников I категории должно предусматриваться дополнительное питание от третьего независимого взаимно резервирующего источника питания. В качестве такого источника могут использоваться местные электростанции, аккумуляторные батареи и т. п. Примеры потребителей I категории — аварийнее освещение зрелищных предприятий, охранная сигнализация, инкубатории, предприятия канализации, варочные, операционные отделения и т. п.
Электроприемники II категории допускают перерыв в электроснабжении до одних суток, их электроснабжение может осуществляться по одной воздушной линии или по одной кабельной линии, состоящей не менее чем из двух кабелей, присоединенных к одному общему аппарату. К потребителям II категории относятся мастерские, молочно-товарные фермы, теплицы и т. п.
Потребители III категории могут питаться от одного источника электроснабжения, при условии, что время ремонта или замены поврежденного элемента не превышает одних суток. К потребителям III категории относят индивидуальные жилые дома, дачи и т. п.
Kак классифицируют электроустановки и помещения по условиям окружающей среды?
Электроустановкой называется совокупность машин, аппаратов, линий и вспомогательного оборудования вместе с сооружениями и помещениями, в которых они установлены.
Открытыми, или наружными, электроустановками называются электроустановки, не защищенные зданием от атмосферных воздействий. Электроустановки, защищенные только навесами, сетчатыми ограждениями и т. п., рассматриваются как наружные.
Закрытыми, или внутренними, электроустановками называются электроустановки, размещенные внутри здания, защищающего их от атмосферных воздействий.
Электропомещениями называются помещения или отгороженные, например сетками, части помещения, доступные только для квалифицированного обслуживающего персонала, в которых расположены электроустановки.
Сухими помещениями называются помещения, в которых относительная влажность воздуха не превышает 60%.
Влажными помещениями называются помещения, в которых пары или конденсирующая влага выделяются лишь кратковременно в небольших количествах, а относительная влажность воздуха более 60%, но не превышает 75%.
Сырыми помещениями называются помещения, в которых относительная влажность воздуха длительно превышает 75%.
Особо сырыми помещениями называются помещения, в которых относительная влажность воздуха близка к 100% (потолок, стены, пол и предметы, находящиеся в помещении, покрыты влагой).
Жаркими помещениями называются помещения, в которых под воздействием различных тепловых излучений температура превышает постоянно или периодически (более 1 сут)+ 35°С (например, помещения с сушилками, сушильными и обжигательными печами, котельные и т. п.).
Пыльными помещениями называются помещения, в которых по условиям производства выделяется технологическая пыль в таком количестве, что она может оседать на проводах, проникать внутрь машин, аппаратов и т. п.
Пыльные помещения разделяютсяна помещения с токопроводящей пылью и помещения с токонепроводящей пылью.
Помещениями с химически активной или органической средой называются помещения, в которых постоянно или в течение длительного времени содержатся агрессивные пары, газы, жидкости, образуются отложения или плесень, разрушающие изоляцию и токоведущие части электрооборудования. По опасности взрыва или пожара помещения бывают взрывоопасными (шесть классов — B-I, В-Iа,в, г, B-II и В-IIа) и пожароопасными (четыре класса - П-1, П-II, П-IIIa, П-III).
Kак классифицируют электроустановки и помещения по опастности поражения электрическим током?
Электроустановки по условиям электробезопасности делят на установки до 1000 В и установки выше 1000В, действующие и недействующие.
В отношении опасности поражения людей электрическим током различаются:
1. Помещения без повышенной опасности, в которых отсутствуют условия, создающие повышенную или особую опасность.
2. Помещения с повышенной опасностью, характеризующиеся наличием в них одного из следующих условий, создающих повышенную опасность:
а) сырости или токопроводящей пыли;
б) токопроводящих полов (металлические, земляные, железобетонные, кирпичные и т. п.);
в) высокой температуры;
г) возможности одновременного прикосновения человека к имеющим соединение с землей металлоконструкциям зданий, технологическим аппаратам, механизмам и т. п., с одной стороны, и к металлическим корпусам электрооборудования, — с другой.
3. Особо опасные помещения, характеризующиеся наличием одного из следующих условий, создающих особую опасность:
а) особой сырости;
б) химически активной или органической среды;
в) одновременно двух или более условий повышенной опасности.
4. Территории размещения наружных электроустановок. В отношении опасности поражения людей электрическим током эти территории приравниваются к особо опасным помещениям.
От чего зависит напряжение , применяемое в электроустановках?
