Основные параметры зубчатых колес
Тмм ответы на вопросы для зачёта
32. Основные параметры зубчатых колёс. Коэффициент перекрытия
Коэффициент перекрытия – геометрическое место точек касания сопряженных профилей (спрямленной дуги основной окружности от входа до выхода из зацепления одной пары зубьев) к шагу pb зубьев по основной окружности.
Коэффициент перекрытия можно представить как отношение длины активного участка линии зацепления –b
Числовое значение коэффициента перекрытия показывает долю времени нахождения в зацеплении двух пар зубьев.Например, e = 1,68 означает, что 68 % времени в зацеплении находится две пары зубьев. Таким образом, коэффициент перекрытия характеризует нагрузочную способность передачи, плавность её работы.
Теоретически максимальное значение коэффициента перекрытия для прямозубых колес =1,98, т.е. в зоне полюса (точкаW) существует область однопарного зацепления.
Значение коэффициента перекрытия определяют через параметры зубчатых колес на основании картины зацепления:
, (1.92)
где aw – угол зацепления передачи; ,
,
– соответственно радиусы окружностей вершин и основных окружностей зубчатых колес:
Коэффициент показывает сколько пар зубьев в среднем одновременно находится в зацеплении. Для прямозубой передачи обычно
. Чем больше
, тем более плавно и бесшумно работает передача.
Другим качественным показателем является коэффициент скольжения, который учитывает влияние геометрии передачи и её кинематики на скольжение и износ профилей, скользящих друг по другу (рис. 74), что видно из картины скоростей. На этой картине:
|
|
Зубчатой передачей называется механизм, служащий для передачи вращательного движения с одного вала на другой, изменения частоты вращения ведомого вала механизма и величины крутящего момента на нем, а также для преобразования вращательного движения в поступательное, и наоборот (реечные зубчатые передачи).
Зубчатое колесо, сидящее на передающем вращение валу, называется ведущим, а на получающем вращение - ведомым.
Меньшее из двух колес зубчатой передачи обычно называют шестерней, а большее - колесом. Термин "зубчатое колесо" относится к обеим деталям передачи.
Зубчатые передачи представляют собой наиболее распространенный вид передач в современном машиностроении, поскольку они наиболее полно удовлетворяют функциональным требованиям в сравнении с другими типами передач (при прочих равных условиях) - они надежны и долговечны, имеют небольшие габариты, относительно дешевы в изготовлении и эксплуатации, обладают рядом других преимуществ и достоинств.
Основные параметры зубчатых колес
|
|
· Делительными окружностями пары зубчатых колес называются соприкасающиеся окружности, условно проведенные из центров колес, и перекатывающиеся одна по другой без скольжения. Делительные окружности колес, находящихся в зацеплении, являются сопряженными. На чертежах делительную окружность выполняют штрихпунктирной линией, а ее диаметр обозначают буквой d.
· Модуль зубчатого зацепления m - это часть диаметра делительной окружности зубчатого колеса, приходящаяся на один зуб, т. е. m = d/z.
Значение модулей для всех передач - величина стандартизированная.
· Диаметр окружности вершин зубьев da - диаметр окружности, описывающей вершины головок зубьев.
· Диаметр окружности впадин зубьев df - диаметр окружности, описывающей основания ножек зубьев.
· Высота делительной головки зуба ha - расстояние между делительной окружностью колеса и окружностью, ограничивающей вершины зубьев.
· Высота делительной ножки зуба hf - расстояние между делительной окружностью колеса и окружностью, описывающей основания ножек (впадин) зубьев.
· Высота зуба h - расстояние между окружностями вершин и впадин зубьев цилиндрического зубчатого колеса h = ha + hf.
· Окружной шаг зубьев Рt - расстояние (мм) между одноименными профильными поверхностями соседних зубьев. Шаг зубьев равен длине делительной окружности, разделенной на число зубьев колеса z.
|
|
23 Основные динамики машин. Режимы движения машины. Роль маховика и регулятор
Чтобы уменьшить коэффициент неравномерности движения δ, т.е. чтобы сделать вращение кривошипа более плавным, на машину устанавливают маховик. Маховик – это массивное колесо, неподвижно скрепленное, обычно с кривошипом, и вращающееся с ним как одно целое.
