Система стандартов по управлению и информации.
Управление и информация тесно связаны между собой. Своевременная и полная информация является залогом принятия правильного управленческого решения. Основной задачей стандартизации в этой области является унификация документации по процессам управления и по информационным технологиям.
Увеличение номенклатуры производимых изделий, расширение сфер международного сотрудничества неизбежно вызывает рост количества управленческой документации и по экспертным оценкам составляет несколько сотен миллиардов в год. Создание и обработка документов требует все больших затрат и качества составления документации. По данным западных фирм из-за некачественно составленных деловых писем компании несут убытки, исчисляемые многими миллионами долларов.
Работа по унификации управленческой документации нашла свое отражение в стандартах унифицированной системы документации (УСД 6-я группа).
Стандартизация нашла свое применение и в информационных технологиях. Информационные технологии представляют собой совокупность средств и методов, которые позволяют обеспечить общество необходимой информацией. По данным ЮНЕСКО, более половины населения развитых стран участвуют в процессах производства и распространения информации; в ряде стран до половины национального продукта связано с информационной деятельностью.
В настоящее время в РФ, в соответствии Программой комплексной стандартизации, формируется комплекс стандартов по информационным технологиям, которая позволит разработать и внедрить в стране более 500 стандартов, соответствующих ИСО/МЭК. Система стандартов направлена на решение таких вопросов, как взаимосвязь локальных вычислительных сетей, методы и средства защиты информации, микрофотография и системы для записи документов и изображений (идентификационный менеджмент) и многое другое.
|
|
К стандартам по информационным технологиям относится Система информационно-библиографической документации (СИБИД). Ее важнейшими задачами являются: создание условий взаимодействия органов информации различных уровней; разработка и обеспечения функционирования систем научно-технической информации.
В комплексе стандартов по информационным технологиям входят стандарты по штриховому кодированию – ГОСТы Р 51001-51003, которые необходимы для автоматизированного учета товаров сферах производства, хранения, транспортировки и реализации.
Межгосударственная система стандартизации (МГСС)
Межгосударственная стандартизация (по ГОСТ 1.0-92) – это стандартизация объектов, представляющих межгосударственный интерес.
|
|
Представителями СНГ в 1992г. подписано «Соглашение о проведении согласованной политики в области стандартизации» и образован Межгосударственный совет по стандартизации, участниками которого являются 12 государств бывшего СССР. МСГ обладает правом принятия межгосударственных стандартов (ГОСТ). В 1995 г. Совет ИСО признал МГС стран СНГ региональной организацией по стандартизации.
Принимаемые Советом решения обязательны для государств, представители которых вошли в МГС. Основной рабочий орган МГС – постоянно действующий Технический секретариат с местом пребывания в Минске.
В результате деятельности МГС сохранены и используются существовавшие в СССР фонды нормативной документации и эталонная база: порядка 21 тыс. ГОСТ, 40 тыс. ОСТ, 35 ОКТЭИ, 140 эталонов единиц физических величин и т.д. За последние годы, было принято свыше 2500 нормативных документов, которые предназначены в основном для установления технических требований к продукции, подлежащей обязательной сертификации. Принятые стандарты гармонизированы с международными стандартами, что способствует продвижению продукции СНГ на мировой рынок.
Методы стандартизации
|
|
Методы стандартизации – это совокупность приемов с помощью которых достигаются цели стандартизации. Это методы :
1) упорядочения объектов – заключается в отборе и систематизации объектов стандартизации, т.е. в проведении научно-обоснованной, последовательной классификации и выделении конкретных свойств. Упорядочение объектов позволяет провести их оптимизацию, которая заключается в определении оптимальных параметров, обеспечивающих заданный уровень качества. Примером результатов работ по систематизации могут служить общероссийские классификаторы (ОКП), классификатор предприятий и организаций (ОКПО) и др.
Типизация объектов стандартизации это деятельность по созданию типовых технологических, организационных и экономических решений.
-2) параметрическая стандартизация – это деятельность на установление и выбор численных значений параметров объектов, подчиняющихся определенной математической закономерности. Примером является ряд предпочтительных чисел , установленных ГОСТ 8032. Ряды предпочтительных чисел позволяют взаимоувязать между собой изделие, полуфабрикаты, контрольно-измерительные приборы, транспортные средства.
3) унификация - это деятельность по рациональному сокращению числа типов деталей, их конструктивных элементов, а также агрегатов одинакового функционального назначения. Основные направления:
|
|
- разработка параметрических и типоразмерных рядов конструкции машин, узлов , деталей;
- разработка типовых изделий в целях создания унифицированных групп однородной продукции;
- разработка унифицированнх технологических процессов:
- сокращение до целесообразного минимума номенклатуры применяемых изделий и материалов.
4) агрегатирование – это метод конструирования машин и оборудования путем применения ограниченного числа унифицированнх и стандартных деталей и сборочных единиц, обладающих функциональной и геометрической взаимозаменяемостью. Агрегатирование позволяет создать новую машину из уже спроектированных и освоенных производством сборочных и агрегатов, а не создавать ее как оригинальную.
5) комплексная стандартизация – это стандартизация при которой осуществляется целенаправленное установление и приенение взаимоувязанных требований как к самому объекту стандартизации, так и к его основным элементам.
6) опережающая стандартизация – заключается в установлении к объектам стандартизации повышенных требований по отношению к уже достигнутым на практике. К опережающей стандартизации можно отнести принятие стандартов предприятий на основе прогрессивных международных стандартов до их принятия в качестве национальных.
Тема 4. Стандартизация в машиностроении
Основы взаимозаменяемости
Одним из факторов, обеспечивающим качество машин и других изделий промышленности является уровень взаимозаменяемости. Под взаимозаменяемостью понимается принцип конструирования, изготовления изделий обеспечивающий равноценную замену одного экземпляра продукции однотипным с обеспечением качества и работоспособности. Для сборочных единиц взаимозаменяемость обеспечивает бесподгоночную сборку.