Напряжение в электроустановках принимают стандартным с учетом класса помещений по условиям окружающей среды и опасности поражения электрическим током.
При питании от государственной энергосистемы номинальное напряжение питающей однофазной сети — 220 В, трехфазной — 380/ 220 В.
В помещениях без повышенной опасности это напряжение применяют без ограничений, в том числе и для электрифицированного инструмента.
В помещениях с повышенной опасностью и особо опасных при выполнении открытых проводок их высота должна быть не менее 2, 5 м за исключением спусков к розеткам, выключателям аппаратов и т. д. При невозможности соблюсти это требование должно применяться пониженное (42 В и ниже) напряжение и выполняться проводки в трубах (например, проводки в подвалах на даче или в смотровой яме гаража и т. п.). Переносной электрифицированный инструмент применяют в этих помещениях на напряжение 36 В, а в особо опасных и на металлических полах или емкостях — при использовании дополнительных защитных средств (диэлектрических бот, перчаток, ковриков и т. п.).
Аналогичные требования предъявляются и к переносным осветительным приборам.
Какие различают виды поражения электрическим током?
Различают два вида поражения электрическим током: электрические травмы и электрический
удар.
Электрические травмы представляют собой местные поражения тканей электрическим током в виде ожогов, электрических знаков и металлизации кожи.
Ожоги возникают при прохождении через тело человека тока более 1 А, в результате чего в тканях выделяется тепло. При нагреве тканей до температуры 60 — 70°С свертывается белок и возникает ожог.
Электрические знаки появляются в месте контакта с токоведущими частями. Они выделяются в виде овальной или круглой припухлости с затвердевшей кожей желтоватого цвета, очерченной белой или серой каймой. Их появление связано с глубоким поражением живой ткани.
Электрометаллизация кожи — пропитывание поверхности кожи частицами металла при его разбрызгивании и испарении под действием тока при горении дуги.
Электрический удар (шок) наблюдается при воздействии тока до нескольких сотен миллиампер. Такой ток не вызывает ожогов, но, действуя на нервную систему и мышцы, может привести к параличу дыхательных мышц, а также мышц сердца, в отдельных случаях - к смертельному исходу.
Что называется напряжением прикосновения?
Если к заземленной установке, в которой возникло напряжение на корпус, прикоснется человек, он окажется под действием напряжения прикосновения.
Напряжением прикосновения называется разность потенциалов между опорными точками под ногами человека и руками, которыми он касается корпуса электроустановки, находящейся под напряжением.
Различают однофазное прикосновение, т. е. прикосновение к одной фазе сети, и двухфазное — прикосновение к двум фазам сети.
Однофазное прикосновение происходит и при одновременном прикосновении к фазному и нулевому проводам, но в этом случае возможность поражения током увеличивается ввиду уменьшения сопротивления, которое в данном случае состоит из сопротивления человеческого тела от руки к руке.
Двухфазное прикосновение более опасно - в этом случае человек попадает под полное линейное напряжение.
Напряжение прикосновения может достигнуть опасной величины в случае большого сопротивления заземлителя или обрыва заземления.
Как защитить себя и окружающих от поражения электрическим током?
Безопасность обслуживающего персонала и прочих потребителей электрической энергии от поражения электрическим током обеспечивается:
• применением изоляции, которая может быть повышенной, а в отдельных случаях — двойной;
• соблюдением расстояния до токоведущих частей или путем закрытия, ограждения токоведущих частей;
• применением блокировки аппаратов и ограждающих устройств для предотвращения ошибочных операций и доступа к токоведущим частям;
• надежным и быстродействующим автоматическим отключением частей электрооборудования, случайно оказавшихся под напряжением, поврежденных участков сети, в том числе защитного отключения;
• заземлением и заземлением корпусов оборудования и элементов электроустановок, которые могут оказаться под напряжением вследствие повреждения изоляции;
• выравниванием потенциалов;
• применением разделительных трансформаторов;
• применением напряжений42 В и ниже переменного тока частотой 50 Гц и 110 В и ниже постоянного тока;
• применением предупреждающей сигнализации, надписей и плакатов;
• применением устройств, снижающих напряженность электрических полей;
• использованием средств защиты и приспособлений, в том числе для защиты от воздействия электрического поля в электроустановках, в кото
рых его напряженность превышает допустимые нормы.
