РОТОРЫ АСИНХРОННЫХ ДВИГАТЕЛЕЙ
И ЯКОРЯ МАШИН ПОСТОЯННОГО ТОКА
Магнитопроводы роторов асинхронных двигателей и Якорей машин постоянного тока с внешним диаметром менее 990 мм собирают из целых листов, которые вырубаются из электротехнической стали толщиной 0,5 мм (рис. 8.45). В листе штампуют пазы, а при необходимости, кроме того, круглые отверстия диаметр 15…35 мм для образования вентиляционных каналов. При большой радиальной высоте листа отверстия располагают в несколько концентрических рядов в шахматном порядке. Для посадки магнитопровода на вал в центре ли штампуются отверстие, в котором предусматривается шпоночная канавка, а также круглая лунка — шихтовочный знак А, для того чтобы при шихтовке укладывать все листы в одно и то же положение относительно друг друга. В результате такой укладки пазы получаются с более ровными стенками. После штамповки и снятия заусенцев листы лакируют и подвергают термообработке для создания оксидной пленки. При изготовлении роторов асинхронных двигателей с литой клеткой магнитопроводы сначала собирают из листов на оправке, а после заливки алюминиевой обмотки напрессовывают на вал. При внешних диаметрах ротора до 200...300 мм магнитопроводы сажают на гладкий вал горячей посадкой, а при больших диаметрах на валу предусматривается шпонка.
Рис. 8.45. Пример листа магнитопровода ротора
Магнитопроводы роторов, имеющие фазную обмотку или сварную клетку, а также магнитопроводы якорей машин постоянного тока набирают из листов непосредствен из вал (рис. 8.46). Магнитопроводы 1 спрессовывают стальными нажимными шайбами, которые имеют кольцевые пояса 4, называемые обмоткодержателями и предназначенные для поддержки лобовых частей обмотки 2. Выполнение обмоткодержателей выбирается в соответствии с формой лобовых частей обмотки.
|
|
Рис. 8.46. Ротор (а) и якорь (б) из целых листов
Магнитопровод ротора или якоря в спрессованном состоянии фиксируется на валу в осевом направлении или с помощью пружинит колец 5, врезанных в канавку на валу, или втулок 6, насаживаемых на вал с большим натягом. Иногда для фиксации магнитопровода с одной стороны упирается в предусмотренный на валу буртик. Лобовые части обмотки закрепляют бандажом 3.
При внешнем диаметре ротора или якоря более 990 мм магнитопровод набирается из штампованных сегментов электротехнической стали (рис. 8.47). В этом случае сегменты набирают на ступицах, которые имеют сварную конструкцию (рис. 8.48). Размеры сегментов выбирают исходя из наилучшего раскроя листа. Для крепления в ступице в сегментах с внутренней стороны предусматривают выступы или углубления в форме ласточкина хвоста. Количество крепящих элементов в каждом сегменте должно быть не менее двух. В целях повышения механической прочности, а также улучшения магнитной проводимости пакеты собирают с перекрытием сегментов при переходе от слоя к слою.
|
|
Рис. 8.47. Сегмент якоря
Рис. 8.48. Якорь из сегментов
В осевом направлении сегменты якоря стягивают нал фланцами и стяжными шпильками, устанавливаемыми внутри вне магнитопровода.
Иногда на ступицах собирают магнитопроводы роторов (якорей) при их диаметрах менее 990 мм. Такое выполнение магнитопроводов целесообразно в том случае, когда разность между внутренним диаметром ротора (якоря), найденным из электромагнитного расчета, и диаметром вала получается значительной, а внутреннюю меньшего диаметра.
8.7.1. Механический расчет магнитопровода
При проектировании роторов (якорей) отдельные их элементы подлежат проверке на механическую прочность.
Расчет напряжений в магнитопроводах.При вращении магнитопроводах роторов и якорей возникают напряжения от центробежных сил. Наибольшие значения эти напряжения имеют у внутренней поверхности магнитопровода:
, (8.92)
|
|
где — диаметр ротора (якоря), м;
— коэффициент, учитывающий ослабление сечения листа шпоночной канавкой и вентиляционными отверстиями:
,
здесь — глубина паза, м (рис. 8.49);
— диаметр вентиляционного отверстия, м;
— минимальная высота ярма ротора (якоря), м:
;
— высота шпонки;
— диаметр вала.
Рис. 8.49. к расчету напряжения
в листе магнитопровода якоря
Коэффициент А определяется по табл. 8.8., в которой принято
;
.
Допустимое напряжение для электротехнической стали 120 106 Па.
