Механическое обезвоживание осадка
Анализ литературных источников и патентной документации по методам обработки осадков промышленных сточных вод
При очистке сточных вод металлообрабатывающих предприятий наиболее сложной проблемой является обработка осадков. Сточные воды, которые поступают на очистные сооружения, имеют весьма разнообразный состав загрязнений[1], поэтому и состав осадков также может быть разным.
Осадки представляют собой суспензии, выделяемые из сточных вод в процессе их механической, биологической и физико-химической очистки [2].
Осадки производственных сточных вод можно разделить на три группы:
а) осадки минерального состава;
б) осадки органического состава;
в) смешанные осадки.
Осадок первой группы обрабатывается и по возможности утилизируется, а осадок второй и третьей группы разнообразен по своему составу и свойствам, поэтому его обработать намного сложнее [3].
Обработка осадков сточной воды состоит из следующих стадий[3,4]:
а) уплотнение (сгущение);
б) стабилизация;
в) кондиционирование;
г) обезвоживание;
д) утилизация;
е) ликвидация.
Эффективное уплотнение является важной частью общей проблемы обезвоживания осадка. На этом этапе снижается влажность осадка до 40%, существенно повышается плотность сухого осадка и значительно уменьшается его объём в 2,5 раза [5]. Вследствие этого уменьшается и строительный объём метантенков в случае сбраживания осадка, так же увеличивается производительность такого оборудования как вакуум-фильтры, центрифуги, фильтр-прессы при механическом обезвоживании. Снижение объёма осадка приводит к уменьшению затрат при его транспортировке и накоплении.
|
|
Различают следующие способы уплотнения осадков[5, 4]:
а) гравитационное уплотнение;
б) флотационное;
в) центробежное;
г) вибрационное.
Гравитационное уплотнение – наиболее распространённый метод уменьшения объёма осадка, но он не настолько эффективен как флотационное уплотнение. Флотационное уплотнение имеет меньшую продолжительность процесса и более глубокий эффект [6]. Центробежное уплотнение применяется редко из-за больших габаритов и дороговизны оборудования. Вибрационное уплотнение является самым эффективным благодаря высокой скорости протекания процесса [7].
Стабилизация осадков применяется для предотвращения их загнивания при длительном хранении на открытом воздухе. Наиболее распространенным методом стабилизации является анаэробное сбраживание в метантенках. Также применяется аэробная стабилизация, под которой понимается длительное аэрирование осадков в сооружениях типа аэротенков-стабилизаторов [8]. Аэробная стабилизация основывается на том, что при недостатке внешнего источника питания, бактерии могут использовать свой собственный клеточный материал [9].
|
|
Цель кондиционирования – улучшение водоотдающих свойств осадков путём изменения их структуры и форм связей воды [10].
Кондиционирование осадков проводят для разрушения коллоидной структуры осадка органического происхождения и увеличения их водоотдачи при обезвоживании [11]. Плохая влагоотдача осадков затрудняет последующую обработку и утилизацию [2].
Применяют следующие методы кондиционирования[3]:
а) реагентная обработка;
б) тепловая обработка;
в) жидкофазное окисление;
г) криогенез (замораживание и оттаивание).
Наибольшее распространение получила реагентная обработка [12].
Реагентная обработка – процесс укрупнения и объединения в хлопья тонкодисперсных и коллоидных частиц при добавлении в осадок коагулянтов [13]. Для этого процесса применяют коагулянты и флокулянты органического и неорганического происхождения, так же применяются высокомолекулярные флокулянты[3,14,15]. Неорганические коагулянты, представляют собой минеральные реагенты, а органические – искусственные полимеры [16].
При коагуляции осадков чаще используют два или несколько реагентов. Часто применяется способ кондиционирования осадков сточных вод с помощью неорганических коагулянтов в сочетании с известью [8]. В качестве неорганических коагулянтов применяют соли железа, алюминия и известь, которые вводят в обрабатываемый осадок в виде 10%-ных растворов [17]. Наиболее эффективным является хлорное железо, применяемое обычно в сочетании с известью [18].
|
|
Известь нейтрализует кислоты, образующиеся при гидролизе коагулянтов, вступает в химические реакции с кислотами и органическими веществами, находящимися в осадках. При этом сокращается расход основного реагента и предотвращается загнивание осадка. Поэтому известь получила наибольшее распространение [19].
У кондиционирования осадка минеральными реагентами есть недостатки: большой массовый расход, высокая коррозийная активность, затруднения при транспортировании и хранении, внесение большого количества (40%) балластных веществ, что значительно увеличивает стоимость вывозки осадка, а также сокращает полезный объём полигона для их захоронения [20].
