Скупчення комах і кліщів в одній ділянці насипу.
Шарове самозігрівання зернової маси виникає при зберіганні її в силосах, сховищах, буртах. Називається так тому, що шар зерна, в якому відбувається самозігрівання, міститься в насипі, котрий має вигляд горизонтального або вертикального пласта. Самозігрівання може виникати в нижньому (низове самозігрівання) або верхньому (верхове) шарі насипу, біля стін зерносховища (вертикально-пластове).
Основною причиною шарового самозігрівання є така фізична властивість зернової маси, як термовологопровідність.
Верхове самозігрівання виникає при зберіганні зернової маси переважно в періоди з найбільшим перепадом температури зерна і навколишнього середовища, тобто пізно восени і рано навесні. Горизонтальний пласт зерна, в якому відбувається самозігрівання, розміщений на глибині 0,7-1,5 м від поверхні зернового насипу, а при товщині останнього у сховищі 1-1,5м–на глибині 0,15-0.25 м від його поверхні.
Воно виникає так: восени в зерносховища закладають недостатньо охолоджене свіжозібране зерно з підвищеною фізіологічною активністю. Внаслідок інтенсивного дихання зерна та інших процесів повітря в міжзерновому просторі нагрівається і зволожується. Потоки теплого й вологого повітря піднімаються вгору, стикаючись на своєму шляху з верхніми шарами насипу, які охолоджені холоднішим атмосферним повітрям, внаслідок чого відбувається конденсація водяної пари.
|
|
Навесні і на початку літа, коли внутрішня частина зернової маси має низьку температуру, а верхні її шари прогріваються теплим повітрям, також можливі конденсація водяної пари і посилений розвиток фізіологічних процесів у зерні. Весняне верхове самозігрівання характерне для теплої ранньої весни після зими із сильними морозами. При різкому перепаді температур в цей час спостерігається верхове самозігрівання сухого зерна або зерна, яке довго зберігається.
Низове самозігрівання розвивається у нижньому шарі насипу зерна на відстані 0,2-0,5 м від підлога або основи силосу елеватора. Зазвичай виникає влітку або восени при завантаженні свіжозібраного неохолодженого зерна у склади з холодною підлогою. Таке самозігрівання часто супроводжується проростанням та злежуванням зерна в нижньому шарі насипу і при недогляді може призвести до суцільного самозігрівання.
Вертикально-пластове самозігрівання характерне для зернових мас, які зберігаються в металевих бункерах, силосах елеватора або в сховищах, при зволоженні будь-якої стіни, що контактує із зерновою масою. Виникає у вертикальному шарі зерна на відстані 0,5-0,6 м від стіни. Йому можна запобігти, якщо стіна засіки буде віддалена на 0,5-0,6 м від зовнішньої стіни сховища.
|
|
Суцільне самозігрівання можливе в зерновій масі з високою вологістю і великим вмістом недозрілих зерен та домішок, а також коли осередки самозігрівання не ліквідовано. Колір зерна при цьому змінюється до темно-коричневого і навіть чорного. На початкусамозігрівання (при температурі до 30°С) зерно набуває комірного запаху, незначно темніє, на зародку з'являється плісеневий наліт. Після охолодження і сушіння таке зерно використовують на продовольчі цілі та для підсортовування до зерна нормальної якості.
Під час самозігрівання (температура до 34-38°С) змінюється якість зерна: знижується сипкість, виникають солодовий запах і плісень, найбільш вологі зерна темніють. Таке зерно на продовольчі цілі непридатне, оскільки хлібопекарські якості його значно погіршуються.
При запущеній формі самозігрівання температура зерна підвищується до 50°С і більше. Різко знижується сипкість зернової маси (або вона втрачається зовсім), зерно набуває коричнево-чорного або чорного кольору, виникають затхлий та гнильно-затхлий запахи. Таке зерно непридатне для продовольчих чи фуражних цілей [8].
1.4. Типи сховищ для зберігання зерна та вимоги до них
|
|
Сучасне зерносховище – складна інженерна споруда. Її будують за типовими проектами, які розробляють спеціалізовані проектні організації з урахуванням досягнень науки і кращого досвіду. Більшість сучасних типових проектів зерносховищ передбачають наявність стаціонарних засобів механізації для проведення завантажувально-розвантажувальних і транспортних робіт, установки для активного вентилювання природним і штучно охолодженим повітрям, аерожолобів, а також робочих споруд для приймання насіння з відділенням для протруювання і затарювання, автоматичних вагів.
В Україні є зерносховища таких типів: елеватори й одноповерхові приміщення з горизонтальними або похилими підлогами. Старі склади (за деяким винятком) мають малу місткість (50, 100, 165, 300 т), у багатьох з них немає механізації. Сучасні склади будують за проектами, які передбачають завантаження зерна конвеєрами, використання принципу самопливу зерна. Місткість їх становить 500, 1000, 1300, 1500, 2000, 2300, 3600, 5000 т.
Типове насіннєсховище місткістю 500 т будують з цегли, каменю або дерева. Воно має 21 засіку загальною місткістю 475 т для розміщення партій насіння насипом і майданчик для укладання насіння в мішках загальною масою до 25 т. Засіки роблять із щитів, що виготовлені з підігнаних сухих дощок. Для запобігання нерівномірному обігріванню або охолодженню насіння стіни засіки розміщують паралельно зовнішній стіні складу на відстані 0,5 м від неї. Вікна зсередини обтягують металевою сіткою для захисту від птахів, а двері знизу оббивають сталевими смугами на висоту 0,5 м для захисту від гризунів.
|
|
Насіннєсховище місткістю 1300 і 2300 т з відділеннями для протруювання і затарювання – це одноповерхова будівля секційного типу. Більшість насіння розміщують у засіках по 125 т при висоті насипу 2,5 м. Кожна секція насіннєсховища розрахована на 500 т насіння. Торцеву частину насіннєсховища використовують для роздільного складування протруєного і непротруєного насіння в мішках штабелями на піддонах (усього на 300 т). Крім складів, сховище має відділення для приймання, протруювання і затарювання насіння, які розміщені у двоповерховій будівлі, що прибудована до торця складу.
Процеси завантаження, розвантаження і транспортування насіння у межах сховища механізовано. Механізація здійснюється норіями, верхніми і нижніми стрічковими конвеєрами і підгрібачами насіння. За допомогою транспортної галереї сховище з'єднане з потоковою лінією для післязбиральної обробки насіння.
Зерно надходить по потоковій лінії і подається до норій. Потім воно може бути направлене: на автоматичні ваги і через верхній конвеєр у сховище; на склад непротруєного насіння для зберігання у мішках; на протруювання й затарювання, а потім на склад для протруєного насіння при зберіганні в мішках.
Для того, щоб запобігти самозігріванню і зниженню якості насіння при тривалому зберіганні, кожну засіку насіннєсховища обладнують системою активного вентилювання у вигляді аерожолобів з осьовими вентиляторами СВМ-5М. Аерожолоби є також засобами транспортування насінного матеріалу всередині засіки, забезпечують розвантаження насіннєсховища.
В насіннєсховищі мажна консервувати вологе насіння охолодженим повітрям за допомогою холодильної машини, яка підключається до аерожолобів.
Продуктивність транспортних механізмів на прийманні насіння 20 т/год, при протруюванні в потоці – 10 т/год. Режим роботи двозмінний. Обладнання насіннєсховища складається з двох ковшових однопотокових норій НПЗ-20, зернових ваг Д-100-3, двох мішкозашивних машин ЗЗЕ-М, верхнього і нижнього стрічкових конвеєрів.
Насіннєсховище місткістю 3200 т має два верхніх і два нижніх стрічкових конвеєри. Його будують разом з цехами для обробки насіння, які мають дві самостійні потокові лінії. Розміри зерносховища у плані 72 х 18 м, висота зовнішніх стін 4 м.
Для одночасного розміщення або переміщення двох партій насіння, а також для створення більшої кількості секцій по всій довжині поздовжньої осі насіннєсховища роблять капітальну стіну з цегли заввишки 6 м.
Для механізації завантаження секції насінням та її розвантаження у кожній половині насіннєсховища є два верхніх і два нижніх конвеєри. Верхні конвеєри галереї розміщені на спеціально передбачених прогонах, на яких вільно укладені настили з дощок, а нижні – в нижніх галереях завширшки 2 і заввишки 1,75 м. Стіни зроблено із цегли, а перекриття – із залізобетону. Галереї з'єднані з прорізами у стіні фундаменту для повернення насіння в очисно-сушильну башту на повторну обробку або відвантаження на автомобільний чи інший транспорт. Підземні галереї мають по два виходи через торці складу.
У кожній секції насіннєсховища є канали із цегли з повітророзподільними щитами для активного вентилювання насіння. З боків сховища над каналами зроблено фундаменти для встановлення вентиляторів СВМ-6М.
Транспортне, технологічне і вагове обладнання в очисно-сушильній башті та сховищі розміщене так, щоб запобігти травмуванню насіння та змішуванню під час обробки, транспортування і зберігання. Швидкість руху норійних і конвеєрних стрічок становить 1,4 м/с.
Насіннєсховище з відділенням для очищення насіння переобладнано із зернового типового складу (з цегли або каменю) місткістю 3,2 тис. т. В зерноскладі замість збірних залізобетонних перегородок заввишки 2,5 м зроблено 16 секцій. Загальна місткість насіннєсховища 1100 т. В торці сховища знаходиться відділення для очищення насіння, яке відгороджене глухою стіною від насіннєсховища і має вхід з вулиці. В поперечному напрямку відділення по ширині дверей зроблено чотири суцільних коридори для конвеєрів, які подають насіння на поздовжній конвеєр, що знаходиться у нижній галереї під поздовжнім коридором сховища.
Передбачене також улаштування в секціях сховища переносної щитової для активної вентиляції. Кожна секція є самостійною системою, яка забезпечує необхідне продування насіння вентилятором ВМ-200 з подачею повітря 11-12 тис. м3/год. У сховищі є 8 самостійних вентиляційних систем з необхідним обміном повітря в між зерновому просторі за стану середньої сухості насіння при висоті насипу 2 м.
Склад із збірних залізобетонних елементів найкраще відповідає завданням індустріалізації складського будівництва і має такі переваги: будівництво може здійснюватись незалежно від пори року та скорочення на будівельному майданчику кількості працюючих; високою є якість будівництва із збірних залізобетонних елементів, що виготовляються в заводських умовах; маса будівельних матеріалів зменшується до 35%.
Зерно- і насіннєсховища бункерного типу найбільше поширені як на державних хлібоприймальних підприємствах, так і в господарствах системи Міністерства аграрної політики України.
У сховищах бункерного типу можна повністю механізувати процеси завантаження і розвантаження зерна, вони займають мало місця, в них є можливість складувати зерно і насіння максимально високим насипом та запобігати змішуванню матеріалу.
Бункерне насіннєсховище місткістю 1,5 тис. т має два відділення: одне з металевих блоків бункерів вентилювання загальною місткістю 1,5 тис. т, а друге – для зберігання насіння в мішках. До бункерного сховища з торцевого боку примикає одноповерхова прибудова для зберігання насіння в тарі, де є приміщення для протруювання, затарювання і зважування насіння.
Насіннєсховище складається із 44 бункерів, які встановлені в чотири ряди. В над- і підбункерних поверхах змонтовано по два стрічкових конвеєри, кожний з яких обслуговує по два ряди бункерів. Насіння з цеху на верхні конвеєри подається за допомогою двох норій продуктивністю по 20 т/год.