Таблица 8.8. Значение коэффициента А
| | |||||||
0,06 | 0,08 | 0,1 | 0,12 | 0,14 | 0,16 | 0,18 | 0,2 | |
0,3 | 0,0201 | 0,0208 | 0,0216 | 0,0225 | 0,0236 | 0,0247 | 0,0262 | 0,0277 |
0,4 | 0,0208 | 0,0217 | 0,0227 | 0,0238 | 0,025 | 0,0263 | 0,0278 | 0,0296 |
0,5 | 0,0219 | 0,023 | 0,0241 | 0,0254 | 0,0269 | 0,0285 | 0,0304 | 0,0324 |
0,6 | 0,0237 | 0,0249 | 0,0265 | 0,0282 | 0,0300 | 0,032 | 0,0344 | 0,0369 |
0,7 | 0,0259 | 0,028 | 0,0303 | 0,0328 | 0,0354 | 0,0382 | 0,0414 | 0,044 |
Расчет колец и втулок, запирающих ротор (якорь) на валу.На кольцо, которым магнитопровод запирается на валу, действует усилие, сдвигающее нажимную шайбу вдоль оси. Это усилие, Н, вызывается упругостью спрессованного пакета и находится по формуле
|
|
, (8.93)
где — диаметр окружности, проведенной через середины пазов, м;
— упругость спрессованного пакета, берется как 1/3 усилия прессовки:
Па. Большие значения
выбирают для машин меньшей мощности.
Напряжение на срез кольца прямоугольного сечения, Па,
, (8.94 а)
где — ширина кольца, м.
Для кольца круглого сечения диаметром
. (8.94 б)
Допустимое значение для колец, выполненных из стали, принимается равным 60·106 Па.
Втулка, запирающая магнитопровод ротора (якоря) на валу, ниже находится под действием силы , определяемой по (8.93). Для предотвращения сдвига втулки на валу под действием этой силы необходимо, чтобы сила сцепления
втулки с валом превышала силу
не менее чем в 1,2 раза. Сила
зависит от натяга, т. е. разницы внутреннего диаметра втулки и наружного диаметра пала. Необходимый натяг рассчитывается исходя из геометрических размеров вала, втулки и силы
, а затем по «Единой системе допусков и посадок» выбирается стандартная посадка. В соответствии с выбранной посадкой устанавливаются допуски на изготовление вала и втулки. После этого уточняется усилие сдвига втулки и проверяется максимальное напряжение на втулке, которое не должно превышать допустимого значения для материала, из которого изготовлена втулка.
Расчет натяга и выбор посадки осуществляется в следующем порядке.
Определяется давление на посадочную поверхность, Па, формулы
, (8.95)
где — коэффициент трения между сопрягающимися поверхностям (для сталей и чугунов в среднем
);
— площадь посадочной поверхности, м2:
(
и
— внутренний диаметр и длин втулки).
Затем определяется необходимый минимальный натяг, м:
, (8.96)
где — коэффициент.
Если вал и втулка изготовлены из стали, а вал не имеет отверстия, то
,
здесь Е — модуль нормальной упругости (для сталей Е = 2,1·1011 Па); — наружный диаметр втулки, м.
По полученному значению натяга выбирается стандартная посадка, имеющая натяг, близкий к расчетному.
Максимальное напряжение на втулке определяется по формуле
. (8.97)
Значение определяется из (8.96) при максимальном натяге
.
Пример.Рассчитать втулку, запирающую магнитопровод якоря на валу. м,
м,
м,
м и
Па.
По (8.93)
Н;
по (8.95)
Па.
Необходимый минимальный натяг из (8.96)
м;
Па.
По стандарту выбираем посадку
(допуски для вала
мкм, а для втулки
мкм). При этой посадке минимальный натяг
мкм (450·10-2 м), максимальный натяг
мкм (940·10-7 м).
Уточняем давление на посадочную поверхность при минимальном натяге из (8.96):
Па.
Уточняем силу по (8.95)
Н;
.
Давление при максимальном натяге
Па.
Напряжение на растяжение в сечении втулки по (8.97)
Па.
Проверка прочности зубцов.Зубцы магнитопровода нагружены центробежной силой, силами от собственного веса, а также от веса обмотки и изоляции, лежащих в пазу. Наиболее слабым в механическом отношении является сечение в основании зубца шириной . Напряжение растяжения в этом сечении, Па, определяется по формуле
. (8.98)
Центробежная сила зубца и содержимого паза на 1 м длины якоря, Н/м,
, (8.99)
где — внешний диаметр ротора (якоря) и высота паза, м.
