Электролитическое рафинирование анодной меди.
Анодная медь содержит 99,4-99,6 % Cu и оставшиеся после огневого рафинирования примеси, включая золото, серебро, селен и теллур. В среднем в 1 т анодной меди содержится 30-100 г золота и до 1000 г серебра.
В процессе электролитического рафинирования решаются две задачи: глубокая очистка меди от примесей и попутное извлечение сопутствующих меди ценных компонентов. Высшая марка электролитной меди МО должна содержать не более 0,04 % примесей, в том числе не более 0,02 % кислорода, а остальные 0,02 % приходятся на долю девяти регламентируемых примесей.
Литые аноды и тонкие матрицы из электролитной меди - катоды попеременно завешивают в электролитную ванну, заполненную электролитом, и через эту систему пропускают постоянный ток.
Электролит - водный раствор сульфата меди (160- 200 г/л) и серной кислоты (135-200 г/л) с примесями и коллоидными добавками, расход которых составляет 50- 60 г/т Cu. Чаще всего в качестве коллоидных добавок используют столярный клей и тиомочевину. Они вводятся для улучшения качества (структуры) катодных осадков.
Механизм электролитического рафинирования меди, включает следующие стадии:
· электрохимическое растворение меди на аноде с образованием катиона:
Cu - 2e = Cu2+
· перенос катиона через слои электролита к поверхности катода;
· электрохимическое восстановление катиона меди на катоде:
Cu2+ + 2e = Cu;
· внедрение атома меди в кристаллическую решетку (рост катодного осадка).
|
|
Для осаждения одного грамм-эквивалента металла (для меди 63,56:2 = 31,78 г) расходуется 96500 Кл электричества или 96500 : 3600=26,8 А-ч. При пропускании через раствор тока силой 1 А в течение 1 ч выделится
1,78/26,8=1,186 г меди.
Эта величина называется электрохимическим эквивалентом меди. Следовательно, для того чтобы осадить на катоде больше меди, нужно пропустить через электролитную ванну больше электричества. Для количественной оценки интенсивности процесса электролиза на практике пользуются величиной плотности тока, которая выражается отношением силы тока к единице поверхности электрода
D=I/F , А/м2
При электролитическом рафинировании меди чаще всего работают при плотности тока 240-300 А/м2. Использование особых режимов электролиза (реверсивный ток, циркуляция электролита и др.) позволяет довести плотность тока до 400-500 А/м2 и более.
На практике выход основного металла на катоде всегда ниже теоретического. Отношение массы фактически выделившегося металла к его теоретическому количеству, которое должно было бы выделиться по закону Фарадея, называют выходом по току.
Этот показатель выражают обычно в %. Физический смысл этого показателя можно определить как степень использования протекающего через электролизер тока на совершение основной электрохимической реакции. Так, при выходе по току, равном 95%, до 5% затраченной электроэнергии расходуется на побочные электрохимические процессы. С повышением выхода по току увеличивается производительность процесса электролиза и снижается удельный расход электроэнергии. Расход электроэнергии зависит также от падения напряжения на ванне, которое при рафинировании меди возникает главным образом в результате преодоления сопротивления электролита (60-65 % от общего) и токоподводящих шин, контактов (~20 %). Напряжение на ванне можно рассчитать по формуле:
|
|
U=IR1 + IR2 + IR3
где I сила тока, подводимого к к ванне; R1, R2, R3 - электрическое сопротивление соответственно электролита, шин, контактов.
Из формулы видно, что напряжение на ванне будет возрастать с увеличением силы тока, т. е. плотности тока. При плотностях тока 250-300 А/м2, выходе по току около 95 % и напряжении на ваннах 0,25-0,3 В. Практический удельный расход электроэнергии на современных заводах составляет 230-350 кВт.ч на 1 т меди.
