Рентгеноспектральный микроанализ (РСМА)
Рентгеноспектральный микроанализ − на взаимодействии пучка электронов с приповерхностным участком образца на глубине нескольких микрон
Качественный РМСА - (какие) данные о составе фаз, частиц, образца в целом
Количественный РМСА - (% содержание) данные о составе фаз, частиц, микроучастков.
Методами рентгеноспектрального анализа можно определять концентрацию любых элементов от бериллия (Be) или бора (B) в диапазоне концентраций от сотых долей весового процента до 100%.
Исследования при РМСА можно проводить
− по основным точкам - количественное определение каждого элемента.
− сканированием вдоль прямой - полуколичественные данные об изменении концентрации определяемых элементов в диффузионных зонах.
− сканированием по площади - позволяет получить наглядные фотографии распределения элементов на выбранном участке шлифа с увеличениями до 2.000 крат
![]() |
Сканирование образца производиться по площади. В виде дифрактограммы представлен спектр поэлементного состава изучаемого образца. В таблице вынесено процентное содержание каждого элемента. Суммарное содержание элементов = 100%. (WT% − массовый %; AT% − атомный %). |
Рис. 2. Рентгеновский спектр и состав образца |
Слайд_6
Физические методы исследования
Термический анализ - основан на регистрации тепловых эффектов превращений, протекающих в исследуемом образце в условиях программируемого изменения температуры (рис. 3).
|
|
Качественный ТА − для построения диаграмм фазовых равновесий.
Количественный ТА − для определения теплофизических характеристик (энтальпии, энтропии).
![]() | Температурная программа может включать: - нагревание, - охлаждение с постоянной скоростью, - выдерживание при t=const (изотерма) - комбинацию этих режимов.
На термограммах перегибы и остановки на кривых указывают на температуру фазовых превращений. Экзотермическая реакция - выделение теплоты Эндотермическая реакция - поглощение теплоты |
Рис. 3. Термограммы нагрева (1) и охлаждения (2) сплава кюрия с алюминием (ТА) |
Различают следующие методы термического анализа (отличаются измеряемым свойством):
1. Дифференциально-термический анализ (ДТА) - температура
2. Дифференциально-сканирующая калориметрия (ДСК) - теплота
3. Термогравиметрический анализ (ТГА) - масса
4. Термомеханический анализ (ТМА) - линейный размер
5. Дилатометрия (Дил) - объём
6. Визуально-политермический анализ (ВПА) - форма
7. Термомагнитный анализ (ТМА) - магнитные свойства
Слайд_7
Методы испытания
Механические испытания
|
|
Под механическими свойствами понимают совокупность свойств, характеризующих сопротивление металла действию приложенных к нему внешних механических сил (нагрузок).
Механические испытания в зависимости от характера изменения нагрузки и времени её действия разделяют на:
- Статические испытания - плавно возрастающая нагрузка (растяжение, сжатие, твердость);
- Динамические испытания - резко действующая нагрузка, возрастающая от нуля до max с большой скоростью (ударный изгиб);
- Испытания долговечностью - многократно прикладываемая нагрузка, (усталостные испытания).
- Длительные высокотемпературные испытания − одновременное действие нагрузки и температуры (ползучесть, длительную прочность).
- Трибологические испытания − это испытание образцов или деталей на износ, износостойкость (испытания на трение).
Слайд_8
Статические испытания
Твердость − это способность металлов и сплавов сопротивляться действию пластической деформации при контактном приложении нагрузки.
Из всех видов механических испытаний твердость определяют чаще всего. Это объясняется простотой и высокой производительностью метода измерения твердости. А также тем, что испытание можно проводить на самом изделии (полуфабрикате или детали), не вызывая его повреждения.
|
|
Для получения достоверной твёрдости поверхность образца или детали должна быть плоскопараллельной и без окалины и грубых дефектов. Расстояние между соседними отпечатками и до края образца должно быть не менее 3 мм.
Основными методами определения твердости металлов и сплавов являются методы Бринелля, Роквелла и Виккерса (показать фото). Различаются они видом и материалом наконечника и размером прилагаемой нагрузки.
Измерение твёрдости данными методами заключаются во внедрении в поверхность испытываемого металла стандартных наконечников из твердых недеформирующихся материалов под действием статических нагрузок. Получаемые значения выражаются числами твердости в различных шкалах.