В жилых, общественных и тому подобных помещениях устройства, служащие для ограждения и закрытия токоведущих частей, должны быть сплошные; в производственных помещениях и электропомещениях допускаются сплошные, сетчатые или дырчатые устройства.
Ограждающие и закрывающие устройства должны быть выполнены так, чтобы снимать или открывать их было можно лишь при помощи ключей или инструментов.
Какие защитные средства применяют в электроустановках?
Защитными средствами называют приборы, аппараты и переносные приспособления, предназначенные для защиты персонала, работающего в электротехнических установках, от поражения электрическим током. Изолирующие защитные средства делятся на основные и дополнительные.
В установках низкого напряжения основными защитными изолирующими средствами являются резиновые диэлектрические перчатки и галоши, инструмент с изолирующими рукоятками, указатели напряжения.
К дополнительным защитным средствам в установках низкого напряжения относятся резиновые коврики и изолирующие подставки.
Техническое состояние всех защитных средств, принятых в эксплуатацию, надо систематически проверять.
Перед вводом в эксплуатацию защитного средства необходимо проверить его исправность и соответствие защитного средства напряжению установки (табл.1).
Таблица 1. Периодичность и нормы электрических испытаний защитных средств
Наименование защитных средств | Напряжение электроустановки, кВ | Испытательное напряжение, кВ | Продолжительность испытания, мин | Ток утечки (не более), мА | Сроки периодических испытаний, мес |
Перчатки резиновые диэлектрические | До 1 | 2,5 | 1 | 2,5 | 6 |
Тоже | Выше 1 | 6,0 | 1 | 6,0 | 6 |
Боты резиновые диэлектрические | Любое | 15 | 1 | 7,5 | 36 |
Галоши резиновые диэлектрические | До 1 | 3,5 | 1 | 2,0 | 12 |
Коврики резиновые | До1 | 3,0 | Протягиванием их между цилиндрическими электродами со скоростью 2-3 см/с | 3,0 | 24 |
Тоже | Выше 1 | 15 | Тоже | 15 | 24 |
Инструмент с изолирующими рукоятками | До 1.0 | 2,0 | 1 | - | 12 |
Токоизмерительные клещи | До 0,04 | 0,5 | 5 | - | 12 |
Тоже | 0,04-0,65 | 2,0 | 5 | - | 12 |
—— » —— | 0,65-1 | 3,0 | 5 | - | 12 |
Изолирующие подставки | Любое | 40 | 1 | - | 24 |
Какие выпускаются устройства защитного отключения?
Защитно-отключающие устройства предназначены для защиты от поражения током людей, работающих с электроустановками переменного тока. В настоящее время разработано большое количество схем защитного отключения. Технические характеристики некоторых устройств, применяемых в сетях с заземленной нейтралью, приведены в таблице 2.
Таблица 2. Технические характеристики защитно-отключающих устройств для передвижных и переносных токоприемников
Тип | Отключаемая мощность, кВт | Напряжение, В | Уставка защиты, мЛ | Время отключения, с | Масса, кг |
ИЭ-9801 | 2,2/1,1 | 220/380 | 10 | 0,05 | 2,5 |
ИЭ-9802 | 4,0/2,2 | 220/380 | 10 | 0,05 | 4,0 |
ИЭ-9811 | 1,1/0,6 | 220/380 | 10 | 0,05 | 3,0 |
ИЭ-9812 | 4,0/2,2 | 220/380 | 10 | 0,05 | 3,0 |
В сетях с заземленной и изолированной нейтралью можно применять защитно-отключающие устройства типа ЗОУП-25. Они рассчитаны на ток потребителя до 25 А при напряжении 380 В; уставка защиты —10 мА, время отключения — 0,05 с, масса — 4,5 кг. При работе с электроинструментами однофазного тока общей мощностью 0,6 кВт при 220 В применяют защитно-отключающие устройства ЗОУ-1. Для электросварочных установок по своим параметрам, электрической схеме и конструктивному выполнению из серийно выпускаемых защитно-отключающих устройств наиболее перспективно устройство типа УСНТ-4. Оно может применяться для укомплектования сварочных установок переменного тока с током сварки от 60 до 500 А. Устройство УСНТ-4 обеспечивает снижение напряжения холостого хода при ручной сварке и не снижает качества сварки.
Kак проверить наличие напряжения в сети?
Проверяют наличие напряжения в сети или на оборудовании указателями («пробниками»), измерительными приборами. Запрещено использовать лампочки («контрольки»).