Конструкцією сховища передбачено консервування насіння з підвищеною вологістю штучно охолодженим повітрям. Для цього бункери активного вентилювання дообладнують системою повітророзподільних труб з холодильною машиною.
Бункерне насіннєсховище місткістю 0,5 тис. т. розроблене для насіннєобробних комплексів і конструктивно складається з металевого або залізобетонного каркаса, всередині якого розміщені в два ряди (по десять у кожному) бункери БВ-25 або К-878. До бункерного насіннєсховища примикає відділення для приймання та очищення насіння, розраховане на одночасну обробку двох партій зерна однієї культури продуктивністю до 40 т/год.
Насіннєсховище розраховане на підсушування вологого насіння з використанням бункерів для активного вентилювання природним підігрітим чи не підігрітим повітрям, а також на очищення некондиційного насіння і тривале його зберігання.
За технологічною схемою очищене насіння подається норією на верхній стрічковий конвеєр і спрямовується у бункери. При розвантаженні його самопливом по трубі воно надходить на нижній стрічковий конвеєр і потрапляє в норію, а потім може бути спрямоване на перевантаження в інші бункери, на додаткову обробку або на відвантажування споживачам.
Насіннєсховища силосного типу – це елеватори із залізобетону і цегли, спеціально побудовані для зберігання насіння, з висотою силосної частини 12-16 м і більше. Як правило, до такого типу сховищ примикає спеціальна башта, де розмішують необхідне обладнання для потокової обробки насіння. У такому сховищі повністю механізовано всі процеси, а в деяких – і автоматизовано.
Насіннєсховище місткістю 3 тис. т. силосне з чотирма рядами збірних залізобетонних елементів промислового виготовлення. Висота силосів 12 м. Можна також побудувати його в комплексі з насіннєобробним цехом.
Підготовлене до зберігання насіння норією продуктивністю 20 т/год подається на автоматичні ваги Д-100-3, потім на верхній стрічковий конвеєр, за допомогою якого надходить у відповідний силос на зберігання. Рівень насіння в силосах, а також його температура контролюються відповідними системами, що розміщені в диспетчерському пункту
Елеватор – це повністю механізоване зерносховище, призначене для зберігання зерна і виконання там необхідних операцій. Сучасний елеватор забезпечує виконання всіх операцій з максимальною ефективністю і надійним забезпеченням збереження зерна. На відміну від складів із стаціонарною механізацією, елеватор досить компактний завдяки великій висоті споруд. Отже, місткість зерносховища на 1 м2 площі різко збільшується. В типових зерносховищах на 1 т місткості припадає 2,5-3 м3 приміщення, а в елеваторах 1,5-1,7 м3.
Елеватор, як повністю механізоване зерносховище, призначений для виконання всіх завантажувально-розвантажувальних робіт, повної технологічної обробки та зберігання зерна. Його можна розглядати як комплексне поєднання основного обладнання та споруд: робоча башта з технологічним і транспортним обладнанням; силосний корпус з транспортним та іншим обладнанням; обладнання для приймання зерна з автомашин, вагонів, суден; обладнання для відпуску зерна на різні види транспорту і зернопереробні підприємства; цех відходів; системи аспірації і видалення відходів.
Робоча башта має висоту 50-65 м, на її поверхах розміщені високопродуктивні зерноочисні машини, аспіраційні пристрої, автоматичні ваги, іноді зерносушарки. Зернові маси зберігаються у силосах заввишки до 30 м і більше. Місткість елеватора залежить від кількості силосів, їх висота й поперечного перерізу. Силоси споруджують з монолітного або збірного залізобетону. Вони бувають циліндричними або прямокутними. Місткість їх найчастіше від 150 до 600 т, тоді як місткість елеваторів – від 27 до 150 тис. т (залежно від цільового призначення і місця розташування).
Технологічні схеми елеваторів різного призначення (заготівельні, млинові, перевалочні, портові) неоднакові. Загальний вигляд схеми руху зерна на елеваторі такий; зернова маса з приймальних точок, вагонів або суден надходить у приймальну яму, розташовану нижче рівня поверхні землі під баштою елеватора. Звідти потужними ковшовими – норіями (100-175 т/год кожна) зерно піднімається у верхню частину башти елеватора, потрапляє на автоматичні ваги, а потім самопливом надходить на зерноочисні машини, розташовані на поверхах башти. Після цього, якщо є потреба, зернова маса направляється у зерносушарку.
Очищене й просушене зерно знову піднімається на верхні поверхи елеватора і розподільними пристроями спрямовується на стрічкові надсилосні конвеєри. Перемішуючись конвеєрами над силосами, зернова маса висипається в призначений для зберігання силос. Із силосу самопливом (після відкриття засувки) зерно йде на стрічки підсилосного конвеєра, а звідси – у спеціальні відпускні силоси та пристрої для навантаження на автомашини, у вагони або судна [4].
2. Технологія післязбиральної обробки і зберігання зерна та насіння
2.1. Підготовка зерносховищ до завантажування
Збереженість насіння залежить не тільки від його вологості, засміченості та зараженості комірними шкідниками, а й від стану приміщень для його зберігання.
Сховища до приймання насіння нового врожаю починають готувати відразу після звільнення їх від насіння або зерна старого врожаю. Період між закінченням весняної сівби і початком дозрівання зернових використовують для ремонту та приведення в повну готовність насіннєсховищ, механізмів, сушарок, зерноочисних машин, інвентарю.
Зернові склади мають бути сухими. В сирих складах насіння легко пошкоджується плісенями, бактеріями, комірними шкідниками. Сирість на складах пов'язана переважно з близькістю ґрунтових вод або з потраплянням води в приміщення через вікна, двері, щілини у стінах, з покрівлі. Для запобігання проникненню у сховище дощової води навколо нього влаштовують водостічні канави. Якщо сиріють стіни, побудовані з цегли або каменю, то їх із середини обшивають дошками або пресованими плитами на висоту насипу насіння, залишаючи між стіною та обшивкою проміжок 10-20 см для циркуляції повітря. Якщо у стінах і підлозі складів є тріщини або щілини, в них накопичується пил, в якому можуть жити комірні шкідники. Тому всі виїмки і щілини в стінах та підлозі законопачують просмоленим ганчір'ям, а великі тріщини зашивають рейками або листовим залізом. Дошки розбірних засік очищають, промивають гарячою водою і добре просушують.
Розбите віконне скло на складах замінюють цілим і з сонячного боку білять вапном або роблять над вікнами невеликі навіси з дощок чи бляхи, щоб захистити насіння від нагрівання сонячним промінням.
Після звільнення складів від насінного матеріалу всі приміщення, інвентар, транспортні засоби очищають від решток насіння та сміття, які спалюють. Після цього проводять хімічну обробку [4].
Заходи захисту хлібних запасів від шкідників поділяють на карантинні, запобіжні та винищувальні. Останні можуть бути хімічними та фізико-нехімічними. До нехімічних заходів належать біологічні, мікробіологічні, термічна дезінсекція, очищення зерна, обробка газовими середовищами, до хімічних – фумігація зерна з використанням різних хімічних засобів.
Карантинні заходи спрямовані на охорону території країни від проникнення із-за кордону карантинних шкідників, збудників хвороб рослин, насіння бур'янів. Ці заходи проводять органи Державної служби з карантину рослин.
Запобіжні заходи спрямовані на запобігання зараженню шкідниками хлібних запасів на хлібоприймальних та зернопереробних підприємствах. Це насамперед заходи, які перешкоджають проникненню шкідників у сховища, додержання правил приймання, розміщення, зберігання, переробки та перевезення зерна, продуктів його переробки і комбікормів. Територію підприємств і сховищ утримують у чистоті. При прийманні зерна і зернопродуктів заражені партії його розміщують окремо. Для зберігання та очищення тари виділяють спеціальні приміщення.
Винищувальні заходи поділяють на дві групи – дезансекції (знищення комах і кліщів) і дератизації (знищення гризунів). До винищувальних належать також біологічні методи, які ґрунтуються на використанні природних ворогів хлібних запасів. Проте застосування цих методів обмежене, оскільки розведення у зерновій масі одних комах для знищення інших зумовлює додаткову засміченість партій зерна, що зберігається.
Мікробіологічний метод, основою якого е використання мікроорганізмів для масового захворювання і загибелі комах і кліщів, вважається перспективним.
Термічна дезінсекція – це вплив на шкідників згубних підвищених (при сушінні) або понижених (при охолодженні) температур. Найбільша її ефективність забезпечується на рециркуляційних зерносушарках.
Найпоширеніші хімічні способи боротьби з шкідниками хлібних запасів. Використовують переважно хімічні препарати, які називаються пестицидами. Основний спосіб застосування пестицидів – фумігація, тобто обробка продукції, що зберігається, газами або твердими речовинами, які утворюють гази. Аерозольну дезінсекцію здійснюють пестицидами у вигляді диму або туману, а вологу – водним розчином або емульсією. Для обробки зерна, що зберігається, і зерносховищ використовують препарати згідно із «Списком хімічних і біологічних засобів боротьби з шкідниками, хворобами рослин і бур'янами, які дозволені в сільському господарстві» у рік проведення боротьби.
Для знищення гризунів ставлять капкани, пастки, різні принади з отрутою, використовують хімічні препарати, природних ворогів гризунів.
За 2-3 тижні до засипання зерна чи насіння нового врожаю проводять знезаражування (дезінсекцію) приміщень свіжогашеним вапном або агрохімікатами (розчинами, аерозолями, емульсіями і суспензіями для вологої дезінсекції та порошкоподібними препаратами); розкладають отруєні принади для знищення гризунів. При цьому можна використовувати агрохімікати згідно із «Списком хімічних і біологічних засобів боротьби з шкідниками, хворобами рослин і бур'янами, які дозволені в сільському господарстві» у рік проведення боротьби.
Вологу дезінсекцію роблять при температурі навколишнього повітря не нижче 12°С. Одночасно з дезінсекцією складів обробляють зовнішні стіни, а також прискладську територію на відстані не менше 5 м і в одні й ті самі строки. Через три доби після проведення вологої дезінсекції об'єкти, що оброблялись, слід добре провітрити і просушити [9].
Насіннєсховища, які можна загерметизувати, найкраще обробляти аерозолями, тобто штучним туманом, який отримують розпиленням будь-якого мінерального масла з розчиненими в ньому агрохімікатами.
Для знезаражування насіннєсховищ використовують також інсектицидні димові шашки «Гамма». Дезінсекцію сховищ проводять за 7 днів до завантаження у них насіння й зерна. Перед проведенням Дезінсекції насіннєсховище ретельно очищають, заносять у нього інвентар, мішки, брезенти тощо. Ефективність знезаражування насіннєсховищ перевіряють через 3-7 діб.
Виявлених у насіннєсховищі гризунів (пацюків, мишей) знищують. Найефективніший і найменш трудомісткий спосіб їх знищення – хімічний, включаючи застосування харчових та водних отруєних принад і газову дератизацію. Механічний спосіб (використання різних знарядь для відлову) є допоміжним у комплексі з хімічним.
