ИСТОЧНИКИ И ХАРАКТЕРИСТИКИ ПРОИЗВОДСТВЕННЫХ ПОГРЕШНОСТЕЙ
Опыт производства любой промышленной продукции показывает, что получить детали, совершенно одинаковые по размерам, невозможно. Если даже технологический процесс, машины, инструмент остаются неизменными и персонал, обслуживающий этот процесс, один и тот же, все же размеры деталей всегда варьируют в более или менее широких границах, т. е. имеют место производственные погрешности.
Погрешности размеров могут возникать как при обработке, так и при контроле деталей. Те и другие погрешности имеют в основном одинаковый характер и подчиняются одним и тем же закономерностям.
Эти погрешности вызываются причинами двоякого рода. Одни из них действуют в постоянном направлении, соответственно вызывая отклонения размеров всегда в одну сторону. Например, износ токарного резца или шлифовального круга будет вызывать систематическое увеличение, при неизменных прочих условиях, диаметра обрабатываемых деталей, износ развертки — уменьшение диаметра отверстий. Также односторонне и систематически влияет на некоторые размеры изготовляемых деталей изменение размеров и геометрии режущих инструментов в результате переточек и др. Причины этого рода не случайны, их принято называть систематическими.
Однако и после устранения такого рода причин изменчивость размеров изделий никогда полностью не исчезает, что обусловлено действием второго рода многочисленных случайных причин. К ним относятся:
|
|
1) погрешности оборудования — неточности кинематической цепи станка, его шкал, лимбов и т. д.; деформации деталей станка; колебания и вибрации из-за недостаточной жесткости станка или фундамента, неполной уравновешенности вращающихся масс, толчков в передачах и т. п.; ненормальные зазоры между деталями станка и изменение силы трения между ними; износ направляющих; неправильности в подаче смазки, охлаждающей жидкости и др.;
2) колебания режимов работы — изменения скоростей резания и подачи, вращения рабочих приводов станка; изменения усилия резания из-за разных причин; нагрев инструмента и обрабатываемой детали, изменения температуры помещения и т. д.;
3) погрешности инструмента — износ и недостаточная жесткость режущего инструмента; затупление режущей грани; пригар; неоднородность материала режущего инструмента; неправильность формы фасонного инструмента; износ и недостаточная жесткость измерительного инструмента и прочее;
4) недостатки рабочего приспособления — неправильности оправок, цанг и т. д.; недостаточная жесткость приспособления, которая приводит к деформации деталей под влиянием усилия резания; нестабильность установки детали и т. п.;
|
|
5) неоднородность материала изделия — колебания в химическом составе, колебания механических свойств, шлаковые включения, внутренние трещины, внутренние напряжения и т. д.; часть этих свойств влияет на колебания режима обработки изделия, часть — вызывает непосредственное изменение размеров или формы изделия;
6) ошибки рабочего: при настройке станка и установке инструмента, при установке и закреплении детали, при снятии пробной стружки, при регулировке режима работы станка и подачи охлаждающей смеси, при заточке инструмента и т. д.;
7) погрешности измерительных приборов — зазоры в подвижных соединениях цепи передачи приборов, изменение характеристики сил трения в измерительных цепях, погрешности аттестации образцовых деталей, по которым настраиваются измерительные приборы, случайное изменение параметров электрической цепи, погрешности отсчетов по шкалам, случайные колебания температуры, субъективные ошибки при измерении и другие.
Действие этих случайных причин устранить невозможно. Они характеризуются следующим:
Число случайных факторов и параметров, вызванных ими частных погрешностей, не изменяются во времени.
Сам процесс контроля состоит из следующих этапов:
|
|
1 - измерение контролируемого параметра (размер, температура и т.п.);
2 - сравнение его с заданным значением;
3 - принятие решения о соответствии контролируемого параметра заданному и выработка необходимой команды;
4 -реализация решения (команды) с помощью соответствующего исполнительного органа.
