Руды, минералы и концентраты молибдена
Содержание молибдена в земной коре составляет 3 ∙ 10-4%. Известны минералы молибдена: молибденит МоS2, повеллит СаМоO4,вульфенит PbМоO4, молибдит (ферромолибдит) Fе2(МоO4)3 ∙ nН2O(n = 7-8), молибдешеелит Са(W, Мо)O4, линдгренит Сu3(МоO4)2(ОН)2, кехлинит Вi2(МоO4)O2, уранолибдат UO2· UO3 · 2MoO3, ильземаннит Мо3SO3 ·nН2O. Промышленное значение имеют первые четыре минерала. MoS2 - наиболее распространенный из них, который является основным молибденсодержащим минералом в концентратах, используемых для получения сплавов молибдена.Молибденит MoS2 залегает в кварцевых жилах, часто совместно с шеелитом (CaWO4), вольфрамитом (Fe, Mn)O4, касситеритом SnО2, халькопиритом CuFeS2 и другими минералами, например, мышьяка и висмута.Руды делятся на простые кварцево- молибденитовые, медно-молибденитовые и молибдено-вольфрамовые. Простые кварцево-молибденитовые руды содержат от нескольких десятых до 1% Mo. Содержание других сульфидов, кроме MoS2, незначительное. Медно-молибденовые руды связаны со вторичными кварцитами. Концентрация молибдена в этих рудах составляет несколько сотых, а иногда и тысячных долей процента [13]. К таким рудам относятся руды крупныхмедных месторождений, таких, как Коунрадское и Бощекульское (Казахстан), Алмалыкское (Узбекистан) и Каржарахское (Закавказье), являющихся важным источником для получения молибденовых концентратов. Медно-молибденовые руды содержат~0,7% Cu и 0,01% Mo. Применяя многостадийную технологию обогащения на первой стадии выделяют коллективный концентрат, содержащий 25-30%Cuи 0,3- 0,5% Mo, а из него получают медный (14% Cu, 23% SiO2, 20% Fe) и молибденовый концентраты. Важным источником получения меди и молибдена является медно- молибденовая руда месторождения «Эрдэнэт» (МНР), где сооружен рудник на средства стран бывшего СЭВ.
|
|
Скарновые (поликристаллические, образовавшиеся в результате замещения одних минералов другими) молибдено - вольфрамовые руды имеют в составе молибденит совместно с шеелитом (CaSO4), пиритом (FeS2) и халькопиритом, содержание которых обычно незначительное. К такому типу руд относятся руды Тырны-Аузcкого месторождения молибдена - вольфрамовых руд на Северном Кавказе. Молибденовые руды подвергают обогащению в основном флотацией. Молибденит обладает хорошей смачиваемостью углеводородами, и поэтому эффективными собирателями при флотации молибдена являются обычно керосин, трансформаторное, веретенное и другие нейтральные масла. Так, при обогащении молибденовольфрамовых руд Тырны - Аузского месторождения первоначально флотацией выделяют молибденит. Определенная часть повеллита (СаМоО4,) изоморфно связана с шеелитом (СаO4), и молибденовые концентраты содержат некоторое количество вольфрама [14].
|
|
Для производства ферромолибдена и лигатур применяют молибденовые концентраты, в которых молибден связан в молибденит МoS2 (таблица 1.1) и которые подвергаются предварительно окислительному обжигу с целью удаления серы.
