Сверхтвердые синтетические материалы
Развитие физики высоких давлений способствовало созданию широкой номенклатуры различных синтетических сверхтвердых материалов на основе алмаза и кубического нитрида бора (эльбора).
Синтетические алмазы и эльбор производятся в виде:
- порошкообразных материалов, применяемых для изготовления различных абразивных инструментов;
- поликристаллических материалов, предназначенных для оснащения лезвийного инструмента (поликристаллические материалы изготавливаются в виде цилиндров и пластин небольшой высоты).
Сверхтвердые поликристаллические материалы в свою очередь условно делят на группы:
- поликристаллы на основе алмаза;
- поликристаллы на основе нитрида бора;
- композиционные (двухслойные) материалы.
Инструменты, оснащенные поликристаллическими алмазами, обладают высокой износостойкостью, хорошей теплопроводностью ( 140 Вт/(м∙К)), малыми коэффициентами трения и линейного расширения, слабой адгезией к металлам и сплавам, за исключением железа и сталей. Недостатком синтетических алмазов (АС) является интенсивное растворение в железе и его сплавах при температуре 700-800°С.
Поликристаллические алмазы АСПК, АСБ-Р, АСБ-Б, АСПВ применяются на операциях точения и растачивания при обработке медных, алюминиевых, титановых сплавов и стеклопластиков.
Физико-механические свойства различных марок поликристаллов на основе алмазов лежат в пределах: микротвердость – 70-100 ГПа, предел прочности на сжатие – от 200-400 (баллас) до 4400-5000 МПа (карбонит); предел прочности на изгиб – от 500 до 2000 МПа; теплостойкость 700-800°С.
|
|
Поликристаллические материалы на основе кубического нитрида бора (КНБ) широко применяются при изготовлении лезвийных инструментов, используемых на операциях точения, торцового фрезерования и зенкерования при обработке закаленных сталей и высокопрочных чугунов. Уступая алмазу по твердости, эльбор отличается высокой теплостойкостью, химической инертностью к углероду, входящему в состав многих обрабатываемых материалов. Промышленностью выпускается несколько марок сверхтвердых материалов на основе эльбора: эльбор-Р (композит 01), белбор (композит 02), композит 03, композит 05, композит 09, гексанит-Р (композит 10) и др. Физико-механические свойства этих материалов изменяются в следующих пределах: микротвердость – 20-40 ГПа, предел прочности на сжатие – 2000-4000 МПа; предел прочности на изгиб – 250-1200 МПа; теплостойкость – 800-1500°С.
Особенностью композиционных материалов на основе алмаза и эльбора является то, что спекание порошков сверхтвердых материалов производится при высоких температурах и давлениях на твердосплавной подложке, в результате чего образуется слой поликристаллов толщиной 0,5-2 мм, прочно связанный с материалом подложки.
|
|
Двухслойные сверхтвердые материалы имеют следующие преимущества по сравнению с однородными по объему материалами:
- упрощается технология крепления режущих элементов в корпусе инструмента;
- наличие подложки существенно увеличивает ударную вязкость слоя из сверхтвердых материалов.
Наиболее известными композитами на основе алмаза являются ДАП, ДИАМЕТ, АМК-25, АМК-27, АТП, а на основе эльбора – 05Д-2С, 10Д, БПК.
Физическая природа износа инструментов
(для самостоятельного изучения)
Износ и связанное с ним затупление режущего инструмента происходят в результате сложного взаимодействия механических, физических и химических явлений. Доминирование одного явления над другими приводит к изнашиванию режущего инструмента различных видов. На основании многочисленных экспериментальных исследований процесса резания материалов установлены четыре вида изнашивания режущих инструментов: абразивное, адгезионное, диффузионное и химическое (окислительное).
Абразивное изнашивание инструмента происходит за счет царапания его рабочих поверхностей стружкой (элементами стружки), частицами нароста, а также твердыми включениями, имеющимися в материале обрабатываемой заготовки. Возможность царапания рабочих поверхностей режущего инструмента, более твердых по сравнению с обрабатываемой заготовкой, обусловлена тем, что инструментальный материал по своей основе неоднороден. В связи с этим на его рабочих поверхностях имеются участки как большей, так и меньшей твердости. Поэтому под воздействием вышеуказанных факторов происходит удаление частиц инструментального материала с менее твердых участков, разрыхление поверхностных слоев с последующим их более интенсивным изнашиванием.
|
|
Адгезионное изнашивание заключается в молекулярном взаимодействии (схватывании) поверхностных слоев режущего инструмента и обрабатываемого материала и последующем вырывании частиц материала инструмента.
Природа данного явления обусловлена тем, что контактные поверхности режущего инструмента и обрабатываемого материала не являются идеально гладкими, то есть имеют вполне определенную шероховатость. Поэтому их точками соприкосновения в процессе резания являются выступающие участки микрорельефа (рис. 44), что вызывает в местах контакта большие удельные нагрузки, разрушающие окисные пленки.
|
|
Рис. 44. Схема образования «мостиков холодной сварки» |
В результате такого контакта происходит образование «мостиков холодной сварки», которые разрушаются и вновь образуются вследствие движения деформируемого материала относительно режущего клина. Причем процесс разрушения «мостиков» сопровождается вырыванием частиц инструментального материала и образованием адгезионных пятен. Данное явление активно проявляется, когда температура в зоне резания составляет более 600 .
Диффузионное изнашиваниеинструмента происходит в результате взаимного растворения металла заготовки и материала инструмента. На активность процесса растворения оказывает влияние высокая температура (900…1200 ) контактного слоя, возникающая при высокой скорости резания. Процесс диффузионного изнашивания приводит к изменению химического состава и физико-химических свойств поверхностных слоев инструмента, снижению его износостойкости. Поэтому диффузионное изнашивание можно рассматривать как разновидность химического изнашивания.
Химическое (окислительное) изнашивание происходит за счет окисления при высоких температурах трущихся слоев благодаря высокой проникающей способности кислорода и ускоренного его соединения с ювенильными поверхностями стружки и инструмента. Образовавшиеся окисные пленки очень хрупки и поэтому легко разрушаются, оголяя нижеследующие слои, которые в свою очередь также окисляются и подвергаются разрушению.
Окислительное изнашивание наступает обычно при температуре
резания, равной 700...900°С. У твердых сплавов наиболее быстро окисляется кобальтовая связка, при разрушении которой нарушается монолитность сплава, ослабляется связь между зернами карбидов титана и вольфрама. Окислительный износ можно существенно уменьшить или даже предотвратить за счет применения в качестве смазочно-охлаждающих технологических средств (СОТС) инертных газов: азота, аргона и гелия.
Дата добавления: 2018-06-01; просмотров: 512; Мы поможем в написании вашей работы! |
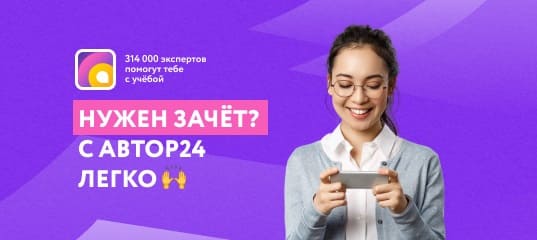
Мы поможем в написании ваших работ!