Масса зубца на 1 м длины якоря, кг,
, (8.100)
где — средняя ширина зубца, м;
— коэффициент заполнения пакета сталью.
Масса меди обмотки и ее изоляции на 1 м длины якоря, кг,
, (8.101)
где — сечение проводника, м2,
— число проводников в пазу;
— ширина паза, м.
Проверка прочности шпонок.Шпонки для фиксации магнитопровода обычно выбирают такого же сечения, что и на свободном конце вала. Они рассчитываются на смятие рабочих поверхностей исходя из наибольшего значения передаваемого момента. Наибольшее распространение получили призматические шпонки. Напряжение смятия, Па,
, (8.102)
где — номинальный момент, Н·м;
— высота и длина шпонки, м.
Коэффициент перегрузки выбирается равным в пределах 2—3.
В шпонках, изготовленных из стали марки Ст5, допустимое напряжение принимается приблизительно равным 150·106 Па.
8.7.2. Расчет бандажей и клиньев
В пазах роторов и якорей располагаются обмотки, на которые при вращении действуют центробежные силы. Для предотвращения перемещения в радиальном направлении обмотки должны быть надежно закреплены.
Лобовые части обмоток закрепляют бандажами, намотанными из проволоки или стекловолокна. Закрепление пазовой части обмотки посредством бандажей можно применять для машин постоянного тока относительно небольшой мощности (при диаметрах якоря до 300...350 мм), имеющих открытые пазы. Бандажи располагают в специальных канавках магнитопровода, которые образуются в результате применения листов меньшего диаметра, чем основные (рис. 8.50).
Рис. 8.50. Якорь машины постоянного
тока с креплением обмотки бандажами
Применение бандажей имеет определенные преимущества, так как при этом уменьшается высота зубца, что приводит к уменьшению магнитного напряжения зубцов и потерь при их перемагничивании. Однако при больших скоростях (при > 35 м/с) применение бандажей становится нерациональным, так как бандажи перекрывают чрезмерно большую поверхность якоря, что ухудшает его отдачу. При наличии проволочных бандажей из-за потерь в них понижается КПД машины, а при бандажах из магнитной проволоки ухудшается коммутация. При наличии кольцевых канавок увеличивается воздушный зазор, а, следовательно, и магнитное напряжение зазора. Поэтому у более мощных машин постоянного тока, имеющих на роторе (якоре) полузакрытые пазы, крепление обмоток в активной части производят клиньями.
Расчет бандажей.Для бандажей применяют магнитную или стальную немагнитную проволоку или стеклоленту. При частотах перемагничивания более 50 Гц и в напряженных по коммутации машинах на активной части преимущественно применяют немагнитную проволоку. Диаметр проволоки для бандажей предварительно выбирают в пределах 0,8…2,0 мм (меньшие диаметры проволоки берут для машины с меньшим диаметром якоря).
Для уменьшения потерь бандаж делят на части, для чего по длине магнитопровода делают несколько канавок. Длину каждой канавки следует принимать не более 15.. .20 мм, а общая длина всех канавок не должна превышать 35% длины магнитопровода. На лобовых частях обмотки ширина бандажей может достигать 40 мм. Более широкие бандажи также следует делить на части или применять укладку в несколько слоев по высоте.
Под проволочными бандажами на пазовой и лобовой частях обмотки якоря подкладывают миканит толщиной 0,3. ..0,4 мм. Внешний диаметр установленных бандажей не должен превышать внешнего диаметра якоря. Для укрепления бандажей по ширине применяют скрепки из белой жести шириной 8. ..15 мм, припаиваемые оловянным припоем (рис. 8.51).
Рис. 8.51. Крепление концов проволоки бандажей якоря:
а — на магнитопроводе; б — на лобовых частях обмотки
По сравнению с проволочными бандажи из стеклоленты, пропитанной синтетическими смолами, имеют преимущества. У них нет собственных потерь, они не требуют наложения изоляции между бандажом и обмоткой, менее трудоемки в изготовлении. Недостатком таких бандажей является их большая толщина, так как стеклолента имеет меньшую механическую прочность.
При расчете бандажа исходят из того, что он испытывает напряжение от центробежных сил обмотки и самого бандажа. Число витков проволочного бандажа
, (8.103)
где — диаметр проволоки бандажа, м;
— допустимое напряжение растяжения, принимаемое для стальной бандажной проволоки равным 450·106 Па;
— максимальная частота вращения, об/мин;
— напряжение от центробежных сил бандажа, Па.