В практике машиностроения контролю чаще всего подвергаются следующие параметры:
1) линейные и реже угловые размеры обрабатываемых деталей;
2) геометрические параметры деталей, такие как прямолинейность, перпендикулярность, соосность, конусность, огранка и т.п.;
3) качество обработанной поверхности – шероховатость, волнистость и т.п.;
4) физические свойства обрабатываемых деталей:
· механические – упругость, твердость, усталостная прочность;
· магнитные – магнитное сопротивление, магнитная проницаемость, коэрцитивная сила;
· электрические – электросопротивление (электропровод-ность);
· коррозионная стойкость;
и т.д.;
5) потребляемая мощность на технологический процесс;
6) параметры технологического процесса – усилия, давление, температура;
7) экономические показатели – производительность, чистое время работы машин, станков, оборудования.
|
|
.
Конструкция измерительного устройства в значительной степени зависит от применяемого метода измерения при контроле. Классификация методов контроля приводится в таблице 3.1.
Таблица 3.1
Методы измерения | Разновидности контроля |
по взаимодействию с объектом | · контактные · бесконтактные |
по способу измерения | · абсолютные · дифференциальные |
по режиму работы преобразователя | · масштабные · компенсационные · предельные |
по измеряемому параметру | · прямые · косвенные |
по месту осуществления | · совмещенные · вынесенные |
Контактные измерительные устройства осуществляют измерение при непосредственном контакте с контролируемым объектом. Для измерения размеров они достаточно просты по конструкции и позволяют получить сравнительно большой выходной сигнал. Однако они в значительной степени подвержены износу, из-за которого могут потерять точность измерения. К числу контактных измерительных устройств для измерения размеров относятся различные рычажные системы с преобразователями.
Бесконтактные измерительные устройства позволяют осуществлять измерения без контакта с исследуемым объектом, вследствие чего они не изнашиваются и длительное время сохраняют начальную точность. Однако, такие устройства сложнее, дороже и, из-за наличия промежуточной среды, могут оказаться менее точными. В таких измерительных устройствах используются фотоэлектрические, индуктивные, лазерные, радиоактивные, пневматические и т.п. преобразователи.
Процесс измерения контролируемого параметра может быть осуществлен по-разному. Можно измерять его абсолютную (суммарную) величину и тогда отсчет необходимо производить относительно некоторой постоянной жестко фиксированной базы. При значительных величинах и требуемой высокой точности измерения этот способ становится трудоемким, поскольку необходимо с высокой точностью совмещать либо начало шкалы с исходным параметром контролируемой величины, либо исходный параметр с началом шкалы измерения. При автоматизации процесса измерения это становится затруднительно, т.к. объект измерения и измерительная система могут иметь разные базы. Тогда оказывается целесообразным использование дифференциального метода измерения, при котором измеряются отклонения от исходных начального и конечного параметров и абсолютная величина определяется как разность этих отклонений от заданного эталона (действительного или мнимого).
В зависимости от способа работы чувствительного элемента преобразователя (датчика) измерительной системы можно выделить три метода измерения: масштабный, компенсационный и предельный.
При масштабном методе измерения чувствительный элемент должен производить в некотором масштабе измерение контролируемого параметра (т.е. выходной сигнал пропорционален измеряемому параметру).
При компенсационном методе измерения производится сравнение измеряемого параметра с эталонным и чувствительный элемент датчика должен зафиксировать равенство их величин. Таким образом, чувствительный элемент представляет собой «нуль-орган». Конструкция такого чувствительного элемента проще и может быть достигнута высокая чувствительность, что позволяет получить весьма высокую точность измерения, поскольку исключаются погрешности измерения.