Рис. 1. Пробники и индикаторы с разнообразным питанием для проверки целости обесточенной электроцепи: а, б, в — от батарейки для карманного фонарика; г —от электросети с напряжением 127 или 220 В; а — оформление транзисторного пробника со световой индикацией; е — искровой пробник типа «Тест» с пьезогенератором; 1 — проволочный патрон; 2 — батарейка; 3 — наушник; 4 — резистор; 5 — измерительный электроприбор; 6 — розетка; 7 — корпус цангового карандаша; 8 -щуп; 9 — глазок над светодиодом; 10 — проводящая часть корпуса; 11 — зажим типа «крокодил»; 12 — курок
Указатели низкого напряжения до 1000 В бывают однополюсные и двухполюсные (рис. 1).
Однополюсные указатели напряжения предназначены для проверки наличия напряжения и определения фазных проводов в электроустановках временного тока при подключении счетчиков, выключателей, патронов электроламп, предохранителей и т. п. Они работают по принципу протекания емкостного тока.
Однополюсный указатель напряжения состоит из сигнальной неоновой лампы типа ИН-3 или МН-3 и резистора типа МЛТ на 1 — 3 МОм, помещенных в корпус из изоляционного ударопрочного материала. Однополюсные указатели напряжения имеют специальную маркировку: УНН-1м, УНН-lx, УНН-90, ИН-90, ИН-91 и др.
Рабочее напряжение указателя типа УНН-1м -90 — 660 В переменного тока частотой 50 Гц; напряжение зажигания — 70 В. Ток, протекающий через указатель при напряжении 660 В, — не более 0, 6 мА. Масса указателя — 0, 1 кг.
Двухполюсные указатели напряжения предназначены для проверки наличия и отсутствия напряжения в электроустановках переменного тока и работают по принципу протекания активного тока.
Двухполюсные указатели напряжения МИН-1 и УНН-10 состоят из сигнальной лампы типа ИН-3, МН-3 или МТХ-90 и двух резисторов МЛТ-2 — ограничивающего и шунтирующего. Элементы указателя напряжения помещены в два корпуса из изоляционного материала, соединенных между собой гибким проводом с изоляцией повышенной надежности.
Рабочее напряжение указателя типа УНН-10 — 70 - 660 В переменного тока и 100 - 700 В
постоянного тока. Напряжение зажигания - 60 -65 В. Масса указателя - 0, 15 кг.
Кроме того, выпускаются двухполюсные пробники напряжения ПН-1, позволяющие по величине светящегося столба и сигнальной лампы определить величину измеренного напряжения, фазные и нулевой провода.
Какие требования техники безопасности предъявляются при эксплуатации переносных
электрофицированных инструментов?
Для обеспечения безопасности корпус переносного электроинструмента должен быть занулен. Штепсельные соединения выполняются таким образом, чтобы фазные выводы нельзя было спутать с зануляющими. Так, в трехфазном штепсельном соединении три фазных вывода расположены рядом, а зануляющий на некотором расстоянии от них. Если электроинструмент однофазный, то зануляющий вывод расположен между рабочими выводами. Зануляющий штырек должен быть длиннее остальных, чтобы включить зануление раньше включения рабочих жил.
В месте ввода провода в корпус электроинструмента на провод надевают гибкие рукава или манжеты, предохраняющие изоляцию провода от перетирания о край корпуса.
Напряжение инструмента не должно превышать 380/220 В при использовании его в помещениях без повышенной опасности и 36 В в остальных помещениях или вне их.
В особо опасных помещениях, а также внутри котлов и резервуаров даже инструмент на 36 В нужно использовать с применением изолирующих защитных средств.
К работе с электроинструментом допускаются лица, обученные безопасному обращению с ним. Каждый электроинструмент закрепляют за конкретным лицом. При неисправностях нельзя самостоятельно на рабочем месте ремонтировать электроинструмент или его провод и штепсельные соединения; такой ремонт обычно бывает низкого качества. Не реже одного раза в месяц надо проверять мегаомметром изоляцию ручного электрифицируемого инструмента, понижающих трансформаторов и преобразовательной частоты, а также отсутствие обрыва заземляющей (зануляющей) жилы в питающем проводе. При каждой выдаче электроинструмент необходимо проверить при помощи специального стенда или прибора (нормо-метра).
Какие требования техники безопасности предъявляются к переносным светильникам?