Преимущество использования органических коагулянтов заключается в образовании меньшего количество осадка, который образуется в процессе коагуляции, так как при обработке воды полимерами гидроксидов не образуется [16].
|
|
В качестве коагулянтов можно использовать отходы некоторых производственных процессов, что значительно сокращает стоимость реагентов и разрешает проблемы их утилизации. Такими реагентами могут быть железный купорос, отходы, содержащие хлористый алюминий, алюмосодержащие отходы, карбидный шлам, кислые железосодержащие сточные воды травления черных металлов [21].
Одним из эффективных способов очистки от тонких дисперсий и коллоидов является флокуляция. Флокуляция – это один из методов коагуляции.
Коллоидные частицы, представляют собой совокупность большого числа молекул веществ, которые содержатся в сточной воде в диспергированном состоянии. При перемещении они прочно удерживают покрывающий их слой воды.
На коллоидные частицы действует диффузионные силы, и частицы стремятся равномерно распределиться во всем объеме жидкой фазы.
Флокулянты – химические соединения, которые при введении в дисперсные системы могут образовывать механические связи между частицами твердой фазы и вызывать ускоренное осаждение частиц. [52]
Для изменения структуры осадка и улучшения его способности отдавать влагу применяют высокомолекулярные флокулянты. Действие флокулянтов проявляется в ускорении процесса образования и повышения прочности коллоидных структур, а также связывании микрохлопьев в крупные агрегаты [22].
Различают катионные, анионные и неионогенные флокулянты[23]. Обычно они используются как добавка к неорганическим коагулянтам для более интенсивного образования хлопьев.
Для обработки осадков, содержащих большое количество органических веществ (зольность 25-50%), применяют катионные флокулянты. При более высокой зольности – смесь катионных и анионных флокулянтов [2,3].
Широко используют синтетический флокулянт–полиакриламид (ПАА), который является основой широко известных флокулянтов «Praestol», «Flopam» [24].
Экспериментально установлено, что введение флокулянта «Praestol» при использовании сорбента-коагулянта приводит к укрупнению хлопьев и улучшению фильтрационных свойств[12].
Применение флокулянта «Zetag» позволяет улучшить водоотдающие свойства осадка в большей степени, чем флокулянт «Praestol»[25].
Синтетические флокулянты дороги, токсичны и являются источником вторичного загрязнения сточных вод, требующего дополнительных мер по очистке или обезвреживанию. Поэтому актуальны поиски безреагентных методов коагуляции [2].
Тепловая обработка применяется для обработки осадков промышленных сточных вод с зольностью 30-40%.
Во многих развитых странах (США, Великобритании, Германии) тепловая обработка используется в качестве основного метода подготовки осадков к дальнейшему обезвоживанию. Впервые этот метод появился в Англии.
Данный метод заключается в нагревании осадка до 150-200°С и выдерживании его в закрытой ёмкости в течении 0,5-2 ч. при этой температуре. Происходит изменение структуры осадка: около 40% сухого вещества переходит в раствор, а оставшаяся часть приобретает водоотдающие свойства [26]. Осадок после тепловой обработки быстро уплотняется до влажности 92-94%, и его объём составляет 20-30% исходного [6]. За рубежом тепловую обработку часто применяют в сочетании со сбраживанием в мезофильных условиях [19]. Сбраживание происходит при средних температурах, обеспечивающих рост микроорганизмов[27].
При тепловой обработке снижается удельное сопротивление осадков, что позволяет легко обезвоживать осадок на вакуум-фильтрах или фильтрах-прессах.
Одним из достоинств метода тепловой обработки является полная стерильность обработанного осадка, так же осадок имеет низкую влажность и не загнивает при хранении[19].
Данный метод обработки осадков имеет недостатки, к которым относится конструкционная сложность оборудования, большие затраты электроэнергии и высокое содержание органических компонентов в фильтрате, которые необходимо направлять на биологическую очистку. При тепловой обработке выделяются дурно пахнущие газы, которые требуют предварительной очистки перед выбросом их в атмосферу[28,19,26].
Применяется и жидкофазное окисление. В зарубежной практике известен как метод Циммермана[26]. Сущность метода заключается в окислении органической части осадка кислородом воздуха при высокой температуре и высоком давлении. Этот метод ещё называют мокрым сжиганием. О глубине процесса жидкофазного окисления органической части осадка судят по снижению величины ХПК (химическое потребление кислорода)[6].
С применением гомогенных или гетерогенных катализаторов значительно сокращается время окисления. В качестве катализаторов применяются оксиды или гидроксиды металлов переменной валентности, активированный уголь, полифталоцианинкобальта[29].
Жидкофазное окисление – это перспективный метод, но он недостаточно хорошо изучен и требует новых конструкторских решений, исследований в этой области[30].
Применение криогенной обработки в Сибири экономически выгодно, так как замораживание может происходить в естественных условиях. При оттаивании образуются меньшие объемы осадков, что позволяет сократить антропогенное воздействие на окружающую среду[26].