Наконец, при осуществлении технического контроля, в ряде случаев нет необходимости знать действительные значения измеряемого параметра, а важно фиксировать определенные значения или границы изменения этого параметра. В этом случае может быть использован предельный метод измерения, при котором преобразователь или чувствительный элемент измерительного устройства генерирует выходной сигнал при достижении измеряемым параметром заданной величины.
Иногда измерительные устройства не совсем верно называют контрольными устройствами или контрольными приспособлениями. Скорее это устройство для контроля, поскольку по результатам измерения должно быть принято решение и действие. Таким образом, нельзя отождествлять часть с целым. Например, калибр для измерения диаметра является измерительным устройством, показывающим лежит ли измеряемый диаметр в пределах допуска или нет, а уже отсюда решение: годен или не годен и что делать дальше.
Разумеется, что любое измерительное устройство связано с контролем, ибо в противном случае отпадает смысл в измерении. Действительно, измеряя диаметр валиков, определяют, пригодны ли они для сопряжения и принимают решение о дальнейших действиях (контроль). Измерять микрометром диаметр гвоздей, чтобы затем забить их в стену и повесить шапку, навряд-ли кому-нибудь придет в голову.
Автоматические измерительные устройства позволяют значительно упростить процесс контроля и являются элементами его автоматизации. Поскольку они находятся на стыке изделие – система и должны осуществлять довольно трудоемкий процесс измерения, то успешное решение автоматизации измерения является залогом успешной работы всей системы контроля.
Автоматические измерительные устройства могут использовать прямые методы измерения или косвенные.
При прямом методе контроля измеряется непосредственно контролируемый параметр, например, диаметр изделия или его твердость.
При косвенном методе измеряется сопутствующая величина, связанная с контролируемым параметром и по ней судят о самой контролируемой величине. Так при обработке валика могут измерять положение инструмента и по нему судить о диаметре изделия, или измерять магнитную проницаемость стальной детали и по ней судить о твердости после закалки. Косвенные методы измерения по своей природе менее точны, но позволяют вести измерения в трудных условиях, в ряде случаев проще осуществляются, а иногда являются единственно возможными.
Наконец по месту осуществления методы измерения могут быть совмещенными и вынесенными. При совмещенных методах измерение осуществляется во время других этапов производственного процесса, например с обработкой или транспортировкой. При использовании вынесенных методов организуется специальная измерительная позиция, где производится измерение заданных параметров. Для вынесенных методов значительно легче достичь высокой точности измерения, поскольку на такой позиция могут быть созданы специальные условия, обеспечивающие исключение помех.
ДАТЧИКИ
![]() |
Как уже отмечалось, первым этапом контроля является измерение контролируемого параметра, т.е. получение информации. Первым элементом, установленным в технологическом оборудовании и воспринимающим контролируемый параметр, является датчик. Он преобразует измеряемые физические величины в сигналы, удобные для дальнейшей передачи в измерительные или управляющие устройства. Измеряемыми параметрами при осуществлении контроля являются геометрические размеры, перемещения, скорость, температура, усилия, давление, вибрации, расход, уровень, загазованность, запыленность и др.
К числу основных признаков, позволяющих классифицировать первичные преобразователи, относятся принцип действия и вид входного и выходного сигналов (рис. 3.3).
В зависимости от принципа действия первичные преобразователи можно разделить на две группы: параметрические и генераторные.
Параметрические преобразователи преобразуют контролируемую величину в один из параметров электрической цепи: проводимость (сопротивление), индуктивность, емкость. Следовательно, для их работы необходимо подводить от внешнего источника электрическую энергию. К параметрическим относят следующие типы преобразователей: потенциометрические, индуктивные, емкостные, тензометрические и др.
В генераторных преобразователях непосредственно преобразуется неэлектрическая энергия входного сигнала в электрическую энергию, значение которой пропорционально значению контролируемого параметра. К генераторным относятся термоэлектрические (термопары), фотоэлектрические, пьезоэлектрические и тахометрические преобразователи. Они работают автономно, т. е. не нуждаются в подводе внешней электроэнергии.
