Основные виды дефектов бурового станка
Nbsp;
Содержание
Введение............................................................................................ 4
1.Виды и причины износа................................................................ 6
2.Основные виды дефектов бурового станка.................................. 14
3. Методы обнаружения неисправностей станков.......................... 16
3.1 Метод пробного включения и осмотра..................................... 16
3.2 Акустический метод................................................................... 16
3.3 Метод измерения........................................................................ 17
3.4 Радиационный метод.................................................................. 18
3.5 Оптический метод....................................................................... 19
3.6 Магнитный метод....................................................................... 19
4. Технология ремонта..................................................................... 21
5. Промышленная безопасность...................................................... 24
Заключение....................................................................................... 26
Список литературы.......................................................................... 29
Введение
В последние годы добыча полезных ископаемых открытым способом возрастает высокими темпами и осуществляется на горных предприятиях различной мощности и с весьма разнообразными горно-геологическими условиями. Это обусловливает большое количество и разнообразие типов и моделей горных машин отечественного и зарубежного производства, применяемых на разрезах и карьерах.
На разрезах для бурения взрывных скважин создаются высокопроизводительные буровые установки. К ним относят, прежде всего, станки шарошечного бурения, которые выполняют основные объемы бурения на разрезах.
|
|
Внедрение сложных по конструкции буровых станков требует систематического повышения квалификации и уровня технических знаний рабочих. Полноценное использование современных буровых установок возможно только при наличии глубоких знаний по устройству каждой машины, ее регулировке, смазке, ремонту и т.п.
Вместе с тем опыт эксплуатации горных машин и оборудования показывает, что используются они недостаточно эффективно. Значительные простои машин приносят огромные убытки и объясняются недостатками в организации горных работ, нарушением действующей системы технического обслуживания и ремонта, ее несовершенством.
Многообразие используемых машин на горных предприятиях, различные срок службы и ресурсы, необходимость в своевременной остановке машин на техническое обслуживание и ремонт без ущерба для основного производства, обеспечение в необходимых количествах запасными частями, эксплуатационными материалами, топливом, маслами, оборудованием для ремонта делают чрезвычайно сложным управление системой эксплуатации и ремонта.
|
|
Цель: изучение вопросов связанных с обслуживанием буровых станков
Задачи:
· Выявить виды и причины износа
· Рассмотреть методы обнаружения неисправностей
· Ознакомиться с технологией ремонта
· Рассмотреть промышленную безопасность
Виды и причины износа
Движущаяся деталь работающего механизма всегда соприкасается с какой-либо другой деталью. Детали в этом случае называются трущимися парами, а их соприкасающиеся поверхности – трущимися поверхностями.
На преодоление сил трения затрачивается значительная энергия, которая обычно составляет более 20 % всей энергии, затрачиваемой на работу машины. Эта величина зависит от ряда причин: вида материала трущихся поверхностей; чистоты их обработки; усилий, прикладываемых к рассматриваемому узлу; наличия и качества смазки и пр.
Элементы машины могут сопрягаться между собой подвижно – с зазорами или неподвижно – с натягом. В процессе работы эти соединения теряют свои первоначальные качества: элементы истираются, ржавеют, изгибаются и т.п., материал стареет, уплотняется, деформируется или меняет структуру под воздействием температуры. При работе соединения, как правило, ослабляются, а при небрежном обращении возможно корродирование металла и снижение подвижности элементов.
|
|
При износе закаленных, особенно цементированных, деталей снижается их твердость. В некоторых случаях бывает наоборот – приобретаемый деталью наклеп приводит к повышению ее твердости и хрупкости.
В зависимости от скорости протекания физический износ подразделяется на естественный и аварийный.
Естественный износ – износ, который нарастает постепенно в течение длительного времени. Он является следствием работы сил трения или других факторов (температуры, влажности, абразивности и т.д.), связанных с нормальными условиями эксплуатации, и имеет место при самом тщательном выполнении технических требований по уходу за машиной.
Аварийный износ – внезапная или ускоренная поломка или деформация элементов машин в результате неправильной эксплуатации, из-за конструктивных недостатков или внутренних пороков материала.
