Современные инструментальные материалы.
Составляя управляющую программу надо учитывать радиус фрезы, для этого предусмотрены функции, управляющие смещением инструмента от заданной траектории:
G41 – коррекция слева от контура, используется для наружной обработки при движении по часовой стрелке или для внутренней обработки при движении против часовой стрелки.
G42 – коррекция справа от контура, используется для наружной обработки при движении против часовой стрелки или для внутренней обработки при движении по часовой стрелке.
. Управляющая программа, которую оператор запускает на станке с ЧПУ, задает движение кромки центра фрезы. Однако по умолчанию система ЧПУ управляет точкой пересечения торца шпинделя с его осью вращения (базовая точка).
G43
Чтобы управлять кромкой фрезы, а не торцем шпинделя, необходимо перенести базовую точку на кромку фрезы. Такое смещение именуют как коррекция длины инструмента. Если данную операцию не применять, то какой бы инструмент не был установлен, станок будет совмещать торец шпинделя с заданными в программе координатами по оси Z со всеми вытекающими последствиями.
Типы производства.
Организация производственных процессов на предприятии, выбор наиболее рациональных методов подготовки, планирования и контроля за производством во многом определяется типом производства.
Тип производства – совокупность организационно-технических и экономических характеристик и особенностей сочетания факторов и элементов организации производства, обусловленных номенклатурой, масштабом и регулярностью выпуска продукции.
|
|
Тип производства определяется следующими факторами:
- номенклатурой выпускаемых изделий;
- объемом выпуска;
- степенью постоянства номенклатуры выпускаемых изделий;
- характером загрузки рабочих мест.
В зависимости от уровня концентрации и специализации различают три типа производств:
- единичное;
- серийное;
- массовое.
По типам производства классифицируются предприятия, участки и отдельные рабочие места.
Тип производства предприятия определяется типом производства ведущего цеха, а тип производства цеха — характеристикой участка, где выполняются наиболее ответственные операции и сосредоточена основная часть производственных фондов.
Единичное производство характеризуется широкой номенклатурой изготовляемых изделий, малым объемом их выпуска, выполнением на каждом рабочем месте весьма разнообразных операций.
В серийном производстве изготовляется относительно ограниченная номенклатура изделий (партиями). За одним рабочим местом, как правило, закреплены несколько операций.
|
|
Массовое производство характеризуется узкой номенклатурой и большим объемом выпуска изделий, непрерывно изготовляемых в течение продолжительного времени на узкоспециализированных рабочих местах.
Тип производства оказывает решающее значение на особенности организации производства, его экономические показатели, структуру себестоимости (в единичном высока доля живого труда, а в массовом — затраты на ремонтно-эксплуатационные нужды и содержание оборудования), разный уровень оснащенности.
3. ISO P – Сталь. Самая большая по составу группа материалов, включающая различные сорта стали - от нелегированных до высоколегированных, включая стальные отливки, ферритную и мартенситную нержавеющую сталь. Как правило, материалы данной группы имеют хорошую обрабатываемость, но это зависит от твёрдости стали и процентного содержания в ней углерода.
Современные инструментальные материалы.
Инструментальные стали
Режущие инструменты, изготовленные из углеродистых инструментальных сталей У10А, У11А, У12А, У13А, обладают достаточной твердостью, прочностью и износостойкостью при комнатной температуре, однако теплостойкость их невелика. При температуре 200…250º С их твердость резко уменьшается. Поэтому они применяются для изготовления ручных и машинных инструментов, предназначенных для обработки мягких металлов с низкими скоростями резания, таких, как напильники, мелкие сверла, развертки, метчики, плашки и др. Углеродистые инструментальные стали имеют низкую твердость в состоянии поставки, что обеспечивает их хорошую обрабатываемость резанием и давлением. Однако они требуют применения при закалке резких закалочных сред, что усиливает коробление инструментов и опасность образования трещин.
|
|
Твёрдые сплавы
Они состоят из карбидов вольфрама, титана, тантала, сцементированных небольшим количеством кобальта. Карбиды вольфрама, титана и тантала обладают высокой твердостью, износостойкостью. Инструменты, оснащенные твердым сплавом, хорошо сопротивляются истиранию сходящей стружкой и материалом заготовки и не теряют своих режущих свойств при температуре нагрева до 750…1100 °С.
Установлено что твердосплавным инструментом, имеющим в своем составе килограмм вольфрама, можно обработать в 5 раз больше материала, чем инструментом из быстрорежущей стали с тем же содержанием вольфрама.
Недостатком твердых сплавов, по сравнению с быстрорежущей сталью, является их повышенная хрупкость, которая возрастает с уменьшением содержания кобальта в сплаве.
|
|
Минералокерамика
Минералокерамика – это инструментальный материал основой, которого является корунд – минерал кристаллического строения, состоящий из оксида алюминия Аl2О3.