Электролитическое рафинирование меди направлено на глубокую очистку ее от примесей. Имеющиеся в анодной меди примеси в процессе электролиза ведут себя по-разному. Их поведение определяется положением в ряду напряжений. Медь, имеющая нормальный потенциал, равный +0,34 В, по отношению к водороду электроположительна. Правее ее в ряду напряжений находятся лишь благородные металлы. Разряд ионов водорода на катоде, приводящий к снижению выхода по току при электролизе меди, возможен при недостаточной концентрации ионов меди. Все присутствующие в анодной меди примеси по их электрохимическому поведению можно разбить на четыре группы.
|
|
К первой группе относятся более электроотрицательные по сравнению с медью примеси, которые практически полностью растворяются на аноде и могут попасть в катодную медь в виде межкристаллических включений (захватов) раствора особенно при чрезмерном повышении их концентрации в электролите (вблизи катода). К ним относятся железо, никель, кобальт, цинк, олово, свинец. Для предотвращения загрязнения катодов примесями часть электролита нужно выводить на очистку (регенерацию). Исключение из числа примесей этой группы составляют олово и свинец, которые выпадают в шлам вследствие образования нерастворимых в сернокислом электролите соединений.
|
|
Вторую группу примесей образуют мышьяк, сурьма и висмут. Их электродные потенциалы близки к потенциалу выделения меди, и поэтому их переход в катодные осадки наиболее вероятен. Для предотвращения попадания этих наиболее опасных примесей в катодные осадки необходимо не допускать повышения их концентрации выше предельно допустимых. На практике этого достигают выводом мышьяка, сурьмы и висмута из раствора при регенерации электролита.
К третьей группе относятся благородные металлы, которые в условиях электролиза меди как более электроположительные анодно не растворяются. По мере растворения анода они теряют с ним механическую связь и на 98- 99 % осыпаются в шлам.
Примеси четвертой группы, представленные растворенными в анодной меди химическими соединениями типа Cu2S, Cu2Se, Cu2Te вследствие электрохимической нейтральности и малой растворимости в электролите также практически полностью переходят в шлам подобно благородным металлам.
Для электролиза применяют железобетонные ванны ящичного типа, в плане - прямоугольного сечения. Для повышения коррозионной стойкости ванн против воздействия сернокислого электролита внутреннюю часть облицовывают винипластом, стеклопластиком, полипропиленом, кислотоупорным бетоном и др. материалами.
Электролитные ванны группируют в блоки по 10-20 ванн, а затем в серии, состоящие, как правило, из двух блоков. Все электроды в отдельных ваннах, катоды и аноды, включены параллельно, а ток через блоки и серии проходит последовательно. Размеры ванн зависят от размеров и числа электродов. Современные ванны имеют длину 3,5- 5,5 м, ширину 1-1,1 м и глубину 1,2-1,3 м. Аноды и катоды подвешивают поочередно. При этом число катодов в ванне всегда на один больше, чем анодов, и они имеют увеличенные на 20-30 мм ширину и высоту по сравнению с анодными пластинами. При установке в ванну анодов их укладывают одним из ушек на токоподводящую шину или же соединяют с катодной штангой катодов соседней ванны. Подвод тока от источника питания осуществляют только к крайним шинам блока или к серии ванн.
Первичными катодами служат тонкие (0,4-0,6 мм) листы из электролитной меди - катодные основы. Их заготавливают электролизом на матрицах из холоднокатанной меди или титана. К содранным с матрицы листам после обрезки кромок приклепывают ушки, обеспечивающие в дальнейшем контакт катода с токоподводящей штангой.
Рис.4.5 Поперечный разрез ванны для электролитического рафинирования медных анодов:
1-анод; 2-катод; 3- токоподводящая штанга. [3,стр.140]
Время наращивания катода в товарных ваннах на заводах колеблется от 6 до 15 сут. Ко времени выгрузки масса катода достигает 60-140 кг. После тщательной промывки готовые катоды направляют потребителю или переплавляют в слитки. Растворение анода длится 20-30 сут. и зависит от его толщины и режима электролиза. Анодные остатки, составляющие 12-18 (2-3) % первоначальной массы, переплавляют в анодных печах в новые аноды. За время работы анодов производят 2-3 съема катодов.
Очистка электролита от примесей. В процессе электролиза электролит загрязняется примесями и обогащается медью. Накопление меди происходит главным образом за счет того, что анодный выход по току меди больше катодного выхода вследствие образования на аноде незначительного количества ионов Cu+. Обогащению электролита медью способствует также химическое растворение катодной и анодной меди и содержащейся в анодах закиси Cu2O.