Аварийный износ, как и любой другой износ, может быть механическим или коррозионным. Он наступает значительно раньше естественного, а величина его достигает таких размеров, при которых дальнейшая эксплуатация машины или ее элемента недопустима или невозможна.
|
|
Наиболее характерные причины, вызывающие аварийный износ, следующие:
· нарушение нормального режима работы станка (перегрузка, нарушение правильного взаимодействия частей, ослабление крепления болтов, шпонок и т.п.);
· неправильный режим смазки (отсутствие смазки, несоответствие сортов смазки, неправильные нормы смазки);
· несвоевременная очистка механизма от грязи и абразивных
частиц;
· несвоевременная замена износившихся деталей или недоброкачественный ремонт;
· низкое качество материала деталей;
· усталостные явления в материале деталей;
· некачественное изготовление деталей;
· неправильная сборка механизма;
· неправильная организация горного производства (поломки при взрывных работах и пр.);
· стихийные бедствия.
При правильной организации плановых ремонтов и правильной эксплуатации оборудования аварийные износы происходят редко.
В буровых станках чаще всего наблюдается механический износ, возникающий под действием сил трения. Механический износ наступает в результате возникновения в поверхностном слое металла напряжений, способных вызвать остаточные деформации. Износ ускоряется окислительными процессами.
Коррозиейназывается разрушение металлических частей машин под действием окружающей среды. Коррозионное разрушение протекает под воздействием воды, воздуха или химических веществ. Оно начинается с поверхности и постепенно распространяется в глубь металла. Наиболее распространенным видом коррозии является ржавение.
Коррозия может проявляться в равномерном разъедании всей поверхности детали, в образовании глубоких пороков отдельных ее мест и в межкристаллическом разъединении металла по всему сечению.
В результате коррозионных процессов детали теряют металлический блеск, покрываются слоем ржавчины. Главной же опасностью является потеря чистоты обработки полированных деталей, для нормальной работы которых необходима зеркальная их поверхность (гидро- и пневмоцилиндры и др.). На деталях, изготовленных из малоуглеродистых сталей, их поверхность может приобрести губчатую структуру, теряя первоначальную прочность.
Коррозионный износ является чаще всего медленным процессом, однако некоторые детали могут выходить из строя достаточно быстро.
Наиболее изнашиваемым узлом буровых станков является буровой инструмент, который непосредственно взаимодействует с горными породами и работает в скважине, т.е. режущие и шарошечные долота, а также пневмоударники и буровые коронки для пневмоударного бурения.
На износ режущего инструмента при бурении существенное влияние оказывают физико-механические свойства горных пород, материал режущего инструмента (резца), его геометрия, режим резания, режим нагрева и теплоотдачи, конструкция коронки и др.
Для режущего инструмента установлено, что интенсивность изнашивания пропорциональна длине пути, пройденного резцом в контакте с породой. При этом в начале пути происходит интенсивное микровыкрашивание и скругление лезвия и постепенно формируется рабочая геометрия резца. После окончания этого процесса интенсивность изнашивания не увеличивается, а геометрия остается практически постоянной.
Зависимость износа режущего бурового долота от пути трения носит прямолинейный характер, и вид ее не зависит от величины осевого усилия. Однако абсолютная величина износа в единицу времени увеличивается при увеличении осевого усилия. Разрыв сплошности забоя обеспечивает снижение интенсивности износа инструмента за счет снижения прочностных свойств породы. Для режущих буровых долот со сплошной режущей кромкой существенное значение имеет форма режущей кромки, обеспечивающая равномерный ее износ. Для долот, оснащенных съемными резцами, важно обеспечить вписывание резцов в выбуриваемые ими канавки.
Существенное влияние на износостойкость режущего бурового инструмента оказывают процессы, связанные с его нагревом, и режим бурения. Количество тепла, образующегося на поверхности трения, увеличивается с увеличением площади износа, а количество отводимого тепла ограничено теплопроводностью материала долота и неблагоприятными условиями его охлаждения. Применение охлаждения благоприятно сказывается на работе инструмента. За счет крайне низкой теплопроводности горных пород до 20 % тепла поглощается инструментом. Температура режущего бурового долота достигает 450–500 °С. При бурении с продувкой воздухом даже незначительное уменьшение скорости воздушного потока влечет за собой быстрое нарастание температуры режущего инструмента.
Наряду с износом режущих кромок значительному износу подвергаются и боковые грани долот, не соприкасающиеся с породой забоя, причем даже тогда, когда они не соприкасаются и со стенками скважины. Очевидно, что главной причиной износа боковых граней долота в этом случае является их взаимодействие с буровой мелочью, заполняющей скважину.
Износ долота, происходящий вследствие его взаимодействия с буровой мелочью, называют вторичным износом в отличие от износа, происходящего от взаимодействия с породой забоя, который можно считать первичным износом.