По виду входного сигнала первичные преобразователи делятся на следующие группы: температуры, давления, разрежения, расхода, уровня, состава и влажности веществ, плотности, перемещения, скорости, ускорения и т. д.
По виду выходного сигнала первичные преобразователи подразделяют на несколько групп. Одна группа преобразует контролируемую величину в изменение активного сопротивления, другая — в изменение емкости, третья — в изменение индуктивности и т. д.
Любой датчик состоит из отдельных частей. Основной частью является чувствительный элемент, а средства защиты, вспомогательных преобразователей и крепления чувствительного элемента относятся к вспомогательным элементам.
Потенциометрические датчики
Потенциометрический датчик представляет собой переменное электрическое сопротивление, величина выходного напряжения которого зависит от положения токосъемного контакта.
Потенциометрические датчики предназначены для преобразования линейных и угловых перемещений в электрический сигнал, а также для воспроизведения простейших функциональных зависимостей в автоматических и вычислительных устройствах непрерывного типа.
В потенциометрах непрерывной намотки переменным сопротивлением служит намотанная на каркас в один ряд тонкая проволока, по зачищенной поверхности которой скользит токосъемник. Сопротивление таких потенциометров лежит в пределах от нескольких десятков ом до десятков килоом. Таким образом, потенциометр непрерывной намотки состоит из каркаса, обмотки и токосъемника (рис. 3.4).
Каркас выполняется из материала, обладающего изоляционными свойствами, и имеет форму стержня, кольца или изогнутой по дуге пластинки. В качестве изоляционного материала используют гетинакс, текстолит, керамику или металл, покрытый непроводящим слоем окисла. Обмотку изготавливают из эмалированной проволоки, диаметр которой определяет точность потенциометра. Датчики высокого класса точности наматываются проволокой диаметром 0,03…0,1 мм, датчики низкого класса — 0,1…0,4мм.В качестве обмоточного провода применяют константан, манганин, фехраль и сплавы на основе благородных металлов. Обмотка укладывается на каркас равномерно, поскольку это также влияет на точность работы датчика. Токосъемник (щетка) выполняется из материала несколько мягче, чем материал обмоточного провода, во избежание перетирания витков при длительной работе. Движок имеет форму изогнутой упругой пластины для создания контактного давления, которое колеблется от 0,5 г до 15 г.
![]() |
В зависимости от характера движения ползунка потенциометры подразделяются на датчики линейного и углового перемещения. Щетка датчика линейных перемещений совершает прямолинейное поступательное движение, а щетка датчика углового перемещения — круговое движение (рис. 3.4).
По конструкции реохорда (каркас с намотанной на нем проволокой) различают два типа потенциометрических преобразователей: линейные и функциональные.
Линейные потенциометрические преобразователи имеют постоянные сечение каркаса, диаметр проволоки и шаг намотки.
Напряжение питания и длина намотки являются постоянными величинами, поэтому выходные напряжения прямо пропорциональны значению перемещения подвижного контакта.
Функциональные потенциометрические преобразователи обладают нелинейной характеристикой, что обеспечивается намоткой проволоки на каркасы с переменным сечением. Такой преобразователь представляет собой как бы несколько включенных последовательно линейных преобразователей. Нелинейность характеристики может быть достигнута также путем шунтирования резисторами отдельных участков намотки линейных потенциометрических преобразователей. Если у линейного потенциометрического преобразователя сделать отвод от середины обмотки, то он будет характеризовать наряду со значением перемещения движка и его направление.
Потенциометрические преобразователи могут включаться по схеме реостата (рис. 3.5, а и б) или потенциометра (рис. 3.5, в) (делителя напряжения). В зависимости от схемы включения перемещение подвижного контакта преобразуется в изменение тока (при последовательном соединении) или напряжения (при включении по схеме делителя). Первая схема применяется довольно редко, так как она не обеспечивает достаточной точности преобразования, на величину которой оказывают влияние сопротивление соединительных проводов и переходного сопротивления между контактом и обмоткой реохорда.