Харчові отруєні принади розкладають у спеціальні ящики або в нори гризунів. У водні принади додають 20 г цукру на склянку води. Воду наливають шаром 1-2 см у плоску і низьку посудину і обпилюють агрохімікатами. Вибір принад залежить від видового складу гризунів, пори року, застосовуваного агрохімікату. Отруєні принади, які гризуни не поїли протягом 10 днів, збирають і спалюють.
Після очищення і знезаражування насіннєсховищ складають акт про їх готовність до приймання зерна та насіння нового врожаю [3].
Таблиця 1
План заходів щодо підготовки зерносховищ до завантажування зерном проса врожаю 2010 р.
Пор.№ | Назва заходу | Строки проведення (дек. міс.) | Трив проведення, діб | Необх. знаряд. і матеріали | Види і норми витр преп (при дезін.) |
1 | Очищення зерносховищ | 1.07 | 1 | Госп. інвентарь | |
2 | Ремонт зерносховищ | 2.07 | 2 | Рем. інвентарь | |
3 | Побілка зерносховищ | 5.07 | 1 | Вапно | 200г/м2 |
4 | Дезинсекція зерносховищ | 10.07 | 1 | Детіа-Газ-Екс Б | 1 упаковка на 4 м3 |
5 | Боротьба з гризунами | 14.07 | 1 | Шторм | По 1 брекету в нору |
6 | Акт приймання зерносховища | 15.07 | 1 |
2.2. Розрахунок параметрів токової площадки
Розраховуємо параметри і кількість токових площадок для розміщення зерна проса, якщо площа його посіву становить 250 га, планова урожайність – 2,2 т/га, а на збиранні урожаю зайнято 5 комбайни ДОН-1500.
Розрахунок максимально можливого надходження зерна на тік за добу проводимо за формулою:
Н = У х К х П
де Н – надходження зерна на тік за добу, т;
У – урожайність т/га;
К – кількість одиниць збиральної техніки, шт.;
П – середня продуктивність одиниці збиральної техніки, га/добу;
Н = 2,2 т/га * 2 шт * 14 га/добу = 61,6 т/добу
Розрахунок тривалості періоду збирання урожаю:
Т = 250 га : (2 шт * 14 га/добу) = 8,9 або 9 доби
Для очищення зерна проса в господарстві задіяна зерноочисна машина ЗАВ-10. Продуктивність даної машини становить: при очищенні зерна – 57 т/добу, а при очищенні насіння – 25 т/добу.
При проведенні обробки зернової маси будь якої культури враховуємо, що по перше обробку слід починати з відбирання насіння. Розрахунок потреби насіння проводимо за формулою:
,
де С – необхідна масса насіння, т;
R – коефіцієнт урахування страхового фонду(1,4);
S – площа під сівбу, га;
Нв – норма висіву т/га;
W – польова схожість, %;
Розрахунок потреби господарства в насінні при його польовій схожості 80%, проводимо за формулою:
З урахуванням добового надходження зерна на тік та продуктивності агрегату ЗАВ-10 складаємо накопичувально-витратний графік руху зерна на току. По осі абсцис відкладаємо календарні строки (дні) з моменту надходження першої партії зерна на тік до повного його звільнення від зернових мас. По осі ординат – прихід та витрату зерна. Будуємо діаграму щодобового руху зерна на току і за її піком визначаємо максимально можливе накопичення зерна на току.
Рис. 1. Накопичувально-витратний графік зерна на току
Виходячи з величини максимального накопичення зерна, розраховуємо площу перерізу насипу зерна при ширині основи 5 м за формулою:
,
де Lн – загальна довжина насипу, м;
m – максимальне накопичення зерна, т;
mн – натура, т/м3;
Sпер – площа перерізу насипу, м2;
,
де – b ширина насипу, м;
α – кут природного скочування.
Розрахунок площі перерізу насипу при куті скочування проса 25о:
Розрахунок загальної довжини насипу зерна проса:
Оскільки загальна довжина насипу становить 33,78 метрів то на мою думку буде не доцільним відведення транспортних проїздів та оперативних проходів. Тому що їх відводять на кожні 50 метрів бунта.
Розрахунок кількості бунтових площадок довжиною 75 м.
33,78 : 75 = 0,45 площадки
Розрахунок площі однієї бунтової площадки шириною 10 м.
75 м * 10 м = 750 м2
Таким чином площа необхідна для розміщення насипу проса довжиною 14 м становить:
0,45 х 750 = 337,5 м2
2.3. Технологія післязбиральної обробки зернової маси
Насіннєва маса, що надходить на тік після обмолоту, є складною механічною сумішшю (ворохом) насіння основної культури та різних органічних і мінеральних домішок. Багато з них, особливо зелені частини рослин, мають високу вологість, що зумовлює підвищення вологості насіння основної культури. вода й активізуються процеси життєдіяльності.
Оскільки при диханні насіння виділяє вуглекислий газ, воду й тепло, температура зернової маси підвищується.
Це призводить до посиленого розвитку мікроорганізмів, цвілевих грибів, а отже, до зниження схожості насіння. Тому насіннєвий ворох потрібно у міру його надходження на тік розділяти на зерно і відходи.
За допомогою очищення і сортування насіннєвої маси розв'язують три важливих завдання: видалення домішок й одержання чистого насіння основної культури; поліпшення фізичних показників насіння; виділення для висівання насіння, що відповідає вимогам стандарту.
Вирішення цих завдань ґрунтується на всебічному використанні відмінностей фізико-механічних властивостей насіння різних культур.
Зернову суміш очищають від домішок з урахуванням різниці між зернами основної культури і домішками: за шириною і товщиною – на решетах з круглими і продовгуватими отворами в зерноочисних, сортувальних і калібрувальних машинах; за довжиною – в циліндричних і дискових трієрах; з використанням аеродинамічних властивостей – за допомогою повітряного потоку в аспіраційних колонках, пневмосепараторах і пневмоколонках; за формою і станом поверхні зерна і домішок – на решетах з отворами трикутної форми в спіральних і стрічкових сепараторах, гірках, змійках; за щільністю (питома маса) – на пневматичних сортувальних столах, каменевідбіркових машинах; за металомагнітними і електричними властивостями, кольором – на електромагнітних і електростатичних, електронних машинах і за допомогою фотоелементів.
Отже насіннєві суміші на сучасних очисних машинах розділяють здебільшого повітряним потоком, решетами і трієрами [5].
2.3.1. Попередня очистка зерна і насіння
Попереднє очищення насіннєвого вороху проводять за його вологості 18-40% і засміченості 10-20% за допомогою машин для попереднього очищення: ЗД-10000; МПО-50; К-52; К-523; К-527А (стаціонарних) і ОВП-20А; ОВС-25 (пересувних). Ворох розділяють на дві фракції: зерно й відходи. Із вороха виділяють не менше ніж 50% домішок. Залишок соломистих домішок завдовжки до 50 мм має становити не більше ніж 0,2% [3].
Зерноочисна стаціонарна машина ЗД-10.000. Призначена для попереднього очищення вороху зернових і інших культур перед надходженням в сушарки. Використовують в потокових лініях стаціонарних пунктів і комплексів.
Основні робочі органи машин: приймальна камера з двома аспіраційними каналами і механізмом регулювання подачі, сітчастий пиловіддільник, що обертається, вентилятор, осадкова камера з шнеком для легких домішок і заслінкою регулювань швидкості повітряного потоку, решітний стан з скребковим транспортером.
У верхній частині приймальної камери є завантажувальне вікно, в ніжній – два живлячі валики з частотою обертання 98 об/мін. Подачу матеріалу регулюють положенням підпружинених клапанів, що знаходяться під валиками.
Легко-очисна частина має два аспіраційні канали, воздуховідвід і відстійну камеру, в якій розміщуються: пиловіддільник, що обертається, і вентилятор середнього тиску, в нижній частині встановлений шнек для виведення легких домішок.
Решітний стан, що має два змінні решета Б1 і Б2. Привід решітного стану здійснюється від ексцентрикового валу через два дерев'яні шатуни. Решета очищаються прогумованими шкрябаннями ланцюгово-планкового транспортера для крупних домішок, встановленого над решетами. Для приводу машини встановлений електродвигун (N=4: кВт, п=955 об/мін).
Матеріал, що очищається, поступає через завантажувальне вікно приймальної камери, живлячими валиками рівномірно подається в два аспіраційні канали, де з нього повітряним потоком виділяються частинки з великим коефіцієнтом аеродинамічного опору.
У розширеній частині осадкової камери крупніші частинки осідають, а пил, відокремлений сітчастим барабаном, що обертається, викидається разом з повітрям з машини. Легкі частинки, що осіли, виводяться з осадкової камери шнеком. Матеріал, очищений від легких домішок, з аспіраційних каналів поступає на решета Б1 і Б2. Крупні домішки сходяться з решіт і з'єднуючись з легкими домішками, виводяться з машини. Очищене зерно, що пройшло через отвори решіт, поступає на скатну дошку і виводиться з машини.
Машина МПО-50.00.000. Машина стаціонарна, призначена для попереднього очищення зернового вороху основних сільськогосподарських культур. Розрахована для роботи на комплексі КЗС-50 і ЗАВ-50 в потокових лініях.
Основні вузли машини: приймальна камера, сітчастий транспортер, діаметральний вентилятор, всмоктуючий аспіраційний канал, дросельна заслінка і осадкова камера з вивантажним шнеком відходів.
Приймальна камера складається з корпусу, в якому розміщується шнек, що розрівнює матеріал, що очищається, по ширині машини. Дно приймальної камери виконане у вигляді клапана, сила притиснення якого регулюється важками.
Сітчастий транспортер нахилений на 18° і служить для відділення крупних домішок. Полягає транспортер з нескінченної сітчастої стрічки, провідного і веденого валів. При обробці вологого і засміченого матеріалу для інтенсифікації процесу відділення крупних домішок включається механізм, що складається з валу, хрестовин і роликів. Під сітчастим транспортером встановлені скатні дошки, що розділяють матеріал на два потоки.
Легко-очисна частина включає всмоктуючий і нагнітальні канали, осадкову камеру з діаметральним вентилятором і шнеком вивантаження легких домішок.
У нижній частині перегородки нагнітального каналу знаходяться жалюзійні отвори. У середній частині нагнітального каналу встановлена дросельна заслінка для регулювання швидкості повітряного потоку.
Технологічний процес відбувається таким чином. Оброблюваний матеріал поступає в машину через завантажувальне вікно, шнек рівномірним шаром розподіляє його по ширині машини і подає по клапану на сітчастий транспортер. Рівномірність подачі регулюється переміщенням вантажу, встановленого на клапані.
Крупні домішки (солома, колоски) притискаються соломоприжимами до транспортера і виносяться останнім у вихід крупних домішок.
Матеріал без крупних домішок, що очищається, пройшов через сітчастий транспортер, подається на скатні дошки, ділиться на два потоки і прямує в, канал аспірації. За рахунок повітряного потоку, що створюється вентилятором, із зерна виділяються легені домішки і виносяться в осадкову камеру. Очищене зерно через вихід, закритий підпружиненими клапанами, прямує на подальшу обробку. Легені домішки з осадкової камери виносяться шнеком [6].
Якщо насіннєвий ворох має вологість не більш як 18% і засміченість до 8%, то його піддають первинному очищенню (без попереднього) [3].