Основная цель стандартизации в машиностроении – обеспечение взаимозаменяемости продукции, технической и информационной совместимости и качества изделий на таких этапах жизненного цикла как проектирование, производство и эксплуатация.
Взаимозаменяемость является одним из основных принципов, которые применяются в процессе разработки, конструирования и изготовления всех деталей машин и механизмов. Под ней подразумевается такое свойство изделий, которое позволяет безо всякой дополнительной обработки или подгонки заменять одни из них на другие таким образом, чтобы сборочная единица сохраняла свою работоспособность полном соответствии с теми техническими условиями, которые заданы изначально.
Потребность во взаимозаменяемости возникла уже довольно давно, однако особую актуальность она приобрела в связи с бурным развитием металлообработки, когда различные машины и механизмы стали выпускаться в массовом порядке, в том числе и с использованием различных средств автоматизации производства.
При строгом следовании принципу взаимозаменяемости существенно упрощается процесс конструирования машин и механизмов, облегчается их сборка и ремонт, становится возможной эффективная специализация и кооперирование. При этом отдельные предприятия, располагающиеся в разных городах даже странах, могут выпускать отдельные детали, узлы и агрегаты, и поставлять их друг другу.
При сборке используются стандартные крепежные детали, подшипники качения, электротехнические, резиновые и пластмассовые изделия, получаемые по кооперации от других предприятий. При полной взаимозаменяемости сборку выполняют без доработки деталей и сборочных единиц. Такое производство называется взаимозаменяемым.
Взаимозаменяемость изделий обеспечивается их изготовлением по определенным нормам точности, которые должны устанавливаться нормативными документами, т.е. стандартами в машиностроении.
Взаимозаменяемость в машиностроении возможно лишь на основе изготовления деталей и изделий с определенной нормируемой точностью геометрических параметров, физико-механических свойств и других показателей. Для обеспечения взаимозаменяемости в машиностроении служит Единая система допусков и посадок ГОСТ 25346 – 89
ЕСПД в нашей стране была принята и вступила в силу 1 января 1977 года.
Единая система допусков и посадок – это их закономерная совокупность, которая построена на основе экспериментальных и технических изысканий, практического опыта, приведенная к единому стандарту и оформленная в его качестве.
Основным ее предназначением является выбор минимально необходимых, но вполне достаточных для создания типовых соединений деталей различных машин и механизмов значений допусков и посадок.
Измерительные средства и режущий инструмент стандартизируется на основе наиболее оптимальной градации допусков и посадок, благодаря чему обеспечивается взаимозаменяемость различных деталей, а также существенно повышается их качество.
Та система стандартизации допусков и посадок, которая принята в нашей стране и используется в настоящее время, была разработана с учетом положений и рекомендаций ISO (Международной организации по стандартизации). Ее предписания направлены на то, чтобы те системы допусков и посадок, которые действуют в различных странах мира, в итоге были заменены единой системой.
Предельные отклонения и допуски для всех размеров устанавливаются при температуре окружающей среды +20 °С.
Несоблюдение стандарта преследуется по закону
Настоящий стандарт распространяется на гладкие элементы деталей, цилиндрические и ограниченные параллельными плоскостями, а также на образованные ими посадки и устанавливает термины, определения и условные обозначения, допуски и основные отклонения системы допусков и посадок для размеров до 3150 мм и любых линейных размеров, если
они не установлены другими стандартами.
1. ОСНОВНЫЕ ПОЛОЖЕНИЯ
1.1. Термины и определения
Номинальный размер – размер, проставленный на чертеже без отклонений. Величины размеров при проектировании определяются расчетом деталей на прочность, жесткость по конструктивным соображениям. Численные значения номинальных размеров принимаются из рядов нормальных линейных размеров, которые установлены стандартами. Номинальные размеры для наружных поверхностей (валов) обозначаются – d, для внутренних поверхностей (отверстий) – D.
Действительный размер это размер детали после ее изготовления. Численные значения действительных размеров можно определить лишь измерением. Поскольку при изготовлении и измерении возникают погрешности, то действительный размер отличается от номинального. Равенство действительного и номинального размера можно получить лишь при грубых измерениях. Деталь по действительному размеру Dд будет годной, если соблюдается условие:
Dmax ≥ Dд ≥ D min.
Для обеспечения работоспособности детали наряду с номинальным размером необходимо определить в обязательном порядке предельные размеры.
Предельные размеры – два предельно допускаемых размера, в диапазоне которых должен находиться действительный размер годной детали. При выходе действительно размера за диапазон предельных деталь не обеспечит требуемые зазоры, натяги в соединении, а также другие эксплуатационные требования и будет непригодной – бракованной.
Наибольший предельный размер — наибольший допустимый размер элемента и обозначается dmax для вала и Dmax для отверстия.
Наименьший предельный размер — наименьший допустимый размер элемента и обозначается dmin для вала и Dmin для отверстия.
dmax = d + es = 65+0,025 =65,025мм.
dmin = d + ei = 65+ (-0,025) = 64,975 мм.
Действительное отклонение — алгебраическая разность между действительным и соответствующим номинальным размерами.
Предельное отклонение — алгебраическая разность между предельным и соответствующим номинальным размерами. Различают верхнее и нижнее предельные отклонения.
Верхнее отклонение ES, es — алгебраическая разность между наибольшим предельным и соответствующим номинальным размерами
Верхнее предельное отклонение размера вала: es = dmax - d.
Нижнее предельное отклонение размера вала: ei = dmin – d.
Верхнее предельное отклонение размера отверстия: ES = Dmax – D.
Нижнее предельное отклонение размера отверстия: EI = D min – D.
На чертежах предельные размеры не проставляются, но для их установления вводятся предельные отклонения размеров:
По проставленным на чертеже предельным отклонениям находятся предельные размеры, определяющие диапазон допустимого рассеяния размеров годных деталей.
Необходимо отметить, что отклонения проставляются с определенными знаками, допуски же величины всегда положительные и знак не указывается.