Потенциометрические преобразователи выполняют с 20 %-ной или 100 %-ной зоной пропорциональности. Последние получили большее распространение, так как они охватывают всю шкалу измерительного прибора.
К преимуществам потенциометрических датчиков можно отнести: 1) простоту конструкции, малые габариты и вес; 2) возможность получения линейных статических характеристик с высокой точностью; 3) стабильность характеристик; 4) возможность работы на переменном и постоянном токе.
Недостатками этих датчиков следует считать: 1) наличие скользящего контакта, который может стать причиной отказов вследствие окисления контактной дорожки, перетирания витков или отгибания ползунка; 2) погрешность в работе за счет нагрузки; 3) сравнительно небольшой коэффициент преобразования и высокий порог чувствительности; 4) наличие шумов; 5) подверженность электроэррозии под действием импульсных разрядов.
Из сопоставления видно, что с течением времени следует ожидать постепенную замену потенциометрических датчиков более совершенными бесконтактными датчиками.
Индуктивные датчики
Индуктивные датчики применяют для преобразования малых линейных или угловых перемещений в электрические сигналы. Принцип их действия основан на зависимости индуктивного сопротивления катушки от изменения зазора вмагнитопроводе, от перемещения магнитопровода в катушке или от изменения площади зазора.
Индуктивный преобразователь датчика с подвижным якорем (изменяющимся зазором) представляет собой катушку индуктивности 3 с магнитопроводом 2 и подвижным якорем 1 (рис. 3.6, а). Катушка индуктивности с магнитопроводом, называемая статором, закрепляется неподвижно, а якорь механически соединяется с подвижной частью системы измерения, перемещение которой необходимо преобразовать в электрический сигнал. Перемещение якоря изменяет воздушный зазор δ (входная величина преобразователя), вызывает изменение индуктивного сопротивления катушки и, как следствие этого, выходной величины тока I при постоянном напряжении U0 .
Чувствительность индуктивных преобразователей с изменяющимся воздушным зазором уменьшается с увеличением зазора δ, поэтому их используют для измерения и контроля очень малых перемещений (до 2 мм). В таком диапазоне рабочих перемещений их чувствительность не превышает 2 мкм.
Индуктивные преобразователи с перемещающимся магнитопроводом (рис. 3.6, б) способны измерять большие перемещения (до 50мм).
У индуктивных преобразователей с изменяющейся площадью воздушного зазора (рис. 3.6, в) статическая характеристика линейна только на определенном участке. Линейность нарушается, когда активное сопротивление становится сравнимым с индуктивным. Диапазоны перемещения якоря больше (до 8 мм), чем у преобразователей с изменяющимся воздушным зазором, однако чувствительность ниже.
Все перечисленные выше виды индуктивных преобразователей обладают высокой надежностью, имеют практически неограниченный срок службы и большую мощность выходного сигнала (до нескольких ватт). К недостаткам можно отнести нереверсивность статической характеристики, небольшой диапазон перемещения якоря, наличие тока холостого хода и влияние колебаний амплитуды и частоты напряжения питания. Эти недостатки практически полностью отсутствуют у дифференциальных индуктивных преобразователей.
Дифференциальный индуктивный преобразователь (рис. 3.6, г) имеет два статора 2 с катушками индуктивности 3 и один подвижный якорь 1. При отклонении якоря от среднего положения происходит изменение индуктивного сопротивления обеих катушек и на выходе преобразователя появляется напряжение Uн. Катушки индуктивности включаются либо в дифференциальную измерительную схему, либо работают как смежные плечи мостовой измерительной схемы.
