Математическое моделирование упругих деформаций в
Министерство образования и науки Российской Федерации
Федеральное государственное бюджетное образовательное
учреждение высшего профессионального образования
«УФИМСКИЙ ГОСУДАРСТВЕННЫЙ АВИАЦИОННЫЙ
ТЕХНИЧЕСКИЙ УНИВЕРСИТЕТ»
Кафедра АТП
Диссертация
на тему: « Анализ модели операции по наладке автоматического оборудования в расписаниях MES и ERP систем»
Выполнил:
студент гр. АТП-146М
Хуббутдинов Р.Ф.
Уфа-2018
СОДЕРЖАНИЕ
Введение……………………….……………………………….……………...3
Глава 1. Процесс обработки деталей на станках с ЧПУ и диагностика
износа инструмента………………………………………………………..….5
1.1 Математическое моделирование упругих деформаций в технологической системе………………………………………………………………………….5
|
|
1.2 Динамическая модель эквивалентной упругой системы……………………………………………………………………..….13
1.3 Процесс достижения точности при смене инструмента на станках с ЧПУ……………………………………………………………………….……19
Диагностика износа инструмента как средство повышения
надежности ……………………………………………………………………23
1.5 Классификация методов контроля состояния режущего инструмента…27
Глава 2. Основные понятия определения планирования и системные решения на базе ERP, APS и MES……………………………………………42
2.1 Определение планирования…………………………...……………….….42
2.2 Системные решения на базе систем ERP, APS и MES….……..………..45
Глава 3. Управление и планирование процессами на базе концепции CALS…………………………………………………………..……………….46
3.1 Управление процессами на базе концепции CALS……………………..46
3.2 Анализ жизненного цикла заказа………………………………………...47
3.3 Идея сокращения этапов ЖЦП на предприятии……………………...…48
Глава 4. Планирование расписаний и принятие решений в ERP, APS
и MES системах………………………………………………………..52
4.1 Учет различных классов обслуживающих устройств………………..…52
|
|
4.2 Алгоритмы планирования с процедурами принятия решения...……....54
Заключение…………………………………...…………………………….....56
Список использованной литературы…………………………………….….60
Введение
Современные гибкие производственные системы (ГПС), построенные на базе автоматизированных технологических участков (АТУ), не только не утратили своей актуальности в качестве основы современного промышленного производства, но и упрочили ее в силу изначально заложенного принципа гибкости построения и функционирования . Особенностью промышленного производства является тот факт, что в процессе работы некоторое оборудование может выйти из строя или потребоваться его профилактический ремонт. Таким образом, необходимо иметь возможность динамически перераспределять нагрузки между оставшимся оборудованием, чтобы не останавливать все производство. Главным фактором успеха сегодня становится повышение качества и скорости производства, поэтому в вопросах управления предприятием особую роль играют информационные системы. Все организационные и технологические решения должны приниматься оперативно. Следует отметить, что неоптимальные решения значительно снижают эффективность построения расписаний работы производственного участка. В рамках оперативного управления одной из важнейших проблем является проблема планирования загрузки технологического оборудования (ТО), т.е. упорядочение работ на выбранной структуре гибких производственных модулей (ГПМ).
|
|
Большинство разработанных до настоящего времени методик для оперативно-календарного планирования основано на упрощенных моделях, что снижает их точность.
Моделирование процесса составления субоптимального производственного расписания работы АТУ производится на основе разработанной объектной модели. Данная модель учитывает различные внешние воздействия, такие как поломка ТО, выполнение плановых ремонтных работ ТО, наладка оборудования, задержка в поставках материалов и прочее. При проектировании формируются очередь заготовок для обработки и очередь свободного ТО, имеющего возможность произвести изготовление заданной партии деталей. Так при составлении расписания моделируется время начала и окончания каждой производственной операции на выбранном типе ТО. Спроектированная таким образом объектная модель позволит составить алгоритм для планирования работы ТО, который легко может быть адаптирован к заданным условиям с учетом дополнительных ограничений.
|
|
Глава. 1 Процесс обработки деталей на станках с ЧПУ и диагностика износа инструмента
Математическое моделирование упругих деформаций в
Технологической системе.
Математическое моделирование играет важную роль в подготовке инженеров. Ее значение заключается в том, что на ней базируется любой метод научного исследования, она позволяет освоить методологические и математические средства исследования систем, в том числе, и машиностроительных. От того, насколько профессионально выполнено моделирование, зависит качество принимаемого решения.
Достижению данной цели служит изучение: 1) общих понятий математического моделирования процессов в машиностроении; 2) теоретических основ математического моделирования и оптимизации процессов в машиностроении; 3) вопросов математического моделирования физических процессов в технологических системах; 4) вопросов математического моделирования и оптимизации технологических станочных систем.
