Определение категории участков производственного объекта по взрывопожарной и пожарной опасности
В зависимости от места расположения технологического оборудования следует определить категорию производственного помещения, зданий и наружных установок по взрывопожарной и пожарной опасности, согласно СП 12.13130.2009
Определение категорий помещений В1-В4 осуществляют путём сравнения максимального значения удельной временной пожарной нагрузки (далее-пожарная нагрузка) на любом из участков с величиной удельной пожарной нагрузки, приведённой в таблице Б.1.
Таблица Б.1- Удельная пожарная нагрузка и способы размещения для категорий В1-В4
Категория помещения | Удельная пожарная нагрузка на участке МДж*м | Способ размещения |
В1 | Более 2200 | Не нормируется |
В2 | 1401-2200 | В соответствии с Б.2 |
В3 | 181-1400 | В соответствии с Б.2 |
В4 | 1-180 | На любом участке пола помещения площадь каждого из участков пожарной нагрузки не более 10м. Способ размещения участков пожарной нагрузки определяется согласно Б.2 |
В помещениях категорий В1-В4 допускается наличие участков с пожарной нагрузкой, не превышающей значений, приведённых в таблице Б.1. В помещениях категорий В4 расстояние между этими участками должны быть более предельных. В таблице Б.2 приведены рекомендуемые значения предельных расстояний Iпр в зависимости от величины критической плотности падающих лучистых потоков qкр, кВт*м-2, для пожарной нагрузки, состоящей из твёрдых горючих и трудно горючих материалов. Значения Iпр, приведённые в таблице Б.2, рекомендуются при условии, если Н>11 м; если Н<11 м, то предельное расстояние определяется как I=Inp+(11-H), где Iпр-определяется из таблицы Б.2; Н-минимальное расстояние от поверхности пожарной нагрузки до нижнего пояса ферм перекрытия (покрытия), м.
|
|
Таблица Б.2- Значения предельных расстояний Iпр в зависимости от критической плотности падающих лучистых потоков qкр.
qкр, кВТ*м | 5 | 10 | 15 | 20 | 25 | 30 | 40 | 50 |
Iпр, м | 12 | 8 | 6 | 5 | 4 | 3.8 | 3.2 | 2.8 |
Значения qкр для некоторых материалов пожарной нагрузки приведены в таблице Б.3.
Таблица Б.3- Значение qкр для некоторых материалов пожарной нагрузки
Материал | qкр,кВт*м |
Древесина (сосна влажностью 12%) | 13.9 |
Древесно-стружечные плиты (плотностью 417 кг*м) | 8.3 |
Торф брикетный | 13.2 |
Торф кусковый | 9.8 |
Хлопок-волокно | 7.5 |
Слоистый пластик | 15.4 |
Стеклопластик | 15.3 |
Пергамин | 17.4 |
Резина | 14.8 |
Уголь | 35 |
Рулонная кровля | 17.4 |
Сено, солома (при минимальной влажности до 8%) | 7 |
Разработка инженерно-технических решений по обеспечению взрывопожаробезопасноститехнологического процесса.
|
|
Разработка мероприятий, направленных на предотвращение пожара:
1)Применение устройств защиты производственного оборудования, исключающих выход горючих веществ в объём помещения,или устройств, исключающих образование в помещении горючей среды [9], [10];
2)Поддержание безопасной температуры нагрева веществ , материалов и поверхностей, которые контактируют с горячей средой [9];
3)Применение способов и устройств ограничения энергии искрового разряда в горючей среде до безопасных значений [10];
4) Устройство молниезащитызданий, сооружений, строений и оборудования [9]
5)Применение электрооборудования, соответствующего классу пожароопасной и (или) взрывоопасной зоны,категории и группе взрывоопасной смеси
6)Механизация и автоматизация технологических процессов, связанных с обращением горючих веществ [9];
7)Установка пожароопасного оборудования в отдельных помещениях или на открытых площадках [9];
8)Применение оборудования и режимов проведения технологического процесса, исключающих образование статического электричества [9], [10].
Разработка мероприятий, направленных на противопожарную защиту
|
|
Способы противопожарной защиты следующие:
1)Устройство аварийного слива пожароопасных жидкостей и аварийного стравливания горючих газов из аппаратуры;
2)Устройство на технологическом оборудовании систем противовзрывной защиты;
3)Применение средств, обеспечивающих ограничение распространения пожара за пределы очага.
Расчет инженерно-технических решений, направленных на обеспечение пожарной безопасности технологического процесса.
Расчет размеров сливных отверстий.
По заданным исходным определить начальные расходы Qi, м3/c, жидкости из аппарата через отверстия, равные сечению трубопроводов, расположенных на аппарате, по формуле :
i ,м3/с
где =0,65-коэффициент истечения жидкости через отверстие;
i-площадь сечения i-го трубопровода м2
g-ускорение силы тяжести, равное 9,81 м/с2
Hi-высота уровня жидкости над i-м трубопроводом.