Маховик выполняет в машине роль аккумулятора (накопителя) кинетической энергии: за одну часть цикла он накапливает энергию, чтобы вернут ее в другую часть цикла. При этом он, накапливая кинетическую энергию, разгоняется в те моменты времени, когда с двигателя поступает на машину больше работы, чем расходуется рабочим органом. И отдавая кинетическую энергию, притормаживается, когда рабочий орган расходует работы больше, чем поступает её в данный момент с двигателя.Чем больше маховик, тем будет меньше ∆ω и коэффициент неравномерности движения для любой машины самое лучшее, когда угловая скорость строго постоянна, т.е. ∆ω=0. Но чтобы получить ∆ω→0, нужен маховик, у которого момент инерции Jмахов→∞. Поэтому маховик рассчитывают из условия, чтобы при установке его в машину, коэффициент неравномерности движения δ стал равен наперед заданной допустимой величине.
|
|
есть два основных варианта установки маховика: на вал кривошипа или на более быстроходный вал.
Регуляторы- устройства, автоматически регулирующие затрачиваемую работу так, чтобы сохранять приблизительно постоянную V двигателя, когда изменяются силы сопротивлений или движущие силы.
24 Режимы работы подшипников ротора.
25. Статическая и динамическая балансировка роторов.
Чтобы устранить возмущающую силу, ротор уравновешивают, т.е. устраняют его небаланс. Операции по устранению небаланса называют балансировкой .
Балансировать можно каждую деталь ротора в отдельности или весь ротор в целом; последний способ экономичнее и точнее.
Чтобы сбалансировать неуравновешенность ротора, нужно на том же расстоянии от оси (там где выявлен небаланс), но в диаметрально противоположном направлении наплавить (подвесить) груз необходимой для балансировки массы; после чего ротор окажется сбалансированным и никакой возмущающей силы при его вращении возникать не будет.
Величину и расположение небаланса находят при выполнении различных видов балансировок.
Различают статическую и динамическую балансировки ротора:
1. Статической балансировка называется потому, что для выявления и устранения небаланса не требуется вращения ротора; уравновешивания достигают, когда ротор находится в состоянии покоя.
Недостатки статической балансировки:
Способствует появлению неуравновешенных пар сил;
Возможно снижение точки балансировки из-за скольжения качения;
после статической балансировки, даже при отсутствии неуравновешенных пар сил, всегда остается значительный остаточный дисбаланс, обусловленный силами трения, действующими на цапфы балансируемого ротора во время балансировочного процесса.
2. Динамическая неуравновешенность наблюдается тогда, когда неуравновешенные массы ротора дают две возмущающие силы, одинаковые по величине, но противоположно направленные и расположенные на разных концах. При этом может оказаться, что общий центр тяжести ротора расположен на оси вращения, т.е. статически ротор уравновешен.Такую неуравновешенность можно выявить только при вращении ротора, так как общий центр тяжести ротора расположен на его оси, и только при вращении обе неуравновешенные массы образуют пару возмущающих сил переменного направления. Следовательно, статически отбалансированный ротор в некоторых случаях может иметь динамическую неуравновешенность. Операция по выявлению и устранению динамического небаланса называется динамической балансировкой.
Статическая балансировка. У неуравновешенной детали ее масса располагается несимметрично относительно оси вращения. Поэтому при статическом положении такой детали, т. е. когда она находится в покое, центр тяжести будет стремиться занять нижнее положение (рис.1). Для уравновешивания детали добавляют с диаметрально противоположной стороны груз массой Т2 с таким расчетом, чтобы его момент Т2L2 был равен моменту неуравновешенной массы Т1L1. При этом условии деталь будет находиться в равновесии при любом положении, так как центр тяжести ее будет лежать на оси вращения. Равновесие может быть достигнуто также путем удаления части металла детали высверловкой, спиливанием или фрезерованием со стороны неуравновешенной массы Т1. На чертежах деталей и в Правилах ремонта на балансировку деталей дается допуск, который называют дисбалансом (г/см).