Метод заключается в том, что при замораживании часть связанной влаги переходит в свободную, происходит коагуляция твёрдых частиц осадка и снижается удельное сопротивление осадка. При оттаивании происходит влагоотдача осадков[26]. Замораживание происходит при температуре от -5°С до -10°С в течении 50-120 минут[8].
В [31] установлено, что метод криогенной обработки приводит к изменению структуры осадка, а так же при этом улучшаются водоотдающие свойства. Процесс криогенеза необходимо регулировать для интенсификации обезвоживания[32].
Этот метод хорош тем, что удаляемая вода не имеет дополнительных загрязнений, как это наблюдается у других методов.
На кафедре Инженерно-строительного института Сибирского федерального университета разработана установка для обезвоживания осадков сточных вод путём замораживания в естественных условиях для улучшения водоотдающих характеристик осадка[33].
Для осуществления процесса замораживания и оттаивания осадков в искусственных условиях используют холодильные машины, основанные на применении аммиака и барабанные установки[34]. Расход электроэнергии при этой обработке составляет 50 кВт/м3 осадка. Для уменьшения затрат электроэнергии, тепло при замораживании собирают и используют для оттаивания[35].
Для небольших объёмов осадка и низких концентраций масел целесообразно использовать электрохимическую коагуляцию. Из литературных источников [8,36] известен метод электрокоагуляционной обработки осадков. Простота устройств, ограниченный расход реагентов, автоматическое управление процессами делают электрообработку перспективным методом[37]. Недостатком электрокоагуляционного метода являются затраты электроэнергии и металла.
Известен метод ультразвуковой обработки осадка[8]. Метод привлекает низкими капитальными затратами, легкостью встраивания в существующие сооружения и простотой эксплуатации[38]. Этот метод широко применяется в Швеции, Германии, Новой Зеландии, Испании, Венгрии, Австралии и Сингапуре [38].
При воздействии ультразвука на осадок высвобождается часть влаги в результате разрушения стенок клетки. Для достижения требуемого эффекта кондиционирования осадка рекомендуется этот метод применять в комплексе с другими методами[1].
Применяется обезвоживание осадка путём фильтрования, заключающееся в процессе отделения твёрдых веществ от жидкости, происходящего при разности давлений над фильтрующей средой и под ней[19].
Для механического обезвоживания осадков производственных сточных вод применяют вакуум-фильтр, фильтр-прессы и центрифуги. Так же применяются вибрационные фильтры, которые имеют высокую производительность и не очень высокую стоимость [39].
При выборе обезвоживающего оборудования нужно учитывать следующие параметры: производительность; влажность осадков, подаваемых на обезвоживание; влажность обезвоженных осадков; эффективность задержания сухого вещества; концентрация взвешенных веществ в фильтрате[40].
В 1991 году был разработан шнековый обезвоживательVOLUTE фирмы AMCON, его структура позволяет выполнять сразу 2 функции: сгущение и обезвоживание в одной машине. В настоящее время установлено более 2500 единиц обезвоживателей в 60 странах мира и более 500 в городах России. Он исключает запах, занимает меньше места и уменьшает эксплуатационные расходы[41].
Широкое распространение получила термическая сушка осадков. Она заключается в обеззараживании и уменьшении влажности осадка с 83-86% до 10-20% [42]. Основана на использовании тепла для испарения влаги [18]. Часто используются в качестве подготовительного процесса для последующего сжигания осадков [43].
Если нет возможности использовать обезвоженный осадок для каких-либо целей, то его сжигают.
Сжигание – процесс окисления органической части осадков при повышенной температуре до нетоксичных газов (двуокись углерода, водяные пары и азот) и выделения минеральной части в виде расплава или сухого порошка (золы). Теплота используется для подогрева воздуха, который необходим для сжигания, а зола применяется как присадочный материал для интенсификации процесса обезвоживания осадков на вакуум-фильтрах или фильтр-прессах [19,44].
Сжигание проводят в топочных устройствах различного вида.
Широко применяемая технология сжигания осадка экологически опасна, поскольку сжигание осадка сопровождается выделением токсичных пылегазовых выбросов, содержащих оксиды серы (IV и VI), хлора и хлорсодержащих соединений, диоксинов, что приводит к необходимости создания комплексной многоступенчатой системы очистки газов от пыли и газообразных примесей[45].
С 2005 года в Германии запретили хранить отходы на полигонах, поэтому там стало широко применяться сжигание [46,43]. Сжигание широко распространено и на очистных сооружениях города Санкт-Петербург [47].
В зарубежных странах часто применяемое сжигание комбинируют с другими бытовыми твёрдыми отходами, что оказывается экономически выгодным [43].
Итогом обработки осадка сточных вод будет являться такой продукт, который будет минимально наносить ущерб окружающей среде после его утилизации.
