Свойства молибдена и его соединений
Молибден увеличивает твердость, глубину закалки стали, ковкость, стойкость против абразивного износа, карбид образование и улучшает литейные свойства. Введение 1% Мо позволяет повысить износоустойчивость стали, содержащей 12% Мn, и белого чугуна, содержащего 15% Сr (3% Мо). Малоуглеродистая сталь, в состав которой входит 1,6% Мn, 0,25% Мо и 0,06% Nb, обладает высокой прочностью, хорошей способностью к сварке; ее применяют для изготовления трубопроводов в северных районах. Около 60% инструментальной стали содержит молибден. Эта сталь превосходит по своим свойствам сталь, содержащую 18% W. Молибден в сочетании с хромом и никелем содержится в нержавеющей стали. Такая сталь дешевле и устойчива в галоидных средах. Около 90% всего молибдена (в виде ферромолибдена) используется для легирования стали. Молибден в чистом виде применяют в электротехнической и электровакуумной промышленности, электронике, для изготовления деталей сверхзвуковых самолетов и ракет, подвергающихся высокому нагреву, для получения сплавов с титаном, хромом, вольфрамом, танталом и ниобием. Для легирования стали можно использовать молибдат кальция СаМоО4 (60,57% МоО3; 23,30% СаО; 3,72% FeO; 0,79% Аl2О3; 9,70% SiO2; 0,2% S и 0,14% Р)[7]. В США для легирования быстрорежущей стали применяют молибден в виде расфасованной МоО3 (50%), ферромолибдена (35%) и брикетированной МоО3 (15%). Чистый молибден получают хлорированием его соединений, возгонкой МоОСl2 или МоСl5, их концен- трацией, затем выщелачиванием в растворе аммиака, выпариванием и прокалкой с получением МоО3 с последующим восстановлением водородом, прессованием и спеканием порошка молибдена и его очисткой методом зонной плавки. Свойства молибдена приведены ниже:
|
|
Атомный номер .................................. 42
Атомная масса..................................... 95,94
Плотность литого молибдена, кг/м3 …10,2
Температура, К:
Плавления............................................ 2883
Кипения ................................................ 5833
Теплота, кДж/г-атом: плавления…….7,37
Испарения………………………………536,3 44
Энтропия при 298К, Дж/(г-атом·К)…28,61
Для реакции молибдена с кремнием величины энтальпий образования приведены ниже:
3Мотв + Siтв = Mo3Siтв; ∆Gот = - 196090Дж/моль; 3Мотв + 2Siтв = Mo3Siтв; ∆Gот = - 132820Дж/моль;
Мотв + 2Siтв = Mo3Siтв; ∆Gот = - 131150Дж/моль;
Силициды устойчивы к кислотам и незначительно окисляются на воздухе. С алюминием молибден образует МоAl4. Большое значение в металлургии молибдена имеют его сульфиды. На заводы поступает концентрат, содержащий молибден в виде сульфидов. Такой концентрат подвергают окислительному обжигу. Для реакций молибдена с серой изменение энергии Гиббса (Дж/моль) приведено ниже:
|
|
Мотв + 2Sромб = MoS2тв; ∆Gот = - 241510 - 66,1Tlg Т + 23,4 · 103T2 - 1,04 · 105T-1 +206,3Т;
Мотв + 2Sромб = MoS3тв; ∆Gот = - 253240 + 33,9TlgТ -41T;
2Moтв + 3 /2S2тв = Mo2S3тв; ∆Gот= - 608390 + 262,7T.
По требованию потребителей ферромолибден марки ФМ1 может поставляться с содержанием молибдена не менее 60%, кремния не более 0,5% и серы не более 0,07%.
Молибденовые концентраты и требования, предъявляемые к их качеству.
В промышленных рудах молибден представлен в основном молибденитом MoS2 (59,95% Мо), вульфенитом РbМоO4 (26,15% Мо) и повеллитом СаМоО4 (47,98% Мо). Молибден принадлежит к числу редких металлов и его содержание в земной коре невелико. Рудами промышленного значения считаются даже такие, которые содержат 0,5% Мо и менее. Все руды подвергают обогащению по сложным технологическим схемам. Для получения 1т концентрата с 85 - 90% MoS2 перерабатывают 100 - 120т руды. Сырой (обогащенный) концентрат, содержащий до 30 - 35% серы, подвергают предварительному обжигу для удаления серы, а затем уже используют для выплавки ферромолибдена. Удаление серы из концентрата достигается окислительным обжигом в многопудовых печах[8]. При обжиге протекают реакции, которые можно разделить на четыре группы:
1) окисление молибденита кислородом до оксида:
|
|
MoS + 7 /2О2 = МоO3 + 2SO2; ∆Gот = - 957,41кДж/моль.
