Огневое рафинирование черновой меди.
Лекция 4. Процессы конвертирования штейнов и рафинирования меди
Конвертирование медных штейнов.
Медные штейны, содержащие в зависимости от состава исходного рудного сырья и вида применяемого процесса плавки от 10-12 до 70-75 % Сu, повсеместно перерабатывают методом конвертирования. На конвертирование, кроме штейна, в расплавленном или твердом состоянии поступают богатые медью обороты, кварцевый флюс (часто золотосодержащий) и другие материалы.
Как уже отмечалось выше, медные штейны состоят в основном из сульфидов меди (Cu2S) и железа (FeS). Основная цель процесса конвертирования - получение черновой меди за счет окисления железа и серы и некоторых сопутствующих компонентов. Благородные металлы практически полностью, а также часть селена и теллура остаются в черновом металле. Вследствие экзотермичности большинства реакций конвертирование не требует затрат постороннего топлива, т.е., является типичным автогенным процессом.
Организационно процесс конвертирования медных штейнов делится на два периода. Первый период - набор сульфидной массы. В основе его лежит процесс окисления сульфидов железа и перевод образующихся при этом его оксидов в шлак. Преимущественное окисление сульфидов железа в первом периоде обусловлено повышенным сродством железа к кислороду по сравнению с медью.
Химизм первого периода конвертирования характеризуется протеканием реакций окисления и ошлакования сульфида железа:
|
|
2 FeS + O2 + SiO2 = 2 FeO.SiO2 +2 SO2 +979 кДж
Медные штейны практически всегда содержат примеси других металлов, в частности Zn, Pb, As, Sb, Bi, Se, Te, Au, Ag и др. Из сравнения величин изменения энергии Гиббса реакций окисления установлена следующая последовательность окисления сульфидов: FeS, ZnS, PbS, Cu2S. С уменьшением концентрации сульфида в перерабатываемой штейновой массе и соответствующем изменении энергии Гиббса наступают условия, при которых возможно совместное окисление сульфидов.
Важное практическое значение имеют закономерности совместного окисления сульфидов и с этой точки зрения последовательность окисления сульфидов может быть выявлена из сравнения величин изменения энергии Гиббса реакций:
FeS + 1,5 O2 = FeO + SO2
3FeS + 5 O2 = FeO + 3 SO2
CuS + 1,5 O2 = Cu2O + SO2
ZnS + 1,5 O2 = ZnO + SO2
PbS + 1,5 O2 = PbO + SO2
|
|
По данным Ю.П. Купрякова результаты расчетов изменения энергии Гиббса низших сульфидов приведены в таблице 4.1.
Таблица 4.1 Изменения реакций окисления сульфидов, Дж/моль SO2
Номер реакции | | |||||
1073 | 1173 | 1273 | 1373 | 1473 | 1573 | |
85 | -372894 | -369502 | -361882 | -354304 | -346725 | -339147 |
86 | -449809 | -436327 | -422845 | -409363 | -395881 | -382399 |
87 | -276342 | -265455 | -254611 | -243725 | -232839 | -221995 |
88 | -394122 | -382189 | -370214 | -358240 | -346307 | -334332 |
89 | -339230 | -330814 | -322399 | -314025 | -305609 | -297193 |
Из данных таблицы можно сделать вывод, что при одинаковых температурных условиях и концентрации кислорода в газовой фазе в первую очередь будет окисляться сульфид железа, затем цинка, свинца и меди.
Реакции дают почти все тепло для процесса и обеспечивают его автогенность. Обычно конвертирование ведут при 1200 - 1280°С. Повышение температуры ускоряет износ футеровки конвертера. При повышении температуры в конвертер загружают холодные присадки - твердый штейн, оборотные материалы, вторичное сырье, цементную медь и гранулированные концентраты. Продуктами первого периода являются обогащенная медью сульфидная масса (белый штейн), конвертерный шлак и серусодержащие газы.
|
|
Холодный ход конвертера и недостаток кварцевого флюса приводят к переокислению железа в шлаке и образованию больших количеств магнетита. Разогрев конвертера достигается заливкой свежей порции штейна или добавкой кварца.