Таблица 1.1 - Химический состав молибденовых концентратов по ГОСТ 212 - 76, %
Марка | Mo, % (не менне) | SiO2 | As | Sn | P | Cu | Na2O | WO3 | Sb |
КМГ - В КМГ - 1 КМФ - 2 КМФ - 0 КМФ - 1 КМФ - 2 КМФ - 3 КМФ - 4 | 58,0 56,0 54,0 52,0 51,0 48,0 47,0 45,0 | 0,3 0,4 0,7 4,0 5,0 7,0 9,0 12,0 | 0,04 0,04 0,07 0,03 0,04 0,06 0,07 0,07 | 0,01 0,01 0,01 0,02 0,03 0,05 0,07 0,07 | 0,01 0,01 0,02 0,02 0,03 0,04 0,05 0,05 | 0,01 0,01 0,02 0,4 0,4 0,8 1,5 2,5 | 0,8 0,8 1,0 - - - - - | 2,0 4,5 5,0 - - - - - | 0,01 0,01 0,01 - - - - - |
Окислительный обжиг сульфидных молибденовых концентратов
В отличие от руд и концентратов, используемых в производстве большинства ферросплавов, молибденсодержащие концентраты содержат до 35%S, представленной в основном MоS2, сульфидами меди, железа и других элементов. Поэтому концентрат подвергают окислительному обжигу для перевода молибдена в кислородные соединения MoO2 и MoО3. Окисление серы сульфидных минералов происходит кислородом воздуха с образованием MoO3 по реакции:
|
|
MoS2 + 7/2O2 = MoO3 + 2SO2; G = -1123670 - 340,2Т
с последующим взаимодействием МоO3 с сульфидом молибдена
MoS2 +6MoO2 = 7MoO2 + 2SO2; G= 185580 + 204,3Т
Поскольку реакция окисления МоS2 до МоO3 экзотермична и сопровождается выделением большого количества тепла, внешний обогрев необходим только в конце процесса обжига, когда количество сульфида молибдена в продукте обжига становится невелико. Одновременно с этим протекают также процессы окисления сульфидов других металлов (FeS2, Cu2S,ZnS, NiS и другие.), присутствующие в качестве примесей в товарных молибденовых концентратах [15].Обжиг ведут в окислительной атмосфере в вертикальных восьмиподовых печах (рисунок 1.1) диаметром 6,8м при максимальной температуре на четвертом и пятом подах 680 - 750°С. Более высокие температуры могут привести к большим потерям молибдена в результате испарения МоO3. Суммарное давление парогазовых компонентов МonO3n(n = 3,4,5) достигает 100кПа при 1000°С. Остаточное содержание серы в концентрате не должно превышать 0,05 - 0,15%. Обожженный концентрат имеет сложный минералогический состав в результате образования промежуточных продуктов молибдена CaMoO4 и FeMoO4. Взаимодействие их с частично образующимся SO3 приводит к получению легкоплавких сернокислых солей Fe2(SO4)3, CuSO4и другие вследствие чего концентрат может оплавляться и комковаться. Наличие Na2O и K2O в концентратах может привести к образованию комплексов типа Na2O - хMoO3 и К2О ∙ хМоO3. Хотя с повышением концентрации оксидов щелочных металлов скорость испарения МоO3 резко уменьшается, однако вследствие низкой температуры плавления увеличивается вероятность окомкования концентрата. Производительность одной обжиговой печи составляет 950кг/ч обожженного концентрата. Согласно ТУ 14 - 5 - 88 - 77 концентрат молибденовый обожженный (КМО) должен иметь химический состав, приведенный в таблице 1.2.Кроме указанных в таблице 1.2 концентрат содержит: 14- 16% СаO, 2,5 - 3,2%FeO, 1,2 - 1,4%MgO, 0,6-0,8%Al2O3, 0,10 - 0,25% P, 0,5 - 0,15% W, а также небольшое (≤ 0,005% каждого) количество цветных металлов (Sb, Bi, Zn, Cd). Часть молибдена (< 10%) в обожженном концентрате представлена MoO2, а остальное -MoO3.
|
|
Таблица 1.2 - Химический состав, %, обожженного молибденового концентрата
Марка | Mo, % (не менее) | Р | S | As | Cu | SiO2 | Sn | C |
КМО-1 КМО-2 КМО-3 | 55 53 50 | 0,03 0,05 0,08 | 0,15 0,18 0,20 | 0,05 0,06 0,07 | 0,60 1,00 1,50 | 5,00 7,00 9,00 | 0,03 0,05 0,07 | 0,20 0,50 1,00 |
Рисунок 1.1 - Вертикальная многоподовая печь для обжига молибденита: 1 - кожух печи; 2 - вертикальный вращаящийся вал; 3 - коническая пара; 4 - гребни; 5 - лопатки
Дата добавления: 2018-08-06; просмотров: 1552; Мы поможем в написании вашей работы! |
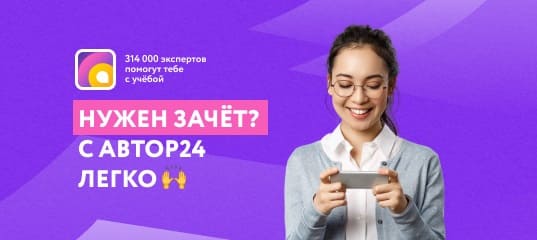
Мы поможем в написании ваших работ!