Таким образом, в настоящее время, актуальным является решение проблемы сокращения отходов промышленных предприятий, так как не достаточно разработано комплексных высокоэффективных технологий обезвоживания и утилизации осадков промышленных предприятий, для условий Сибири и Крайнего Севера.
Кондиционирование осадков
Под кондиционированием осадков понимают вид обработки, при котором осадок изменяет структуру и формы связи воды, благодаря чему лучше обезвоживается.
(С.В. Яковлев)
Кондиционирование проводят реагентными и безреагентными способами. При реагентной обработке осадки обрабатывают 10 % раствором коагулянтов (FeSO4, Fe2(SO4)3, Al2(SO4)3 и др.). Вместо коагулянтов можно использовать и флокулянты. К безреагентным методам обработки относятся: тепловая обработка, замораживание с последующим отстаиванием, жидкофазное окисление, электрокоагуляция и радиационное облучение. В отечественной практике тепловая обработка осадка находится в стадии освоения и внедрения.
(О.А. Федяева Пром экология)
К недостаткам метода реагентной обработки относятся:
- высокая стоимость;
- повышенная коррозия материалов;
- сложность транспортирования, хранения и дозирования реагентов.
К безреагентным методам кондиционирования осадка относятся тепловая обработка и замораживание с последующим оттаиванием. Тепловая обработка заключается в нагревании осадка до температуры 170-220°С и выдерживании их при этой температуре в закрытых емкостях - автоклавах, реакторах в течение 30-120 мин.
Осадок после тепловой обработки быстро уплотняется до влажности 92-94%, т.е. его объём сокращается в 2-4 раза, причём обезвоживаются осадки без обработки их химическими реагентами.
Осадок после замораживания и оттаивания обезвоживается механическим путём тоже без применения дополнительных реагентов.
Механическое обезвоживание осадка
Обезвоживание осадков сточных вод на иловых площадках для очистных сооружений средней и большой производительности часто оказывается невозможным из-за отсутствия свободных земельных площадей. Поэтому на таких станциях применяют механическое обезвоживание осадков на вакуум-фильтрах, фильтр-прессах, центрифугах либо других аппаратах.
При фильтровании происходит процесс отделения твёрдых частиц от жидкости при разности давления над фильтровальной средой и под ней. Фильтрующей средой на барабанных вакуум-фильтрах и фильтр-прессах является фильтровальная ткань и слой осадка, налипающий на ткань в процессе фильтрования. Первоначальное фильтрование происходит через ткань, в порах которой твёрдые частицы осадка задерживаются и создают добавочный фильтровальный слой. Этот слой по мере фильтрования увеличивается и является главной фильтрующей средой, а ткань служит лишь для поддержания фильтрующего слоя.
При фильтровании жидкость протекает через пористую массу и образуется слой осадка (кека). При увеличении слоя кека уменьшается скорость протекания жидкости (фильтрата).
В зоне фильтрования осадок фильтруется под действием вакуума (в барабанных вакуум-фильтрах), а на фильтр-прессах – под давлением.
Реагенты вводятся непосредственно перед подачей осадка на механическое обезвоживание (перед фильтр-прессами, центрифугами). На рис. 2.14 приведена схема механического обезвоживания осадков.
Сброженный осадок, выгружаемый из метантенка, перед подачей на механическое обезвоживание подвергается промывке технической водой в течение 15-20 мин. из расчета 2-4 м3воды на 1 м3осадка и продувается воздухом в объёме 0,5 м3на 1 м3смеси осадка и воды. Затем эта смесь направляется в илоуплотнители, где в течение 12-24 ч. уплотняется осадок и удаляется вода. Иловая вода, содержащая до 1,5 г/л взвешенных веществ и БПК до 900 мг/л, направляется на очистные сооружения, а уплотнённый осадок (кек) влажностью 94-96% подвергается коагулированию и затем поступает на обезвоживание.
![]() |
Осадок после такой обработки имеет более низкое удельное сопротивление и значительно легче отдаёт воду.
Рис. 2.14– Схема подготовки осадка к механическому обезвоживанию:
1 – метантенк; 2 – сборный резервуар; 3 – плунжерный насос;
4 – подача воды; 5 – подача сжатого воздуха; 6 – промывка осадка;
7 – уплотнитель; 8 – резервуар уплотненного осадка; 9 – подача коагулянта;
10 – отделение коагулирования; 11 – вакуум-фильтр; 12 – конвейер;
13 – подача осадка в отделение термической сушки
Обезвоживание осадка на центрифугах – это процесс разделения неоднородных систем (эмульсий, суспензий) под действием центробежных сил, возникающих во вращающемся роторе. Подающийся непрерывно осадок под действием центробежных сил прижимается к внутренней поверхности сплошного ротора. Твердые частицы, имеющие большую плотность, осаждаются в объеме суспензии и концентрируются на стенках ротора, вытесняя воду в пространство, расположенное ближе к центру вращения (рис. 2.23). Это дает возможность разделить осадок на фракции: твердую – кек и жидкую – фугат.
