Машины для механических испытаний на растяжение
Основными частями разрывной машины являются механизм для нагружения образца и механизм для измерения силы, вызывающей деформацию.
Механизм для нагружения образца может действовать от гидравлического или механического привода. В первом случае перемещение одного из захватов происходит под действием поршня гидравлического цилиндра, во втором случае - при помощи механической передачи. Гидравлические машины применяются преимущественно для больших нагрузок (свыше 30т).
Механизм, измеряющий силу, вызывающую деформацию образца, может быть рычажным, рычажно-маятниковым, гидравлическим или пружинным. Наиболее точными и чувствительными являются машины с рычажно-маятниковым измерением силы, которые и получили наибольшее распространение в лабораторной практике.
Большая часть современных разрывных машин позволяет испытывать образцы не только на растяжение, но и под сжимающими нагрузками. Такие машины называются универсальными. На них можно производить испытания также на сжатие, изгиб, срез и другие виды нагружения, для чего машины снабжаются соответствующими приспособлениями.
Машины для испытания на растяжение должны обеспечить:
a) надежное центрирование образца;
b) сохранение показаний нагрузки в течение не менее 30 сек, а также постоянства показаний при повторных нагружениях;
c) плавность статического нагружения и разгружения, действие без ударов и толчков;
|
|
d) регулирование скорости перемещения подвижного захвата машины под нагрузкой до 20 кг/мм2;
e) при помощи специального регулятора;
f) возможность приостанавливать нагружение с точностью одного наименьшего деления силоизмерителя машины;
g) точность показаний нагружения до ±1 % от величины измеряемой силы (нагрузки).
Скорость перемещения захвата машины при испытаниях независимо от длины образца устанавливается равной: не более 4 мм/мин за пределом текучести.
Механические испытания при повышенных температурах
Для установления механической характеристики жаропрочных сплавов большое значение имеют методы испытаний при высоких температурах. Основным методам нагрева образцов при горячих испытаниях является метод нагрева их в электрических печах сопротивления в атмосфере горячего воздуха.
Для поддерживания постоянной температуры в печах применяются автоматические терморегуляторы. Наиболее точными являются терморегуляторы, действие которых основано на тепловом изменении размеров металлического муфеля печи. Эти регуляторы поддерживают температуру с колебаниями от ±1 до ±5 0С.
Температура испытуемого образца должна измеряться не менее чем в двух точках; при испытаниях на твердость и сжатие и применении малых образцов достаточно измерять температуру в одной точке.
|
|
Величины деформаций образцов при горячих испытаниях измеряются либо непосредственным наблюдением на образце через окно в стенке печи при помощи катетометра, либо с применением удлинительных планок, закрепленных на образце и выведенных из печи, перемещение которых измеряют при помощи индикаторов, экстензометров и других измерительных приборов.
Испытания на ползучесть
Под ползучестью понимается свойства металлов и сплавов медленно и непрерывно пластически деформироваться под воздействием постоянной нагрузки при напряжениях ниже предела упругости для данного металла.
Обычно определяют условный предел ползучести, величину наибольшего длительно приложенного напряжения, при котором материал при данной температуре за определенный период времени обнаруживает заданное суммарное удлинение образца или заданную скорость ползучести.
На рисунке.4 показана диаграмма, получаемая при испытании образца на ползучесть в координатах «относительное удлинение - время» (δ-t).
В момент нагружения в образце возникает упругая деформация δн выраженная на кривой рисунке.4. вертикальным участком Оа. За этим начинается первый этап испытания - образование остаточной пластической деформации δн с большой, но постепенно затухающей скоростью (участок ab на рисунке.4).
|
|
За первым этапом испытания следует второй этап условно равномерной скорости деформации, выраженный на кривой участок bc за которым следует третий этап - участок cd возрастающей скорости ползучести, заканчивающийся разрушением образца.
Рисунок.4. Первичная кривая ползучести.
Для определения предела ползучести ограничиваются первым и вторым этапом (образец до разрушения не доводится), получением лишь участков диаграммы: начального криволинейного ab и следующего за ним условно прямолинейного участка bc длительной деформации со сравнительно низкими скоростями ползучести, на котором возможно измерить с достаточной точностью величину деформации δc, суммарное удлинение (упругое δн + остаточное δ0) в % за время испытания.
Скорость ползучести определяется по формуле:
(16)
Длительность испытания на ползучесть устанавливается в 100, 50,
500 или 1000 час и выше в зависимости от хода кривой δ - t.
Испытания производят в следующем порядке, нагретый до заданной температуры образец выдерживают при этой температуре в течение не менее 1 часа, после чего к образцу плавно прикладывают предварительную нагрузку, равную около 10 % от заданной общей нагрузки и не вызывающую в образце напряжение более 1 кг/мм2. При помощи специального прибора измеряют удлинение образца с точностью 0,005 - 0,001 мм. Если удлинения остаются в течение 5 мин неизменными, то плавно нагружают образец до заданной нагрузки и замеряют удлинения через интервалы, позволяющие установить характер измерения удлинений.
|
|
По окончании испытания образец разгружают до величины предварительной нагрузки и определяют абсолютную величину остаточного удлинения.
Для определения условного предела ползучести испытывают не менее трех образцов при данной температуре и разных напряжений и на основе полученных первичных кривых ползучести строят диаграммы зависимости между напряжением и суммарным удлинением или между напряжением и средней равномерной скоростью удлинения на прямолинейном участке кривой и по ним находят интерполированием искомое напряжение, которое вызывает при данной температуре за определенный промежуток времени заданную скорость или заданную суммарную деформацию.
Для испытания используют два основных типа стандартных образцов, нормальный - диаметром 10 мм и расчетной длиной 100 мм и удлиненный – диаметром 10 мм и расчетной длиной – 200 мм. Допускаемые отклонения по площади сечения образцов ± 0,5 %.
Машины для испытания на ползучесть должны обеспечивать:
· плавность нагружения образца, постоянство нагрузки в течение всего процесса испытания, приложение нагрузки с точностью ±1 %.
· и без эксцентриситета;
· точность измерения деформации 0,001 мм;
· равномерный нагрев образца до заданной температуры и сохранение ее на протяжении всего испытания; колебания температуры образца допускаются не более ± 2 0С в любой точке образца, а разница температур в различных точках по длине образца – не больше 2-4 С в зависимости от температуры испытания; измерения температуры должны производиться с точностью 0,5 °С; колебания температуры в помещении, где производятся испытания, не должны превышать
3 0С.
Дата добавления: 2018-08-06; просмотров: 442; Мы поможем в написании вашей работы! |
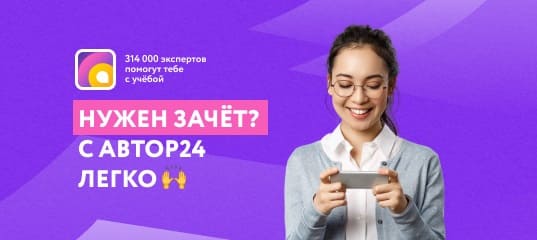
Мы поможем в написании ваших работ!