При обработке деталей на металлорежущих станках сам станок, приспособление, инструмент и элементы его крепления, обрабатываемая заготовка представляют собой упругую систему, которая называется упругой системой СПИД.
При обработке сила резания изменяется под действием переменных условий обработки, а именно неравномерности глубины резания, колебания твердости обрабатываемого материала и т.д. Колебания силы резания приводят к упругим деформациям деталей системы СПИД и смещению этих деталей по отношению друг к другу за счет наличия зазоров в соединениях. Кроме этого упругая система СПИД обладает не бесконечной жесткостью, причем эта жесткость также является случайной величиной, т.е. может изменять свое значение от наименьшего до наибольшего. Все это вместе взятое оказывает влияние на формирование точности обработки.
(function(w, d, n, s, t) { w[n] = w[n] || []; w[n].push(function() { Ya.Context.AdvManager.render({ blockId: "R-A-209096-6", renderTo: "yandex_rtb_R-A-209096-6", async: true }); }); t = d.getElementsByTagName("script")[0]; s = d.createElement("script"); s.type = "text/javascript"; s.src = "//an.yandex.ru/system/context.js"; s.async = true; t.parentNode.insertBefore(s, t); })(this, this.document, "yandexContextAsyncCallbacks"); Формирование упругих перемещений и смещения элементов в технологической системе и влияния их на точность обработки могут быть представлены следующей схемой – см. рис. 1.1.
Рис 1.1. Схема формирования упругих перемещений и смещения элементов в технологической системе и влияния их на точность обработки
Жесткость упругой системы СПИД – это отношение составляющей силы резания, направленной по нормали к обрабатываемой поверхности, к смещению лезвия инструмента, установленного на размер в данном направлении.
Таким образом, жесткость системы равна:
где – радиальная составляющая силы резания;
Н 1мм - смещение режущей кромки инструмента (деформация упругой системы). Логично выражается жесткость отдельных элементов технологической системы: для суппорта – j суп, для передней бабки – j ПБ и т.д.
Жесткость может быть выражена также отношением приращения силы резания к приращению перемещения
:
В практических расчетах иногда используют величину, обратную жесткости – податливость .
Величина деформации упругой системы равна:
Для определения статической жесткости узла станка производят ряд нагружений, возрастающих от нуля до некоторого предельного значения, которое определяется размерами станка. Для каждого значения нагрузки измеряют смещение узла в направлении действия силы. Затем производят разгружение этого узла, постепенно уменьшая нагрузку и фиксируя остаточные изменения.
Рис 1.2 Зависимости y = f(Py) при определении статической жесткости узла станка отжатия.
При нагружении и разгружении строятся зависимости – рис 1.2.
При этом нагрузочная и разгрузочная ветви характеристики жесткости обычно не совпадают, т.е. имеет место гистерезис. Площадь петли гистерезиса – работа, затраченная на преодоление сил трения, контактных деформаций и т.д. При повторных циклах нагрузки площадь петли гистерезиса уменьшается вследствие выборки зазоров в стыках деталей при первом нагружении и уменьшения пластического деформирования.
(function(w, d, n, s, t) { w[n] = w[n] || []; w[n].push(function() { Ya.Context.AdvManager.render({ blockId: "R-A-209096-7", renderTo: "yandex_rtb_R-A-209096-7", async: true }); }); t = d.getElementsByTagName("script")[0]; s = d.createElement("script"); s.type = "text/javascript"; s.src = "//an.yandex.ru/system/context.js"; s.async = true; t.parentNode.insertBefore(s, t); })(this, this.document, "yandexContextAsyncCallbacks"); Для оценки жесткости в любой точке (например, в точке А) кривой необходимо найти производную в данной точке
Численно производная равна тангенсу угла наклона касательной к кривой в точке А.
Жесткость станка зависит от его конструкции и от качества сборки. Для многих станков жесткость и податливость регламентированы ГОСТами.
Как показывает практика, статическая жесткость станков в 1,2 – 1,4 раза выше , чем жесткость работающих станков. Поэтому более объективной величиной является динамическая жесткость станков, которая определяется с помощью произвольного метода, который основан на обработке заготовок с переменным припуском и последующих расчетах .
Пример. Определение динамической жесткости токарного станка
(рис 1.3.).
Пояски диаметрами D1 и D2 обрабатываются за один рабочий ход при неизменных условиях (подаче, скорости резания и т.д.). Уступ , образовавшийся вследствие разных глубин резания и, следовательно, разных отжатий в технологической системе, будет меньше
(т.е.
).
Рис 1.3. Схема испытания токарного станка для определения его динамической жесткости.
Отношение называется уточнением. Оно показывает, во сколько раз в результате обработки уменьшилась погрешность заготовки. Уточнение характеризует жесткость технологической системы:
где - константа (постоянная силы резания).
