Методы обнаружения неисправностей станков
Существует несколько методов обнаружения неполадок в станках – методов дефектоскопии. Основными из них являются: метод пробного включения и осмотра станка; акустический метод; метод измерения; метод определения содержания металла в смазке.
Метод пробного включения и осмотра
Заключается в том, что станок опробуют при работе вхолостую или под нагрузкой с одновременным или последующим осмотром. Неполадки, которые могут вызвать отказ, устанавливают ориентировочно по посторонним стукам, повышенному шуму, повышенному расходу смазки и т.д. Этим методом сразу же устанавливают полный отказ того или иного узла, выявляют течи гидросистем и коммуникаций и другие крупные неисправности. В зависимости от размеров дефекта осмотр производят визуально или с помощью простых оптических средств.
Акустический метод
Определения неисправностей заключается в том, что наличие некоторых дефектов (например, увеличенных зазоров в подшипниках) можно установить прослушиванием. Для этой цели применяют стетоскоп, представляющий собой трубку с мембраной и наушниками. С его помощью выявляют стук, отличный от шума нормально работающего станка. Существуют электронные стетоскопы, имеющие довольно высокую чувствительность.
Акустическим методом пользуются также для обнаружения в деталях трещин путем простукивания детали и прослушивания звука. Если деталь не имеет трещин, получается чистый, ровный звук.. Чаще всего используют упругие волны ультразвукового диапазона (с частотой колебаний выше 20 кГц). Этот метод также называют ультразвуковым. Детали с трещинами дают дребезжащий звук.Главная отличительная особенность данного метода состоит в том, что в нем применяют и регистрируют не электромагнитные, а упругие волны.
|
|
Метод измерения
Используется и для определения величины износа отдельных деталей. Износ определяют как разность между первоначальным (чертежным) размером детали и фактическим. Замер производят линейками, штангенциркулями, микрометрами, а также индикаторами и щупами. При отсутствии щупов пользуются свинцовой проволокой. Величину биения вала определяют индикатором биения.
Чрезмерное повышение температуры трущихся деталей можно определить на ощупь. При этом принимают, что ладонь человека может выдержать температуру около 60 °С.
Определение содержания металла в смазке заключается в том, что периодически отбирают пробы масла и химическим путем определяют содержание в нем металла, попадающего туда в результате износа трущихся деталей. Этим методом нельзя определить износ отдельных деталей. Кроме того, металл может осаждаться в маслобаках, картерах и т.п.
|
|
Для определения дефектов отдельных деталей буровых станков может использоваться также ультразвуковой, магнитоакустический, рентгеновский методы, а также методы керосиновой пробы, цветной дефектоскопии, люминесцентный и другие.
Радиационный метод
Основан на регистрации и анализе проникающего ионизирующего излучения после взаимодействия его с ОК. В зависимости от природы ионизирующего излучения вид контроля подразделяют на подвиды: рентгеновский, гамма-, бета- (поток электронов), нейтронный. Интенсивность прошедшего излучения будет больше на участках меньшей толщины или меньшей плотности, в частности в местах дефектов - несплошностей или неметаллических включений.
К недостаткам радиационных методов необходимо, прежде всего, отнести вредность для человека, в связи, с чем требуются специальные меры радиационной безопасности: экранирование, увеличение расстояния от источника излучения и ограничение времени пребывания оператора в опасной зоне.
Оптический метод
Основан на наблюдении или регистрации параметров оптического излучения, взаимодействующего с ОК. Это взаимодействие связано с поглощением, отражением, рассеиванием, дисперсией, поляризацией и др. оптическими эффектами. Данный метод применяют для измерения геометрических параметров изделий, контроля состояния поверхности и обнаружения поверхностных дефектов.
|
|
Магнитный метод
неразрушающего контроля применяют для выявления дефектов в деталях, изготовленных из ферромагнитных материалов (сталь, чугун), т. е. материалов, которые способны существенно изменять свои магнитные характеристики под воздействием внешнего магнитного поля.
Магнитный неразрушающий контроль основан на выявлении различными способами магнитных полей рассеяния, возникающих над дефектами, или на определении и оценке магнитных свойств объекта контроля.