![]() |
Рис. 2.23 – Схема процесса обезвоживания осадка центрифугированием
Центрифугирование осадков находит всё большее распространение, так как этот метод является довольно простым в эксплуатации, экономичен, процесс легко управляем, но влажность кека по сравнению с кеком, полученным после фильтр-прессования, выше.
Обезвоживанию методом центрифугирования подлежат все виды осадка (из первичных отстойников, избыточного активного ила, смеси).
Основными недостатками метода являются пока что высокая стоимость флокулянтов, а при центрифугировании без флокулянтов – низкая эффективность задержания сухого вещества осадка, т.е. образуется фугат с высокими значениями БПК, ХПК, содержанием взвешенных веществ и его необходимо направлять на дальнейшую обработку на сооружения биологической очистки, увеличивая тем самым нагрузку на них. Поэтому основным сдерживающим фактором применения центрифуг является использование флокулянтов, так как наша промышленность выпускает ограниченное число флокулянтов, а импортные очень дороги. Для обезвоживания осадков сточных вод применяют серийные, непрерывно действующие осадительные шнековые центрифуги типа ОГШ. Основными элементами центрифуги являются конический ротор со сплошными стенками и полый шнек. Ротор и шнек вращаются в одну сторону, но с разными скоростями. Под действием центробежной силы частицы осадка отбрасываются к стенкам ротора и вследствие разности частоты вращение ротора и шнека перемещаются к отверстию в роторе, через которые обезвоженный осадок выгружается в бункер кека, а фугат (жидкая фаза) отводится через отверстия, расположенные с противоположной стороны ротора (см. рис. 2.24 и 2.25).
Эффективность задержания твердой фазы осадка и влажность кека зависят от характеристики обезвоживаемого осадка. Наибольшее количество
Рис. 2.24 – Принципиальная схема устройства центрифуг типа ОГШ:
а –противоточная, б – прямоточная;
1 – подача осадка; 2 –подача флокулянта; 3 –вход осадка из приемной
полости шнека в ротор; 4 –ротор; 5 – шнек; 6 –переливные трубы
в шнеке для отвода фугата; 7 – отверстие для слива фугата;
8 –бункер для приема фугата; 9 –окно для выгрузки кека;
10 –бункер для приема кека; 11 –кожух
взвешенных веществ содержится в фугате при центрифугировании активного ила. При обезвоживании осадка на центрифугах возникает проблема дальнейшей обработки фугата. Есть разработанный ряд технологических схем как обработки фугата, так и осадка (раздельное центрифугирование сырого осадка и активного ила, смеси осадков и др.).
Подбор центрифуг ведется по их пропускной способности и по количеству исходного осадка, а эффективность задержания сухих веществ и влажность кека зависят от характеристики обрабатываемого осадка. По табл. 63 СНиП [1] эффективность задержания сухого вещества равна 10-65%, а влажность кека 60-85%.
![]() |
Рис. 2.25 – Горизонтальная шнековая центрифуга типа ОГШ-459:
1 – труба питания; 2 – ротор Др=450 мм; 3 – шнек; 4 – шахта фугатаl=1,01 м; 5 – редуктор; 6 – виброизолятор; 7 – шахта кека; 8 – станина
Перед подачей осадка на центрифугу предусматривается удаление из него песка. При подаче фугата после центрифуг на очистные сооружения необходимо учитывать увеличение нагрузки на них по БПК и взвешенным веществам в зависимости от эффективности задержания сухого вещества.
При введении в осадок флокулянта производительность центрифуг уменьшается в 2 раза, но зато эффективность задержания сухого вещества увеличивается до 90-95%.
Принцип работы горизонтальной шнековой центрифуги типа ОГШ-459 (рис. 2.25), представляющей собой машину непрерывного действия, следующий. Осадки, подлежащие обезвоживанию, поступают по трубе питания 1 внутрь вращающегося ротора 2. Под воздействием центробежной силы более тяжелые, чем вода, частицы твердой фазы (кек) осаждаются на внутренней поверхности ротора. Осветленная вода (фугат) стекает через отверстия в днище ротора. Вращение шнека относительно ротора производится планетарным редуктором 5. Изменение относительной частоты вращения шнека осуществляется путем вращения солнечной шестерни редуктора с помощью клиноременной передачи. Предусмотрены подача раствора флокулянта внутрь ротора и промывка конической части ротора водными растворами.
На рис. 2.26 приведена схема раздельного центрифугирования сырого осадка первичных отстойников и избыточного активного ила. По этой схеме фугат от центрифугирования сырого осадка сбрасывается в первичные отстойники (продолжительность осветления сточных вод при этом увеличивается до 4-4,5 сут.), а фугат от центрифугирования активного ила используется как циркулирующий активный ил в аэротенках. При этом из схемы очистных сооружений исключаются илоуплотнители.