Дифференциальные индуктивные преобразователи по сравнению с ранее рассмотренными конструкциями обладают более высокими точностью и чувствительностью. Их статическая характеристика линейна и реверсивна. Поэтому они получили наибольшее распространение.
Трансформаторные преобразователи являются разновидностью индуктивных. Они представляют собой трансформаторы с пере- менным коэффициентом трансформации за счет изменения коэффициента взаимоиндукции между обмотками. Трансформаторные преобразователи применяют для преобразования небольших линейных и угловых перемещений в электрический сигнал (напряжение переменного тока).
Первичная обмотка 2 (рис. 3.7) дифференциального трансформаторного преобразователя с угловым перемещением якоря намотана на центральном стержне 1 магнитопровода, а две совершенно одинаковые вторичные обмотки 3 располагаются на крайних стержнях. Они соединены последовательно и имеют встречную намотку. При симметричном положении якоря 4 по отношению к стержню 1 во вторичных обмотках будут индуцироваться одинаковые по значению и противоположные по фазе ЭДС, а напряжение на выходе преобразователя будет равно нулю. При повороте якоря, механически связанного с подвижной частью системы измерения, изменяется значение магнитных потоков и в соответствии с этим значение ЭДС, т. е. на выходе появляется напряжение, амплитуда которого равна разности амплитуд ЭДС вторичных обмоток. Статическая характеристика рассмотренного преобразователя линейна и реверсивна. Реверсивность означает изменение в знаке выходного сигнала при изменении знака входного сигнала. Чувствительность преобразователя в 2 раза выше чувствительности обычных индуктивных преобразователей.
Интересна конструкция ферродинамического преобразователя, предназначенного для преобразования угловых перемещений в электрические сигналы.
Ферродинамический преобразователь (рис. 3.8) имеет магнито-провод, состоящий из шихтованного ярма 1 с полюсными наконечниками 2 и сердечника 3. На сердечнике 3 укреплены агатовые подпятники (на схеме не показаны), в которых на кернах установлена поворотная рамка 4, механически соединенная с подвижной частью системы измерения. Концы обмотки подвижной рамки подсоединяются с помощью спиральных пружин и проводов. Принцип работы преобразователя заключается в следующем. При подаче переменного тока на обмотку возбуждения 5 в магнитопроводе возникает магнитный поток. Если рамка 4 расположена по нейтрали ММ, то значение наведенной ЭДС равно нулю. При повороте рамки на некоторый угол α в ней индуцируется ЭДС, величина которой пропорциональна углу поворота. Рабочий угол рамки от нейтрали составляет 40°. В зависимости от типа преобразователя напряжение на выходе рамки изменяется от —1 до +1 В или от 0 до 2 В.
Высокочастотные индуктивные преобразователи позволяют измерить толщину фольги металлов, толщину гальванических покрытий, разностенность металлических труб и т. д. Принцип их действия основан на изменении индуктивности обмотки при возникновении вихревых токов в проводящем теле, расположенном вблизи этой обмотки.
В таких преобразователях используется так называемый поверхностный эффект, т. е. затухание вихревых токов по мере проникновения их в глубь проводящей среды, обусловленных переменным магнитным полем; при этом разность токов возбуждающего поля и поля вихревых токов уменьшается.
Емкостные датчики
Основу этих датчиков составляют емкостные преобразователи, которые преобразуют неэлектрические величины (перемещение, уровень жидкости, влажность, усилие и т. д.) в изменение электрической емкости. Емкостной преобразователь является частью регулирующего или измерительного устройства с чувствительным элементом, выполненного в виде конденсатора и реагирующего на изменение измеряемого параметра технологического процесса. Чувствительный элемент емкостного преобразователя представляет собой плоский или цилиндрический конденсатор, у которого при воздействии измеряемого параметра изменяется расстояние между пластинами, площадь пластин или диэлектрическая проницаемость среды между обкладками. Емкость конденсатора C возрастает с увеличением активной площади F и диэлектрической проницаемости ξ (для воды ξ =81; для воздуха ξ = 1; для формовочной смеси ξ = 1 ... 4) и уменьшается с увеличением расстояния между пластинами X, т. е. C = ξ0·ξ·F/X, где ξ0 — диэлектрическая проницаемость вакуума, ф/м. Учитывая влияние перечисленных факторов на размеры чувствительного элемента, различают три типа емкостных преобразователей: с переменным расстоянием между пластинами, с изменяемой площадью пластин и изменяемой диэлектрической проницаемостью среды. Перечисленные параметры емкостных преобразователей являются входными величинами, а выходной величиной будет емкость конденсатора.