Магнитопорошковый метод основан на выявлении магнитных полей рассеяния, возникающих над дефектами в детали при ее намагничивании, с использованием в качестве индикатора ферромагнитного порошка или магнитной суспензии. Этот метод среди других методов магнитного контроля нашел наибольшее применение. Примерно 80 % всех подлежащих контролю деталей из ферромагнитных материалов проверяется именно этим методом. Высокая чувствительность, универсальность, относительно низкая трудоемкость контроля и простота - все это обеспечило ему широкое применение в промышленности вообще и на транспорте в частности. Основным недостатком данного метода является сложность его автоматизации.
|
|
Технология ремонта
Технологический процесс ремонта буровых станков состоит из подготовительных, основных и заключительных операций.
К подготовительным операциям относят доставку станка на ремонтное предприятие или его переход на ремонтную площадку.
Основные операции: общая разборка, очистка и мойка деталей, дефектация деталей и сборочных единиц, т.е. определение степени их пригодности для дальнейшей работы; восстановление деталей, ремонт механизмов; изготовление новых деталей и элементов конструкций; сборка механизмов; приработка и испытание собранных механизмов; общая сборка; испытание станка вхолостую и под нагрузкой; окраска.
Заключительные операции: доставка станка в забой, подключение к источникам электроэнергии, проведение промышленных испытаний и устранение дефектов в первое время эксплуатации.
При ремонте станков применяются три метода: индивидуальный, сменно-узловой и поточный (при большом числе ремонтируемых машин).
При индивидуальном методе ремонта все годные для работы детали, снятие с данного станка после необходимого восстановления, вновь устанавливают на этот же станок, и весь комплекс ремонтных работ выполняют в период ремонта станка.
При сменно-узловом методе ремонта детали каждого ремонтируемого станка делят на три основные группы: годные, требующие ремонта и негодные.
Поточный метод ремонта характеризуется строгой последовательностью операций и большим расчленением технологического процесса ремонта на отдельные операции, выполняемые специализированными постами. Для эффективного применения поточного метода необходимо иметь в год 100 и более ремонтируемых однотипных станков.
Для доставки буровых станков на ремонтное предприятие (мастерские или завод) используется железнодорожный или автомобильный транспорт.
Степень пригодности деталей к дальнейшей эксплуатации устанавливается после разборки станка. Только к отдельным деталям и сборочным единицам, непригодность которых не вызывает сомнений, могут применяться способы ускоренной разборки (вырубание бронзовых втулок, резка ацетиленокислородным пламенем изломанных элементов и др.).
Наибольшую трудность представляет разборка прессовых соединений деталей, главным образом валов с зубчатыми колесами и тормозными шкивами. Для расспресовки (и запрессовки) деталей в труднодоступных местах применяют переносные ручные гидравлические и винтовые домкраты или гидравлические цилиндры, монтируемые на специальном приспособлении.
Такие детали, как подшипники качения и их внутренние кольца, полумуфты, тормозные шкивы и шестерни снимают с валов с помощью разного рода винтовых и гидравлических съемников. Внутренние кольца конических и роликовых подшипников снимают с помощью индукционных съемников, предварительно нагревающих кольца. Частичную разборку станка для мелких ремонтов и замены неисправных деталей часто производят непосредственно в забое.
До начала разборки следует подготовить рабочее место в виде площадки необходимых размеров, сделать настил из досок или расстелить брезент для обеспечения чистоты и сохранности демонтируемых деталей, подготовить необходимый инструмент и приспособления, ванны и керосин для промывки деталей, а также обтирочный материал.
При разборке редукторов и зубчатых передач рекомендуется придерживаться следующей последовательности. Выпустить из редуктора смазку, отвернуть болты и снять крышки, отсоединить и снять вилки и тяги, снять скобы, служащие для крепления подшипников, после чего приступить к демонтажу валов.
Целесообразно демонтировать сначала легкие, а затем тяжелые валы. Вал в сборке следует демонтировать так, чтобы ось вала осталась параллельной первоначальному положению, т. е. перемещалась поступательно. Для вывода зубчатых колес из зацепления вынимаемый вал в сборе следует слегка проворачивать. Для демонтажа тяжелых валов в сборе необходимо пользоваться грузоподъемными средствами и соблюдать необходимую осторожность. После демонтажа сборок валов в случае необходимости приступают к их разборке на отдельные детали.
При снятии деталей не разрешается ударять непосредственно по ним молотком или кувалдой. Необходимо пользоваться прокладками из меди, твердого дерева или применять специальные выколотки.