На машиностроительных чертежах номинальные размеры и предельные отклонения проставляют в мм. без указания единиц, например
35 -0,01, 45 +0,05, 65 ±0,025.
Основное отклонение — одно из двух предельных отклонений (верхнее или нижнее), определяющее положение поля допуска относительно нулевой линии. В данной системе допусков и посадок основным является отклонение, ближайшее к нулевой линии.
3.1. Числовые значения основных отклонений валов приведены в табл-х
3.2. Второе отклонение поля допуска вала и отв. определяется из основного отклонения и допуска IT
ИНТЕРВАЛЫ НОМИНАЛЬНЫХ РАЗМЕРОВ Для размеров до 500 мм установлены промежуточные интервалы для валов с основными отклонениями от «а» до «с» и от «г» до «zс», для отверстий с основными отклонениями от «А» до «С» и от «R» до «ZC».
Для размеров свыше 500 до 3150 мм установлены промежуточные интервалы для валов с основными отклонениями «с», «cd» и от «г» до «v», для отверстий с основными отклонениями «С», «CD» и от «R» до «V».
Интервалы номинальных размеров, принятые в данной системе допусков и посадок, приведены в табл. 4.
Допуск Т — разность между наибольшим и наименьшим предельными размерами или алгебраическая разность между верхним и нижним отклонениями (черт. 2). Примечание. Допуск — это абсолютная величина без знака.
Стандартный допуск IT — любой из допусков, устанавливаемых данной системой допусков и посадок. Допуском размера называется разность наибольшего и наименьшего предельных размеров. Так для вала:
Td = dmax - dmin = (d + es) – (d + ei) = es – ei.
Для размера отверстия
TD = Dmax - D min = ES - EI.
Например: Td = 0,025 – (-0,025) = 0,05 мм.
Допуск размера определяет точность изготовления детали и влияет на показатели качества изделий. С уменьшением допуска деталей, работоспособность которых определяется износом (поршень, цилиндр двигателя внутреннего сгорания) такой важный эксплуатационный показатель, как ресурс работы увеличивается. С другой стороны, уменьшение допусков увеличивает затраты на изготовление.
Поле допуска — поле, ограниченное наибольшим и наименьшим предельными размерами и определяемое величиной допуска и его положением относительно номинального размера. При графическом изображении поле допуска заключено между двумя линиями, соответствующими верхнему и нижнему отклонениям относительно нулевой линии
Поле допуска обозначается сочетанием буквы (букв) основного отклонения и порядкового номера квалитета. Например: g6, js7, H7, Н11.
Обозначение поля допуска указывается после номинального размера элемента. Например: 40g6, 40Н7, 40Н11.
Численные значения допусков для размеров до 500 мм. установлены стандартом СТ СЭВ 145-88, для размеров свыше 500 до 10000мм стандартом СТ СЭВ 177-78.
Вал — термин, условно применяемый для обозначения наружных элементов деталей, включая и
нецилиндрические элементы.
Отверстие — термин, условно применяемый для обозначения внутренних элементов деталей, включая и
нецилиндрические элементы.
Основной вал — вал, верхнее отклонение которого равно нулю.
Основное отверстие — отверстие, нижнее отклонение которого равно нулю.
Предел максимума материала — термин, относящийся к тому из предельных размеров, которому соответствует наибольший объем материала, т.е. наибольшему предельному размеру вала или наименьшему предельному размеру отверстия.
Предел минимума материала — термин, относящийся к тому из предельных размеров, которому соответствует наименьший объем материала, т.е. наименьшему предельному размеру вала или наибольшему предельному размеру отверстия.
2. Формулы для расчета допусков
Формулы для расчета допусков приведены в табл. 5.
3. Округление числовых значений допусков
3.1. Числовые значения допусков для квалитетов до 11-го включительно, рассчитанные по формулам п. 2 настоящего
приложения, округлены в соответствия с табл. 6.
3.2. Значения допусков в квалитетах грубее 11-го, рассчитанные в соответствия с пояснением 4 к табл. 5, не требуют
округления, т. к. они получены из округленных значений допусков для квалитетов от 7-го до 11-го.
Вопрос 4.2.
Основные отклонения, образование полей допусков
Рис. 4.1 Изображение полей допусков деталей
Заштрихованная область носит название поле допуска размера. Эта область в виде прямоугольника расположена между предельными размерами dmax и dmin определяет диапазон рассеяния действительных размеров годных деталей. За нулевую линию принято номинальное значение d размера вала. Поле допуска определяется численным значением допуска Td и расположением относительно нулевой линии, т.е. двумя параметрами.
Для того, чтобы задать поле допуска размера, определяющего величины предельных размеров необходимо задать два численных параметра. Один численный параметр – допуск Td задается по определенному квалитету и обозначается цифрой – 01; 0; 1; 2…….18. Для задания второго параметра вводится понятие основного отклонения.
При расположении поля допуска в области положительных значение отклонений, основным отклонением является нижнее отклонение ei. Если поле допуска находится ниже нулевой линии – то основное отклонение es.
Рис 4.2. Основные отклонения полей допусков
В обоснованных случаях допускается обозначать поле допуска с основным отклонением “Н” символом “+IТ”, с основным отклонением “h” — символом “—IT”, с отклонениями “js” или “JS” — символом “±IТ/2”.
Например: +IТ14, —IТ14, ±IТ14/2.
Для определения численных значений полей допусков изделий стандартами системы ИСО (в России системой ЕСДП – единая система допусков и посадок) установлено 20 квалитетов.
Квалитеты обозначаются цифрами: 01,0,1,2,3,……….18, в порядке понижения точности и увеличения допусков. Обозначение IT8 означает, что допуск на размер установлен по 8-му квалитету точности.
Квалитет (степень точности) — совокупность допусков, рассматриваемых как соответствующие одному уровню точности для всех номинальных размеров.