Для предупреждения накопления примесей и удаления избытка меди электролит подвергают обновлению (регенерации) Для регенерации часть электролита выводят из ванн. Количество выводимого электролита рассчитывают по предельно допустимой концентрации ведущей примеси, накопление которой идет наиболее быстро. Обычно такой примесью является никель, реже мышьяк.
Вывод электролита на регенерацию осуществляется во время организации его обязательной непрерывной циркуляции в электролитных ваннах. Помимо частичного обновления электролита, циркуляция должна обеспечивать выравнивание его состава в межэлектродном пространстве. Это обеспечивает получение качественных катодных осадков и снижение расхода электроэнергии Циркуляция должна обеспечивать смену всего электролита за 3-4 ч. Циркуляцию электролита можно проводить путем подачи электролита с одного торца ванны и вывода с противоположного торца (перпендикулярно электродам) или прямоточно через все ванны блока параллельно электродам. В последнем случае становится возможным значительно повысить плотность тока без нарушения качества катодной меди. Во время циркуляции электролит по пути из напорного бака к ваннам подогревают паром до 50-55°С, что способствует снижению его электрического сопротивления. Регенерацию электролита с целью его обезмеживания можно проводить несколькими способами. В настоящее время распространено выделение меди электролизом с нерастворимыми (свинцовыми) анодами.
При электролитическом способе медь осаждается из раствора на катоде, а на свинцовых анодах выделяется кислород:
Cu2+ + 2е = Cu
2 ОН- - 2е = Н2О + ЅO2
В результате этих двух реакций раствор обедняется медью и обогащается свободной серной кислотой. После частичного обеднения медью такой электролит можно возвратить в основной электролиз. Осаждение меди электролизом с нерастворимыми анодами характеризуется повышенным расходом электроэнергии на 1 т меди (до 3000 - 3500 кВт.ч) вследствие высокого напряжения на ванне, которое составляет около 2-2,5 В и слагается из потенциалов образования меди и кислорода из ионов. Этот способ прост, но дорог. На многих заводах регенерацию электролита совмещают c получением медного купороса. По этому способу отобранный раствор нейтрализуют в присутствии воздуха анодным скрапом или специально приготовленными гранулами меди. В результате протекания реакции раствор обогащается медью и обедняется серной кислотой.
Cu + H2SO4 + 1/2 O2 = CuSO4 + Н2О
Полученный раствор упаривают и направляют в кристаллизаторы, где при охлаждении из выделяются кристаллы медного купороса (CuSO4 .5H2O). Для интенсификации процесс получения медного купороса проводят, в вакуумных кристаллизаторах. Кристаллизацию купороса проводят в три стадии. Раствор после третьей стадии, содержащий около 50-60 г/л Cu, подвергают электролитическому обезмеживанию в ваннах с нерастворимыми анодами. В результате электролиза получают рыхлый катодный осадок меди, загрязненный мышьяком и сурьмой, который отправляют на медеплавильные заводы, и раствор, содержащий около 1 г/л меди.
Катодную медь отправляют в переплав, а раствор - на получение никелевого купороса выпариванием с последующей кристаллизацией. Остаточный раствор после выделения никеля, содержащий серную кислоту, возвращают в электролизный цех для приготовления свежего электролита.
Получающиеся при электролитическом рафинировании шламы перерабатывают для извлечения благородных металлов, селена и теллура. Стоимость компонентов шлама окупает в большинстве случаев все затраты на рафинирование меди.
Катодная медь - основной продукт электролиза - не всегда пригодна для непосредственного использования, особенно в электротехнической промышленности. Поэтому ее расплавляют и разливают в слитки. Раньше переплавку проводили повсеместно в отражательных печах по методу, близкому к огневому рафинированию черновой меди, с получением слитков стандартной формы - вайербарсов.
Дата добавления: 2018-06-01; просмотров: 1438; Мы поможем в написании вашей работы! |
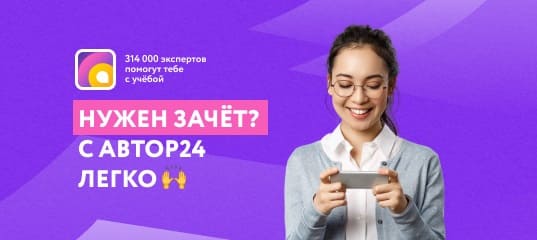
Мы поможем в написании ваших работ!