Рукоятка переносного светильника должна быть выполнена из изоляционного материала, а патрон и лампа закрыты предохранительной металлической сеткой. Для подвода напряжения используют гибкий шланговый шнур.
Переносные светильники, подключенные к сети напряжением 110 — 220 В, могут представлять значительную опасность при повреждении изоляции провода. В помещениях с повышенной опасностью и особо опасных переносные светильники применяют на напряжение не выше 36 В. В случае, если рабочий может соприкасаться с металлическими (хорошо заземленными) поверхностями или находится в особо сырых помещениях (в баках, колодцах, котлах), для питания переносных светильников применяют напряжение не выше 12 В.
Переносные светильники присоединяют к сети напряжением 12 - 36 В или к сети 110 - 220 В через понижающие трансформаторы. Длина проводов от штепсельной розетки на 127 — 220 В до переносного трансформатора должна быть не более 2 м. У понижающих трансформаторов корпус и обмотки низшего напряжения заземляют, открытые незащищенные токоведущие части ограждают.
При работе внутри металлических баков и котлов понижающий трансформатор располагают снаружи. Изоляцию переносных проводов, а также понижающих трансформаторов проверяют мегаомметром не реже одного раза в месяц.
Какие требования предъявляются к лестицам и стремянкам?
Для изготовления лестниц и стремянок необходимо использовать сухое дерево, желательно без сучков. Ступени (перекладины) врезают в тетивы и через каждые 2 м скрепляют стяжными болтами. Запрещается работать на лестницах и стремянках, у которых перекладины прибиты гвоздями. Разрешается использовать приставные деревянные лестницы длиной не более 5 м и шириной не менее 0,5 м. Нижние концы лестниц и стремянок должны быть снабжены шипами или резиновыми наконечниками. Если пол деревянный крашеный, паркетный, асфальтовый, бетонный и т.д., используются резиновые наконечники; если же пол земляной или деревянный торцовый, применяются металлические шипы. Нельзя устанавливать лестницы и стремянки на дополнительные промежуточные сооружения из ящиков, бочек и др.
Как освободить человека от воздействия электрического тока?
При соприкосновении человека с токоведущими частями надо немедленно освободить его от действия тока, быстро отключив ту часть установки, к которой прикоснулся пострадавший. В том случае, когда с отключением электроустановки одновременно отключается и электрическое освещение, необходимо обеспечить освещение от других источников. Если выключатель находится далеко и установку нельзя отключить достаточно быстро, надо принять меры к отделению пострадавшего от токоведущих частей.
Оказывающий помощь должен принять необходимые меры-предосторожности: надеть диэлектрические перчатки, галоши или обернуть руки сухой тканью и подложить под ноги сухую одежду или сухую доску.
Если поблизости окажется топор, можно, подсунув под провода доску, перерубить их. Рубить каждый провод надо в отдельности. Топорище должно быть совершенно сухим.
Можно также перекусить каждый провод в отдельности кусачками или пассатижами с изолированными ручками.
При отделении пострадавшего от токоведущих частей или проводов нельзя прикасаться к его телу незащищенными руками.
Как оказать доврачебныю помощь пострадавшему?
Сразу же после освобождения человека от действия электрического тока необходимо определить характер оказания первой помощи и вызвать врача. Если пострадавший находится в сознании, его следует уложить в удобное положение, освободить от стесняющей дыхание одежды, обеспечить доступ свежего воздуха и обязательно накрыть. До прихода врача необходимо наблюдать за дыханием и пульсом.
Когда человек находится в бессознательном состоянии, но сохраняется устойчивое дыхание и пульс, пострадавшему следует дать понюхать нашатырный спирт и обрызгать лицо водой.
Если пострадавший не дышит или дышит очень редко и судорожно, ему следует немедленно начать делать искусственное дыхание. Для этого пострадавшего кладут на спину. Оказывающий помощь одну руку подкладывает под шею пострадавшего, а другой старается как можно больше запрокинуть его голову назад. При таком положении головы восстанавливается проходимость дыхательных путей — запавший язык отходит от задней стенки гортани.
Следует проверить, нет ли во рту посторонних предметов и при помощи носового платка освободить рот от слизи; под лопатки надо подложить валик из свернутой одежды.
Сделав глубокий вдох, надо через марлю или платок вдувать воздух в рот пострадавшего. Выдох будет происходить самопроизвольно. Вдувание воздуха производят через каждые 5 — 6 с.