Единица допуска i, I — множитель в формулах допусков, являющийся функцией номинального размера и служащий для определения числового значения допуска.
Примечание. i — единица допуска для номинальных размеров до 500 мм, I — единица допуска для номинальных размеров св. 500 мм.
Примерные области применения квалитетов точности в машиностроении таковы:
- IT01 поIT3 для высокоточных средств измерений, калибров, шаблонов, для деталей машиностроения такая точность, как правило, не назначается;
- IT 4 по IT5 для прецизионных деталей машиностроения.
- IT 6 по IT7 точные детали машиностроения, применяются весьма широко;
- IT 8 по IT9 средняя точность деталей машиностроения;
- IT 10 по IT12 пониженная точность деталей. Все вышеперечисленные квалитеты образуют посадки соединений;
Квалитеты грубее 12-го назначают для нормирования точности свободных, несопрягаемых поверхностей деталей, точности размеров заготовок.
Допуски по квалитетам составлены с учетом влияния технологических, конструктивных и метрологических факторов в зависимости от номинального размера. Допуски и отклонения установлены к размерам деталей при нормальной температуре, принятой во всех странах равной +20оС.
Вал — термин, условно применяемый для обозначения наружных элементов деталей, включая и нецилиндрические элементы.
Отверстие — термин, условно применяемый для обозначения внутренних элементов деталей, включая и нецилиндрические элементы.
Основной вал — вал, верхнее отклонение которого равно нулю.
Основное отверстие — отверстие, нижнее отклонение которого равно нулю.
Предел максимума материала — термин, относящийся к тому из предельных размеров, которому соответствует наибольший объем материала, т.е. наибольшему предельному размеру вала или наименьшему предельному размеру отверстия.
Предел минимума материала — термин, относящийся к тому из предельных размеров, которому соответствует наименьший объем материала, т.е. наименьшему предельному размеру вала или наибольшему предельному размеру отверстия.
В системе ИСО для основных отклонений используются одна или две буквы латинского алфавита. Для образования полей валов основные отклонения обозначаются 27 строчными (малыми) буквами; для образования полей допусков отверстий – 27 прописными (большими) буквами.
Схема расположения основных отклонений показана на рис 4.3.
Условное обозначение поля допуска состоит из обозначения основного
отклонения (буквы) и квалитета (цифры).
Примеры обозначения полей допусков валов: h6, r7, a11, отверстий - H7, R6, F9.
Численные значения основных отклонений валов и отверстий размеров до 500 мм. установлены стандартом СТ СЭВ 145-88. Как правило, величина основного отклонения поля допуска размера не зависит от сочетаемого с ним квалитета. Например, величина основного нижнего отклонения «A» для отверстия размером 10мм равна +0,270 мм одинакова для всех квалитетов. Величина верхнего отклонения находится по формуле:
ES=EI+IT,
где IT –допуск квалитета.
Если основное отклонение верхнее, например «Z» равное 0,042 мм, то нижнее отклонение EI = ES – IT. Аналогичные соотношения справедливы и для валов.
Для основных отклонений «K», «М», «N» отверстий и валов численное значение отклонения зависит от сочетаемого с ним квалитета и устанавливается по специальному правилу.
Сочетание 27 основных отклонений и 20 квалитетов позволяет образовать большое (около800) количество полей допусков, что не целесообразно по многим причинам. Поэтому исходя из практики проектирования изделий машиностроения стандартом СТ СЭВ 144-88 рекомендованы для применения примерно 80 полей допусков валов и отверстий. Из числа рекомендуемых отобраны предпочтительные (примерно 15) выделенные в таблицах жирным шрифтом.
Рис. 4.3. Основные отклонения для образования
полей допусков валов и отверстий
Вопрос 4.3. Посадки гладких соединений
В машиностроении существует понятие сборочная единица, которая определяется как изделие, собранное из отдельных деталей. Поверхности, по которым происходит соединение деталей, называют сопрягаемые. Остальные поверхности называют несопрягаемыми или свободными.
Посадка двух деталей определяется как частный случай соединения, в котором поверхность одной детали является наружной поверхностью, а поверхность другой – внутренней.
(На рис 3.8.3 показаны соединения двух деталей, первое из которых не образует посадку, а второе образует. Кроме этого в соединении, образующем посадку номинальный размер L должен быть одинаков. )
Форма сопрягаемых поверхностей П1 и П2 может быть различной. Например, плоской, как на рисунке, цилиндрической, резьбовой. Поэтому все наружные, охватываемые поверхности называют валом, а внутренние охватывающие – отверстием.
Таким образом, в соединении, образующем посадку, одна поверхность является валом, а другая отверстием.
Рис 4.4. Соединения двух деталей:
а - посадка не образуется, б - посадка образуется
В зависимости от взаимного расположения полей допусков вала и отверстия, которые, как указывалось, определяют предельные размеры, возможно образование трех групп посадок:
1-я с зазором:
2-я с натягом;
3-я переходная.
В посадках с зазором предельные размеры отверстия Dmax, D min больше предельных размеров вала dmax , dmin и поле допуска отверстия H7 расположено выше поля допуска вала f6, Причем номинальные размеры D= d.
Рис. 4.5. Расположение полей допусков в посадках с зазором
Посадки с зазором характеризуются: Smax – наибольшим зазором, Smin – наименьшим зазором.
Наибольший зазор возникнет в том случае, если отверстие имеет наибольший предельный размер, а вал – наименьший:
Smax = Dmax – d max =(ES + D) – (ei + d) = ES – ei.
Наименьший зазор возникнет тогда, если отверстие имеет наименьший предельный размер, а вал – наибольший. Аналогично вышеприведенному получим:
Smin = Dmin – d max = EI – es.
Значения предельных зазоров показаны на рисунке в виде отрезков.
Следует отметить, что к посадкам с зазором относят также посадки, в которых нижняя граница поля допуска отверстия совпадает с верхней границей поля допуска вала и Smin = 0 .