2.3.2 Первинна очистка зернової маси
Первинне очищення здійснюють на стаціонарних (ЗАВ-10 30.000: ЗВС-20; ЗВС-20А; СВУ-5А; К-218; К-531А; К-546А) або пересувних (ОС-4.5М; СМ-4) очисних машинах. За допомогою повітряного потоку, решіт і трієрів насіннєвий ворох розділяють на три фракції: насіння, фуражні й крупні відходи, легкі та дрібні домішки [3].
Агрегати для очищення вороху випускають серійно таких марок: ЗАР-5, ЗАВ-10, ЗАВ-20, ЗАВ-25, ЗАВ-40, ЗАВ-50, ЗАВ-100. Вони призначені для доведення зерна до базисних норм за один пропуск і забезпечують приймання, очищення, відвантаження та зберігання зерна вологістю не вище 13%.
Зерноочисний агрегат вороху (ЗАВ) складається з будівельної частини, металевої арматури та машин і обладнання. До будівельної частини входять: приймальне відділення зерна, приямок норії, фундамент під опору блоків бункерів, майданчик для авторозвантажувача, пандус для заїзду автомобіля на авторозвантажувач. Металева арматура – це майданчик, де змонтовано всі машини й обладнання.
Машини й обладнання складаються з авторозвантажувача, завальної норії, повітряно-решітних машин, трієрних блоків, централізованої повітряної системи, передавальних конвеєрів, зернопроводів, пульта керування. Авторозвантажувачі (ГАП-2Ц або ГУАР-15) розвантажують автомобіль. Норії бувають одно- чи двопоточні. Норія має автомат для закривання заслінки в нижній її частіші. Автомат приєднаний до загальної електричної схеми агрегату.
Централізована повітряна система має електровентилятор, відцентрово-інерційний відокремлювач домішок, раму, комплект повітропроводів, розтруб з покрівлею і труби (ЗАВ-10 і ЗАВ-20). В агрегатах ЗАВ-25 та ЗАВ-40 повітрорешітні машини мають свої вентилятори, тому аспіраційна система в них працює тільки для виділення пилоподібних та легких домішок з повітря.
Технологічна схема зерноочисних агрегатів вороху має вертикальну конструкцію. Зерно із завальної ями подається норією на другий поверх і з головки норії самопливом надходить у розміщені на цьому поверсі зерноочисні машини, а з них системою конвеєрів – в трієри, з трієрів – у бункери. В зерноочисній машині виокремлюються легкі домішки, а зерно розділяється на три фракції: велике, середнє та дрібне (зерновідходи). Якщо у великому зерні є довгі домішки чи биті зернини, які відділяються важко, то його спрямовують у трієри, а звідти – в бункер для основного зерна та зерновідходів для розділення фракцій зернової маси.
Керування робочим процесом здійснюється з дистанційного пульта, на якому передбачено систему блокування та сигналізації.
Технологічний процес усіх агрегатів ЗАВ принципово однаковий. Базовою є конструкція агрегату ЗАВ-10, який обслуговує один механізатор. Агрегат може працювати за трьома схемами.
Схема 1. Зерно очищається від легких, великих, дрібних, довгих чи коротких домішок. Одночасно працюють повітряно-решітна машина і трієрний блок. Аспіраційні канали первинного очищення виділяють з вороху легкі домішки, після чого ворох подається на решітний стан. Запорошене повітря надходить у відцентрово-інерційний повітроочисник, де домішки залишаються в осаджувальному конусі і через клапани виводяться в секцію відходів, а очищене повітря вентилятором викидається назовні. На решітному стані виділяються великі і дрібні домішки та щупле зерно. Очищене зерно спрямовується у трієрний блок, який при очищенні продовольчого зерна настроюють на паралельну роботу, а при очищенні насінного – на послідовну. При очищенні насінного зерна уточнюють підбір решіт, вдвічі зменшують продуктивність блока і заново регулюють аспірацдйну систему.
Схема 2. Цією схемою (робота без трієрного блока) користуються тоді, коли зернова маса не містить довгих та коротких домішок.
Схема 3 – налагоджувальна.
Агрегат ЗАВ-25 – це вдосконалений агрегат ЗАВ-20. Він складається з двох частин – відповідно для приймання та для попереднього очищення зерновороху і бункерів місткістю (200 т) для тимчасового зберігання зерна з одночасним його аеруванням.
Технологічна схема агрегату ЗАВ-25 така: зерно з приймального бункера норією подається в машину попереднього очищення, де виділяються великі й легкі домішки, а зерно самопливом надходить у проміжний бункер. Після попереднього очищення основна фракція надходить у машину первинного очищення і далі в бункер для чистого зерна або після первинного очищення на проміжну норію і на трієрні блоки. Однак за допомогою агрегатів ЗАВ не завжди можна відділити від зерна всі домішки, тому промисловість випускає насіннєочисні приставки для цих агрегатів: СП-10, СП-20 [4].
Стаціонарна легко-решітна зерноочисна машина ЗВС-20. Застосовують в агрегатах і комплексах для первинного очищення вороху зернових, бобових, круп'яних і олійних культур з доведенням зерна до продовольчих кондицій.
Але загальним для решітних машин є те що для того щоб насіння не скочувалося і не потрапляло в сход на поверхні двох третин сортувальних решіт (рахуючи від початку) на сепаратор навішують фартух з брезента.
Половинки і подрібнені частинки гороху видаляють на підсівних решетах з довгастими отворами шириною 4,5-5 мм.
Легкі домішки і пошкоджене насіння гороху видаляють на у пневмосортувальних каналах сепараторів при швидкості повітряного потоку 8-12 м [6].
2.3.3. Вторинна очистка зерна і насіння
Безпосередньо вторинному очищенню можна піддавати насіннєвий ворох вологістю до 18 і засміченістю до 8%. На тих самих машинах, що проводять первинне очищення, вихідний ворох розділяють на чотири фракції: насіння, фуражні відходи, легкі домішки, крупні та дрібні домішки. Після вторинного очищення насіння за чистотою має відповідати вимогам стандарту [3].
Для вторинної обробки зерна використовують трієрні машини, в яких виділяються компоненти смітної та зернової домішок. На них обробляють зерно основної культури з домішками, які неможливо виділити робочими органами машин первинного очищення, та відділяють малоцінні насінини основної культури. До таких машин належать СМ-4, СВУ-5А, машини фірми «Петкус» (К-545А, К-647А10, К-546, К-548) для очищення насіння трав.
Насіннєочисна приставка СП-10 має дві насіннєочисні машини СВУ-5, два пневматичних сортувальних столи ПСС-2,5, дві норії, автоваги, мішкозашивальну машину, аспіраційну систему, комплект зернопроводів та пульт керування. Залежно від стану та призначення зерна приставка може працювати за трьома технологічними схемами:
1) зерно надходить на решітний стан, на другу аспірацію і в результаті розділяється на 1-й і 2-й сорти, відділяються легкі та важкі домішки. Потім зерно 1-го сорту надходить на два паралельно працюючі пневматичні сортувальні столи, які також розділяють зернову масу на 1-й і 2-й сорти та легкі зерна. Насіння 1-го сорту надходить на автоваги, ваговибійний апарат та мішкозашивну машину;
2) поточна лінія працює без пневматичних сортувальних столів;
3) лінія працює за схемою 1 або 2, але без зважування та затарювання мішків.
Насіннєочисна машина СМ-4 призначена для вторинного очищення зерна і сортування насіння зернових, зернобобових, олійних культур і насіння трав.
Основні вузли машини: зварна рама, завантажувальний транспортер, аспіраційна частина, решітний стан, елеватор, трієрний блок і механізм самопересування.
Живлячий пристрій об'єднаний з пристроєм для автоматичного регулювання завантаження машини системою включення і виключення самохода. Якщо очищувальної маси надходить забагато то механізм самопересування вимикається, зменшуючи подачу матеріалу на очищення і навпаки.
Легко-очисна частина має дві замкнуті системи першої і другої аспірації. Ці системи між собою з’єднані. Таким чином, замкнута система аспірації запобігає викиду запиленого повітря в атмосферу. Через матерчатий фільтр пилозбірника і жалюзі камери пилозбірника викидається не більше 10% відпрацьованого повітря. Вікно в загальній стінці систем аспірації дозволяє заповнювати недолік повітря у всмоктуючій магістралі другої аспірації через нагнітаючу магістраль першої аспірації.
Суцільнометалевий решітний стан має чотири решета: Б1 і Б2, В і Р. Оскільки на насіннєочисній машині СМ-4 встановлений один решітний стан, сили інерції зрівнюються противагами, встановленими на ексцентриковому валу. Трієрний блок встановлений горизонтально збоку машини; верхній трієр призначений для видалення коротких домішок (куколя), ніжній – для видалення довгих домішок (вівсюга).
Циліндрові трієри мають сталевий циліндр, що обертається, з виямками 5,0 мм для кукіля і 8,5 мм для вівсюга. По всій довжині циліндра розміщений нерухомий жолоб-приймач, усередині якого розташований шнек, що обертається, для виведення виділеного матеріалу. При обертанні циліндра в виямки потрапляють короткі домішки (кукіль), піднімаються на певний кут і, випадаючи з виямок, потрапляють в нерухомий жолоб, з якого віддаляються шнеком, а зерно і довгі домішки переміщаються далі по жолобах.
У циліндрі в виямками потрапляє зерно основної культури. Для передачі оброблюваного матеріалу від решітного стану до трієрному блоку служить шнек і одна гілка двопоточного ковшового елеватора.
У верхній головці двопотокового елеватора встановлена заслінка, напрямна очищеного матеріалу в трієрний блок для відділення коротких і довгих домішок, або на виведення очищеного матеріалу з машини, якщо не потрібне очищення по довжині. При очищенні зерна по довжині (включені трієрниє циліндри) після проходження трієрних циліндрів друга гілка ковшового елеватора виводить зерно з машини.
Технологічний процес відбувається таким чином. При русі машини шнекові живильники з бунту подають оброблюваний матеріал до верхньої головки завантажувального транспортера, який подає матеріал в розподільний шнек-живильник і, проходячи підпружинений клапан-живильник, рівномірним по ширині машини шаром подається в перший канал аспірації. Виділені легені домішки разом з повітрям потрапляють в осадкову камеру і виводяться з неї шнеком у вихід. Вентилятор подає очищене повітря в нагнітальний канал.
Матеріал, що пройшов першу аспірацію, поступає на решето Б1, де розділяється на дві рівні по масі частини. Сходячи з решета Б1, крупніша частина зерна і крупні домішки, поступають на Б2 де відділяються крупні домішки, які сходом поступають у вихід, а очищене зерно по скатній дошці – на кінець решета Г і в шнек для очищеного зерна. Прохід через решето Б1 (дрібніша частина насіння, дрібні і зернові домішки) поступає на підсівне решето В, де відділяються (у прохід) дрібні домішки і прямують по лотку у вихід, з'єднуючись з легкими домішками. Схід з решета В (дрібніша частина зерна і зернові домішки) поступає на сортувальне решето Г, де відділяються (у прохід) зернові домішки і виводяться у вихід, а очищене зерно, з'єднуючись з проходом решета Б2, прямує в шнек чистого зерна.
Під час переходу очищеного матеріалу від решітного стану до шнека зерно піддається другій аспірації в каналі, де відділяються легеші, що залишилися, домішки, які частково осідають в камері, а пил виноситься вентилятором у фільтр і пилозбірник пиловіддільника.