Вторичный износ приводит к уменьшению диаметра корпуса, а также к обнажению режущих элементов (резцов или пластинок твердого сплава), их отрыву, и, в конечном счете, к преждевременному выходу долота из строя. Вторичному износу могут подвергаться наряду с корпусом и резцы. Для долот, оснащенных съемными резцами, износостойкость корпуса должна быть в несколько раз больше износостойкости резцов, т. е. вторичный износ в этом случае должен быть минимальным. Однако при испытаниях долот фиксировался износ, как резцов, так и корпуса. При бурении скважин с очисткой их сжатым воздухом корпуса режущих долот изнашиваются незначительно, хотя износ резцов в ряде случаев достаточно велик.
Шарошечные долота теряют работоспособность по причине износа их вооружения или опор. Могут быть аварийные выходы долот из строя вследствие выкрашивания твердого сплава или заклинивания опор. В первом случае это свидетельствует о некачественной пайке твердого сплава, а во втором – о засорении продувочных отверстий, заводских дефектах подшипников или высоких осевых усилиях. Кроме того, преждевременный выход из строя вооружения долот может свидетельствовать о несоответствии типа долота буримым породам.
Данные, полученные при бурении взрывных скважин, показывают, что стойкость шарошечных долот зависит от выбора типа долота, режима бурения и качества выпускаемых долот.
Стойкость долот принято выражать двумя показателями: стойкость по вооружению и стойкость по опорам. На стойкость по вооружению оказывают влияние как крепость, так и абразивность буримых пород. У зубчатых долот в основном разрушаются периферийные венцы шарошек от пластических деформаций, выколов и абразивного износа. Вооружение в этих долотах довольно быстро выходит из строя, особенно вершины и периферийные венцы, работающие в наиболее трудных условиях. Средние венцы шарошек работают в более благоприятных условиях и поэтому меньше изнашиваются, хотя и на них имеются сколы металла, обусловленные некоторыми факторами изготовления долот с фрезерованным вооружением.
Стойкость штыревых долот в значительной степени определяется качеством запрессовки штырей. При слабой запрессовке штыри выпадают на забой, разрушают долото и приводят к выходу его из строя. Если штыри запрессованы очень туго, то остаточные напряжения в комплексе с динамическими нагрузками, возникающими при разрушении забоя, приводят к поломкам штырей и резкому снижению производительности долота.
Комбинированные шарошечные долота содержат в себе элементы зубчатых и штыревых долот. Вследствие различной износостойкости штырей и легированных зубьев последние разрушаются значительно быстрее. После этого вся нагрузка ложится на оставшуюся часть штырей, долото начинает работать с большими вибрациями и часто выходит из строя из-за динамических перегрузок. Все же следует отметить, что комбинированные долота в диапазоне пород с коэффициентами крепости f =7÷14 значительно более стойкие, чем зубчатые и даже штыревые долота.
Анализ износа вооружения штыревых долот показывает, что срабатываются твердосплавные зубки, обрабатывающие забой, а калибрующие зубки изнашиваются незначительно. Интенсивный износ вооружения обычно наблюдается в крепких абразивных породах. При этом причиной выхода из строя вооружения является не только абразивный износ, но и скол зубков. В результате износа зубков происходят постепенное уменьшение контактной нагрузки на породу забоя и снижение механической скорости бурения.
При бурении в крепких породах наряду с износостойкостью зубки вооружения должны обладать достаточной вязкостью, так как они работают при больших изгибающих и ударных нагрузках. Этим требованиям в большей степени соответствует твердый сплав марки ВК-15, который более пластичен, чем сплав марки ВК-8В.
В ряде случаев отработанные серийные долота имеют спинки и козырьки лап, изношенные до обнажения тел качения периферийных подшипников. Одной из причин этого является недостаточная производительность компрессоров буровых станков. Иногда изнашиваются до обнажения опор вершины шарошек, которые работают в весьма тяжелых условиях, особенно при бурении крепких и абразивных пород.
Анализ наработки шарошечных долот на горных предприятиях показывает, что до 80 % общего количества используемых шарошечных долот выходят из строя в результате износа их опор, т. е. стойкость шарошечных долот в настоящее время определяется главным образом стойкостью их опор.