В посадках с натягом предельные размеры вала больше предельных размеров отверстия (до сборки деталей). После соединения деталей их сопрягаемые поверхности деформируются и образуется натяг. Посадки с натягом характеризуются: Nmax – наибольшим натягом, Nmin –наименьшим натягом.
Наибольший натяг образуется, если вал имеет наибольший предельный размер, а отверстие – наименьший:
Nmax = d max - Dmin = es – EI.
Наименьший натяг возникнет при сочетании наименьшего предельного размера вала и наибольшего предельного размера отверстия:
Nmin = dmin – D max = ei – ES.
Рис 4.6. Расположение полей допусков в посадках с натягом
В переходных посадках поля допусков вала и отверстия перекрываются и для одной пары соединяемых деталей возможно получения зазора, а для другой натяга. Поэтому характеристикой переходной посадки является наибольший зазор – Smax и наибольший натяг Nmax, которые определяются по формулам, приведенным выше.
Рис 4.7. Расположение полей допусков в переходных посадках
На сборочных чертежах посадки обозначаются с указанием номинального размера соединения, условного обозначения поля допуска отверстия (в «числителе») и условного обозначения поля допуска вала (в «знаменателе»): 45H7/k6.
В некоторых случаях количественной характеристикой посадок является допуск посадки:
TS = Smax – Smin – для посадок с зазором, TN = Nmax – Nmin для посадок с натягом и для переходных Тпер = Smax + Nmax. Для всех посадок их допуски равны сумме полей допусков и отверстия и вала TS(TN)= TD + Td.
Пример расчета посадок. Определить предельные размеры деталей, характеристики посадок, образованных в системе отверстия.
Поле допуска отверстия принять постоянным - 40H7. Предельные отклонения размера отверстия ES = +0,025мм. EI = 0,000мм. Предельные размеры отверстия D max = 40,000 + 0,0250= 40,025мм. Dmin = 40,000+0,000 = 40,000мм. Допуск размера отверстия
TD = ES - EI = +0,025мм - 0,000мм= 0.025мм.
Предназначение посадок, методы их выбора
Посадки с зазором предназначены: а) для подвижных соединений, в которых одна деталь при работе перемещается относительно другой; б) для неподвижных соединений при необходимости беспрепятственной их сборке.
Примером посадки с зазором является соединение поршня и цилиндра двигателя внутреннего сгорания. Зазор необходим для размещения слоя смазки между поверхностями, компенсации температурных деформаций и погрешностей, возникающих при обработке деталей.
В соединении крышки подшипника с корпусом редуктора зазор необходим для простоты сборки, затем детали закрепляются неподвижно при помощи резьбовых соединений.
Посадки с натягом предназначены для неподвижных неразъемных соединений. Натяг обеспечивает фиксацию деталей, прочность соединения, которое может передавать крутящие моменты, осевые усилия. Поскольку в посадках с натягом размеры вала до сборки больше размеров отверстия, то при монтаже деталей необходимо применять напрессовку или предварительно нагревать отверстие. Пример посадки с натягом – неподвижное соединение вала с зубчатым колесом коробки переключения передач автомобиля.
Переходные посадки предназначены для неподвижных, но разъемных соединений, в которых необходимо обеспечить центрирование деталей. Сборка соединений по переходным посадкам упрощена, не требует, как правило, применения прессового оборудования, такое соединение может быть разобрано при ремонте. Центрирование означает совмещение осей вала и отверстия, особенно необходимое на вращающихся деталях.
Посадки можно образовать сочетанием любых полей допусков вала и отверстия. Однако стандартами рекомендованы посадки в системе отверстия либо в системе вала. (На рис 3.8.7. показаны принципы образования посадок. )
В посадках в системе отверстия различные зазоры и натяги обеспечиваются изменением полей допусков валов в сочетании полем допуска основного отверстия, имеющего основное отклонение «Н».
В посадках в системе вала различные зазоры и натяги обеспечиваются изменением полей допусков отверстий в сочетании с полем допуска основного вала, имеющего основное отклонение « h ».
Посадки в системе отверстия и вала совершенно равнозначны по численным величинам зазоров или натягов. Однако, посадки в системе отверстия имеют практические преимущества и предпочтительны для применения.
Посадки, в которых нет основных отклонений вала и отверстия, например, 10 D9/f8 называются комбинированные и также могут применяться.
При конструировании соединений всегда возникает вопрос выбора определенной посадки, которая обеспечила бы надежную работу механизма. В настоящее время применяют два метода выбора 1-й метод аналогов, 2-й расчетный метод.
По методу аналогов в справочной литературе отыскивается соединение подобное проектируемому по конструкции и условиям работы и посадка назначается такая же как существующая. В справочной литературе приведены также примеры применения различных посадок. Недостатком метода является невозможность учета количественных характеристик условий работы соединения по действующим нагрузкам, перегрузкам, температурам.
Посадки Н/h – «скользящие». Установлены во всех квалитетах точности. В подвижных соединениях применяют при медленных перемещениях деталей при продольном и круговом движениях. Посадки высокой точности Н5/h4 применяют в неподвижных соединениях при их частой разборке и необходимости центрирования. Посадки низкой точности Н11/h11 для неподвижных соединений низкой точности.
Посадки Н/g –«движения» установлены в точных квалитетах, для подвижных соединений при возвратно-поступательных перемещениях с обеспечением герметичности.
Посадки H/f – «ходовые» обеспечивают размещение слоя смазки в подшипниках скольжения.
Посадки H/a, H/b обеспечивают большие гарантированные зазоры, часто назначаются для нецентрирующих поверхностей.
Посадки с натягом условно разделены на 3 подгруппы:
1 – «легкопрессовые» Н/р, которые обеспечивают минимальный гарантированный натяг;
2 – «прессовые средние» H/r, H/t обеспечивают передачу нагрузок средней величины без дополнительных конструктивных элементов. В соединяемых поверхностях деталей возникают упругие деформации.
3 – «прессовые тяжелые», предназначены для передачи значительных, в том числе, динамических нагрузок.
