Практика термической обработки сталей
Отжиг сталей
Отжиг сталей - это отжиг II рода, то есть термическая обработка, при которой главными процессами являются аустенизация с последующим перлитным превращением (А-g-фаза, g → a + Fe3C - перлитное превращение).
Рис. 3.14. Температуры нагрева сталей для отжига второго рода: 1 – полный отжиг, 2 – неполный отжиг, 3 – сфероидизирующий отжиг, 4 – изотермический, низкий отжиг; 5 – нормализация
Различные виды отжига сталей отличаются способами охлаждения и степенью переохлаждения аустенита, а также положением температур нагрева относительно критических точек (рис. 3.14.).
1. Полный отжиг.
Данный вид отжига применяется для доэвтектоидных сталей. Для проведения полного отжига доэвтектоидную сталь нагревают до температуры, которая на 20 - 40°С выше А3. Охлаждение проводят с малой скоростью, чтобы аустенит распадался при небольшой степени переохлаждения. Структура доэвтектоидной стали после отжига состоит из избыточного феррита и перлита.
Цели полного отжига: в устранение пороков структуры, возникших при предыдущей обработке металла (литье, горячая деформация, сварка); смягчение стали перед обработкой резанием; уменьшение напряжений.
2. Неполный отжиг.
Неполный отжиг доэвтектоидной стали проводят при нагреве до температур выше A1, но ниже А3. При температуре неполного отжига избыточный феррит не исчезает. Этот отжиг применяют ограниченно, так как он не устраняет полностью пороки предыдущей обработки.
|
|
Цель неполного отжига - смягчение стали перед обработкой резанием. Неполный отжиг позволяет сэкономить время и снизить стоимость обработки.
3. Сфероидизирующий отжиг.
Для заэвтектоидных сталей полный отжиг с нагревом выше Асm (линия ES на диаграмме железо-карбид) вообще не используют, так как при медленном охлаждении после такого нагрева образуется грубая сетка вторичного цементита, ухудшающая механические свойства. К заэвтектоидным углеродистым сталям широко применяют отжиг с нагревом на 20 - 40°С выше A1 с последующим медленным охлаждением.
После такого нагрева в структуре стали остается большое количество вторичного цементита, который служит подложкой для образования цементита при распаде аустенита. В результате такого отжига образуется структура зернистого перлита (сфероид), а отсюда и название отжига - сфероидизирующий. Мелкие частицы цементита при температуре отжига образуются в результате деления цементитных пластин. Конечная структура зависит от скорости охлаждения и температуры нагрева при сфероидизирующем отжиге. Чем меньше скорость охлаждения, тем больших размеров вырастают глобули карбида при распаде аустенита. С повышением температуры отжига до 800-820°С твердость снижается из-за развития сфероидизации, а при дальнейшем увеличении температуры отжига твердость растет из-за увеличения количества пластинчатого перлита.
|
|
Цели сфероидизирующего отжига: улучшение обрабатываемости резанием (так как сталь со структурой зернистого перлита обладает наименьшей твердостью); получение зернистого перлита, который является оптимальной структурой перед закалкой (рис.3.15.).
Рис. 3.15. Микроструктура пластинчатого перлита (х2500) и зернистого перлита (х2000)после сфероидизирующего отжига
4. Изотермический отжиг, низкий отжиг.
Малая степень переохлаждения аустенита, необходимая при отжиге может быть получена не только при медленном непрерывном охлаждении но и при изотермической выдержке в интервале перлитного превращения. Данный вид термической обработки называется изотермическим отжигом. Этот вид отжига рассматривался ранее в разделе изотермические превращения в стали. После нагрева выше температуры А3 (g-область), сталь ускоренно охлаждают до температуры изотермической выдержки, которая находится ниже температуры A1. Время изотермической выдержки должно быть несколько больше времени полного изотермического превращения аустенита. Это время определяется по С-образной диаграмме. Основное преимущество изотермического отжига перед полным - это получение более однородной структуры, так как при изотермической выдержке температура по сечению изделия выравнивается и превращение по всему объему стали происходит при одинаковой степени переохлаждения.
|
|
При этих же температурах можно проводить низкий отжиг, который соответствует отжигу I рода. Он используется если исходная структура «хорошая» и нет необходимости в фазовой перекристаллизации а требуется снизить только внутренние напряжения в стали.