По наибольшему из вычисленных начальных расходов Qм выбрать площадь отверстия в аппарате и высоту уровня жидкости над ним Н0.
Из конструктивных соображений выбрать площадь поддона Fп, м2.
Вычислить объём жидкости, поступающей в поддон в единицу времени от установки пожаротушения ( с учетом выгорания горючей жидкости) Q0, м3/с, по формуле:
|
|
где- плотность огнетушащей жидкости , кг/м3
При отсутствии данных по скорости выгорания W следует положить равной нулю.
Интенсивность утечек паров и газов , выходящих из работающих под давлением герметичных аппаратов используется формула:
Интенсивность утечек паров и газов из работающего под давлением герметичного оборудования определяют по формуле:
где - интенсивность выхода паров из аппарата, Кг/с
Где IP- интенсивность выхода паров или газа из аппарата кг/с;
К- коэффициент , учитывающий степень износа производственного оборудования , принимается в пределах от 1 до 2;
C- коэффициент , зависящий от давления паров или газов ;
V- внутренний (свободный объём аппаратов и коммуникаций, находящихся под давлением, м3);
M- молекулярный вес газов или паров , находящихся под давлением в аппаратах ;
Траб-температура паров или газов , находящихся в аппаратах К
При т 1 порядок расчета f следующий :
Определить напор , создаваемый сжатыми газами в аппарате :
Где- плотность воды , кг/м3.
Вычислить значение параметра:
где Qmax- максимальный расход жидкости из аппарата определяемый по п.1.2
По b необходимо найти а=18.313;
Рассчитать площадь сливного отверстия f, м3, по формуле: м2
F=2 а δ √Fn/Fa
Ректификация
Ректификация известна с начала XX века как один из важнейших технологических процессов главным образом спиртовой и нефтяной промышленности. В настоящее время ректификацию всё шире применяют в самых различных областях химической технологии, где выделение компонентов в чистом виде имеет весьма важное значение (в производствах органического синтеза, изотопов, полимеров, полупроводников и различных других веществ высокой чистоты). Таким образом, процесс ректификации позволяет решить одну из главных задач химической технологии - выделение целевых продуктов требуемой чистоты.
Процессы перегонки растворов, говоря иначе, разделения растворов на составляющие их компоненты, весьма распространены в современной технологии.
Например, разделение природных углеводородов нефти с целью получения моторных топлив и смазочных масел.
Выделение индивидуальных газов из их смесей происходит путем предварительного их сжижения с последующей разгонкой жидкой смеси.
Подавляющее большинство ЛВЖ и ГЖ (спирт, ацетон, уксусная кислота, бензол и его гомологи, бензин, керосин и многие другие продукты) получаются с использованием также процессов перегонки.
Различают простую перегонку и ректификацию.
Простой перегонкой называется процесс частичного испарения раствора и полной конденсации образующихся паров.
Ректификация же - это процесс разделения жидких однородных смесей на составляющие их компоненты в результате многократного противоточного взаимодействия пара с жидкостью.
Согласно первому закону Коновалова пар обогащается тем компонентом, прибавление которого к жидкости повышает давление пара над ней или понижает температуру кипения.
Идеальные смеси подчиняются закону Рауля, согласно которому парциальное давление компонента в системе равно давлению пара чистого компонента, умноженному на его мольную долю в растворе: Рпарц=Рпараm
И согласно закону Дальтона парциальное давление компонента в газовой смеси равно общему давлению, умноженному на мольную долю этого компонента в смеси: Рпарц=Робщm
Схематично процесс ректификации можно представить следующим образом.
![]() |
Где m1, m2, m3 - количества поступившей на ректификацию смеси, образовавшегося дистиллята и остающегося остатка;
X1, Х2, Х3- содержание (мольная доля) легколетучего компонента в них, соответственно.
Процессы ректификации осуществляют на ректификационных установках.
Ректификационные колонны классифицируют:
по конструктивному исполнению: тарельчатые; насадочные.
в зависимости от рабочего давления: работающие под вакуумом* работающие при атмосферном давлении; работающие под давлением.
Тарелки различают: клапанные; струйные; ситчатые; колпачковые.
Давайте с вами рассмотрим, как осуществляется процесс ректификации.
В среднюю часть колонны поступает подлежащее ректификации сырье, нагретое до определенной температуры.
Сырье может подаваться в колонну в виде жидкости, паров или смеси паров и жидкости.
При входе сырья в колонну происходит процесс однократного испарения, в результате которого образуются пары и жидкость определенного состава, находящиеся в равновесии.