Шнек для очищеного матеріалу подає зерно на одну з гілок двопотокового ковшового елеватора, який направляє матеріал у верхній ляльковий трієрний циліндр для видалення коротких домішок. Короткі домішки, що потрапили в нерухомий лоток, шнеком виводяться з циліндра і потім, з'єднуючись з проходом решета Г, виводяться з машини через вихід.
Схід циліндра (лялькового) підйомним трипелюстковим колесом передається по зливу в (вівсюжний) трієрний циліндр для видалення довгих домішок. Довгі домішки виводяться через вихід, а очищений матеріал, випадний в осередки трієра, потрапляє в нерухомий жолоб-приймач, шнеком передається в другу гілку відвантажувального ковшового елеватора і виводиться з машини.
Також на сучасних сільськогосподарських підприємствах застосовуються зерноочисно – сушильні комплекси. Які за один прохід очищають і висушують зернову масу. Після обробки зернова маса повністю відповідає вимогам стандарту.
У районах виробництва зерна з підвищеною вологістю найраціональнішою системою обробки зернових мас є комплекси з одночасним очищенням і сушінням зерна. Такі комплекси набули великого поширення. Очищається зернова маса зерноочисними агрегатами, а сушиться на сушарках барабанного (КЗС-5, КЗС-10Б, КЗС-20Б) або шахтного типу (КЗС-10Ш, КЗС-20Ш, КЗР-5).
Для кращої обробки насіння до комплексу КЗС-10Ш додається насіннєочисна приставка, яка може бути використана за шістьма технологічними схемами.
Специфічними за призначенням обладнання та технологічною схемою є насіннєочисний сушильний пункт продуктивністю 1,5-2 т/год, тобто розрахований на 750-1000 т насіння за сезон.
Устаткування цього пункту складається з машин об'єднання «Петкус» (НДР) вітчизняного виробництва. Обробка і підготовка насіння за основною технологічною схемою складається з таких операцій: попереднього очищення, активного вентилювання зернової маси, сушіння, вторинного очищення, протруювання і затарювання в мішки. Для проведення цих операцій комплекс оснащений машиною «Петкус-Вибрант» (для попереднього очищення), двома силосами місткістю по 30 т для активного вентилювання, шахтною зерносушаркою, машиною «Петкус-гігант» (для вторинного очищення), протруювачем, ваговибійним апаратом та мішкозшивальною машиною. Залежно від культури та засміченості насіння застосовують одну із семи технологічних схем [6].
2.3.4. Сушка зерна і насіння
Сушіння – основна технологічна операція з приведення зерна й насіння до стійкого стану [4].
Зерно сушать для зменшення вологості до межі, яка забезпечує стійкість його в процесі зберігання, для доведення його до потрібних параметрів під час заготівлі і постачання на переробку, а також для знищення комірних шкідників [2].
Усі способи сушіння зерна враховують сорбційні та інші його властивості. Зерно як об'єкт сушіння – це живий організм з капілярно-пористою структурою. Плодові оболонки насіння пронизані капілярами, тому є проникними для пари води. Насінні оболонки й алейроновий шар, малопроникні для пари води і за неправильного режиму сушіння можуть бути причиною здуття зерна. Крім того, при температурі вище 41-42°С білки зародка, денатурують, тобто насіння втрачає схожість.
Сушіння – складний технологічний тепломасообмінний процес, який повинен забезпечити збереженість усіх властивостей речовин у зерні, що можливо за умови дотримання оптимальних параметрів цього процесу.
Застосовують три способи сушіння зерна: теплове (в тому числі вакуумне); сорбційне (контактне); механічне (відтискання, центрифугування). Найчастіше практикують теплове сушіння, рідше – сорбційне, а механічне – тільки у мийних машинах на борошномельних заводах. Під час теплового сушіння рідина перетворюється на пару, на що витрачається теплова енергія. При сорбційному сушінні волога із зерна може видалятися як у пароподібному, так і в рідкому стані.
Серед численних способів теплового сушіння, які різняться способом передачі теплоти зерну, найпоширеніший конвективний. Суть його полягає в тому, що теплота передається конвекцією від теплоносія, який вбирає вологу, і видаляється в атмосферу. За таким принципом працюють шахтні, рециркуляційні, барабанні, стрічкові та інші типи сушарок.
Процес сушіння ґрунтується на здатності зерна випаровувати поверхнею вологу за умови, що тиск водяної пари в зерні вищий за тиск її в зовнішньому повітрі.
Закономірності сушіння зерна такі:
- чим більша початкова вологість зерна, тим вища швидкість сушіння в початковий період і тим він коротший. У сирому зерні є механічно зв'язана волога, яка видаляється в першу чергу. Капілярно зв'язана волога міцно зв'язана з крохмальними зернами і ще міцніше – з білками. Тому процес сушіння зерна лімітується переважно сушінням білкового комплексу;
- під час сушіння зерно нагрівається швидше, ніж випаровується волога. Це й визначило доцільність застосування для сушіння зерна рециркуляцінного (з відлежуванням) способу;
- сушіння можливе лише тоді, коли тиск пари всередині зернівки вищий, ніж в навколишньому середовищі, тобто відбувається її випаровування. Коли температура поверхні зерна дорівнює температурі середовища сушильної камери, процес сушіння (випаровування води) припиняється;
- одночасно з переміщенням вологи рухаються розчинені в ній мінеральні речовини, тому зольність периферійної частини зернівки і зародка збільшується;
- при вмісті в насипу органічної легкої домішки понад 0,1 % можливе загоряння її в сушарці;
- якщо зерно перед сушінням зберігалося в анаеробному стані в насипу висотою понад 4 м, то в зернівках накопичується етиловий спирт, який при різкому нагріванні може призвести до загибелі зародків. Тому зерно треба попередньо провітрити для видалення спирту;
Контактний (кондуктивний) спосіб сушіння ґрунтується на контакті висушуваного матеріалу з нагрітою поверхнею і потребує великих витрат теплоти, тому поширений мало.
За радіаційного способу сушіння використовують теплоту енергії сонця чи інфрачервоних променів. Приклад – повітряносонячне сушіння, коли волога випаровується тільки через поверхню насипу зернової маси. Шар зерна зернових злакових має бути гребенистим завтовшки 10-20 см, зернобобових 10-15, см. При температурі насипу 25-30°С його треба переміщувати.
При додержанні всіх вимог та достатній інсоляції, якщо вологість зерна не перевищувала 17-18%, вона за один день знижується на 1-3%. Якщо вологість зерна вища, повітряно-сонячне сушіння малоефективне. За такого сушіння поліпшується схожість зерна, успішніше відбувається післязбиральне дозрівання, зменшується кількість мікрофлори та пошкодженість зерна шкідниками.
Молекулярне сушіння зерна проводять у вакуумних установках. Тут спочатку створюють вакуум, в результаті чого волога від перепаду тиску в зерні та в середовищі виділяється на поверхню і замерзає, а при наступній подачі до зерна теплоти швидко випаровується. Так можна сушити овочі, фрукти. Собівартість такого сушіння занадто висока і на практиці його застосовують мало.
При конвективному сушінні зерно, залежно від типу зерносушарки, перебував в нерухомому (камерні зерносушарки), малорухомому (шахтні) та падаючому (рециркуляційні) стані. Зерно в нерухомому стані сушать у жалюзійних, лоткових і стелажних сушарках або за допомогою установок активного вентилювання. Як правило, використовують теплоносій з температурою 35-40°С при швидкості висушування 0,5-1,5% його за годину, тобто ці сушарки малопродуктивні. Крім того, зерно у них не завжди рівномірно просихає.
Конвективним способом сушать зерно й насіння всіх культур, а також малосипучі матеріали — лляний ворох, насінники овочевих культур тощо.
Камерні зерносушарки.
Найпростіша двокамерна установка для сушіння складається з припіднятої решітки-основи і тепловентиляційного пристрою, який забезпечує нагрівання і подачу агента сушіння в підрешітний простір. Агент сушіння під тиском проникає крізь решето і проходить потім через зернову масу знизу вгору.
Сушарка складається з корпуса й топкового відділення, від якого із обох боків підходять до корпуса цегляні канали, по яких надходить гаряче повітря. Перед надходженням у розподільні коридори топкові гази змішуються (за допомогою всмоктувально-нагнітального вентилятора) із зовнішнім повітрям, а потім подаються в камери. Технологічний процес сушіння починається із завантаження в сушарку матеріалу (качани кукурудзи шаром 2-3 м, зерно інших культур – 0,6-0,8 м) через верхні завантажувальні вікна.
Камера – це закрите приміщення з люками для завантаження та розвантаження і похилим решітчастим металевим днищем, що не допускає втрат зерна в результаті просипання. Під час сушіння кукурудзи в качанах повітря подають послідовно з камери в камеру, то при сушінні інших культур – паралельно.
Режими сушіння зерна гороху вологістю 26 % та 16 % проводять при температурі 33°С, висоті насипу 1 м, тривалість сушіння 24-30 год.
Перед початком роботи сушарки торцеві стальні двері коридорів, через які в камери надходить повітря, щільно зачиняють. Сушильний агент подають почергово то зверху, то знизу, добиваючись рівномірного висушування шару качанів або зерна висотою відповідно 1,5-2,5 м і 60-70 см
Недолік камерних сушарок – втрати агента сушіння, нерівномірність висушування: зверху та знизу зерно висушується краще, посередині – гірше.
Рухомий шар зерна сушать в шахтних, барабанних чи рециркуляційних сушарках.
Шахтні зерносушарки.
Шахтна зерносушарка складається з однієї або двох прямокутних вертикальних камер – шахт, які заповнюють зерном по всій висоті. Верхня частина шахти – сушильна камера, що складається з однієї або кількох зон сушіння, нижня – камера охолодження. Над шахтами змонтовано бункери, в яких міститься запас зерна.
Для підведення свіжого і відведення відпрацьованого агента сушіння по всій висоті шахти встановлюють металеві короби, призначення яких – рівномірно розподілити агент сушіння по всій зерновій масі. Кожний короб у поперечному розрізі – це відкритий знизу п'ятикутник. Один кінець короба закритий стінкою, а другий – відкритий.
Для того, щоб зерно перемішувалося краще, короби розмішують у шаховій послідовності.
Зерносушарки ДСП (двоступінчасті) випускають продуктивністю 12, 16, 20, 24, 32 і 50 т/год. На хлібоприймальних пунктах найбільш поширена зерносушарка марки ДСП-32-ОТ.
Зерносушарка – це установка відкритого типу з двоступінчастим режимом сушіння. Вона складається з двох паралельно працюючих шахт. Кожна шахта складається з семи секцій і по висоті ділиться на три зони; перша і друга – зони сушіння; третя – зона охолодження (нижня частина). В кожній секції 8 рядів коробів по 16 шт. у кожному.
Технологічна схема роботи зерносушарки ДСП-32-ОТ така. Сире зерно піднімається норією в надсушильний бункер, після чого рівномірно рухається по сушильних шахтах (відповідно в першій і другій зонах сушіння) та шахті охолодження (зоні охолодження). Випуск зерна з шахт проводиться випускним механізмом періодичної дії. Сухе охолоджене зерно із зерносушарки спрямовується за допомогою норії сухого зерна в зерносховище.
Агент сушіння з топки вентиляторами подається в нагнітально-розподільні камери першої і другої зон сушіння.
Атмосферне повітря вентилятор подає в нагнітально-розподільну камеру шахти охолодження. В зерносушарці ДСП-32-ОТ застосовується конвективне сушіння, коли теплота подається до зерна від агента сушіння.