Для бандажей из стали
, (8.104)
При определении числа витков бандажа, располагаемого на магнитопроводе, в (8.103) подставляют массу проводников и изоляции
пазовой частиобмотки, кг:
, (8.105)
где — число пазов якоря;
— полная длина магнитопровода якоря, м;
— по (8.101).
Для нахождения винтов бандажа с одной стороны лобовой части в (8.103) подставляют массу ,кг:
, (8.106)
где — длина лобовой части проводника, м;
— площадь поперечного сечения проводника, м2; коэффициент 1,2 приближенно учитывает массу изоляции.
Число витков бандажа из стеклоленты определяют по формула
, (8.107)
где — площадь поперечного сечения ленты, м2;
— допустимое напряжение растяжения, равное 150·106 Па для стеклоленты класса нагревостойкости
и 130·106 Па для класса
.
Для бандажей из стеклоленты, Па,
. (8.108)
Для бандажей используется лента ЛСБ (ТУ 6.11.22) толщиной 0,18. ..0,2 мм и шириной 10, 15, 20, 25, 30 мм. Высоту бандажных канавок на магнитопроводе якоря выбирают равной от 2 до 3,5 мм.
Пример.Двигатель постоянного тока имеет данные: кВт, максимальная эксплуатационная частота вращения (при ослаблении поля) 2200 об/мин,
м,
м,
,
м,
м;
м2,
м2.
Из (8.101)
кг.
Масса пазовой части обмотки с изоляцией по (8.105)
кг.
Напряжение от центробежных сил по (8.108)
Па.
По (8.107)
.
Расчет клиньев.Клинья изготовляют из гетинакса, текстолита, стеклотекстолита и дерева (бука, клена, ясеня). Клин рассчитывают на изгиб как балку с сосредоточенной нагрузкой посредине. Эта нагрузка равна центробежной силе пазовой части обмотки. Расчет производится на 1 м. Исходя из этого определяется предварительная высота клина , (рис. 8.51), м:
. (8.109)
Центробежная сила пазовой части обмотки на 1 м, Н/м,
,
где — по (8.101);
— средняя ширина клина, м (рис. 8.52),
.
Допустимое напряжение на изгиб для гетинакса равно 20 МПа, для текстолита — 35 МПа, для дерева при расположении волокон поперек паза — 8 и вдоль паза — 4 МПа.
По найденной высоте из табл. 8.9 подбирают нормализованные размеры клина. Приведенные в таблице размеры даны в соответствии с рис. 8.52. По производственным соображениям высота клина должна составлять не менее 0,256
.
После выбора клина проводят поверочный расчет. Напряжение на изгиб, Па,
. (8.110)
Напряжение на срез, Па,
, (8.111)
где — в метрах по рис. 8.52 и табл. 8.9.
Рис. 8.52. К расчету пазового клина
Таблица 8.9. Размеры клина
![]() | 3 | 4 | 5 | 6 | 7 | 8 |
![]() | ![]() | ![]() | ![]() | ![]() | ![]() | ![]() |
![]() | 2,5 | 3,5 | 4,5 | 5,5 | 6,5 | 7 |
Допустимое напряжение на срез для гетинакса равно 10 МПа, для текстолита — 15 МПа, для дерева при расположении волокон поперек паза — 4 и вдоль паза — 2 МПа.
Пример.Тот же двигатель, что и в предыдущем примере ( кВт). Размеры паза
м. Остальные данные те же.
Из (8.101)
кг.
Центробежная сила пазовой части обмотки
Н/м.
Материал клина — текстолит с МПа. Выбираем
=14·10-3 м.
Из (8.109)
м.
По табл. 8.9 выбираем клин с = 4·10-3 м;
= 12 + 1,2 = 13,2 мм;
= 3,5 мм.
Проводим проверку:
По (8.110)
Па;
по (8.111)
Па.
Выбранный клин имеет достаточную механическую прочность.
КОЛЛЕКТОРЫ
Коллектор является ответственной и сложной частью постоянного тока. Он состоит из коллекторных пластин, изготовляют из твердотянутой меди трапецеидального сечения толщиной 3...15 мм. Иногда для повышения механической прочности применяют пластины из меди с присадкой кадмия. Для медных пластин друг от друга между ними укладывают прокладки из специального коллекторного миканита толщиной 0,8...1,5 Набор коллекторных пластин с изоляцией между ними должен прочно закреплен и иметь строго цилиндрическую форму при режимах работы машины. Существующие конструкции коллекторов различают по способу крепления пластин и имеют большое многообразие. Здесь рассматриваются наиболее употребляемые в современных машинах способы крепления: нажимными конусными фланцами и конструкционной пластмассой.