На стойкость шарошечных долот по опорам, которая значительно меньше нормальной долговечности подшипников, большое влияние оказывают абразивные свойства разрушаемых горных пород. Основной причиной выхода долот из строя по этому показателю является проникновение породной мелочи через зазор между шарошкой и лапой в полость подшипников. Пыль, проникая в элементы подшипников, поглощает смазку и спрессовывается. Затем наступает нагрев и заклинивание шарошки. Заклиненные шарошки быстро изнашиваются вследствие истирания о забой. Самое качественное долото выходит из строя в крепких породах через 10–15 м после забивания буровой мелочью опор шарошек.
Если же пыль, попадающая в подшипник, абразива, то она интенсивно изнашивает тела качения и дорожки на шарошке и цапфе. В этом случае заклинивание шарошек на цапфе, как правило, не происходит, а долото выходит из строя из-за износа подшипников и нарушения вследствие этого нормального режима бурения. Стойкость долот, имеющих опоры по схеме ролик–шарик–ролик, больше чем долот с опорами по схеме шарик–шарик–ролик. В крепких породах опоры шарик–шарик–ролик быстрее разрушаются, но с возрастанием частоты вращения (при бурении пород средней крепости и ниже) они более устойчивы. Опорные поверхности (дорожки) цапф изнашиваются в большей степени, чем опорные поверхности шарошки. Особенностью работы опорных поверхностей цапф является их одностороннее нагружение.
Перекашивание шарошки и возникающее в связи с этим неравномерное распределение нагрузки также отражается на работе опор. В результате перекашивания только часть дорожек цапфы участвует в работе. Это приводит к образованию сравнительно высоких удельных давлений на контактных поверхностях, интенсивному их изнашиванию и не позволяет эффективно использовать рабочую поверхность беговых дорожек.
Основными видами износа опорных поверхностей цапф являются выкрашивание и сколы, осповидный и абразивный износ. Во всех случаях выкрашиванию и сколу предшествует возникновение мелких трещин, расположенных в зоне максимальных контактных нагрузок.
Большинство трещин располагается почти перпендикулярно к направлению движения опорных элементов.
Износ тел качения (шариков и роликов) определяется конструктивными особенностями долот. В ряде случаев изношенные тела качения не теряют своей формы и имеют относительно гладкую поверхность. Изменение формы, раскалывание и выкрашивание шариков и роликов – результат высоких контактных напряжений и зажима. Появление расколотых тел качения способствует перегрузке оставшихся целых и ускоряет их износ и раскалывание.
Незначительный естественный или аварийный износ, если его своевременно не устранить, в конечном счёте, может привести к серьёзным отказам, приводящим к длительному простою. Поэтому своевременное обнаружение возникающих отказов и правильная диагностика имеют важное значение для предупреждения длительных простоев машин на ремонтах и способствуют его высокой эффективности.
Основные виды дефектов бурового станка
Диагностирование буровых станков производится с целью оценки их технического состояния, как в период расчетного срока службы, так и выработавших свой расчетный ресурс. Внеочередное обследование буровых установок проводят в следующих случаях:
• если в процессе эксплуатации наблюдается неоднократное появление дефекта в узлах металлоконструкций и механизмах;
• при наличии деформаций, возникающих в результате высокихдинамических нагрузок, пожара и т.п.;
• если буровая установка подлежит перемонтажу или реконструкции.
Основные виды дефектов буровых станков:
1. Деформации
2. Вмятины;
3. Трещины
4. Коррозия;
Деформация - изменение формы и размеров тела под действием внешних сил.Деформация и излом возникают при чрезмерном увеличении напряжений в материале конструкции, превосходящих соответственно предел текучести или предел прочности.
Вмятина-местное углубление различной величины и формы с пологими краями
.
Трещина-дефект поверхности, представляющий собой разрыв металла, идущий вглубь под прямым углом к поверхности, образовавшийся вследствие напряжений, связанных со структурными превращениями или неравномерным нагревом или охлаждением.
Коррозия - это самопроизвольное разрушение металлов и сплавов в результате химического, электрохимического или физико-химического взаимодействия с окружающей средой
Дата добавления: 2018-06-27; просмотров: 2185; Мы поможем в написании вашей работы! |
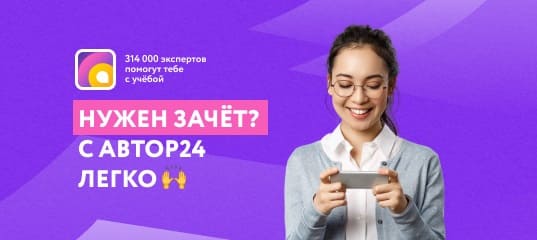
Мы поможем в написании ваших работ!