Зерно в зерносушарці ДСП-32-ОТ підсушується сумішшю опалювальних газів з повітрям.
Сушарка СЗШ є складовою частиною зерноочисно-сушильних комплексів КЗС-20, КЗС-40. У нових комплексах КЗС-25Ш використовують модернізовану сушарку СЗШ-16А.
Зерно від машини первинного очищення комплексу надходить до норій і піднімається в надсушильні бункери, самопливом заповнюючи шахти сушарки. Агент сушіння подається від топки по трубопроводу в напірну камеру між шахтами, а потім через вікна і канали підвідних коробів у зернову масу.
Зерно в шахті переміщується самопливом зверху донизу. Висушене зерно надходить через розвантажувальне обладнання в підсушувальний бункер, а потім самопливом у ковші норій, які піднімають його і подають у колонки для охолодження. Зерно охолоджують активним вентилюванням.
При вологості зерна вище 26 % висушити його за один пропуск, навіть при послідовному пропусканні через дві шахти, неможливо. Краще сушити його в сушарках камерного типу або бункерах активного вентилювання.
Пересувна зерносушарка К4-УС2-А з плановою продуктивністю 10 т/год при 6%-му видаленні вологи складається із сушильних шахт, транспортного обладнання і топки, які змонтовані на шасі автомобільного причепу МАЗ-8925.
Сушильна частина зерносушарки має дві шахти з повітророзподільним пристроєм, два Г-подібних конвеєри, два випускних механізми, три шнеки, бункер для сирого зерна та вентилятори із заслінками, зону охолодження.
Сушити зерно можна паралельно, послідовно і методом рециркуляції (при сушінні з високою вологістю).
Барабанні зерносушарки.
Зерносушарку стаціонарну барабанну СЗСБ-8 використовують для сушіння зерна різних зернових, бобових і олійних культур будь-якого ступеня вологості та засміченості без попереднього очищення. Встановлюють її на масложирових підприємствах для сушіння соняшнику та на токах для сушіння зерна різних культур.
Зерносушарка СЗСБ-8 складається з топки, камери завантаження, колонки охолодження, розвантажувальної та завантажувальної норій, вентиляторів колонки охолодження та сушильного барабана, приводного механізму.
По перерізу барабан розділений на шість секторів, у кожному з яких закріплено полички, що захоплюють зерно під час обертання барабана. Пересувається зерно вздовж барабана в момент його пересипання під дією підпору і потоку агента сушіння. З розвантажувальної камери зерно подається в шлюзову заслінку, звідки надходить в охолоджувальну колонку. Тривалість перебування зерна в контакті з агентом сушіння в барабанних сушарках регулювати важче, оскільки температура нагрівання агента сушіння в них 90-130°С для насіння і понад 180°С для продовольчого та фуражного зерна. Недоліком конструкції сушарок цього типу є те, що зерно, яке надходить в сушарку, контактує з досить нагрітим агентом сушіння.
Барабанні сушарки не можна використовувати для сушіння насіння гороху, рису, кукурудзи, тому що воно травмується – розтріскується.
Рециркуляційні зерносушарки.
При рециркуляційному сушінні зерна змішують певну кількість сирого зерна з великою кількістю сухого і чергують короткочасне нагрівання суміші зерна з наступним охолодженням та рециркуляцією великої частини просушеного зерна. Зерно за короткочасного (2-3 с) перебування в камері нагрівання при температурі агента сушіння 250-380°С нагрівається до 50-60°С.
Зерносушарки з рециркуляцією, за конструкцією та способом нагрівання зерна поділяють на рециркуляційні з камерами нагрівання і шахтні рециркуляційні без камер нагрівання.
Технологічна схема роботи газової рециркуляційної зерносушарки «Цілинна-50» продуктивністю 50 т/год така: вологе зерно надходить в оперативний бункер, де завжди повинен бути запас зерна, щоб запобігти перервам у роботі сушарки. З оперативного бункера зерно спрямовується на норію продуктивністю 350 т/год, піднімається вгору і надходить у бункер камери нагрівання, в якій встановлено в шаховому порядку 20 горизонтальних рядів стержнів. Розміщення стержнів сприяє рівномірному розподілу зерна по об'єму камери та інтенсивному його перемішуванню.
Зерно в камеру нагрівання рівномірно надходить з бункера із завантажувальним пристроєм і падає у вигляді дощу в потоці агента сушіння з високою початковою температурою (250-380°С). При цьому за дуже короткий час (2-3оС) воно нагрівається до 55-60°С. Із камери нагрівання гаряче зерно потрапляє в бункер тепло- і вологообмінника, де під час його перебування протягом 10-12 хв відбуваються вирівнювання температури і частковий перерозподіл вологи між окремими зернами.
Досвід експлуатації газово-рециркуляційних зерносушарок показав, що в них можна одночасно сушити до заданих норм без попереднього очищення кілька партій зерна різної вологості (від 17 до 25-30 % із збереженням його насінних якостей.)
Важливим фактором забезпечення високоефективної роботи зерносушарок є контроль за дотриманням режимів сушіння, якістю та кількістю висушеного зерна. Режими сушіння зерна насінного призначення передбачають сушіння насіння пшениці, жита, ячменю, вівса, соняшнику, гречки і проса з початковою вологістю до 19% і максимальним нагріванням їх до 40оС при температурі агента сушіння до 70°С. При сушінні насіння гороху, вики, квасолі, люпину та рису гранична температура нагрівання має бути нижчою – для зерна до 35°С, а для агента сушіння – до 60°С. Якщо на сушіння надходить насіння вологістю вище 19 %, його треба сушити ступінчастим способом, знижуючи температуру агента сушіння в першій зоні сушіння нижче граничної на 10°С, а допустиме нагрівання насіння – на 5°С.
При сушінні зерна, призначеного для виробництва крупи, в шахтних сушарках зниження вологості за один пропуск рису і сої не повинно перевищувати 3 %; проса і гречки 2-3; гороху і ячменю 3,5-4; кукурудзи 4,5-5,5, а при сушінні інших культур 6 %.
Зерно бобових порівняно із зерном інших культур містить більше білка, більше за розміром, сухе, щільне, має структурно відособлені оболонки, а тому й меншу поверхню випаровування, що знижує їх вологовіддачу. Вся теплота витрачається переважно на нагрівання насіння, а не на випаровування вологи. При цьому поверхня зерна швидко зневоднюється, а центральна частина зернівки залишається вологою. Тому при застосуванні інтенсивних режимів сушіння розтріскуються насінні оболонки.
Для сушіння зерна бобових використовують лише шахтні сушарки. Допускається видалення за один пропуск 3-4 % вологи, а для крупнонасінних (квасоля, боби) – 2%. Бобові обов'язково сушать з відлежуванням.
При сушінні зерна і насіння пропускну здатність сушарок визначають за допомогою перевідного коефіцієнта К, який характеризує здатність зерна віддавати вологу з урахуванням рекомендованих температур агента сушіння та видалення вологи за один пропуск. Наприклад перевідного коефіцієнта для пшениці, вівса, ячменю, соняшнику становить 1,0 для жита 1,1, гречки 1,2, проса 0,8, кукурудзи 0,6, а для гороху, вики, рису він становить 0,3-0,4.
Найважливішим параметром процесу сушіння є температура агента сушіння та нагрівання зерна. Відхилення в температурі агента сушіння від заданих норм не повинно перевищувати ± 3°С, а температура нагрівання зерна ± 2°С.
Температуру агента сушіння вимірюють у нагнітальній камері перед вхідними отворами підвідних коробів. Вимірювання проводять через кожні 30 хв за допомогою встановлених на сушарці електротермометрів, покази яких записують у журналі оператора через кожні 2 год.
Температуру зерна визначити складніше, ніж температуру агента сушіння. В перші години роботи сушарки температуру насіння перевіряють через кожні 10-15 хв, відбираючи проби зерна при виході його з камери нагрівання. Регулюють температуру відкриванням дверець впуску повітря або піддувальних дверець. Після встановлення режиму сушіння температуру зерна вимірюють не рідше як через кожні 2 год.
У сучасних шахтних сушарках температуру нагрівання зерна контролюють за допомогою датчиків дистанційних термометрів, які встановлюють у підсушувальному бункері. Однак такий контроль дає тільки орієнтовні результати.
Після охолоджувальної колонки перевіряють також температуру зерна (вона може бути на 8-10°С вищою за температуру навколишнього середовища), а також якість зерна за такими органолептичними показниками, як колір, блиск, наявність сторонніх запахів. При порушенні режимів сушіння зерно може запаритись, окремі зернівки можуть підгоріти, обвуглитись, потемніти, містити сажу й мати запах диму.
Режими сушіння зерна і насіння гороху в шахтних і в барабанних сушарках залежно від вологості проведено нижче в таблиці:
Таблиця 2
Режими сушіння зерна і насіння проса в сушарках
Призначення зерна | Початкова вологість. | Тип сушарки | |||
шахтна | барабанна | ||||
температура, С° | температура, С° | ||||
агента сушіння | зерна (насіння) | агента сушіння | зерна (насіння) | ||
Продовольче | до 21% до 27% | 90 80 | 45 40 | ___ | ___ |
Насіння | до 21% до 27 % | 80 70 | 40 35 | ___ | ___ |
Продуктивність сушарок визначається різними показниками: масою сирого зерна, що надходить у сушарку; кількістю випаровуваної вологи в кілограмах за годину; тонно-процентах зниження вологості та ін.
Масу зерна і продуктивність сушарок виражають у натуральному (умовному) обчисленні – планових одиницях. Планова одиниця сушіння (планова тонна) – де зниження вологості однією тонною продовольчого зерна пшениці на 6 % (з 20 до 14 % вологості) [4].
Отже як зазначалося вище для сушіння зерна гороху використовують лише шахтні сушарки. Допускається видалення за один пропуск 3-4 % вологи. Тобто якщо вологістю насіння гороху 25% то для доведення його до базисної вологості 16% необхідно застосувати ступінчастий режим сушіння. Він полягає в тому що зерно пропускається двічі через сушарку із зниженням вологості кожного разу на 4%.
Розрахувати виробіток зерносушарки при висушуванні 548,2 т продовольчого зерна та 8,75 т насіння проса з початковою вологістю 17% та базисною нормою вологості 13%.
Маса просушеного зерна в планових тонах (mпл) для всіх типів сушарок розраховується за формулою:
mпл = mф * Кв * Кк
де mпл – маса просушеного зерна в планових тонах;
mф – фізична маса зерна, яке надійшло в сушарку, т;
Кв – коефіцієнт перерахунку маси зерна в планові одиниці в залежності від його початкової вологості;
Кк – коефіцієнт перерахунку маси зерна в планові одиниці в залежності від культури;
Розрахунок виробітку при сушінні продовольчого зерна:
mпл = 548,2 * 0,87 * 1,25 = 596,2 т
Розрахунок виробітку при сушінні насіння:
mпл = 8,75 * 0,87 * 2,5 = 19,03 т
Сумарний виробіток зерносушарки:
596,2 + 19,03 = 615,23 планових тонн.
Отже виробіток зерносушарки при висушуванні 548,2 т продовольчого зерна та 8,75 т насіння проса з початковою вологістю 17% та базисною нормою вологості 13% становить 615,23 планових тонн.