При креплении нажимными конусными фланцами коллекторные пластины выполняют в виде ласточкина хвоста. Изоляционные прокладки между пластинами — такой же формы. Коллекторы с креплением нажимными конусными фланцами делят на арочные и клиновидные. В первом случае нажим на пластины осуществляется только на ласточкин хвост (рис. 8,53, а), во втором — на ласточкин хвост и концы пластин (рис. 53, б).
Рис. 8.53. Способы крепления коллекторных пластин
Наибольшее распространение получили арочные коллекторы, как более технологичные. На рис. 8.54 и 8.55 показаны конструкции таких коллекторов.
Ни рис. 8.54 нажимные фланцы 1, надетые на втулку 2, стягиваются кольцевой гайкой 3. Для изоляции всех коллекторных пластин от корпуса на нажимные фланцы надевают прессованные из миканита манжеты 4, а на втулку — миканитовый цилиндр 5. Со стороны якоря у коллекторной пластины имеется выступ 6, называемый петушком, в котором выфрезеровывается шлиц. В этот шлиц закладывают, а затем припаивают проводники обмотки якоря.
Рис. 8.54. Коллектор малых машин
Рассмотренную конструкцию применяют при диаметрах коллекторов до 200...250 мм и малой длине. В коллекторах с общей длиной более 200 мм не рекомендуется применять затяжку фланцев кольцевой гайкой, так как в этом случае при нагреве пластин из-за температурной деформации происходит бочкообразный выгиб пластин.
Пример конструкции коллекторов с большими диаметрами показан на рис. 8.55. Здесь нажимные фланцы 1 стягивают стальными шпильками 2. На фланцы надевают миканитовые манжеты 3. При большой разнице в диаметрах якоря и коллектора в шлиц пластины впаивают медные полоски 4 — петушки, к которым присоединяют проводники якоря.
Рис. 8.55. Коллектор на пластмассе
В коллекторах относительно небольших размеров (с внешним диаметром до 40...50 см) в настоящее время находит широкое применение крепление пластин пластмассами (рис. 8.56). По сравнению с креплением нажимными фланцами такие коллекторы более надежны в эксплуатации в отношении сохранения правильной цилиндрической формы, имеют меньшую трудоемкость изготовления и себестоимость за счет отсутствия механической обработки пластин на станке. Для посадки коллектора на вал внутри его предусматривают стальную втулку 1, в которой для лучшего сцепления с пластмассой проточены кольцевые канавки. Пластмассу 2 впрессовывают в пространство между втулкой и коллекторными пластинами. Для этого применяют пластмассу марки К6 или АГ-4. В целях повышения механической прочности в углубления коллекторных пластин 3 вкладывают армировочные кольца 4, выполненные из стальной проволоки или полосы. Размеры колец и число их витков зависят от диаметра коллектора. Показанная на рис. 8.5 конструкция коллектора применяется при их диаметрах до 25 см.
Внешний диаметр коллектора , его общую длину
и ширину коллекторного деления
определяют из электромагнитного расчета. Ниже даны некоторые соотношения, позволяющие выбрать размеры коллекторных пластин (рис. 8.57).
Высоту коллекторной пластины принимают равной:
. (8.112)
Рис. 8.56. Коллектор на пластмассе
Рис. 8.57. Коллекторная пластина
Высота ласточкина хвоста
. (8.113)
Дня равномерного распределения центробежных сил ласточкины хвосты стараются располагать несимметрично: . При выборе длины
можно исходить из соотношения
. (8.114)
Ширину выточки , нужной для выхода шлифовального круга и фрезы при продорожке изоляции между пластинами, берут равной 6…8 мм.
Размер выбирается для якорей с многовитковыми секциями равной 12...15 мм, а для якорей с одновитковыми секциями 15…20 мм.
Толщина миканитовых манжет равна 1…1,5 мм, а миканитового цилиндра 0,75…1 мм.
Профиль ласточкина хвоста задается углами и
, которые обычно применяются равными соответственно 30 и 3°. При диаметре коллектора менее 15 см эти углы принимаются равными 45 и 3°. Число шпилек для стягивания нажимных фланцев зависит от диаметра коллектора. При
менее 50 см число шпилек выбирается в пределах от 6 до 12. Диаметр шпилек не рекомендуется брать менее 16 мм.
8.8.1. Механический расчет коллектора
с нажимными конусными фланцами
Ниже дается упрощенная методика, позволяющая получить удовлетворительные результаты для большинства практических случаев.
В предлагаемой методике механического расчета коллектора проводится проверка напряжений в наиболее опасных сечениях пластины, стяжных болтах и миканитовой манжете. Опасными сечениями коллекторных пластин являются сечения I—I II—II, III—III (рис. 8.58).
