Пути повышения качества широкослойной
Способы повышения производительности процесса наплавки ленточным электродом
Производительность способа наплавки ленточным электродом может быть повышена, в частности путем выбора:
- оптимальных соотношений его ширины и толщины;
- скорости наплавки;
- применения многоэлектродных вариантов наплавки (двумя лентами, составными лентами и др.);
- наплавки с увеличенным вылетом (например, профилированным ленточным электродом);
- наплавки с поперечными колебаниями;
- наплавки расщепленной лентой;
- металлокерамической и порошковой лентами и др.
Увеличение ширины ленточного электрода
Необходимость повышения производительности процесса наплавки, получения однородного по составу и свойствам наплавленного слоя металла определяет целесообразность увеличения ширины ленточного электрода. При этом также будет обеспечиваться уменьшение числа перекрытий валиков на единицу площади наплавляемой поверхности, где вероятность образования дефектов наиболее высока.
Однако при использовании ленты шириной свыше 100 мм существенно ухудшаются устойчивость горения дуги и качество формирования валиков [2, 29, 89]. Увеличение тока в случае наплавки лентами шириной более 100 мм приводит к усилению воздействия собственного магнитного поля, которое оказывает отрицательное влияние на процесс горения дуги, плавление и перенос электродного металла через межэлектродный промежуток, а также вызывает появление эффекта “магнитного дутья” [16].
|
|
Многоэлектродные варианты наплавки
Для увеличения производительности процесса наплавки, а также для улучшения условий горения дуги на торце ленты, плавления основного металла и снижения влияния “магнитного дутья” на формирование валика известен способ наплавки несколькими ленточными электродами с общей сварочной ванной (рис. 1.9) [38].
Рис. 1.9 – Схема наплавки несколькими ленточными электродами [38]: 1 – широкая лента; 2 – узкая лента; 3 – источник питания; 4 – токоподвод; 5 – подающие ролики; 6 – флюс; 7 – наплавленный валик; 8 – основной металл
Ленточные электроды шириной 25 мм присоединяют к положительному полюсу одного источника питания, а шириной
50 мм - к отрицательному полюсу другого источника [38]. При этом узкие ленты устанавливают с опережением широких на 15¸20 мм в направлении наплавки, а расстояние между смежными краями лент составляет 2¸5 мм. Производительность процесса может достигать 50 кг/ч при высоте валика 5¸7 мм, а доля участия основного металла в наплавленном составляет 7 %. Однако этот способ не нашел широкого применения из-за сложности и громоздкости оборудования, необходимости использования двух источников питания, проблемы обеспечения надежной, одновременной подачи всех лент.
|
|
Относительно менее сложным является способ, основанный на подаче в зону наплавки широкой ленты, которая при подходе к сварочной ванне разрезается на узкие полосы, дополнительно гофрируемые с целью придания им жесткости (рис. 1.10) [2]. Такая схема позволяет равномерно и одновременно подавать все ленты. Для обеспечения независимого расплавления каждой полосы и повышения устойчивости горения дуги они разводятся относительно друг друга в пределах, обеспечивающих получение сплошной сварочной ванны. При этом изменяется ее форма, создаются условия для существования независимых сварочных дуг на каждой полосе. Однако данное устройство также является чрезвычайно громоздким, а формирование валика ухудшается вследствие воздействия магнитного поля, наведенного проходящим сварочным током.
Рис. 1.10 – Схема подачи с одновременным «расщеплением» широкой ленты на пять узких полос (Вл = 5 Вп), разведенных на расстояние а [2]: 1 - широкий ленточный электрод; 2 – подающие ролики; 3 – режущие кромки; 4 – гофрирующие профили; 5 – узкие полосы; 6 - направляющие; 7 – основной металл
|
|
Для повышения производительности процесса наплавки в сочетании с обеспечением минимальной доли основного металла в наплавленном покрытии разработан способ наплавки двумя ленточными электродами, основанный на использовании преимуществ электрошлакового процесса (рис. 1.13) [16, 25, 32, 2-85, 2-86 ЛЛК] при котором подогрев и плавление лент осуществляется за счет тепла, выделяемого при прохождении тока через шлаковую ванну, расположенную между лентами. При этом доля основного металла в наплавленном не превышает 10 %, а производительность достигает 30 кг/ч и более [16].
Подача второй ленты, расположенной параллельно вслед за первой, при ограниченном зазоре между ними (6¸10 мм), затрудняющем поступление нерасплавленного флюса, охлаждающего перегретый шлак, позволяет уменьшить долю участия (g) основного металла в наплавленном до 10¸12 % и повысить производительность процесса Gн до ~25 кг/час. С увеличением зазора между лентами до 20¸30 мм процесс наплавки под флюсом высокой электропроводности переходит в горизонтальный электрошлаковый (g » 8¸10 %, Gн до 40 кг/час) [2-87, 2-88, 1-90]. Однако как для перемежающегося, так и электрошлакового процесса, стабильное качество шва и зоны сплавления трудно обеспечить без применения надёжных способов управления тепломассопереносом и формообразованием ванны.
|
|
Эффективность такого управления определяется способностью предотвратить возникновение дефектов формирования шва и зоны сплавления. Для процесса наплавки двумя ленточными электродами под флюсом в перемежающемся режиме перераспределение энергии по фронту плавления, а также сил, действующих на ванну, связано с поведением шлака в зазоре между лентами и изменением соотношения тока дуги и шлаковой проводимости, зависящих от токовой нагрузки на электродах [1-89, 2-89]. Эффективным путем повышения качества наплавки двумя ленточными электродами является обеспечение равномерного поступления расплавленного электродного металла и движения расплава по всей ширине сварочной ванны. Для его реализации предложен способ наплавки двумя ленточными электродами с изменением соотношения токов в электродах позволяющий регулировать уровень шлаковой ванны у каждого из электродов, управлять характером оплавления их торцов и поступлением электродного металла в сварочную ванну, формой и глубиной проплавления, а также долей участия основного металла [Лаврик, 2-89].
Вместе с тем, как показывает анализ литературных источников [98] и опыт работы предприятий отечественного и зарубежного машиностроения, широкое применение способа наплавки двумя лентами ограничивается вследствие увеличения возможности появления дефектов в наплавленном слое (шлаковых включений, кратероподобных дефектов в центральной части валика и др.), относительного усложнения конструкции устройства для подачи ленточных электродов.
Дальнейшее совершенствование процесса наплавки ленточным электродом должно быть направлено, прежде всего, на повышение его производительности (увеличением плотности тока в ленточном электроде; повышением скорости наплавки; увеличением ширины ленты в сочетании с профилированием или применением управляющего внешнего магнитного поля) и улучшение качества наплавленного металла (выбором оптимальных параметров режима наплавки; обеспечением необходимой проплавляющей способности дуги).
Пути повышения качества широкослойной
Дата добавления: 2018-06-27; просмотров: 210; Мы поможем в написании вашей работы! |
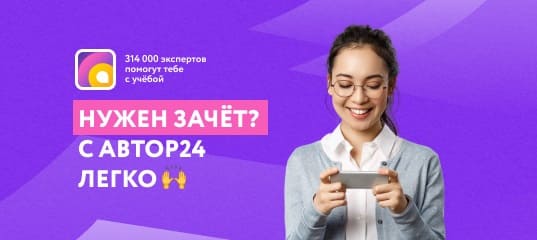
Мы поможем в написании ваших работ!