Вдавливание осуществляется под действием двух последовательно прилагаемых нагрузок
- предварительной (P0=98н=10кгс) | Þ общая нагрузка Р=Р0+Р1 |
- основной (P1) |
![]() | Рис. 4. Схема определения твердости: а) по Бринеллю; б) по Роквеллу; в) по Виккерсу |
Слайд_9
Метод | Индентор | Метод измерения | Нагрузка | Шкала | Тип материала | Пример | ||
Бринеллю (рис. 3а) | Стальной шарик (D= 5мм, 10мм) | Замер диаметра от отпечатка (d,мм) Перевод в числа твёрдости по табл. | для D=10 мм Р=30.000 Н (3.000 кгс) для D=5 мм Р=7500 Н (750 кгс) | НВ | Металлы с твёрдостью не более 450НВ | НВ=350 кгс/мм2 НВ=3600 МПа | ||
Роквеллу
(рис. 3б) | Алмазный конус с углом при вершине 120°. | Непосредственно значения твёрдости | Р=1470н (150кгс) | «с» | Твердые материалы (закаленные стали) | 58 HRC | ||
Р=588н (60кгс) | «А» | Очень твердые материалы (твердые сплавы) | 115 HRА | |||||
Стальной закаленный шарик (D=1,588мм) | Р=980н (100кгс) | «В» | Нетвердые металлы (бронзы, латуни). | 90 HRВ | ||||
Виккерс (рис. 3в) | Четырехгранная алмазная пирамида с квадратным основанием и углом при вершине 136°. | Замер длины двух диагоналей от отпечатка (l, мкм). Перевод в числа твёрдости по табл. | Р= 49 − 1176 н (5 - 120кгс). | HV | Твёрдость поверхности | HV=400 кгс/мм2 HV=3200 МПа). | ||
Микро- твёрдость (рис. 3в) | Р= 0,05 − 4,9 н (5 - 500 кгс). | HV0,5 | Твердость тонких поверхностных слоев, покрытий, отдельных составл. | HV0,5=1810 МПа |
Слайд_10
В производственных условиях иногда используют (массивная конструкция, сложная конфигурация изделия) другие методы определения твердости.
− метод ударного отпечатка,
− метод упругого отскока бойка (метод Шора),
− Ультрозвуковой метод определения твёрдости
Как правило, применяются переносной прибор. Он снабженн трубкой, внутри которой может свободно падать боек определенной массы с алмазным наконечником в виде конуса. Твердость оценивается в условных единицах (HSD), пропорциональных высоте отскока бойка. Чем мягче испытуемый материал, тем меньше будет высота отскока; так как большая энергии удара будет расходоваться на остаточную деформацию материала детали.
Слайд_11
Испытание на растяжение (ГОСТ 1497-73) - позволяет по результатам одного опыта определить несколько механических свойств:
- прочность - сопротивление металла деформации,
- пластичность - способность к остаточной деформации без разрушения.
При испытании на растяжение образец растягивается двумя равными и противоположными силами, приложенными к его оси. Используются стандартные образцы - цилиндрические Æ³3 мм и плоские h³0,5 мм.
Перед испытанием на образцы слабыми рисками наносят расчетную длину (l0), которая зависит от площади поперечного сечения (F0).
После завершения испытаний измеряют конечную длину расчетной части образца (lк) и рассчитывают конечную площадь поперечного сечения образца (Fк). Точка k на диаграмме растяжения соответствует моменту разрушения образца.
По итогам испытаний строят первичную диаграмму растяжения в координатах «Нагрузка (P) - деформация (удлинение − Dl)» (рис. 6). Характер диаграммы растяжения зависит от свойств испытуемого материала.
Для большинства пластичных материалов характерна диаграмма растяжения с постепенным переходом от упругой в пластическую область. Для некоторых пластичных материалов (например, низкоуглеродистая сталь) свойственна диаграмма растяжения с переходом в пластическую область в виде площадки текучести. На диаграммах растяжения хрупких материалов участок, отвечающий пластической деформации отсутствует (образец разрывается без образования шейки).
![]() |
|
![]() | |
Образцы для испытания на растяжение:
а - круглый цилиндрический; б – плоский
(длина образца ![]() ![]() | Рис. 5. Характерные точки на диаграмме растяжения, по которым рассчитывают характеристики прочности |
На диаграмме растяжения (рис. 4) отмечены характерные точки, по которым определяют механические свойства металла:
Слайд_12
На плакате последовательно, по щелчку, появляются свойства, которые можно определить при испытаниях на растяжение. Зачитываю только название свойства и соответствующий ему отрезок на диаграмме растяжения.
