Технологическая характеристика производства меди и цинка.
Медь обладает высокой электро- и теплопроводностью, пластичностью, хорошей коррозионной стойкостью, способностью сплавляться со многими металлами, хорошие технологические свойства – ковкость и обрабатываемость режущими инструментами. Самый распространённый сплав с использованием меди – латунь – сплав меди и цинка. Другой распространённый сплав – бронза – сплав меди и олова (классическая бронза). К белым сплавам меди относятся мельхиор (сплав меди и никеля) и нейзельбер («новое серебро»; сплав меди, никеля и цинка).
Около 50% добываемой меди используется в электротехнике, 25% - в машиностроении и как детали для транспортных средств и около 20% - в строительстве.
В основном, медь добывают из сульфидных руд. Самая распространённая медная руда – медный колчедан (халькопирит), также используются медный блеск (халькозин), ковилин. Из сульфидных руд добывается до 90% меди. Остальная медь добывается из окисленных руд – куприта, азурита и малахита.
В халькопирите содержится 0,8-1,5% меди. Стадии переработки меди:
1. Дробление и измельчение.
2. Обогащение. Получение медного концентрата, содержание меди в котором составляет 10-30%. В процессе обогащения также получаются хвосты – пустая порода.
3. Обжиг. Удаление серы. Проводится в специальных печах, в которых сера выводится в среде диоксида серы, который можно использовать для производства серной кислоты. Продукт обжига называется огарком.
|
|
4. Плавка на штейн. Из огарка с добавлением топлива и флюсов удаляется ещё больше серы. Флюсы нужны для удаления железа в виде шлака. В результате получается штейн – сплав сульфидов меди и железа.
5. Конвертирование (продувка в конверторе). Используется воздух для удаления серы и флюсы для удаления железа. Продувка производится в течение суток. В результате получается черновая медь, содержание меди в которой около 96%.
6. Электролитическое рафинирование. Реакция проводится в электролизёрах. В результате получается чистая медь, с содержанием меди до 99,99%. Побочным продуктом является шлак, который отправляется на извлечение редких и благородных металлов.
На 1 т готовой меди нужно около 100 т руды, следовательно, это очень высокоматериалоёмкое производство. На 1 т электролитической меди нужно 2,5-5 тыс. кВатт·ч электроэнергии, что говорит об этой стадии производства меди как об очень высокоэнергоёмкой. В целом, производство меди характеризуется высокой материалоёмкостью до рафинирования и энергоёмким рафинированием. При размещении предприятий по переработке меди должна учитываться хорошая транспортная доступность топливных ресурсов.
Возможны два варианта размещения предприятий по производству меди:
|
|
· Выплавка черновой и электролитической меди ориентируется на районы сырья с учётом дешёвой электроэнергии для электролитического рафинирования.
· Разрыв технологической цепочки в пространстве перед электролитическим рафинированием. Первые стадии цепочки размещаются в районах сырья, а электролитическое рафинирование – в районах дешёвой электроэнергии или в районах потребления с дешёвой электроэнергией.
Цинк – хрупкий металл, сплавляется со многими металлами, пластичный, обладает высокой коррозионной стойкостью, ковкостью, взаимодействует с неметаллами.
45-60% цинка идёт на цинкование, до 10% используется в медицине (в качестве антисептиков), 10% идёт на производство сплавов, ещё 10% - на производство резиновых шин и 10% - на производство масляных красок.
Сырьём для производства цинка является цинковая обманка (сернистый цинк), встречающаяся, как правило, в составе полиметаллических руд. В руде содержится от 2 до 6-7% цинка.
Стадии производства цинка:
1. Флотация. Цинковая обманка отделяется от руд других цветных металлов. В результате получается цинковый концентрат.
2. Обжиг. Цинковый концентрат подвергается обжигу до полного выгорания серы и образования окиси цинка, содержащей 60% цинка.
|
|
3. Получение металлического цинка происходит двумя способами: гидрометаллургическим и пирометаллургическим.
· Гидрометаллургический способ. На цинковый концентрат действуют слабой серной кислотой, и цинк переводится в растворимое соединение. Раствор сернокислого цинка очищается и подвергается электролизу. В качестве катода применяются алюминиевые листы, анода – свинцовые. При электролизе на катоде выделяется металлический цинк. Затем он плавится в индукционных печах. Расплавленный цинк отливают в слитки, его чистота составляет 99,99%.
· Пирометаллургический способ более распространён. Цинк получается путём восстановления окиси цинка углеродом (коксом). Для этого обожжённый концентрат цинка смешивается с коксом и прокаливается в закрытых ретортах, помещённых в специальные печи, при температуре 1200-1300°. При прокаливании восстанавливается металлический цинк. Пары цинка по специальным трубам отводятся и конденсируются. Этот процесс называется дистилляцией и длится до суток. Таким образом получается черновой цинк. Он подвергается вторичной возгонке при температуре 1000° и переходит в чистый цинк.
Производство цинка – высокоматериалоёмкое производство. Гидрометаллургический способ требует большого количества электроэнергии, следовательно это высокоэлектроёмкий процесс. Пирометаллургический способ – топливоёмкий, т.к. для него нужно много каменного угля.
Первичная обработка цинковых руд осуществляется в местах их добычи. Полученные концентраты имеют хорошую транспортабельность, поэтому могут перерабатываться в зависимости от технологического процесса и в районах добычи сырья, и в районах, богатых топливом и с дешёвой электроэнергией.
Дата добавления: 2018-08-06; просмотров: 1061; Мы поможем в написании вашей работы! |
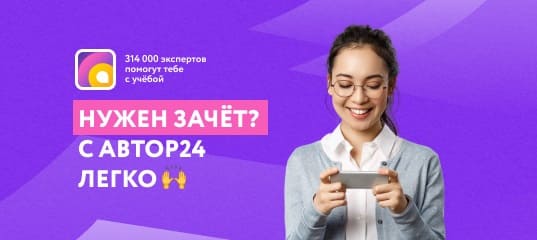
Мы поможем в написании ваших работ!