Для обеспечения ректификации необходимо в верхней части колонны навстречу парам организовать поток жидкости (флегмы, орошения). Для этого на верху колонны тем или иным способом отнимается тепло (тепло парциального конденсатора). За счет этого часть паров, поднимающихся с верхней тарелки, конденсируется, образуя необходимый нисходящий поток жидкости.
Флегмовое число - отношение количества возвращаемого в колонну дистиллята (флегмы) к количеству отобранного дистиллята в виде продукта.
В нижней части колонны нужно обеспечить восходящий поток паров. Для этого в низ колонны тем или иным способом подводится тепло (тепло кипятильника) При этом часть жидкости, стекающей с нижней тарелки, испаряется, образуя поток паров.
При таком режиме: самая низкая температура будет вверху колонны, а самая высокая - внизу колонны.
Отбираемый сверху колонны продукт, обогащенный низкокипящим компонентом, называется ректификатом (или дистиллятом). А снизу колонны, отбираемый продукт, обогащенный высококипящим компонентом, называется остатком или кубовым (нижним) продуктом.
Та часть колонны, куда вводится сырье, называется секцией питания или эвапорационным пространством. Часть ректификационной колонны, находящаяся выше ввода сырья - верхней, концентрационной или укрепляющей, а ниже ввода сырья - нижней, отгонной или исчерпывающей.
В обеих частях колонны протекает один и тот же процесс ректификации.
На данном рисунке показана схема простых (I) и сложных (II) колонн:
a) - полная; b) - укрепляющая; c) - отгонная; d) - с отбором дополнительных продуктов сверху и снизу из основной колонны; e) - с отбором дополнительного продукта сверху из отпарной колонны.
Азеотропная ректификация. Для некоторых бинарных смесей кривые равновесия у* =f(x) при определенных условиях пересекают диагональ у-х -диаграммы; в точке пересечения составы пара и жидкости одинаковы (азеотропная смесь), вследствие чего подобные смесиобычной Р. разделить невозможно. Поэтому к исходной смеси добавляют растворитель-т. наз. разделяющий агент, образующий с одним из компонентов азеотропную смесь, к-рая при Р. выделяется в виде дистиллята; кубовая жидкость представляет собой высококипящий компонент с миним. содержанием разделяющего агента. Однако его выделение из азеотропной смеси (дистиллята) затруднено. Один из методов, позволяющий осуществить рецикл р-рителя, заключается в применении таких разделяющих агентов, к-рые обладают ограниченной взаимной р-римостью в компонентах, отбираемых в виде дистиллята. При этом благодаря его расслаиванию в разделит, сосуде слой, обогащенный JIJIK, поступает в среднюю часть регенерац. колонны, откуда в результате Р. в виде кубового продукта отбирается JIJ1K исходной смеси, а в виде дистиллята-азеотроп, направляемый в разделит, сосуд.
Экстрактивную Р. используют обычно для разделения смесей близкокипящих компонентов, характеризующихся низкой относит, летучестью а. Разделение таких смесей приходится проводить в колоннах с очень большим числом ТТ и высоким расходом пара из-за необходимости поддерживать большое R. Однако если к исходной смеси добавить практически нелетучий разделяющий компонент, способный повысить а осн. компонентов, разделение можно осуществить в двух ректификац. колоннах. На одну из верх, тарелок первой колонны подается разделяющий агент, к-рыйраств. в потоке флегмы и повышает а смеси, в результате чего в виде дистиллята выделяется ЛЛК, а в виде остатка-смесь ТЛК и разделяющего агента. Эта смесь направляется в середину второй колонны, где, в свою очередь, разделяется на ТЛК (дистиллят) и остаток (разделяющий агент), к-рый возвращается в первую колонну.
Контактные устройства ректификационной колонны (тарелки и насадки).
Отвечают за многократное и одновременное разделение смеси на жидкость и пар с последующей конденсацией пара в жидкость - достижение в колонне состояния равновесия. При прочих равных условиях, чем больше в конструкции контактных устройств, тем эффективнее ректификация в плане очистки спирта, поскольку увеличивается поверхность взаимодействия фаз, что интенсифицирует весь тепломасообмен.
Теоретическая тарелка - один цикл выхода из равновесного состояния с повторным его достижением. Для получения качественного спирта требуется минимум 25-30 теоретических тарелок.
Физическая тарелка - реально работающее устройство. Пар проходит сквозь слой жидкости в тарелке в виде множества пузырьков, создающих обширную поверхность контакта. В классической конструкции физическая тарелка обеспечивает примерно половину условий для достижения одного равновесного состояния. Следовательно, для нормальной работы ректификационной колонны требуется в два раза больше физических тарелок, чем теоретических (расчетных) минимум - 50-60 штук.