![]() ![]() ![]() |
Емкостные преобразователи с переменным расстоянием между пластинами (рис. 3.9, а) как правило конструктивно выполняют в виде плоского конденсатора, состоящего из двух или более пластин, одна из которых закреплена, а другая механически связана с подвижной частью системы измерения. Емкостные преобразователи этого типа применяют для измерения толщины изделий, а также используют для измерения давления, усилия или вибрации.
Емкостные преобразователи с изменяемой площадью пластин выполняют как цилиндрическими (рис. 3.9, б), так и плоскими (рис. 3.9, в).
Цилиндрический емкостной преобразователь (рис. 3.9, б) представляет собой два цилиндра разного диаметра, помещаемые один в другой. Емкость конденсатора зависит от осевого перемещения δ внутреннего цилиндра. Преобразователи этого типа предназначаются для измерения линейных перемещений.
В плоском преобразователе (рис. 3.9, в) емкость зависит от изменения активной площади пластин при повороте одной пластины относительно другой. Такие преобразователи используют при измерении угловых перемещений.
Емкостные преобразователи с изменением диэлектрической проницаемости среды между пластинами могут применяться, например, для регулирования влажности формовочной смеси и дозирования воды при ее приготовлении. При колебании уровня жидкости изменяется емкость конденсатора (рис. 3.9, г), электродами которого служат корпус 1 и металлический стержень 2. Емкость такого преобразователя складывается из емкости цилиндрического конденсатора без жидкости и параллельно включенной емкости цилиндрического конденсатора с жидкостью. Емкость и чувствительность такого преобразователя увеличиваются с уменьшением отношения диаметров электродов, а также с ростом высоты цилиндра.
Емкостные преобразователи просты по устройству, обладают достаточно высокой чувствительностью, малыми размерами и массой. Однако они имеют три недостатка: мощность выходного сигнала мала, поэтому необходимо применять усилитель; при промышленной частоте электрического тока практически невозможно получить достаточную мощность, в этой связи они получают питание от источника высокой частоты (10 кГц и более); сильное влияние оказывают паразитические емкости и посторонние электрические поля, поэтому требуется тщательное экранирование как самих датчиков, так и соединительных проводов.
Тензометрические датчики
Работа преобразователя тензометрического датчика (тензорези-стора) основана на изменении электрического сопротивления проводников при упругих деформациях растяжения или сжатия. Они применяются для преобразования деформаций, усилий и напряжений в электрический сигнал. В зависимости от конструкции и материала чувствительного элемента тензорезисторы подразделяются на проволочные, фольговые, полупроводниковые и тензолитовые.
Простейшим проволочным тензорезистором может служить отрезок тонкой проволоки. При деформации детали одновременно будет деформироваться и наклеенная проволока. Изменение электросопротивления ΔR проволоки при ее растяжении или сжатии связано с относительной деформацией ε соотношением
где R — номинальное сопротивление проволоки, Ом; k — коэффициент чувствительности.
Коэффициент чувствительности k зависит от вида материала и технологии изготовления преобразователя; его значение определяют экспериментально. Наибольшее распространение получили константан и нихром, для которых k = 1,9…2,1.