Изменение энергии Гиббса (Дж/моль) выражается уравнением:
∆Gот= - 1123670 - 340,2TIg + 351,3T,
Реакция окисления M0S2 является практически необратимой уже при 873К;
2) вторичное взаимодействие молибденита с оксидом молибдена с образованием низших оксидов:
MoS2 + 6МoО3 = 7МоО2 + 2SO2; ∆Gот= 185580 + 204,37 lgT - 915,5T;
3) окисление сульфидных минералов примесей (FeS2, Cu2S, ZnS, NiS);
4) взаимодействие оксида молибдена с кислородными соединениями других металлов с образованием молибдатов:
MeО + МоО3 = MeMoO4; МеСО3 + МоО3 = MeМоО4 + СО2.
В присутствии СаО образуется молибдат кальция СаМоO4 (при 673 - 773К) или молибдат магния MgMoO4. Упругость паров образующегося при обжиге оксида МоО3 при 1328К достигает 100кПа. В отличие от МоО3 низший оксид МоО3 при температурах обжига возгоняется незначительно. Сульфид молибдена (MeS2) возгоняется уже при 723К. Технология выплавки ферромолибдена. В качестве восстановителей молибдена применяют углерод, алюминий и кремний. Восстановление МоО3 углеродом может быть представлено реакцией
2 /3МоО3 + 2С = 2 /3Мо + 2СО.
Изменение энергии Гиббса (Дж/моль) выражается уравнением:
∆Gот = 209210 - 309,97Т,
|
|
Эндотермичность этого процесса обусловливает необходимость получения ферромолибдена в электропечи. Применение углерода как восстановителя приводит к получению ферромолибдена с содержанием углерода более высоким, чем это допускается стандартом. Поэтому в промышленной практике нашел применение внепечной силикотермический процесс получения ферромолибдена. При этом восстановление молибдена протекает по реакциям:
2 /3МоО3 + Si = 2 /3Мо + SiO2; ∆Gот = - 469870 + 65,6Т; МоО2 + Si = Мо + SiO2; ∆Gот = - 343040 + 19,52Т.
Восстановление оксидов молибденового концентрата кремнием характеризуется высокой экзотермичностью[9]. Присутствие в концентрате других оксидов приводит к снижению удельной теплоты процесса. Поэтому в шихту вводят небольшое количество алюминия, получая при этом необходимую для процесса термичность шихты. Восстановление оксидов молибдена алюминием может быть представлено следующими реакциями:
2 /3МоО3 + 4 /3Аl = 2 /3Мо + 2 /3Al2O3; ∆Gот = - 633400 +51,2Т;
МоО2 +4 /3АI = Мо + 2 /3Al2O3; ∆Gот = - 519140 - 51,53Т
При выплавке ферромолибдена шихта состоит из обожженного концентрата, измельченного ферросилиция ФС75, порошка алюминия (размером зерен ниже 2мм), железной руды и плавикового шпата. Целесообразнее в качестве восстановителя использовать ферросиликоалюминий с 8- 12% Al и не менее 77% (Si+Al) в виде крупки. Шихта (на одну плавку) включает 42 колоши. Состав колоши примерно следующий, кг:
Молибденовый концентрат…… 100
Ферросилиций (75%) ................. 30
Железная руда............................ 20
Стальная стружка……………….23
Плавиковый шпат ...................... 2
Алюминиевая крупка (втор. АI). 4,5
Шихту взвешивают и тщательно перемешивают порциями (семь колош), после чего подают в плавильную шахту. Плавку ведут с верхним запалом для улучшения условий осаждения металла. Продолжительность плавки составляет 25- 40минут. После окончания процесса шлак выдерживают в шахте в течение 40 -50 минут для более полного осаждения корольков ферромолибдена. Затем шлак выпускают через летку и гранулируют. Примерный химический состав отвального шлака приведен ниже, %: Мо 0,06 -0,17 Аl2О3 9 - 13 SiO2 62 - 68 СаО 6 - 8 FeO 7 - 11 MgO 1 - 3. После выпуска шлака шахту снимают с песочного «гнезда», и металлический блок оставляют в «гнезде» на 7 - 8 часов для затвердевания. Получаемый таким методом ферромолибден содержит 59,5 - 61,5% Мо; 0,15 -0,90% Si; 0,4 - 0,6% Сu; 0,04 - 0,05% Sb; 0,04 - 0,1% С и 0,06 - 0,08% S[10]. Применение подогретой до 150°С шихты приводит к сокращению длительности плавки (в 2 - 3,5 раза), но при этом увеличивается унос