Рис. 2.26 – Схема раздельного центрифугирования сырого осадка и активного ила:
СВ – сточные воды; ОВ – очищенные сточные воды; СО – сырой осадок из первичных отстойников; ЦИ – циркулирующий активный ил;
ИИ – избыточный активный ил; К – кек; Ф – фугат; Ф+ЦИ – смесь фугата и циркулирующего активного ила;
1 – первичный отстойник; 2 – аэротенк; 3 – вторичный отстойник;4 –
центрифуги
На рис. 2.27 приведена комбинированная схема центрифугирования сырого осадка первичных отстойников с последующей аэробной стабилизацией фугата в смеси с неуплотненным избыточным активным илом и центрифугирования сброженной смеси. По этой схеме продолжительность аэробной стабилизации составляет 6-8 суток, продолжительность уплотнения сброженной смеси – 6-8 ч., а влажность уплотненного осадка – 97,5%.
![]() |
Рис. 2.27 – Комбинированная схема центрифугирования осадков сточных вод:
СВ – сточные воды; ОВ – очищенные сточные воды; СО – сырой осадок из первичных отстойников; ЦИ – циркулирующий активный ил;
ИИ – избыточный активный ил; К – кек; Ф – фугат; ИВ – иловая вода; УСтО – уплотненный стабилизированный осадок;
1 – первичный отстойник; 2 – аэротенк; 3 – вторичный отстойник;
4 – центрифуги; 5 – аэробный стабилизатор; 6 - илоуплотнитель
Утилизация осадков сточных вод промышленных предприятий предназначена для извлечения и использования ценных веществ (1).
Использование отходов как вторичных материальных ресурсов.
Под вторичными материальными ресурсами принято понимать любые отходы, образующиеся и накопленные в процессе материального производства, а также при оказании услуг и конченом потреблении.
Все возможные направления использования отходов как вторичных материальных ресурсов могут быть классифицированы следующим образом:
1. Применение в хозяйственных целях без переработки (реализация на другие предприятия или использование в собственном производстве);
2. Подготовка отходов для использования в качестве вторичного сырья для частичной или полной замены первичного сырья в промышленном производстве;
3. Использование в качестве вторичного сырья в производстве строительных материалов;
4. Использование в качестве сырья для извлечения полезных компонентов;
5. Использование в качестве энергоресурсов. (8)
В процессе поиска альтернативных способов утилизации ОСВ путем проведения теоретических и экспериментальных исследований и опытно-промышленной апробации нами было доказано, что решение экологической проблемы — ликвидации накопленных объемов отходов — возможно путем их активного вовлечения в хозяйственный оборот в следующих отраслях:
1. дорожное строительство (производство органо-минерального порошка взамен минерального порошка для асфальтобетона);
2. строительство (производство утеплителя типа керамзит и керамического эффективного кирпича);
3. аграрный сектор (производство высокогумусного органического удобрения) [2].
Сбор отработанных нефтепродуктов в качестве вторичного сырья позволяет удешевить производство строительных материалов, расширить топливно-энергетические ресурсы и предотвратить загрязнение окружающей среды (5).
Принципы построения системы переработки нефтесодержащих отходов должны включать следующую информацию:
1. объем образующихся и накопленных нефтесодержащих отходов;
2. наличие в составе нефтесодержащих отходов ценных компонентов, которые могут быть использованы в качестве вторичных материальных ресурсов;
3. класс опасности отхода;
4. размер удельной платы за размещение отходов, за сброс со сточными водами по каждому веществу, входящему в состав нефтесодержащего отхода.
Пригодность нефтешламов для использования в качестве вторичного сырья должна определяться их составом, свойствами и экологической опасностью.
Кроме того, адаптация и выбор технологии для конкретного региона или территории зависит от количественного состава образующихся отходов (3).
В таблице 1.1 представлен состав того или иного вида отхода НПЗ.
таблица 1.1
Область применения | Виды нефтесодержащего отхода | Состав нефтешлама, % масс. | ||
органическая часть | минеральная часть | вода | ||
Строительные материалы | Нефтешлам сгущенный | 20-25 | 55-65 | 10-25 |
Масло и нефтешлам НПЗ | 13-28 | 59-77 | 10-22 | |
Нефтешлам с установки «Альфа-Лаваль» | 13-18 | 61-78 | 11-23 |
Осадок с высоким содержанием минеральной части может быть использован в качестве заполнителя при производстве строительных материалов и конструкций (4).
В данной главе рассматривается производство керамического кирпича методом добавления осадков сточных вод нефтеперерабатывающего предприятия.