– подача.
Жесткость станка зависит и от степени его нагрева. Так, например, жесткость шпиндельной бабки круглошлифовального неработающего станка составляет 15100 Н/мм. После 30 мин его работы на холостом ходу жесткость достигла 22400 Н/мм, т.е. увеличилась на 44%.
Жесткость узлов станков с вращающимися деталями не одинакова в радиальном направлении. Например, для токарных станков характерны следующие круглограммы жесткости шпиндельной группы (j) и упругих перемещений шпинделей (y), подобные приведенным на рис.1.4.
Рис 1.4. Круглограммы жесткости шпиндельной группы ( j ) и упругих перемещений шпинделей ( y ) токарных станков.
Учитывая, что жесткость технологической системы переменна, и ее значение зависит от многих факторов, проявление которых невозможно предвидеть заранее, ее характеристику следует отнести к разряду случайных величин.
Вследствие рассеяния значений припусков и характеристик свойств материалов заготовок, например, твердости, значения силы резания будут также рассеиваться от PНМ до РНБ. Если при этом учесть, что значения жесткости технологической системы случайны и подлежат рассеянию от jНМ до jНБ, то даже при стабильном рассеянии значений силы резания, значения поля рассеяния и координаты его середины
не будут оставаться постоянными – рис.1.5. Участок диаграммы между кривыми jНМ и jНБ на этом рисунке представляет собой поле
рассеяния значений жесткости технологической системы.
Рис 1.5. Иллюстрация формирования полей рассеяния упругих перемещений в технологической системе.
Сначала разрабатывается расчетная схема упругой системы станка, которая представляет собой многомассовую модель. Для этого станок разбивается на ряд узлов, каждый из которых представляет собой отдельную массу. Кроме этого какая-либо деталь станка принимается как деталь условно бесконечной массы, к которой «привязываются» все остальные массы. Расчетная схема упругой системы плоскошлифовального станка представляет собой четырехмассовую модель. В качестве детали условно бесконечной массы принята станина, к которой «привязаны» все остальные массы (рис. 1.6).
На данном рисунке приняты следующие обозначения:
1. шпиндель;
2. шпиндельная бабка;
3. продольный стол;
4. поперечный стол;
5. станина;
М1, М2, М3, М4 – приведенные массы шпинделя, шпиндельной бабки, продольного стола, поперечного стола;
С1, С2, С3, С4 – жесткости;
Н1, Н2, Н3, Н4 – коэффициенты демпфирования;
- вектор радиальной составляющей силы резания;
VЗ – скорость продольного перемещения заготовки.
Рис 1.6. Расчетная схема упругой системы плоскошлифовального станка
Взаимодействие между отдельными массами описывается, как правило, двумя видами связей:
1. упругими связями, которые характеризуются жесткостью;
2. демпфирующими связями, которые характеризуются коэффициентами демпфирования.
Иногда, рассматривая взаимодействие масс, учитывают третью связь, которая называется инерционной, которая как и две предыдущие также зависит от массы узлов. Все три вида связей зависят и от величины перемещения узла, от его скорости и ускорения. Инерционные связи в данной модели мы рассматривать не будем .
(function(w, d, n, s, t) { w[n] = w[n] || []; w[n].push(function() { Ya.Context.AdvManager.render({ blockId: "R-A-209096-6", renderTo: "yandex_rtb_R-A-209096-6", async: true }); }); t = d.getElementsByTagName("script")[0]; s = d.createElement("script"); s.type = "text/javascript"; s.src = "//an.yandex.ru/system/context.js"; s.async = true; t.parentNode.insertBefore(s, t); })(this, this.document, "yandexContextAsyncCallbacks"); Здесь исследуется механизм образования непрямолинейности, поэтому считают, что данная четырехмассовая упругая система имеет свободу перемещения вдоль оси Y. Следовательно, в качестве возбуждающей силы будет рассматриваться только радиальная составляющая сила резания. Т.к. смещение упругой системы необходимо рассматривать только вдоль оси Y, приведению выше на рис. 1.6. расчетную схему нужно заменять эквивалентной схемой.
Дата добавления: 2018-08-06; просмотров: 610; Мы поможем в написании вашей работы! |
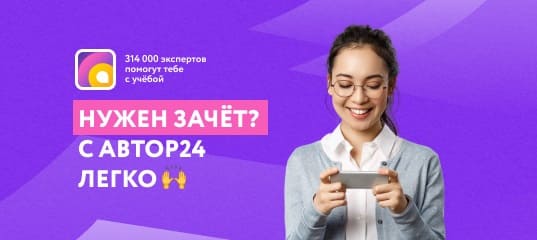
Мы поможем в написании ваших работ!