шихтовых материалов, а также возрастает извлечение молибдена и уменьшается на 35% расход алюминия с возможной заменой его ферросилицием. Стоимость молибденового концентрата очень высока, она составляет около 97,5% от себестоимости ферромолибдена. Поэтому снижению потерь молибдена при производстве ферромолибдена уделяется большое внимание. В процессе производства ферромолибдена получают отходы, которые могут быть использованы для повышения извлечения молибдена. Расход материалов и энергии с учетом использования отходов при производстве 1т ферромолибдена с содержанием 60% Мо приведен ниже:
Молибденовый концентрат (51% Мо), кг… 1191
Железная руда, кг......................................... 270
Стальная стружка, кг.................................... 230
Ферросилиций (75%), кг............................... 362 47
Алюминий (вторичный), кг .......................... 57
Известь, кг .................................................... 265
Плавиковый шпат, кг ................................... 30
Природный газ, м3.........................................380
Электроэнергия, кВт /ч................................ 800
Суммарное извлечение молибдена, %......... 98 - 99
При выплавке ферромолибдена возможны и другие составы шихты. Так, в зависимости от вида восстановителя могут быть применены следующие шихты (на 100кг молибденового концентрата с 60% молибдена),кг:
Восстановление алюминием
ФС75................................................ 31,5
Алюминиевая крупка (99,5% А1)…9,0
Стальная стружка ........................... 5 - 6
Окалина............................................ 29
Восстановление кремнием ФС75 21 - 23 СК 17 - 18
Окалина 16 - 18 Стальная стружка..18
Восстановление алюминием и кремнием
Ферросиликоалюминий (45% Si и 10% Аl)…. 65
Окалина............................................................. 35
Плавиковый шпат ............................................ 7
Ферромолибден силикотермического производства содержит допустимое стандартом количество примесей, однако в ряде случаев этот уровень загрязненности оказывается высоким, что вынуждает использовать при выплавке специальных сталей и сплавов чистый и дорогой молибден[11]. Чтобы получить ферромолибден требуемого качества, применяют концентраты повышенного качества; вакуумируют ферромолибден при 1873К и остаточном давлении 133мПа. При этом содержание висмута, цинка и свинца снижается до следов, меди на 70 - 90%, серы на 45 - 89%, углерода на 52 -69%; рафинируют ферромолибден окислительно-восстановительной плавкой. В результате обработки расплава (40% Мо) известково - железистыми шлаками достигается снижение концентрации фосфора и примесей цветных металлов. Наша ферросплавная промышленность выпускает хромомолибденовую лигатуру, применяемую вместо металлического молибдена и хрома для выплавки сплавов системы Ni - Сr с молибденом. Такие лигатуры получают алюминотермическим методом. В качестве шихты используют обожженный молибденовый концентрат или технический оксид молибдена, оксид хрома и первичный алюминий. Сплав обычно содержит 35 - 40% Мо; 0,9 - 1,0% W; 0,2 - 0,6% Аl; 0,02 - 0,06% С; 0,015 -0,02% S; 0,002 - 0,005% Р; 0,008 - 0,01% С; 0,9 - 1,0% Fe и остальное - хром. Сплав получают алюминотермическим методом из молибденового концентрата или технически чистого оксида МоО3. Фактический состав сплава: 48 - 53% Мо; 0,1 - 0,7% Si; 0,2 - 0,8% Fe; 6 - 10% Ti; 0,04 - 0,4% Сr и остальное - алюминий. Температура плавления сплава 1753 - 1813К. Лигатуру получают алюминотермическим методом из концентратов или оксидов II молибдена с применением первичного алюминия[12].
Дата добавления: 2018-08-06; просмотров: 943; Мы поможем в написании вашей работы! |
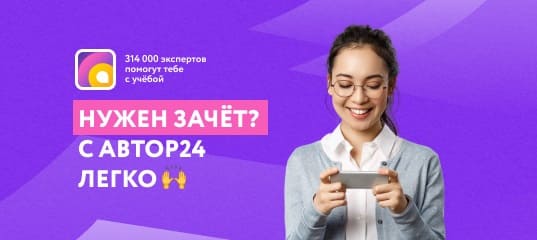
Мы поможем в написании ваших работ!