Переходные посадки H/js обеспечивают наиболее вероятный зазор в соединении, сборка таких соединений упрощена.
Посадки H/k наиболее распространены, обеспечивают хорошее центрирование и сборку с применением ручных молотков.
Посадки H/m обеспечивают преимущественно натяг, применяются на быстровращающихся валах с передачей нагрузок дополнительными конструктивными элементами.
Посадки H/n являются наиболее прочными из переходных посадок. Сборка требует применения значительных усилий, обеспечивают передачу крутящих моментов при наличии дополнительных конструктивных элементов при динамических нагрузках.
При расчетном методе количественные характеристики посадок (Nmax, Nmin) определяются исходя из условий передачи требуемого крутящего момента и усилия с последующей проверкой на прочность.
Вопрос 4.5. Нормирование отклонений формы и расположения.
При обработке поверхностей деталей наряду с отклонениями размера возникает отклонения формы и расположения поверхностей, которые оказывают влияние на работоспособность и качество работы изделий. Поэтому должны быть установлены нормы точности, ограничивающие эти отклонения.
Основные термины :
Номинальная поверхность – это идеальная воображаемая поверхность, предусмотренная чертежом детали.
Реальная поверхность – это поверхность детали ее после изготовления. Геометрию реальной поверхности можно узнать лишь путем измерений с помощью средств измерений. Реальная поверхность вследствие погрешностей при обработке и различных деформаций отличается от номинальной поверхности.
Отклонение формы – это отклонение формы реальной поверхности от формы номинальной поверхности. Отклонение формы, например, овалообразность цилиндрических поверхностей оказывает влияние на износостойкость цилиндрических соединений, работающих в условиях износа (поршень и цилиндр двигателя внутреннего сгорания) и в ряде других случаев, поэтому возникает необходимость ограничения этих отклонений, т.е. установление норм точности – допусков.
Количественное определение величин отклонений формы и расположения производится относительно прилегающих линий, поверхностей.
Прилегающая окружность – это окружность минимального диаметра, описанная вокруг реального профиля наружной поверхности вращения (рис. 4.8) или максимального диаметра, вписанная в реальный профиль внутренней поверхности вращения.
Отклонение формы профиля цилиндрической поверхности в плоскости поперечного сечения (виды отклонения от круглости) – это овалообразность (рис 4.8) и огранка. Овальность – отклонение от круглости при котором реальный профиль представляет собой овалообразную фигуру. При огранке реальный профиль выглядит в виде многогранной фигуры с четным или нечетным числом граней.
Отклонения формы в плоскости продольного сечения – конусообразность, бочкообразность и седлообразность показаны на рис. 4.9.
Конусообразность – отклонение профиля в плоскости продольного сечения, действительные размеры монотонно изменятся от одного торца детали к другому.
При седлообразности – диаметры увеличиваются от средины к торцам, а при бочкообразности наоборот.
Рис 4.8. Отклонение формы цилиндрических поверхностей
в поперечном сечении: б) овальность, в) огранка
Рис. 4.9. Отклонения формы цилиндрической поверхности
в плоскости продольного сечения: г) конусообразность;
д) бочкообразность; е) седлообразность
Отклонения формы во всех случаях кроме огранки можно измерить двухконтактным способом. Величина отклонения формы будет равна половине разности наибольшего и наименьшего действительных размеров (на рисунках они обозначены как d max и dmin) и получены измерением. Величину огранки Δ получить двухконтактным измерением не представляется возможным.
Частными случаями отклонения формы плоских поверхностей является выпуклость (рис.4.10) и вогнутость. Величина отклонения от плоскостности определится как наибольшее расстояние Δ между прилегающей плоскостью и какой-либо точкой реальной поверхности. Поле допуска плоскостности буде представлять собой параллелепипед, у которого высота между гранями равна численному значению допуска Т, а длина и ширина фигуры равна размерам детали L1 и L2. Условие годности детали по допуску плоскостности следующее: если все точки реальной поверхности детали будут находиться в области параллелепипеда, то деталь годная. При выходе реальной поверхности за область допуска – деталь бракованная.
Вид допуска формы и расположения по ГОСТ 2.308-79 следует обозначать на чертежах знаками (графическими символами), приведенными в таблице 3.8.2.
Рис 4.10. Отклонения формы плоских поверхностей:
в – выпуклость, г – вогнутость
Отклонением расположения поверхностей называют отклонения реального расположения от его номинального расположения. Номинальное расположение задается чертежом детали и является воображаемым.
При определение отклонения расположения опытным путем необходимо исключить из измерений отклонения формы рассматриваемых элементов. Под термином элемент понимается часть или вся поверхность, ось поверхности, плоскость симметрии, точка – как центр окружности.
Рассмотрим случаи отклонения расположения поверхностей (рис. 4.11)
Рис. 4.11. Отклонение от параллельности поверхностей
Величина отклонения от параллельности двух плоских поверхностей определится как разность наибольшего «а» и наименьшего «в» расстояний между прилегающими поверхностями в пределах нормируемого участка. При рассмотрении отклонений расположения один из прилегающих элементов принимается за базовый (базу). Поле допуска параллельности представляет собой часть пространства, ограниченного двумя плоскостями, параллельными базовой, расстояние между которыми «Т» численно равно допуску плоскостности. Условие годности детали по допуску параллельности таково: прилегающая плоскость к реальной поверхности должна находиться в области этого пространства. Аналогично рассматривается отклонение от перпендикулярности.
Отклонение от соосности назначается для поверхностей вращения П1 и П2. и представляет собой наибольшее расстояние Δ между реальными осями О1 и О 2.
Рис. 4.12. Отклонение и допуск соосности
Отклонение от симметричности относительно базовой плоскости симметрии (рис. 4.13) представляет собой наибольшее расстояние Δ между плоскостью симметрии рассматриваемого элемента – паза, и базовой плоскостью симметрии.