2.3.5.Кількісний облік зерна і насіння при післязбиральній обробці
При післязбиральній обробці зернової маси її вага зменшується у зв’язку із зниженням вологості і вмісту смітних домішок. Через це і необхідно проводити кількісний облік зерна і насіння при післязбиральній обробці
Розрахунок зменшення маси партії проса продовольчого (548,2 т) і насіннєвого (8,75 т)призначення при початковій вологості 17% і вмісті смітних домішок 9%
Втрати маси при висушуванні розраховуються за формулою:
де хв – втрати маси зерна %;
а – вологість зерна при приході;
б – вологість зерна при витраті;
Розрахунок втрат маси продовольчого зерна і насіння при висушуванні:
Зменшення маси від зниження вмісту смітної домішки розраховується за формулою:
де хз – втрати маси зерна, %;
в – вміст смітної домішки по приходу, %;
г – вміст смітної домішки при витраті, %;
Розрахунок зменшення маси продовольчого зерна при очищені від смітних домішок:
Розрахунок зменшення маси насіння при очищені від смітних домішок:
Розрахунок загальних втрат маси при післязбиральній обробці продовольчого зерна:
4,60 % + 7,70 % = 12,3% або
548,2 т * 12,3 % : 100 = 67,43 т
Розрахунок загальних втрат маси при післязбиральній обробці насіння:
4,60 % + 6,81 % = 11,41 % або
8,75 т * 11,41 % : 100 = 0,99 т
Таким чином на зберігання у сховище буде закладено:
- продовольчого зерна
548,2 т – 67,43 т = 480,77 т
- насіння
8,75т – 0,99 т = 7,76 т
2.4. Технологія зберігання зерна і насіння
2.4.1. Розрахунок необхідної ємкості зерносховища
Просо найкраще зберігається при вологості 13% насипом висотою 2-2,5 м в залежності від пори року. І не більше як 6 рядів при зберіганні насіннєвого гороху в мішках.
Необхідно розрахувати потребу в складській площі та скласти план розміщення у сховищі 480,77 т насіння та 7,76 т продовольчого зерна проса.
Просо будемо зберігати насипом висотою 2,5 м виходячи з цього і розрахунок необхідної кількості засіків:
Об’єм засіки становить:
6 м * 6 м * 2,5 м = 90 м3
Масу зерна в засіку розраховуємо в залежності від натурної маси зерна, а вона становить 0,7 т/м3:
90 м3 * 0,7 т/м3 = 63 т
Виходячи з цього і розрахунок необхідної кількості засіків для зберігання продовольчого зерна:
480,77 : 63 = 7,6 або 8 засіки
Оскільки насіннєве зерно бажано зберігати в мішках то необхідна розрахувати їх кількість (об’ємом 1 мішка 0,05 м3):
Маса зерна в одному мішку:
0,05 м3 х 0,7 т/м3 = 0,035 т
Необхідна кількість мішків:
7,76 т : 0,035 т = 221,7 або 222 мішки
Розрахунок кількості штабелів висотою 6 рядів мішків укладених п’ятериком:
222 : 6 : 5 = 7,4 або 8 штабелів
За схематичним планом розміщення зерна і насіння в сховищі визначаємо його мінімальну площу:
49,4 * 17,5 = 864,5 м2
![]() ![]() ![]() ![]() ![]() ![]() ![]() ![]() |
Рис. 2 Схематичний план розміщення зерна і насіння в сховищі
Рис. 2. Схематичний план розміщення зерна і насіння в сховищі
2.4.2. Спостереження за зерном і насінням під час зберігання
Істотними і обов'язковими заходами для зниження втрат зерна та насіння при зберіганні і підвищення їх стійкості є правильно розміщення партій у сховищах та спостереження за ними.
Потреба в систематичному спостереженні за зерновими масами при зберіганні випливає з їх властивостей і процесів, які відбуваються в них. Добре організоване спостереження і вмілий, правильний аналіз добутих даних дають змогу своєчасно запобігати небажаним явищам і з мінімальними затратами довести зернову масу до стану консервації або реалізувати її без втрат.
Оскільки спостереження повинні бути організовані за кожною партією зерна, їх прагнуть вести найпростішими, але досить надійними методами. Так, визначаючи температуру зернової маси, вологість її, стан за зараженістю шкідниками і показники свіжості (колір і запах), можна дістати достатнє уявлення про ступінь консервації і якість. У партіях насінного зерна перевіряють ще схо- жість, енергію проростання і життєздатність.
Найважливішим показником, що характеризує стан зернової маси при зберіганні, є температура. Низька температура в усіх ділянках насипу (8-10° і нижче) свідчить про консервацію зернової маси, а отже, і благополучне зберігання.
Вплив навколишнього середовища (зовнішнього повітря, стін зерносховищ тощо) і фізіологічні процеси в зерновій масі можуть призвести до появи неоднакової температури в різних ділянках насипу, тому температуру треба визначати в різних шарах зернової маси. Підвищення температури зернової маси, яке не відповідає зміні температури повітря, свідчить про активізацію фізіологічних процесів і початок самозігрівання.
Для визначення температури зернової маси, а також температури повітря в сховищах і поза ними використовують спиртові або ртутні термометри. Термометри вміщують у металеву оправу, яка нагвинчується на дерев'яну або металеву штангу. Така штанга складається з кількох колін (двох-трьох), які згвинчуються, що дає змогу змінювати довжину термометра залежно від висоти насипу зерна в складі.
При зберіганні насінних фондів слід мати одну термоштангу на кожний засік. Термоштанга повинна постійно перебувати в насипу, у його верхньому (20-30 см від поверхні), середньому або нижньому шарі (20-30 см від підлоги. Переміщення штанги в межах насипу періодично здійснює спостерігач.
Відомі й інші методи вимірювання температури зернової маси – електрометричні із застосуванням термометрів опору та з центральним пультом спостереження. Найчастіше їх застосовують у силосах елеваторів.
Контроль за станом зараженості зернових мас дає змогу своєчасно локалізувати розвиток кліщів і комах або повністю знищити їх. Зараженість зернової маси в складі перевіряють роздільним дослідженням виїмок за шарами насипу (у верхньому, середньому і нижньому), тому що шкідники можуть мігрувати в різні ділянки її.
Дуже добре, якщо в господарстві є можливість перевіряти і вологість партій, які зберігаються. Цей показник при зберіганні доцільно виявляти в усіх шарах насипу. Перевірку посівних якостей насіння, одночасно вологості і зараженості їх провадять у контрольно-насінних лабораторіях.
Періодичність спостереження за зерновими масами залежить віл їхнього стану. Так, у партіях свіжозібраного насіння з підвищеною вологістю температуру перевіряють щодня, а в сухих – двічі на декаду. У партіях охолодженого зерна її досить перевіряти раз у декаду або навіть раз у 15 днів. Залежно від температурного фактора встановлена і періодичність перевірки на зараженість шкідниками хлібних запасів. При температурі зернової маси нижче 0° досить проводити протягом місяця одне спостереження, а при температурі вище 10° – раз у 10 днів.
Схожість насіння в кондиційних партіях визначають не рідше одного разу в 4 місяці і не пізніше як за 10-20 днів до сівби. Вологість насіння в цих партіях перевіряють 1-2 рази на місяць.
Результати спостереження записують у журнал за рекомендованою формою. Крім того, ведуть насінну шнурову книгу [5].
2.4.3. Активне вентилювання зернових мас
Активне вентилювання зернової маси полягає у примусовому продуванні її атмосферним повітрям. Його проводять для збереження якості сирого і вологого зерна, запобігання розвиткові плісені та шкідників хлібних запасів. В окремих випадках його застосовують для прискорення процесу післязбирального дозрівання, вирівнювання температури і вологості зернової маси. Під впливом активного вентилювання змінюється повітря в міжзернових проміжках насипу.
За інтенсивністю та характером руху повітря в насипу розрізняють вентилювання пасивне й активне, безперервне й переривчасте.
При пасивному вентилюванні повітря в насипі перемішується переважно через його різну щільність, різницю температур, виникнення або посилення протягів через відкриті двері сховища. Воно малоефективне.
Активне, вентилювання зерна характеризується інтенсивним повітрообміном у насипу. Його проводять за допомогою установок, обладнаних вентиляторами. Буває безперервним і переривчастим.
Активне вентилювання зерна використовують для охолодження насипів, їх проморожування, сушіння, дегазації, ліквідації самозігрівання, прогрівання насіння перед сівбою тощо. Режими його залежать від подачі повітря, його температури і вологості, тривалості продування, висоти (товщини) зернового шару.
Профілактичне вентилювання, застосовують для збагачення киснем повітря міжзернового простору, вирівнювання температури і вологості в зерновому насипі, ліквідації комірного запаху, зберігання життєздатності насіння, запобігання виникненню осередків самозігрівання та ін.
Вентилювання для охолодження зерна. Відомо що, при зниженні температури зерна від плюс 10°С і нижче у ньому значно гальмуються всі фізіологічні та мікробіологічні процеси. Спочатку зернову масу охолоджують, використовуючи нічні пониження температури повітря, потім проводять охолодження вентиляторами.
Вентилювання для проморожування зерна. Температуру зерна знижують до мінусових значень. Зерно після цього перебуває в анабіозному стані..
Вентилювання для сушіння зерна і насіння проводять у камерних сушарках заводів, у сховищах, обладнаних відповідними установками. Так, щоб не допустити або звести до мінімуму травмування насіння бобових, соняшнику та деяких інших культур, його часто висушують у насипу вентилюванням.
Вентилювання насінного зерна забезпечує прискорення післязбирального дозрівання і підвищення енергії проростання та схожості свіжозібраного недозрілого насіння.
Активне вентилювання насипу освіжає повітря міжзернових просторів, збагачує його на кисень, і запобігає загибелі зерна в безкисневому середовищі.
Вентилювання для дегазації зазвичай проводять у теплі весняні дні. При цьому немає потреби перемішувати зерно. Тривалість такого способу вентилювання залежить від повноти дегазації, яку контролюють за кількістю залишку фуміганту в зерні [4].
Поряд із значним технологічним ефектом активне вентилювання вигідне і в економічному відношенні. При цьому не потрібно переміщувати зернову масу, що дає змогу значно скоротити потребу в робочій силі. Порівняно з перелопачуванням, наприклад, воно обходиться в 10-20 разів дешевше, а за технологічним ефектом взагалі незрівнянне.
Активне вентилювання застосовують в елеваторах, складах і на площадках, обладнавши їх спеціальними переносними або стаціонарними установками. У господарствах поширені такі установки:
1) стаціонарні з влаштуванням постійних каналів у підлозі складу або площадки:
2) підлогові переносні – являють собою систему переносних повітророзподільних решіток, які кладуть у потрібному місці на підлогу складу або площадки;
3) бункери і силоси;
4) пересувні трубні.
Як у першому, так і в другому типах установок повітря в канали і решітки надходить крізь дифузор, з'єднаний з осьовим або відцентровим електровентилятором достатньої потужності і продуктивності. Вентилятори приєднують до дифузора за межами складу, вздовж його поздовжньої або торцевої стіни і захищають від опадів.
Для активного вентилювання зернових мас використовують багато марок осьових (ВМ-200 «Проходка», СВМ-4, СВМ-5 та ін.) і відцентрових (Ц-9-55 і Ц-9-57 різних номерів, ЕВР різних номерів та ін.) вентиляторів.