5. Нормализация.
При нормализации сталь нагревают до температур на 30 -50°С выше А3 или Асm и охлаждают на воздухе. Ускоренное охлаждение обусловливает несколько большее переохлаждение аустенита по сравнению с другими видами отжига, поэтому в структуре стали образуется сорбит.
Под нормализацией понимают такую термообработку стали, при которой охлаждение на воздухе приводит к распаду аустенита в температурном интервале перлитного превращения. Нормализацию применяют как промежуточную операцию и для улучшения структуры перед закалкой и для смягчения стали перед обработкой резанием. Нормализация имеет такое же назначение, как и полный отжиг, а так как нормализация выгоднее полного отжига (для данного вида обработки требуется меньше времени), то ее часто предпочитают полному отжигу. Однако нормализация не всегда может заменить полный отжиг как обработку для смягчения стали.
|
|
6. Патентирование.
Сталь нагревают выше температуры А3, а затем переносят в ванну с температурой 450 - 550°С. После обработки сталь имеет структуру троостит (малое межпластинчатое расстояние), избыточный феррит или цементит не успевает выделиться.
Целью данной обработки является получение высокой прочности стали, так как границы между пластинами феррита и цементита представляют собой непроницаемые барьеры для дислокаций. В основном применяется при производстве высокопрочной проволоки.
Закалка сталей
Температура закалки для сталей большинства марок определяется положением критических точек А1 (иногда Ас1) и А3 (иногда Ас3).
Для углеродистых сталей температуру закалки можно определить по диаграмме железо-углерод (рис. 3.16.). Обычно для доэвтектоидной стали она должна быть на 30-500С выше А3, а для заэвтектоидной стали – на 30-500С выше А1.
Рис. 3.16. Интервал закалочных температур углеродистых сталей.
При закалке доэвтекоидной стали с температуры выше А1, но ниже А3, в структуре наряду с мартенситом сохраняется часть феррита, который снижает твердость в закаленном состоянии и ухудшает механические свойства после отпуска. Такая закалка называется неполной.
Для заэвтектоидных сталей оптимальная температура закалки лежит в интервале между А1, и А3 и теоретически является неполной.
Наличие в структуре закаленной стали избыточного цементита полезно во многих отношениях. Например, включения избыточного цементита повышают износоустойчивость стали. Нагрев же выше А3 опасен и не нужен, т.к. он не превышает твердости, наоборот твердость даже несколько падает вследствие растворения избыточного цементита и увеличения остаточного аустенита; при таком нагреве растет зерно аустенита, увеличивается возможность возникновения больших закалочных напряжений, интенсивнее обезуглероживается сталь с поверхности.
Таким образом, оптимальной является закалка доэвтектоидной стали от температуры на 30-500С выше А3, а для заэвтектоидной стали на 30-500С выше А1.
Повышение температуры закалки выше этих температур и вызванный этим рост зерна аустенита обнаруживается в первую очередь в получении более грубой и крупноигольчатой структуры мартенсита, или грубого крупнокристаллического излома. Следствием такого строения является низкая вязкость.
Наследственная склонность к росту зерен аустенита зависит от нескольких факторов и, прежде всего, - от условий раскисления стали при выплавке. Одна и та же сталь, в зависимости, от способа выплавки может быть наследственно мелко- или крупнозернистой. Так, сталь, раскисленная ферромарганцем и ферросилицием, является наследственно крупнозернистой. Если сталь дополнительно раскислить алюминием, она становится наследственно мелкозернистой. Причиной изменения наследственной склонности является наличие дисперсных частиц нитридов алюминия, которые располагаются на границах зерен и служат барьерами для роста зерна. При достаточно высокой температуре частицы нитридов алюминия растворяются в аустените, и зерна начинают бурно расти.