1. Предел пропорциональности (sпц), − это наибольшее напряжение, до которого деформация прямо пропорциональна нагрузке (отрезок ОP);
2. Предел упругости (sупр) − наибольшее напряжение, до которого остаточная деформация при разгрузке не обнаруживается (отрезок Оe);
3.Физический предел текучести (sТ) − наименьшее напряжение, при котором образец деформируется без заметного увеличения нагрузки (площадка SS');
4. Условный предел текучести (s0,2) − напряжение, при котором остаточное удлинение достигает 0,2% от расчетной длины образца (точка S') (в случае если на диаграмме нет площадки текучести);
5. Предел прочности (временное сопротивление разрыву − (sв) − максимальная нагрузка, которую выдерживает образец во время испытания (точка В)
6. Относительное удлинение образца (d) − это отношение приращения расчетной длины образца после разрыва к первоначальной расчетной длине, выраженной в процентах ;
7. Относительное сужение образца (y) − это отношение уменьшения площади поперечного сечения образца к первоначальной площади, выраженное в процентах ,
Слайд_13
Динамические испытания
Детали машин в процессе эксплуатации испытывают не только статические, но и динамические нагрузки, под действием которых может произойти их разрушение. Поэтому необходимо знать, насколько хорошо материал сопротивляется таким нагрузкам.
Испытания на удар с изгибом (ГОСТ 9454-78) − проводят на маятниковом копре путем разрушения стандартного образца квадратного сечения с надрезом U-, v-, т-образной формы (рис).
![]() | U- образный надрез - ширина и глубина 2 мм, Rскругл=1 мм. v-образный надрез - с углом при вершине 45°, Rскругл=0,25 мм. т-образный надрез - с усталостной трещиной Копер имеет тяжелый маятник, который свободно качается вокруг своей оси. Образец устанавливают на пути падения маятника на две опоры копра надрезом в сторону, противоположную удару маятника. Падая, маятник изгибает образец и ломает его. |
Образец для испытания на ударный изгиб |
ударная вязкость (КС) - это работа, израсходованная на ударный излом образца, отнесенная к площади поперечного сечения образца в месте надреза: КС=K/F (Дж/м2, Дж/см2)
Для определения трещинностойкости высокопрочного материала проводят испытания на вязкость разрушения (KIc, МПа´м1/2), которая характеризует сопротивление развития вязкой трещины.
Испытания на долговечность
Многие детали машин работают с вибрацией. При этом они испытывают многократное действие изменяющихся по величине или величине и направлению напряжений. За свою «жизнь» материал детали должен выдерживать большое число таких перемен или циклов. Например, за время своей работы паровозная ось испытывает 400 миллионов циклов.
Испытания на усталость. В результате действия циклических напряжений металл как будто «устает», прочность его снижается и наступает разрушение детали. Данное явление называется усталостью, а сопротивление усталости - выносливостью. Разрушение от усталости происходит всегда внезапно вследствие накопления металлом необратимых изменений, которые приводят к возникновению микроскопических трещин - трещин усталости.
Предел выносливости - наибольшее напряжение, которое может выдержать материал без разрушения при произвольно большом числе циклов нагрузки.
Для определения предела выносливости испытывают серию одинаковых образцов.
Первый образец нагружают так, чтобы максимальное напряжение заведомо превышало предел выносливости.
Для остальных образцов нагрузку постепенно снижают.
Испытания проводят до разрушения образцов и фиксируют число циклов до разрушения.
По результатам испытаний строят кривую усталости в координатах «Max напряжение (sмах) - число циклов до разрушения (N)» (рис. 6)
![]() |
База испытания (sr), наибольшее напряжение, которое материал выдерживает, не разрушаясь в течение определенного числа циклов нагружения. Это число циклов называют. Стали sr = 10 млн. циклов Цветные металлы sr = 20-100 млн. циклов |
Рис. 6. Кривая усталости: I – квазистатическое разрушение; II – малоцикловое разрушение; III – многоцикловое усталостное разрушение |
Слайд_14
Дата добавления: 2018-08-06; просмотров: 649; Мы поможем в написании вашей работы! |
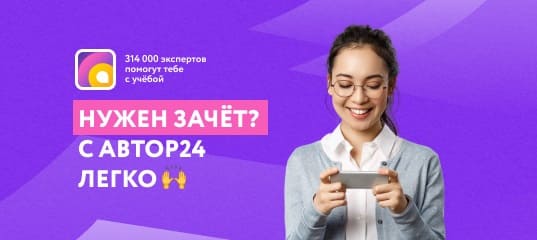
Мы поможем в написании ваших работ!