При разборке соединений, имеющих регулировочные прокладки, следует привязывать их проволокой к деталям, с которыми они устанавливаются, во избежание лишней регулировки при сборке.
При демонтаже однорядных радиальных роликоподшипников обязательно хранить вместе (комплектно) их наружное и внутреннее кольцо во избежание смешивания их с кольцами других подшипников того же номера, что недопустимо, кроме того, следует помечать места установок одинаковых номеров шарико – и роликоподшипников.
Гайки и болты необходимо отвинчивать только гаечными ключами. Пользоваться зубилом или молотком для этой цели воспрещается.
Для выявления степени износа демонтированных деталей их тщательно промывают и обезжиривает.
Для мойки деталей буровых станков применяют горячие водные растворы щелочи. Простейшим устройством для мойки деталей является ванна, изготовляемая из листовой стали и снабженная кранами и металлической решеткой расположенной на 200–300 мм выше дна.
Промышленная безопасность
К работе по профессии слесарь по обслуживанию буровых установок допускаются лица не моложе 18 лет, прошедшие медицинское освидетельствование и не имеющие противопоказаний по состоянию здоровья, профессиональную подготовку в специализированных организациях, стажировку на рабочем месте, прошедшие инструктаж на рабочем месте и проверку знаний в объёме настоящей Инструкции, имеющие удостоверение на право допуска к работе. Слесарь по обслуживанию буровых должен иметь I квалификационную группу по электробезопасности.
По окончанию работы:
· Необходимо выключить станок и привести в порядок рабочее место.
· Рабочий инструмент и приспособления следует убрать в отведенное для хранения место или сдать в кладовую.
· Очистить одежду, обувь. Обдувать одежду, пол, оборудование сжатым воздухом запрещается.
· Проверить исправность всех узлов и деталей. При невозможности устранения неисправностей своими силами доложить о них руководителю работ.
· Уходя с рабочего места, необходимо сообщить сменщику или руководителю работ обо всех имеющихся неполадках в работе и о мерах, принятых к их устранению.
· По завершении всех работ следует вымыть теплой водой с мылом (моющими пастами и т.п.) руки и лицо, при возможности принять душ.
Слесарь по обслуживанию буровых установок при работе на опасных производственных объектах обеспечивается сертифицированными средствами индивидуальной защиты, смывающими и обезжиривающими средствами.
Специальная одежда, специальная обувь, другие средства индивидуальной защиты выдаются слесарю по обслуживанию буровых установок в соответствии с «Типовыми нормами бесплатной выдачи специальной одежды, специальной обуви и других средств индивидуальной защиты работникам нефтяной промышленности, занятым на работах с вредными и (или) опасными условиями труда, а также на работах, выполняемых в особых температурных условиях или связанных с загрязнением», утверждёнными приказом Минздравсоцразвития Российской Федерации от 09.12.2009 г. № 970н.
Спецодежда, предназначенная для использования на взрывопожароопасных объектах (взрывопожароопасных участках производства), должна быть изготовлена из термостойких и антистатичных материалов.
Слесарь по обслуживанию буровых установок должен добросовестно выполнять свои трудовые обязанности, правила внутреннего трудового распорядка предприятия, установленные режимы труда и отдыха и трудовую дисциплину. Запрещается употреблять спиртные напитки, находиться в состоянии алкогольного или наркотического опьянения на территории предприятия или на объекте.
Слесарь по обслуживанию буровых установок не реже 1 раза в квартал должен проходить повторный инструктаж и одного раза в год − проверку знаний.
В особых случаях, вызванных производственной необходимостью, должен проводиться внеплановый инструктаж.
Внеплановый инструктаж слесарям по обслуживанию буровых проводится:
• при введении в действие новых или переработанных стандартов, правил, инструкций по охране труда, а также изменений к ним;
• при изменении производственного (технологического) процесса, замене или модернизации оборудования, приспособлений и инструмента, материалов или других факторов, влияющих на производительность труда;
• при нарушении работниками требований безопасности труда, которые могут привести или привели к травме, аварии, взрыву, отравлению;
• по требованию органов надзора.
Слесарь по обслуживанию буровых установок, работающий в составе вахты, должен быть обучен и проинструктирован по безопасному ведению всех видов работ, выполняемых бригадой.
Слесарь по обслуживанию буровых установок должен выполнять только те работы, которые на него возложены.