Рис.4.1 Горизонтальный конвертер 3,66 х 6,1 м:[3,стр.137]
Рис.4.2 Общий вид конвертера с боковым отводом газов:
1-уплотнение подвижного стояка с газовой коробкой; 2-газовая коробка; 3-П-образный газоход; 4-горловина; 5-кожух. [3,стр.140]
В первом периоде происходит также окисление сульфидов меди, но вследствие повышенного сродства к сере она вновь сульфидируется сернистым железом. Содержание меди в конвертерных шлаках обычно составляет 1,5 - 2%. Вследствие высокого содержания меди конвертерные шлаки с целью обеднения либо возвращаются в оборот (в плавку на штейн), либо подвергаются самостоятельной переработке.
Первый период процесса конвертирования носит циклический характер; Каждый цикл состоит из операций заливки жидкого штейна, загрузки кварцевого флюса и холодных присадок, продувки расплава воздухом, слива конвертерного шлака. Длительность каждого цикла в зависимости от состава исходного штейна составляет 30 - 50 мин. После каждой продувки в конвертере остается обогащенная медью сульфидная масса. Содержание меди в массе постепенно возрастает до предельной величины, отвечающей почти чистой полусернистой меди (Cu2S). Продолжительность первого периода определяется, кроме содержания меди в штейне, и количеством подаваемого воздуха, которое зависит в основном от размеров (числа фурм) и состояния конвертера и организации работы.
|
|
При богатом штейне (35 - 45% Сu) первый период продолжается 6 - 9 ч, при бедном (20-25% и менее Сu) до 16-24 часов. На 1кг FeS в штейне, требуется около 2м3
воздуха. Коэффициент использования конвертера под дутьем в первом периоде составляет 70 - 80 %. Остальное время тратится на слив шлака и на загрузку конвертера. По окончании первого периода и слива последней порции шлака в конвертере остается почти чистая полусернистая медь - белый штейн (78 - 80% Сu).
Второй период - получение черновой меди за счет окисления ее сульфида проводится непрерывно в течение 2 - 3 ч без загрузки каких-либо твердых и оборотных материалов и при подаче только воздуха по суммарной реакции:
Cu2S + O2= 2 Cu + SO2 + 215000 кДж
Готовую черновую медь в зависимости от места проведения рафинирования либо заливают в жидком виде в миксер и далее по мере надобности в рафинировочную печь, либо разливают в слитки массой до 2 т и отправляют на рафинировочные заводы.
Черновая медь согласно ОСТ 47-33-72 выпускалась шести марок с суммарным содержанием меди, золота и серебра не менее 99,4% (МЧ1) и 96 % (МЧ6). Наиболее строгие требования при этом предъявляются к содержанию в черновой меди висмута, мышьяка и сурьмы. Прямое использование черновой меди потребителями не допускается вследствие присутствия примесей, ухудшающих электрические, механические и другие важнейшие свойства меди, и ценных элементов-спутников. Вся черновая медь подлежит обязательному рафинированию.
Рафинирование черновой меди по экономическим соображениям проводят в две стадии. Сначала очистку меди от ряда примесей проводят методом огневого (окислительного) рафинирования, а затем - электролитическим способом. Возможна одна операция электролитического рафинирования. Однако без предварительной, частичной очистки меди электролиз становится чрезмерно дорогим и громоздким.
Огневое рафинирование черновой меди.
Цель огневого рафинирования сводится к частичной очистке меди от примесей, обладающих повышенным сродством к кислороду, и подготовке ее к последующему электролитическому рафинированию. При огневом рафинировании из меди стремятся максимально удалить кислород, серу, железо, никель, цинк, свинец, мышьяк сурьму и растворенные газы. Медь после огневого рафинирования разливают в слитки пластинчатой формы с ушками - аноды, которые направляют в электролизный цех. Для огневого рафинирования меди используют два типа печей: стационарные отражательные и наклоняющиеся.