Легирующие элементы оказывают влияние на наследственную склонность стали к росту зерен. В сталях, легированных титаном, ниобием, ванадием, роль барьеров выполняют частицы карбидов, трудно растворимые в аустените при нагреве.
Состав аустенита также оказывает влияние на наследственную склонность стали к росту зерна. Легирующие элементы в большинстве случаев замедляют диффузионные процессы при нагреве и задерживают рост зерен аустенита. Наиболее эффективно действуют вольфрам и молибден. Однако есть элементы, способствующие росту зерна, к ним относятся марганец и бор.
Разделение сталей на наследственно крупно- и мелкозернистые не означает, что данная сталь всегда будет иметь крупное или мелкое аустенитное зерно, а лишь указывает на склонность зерен к росту при высоких температурах. Знание наследственной склонности необходимо для правильного выбора стали и режима ее обработки.
Отпуск сталей
Твердость отпущенной стали определяется несколькими факторами: уменьшение тетрагональности решетки, степени фазового наклепа и укрупнение карбидных частиц вызывают снижение твердости; выделение когерентных кристаллов e-карбида и дисперсных кристаллов специальных карбидов, а также распад остаточного аустенита способствуют ее повышению.
в конструкционных сталях, в которых количество углерода обычно не превышает 0,7%, твердость уменьшается непрерывно, однако ее снижение невелико до 100 - 120ос. в инструментальных сталях с более высоким содержанием углерода эффект твердения вследствие выделения e-карбида преобладает, поэтому твердость при отпуске до 100- 120ОС несколько увеличивается. Изменение твердости углеродистых сталей в интервале температур IIпревращения в большой степени зависит от количества остаточного аустенита; например, в стали с содержанием 1,2%С в интервале 200- 300ос интенсивность снижения твердости уменьшается (рис. 3.17.).
Рис. 3.17. Изменение твердости закаленных углеродистых сталей при отпуске
Изменение структуры при отпуске вызывает изменение механических свойств закаленной стали. При температурах отпуска до 200ОС в результате незначительного распада мартенсита и выделения карбидов уменьшаются внутренние напряжения и несколько возрастает вязкость, уменьшается склонность к хрупкому разрушению, но сохраняется высокая твердость (рис. 3.18).
Рис. 3.18. Зависимость механических свойств закаленной стали 40 от температуры отпуска
сповышением температуры отпуска твердость и прочность снижаются, а пластичность и вязкость повышаются. Прочность феррито-цементитных смесей (перлита, сорбита и троостита), получаемых при отпуске, объясняют наличием включений цементита, которые препятствуют сдвигу по плоскостям скольжения при действии внешних сил. Чем больше включений цементита и чем меньше их размер, тем сильнее они препятствуют сдвигу по плоскостям скольжения. Поэтому троостит, в котором частицы цементита наиболее мелкие, имеет большую твердость и прочность по сравнению с сорбитом, а перлит, содержащий наиболее крупные включения цементита, - наименьшую прочность и твердость.
Поэтому в зависимости от требуемого комплекса свойств закаленные стали подвергают низкому (до 200ОС), среднему (при 400-500ос) и высокому (при 550-650ос), отпуску.
Низкотемпературный (низкий)отпуск (150-200°) применяют в тех случаях, когда требуется снизить хрупкость, но сохранить высокую твердость закаленной на мартенсит стали. При этих температурах происходит распад мартенсита, в результате которого однородная структура закалки - мартенсит - перейдет в неоднородную структуру - мартенсит отпущенный, состоящую из менее пересыщенного углеродом a-раствора и тончайших пластинок промежуточного метастабильного цементита FexC в когерентной форме. Вследствие значительно уменьшается хрупкость стали.