При расчете напряжений в сечениях I—I и II—II консольную часть пластины рассматривают как балку с заделанным концом, на которую действует распределенная нагрузка. Распределенная нагрузка создается двумя силами: центробежной силой части пластины
и радиальной составляющей силы арочного распора
,которая возникает в результате сжатия пластин нажимными фланцами.
Рис. 8.58. К расчету коллектора
Консольные части пластины рассчитывают для изношенного коллектора. Радиальный износ можно принять до 20…40%
(см. рис. 8.58).
Исходя из сказанного, напряжение изгиба в сечении I—I, Па, находится по формуле
, (8.115)
где — средняя толщина консольной части пластины, м:
;
здесь — толщина миканитовой прокладки;
— число коллекторных пластин;
— размеры, м, по рис. 8.57.
Центробежная сила ,Н, определяется по формуле
, (8.116)
где — радиус инерции консольной части, м;
— масса выступа (консольной части), кг:
;
— площадь боковой поверхности выступа, м2.
Радиальная составляющая силы арочного распора, Н,
. (8.117)
Давление между пластинами выбирают таким, чтобы обеспечить сжатие миканитовых прокладок, при котором они не имели бы возможности перемещаться радиально. Это давление может быть определено по эмпирической формуле, Па,
, (8.118)
где — диаметр коллектора, см.
Для сечения II—II напряжение подсчитывают аналогично (с учетом петушков). При расчете напряжения от растягивающих и сжимающих сил в сечении III—III,Па, уголок хвоста рассматривают как балку, заделанную в этом сечении и нагруженную сосредоточенной силой:
, (8.119)
где — толщина пластины в средней части хвоста, м:
;
— размеры, м, по рис. 8.58.
Центробежную , и радиальную
составляющие силы арочного рассчитывают по (8.116) и (8.117). При этом вместо массы
должна быть взята полная масса коллекторной пластины и вместо
— расчетная площадь боковой поверхности пластины. Радиус инерции берется равным
. Напряжения
, и
не должны превосходить 120 МПа. Напряжение сжатия в миканитовых манжетах, отнесенное к 1 м2 площади прилегания манжеты к конусу с углом
, находят по формуле
, (8.120)
где — по рис. 8.58.
Напряжение сжатия не должно превосходить 50 МПа.
Сжатые болты рассчитывают, исходя из осевого давления, которое должны создать нажимные шайбы.
Напряжение в болтах на растяжение, Па,
, (8.121)
где — диаметр болта, м;
— число болтов.
Значение не должно превышать 300 МПа.
Когда фланцы стягивают кольцевой гайкой, проверяют напряжение на срез витков резьбы гайки от силы запрессовки, Па:
, (8.122)
Напряжение не должно быть более 80 МПа.
При нагреве коллектора возникают дополнительные напряжения вследствие неодинакового расширения меди и стали. Эти напряжения учитывают путем умножения найденных выше напряжений и коэффициент 1,1...1,2.
Пример. Исходные данные: м,
м,
м,
м,
м,
м, 59
м,
м,
м,
м,
м2,
м2,
м2,
м2,
об/мин,
м,
м
Из (8.118)
Па.
Сечение I—I:
из (8.117)
Н;
м;
масса консольной части
кг;
радиус инерции консольной части
м;
центробежная сила по (8.116)
Н;
напряжение изгиба по (8.115)
Па.
Сечение II—II (с учетом петушков, рис. 8.58):
Н;
центробежную силу определяем для двух участков консольной части (А и на рис. 8.58):
кг;
Н;
кг;
Н,
где м — радиус центра тяжести петушков; напряжение изгиба по (8.115)
Па.
Сечение III—III: из (8.117)
Н;
м;
кг;
м;
центробежная сила по (8.116)
Н;
м;
Па;
напряжение сжатия в манжетах по (8.120)
Па;
напряжение на срез резьбы гайки по (8.122)
Па.
Коллектор имеет достаточную механическую прочность.
8.8.2. Механический расчет коллектора на пластмассе
При механическом расчете коллектора на пластмассе определяют напряжение в кольце из пластмассы, удерживающем пластину. Давление на кольцевой выступ пластмассового кольца, Па (рис. 8.59), определяется по формуле
, (8.123)
где — толщина миканитовой прокладки, м;
кг/м3;
кг/м3;
кг/м3 — плотности миканита, пластмассы и меди;
— диаметр окружности по центру тяжести коллекторных пластин, м;
— коэффициент трения меди по миканиту:
;
— радианная мера толщины прокладок, рад;
— площадь поперечного сечения пластмассового кольца, м2;
— боковая площадь коллекторной пластины, м2;
— приведенная площадь пластмассового кольца с учетом стальных колец, м2;
— ширина кольцевого выступа, м:
;
— площадь поперечного сечения армирующего кольца, м2;
Па;
Па;
Па — модули упругости миканита, пластмассы и стали; т — коэффициент, равный отношению испытательной частоты вращения коллектора к максимальной частоте вращения якоря
, принимают
;
— коэффициент заполнения коллектора медью:
.