Статической балансировке подвергают плоские детали, имеющие небольшое отношение длины к диаметру: зубчатое колесо тягового редуктора, крыльчатку вентилятора холодильника и т.п. Статическая балансировка ведется на горизонтально-параллельных призмах, цилиндрических стержнях или на роликовых опорах. Поверхности призм, стержней и роликов должны быть тщательно обработаны. Точность статической балансировки во многом зависит от состояния поверхностей этих деталей.
Динамическая балансировка. Динамической балансировке обычно подвергают детали, длина которых равна или больше их диаметра. На рис. 2 показан статически отбалансированный ротор, у которого масса Т уравновешена грузом массой М. Этот ротор при медленном вращении будет находиться в равновесии в любом положении. Однако при быстром его вращении возникнут две равные, но противоположно направленные центробежные силы F1 и F2. При этом образуется момент FJU который стремится повернуть ось ротора на некоторый угол вокруг его центра тяжести, т.е. наблюдается динамическое неравновесие ротора со всеми вытекающими отсюда последствиями (вибрация, неравномерный износ и т. п.). Момент этой пары сил может быть уравновешен только другой парой сил, действующей в той же плоскости и создающей равный противодействующий момент.
Статический дисбаланс
Дисбаланс моментов m1 = m2
Динамический дисбаланс m1 ¹ m2
30 При уравновешивании многоцилиндровых машин за счёт различного расположения кривошипов
Конструкция многоцилиндровых поршневых машин зависит от типа рабочего процесса и связана также с возможностью уравновешивания сил инерции, действующих в различных цилиндрах. Большинство поршневых ДВС имеет несколько цилиндров и одинаковых звеньев шатунно – поршневых групп, соединенных общим коленчатым валом. При проектировании многоцилиндровых машин идут путём выбора разного числа цилиндров и рядного или углового их расположения Угловой сдвиг кривошипов коленчатого вала выбирают с целью равномерного чередования рабочих процессов.
Многоцилиндровые двухтактные двигатели Рабочий процесс в цилиндре двухтактного двигателя совершается за один оборот коленчатого вала. Поэтому при соблюдении равенства угловых интервалов между рабочими ходами в многоцилиндровых двухтактных двигателях коленчатые валы получаются с несимметрично расположенными кривошипами. Рассмотрим способы уравновешивания многоцилиндровых двухтактных двигателей. Однорядный четырехцилиндровый двигатель. В однорядном четырехцилиндровом двигателе применяется коленчатый вал с кривошипами под углом 90º: 360º/iц = 360º/4 = 90º, что обеспечивает равенство интервалов между рабочими ходами. На рис. 38 приведена схема коленчатого вала четырехцилиндрового двухтактного двигателя; порядок работы 1 – 3 – 4 – 2. Все силы инерции в двигателе с таким коленчатым валом взаимно уравновешиваются. Действительно, центробежные силы инерции Kr при крестообразном расположении кривошипов взаимно уравновешиваются при проектировании на оси x и y.
Четырехцилиндровый V-образный двигатель с углом раз- вала цилиндров γ = 90° и с кривошипами под углом δ = 180°. V-образное расположение цилиндров с углом развала γ = 90° и кривошипами под углом δ = 180° (рис. 41) применяется главным образом для двухтактных двигателей, для которых при по- рядке работы 1 – 2 – 3 – 4 обеспечивается равномерное чередование вспышек с угловым интервалом 90°. Рис. 41. Силы инерции, действующие в четырехцилиндровом V-образном двигателе (γ = 90º, δ = 180º) 78 Для четырехтактных серийных двигателей такое расположение цилиндров и кривошипов не применяется вследствие неравномерного чередования вспышек.
Дата добавления: 2018-06-01; просмотров: 907; Мы поможем в написании вашей работы! |
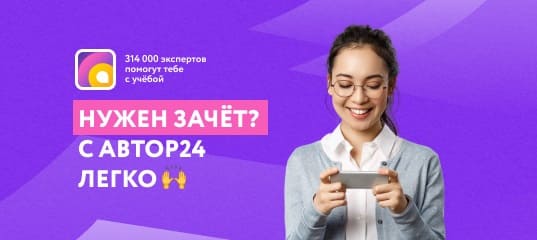
Мы поможем в написании ваших работ!