Бункерні установки – це циліндричні або прямокутні різної висоти бункери (до 8-12 м) або силоси елеватора (до 30 м), обладнані спеціальними каналами для нагнітання повітря в зернову масу. Повітря подається знизу і проходить крізь усю висоту насипу, в інших продування зернової маси відбувається радіально або пошарово.
У сільськогосподарських підприємствах використовують циліндричні бункери з металу з радіальним подаванням повітря місткістю на 12,5-25-50 т пшениці. Усередині бункера (по центру) вертикально встановлюється циліндричний канал, стінки якого, як і самого бункера, мають виштампувані отвори для проходу повітря. Повітря, що нагнітається вентилятором, надходить у канал (внутрішній циліндр), з нього потрапляє в зернову масу і виходить крізь перфоровані стінки назовні. Усередині повітророзподільного каналу є рухомий поршень, який забезпечує рівномірний розподіл повітря в зерновій масі. Бункери такого типу оснащені електричними повітропідігрівачами.
З трубних установок у сільськогосподарських підприємствах зустрічаються пересувні трубні установки ПВУ-1. У зернову масу залежно від об'єму її вводять одну або кілька труб. Кожна труба складається з трьох частин: нижньої, верхньої і перехідної муфти, що з'єднує їх. На верхній кінець труби надівається вентиляційний агрегат.
Заглиблення труб у насип зерна і витягування їх провадять за допомогою електровібромолота. Установки ПВУ-1 використовують при висоті насипу зернової маси до 3,5-5,5 м.
Вентилювання відсмоктуванням рекомендується використовувати для ліквідації низового, гніздовою і суцільного самозігрівання зернової маси, а також для часткового її знезаражування від дрібних шкідників.
Недоліком пересувних трубних установок є система використання повітря. Тобто для вентилювання використовується не зовнішнє повітря, а те, що є в складі. Тому при обробці великих мас зерна у складі підвищується температура повітря і його вологість. Тому необхідно забезпечувати природний приплив свіжою повітря. Другим недоліком установок ПВУ-1 є їх порівняно велика енергоємність.
В останні роки застосовують телескопічні вентиляторні установки (ТВУ-2). У зібраному вигляді для транспортування – це труба, в якій розміщені 4 ланки, що входять одна в одну. Ці ланки перфоровані по всій поверхні отворами діаметром 3 мм. До зовнішнього кінця труби приєднують вентилятор, який подає 12 тис. м3 повітря на годину.
В останні роки в сільському господарстві багатьох країн, які одержують при збиранні врожаю зернову масу з підвищеною вологістю, великого поширення набуло сушіння способом активного вентилювання підігрітим повітрям. Найбільшого ефекту досягають при підігріванні повітря на 10-15°. Технічно його здійснюють, використовуючи бункери для активного вентилювання, які оснащені підігрівачами повітря. Або насіння різних культур насипають шаром 0,5-1 м на спеціально обладнані площадки з подвійною підлогою. Верхня підлога являє собою повітророзподільні решітки, а нижня є суцільною і щільною.
Для підігрівання повітря використовують електрокалорифери (ВПЗ-4) або теплогенератори (ТГ-75, ТГ-160, ВПТ-400, ВПТ-600 та ін.). Для прискорення сушіння в установку монтують додаткові вентилятори [5]
Отже з огляду на все вищесказане активне вентилювання зернової маси продовольчого зерна проса з вологістю 13% і рівноважною вологістю 12,5% при температурі 10оС та відносній вологості зовнішнього повітря 60% є доцільним. Оскільки вологістю проса вища за рівноважну вологість.
Оптимальна питома подача повітря для охолодження зерна проса на установці ПЗП – 48 становить 50 м3/т год. А загальна потужність вентилятора розраховується за формулою:
V = g * m
де V – загальна потужність вентиляторів, м3/год;
g – оптимальна питома подача повітря м3/т;
m – маса зерна що вентилюється, т;
V = 50 м3/т год * 480,77 т = 24038,5 м3/год
Для забезпечення оптимальної питомої подачі повітря в зернову масу необхідно 1 вентилятор ЦЧ – 70 №8 потужністю 21000 м3/год оскільки:
24038,5 м3/год : 21000 м3/год = 1,14 або 2 вентилятор
При різниці температури зерна і зовнішнього повітря 5оС питомій подачі повітря в зернову масу 50 м3/т год, швидкість охолодження дорівнює 0,12 оС/год. Отже тривалість активного вентилювання становитиме:
5оС * 0,12оС/год = 41,7 год
Отже для охолодження насипу і підтримання оптимальної вологості зерна проса необхідно проводити його вентилювання на протязі 41,7 год вентиляційною установкою ПЗП – 48 в комплекті з двома вентиляторами ЦЧ – 70 №8.
2.4.4. Кількісний облік зерна і насіння при зберіганні
Під час зберігання в зерновій масі проходять процеси життєдіяльності, які призводять до зменшення її маси.
Якісні показники сухого, чистого, незараженого шкідниками та охолодженого зерна майже не змінюються і втрати його мінімальні. Розрізняють дійсні та уявні втрати зерна.
Уявні втрати зумовлені помилками у визначенні маси та якості зерна під час його приймання та витрачання.
Дійсні втрати поділяють на природні (нормативні) і наднормативні. Вони можуть бути зумовлені недоліками в організації й технології проведення операцій із зерном. За своєю природою дійсні втрати бувають механічними і біологічними. Механічні втрати зерна під час його зберігання полягають виключно в його розпиленні. Ці втрати виникають внаслідок видалення із зернової маси при її переміщеннях, очищенні і сушінні найдрібніших частинок, які не можуть затримуватися звичайними фільтрами.
Для зменшення механічних втрат і травмування зерна кількість переміщень його зводять до мінімуму, регулюють роботу зерноочисних машин і транспортних механізмів так, щоб травмування зерна було мінімальним, що сприятиме скороченню втрат в результаті зменшення розпилення.
Біологічні втрати, зумовлюються фізіолого-біохімічними властивостями зернової маси. В нормативних умовах зберігання відбувається природний процес розкладання речовин, пов'язаний з диханням зерна. Втрати сухої речовини в результаті дихання зерна називають природними. Величина біологічних втрат залежить також від вологості зерна.
Визначення природних втрат сухого і чистого зерна при тривалому зберіганні у виробничих умовах дало змогу вивести середні їх величини. Діючі норми природних втрат зерна при зберіганні на підприємствах диференційовані для культур, типів зерносховищ залежно від умов і строків зберігання і не повинні перевищувати максимально допустимі норми [4].
Розрахуємо природні втрати маси продовольчого зерна і насіння проса за 250 діб зберігання відповідно насипом і в мішках.
Розрахунок фактичного терміну зберігання:
В = 250 : 30 = 8,3 міс.
Якщо термін зберігання перевищує три місяці то норма природних втрат розраховується за формулою:
де х – норма природних втрат для фактичного терміну зберігання, %;
а – норма природних втрат для встановленого попереднього у порівнянні з фактичним терміном зберігання, %;
б – норма природних втрат для встановленого наступного після фактичного терміну зберігання, %;
в – фактичний термін зберігання, міс.;
г і д – відповідно попередній і наступний у порівнянні з фактичним терміни зберігання, для яких встановлено норми природних втрат, міс.;
Розрахунок норм природних втрат для продовольчого зерна:
Розрахунок норм природних втрат для насіння:
Фактичні природні втрати становлять:
- продовольчого зерна
480,77 т * 0,165 % : 100 = 0,79 т
- насіння
7,76 т * 0,088 % : 100 = 0,0068 т
Висновки
Просо є дуже цінною крупяною культурою. І для того щоб в процесі післязбиральної обробки і зберіганні зберегти його цінні властивості ми повинні зменшувати втрати, як в якості так і в масі.
Основні причини погіршення як зерна так і насіння є: травмування на технологічних лініях; низький вихід на неправильно відрегульованих машинах і лініях; втрати схожості в наслідок самозігрівання, порушення технологічних процесів під час сушіння, знезаражування і протруювання; значне засмічування важковідокремлюваними культурами при переробці, транспортуванні та зберіганні.
Досягти високої якості післязбиральної обробки зерна і насіння і уникнути його втрат під час обробки можна при дотриманні організаційних і технологічних рекомендацій. Вони полягають в узгодженні дій між окремими підрозділами господарства в питанні якісного і своєчасного виконання зобов’язань по прийманню і переробці насіння. Це означає, що насіння на пункти обробки має надходити в такому обсязі, щоб можна було максимально використати виробничі потужності оброблюваних підприємств і не допустити нагромадження на майданчиках, токах і сховищ необробленого насіння.
Технологічний процес насіннєобробних агрегатів треба розраховувати на одноразовий пропуск насіння з доведенням його до необхідних кондицій, оскільки повторні обробки призводять до збільшення травмування насіння, зниження його якості. Технологічні лінії повинні мати якнайменші перепади висоти подачі насіння, забезпечувати мінімальне травмування його під час сушіння, очищення протруювання, переміщення.
Всі технологічні процеси по обробці насіння повинні проводити висококваліфіковані оператори з суворим дотриманням всіх елементів технології, а також оптимальних норм виходу кондиційного насіння з вороху.
Правильно організований контроль за станом зберігання насіння, своєчасне прийняття дійових заходів по утриманні на рівні або поліпшенню його якісних показників також є одним із елементів усунення втрат насіння.
Список використаної літератури
1. Денисенко О.Г., Зінкевич Л.Л, Довідник по закупівлі, зберіганню і реалізації насіння. – К.: Урожай, 1986 – 201 с.
2. Жемела Г. П., Шемавньов В.І., Олексик О.М., Технологія зберігання і переробки продукції рослинництва. – Полтава 2003.-420 с.
3 Зозуля О. Л., Мамалиґа В. С. Селекція та насінництво польових культур. - К.: Урожай, 1990-416 с.
4. Подпрятов Г.І., Скалецька Л.Ф., Сеньков А.М., Хилевич В.С., Зберігання і переробка продукція рослинництва. –К.: Мета, 2002.-495.с.
5. Лесик Б.В., Трисвятський Л.О., Снежко В.А., Сабуров М.В., Зберігання і технологія сільськогосподарських продуктів. –К: Вища шк.. 1980.- 416с.
6. Окнін Б.С., Горбачєв І.В., та ін..-М.: Агропроміздат, 1987.-238 с. Машини для післязбиральної обробки насіння.
7. Танчик С.П., Дмитрищак М.Я., та ін.. Технологія виробництва продукції рослинництва. Підручник.- К: -2008р. 1000 с.
8. Технологія післязбиральної обробки і зберігання насіння. – М.: Агропроміздат, 1987.- 288с.:. Карпов Б.А.
9. Фітофармакологічний довідник /За ред. М.Д. Євтушенка, М.Ф.Марютіна/ ХНАУ. – Х., 1997.-297 с
Дата добавления: 2018-06-01; просмотров: 263; Мы поможем в написании вашей работы! |
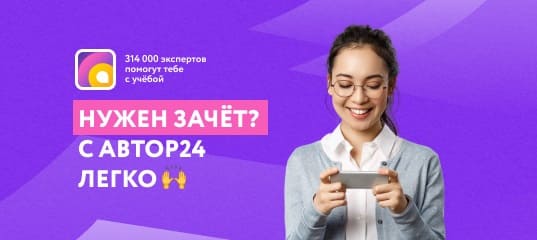
Мы поможем в написании ваших работ!