Насадки. Зачастую тарелки ставят только на промышленные устан . В лабораторных и домашних ректификационных колоннах в каче контактных элементов используются насадки - скрученная специальным образом медная (либо стальная) проволока или сетки для мытья посуды, этом случае флегма стекает тонкой струйкой по всей поверхности насадки, обеспечивая максимальную площадь контакта с паром.
Производительность. Не зависит от размеров колонны, поскольку, чем выше царга (труба), тем больше физических тарелок находится внутри, следовательно, качественнее очистка. На производительность влияет мощность нагрева, которая определяет скорость движения потоков пара и флегмы. Но при переизбытке подаваемой мощности колонна захлебывается (перестает работать).
Средние значения производительности домашних ректификационных колон - 1 литр в час при мощности нагрева 1 кВт.
Влияние давления. Температура кипения жидкостей зависит от давления. Для успешной ректификации спирта давление вверху колонны должно быть приближено к атмосферному - 720-780 мм.рт.ст. В противном случае при уменьшении давления снизится плотность паров и увеличится скорость испарения, что может стать причиной захлебывания колонны. При слишком высоком давлении падает скорость испарения, делая работу устройства неэффективной (нет разделения смеси на фракции). Для поддержания правильного давления каждая колонна для ректификации спирта оборудована трубкой связи с атмосферой.
Используемая литература
1. ФЭ-123 «Технический регламент о требованиях пожарной безопасности» от 22.07.2008 (ред. 03.07.2016 года).
2. ФЗ-116 «О промышленной безопасности опасных производственных объектов» от 21.07.1997 (ред. 02.06.201 бгода).
3. ГОСТ 12.3.047-2012 ССБТ. Пожарная безопасность технологических процессов. Общие требования. Методы контроля.
4. ГОСТ 12.1.044.-89 ССБТ. Пожаровзрывоопасность веществ и материалов. Номенклатура показателей и методы их определения.
5. СП 12.13130.2009. Определение категорий помещений, зданий и наружных установок по взрывопожарной и пожарной опасности
6. ГОСТ 9.049-91ЕСЗКС. Полимерные материалы и их компоненты.
7. ГОСТ 9.050-75 ЕСЗКС. Покрытия лакокрасочные.
8. ГОСТ 12.1.004-91 ССБТ. Пожарная безопасность. Общие требования.
9. ГОСТ 12.3.046-91 ССБТ. Установки пожаротушения автоматические. Общие технические требования.
10. ГОСТ 4765-73 Материалы лакокрасочные. Метод определения прочности при ударе.
11. ГОСТ 5233-89 Материалы лакокрасочные. Метод определения твердости по маятниковому прибору.
12. ГОСТ 15140-78 Материалы лакокрасочные. Методы определения адгезии.
13. ГОСТ 19433-88 Грузы опасные. Классификация и маркировка.
14. ГОСТ 26952-86 Порошки огнетушащие. Общие технические требования и методы испытаний.
15. ГОСТ 30247.0-94 Конструкции строительные. Методы испытаний на огнестойкость. Общие требования.
16. ГОСТ 30247.1-94 Конструкции строительные. Методы испытаний на огнестойкость. Несущие и ограждающие конструкции.
17. ГОСТ 30247.2-97 Конструкции строительные. Методы испытаний на огнестойкость. Двери и ворота.
18. ГОСТ Р 50680-94 Установки водяного пожаротушения автоматические. Общие технические требования. Методы испытаний.
19. ГОСТ Р 50800-95 Установки пенного пожаротушения автоматические. Общие технические требования. Методы испытаний.
20. ГОСТ Р 50969-96 Установки газового пожаротушения автоматические. Общие технические требования. Методы испытаний.
21. ГОСТ Р 51043-97 Установки водяного и пенного пожаротушения автоматические. Оросители спринклерные и дренчерные. Общие технические
22. Демидов П.Г., Шандыба В.А., Щеглов П.П.. Горение и свойства горючих веществ. - Москва, Химия, 1981.- 272 с.
23. Мельникова Т.В.. Пожарная безопасность технологических процессов.Методические указания по выполнению курсовой работы. — Волгоград :ВолгГТУ, 2016.
Дата добавления: 2018-06-27; просмотров: 277; Мы поможем в написании вашей работы! |
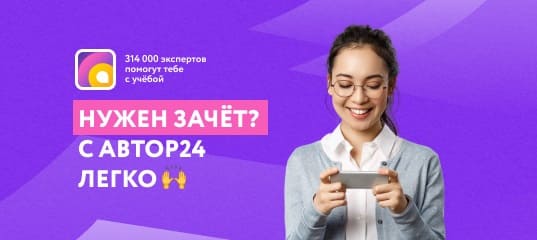
Мы поможем в написании ваших работ!