Распад остаточного аустенита происходит при температурах нагрева 200-300°С. В результате этого превращения при отпуске, когда вновь образуется мартенсит из остаточного аустенита, происходит повышение твердости и хрупкости стали. Поэтому отпуск углеродистых сталей в интервале температур 200-3000С не применяется, он вызывает отпускную хрупкость I рода.
Средний отпуск (350-450°С) применяют тогда, когда необходимо сочетание высокой прочности и упругости с достаточной вязкостью. При этих температурах нагрева произойдет полное выделение углерода из мартенсита и образование стабильного цементита Fe3C. В результате полного распада мартенсита образуется троостит отпуска - высокодисперсная смесь феррита и цементита. Среднему отпуску подвергают пружины и рессоры из углеродистых конструкционных сталей с содержанием углерода 0,65-0,75%.
Высокотемпературный (высокий)отпуск (550-650°)применяют к изделиям, которые должны иметь высокую вязкость и, вместе с тем, достаточную прочность. При высоких температурах отпуска произойдет коагуляция и сфероидизация цементитных частиц. Образующаяся при этом дисперсная феррито-цементитная смесь имеет зернистую форму цементита и называется сорбитом отпуска. Высокому отпуску подвергают детали ответственного назначения из конструкционных сталей, испытывающие при эксплуатации ударные и знакопеременные нагрузки. Термическая обработка стали, состоящая из закалки и высокого отпуска, называется улучшением, а стали называют улучшаемыми.
Химико-термическая обработка сталей.
Химико-термической обработкой называют поверхностное насыщение стали соответствующими элементами (например, углеродом, азотом, алюминием, хромом и др.) путем его диффузии в атомарном состоянии из внешней среды при высокой температуре. Химико-термическая обработка заключается в нагреве изделия до заданной температуры в твердой, газовой или жидкой среде, легко выделяющей диффундирующий элемент в атомарном состоянии, выдержке при этой температуре и последующем охлаждении. В отличие от термической обработки химико-термическая обработка изменяет не только структуру, но и химический состав поверхностных слоев, что позволяет в более широких пределах менять свойства стали.
Процесс химико-термической обработки состоит из трех элементарных стадий: 1) выделения диффундирующего элемента в атомарном состоянии в результате реакций, протекающих в насыщающей среде; 2) контактирования атомов диффундирующего элемента с поверхностью стального изделия и проникновения (растворения) в решетку железа (адсорбция); 3) диффузии атомов насыщающего элемента в глубь металла. Скорость диффузии атомов насыщающего элемента в решетку железа неодинакова и зависит от состава и строения образующих фаз. При насыщении углеродом или азотом, составляющим с железом твердые растворы внедрения, диффузия протекает быстрее, чем при насыщении металлами, образующими твердые растворы замещения.
Поэтому при диффузионном насыщении металлами процесс ведут при более высоких температурах и длительно, несмотря на это, получают меньшую толщину слоя, чем при насыщении азотом и особенно углеродом (рис. 3.19).
Рис. 3.19. Схема зависимости толщины диффузионного слоя х от продолжительности насыщения (а) и температуры (б): 1 - диффузия элементов, образующих твердый раствор замещения (Сr, Al, Si и др.); 2- диффузия элементов, образующих твердый раствор внедрения (с, N)
Цементацией называется процесс насыщения поверхностного слоя стали углеродом. Различают два основных вида цементации: твердыми углеродсодержащими смесями (карбюризаторами) и газовую.
Цементацию с последующей закалкой и отпуском применяют для повышения работоспособности деталей машин (всевозможные шестерни, зубчатые муфты и втулки, пальцы, втулки и ролики шлепперов и т.д.), испытывающих в процессе эксплуатации статические, динамические и переменные нагрузки и подверженных изнашиванию.