Рис.4.3 Отражательная печь для рафинирования меди:
1-столбчатый фундамент; 2-подина; 3- газоход; 4-распорно-подвесной свод; 5-горелка; 6-рабочее окно с заслонкой; 7-шлаковое окно; 8-щелевая летка. [3,стр.140]
Стационарная рафинировочная печь по устройству похожа на отражательную печь для плавки концентратов, но имеет ряд конструктивных особенностей. Вместимость современных анодных печей - до 400 т жидкой меди.
Анодные печи покоятся на столбчатом фундаменте, что обеспечивает повышенную стойкость подины. На одной из продольных стен печи имеются рабочие окна с опускающимися заслонками, предназначенные для загрузки в печь твердых материалов и обслуживания печи во время работы. Рафинировочные печи отапливаются только высококачественным топливом (природный газ или мазут). Топочная сторона печи имеет форкамеру, в которой начинается горение топлива. Окна для съема шлака расположены в одной из боковых или в задней торцовой стенке печи.
Рабочие и шлаковые окна можно использовать для окислительной и восстановительной обработки расплавленной меди. На противоположной длинной стороне печи имеется щелевая летка, которую перед началом загрузки закладывают огнеупорным кирпичом или заделывают глиной. Во время разливки меди в конце операции щель постепенно разбирают сверху, что обеспечивает почти постоянный напор струи жидкой меди. Стационарные отражательные печи применяют для огневого рафинирования как жидкой, так и твердой черновой меди, а также, для переплавки и дополнительного рафинирования катодной меди при изготовлении из нее вайербарсов - слитков особой формы, используемых в дальнейшем для проката и волочения проволоки.
Рис.4.4 Наклоняющаяся печь для рафинирования меди:
1-кожух; 2-футеровка; 3- горловина; 4-крепление; 5-загрузочное окно; 6-привод; 7-летка; 8-окно горелки. [3,стр.140]
Наклоняющиеся рафинировочные печи конструктивно сходны с горизонтальными конвертерами, но имеют большую емкость (до 300 т). У таких печей горловина смещена обычно к одному торцу. Ее используют для заливки жидкой черновой меди, загрузки твердых оборотов и отвода отходящих газов. Для выпуска рафинированной меди со стороны разливочной машины в печи сделана летка диаметром - 60 мм. Напор струи жидкой меди регулируется в этом случае углом поворота печи в сторону розлива. Наклоняющиеся рафинировочные печи имеют ряд преимуществ перед стационарными, но пригодны только для переработки жидкой черновой меди. Загрузка через горловину слитков черновой меди приводит к быстрому разрушению футеровки пода.
Огневое рафинирование меди- периодический процесс и состоит из стадий, включающих подготовку и загрузку печи, плавление или разогрев меди, окислительную обработку расплава и съем шлака, восстановительную обработку (дразнение) и разливку готовой меди. Подготовка печи сводится к ее осмотру, заделке изъянов в футеровке и заправке выпускной летки. Далее производят загрузку печи. При рафинировании твердой меди массивные слитки загружают в стационарную печь через рабочие окна с помощью загрузочной машины - шарнирного крана с хоботом. Жидкую медь заливают ковшами по желобу или через горловину; продолжительность загрузки - до 2 ч.
Расплавление меди занимает до 10 ч. При переработке жидкой меди и небольшого количества твердых, главным образом оборотных материалов, длительность этой стадии сокращается. Период расплавления и разогрева расплава сопровождается частичным окислением твердой меди и расплава кислородом, присутствующим в атмосфере печи. После разогрева ванны до 1200°С начинается стадия окислительной продувки меди для окисления примесей с повышенным по сравнению с медью сродством к кислороду. Медь окисляют воздухом, который вдувают в ванну на глубину 600 - 800 мм с помощью погружаемых в расплав стальных трубок, покрытых снаружи огнеупорной обмазкой.