Если челюсти у пострадавшего плотно стиснуты и их нельзя быстро разжать, необходимо производить искусственное дыхание методом «рот в нос», т. е. вдувать воздух в нос пострадавшего.
Когда воздух вдувается в рот, рукой зажимают нос пострадавшего, а если вдувание производится в нос, зажимают рот. Маленьким детям воздух вдувают одновременно в рот и нос.
Для искусственного дыхания по способу «рот в рот» наша промышленность выпускает ручные портативные аппараты РПА-1 и РПА-2. Этими аппаратами осуществляется ритмичное вдувание в легкие пострадавшего атмосферного воздуха в одном из заданных объемов: 0, 25; 0, 5; 1; 1, 5 л.
Помимо искусственного дыхания рекомендуется производить также наружный массаж сердца. Для этого грудную клетку пострадавшего освобождают от одежды, а спину его укладывают на твердое основание. Ноги пострадавшего следует приподнять примерно на 0, 5 м.
При нахождении потерпевшего в состоянии мнимой смерти рекомендуется производить комплексное оживление — искусственное дыхание совместно с массажем сердца. Наиболее целесообразно проводить оживление вдвоем, в этом случае можно поочередно проводить искусственное дыхание и массаж сердца.
Если первую помощь оказывает один человек, он делает пострадавшему 2—3 глубоких вдувания, после чего в течение 15—20 с проводит массаж сердца, затем снова искусственное дыхание, опять.массаж и т. д.
О восстановлении сердечной деятельности свидетельствует появление пульса, который сохраняется, если на несколько секунд прекратить массаж.
Как проверить эффективность оказываемой помощи?
При правильном проведении искусственного дыхания каждое вдувание вызывает расширение грудной клетки, прекращение вдувания вызывает ее спадание, сопровождаемое характерным шумом при выходе воздуха из легких пострадавшего через рот и нос. При затруднении вдувания надо проверить, свободны ли дыхательные пути пострадавшего.
Эффект наружного массажа сердца проявляется в первую очередь в том, что каждое надавливание на грудину вызывает появление пульса — на лучевой артерии у запястья или на сонной артерии на шее.
При правильном проведении искусственного дыхания и массажа сердца у пострадавшего появляются следующие признаки оживления: улучшается цвет лица — оно приобретает розовый оттенок вместо серо-землистого цвета с синеватым оттенком, который был до оказания помощи; появляются самостоятельные дыхательные движения, которые становятся все более и более равномерными по мере продолжения мероприятий по оживлению; сужаются зрачки.
Степень сужения зрачков может служить наиболее точным показателем эффективности оказываемой помощи. Узкие зрачки указывают на достаточное снабжение мозга кислородом. Начинающееся расширение зрачков указывает на ухудшение кровообращения мозга.
Следует помнить, что даже кратковременное прекращение искусственного дыхания или массажа сердца может привести к непоправимым последствиям.
При поражении электрическим током ни в коем случае нельзя зарывать пострадавшего в землю, так как это принесет ему только вред.
Kак погасить огонь в действующих электоустановках?
При тушении пожара в электроустановках, находящихся под напряжением, надо применять ручные огнетушители типаОУ-2 и ОУ-5.
Для приведения в действие этих огнетушителей необходимо левой рукой взяться за ручку, а правой повернуть маховичок вентиля в направлении против часовой стрелки до отказа.
После этого из раструба огнетушителя начнет выбрасываться струя углекислоты длиной около 2 м. Действие огнетушителя ОУ-2 - 30 с, а ОУ-5 - 50 с.
Во время тушения пожара необходимо отключить электроустановку. После ликвидации очагов пожара включать электроустановку можно только после очистки, проверки и восстановления нормального состояния всех питающих ее линий.
Применять пенные огнетушители нельзя, так как пена является хорошим электропроводником.
Рис. 1. Пробники и индикаторы с разнообразным питанием для проверки целости обесточенной электроцепи:
Изображение:
Дата добавления: 2018-08-06; просмотров: 737; Мы поможем в написании вашей работы! |
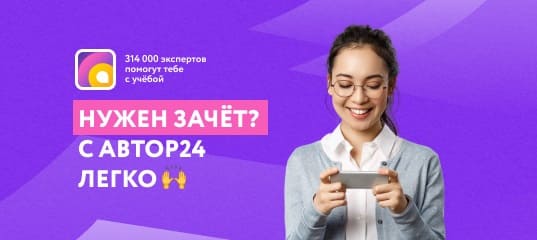
Мы поможем в написании ваших работ!