Оксидную керамику рекомендуется использовать для чистового и получистового точения нетермообработанных сталей, а также серых и ковких чугунов с твердостью НВ 200 и менее.
Сверхтвёрдые материалы
Природные и синтетические алмазы обладают самой высокой твердостью (HV 10000 кгс/мм2), малыми коэффициентами линейного расширения и трения и высокой теплопроводностью, адгезионной стойкостью и износостойкостью. Недостатки алмазов – невысокая прочность на изгиб, хрупкость и растворимость в железе при относительно низких температурах (750°С), что препятствует использованию их для обработки железоуглеродистых сталей и сплавов на высоких скоростях резания, а также при прерывистом резании и вибрациях. Теплостойкость алмаза около 800° С.
Природные алмазы используются в виде кристаллов, закрепляемых в металлическом корпусе резца.
По твердости синтетические поликристаллы лишь незначительно уступают природным монокристаллам алмаза.
5. В организации должен быть организован метрологический учет всех средств измерительной техники.
Для всех средств измерительной техники установлены следующие виды поверок / калибровок:
- первичная
- периодическая
- внеочередная.
Первичная поверка / калибровка проводится при вводе СИТ в эксплуатацию (при отсутствии годного свидетельства поверке / калибровке) или после ремонта.
Периодическая поверка / калибровка проводится в процессе эксплуатации в соответствии с межкалибровочным / межповерочным интервалом, установленным для данного типа СИТ.
Внеочередная поверка / калибровка СИТ осуществляется независимо от межповерочного интервала, в сроки ранее установленных при:
- вводе в эксплуатацию после хранения;
- утере документов, подтверждающих проведение периодической поверки / калибровки;
- необходимости удостовериться в пригодности СИТ к выполнению измерений с соответствующими ТХ и МХ.
Метрологический учет СИТ может быть организован произвольным образом.
6. Калибровка СИКалибровка средств измерения (СИ) представляет собой комплекс операций, которые осуществляются для вычисления и подтверждения фактических значений метрологических параметров и/или пригодности калибруемых измерительных средств к дальнейшему использованию по назначению. Фактически это тот же перечень мероприятий, которые используются при поверке. Разница заключается в том, что калибровку проходят СИ, которые не требуется подвергать в обязательном порядке государственному надзору и контролю в рамках метрологических поверок.
Калибровка средства измерения выполняется с целью определения и подтверждения действительных значений метрологических характеристик и (или) пригодности к применению средства измерений, не подлежащего государственному метрологическому контролю и надзору.
7. Производительность механической обработки во многом зависит от того, насколько правильно назначены режимы резания для каждой операции. При этом стремятся достигнуть наибольшей производительности труда при наименьшей себестоимости данной технологической операции. [1]
Производительность механической обработки резанием увеличивается с повышением параметров режимов резания - подачи, глубины, скорости резания. Вместе с тем увеличение скорости резания приводит к повышению температуры резания и интенсивному износу инструмента, к понижению его стойкости. Под периодом стойкости, или стойкостью, понимают время между переточками инструмента. [2]
Производительность механической обработки практически прямо пропорциональна продольной подаче 5 при конкретных условиях резания, определенных значениях t, Я, о. Поэтому для сокращения основного времени обработку следует выполнять с 5ямх, соответствующей полному использованию режущих способностей инструмента, динамических возможностей станка при условии обеспечения заданной точности обработки. [3]
Производительность механической обработки валов во многом зависит от вида заготовки, ее материалов, размера и конфигурации, а также от характера производства. Заготовки получают отрезкой от горячекатаных или холоднотянутых нормальных прутков и непосредственно подвергают механической обработке. [4]
Для увеличения производительности механической обработки и повышения чистоты и точности ее большое значение имеет обработка н а п р о х о д со свободным входом и выходом режущего инструмента за пределы обрабатываемой поверхности. [6]
Для увеличения производительности механической обработки целесообразно обрабатывать максимальное число поверхностей на одном станке, с одного установа, за одну операцию, с применением одного инструмента, используя все возможности станка, на котором производится основная операция. [7]
Дата добавления: 2018-06-01; просмотров: 679; Мы поможем в написании вашей работы! |
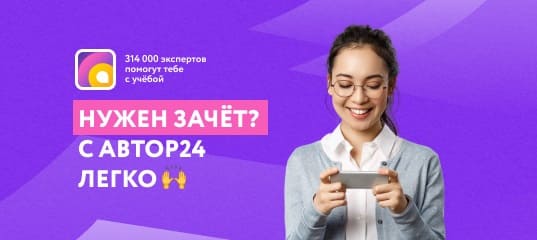
Мы поможем в написании ваших работ!