Теоретически при взаимодействии с кислородом дутья должны были бы сразу окисляться примеси, обладающие большим по сравнению с медью сродством к кислороду. Однако на практике с учетом закона действующих масс в первую очередь окисляется медь, концентрация которой по сравнению с примесями является преобладающей. При продувке воздухом медь окисляется до Сu2О, которая, растворяясь в ванне меди до концентрации 10-12%, переносит кислород к более активным металлам и окисляет их по обратимой реакции
Сu2О + Ме = 2 Сu + МеО
Оксиды металлов- примесей вместе с избытком Сu2О и кремнеземом, загружаемым в небольшом количестве в печь для ошлакования примесей, образуют на поверхности ванны шлак. В конце окислительной продувки шлак обычно сгребают деревянными гребками. Шлаки рафинировочных печей содержат до 50 % Сu. Выход шлаков составляет 1- 2 % от массы меди. Рафинировочные шлаки возвращают в процесс конвертирования.
Наиболее полно окисляются и удаляются в шлак примеси с наибольшим сродством к кислороду: алюминий, цинк, железо, олово. Однако если примесь обладает высокой растворимостью в меди, то степень ее удаления будет небольшой. Так, концентрацию никеля, обладающего неограниченной растворимостью в меди, не удается снизить ниже 0,25 - 0,3%. К числу трудноудаляемых примесей относятся мышьяк и сурьма, особенно при их совместном присутствии с никелем. Практически полностью при огневом рафинировании в меди остаются благородные металлы, селен и теллур. Продолжительность окислительной продувки зависит от степени загрязнения исходной черновой меди и составляет 1,5 - 4 ч.
Продутая воздухом медь насыщена кислородом и газовыми пузырьками, которые удаляются при восстановительной обработке меди (дразнении). Дразнение можно производить свежесрубленной древесиной (бревнами), мазутом или природным газом. При разложении реагентов образуются водород, оксид углерода и углеводороды, которые взаимодействуют с растворенной Сu2О и восстанавливают ее по реакциям:
Сu2О + Н2 = 2 Сu + Н2О
Сu2О + СО = 2 Сu + СО2
4 Сu2О + СН4 = 8 Сu + СО2 + 2 Н2О и т. д.
В процессе дразнения ванна хорошо перемешивается газовыми пузырьками, что обеспечивает высокую степень восстановления Сu2О, удаление растворенных газов и способствует глубокой десульфуризации меди. Продолжительность периода дразнения достигает 2,5 - 3 ч и определяется степенью насыщения продутой ранее меди кислородом. После дразнения получают плотную - красную медь, содержащую не более 0,01 % S и до 0,2 % О2. Такую медь разливают в аноды. Для разливки применяют изложницы, установленные на горизонтальных разливочных машинах карусельного типа.
Готовые аноды имеют длину 800 - 900 мм, ширину 800 - 900 мм и толщину 35 - 40 мм. Масса анодов на разных заводах составляет 240 - 320 кг. Общая продолжительность огневого рафинирования при переработке твердой меди составляет около 24 ч.
Дата добавления: 2018-06-01; просмотров: 2732; Мы поможем в написании вашей работы! |
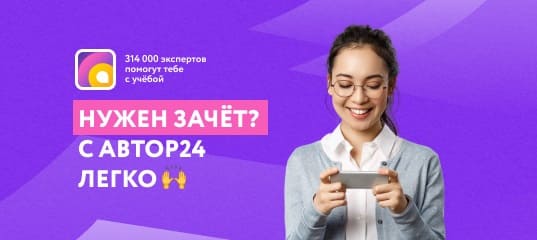
Мы поможем в написании ваших работ!