Подготовка выгорающих добавок
Лекция 9
Подготовка непластичных материалов и добавок
Приготовление шамота
Подготовка каменистых материалов
Формование керамических изделий из пластических масс
Ленточное формование
Штамповка из пластичных масс
Формование вытачиванием из пластичных масс
Лепка
Прессование изделий из порошков
Пороки изделий, спрессованных из порошкообразных масс
Формование керамическим литьем
Дефекты при литье
Приготовление шамота
Шамот получают обжигом огнеупорных глин или отходов производства (размолотого брака, боя шамотных огнеупорных изделий, бывших в употреблении и тщательно очищенных), в последнем случае качество шамотного боя непостоянно.
Для получения шамота постоянного качества глины обжигают в печи, куда она поступает в виде кусков или брикетов, которые должны быть достаточно прочными.
7.1.1 Подготовка брикетов. Существует два способа формования брикета:
1) мокрый (влажность брикета 18 – 20%) более экономичный по расходу энергии при приготовлении брикета и обжиге;
2) сухой – 10 – 14% - более экономичный по затратам труда.
Технологическая схема изготовления приведена на рисунке 9.1.
Рисунок 9.1 – Технологическая схема производства шамотного порошка из кусковой глины или брикетов.
При полусухом прессовании брикетов важно уплотнение молотой глины для удаления воздуха, увеличения механической прочности брикета. Воздух препятствует спеканию частиц, повышает пористость брикета, снижая прочность. Качество массы улучшается при обработке ее паром.
|
|
При обжиге глину доводят почти до спекания, не допуская пережога, иначе шамот теряет способность поглощать воду.
Качественный шамот должен обладать определенной огнеупорностью, химическим составом, постоянным водопоглощением (6 – 7%) – высокожженый, (24 – 26%) – низкожженый. В шамоте не должно быть ошлаковки от золы топлива и других выплавок, плотность должна быть 2,6 – 2,7 г/см3.
Шамот нужно хранить в закрытых помещениях или бункера, перевозить в закрытых устройствах.
При помоле шамота, варьируя зерновой состав отдельных компонентов массы, можно существенно изменять свойства керамических изделий – плотность, прочность, газопроницаемость, термическую устойчивость.
Количество и величина частиц материала рассчитывается так, чтобы пространство между крупными частицами было заполнено мелкими, т.е плотная упаковка. Изготавливают три фракции шамота: крупная – 2 – 4мм, средняя – 0,5 – 2мм, мелкая – 0,5 – 0,15мм. Максимальная плотность упаковки достигается при соотношении К:С:М = 43:23:34%.
|
|
Форма зерен шамота влияет на сцепление их с глиной: острогранные продолговатые зерна более прочно сцепляются с глиной, чем круглые.
Если используется мокрый помол, то достигается тонкая степень измельчения, тщательное перемешивание компонентов массы, но производительность агрегатов ниже, чем при сухом помоле.
Аналогичный шамоту применяется обожженный каолин и дегидратированная глина. В качестве отщающей добавки – бой готовых изделий («череп»).
Обожженный каолин – готовят, как шамот, добавляя в брикеты при формовании огнеупорную глину для упрочнения и уменьшения уносов с отходящими газами.
Дегидратированная глина – низкожженый шамот – обжигают при температурах, выше температуры дегидратации (700 – 800 °С) во вращающихся печах.
Череп – подвергается дроблению, грубому помолу, просеву.
Подготовка каменистых материалов
Каменистые непластичные материалы – кварц, полевой шпат, пегматит – поставляющиеся на производство крупными кусками, предварительно обжигают при 1000 – 1100 °С, для облегчения последующего измельчения и улучшения термических свойств.
Обожженные куски подвергают первичному дроблению (щековые или валковые дробилки), затем промывают для удаления загрязнений (моечные установки с вибрирующими лотками), затем подвергают грубому дроблению (бегуны с гранитным подом и гранитными катками иначе возможно загрязнение массы намолом железа), отправляют в расходный бункер. Эта схема работает по замкнутому циклу, с возвратом «отказа» на вторичный помол.
|
|
Песок для производства грубой керамики только просеивают через сита №3 для выделения каменистых включений. При изготовлении тонкой керамики используют чистые пески, не требующие обогащения.
Подготовка выгорающих добавок
Опилки просеивают через сито №10, по схеме: склад опилок – многоковшовый экскаватор – плоское качающееся сито – транспортер – ящичный подаватель. Или склад опилок – бульдозер – эстакада – сито-бурат – ящичный подаватель.
Угли различных марок (каменные, бурые, антрациты) подвергают помолу на молотковых или валковых дробилках и просеивают через сито №3. Мелкие фракции наименее дефицитные, дешевые и требуют лишь просева.
Иногда применяют централизованную подготовку выгорающих добавок с совместным помолом опилок и угля в вертикальных молотковых дробилках (рисунок 9.2).
Рисунок 9.2 – Подготовка выгорающих добавок.
Дата добавления: 2018-06-27; просмотров: 672; Мы поможем в написании вашей работы! |
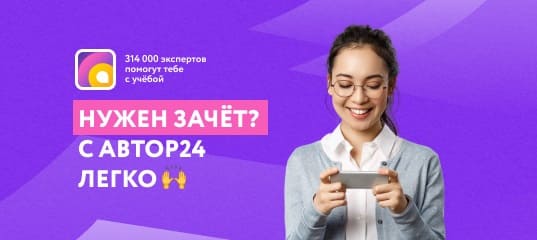
Мы поможем в написании ваших работ!