Требования к нефтешламамводоочистных сооружений для получения кирпича (табл. 1.2)
Таблица 1.2
Наименование показателей | Значение |
Массовая доля нефтепродуктов, % не менее | 30 |
Массовая доля воды, % | 22-70 |
Механических примесей, % | 15-20 |
Предел прочности при сжатии кирпича определяли по ГОСТ 8462-85.
На морозостойкость кирпич испытывали по ГОСТ 7025 – 91.
Для поиска новых путей использования в качестве вторичного сырья - нефтешламов водоочистных сооружений представлялось интересным изучить возможность применения их в качестве компонента глинистого сырья, подвергаемому термической обработке – обжигу.
«Глиной называются землистые минеральные массы, или землистые обмолоченные горные породы, способные образовывать с водой пластичное тесто, сохраняющее приданную ему форму после высыхания, а после обжига получающее твердость камня».
Рисунок - Принципиальная технологическая схема получения кирпича
1 – винтовые каменно – выделительные вальцы; 2 – бегуны (измельчители); 3 – глиномешалка; 4 – емкость приема нефтешламов водоочистных сооружений; 5 – дробилка; 6 – грохот; 7 – ленточный пресс (для промятия глины); 8 – шихтозапасник; 9 – промежуточная емкость; 10 – формовочная машина; 11 – автомат укладчик; 12 – сушильные вагонетки; 13 – тоннельное сушило; 14 – обжиговые вагонетки; 15 – тоннельная печь; 16 – насос – дозатор.
Глина со склада поступает в ящичный питатель для дозирования и ленточным конвейером подается в винтовые каменно-выделительные вальцы (1), где глина измельчается и освобождается от крупных твердых включений. Для более эффективного измельчения глина подается на бегуны (2). Далее она направляется в глиномешалку (3), в которой он увлажняется.Перемешивается до получения однородной массы. Выгорающие добавки – нефтешламы поступают на предприятие автомобильным транспортом, затем насосом дозатором (16). Сначала они проходят дробилку(5) и грохот (6), затем при помощи насоса-дозатора также подаются в дозированных количествах в глиномешалку(3). Тщательно приготовленная однородная масса поступает затем в ленточный пресс(7). Для работы автоматизированных линий необходимо в технологической схеме перед прессом предусматривать шихтозапасник (9) для равномерной выдачи массы через промежуточную емкость 9. Формование – одна из основных операций при производстве керамических изделий (10). Глиняный формованный брус режется струнным резательным автоматом на отдельные кирпичи, затем на сушильные вагонетки кирпич-сырец укладывает автомат-укладчик (11), транспортировка которых осуществляется с помощью электропередаточной тележки (12). При сушке используют горячий воздух из тоннельной печи (13), рециркулятор и атмосферный воздух, а также дымовые газы из топки Сушильные вагонетки (12) поступают к автомату-укладчику (11) после завершения процесса сушки, который укладывает полуфабрикат на обжиговые вагонетки (14) для обжига в печи. Обжиг проводят при температуре 1000оС в туннельной печи. В канале уложены рельсы, по которым движутся вагонетки с кирпичом сырцом. Тоннельная печь (15) имеет три зоны: подогрева, обжига и охлаждения, через которые последовательно в течение 18-36 ч проходят вагонетки с кирпичом-сырцом. После окончания обжига вагонетки подаются на участок разгрузки, где установлен автомат разгрузки и пакетировки. (6)
Оборудование туннельная печь
Изобретение относится к области техники, связанной с обжигом природных материалов и изделий из них, и может быть использовано при производстве строительных керамических изделий, в частности для производства кирпичей.
Туннельная печь входит в состав оборудования для изготовления керамических изделий. Оборудование для изготовления керамических изделий содержит сушильную печь и печь для обжига керамических изделий. Причем, с целью увеличения расхода газа (воздуха) через межсводовое пространство, межсводовое пространство посредством трубопровода (воздуховода или газовода) и вентилятора соединено с сушильной печью.
Рисунок – туннельная печь
Позицией 1 на чертеже обозначена зона предварительного нагрева рабочего канала, позицией 2 - зона обжига, позицией 3 - зона охлаждения. Между основным сводом 4 и дополнительным сводом 5 находится межсводовое пространство 6. Система газораспределения (вентиляции) включает всасывающий трубопровод 7, вентилятор 8, подающий трубопровод 9 и коллектор-распределитель 10 с патрубками 11, при этом всасывающий трубопровод 7 соединяет межсводовое пространство 6 печи над зоной 2 обжига с вентилятором 8, а патрубки 11 коллектора-распределителя 10 выходят непосредственно в зону 3 охлаждения вблизи зоны 2 обжига рабочего канала. Позицией 13 на чертеже обозначены горелки, расположенные в зоне 2 обжига. Система вентиляции может включать несколько вентиляторов 8 с соответствующим количеством соединительных трубопроводов. Кроме того, печь может быть снабжена вытяжной вентиляцией для сброса части газов в атмосферу, а также трубопроводами для подачи горячих газов в зону 1 предварительного нагрева керамических изделий (такие конструктивные элементы на чертеже не изображены, поскольку не относятся к предмету изобретения).