Напряжение растяжения всего кольца, вызванное радиальной деформацией, Па,
Рис. 8.59. К расчету коллектора на пластмассе
. (8.124)
Предел прочности при растяжении составляет 20 МПа пластмассы К6 и 80 МПа для пластмассы АГ-4.
Прочность коллекторных пластин проверяется на напряжение в них от арочного распора и центробежной силы С.
Консольные части пластин проверяют, так же как и в предыдущем случае, по (8.115). Кроме того, проверяется напряжение в сечениях и
(рис. 8.59).
Напряжение растяжения пластины в сечении , Па,
(8.125)
где — толщина коллекторной пластины в сечении
идлина хвостовой части пластины в этом сечении, м.
Силы и
определяют по (8.116) и (8.117) соответственно для части пластины, расположенной выше линии
.
Напряжение среза в сечении . Па,
, (8.126)
где — средняя толщина и высота пластины в сечении
, м.
Силы и
определяют для всей пластины.
Среднее давление между пластинами, обеспечивающее необходимый арочный распор, Па, определяют по формуле
. (8.127)
Пример.Исходные данные: м,
м,
м,
м2,
м2,
м2,
м,
м,
об/мин,
м.
Коэффициент заполнения коллектора медью
.
Приведенная площадь пластмассового кольца
м2.
Из (8.123)
Из (8.124)
Па.
Давление между пластинами по (8.127)
Из (8.117)
Н.
Средняя толщина коллекторной пластины
м.
Средняя толщина пластины в сечении (рис. 8.59)
м.
Масса пластины
кг.
Из (8.116)
Напряжение среза в сечении по (8.126)
Па.
Коллектор имеет достаточную механическую прочность.
КОНТАКТНЫЕ КОЛЬЦА
Контактные кольца применяют в синхронных машинах и асинхронных двигателях с фазным ротором. Они располагаются на валу машины, и к ним подсоединяют обмотку ротора. У синхронных машин устанавливают два кольца, а у асинхронных — три. К контактным кольцам синхронных машин через неподвижные щетки подсоединяют источник питания для обмотки возбуждения, а в асинхронных двигателях пусковой или регулировочный резистор. Контактные кольца или располагают между магнитопроводом ротора и подшипниковым щитом, или выносят за подшипниковый щит. Наиболее часто применяют последнюю конструкцию, так как в этом случае можно выполнять оба подшипниковых щита одинаковыми, кроме того, устраняется опасность попадания на обмотки щеточной пыли.
Материалом для колец служат сталь, чугун, латунь или медь. На 9.5 показана конструкция узла контактных колец для асинхронных двигателей. На рис. 10.2 приведена конструкция узла колец для синхронных двигателе СДН2.
У машин относительно небольшой мощности контактные кольца 1 в холодном или горячем состоянии напрессовывают на втулку 2, расположенную на валу (рис. 8.60). Для изоляции колец от втулки применяют наложенный в несколько слоев формовочный миканит 3 толщиной 0,5...0,7 мм. При внешнем диаметре до 100 мм контактные кольца иногда выполняют на пластмассе.
Рис. 8.60. Контактные кольца на втулке
Для машин большой мощности применяют кольца с болтовым креплением (рис. 8.61). Контактные кольца 1 изолированы друг от друга и от болтов 3 изоляционными трубками 2. Весь узел прикрепляют к торцу вала 4. Эта конструкция имеет сравнительно небольшую массу, хорошее охлаждение колец, но она менее надежна в отношении прочности крепления и биения.
Рис. 8.61. Контактные кольца с болтовым креплением
Механический расчет контактных колец производят в целях определения напряжения в них от действия центробежной силы. Расчет производится для колец после их предельного износа. Предельный диаметральный износ принимают: 8 мм для колец диаметре до 100 мм, 12 мм для диаметров 100...250 мм и 16 мм для диаметров свыше 250 мм.
Центробежная сила кольца, Н,
, (8.128)
где — масса кольца, кг;
— средний радиус кольца, м;
— максимальная частота вращения, об/мин.