Рис 4.13. Отклонение от симметричности
При проектировании деталей, которые фиксируются с помощью крепежных изделий между собой для обеспечения собираемости необходимо, чтобы отверстия совпадали между собой. Например, крышка устанавливается в корпус и крепится болтами, которые ввинчиваются в корпус и должны свободно проходить в отверстиях крышки. Для обеспечения этого необходимо установить допустимое отклонение расположения осей отверстий в деталях. Это выполняется двумя способами:
1) предельными размерами, координирующими оси отверстий;
2) позиционными допусками.
На чертеже позиционный допуск (рис. 4.14) проставляется с номинальными размерами, которые проставляются в рамках и определяют номинальное расположение осей отверстий. Допустимое отклонение от номинального расположения реальной оси отверстий определяется полем позиционного допуска, представляющего окружность, диаметр которой равен численному значению позиционного допуска в диаметральном выражении.
Рис 4.14. Позиционный допуск расположения
поверхностей отверстий (в рамках - номинальные размеры)
Рис 4.14 (а) Позиционный допуск осей отв. Б в диаметральном
выражении 0,4 мм. База- ось пов. А.
Совместным проявлением отклонений формы и расположения поверхностей является торцевое и радиальное биение (рис. 4.15).
Радиальное биение поверхности вращения относительно базовой оси представляет собой совместное проявление отклонения от круглости и отклонения от соосности. Определяется как разность наибольшего и наименьшего расстояний Δ от базовой оси до точек реального профиля.
Рис 4.15. Радиальное (а) и торцевое (б) биение
Торцевое биение – суммарное проявление отклонения от плоскостности и отклонения от перпендикулярности торцевой поверхности относительно базовой оси.
Применение допусков радиального и торцевого биений упрощает контроль точности формы и расположения поверхностей.
Таблица 4.1
Условные обозначения допусков формы
и расположения поверхностей
Вопрос 4.6. Выбор численных значений допусков формы и расположения
Стандартизация числовых значений допусков формы и расположения поверхностей позволяет унифицировать технические требования к изделиям, повысить их взаимозаменяемость. Преимущества стандартизации заключается также в том, что допуски взаимоувязываются с номинальными размерами и допусками размеров по квалитетам.
Стандартами установлены 16 степеней точности допусков формы и расположения. Области применения примерно одинаковы с квалитетами точности размеров. Численные значения допусков формы выбираются по методу аналогов из справочной литературы. Например, 1-2 степени точности допусков плоскостности и прямолинейности применяется для измерительных и рабочих поверхностей особо точных средств измерений (концевые меры длины, направляющие прецизионных шлифовальных станков). Для всех случаев отклонений формы численное значение допуска формы должно ограничиваться допуском на размер:
Тф ≤ Тразм.
Допуски формы назначаются для тех случаев, когда отклонение формы оказывает влияние на работоспособность и качество изделия. Так, для поверхностей, сопрягаемых с кольцами подшипников качения, допуски круглости должны составлять менее 25% допуска на размер. В зависимости от соотношения между допусков размера и допусками формы и расположения устанавливаются уровни относительной геометрической точности: А – нормальная относительная геометрическая точность (допуск формы в среднем составляет 60% от допуска размера); В – повышенная относительная геометрическая точность (40%); С – высокая, для которой допуск формы составляет в среднем 25%. Стандартами рекомендовано назначение степеней точности в зависимости от уровней относительной геометрической точности и квалитета допуска размера. Если на чертеже численное значение допуска не указано, то, автоматически, численное значение допуска формы ограничивается допуском на размер.
Численное значение допусков расположения также можно выбрать по методу аналогов и примерам назначения допусков расположения в справочной литературе. Так, для вращающихся валов допуск соосности поверхностей, сопрягаемых с подшипниками качения рекомендуется принимать по эмпирической формуле Т= 48/ n, где n – частота вращения вала.
Для определения численных значений допусков расположения используется и расчетный метод, основанный на теории размерных цепей.
В отличие от отклонений формы, отклонения расположения не выявляются при контроле точности размеров и численные значения допусков расположения (кроме допусков параллельности) могут превышать допуски на размер.
Вопрос 4.7. Шероховатость поверхности и ее влияние на работоспособность
Шероховатостью называют совокупность микронеровностей поверхности образующихся при изготовлении деталей различными способами. Шероховатость является одним из параметров определяющих качество поверхностного слоя деталей. Влияние шероховатости поверхности на эксплуатационные показатели многообразно:
- шероховатость влияет на износостойкость деталей;
- микрогеометрия, являясь концентратором напряжений, для циклически нагруженных деталей определяет предел выносливости:
- коррозионная стойкость поверхностей во многом зависит от шероховатости;
- шероховатость влияет на прочность соединений по посадкам с натягом;
и др. Поэтому на деталировочных чертежах параметры шероховатости указываются в обязательном порядке.
Вопрос 4.8. Параметры, нормирующие шероховатость
Оценка параметров шероховатости производится от средней линии профиля – m (рис. 3.8.15) в пределах базовой длины –l. Стандартом установлено шесть параметров шероховатости поверхностей:
1) Ra = ∑│yi │/ n,где yi –высота профиля от средней линии профиля, n – число точек измерения.
2) Rz – высота неровностей профиля по десяти точкам. Определяется как сумма средних значений абсолютных высот пяти наибольших выступов и глубин пяти наибольших впадин.
3) Rmax – наибольшая высота неровностей профиля. Представляет собой расстояние между линиями выступов и впадин. Указанные выше параметры называют высотными, имеют размерность в мкм (микрометрах).
Рис 4.16. К определению параметров шероховатости
4) Sm – средний шаг неровностей профиля по средней линии в пределах базовой длины.
5) S – средний шаг неровностей профиля по вершинам, как среднее значение шага местных выступов профиля в пределах базовой длины. Размерность шаговых параметров – мм.
6) tp – относительная опорная длина профиля (%). Для определения параметра проводится на расстоянии Р от линии выступов опорная линия, подсчитывается сумма отрезков bi и находится отношение этой суммы к средней линии l.