Предлагаемая туннельная печь работает следующим образом.
По рабочему каналу печи движутся обжиговые вагонетки, груженные высушенными керамическими изделиями. На чертеже вагонетки с обжигаемым материалом движутся справа налево, дымовые газы - в противоположном направлении. Подвергаемые термообработке керамические изделия проходят последовательно зоны предварительного нагрева, обжига и охлаждения, обозначенные позициями 1, 2 и 3 соответственно. Сначала изделия нагреваются в зоне 1 предварительного нагрева за счет тепла, поступающего из зоны 2 обжига, образующегося при сжигании топлива. Далее происходит собственно обжиг при максимальных температурах (зона 2). Затем изделия постепенно остывают в зоне 3 охлаждения.
При обжиге в туннельной печи изделия (в частности, кирпичи) подвергаются воздействию повышающейся температуры от 80°С до 750°С - в зоне предварительного нагрева; воздействию температуры от 750°С до 1100°С - в зоне обжига; воздействию понижающейся температуры от 1100°С до 50°С - в зоне охлаждения. Обжиг осуществляют в течение 40-55 часов.
Воздух, нагнетаемый в конце печи, проходит зону 3 охлаждения, нагревается и поступает в зону обжига, где участвует в процессе сгорания топлива, подаваемого в зону 2 обжига. Нагретый воздух также может отводиться для сушки сформованных изделий в сушильных установках. Дымовые газы от сгорания топлива направляют в зону 1 предварительного нагрева, где они используются в процессах окончательного удаления влаги, собственно нагрева и подготовки изделий к обжигу.
Тепло, образующееся от сгорания топлива, затрачивается не только на обжиг изделий, но и нагрев ограждающих конструкций печи (так называемые потери тепла), в том числе и подвесного свода. В конце зоны 1 предварительного нагрева, зоне 2 обжига и начале зоны 3 охлаждения создаются достаточно высокие температуры, влияющие на прочностные показатели поддерживающих металлических конструкций основного и дополнительного сводов. Тепло из рабочего канала за счет теплопередачи через основной свод попадает в межсводовое пространство.
Горячий воздух из межсводового пространства 6 через всасывающий трубопровод 7 отбирается вентилятором 8 и направляется по подающему трубопроводу 9 в зону 3 охлаждения рабочего канала или в пространство между зоной 2 обжига и зоной 3 охлаждения рабочего канала. Температура отбираемых из межсводового пространства 6 газов составляет 250-300°С, что явно ниже, чем температура изделий, покидающих зону обжига, но заметно превышает температуру атмосферного воздуха, также направляемого на охлаждение обожженных изделий. За счет начала охлаждения изделий воздухом с относительно высокой температурой (по сравнению с атмосферным воздухом) и постепенного понижения температуры охлаждающего воздуха по мере движения вагонеток с изделиями по зоне охлаждения к выходу рабочего канала достигается оптимальный режим остывания изделий. При этом по сравнению с процессом охлаждения только с помощью обдува атмосферным воздухом заметно уменьшается брак изделий, вызываемый резкими перепадами температур при охлаждении и неравномерным охлаждением разных участков изделий.
Когда температура газов, подаваемых в зону 3 охлаждения, оказывается слишком высокой, она может быть понижена до необходимого уровня путем смешивания горячих газов с атмосферным воздухом. Для этой цели на всасывающем трубопроводе 7 установлен патрубок 12 забора атмосферного воздуха. С целью регулирования количества отбираемого воздуха на всасывающем трубопроводе может быть установлен регулятор расхода (заслонка).
Система газораспределения обеспечивает подачу газа из межсводового пространства в рабочий канал с расходом от 0,01 м3/c до 10 м3/с. Система выполнена с возможностью регулирования расхода газа.
При этом обеспечивается стабилизация качественных показателей керамических изделий. Кроме того, обеспечивается наиболее рациональный температурный режим обработки керамических изделий, снижается расход топлива за счет использования тепла из межсводового пространства. Подача подогретого газа из межсводового пространства в рабочий канал компенсирует потери тепла, происходящие при открытии дверей печи. (7)
Дата добавления: 2018-06-27; просмотров: 726; Мы поможем в написании вашей работы! |
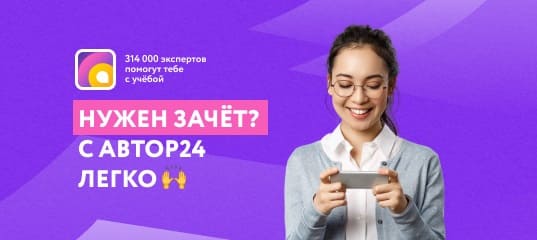
Мы поможем в написании ваших работ!