Напряжение на растяжение в опасном сечении (сечение кольца ослабленное отверстием для контактной шпильки), Па,
, (8.129)
где — площадь сечения кольца, м2:
, (8.130)
— внешний диаметр кольца после износа, м;
— внутренний диаметр кольца и диаметр отверстия под шпильку, м;
— ширина кольца, м.
Напряжения в контактных кольцах, напрессованных на втулку, должны быть рассчитаны с учетом натяга при прессовой посадке по (8.97). Допускаемые напряжения не должны превышать 150 МПа для стальных колец и 75 МПа для латунных.
ТОКОСЪЕМНЫЙ АППАРАТ
Токосъемный аппарат, предназначенный для съема тока с коллектора или с контактных колец, состоит из щеток, щеткодержателей, щеточных пальцев и траверсы. На рис. 8.62 показаны некоторые из возможных конструкций щеткодержателей.
Щетки для электрических машин прессуют из угольных и графитных порошков. Электрические свойства щеток и стандартизованные их размеры приведены в приложении 5. Для отвода тока в щетки заделываются гибкие плетеные канатики 4, которые вторыми своими концами посредством припаянных к ним наконечников соединяют к неподвижной части щеткодержателя. Щетки 2 устанавливают в обойму щеткодержателя 1. Щеткодержатели выполняют из латуни литыми или штампованными. Для того чтобы осуществить плотный контакт с коллектором или контактными кольцам на щетки с помощью пружины 3 осуществляется давление, которое выбирается равным 0,02...0,04 МПа. Щеткодержатели укрепляют на щеточных пальцах с помощью колодок 5. На щеточном пальце обычно размещают несколько щеткодержателей. Наиболее распространенным видом щеткодержателей являются радиальные (рис. 8.62, а), у них направление щетки совпадает с продолжением радиуса коллектора. Такие щеткодержатели применяют для реверсивных машин, так как условия работы щеток не зависят от направления вращения. На рис. 8.63 показана еще одна конструкция радиального щеткодержателя.
Для машин одностороннего вращения чаще находят применение реактивные щеткодержатели (см. рис. 8.62, 6), достоинство которых заключается в том, что при определенном нажиме и угле наклона щетка не упирается в обойму и скользит в ней без трения.
Рис. 8.62. Щеткодержатели машин постоянного тока:
а — радиальный; б — реактивный
Рис. 8.63. Радиальный щеткодержатель
1 — щетка; 2 — щеткодержатель;
3 — фарфоровый наконечник; 4 — пружина; 5 — рычаг;
6 — нажимная пружина; 7 — корпус щеткодержателя
В машинах постоянного тока щеточные пальцы крепят к траверсе, являющейся несущей конструкцией всего узла токосъема. Траверса должна иметь возможность перемещения по окружности в целях установки щеток на геометрическую нейтраль при сборке и наладке машины. На рис. 8.64 показана одна из возможных конструкций траверсы, которая применяется для машин относительно небольших мощностей. Траверсу закрепляют на специальной заточке подшипникового щита стяжными и стопорными болтами.
Рис. 8.64. Траверса
Пальцы, на которых укрепляют щеткодержатели, представляют собой цилиндрические или призматические стержни. Второе исполнение встречается чаще, так как оно проще в производстве и лучше фиксирует положение щеток. Призматические пальцы выполняют гетинакса или текстолита либо из полосы стали, спрессованной в месте крепления с траверсой. Цилиндрические пальцы изолируют от траверсы миканитовыми втулками и шайбами или спрессовывают пластмассой. Число пальцев в машине обычно равно числу полюсов. Щеточные пальцы одинаковой полярности соединяют между собой медными шинами или проводами.
Щеткодержатели асинхронных и синхронных машин располагаются на изолированной части пальца, металлический конец которого спрессован или ввинчен в прилив подшипникового щита.
Иногда у машин постоянного тока применяется также крепление щеточных пальцев непосредственно к подшипниковому щиту. Такое крепление принято, например, у машин серии 2П с высотой оси вращения мм.
Дата добавления: 2018-06-01; просмотров: 659; Мы поможем в написании вашей работы! |
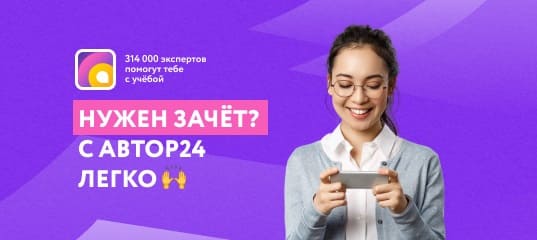
Мы поможем в написании ваших работ!