Вопрос 4.9. Выбор параметров шероховатости и их численных значений
Выбор параметров шероховатости должен производиться в зависимости от эксплуатационного предназначения поверхности детали. Так, на процессы трения основное влияние оказывает Ra и tp, (Косилова) на сопротивление усталости – Rmax, на контактную жескость – tp.
Числовые значения параметров шероховатости установлены ГОСТ 2789-73. Наиболее полно примеры нормирования шероховатости поверхностей для типовых деталей приведены в (Мягков).
Так для посадочных поверхностей подшипников скольжения значение параметра Ra =-0.4-0.8 мкм, для поверхностей валов и осей под уплотнения, в зависимости от окружной скорости, в диапазоне 0.2 – 1.6 мкм при обработке полировкой.
Поскольку шероховатость влияет на характер посадки то выбор шероховатости многие авторы рекомендуют производить из соотношения Ra ≤0.05 Тразм…
Вопрос 4.10. Обозначение шероховатости на чертежах
Обозначение шероховатости на чертежах проводилось с соответствии со стандартом ГОСТ 2789-73. В настоящее время внесены изменения в указанный стандарт, которые полностью соответствуют стандарту ИСО 1302.
Шероховатость поверхности обозначают на чертеже для всех выполняемых по данному чертежу поверхностей изделия, независимо от методов их образования, кроме поверхностей, шероховатость которых не обусловлена требованиями конструкции.
Структура обозначения шероховатости поверхности приведена на рис 4.17.
При применении знака без указания параметра и способа обработки его изображают без полки.
![]() |
![]() | ![]() | ![]() |
Поверхности детали, изготовляемой из материала определенного профиля и размера, не подлежащие по данному чертежу дополнительной обработке, должны быть отмечены знаком (рис.4.20) без указания параметра шероховатости.
![]() | ![]() |
Тема 5. Стандартизация типовых соединений деталей машиностроения
Вопрос 5.1 Стандартизация резьбовых соединений
Цилиндрические метрические резьбы с диаметром от 1 до 600 мм широко применяются во всех отраслях машиностроения и приборостроения.
Рис 5.1. Геометрические параметры метрической резьбы
Основные геометрические параметры резьбы показаны на рис 5.1:
D (d) – номинальный наружный диаметр (Большие буквы для резьбы гайки, строчные для резьбы болта);
D2 (d2) – номинальный средний диаметр;
D1 (d1) – номинальный внутренний диаметр;
Р – шаг резьбы;
ά – угол профиля резьбы, для метрической равен 60о.
Геометрические параметры стандартизованы. Метрические резьбы установлены с мелким и крупным шагом. У резьбы с крупным шагом каждому наружному диаметру соответствует одно определенное значение шага. Для резьб с мелким шагом одному и тому же наружному диаметру могут соответствовать разные шаги.
Взаимозаменяемости резьб сводится к обеспечению свинчивания по всей длине и прочности соединения. При изготовлении резьбовых деталей неизбежны различные отклонения поверхностей профиля и, для обеспечения взаимозаменяемости, необходимо установить допуски на все основные параметры резьбы. Допуски на все параметры устанавливаются для точных резьб, например, резьбовых калибров.
Для большинства резьб допуски устанавливаются не на все параметры. Это возможно потому, что: во первых по наружной и внутренней поверхностям предусмотрены зазоры и контакт при свинчивании происходит лишь по боковой поверхности, геометрия которой определяется шагом Р, углом профиля ά и средним диаметром D2 (d2); во вторых – погрешности шага и угла профиля, исходя из их взаимосвязи, можно компенсировать назначением расширенных допусков на средний диаметр D2 (d2). Поэтому для цилиндрических резьб допуски назначаются на средние диаметры гайки и болта TD2 (Td2), на наружный диаметр резьбы болта (Td) и внутренний диаметр резьбы гайки (TD1).
Образование полей допусков резьбовой поверхности на указанные параметры аналогично образованию полей допусков для гладких соединений. Установлены стандартом 8 степеней точности: 2,3,4,5,…..9, и основные отклонения в зависимости от вида посадки. На рис 3.9.1. показаны расположения полей допусков метрической резьбы в посадках с зазором
Поля допусков на диаметры отсчитываются от номинального профиля в радиальном направлении.
Посадки с натягом и переходные по среднему диаметру резьбы применяют для соединений, работающих в условиях сотрясений, вибраций, температурных деформаций. В таких условиях требуется обеспечить неподвижность соединения. Например, на соединение шпильки с резьбовым отверстием корпуса назначается переходная посадка, но с дополнительным элементом заклинивания по коническому сбегу резьбы.
Рис 5.2. Расположение полей допусков метрической резьбы
в посадках с зазором:
а – для наружной резьбы болта;
б – для внутренней резьбы гайки.
Посадки резьбовых деталей на чертежах обозначаются дробью, в числителе которой указывается поле допуска гайки, а в знаменателе – поле допуска болта.
Например, М22x1.5 –5Н6Н/ 5g6g. Буква М означает метрическую резьбу; цифра 22 – номинальный наружный диаметр гайки и болта; 1.5 – шаг; 5Н6Н – поле допуска среднего и внутреннего диаметров гайки, соответственно; 5g6g – поле допуска среднего и наружного диаметров болта, соответственно.
Дата добавления: 2018-06-01; просмотров: 1466; Мы поможем в написании вашей работы! |
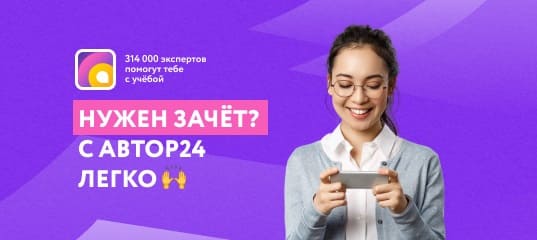
Мы поможем в написании ваших работ!