При производстве работ на слесаря по обслуживанию буровых установок могут оказать вредное влияние следующие производственные факторы:
· нефть, нефтяной попутный газ, сероводород;
· горюче смазочные материалы;
· химические реагенты;
· движущиеся машины и механизмы, вращающиеся части оборудования, падение предметов с высоты;
· шум, вибрация;
· поражающее действие электрического тока;
· климатические условия.
Ответственность за готовность к применению средств индивидуальной защиты несёт технический руководитель предприятия, за правильность их использования непосредственно на месте проведения работ − исполнитель работ.
Эксплуатация неисправного оборудования, механизмов, инструмента, приспособлений, пользование непригодными средствами индивидуальной защиты, а также работа при снятых или неисправных ограждениях запрещается.
При работах на скважинах, интенсивно выделяющих газ, во избежание искрообразования, необходимо пользоваться ударным инструментом из цветного металла или обмеднённым, а режущий инструмент − обильно смазывать литолом или солидолом.
Заключение
Буровыестанки - один из видов нефтегазового оборудования, является комплексом оборудования и буровых сооружений, предназначенных для бурения нефтегазовых скважин. Буровые станки для разработки и разведки нефтяных и газовых месторождений в общем виде включают в себя:
- Спускоподъемное оборудование (кронблок, лебедка, крюкоблок)
- Циркуляционное оборудование (буровые насосы, вертлюги, емкости, манифольды)
- Буровые сооружения (буровые вышки, мостики, основания вышки, стеллажи)
- Противовыбросное оборудование - Оборудование для приготовления буровых растворов (шламовые насосы, гидроворонки, гидромешалки)
- Силовое оборудования для привода лебедки, буровых насосов, ротора (дизельные двигатели, электрические двигатели)
Таким образом, буровые установки характеризуются:глубиной и диаметрами буримых скважин, грузоподъёмностью, мощностью двигателей и др.
Буровая установка оснащается контрольно-измерительной аппаратурой, обеспечивающей непрерывный контроль за режимом бурения (осевая нагрузка на породоразрушающий инструмент и частота его вращения, скорость бурения, количество и давление промывочного агента, подаваемого в скважину).
Список литературы
1. Лобкин А.Н. Обслуживание и ремонт буровых установок. - М.: Недра, 2014. - 320 с.
2. Буровая установка: Джесси Рассел — Санкт-Петербург, Книга по Требованию, 2013 г
3. Инженерно-техническое творчество в нефтегазовой отрасли: С. В. Елкин, Д. А. Гаврилов — Москва, Центр стратегической кон, 2014 г.
4. Нефтяная промышленность России-сценарии сбалансированного развития: В.В. Бушуев — Москва, Книга по Требованию, 2010 г
5. Лесецкий В.А., Ильский А.Л. Буровые машины и механизмы: Учебник для техникумов. - М.: Недра, 2016. - 391 с
6. Ганджумян Р.А., Фролова М.С. Буровые машины и механизмы. Учебное пособие. – М: РГГРУ, 2011.
7. Давиденко А.Н., Игнатов А.А. Абразивно-механическое ударное бурение скважин. Монография. - Днепропетровск: НГУ, 2013. – 110 с.
8. Ефимов Я., Корнишин К., Стрелецкая В., Урычева М. Уменьшение времени и затрат на бурение разведочных и эксплуатационных скважин путем оптимизации параметров бурения М.: РГУ нефти и газа им. Губкина, 2012. — 20 с.
9. Заливин В.Г. Аварии при бурении нефтегазовых скважин Иркутск : ИРНИТУ, 2015. — 278 с.
10. Кузнецов В. С. Обслуживание и ремонт бурового оборудования. М., «Недра», 2016, 344 с.
Дата добавления: 2018-06-27; просмотров: 2331; Мы поможем в написании вашей работы! |
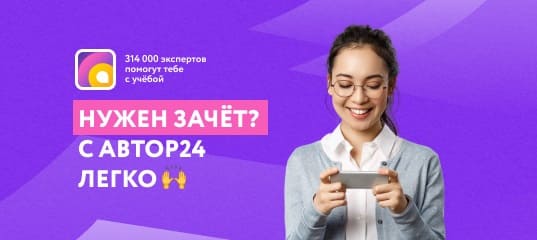
Мы поможем в написании ваших работ!