Для цементации обычно используют низкоуглеродистые стали (0,1-0,18%С). Для крупногабаритных деталей применяют стали с более высоким содержанием углерода (0,2-0,3 %). Выбор таких сталей необходим для того, чтобы сердцевина изделия, не насыщающаяся углеродом при цементации, сохраняла высокую вязкость после закалки. Цементованный слой имеет переменную концентрацию углерода по глубине, убывающей от поверхности к сердцевине детали. В связи с этим после медленного охлаждения в структуре цементованного слоя можно различить (от поверхности к сердцевине) три зоны: заэвтектоидную, состоящую из перлита и вторичного цементита, образующего сетку по бывшему зерну аустенита; эвтектоидную из одного пластинчатого перлита и доэвтектоидную зону из перелита и феррита.
Концентрация углерода в поверхностном слое должна составлять 0,8-1,0%С. Для получения максимального сопротивления контактной усталости содержание углерода может быть повышено до 1,1-1,2%С. Более высокая концентрация углерода вызывает ухудшение механических свойств цементуемого изделия.
Цементацию выполняют при 930-950ОС. продолжительность цементации для получения слоя толщиной 0,7-1,5 мм при 930ОС в муфельных (безмуфельных) печах непрерывного действия составляет 6-12 ч, а в шахтных 3-10 ч. термическая обработка стали после цементации; свойства цeментованных деталей. окончательные свойства цементованные изделия получают в результате термической обработки; выполняемой после цементации. Этой обработкой можно исправить структуру и измельчить зерно сердцевины и цементованного слоя неизбежно увеличивающихся во время длительной выдержки при высокой температуре цементации. Различают следующие основные вида цементации: твердыми углеродсодержащими смесями (карбюризаторами), газовую цементацию.
Цементацию с последующей закалкой и отпуском применяют для повышения работоспособности деталей машин (шестерен, зубчатых колес, втулок). Иногда термическая обработка состоит из двойной закалки и отпуска. Первую закалку (или нормализацию) с нагревом до 880-900ОС назначают для исправления структуры сердцевины. Кроме того, при нагреве в поверхностном слое в аустените растворяется цементитная сетка, которая при быстром охлаждении вновь не образуется. Вторую закалку проводят с нагревом до 760-780ОС для устранения перегрева цементованного слоя и придания ему высокой твердости. Заключительной операцией термической обработки цементованных изделий во всех случаях является низкий отпуск при 160-180ОС, переводящий мартенсит закалки в поверхностном слое в отпущенный мартенсит. Твердость поверхностного слоя для углеродистой стали составляет НRC 60-64, а для легированной НRC 58-61. Твердость сердцевины обычно составляет нRC 30-40.
Рис.3.20. Диаграмма Fe-N
Aзoтированием называют процесс диффузионного насыщения поверхностного слоя стали азотом при нагреве ее в аммиаке. Азотирование повышает твердость поверхностного слоя, его износостойкость, предел выносливости и сопротивление коррозии в таких средах, как воздух, вода, пар и т. д. Твердость азотированного слоя заметно выше, чем цементуемого слоя. Азотирование широко применяется для зубчатых колес, цилиндров мощных двигателей, многих деталей станков и других изделий. Азотирование изделий сложной конфигурации рекомендуется выполнять при 500-5200С. Продолжительность процесса зависит от требуемой толщины азотированного слоя. Чем выше температура азотирования, тем ниже твердость азотированного слоя и больше толщина слоя. При азотировании желательно иметь слой толщиной 0,3-0,6 мм. Тогда процесс азотирования при 500-5200С продолжается 24-90 ч. Структуру азотированного слоя можно изучать, если внимательно рассмотреть диаграмму железо- азот (рис. 3.20.).
В этой системе возможно образование следующих фаз a - азотистый феррит, содержащий от 0,1 до 0,01 % N, g - азотистый аустенит, существующий до как равновесная фаза лишь выше эвтектоидной температуры (5910С), g’ – нитрид Fe4N, e - нитрид Fe2N. В азотированном слое присутствуют различные азотистые фазы в соответствии с диаграммой и температурой процесса. При температуре азотирования низе эвтектоидной азотированный слой состоит из трех фаз: e, g’ и a. При более высокой температуре 600-6500С образуются все 4 фазы (рис. 3.21.). При медленном охлаждении с этой температуры g-фаза распадается на эвтектоид (темный слой на рис.), так называемый браунит, при быстром охлаждении образуется мартенсит. Распределение азота по глубине слоя имеет скачкообразный характер вследствие отсутствия переходных двухфазных слоев. На практике осуществляют азотирование легированных сталей, наличие легирующих элементов существенно не нарушает кинетику образования азотированного слоя. Азотированию подвергают среднеуглеродистые легированные стали, которые приобретают особо высокую твердость (HV=1200 ) и износостойкость. Например, для повышения твердости наиболее часто азотируют сталь 35ХМЮА.
Рис. 3.21. Структура азотированного слоя в стали (слева на право: азотирование ниже эвтектоидной температуры, азотирование выше эвтектоидной температуры – быстрое охлаждение, азотирование выше эвтектоидной температуры – медленное охлаждение)
Азотирование также применяется и для некоторых цветных сплавов, например, титановых. Структура азотированного титанового сплава будет определяться системой титан-азот.
Достаточно широко применяется нитроцементация – насыщение поверхности стали азотом и углеродом одновременно в газовой среде.
Насыщение железа (стали) металлами, а также кремнием и бором повышает жаростойкость, коррозионную стойкость, износостойкость и твердость.
Поверхностное насыщение стали металлами, а также кремнием и бором, можно проводить при 900-1050ОС упаковкой изделий в соответствующие порошкообразные смеси (обычно фeppocплaвы и 0,5-5% NH4Cl), погружением их в расплавленный металл, если диффундирующий элемент имеет невысокую температуру плавления (например, цинк и алюминий), или насыщением из газовой среды.
Алитированием называется насыщение поверхности стали алюминием. в результате алитирования сталь приобретает высокую окалиностойкость (до 850-900ОС), так как в процессе нагрева на поверхности алитированных изделий образуется плотная пленка Оксида алюминия Al2O3, предохраняющая металл от окисления. Алитированию подвергают детали, работающие при высоких температурах.
Хромирование стали, т. е. насыщение поверхности стальных изделий хромом, обеспечивает повышенную устойчивость против газовой коррозии (окалиностойкость) до 800ОС, высокую коррозионную стойкость в таких средах, как вода, морская вода и азотная кислота, что повышает твердость и износостойкость. Хромированию подвергают детали, работающие на износ в агрессивных средах.
Цинкование, т.е. насыщение поверхностного слоя цинком, применяют для повышения коррозионной стойкости стали в атмосфере, пресной воде, бензине.
Силицирование – это насыщение поверхности стали кремнием. В результате силицирования сталь приобретает высокую коррозионную стойкость в морской воде, азотной, серной и соляной кислотах, а также повышенную устойчивость против износа. Силицированию подвергают детали, применяемые в оборудовании химической, бумажной, нефтяной промышленности.
Борирование, т.е. насыщение поверхностного слоя бором, создает высокую твердость (HV 1800-2000), износостойкость и устойчивость против коррозии в различных средах. Бoрированный слой на поверхности состоит из борида FeB и ниже из борида Fe2B и a-твердого раствора. Борирование применяют для повышения износостойкости втулок грязевых нефтяных насосов, вытяжных, гибочных и формовочных штампов, деталей пресс-форм, машин для литья под давлением и др. Стойкость указанных деталей возрастает в 2-6 раз.
Дата добавления: 2018-08-06; просмотров: 325; Мы поможем в написании вашей работы! |
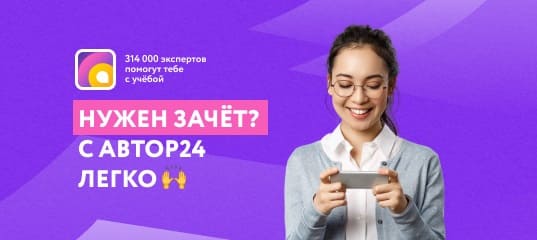
Мы поможем в написании ваших работ!