![]() ![]() ![]() ![]() |
Размеры детали часто не позволяют закрепить на ней преобразователь в виде прямолинейного отрезка проволоки большой длины. Поэтому промышленность изготовляет тензометрические преобразователи в виде спирали (решетки) из нескольких петель проволоки (рис. 3.10, а). Проволоку 1 наклеивают на подложку 2 из тонкой бумаги или лаковой пленки и сверху наклеивают такую же тонкую бумагу. К проволоке приваривают (или припаивают) выводы 3, выполненные из тонких полосок медной фольги. Недостатком данной конструкции решетки, является чувствительность преобразователя к поперечным деформациям. Для устранения этого недостатка петли между рядами заменяют медными перемычками 4 (рис. 3.10, б). Основными параметрами решетки являются: длина l (3 ... 75 мм), ширина а (0,03 ... 10 мм) и радиус закругления r (0,1 ... 0,3 мм).
Проволочные тензорезисторы просты по конструкции, имеют малую массу и невысокую стоимость. Их статическая характеристика линейна и реверсивна. К недостаткам проволочных тензорезисторов относятся низкая чувствительность и одноразовость действия. Они подвержены влиянию окружающей среды (температура и влага).
Фольговые тензорезисторы по принципу действия и основным параметрам сходны с проволочными преобразователями и отличаются только конструкцией решетки (рис. 10, в) и способом ее получения. Для фольговых тензорезисторов применяется фольга толщиной 4 ... 12 мкм из константана, нихрома, титан-алюминиевого или золото-серебряного сплавов. Решетку фольговых тензодатчиков получают методом фотолитографии, который позволяет изготовлять преобразователи любой конструкции (линейные, розеточные, мембранные и т. п.) с высокой повторяемостью параметров. Фольговые тензорезисторы по сравнению с проволочными имеют ряд преимуществ. Они более чувствительны и точны за счет лучшей передачи деформации от детали к фольге, имеют хороший механический контакт с контролируемой деталью и позволяют пропускать через фольгу большой ток.
В настоящее время находят все большее применение полупроводниковые тензопреобразователи, изготовленные из полупроводниковых материалов — кремния, германия, мышьяка, галия и др.
В отличие от проволочных и фольговых преобразователей изменение сопротивления при деформации у полупроводниковых происходит благодаря изменению удельного сопротивления.
Основным преимуществом полупроводниковых преобразователей является высокая чувствительность (почти в 100 раз выше, чем у проволочных). Они имеют большой выходной сигнал, что позволяет в некоторых случаях отказаться от применения усилителя. Однако у них большой разброс параметров и низкая механическая прочность, т. е. они хрупки.
3.3.5. Фотоэлектрические датчики
Принцип действия преобразователей фотоэлектрических датчиков (фотоэлементов) основан на использовании фотоэлектрического эффекта, т. е. они реагируют на изменение светового потока. Создание фотоэлектрических преобразователей оказалось возможным, когда были открыты материалы, электроны которых получают дополнительную энергию при воздействии световой энергии. Причем значение дополнительной энергии может быть таково, что часть электронов оказывается свободной.
![]() |
В зависимости от поведения электронов, высвобождающихся под действием светового потока, различают три группы фотоэлементов: с внешним и внутренним фотоэффектом и с запирающим слоем (вентильные).
Фотоэлемент с внешним фотоэффектом (рис. 3.11, а) представляет собой вакуумную двухэлектродную лампу. Катод 1 образован светочувствительным слоем (цезий или сплав сурьмы с цезием) и нанесен на внутреннюю поверхность лампы, а анод 2 выполняется в виде кольца или пластины. Нередко в лампу вводят некоторое количество нейтрального газа (аргона), который не окисляет поверхность металла, но способен ионизироваться под ударами летящих электронов и увеличивать за счет своих ионов значение протекающего тока. Под действием световой энергии с поверхности выбиваются электроны, образующие электрический ток (внешний фотоэффект). Промышленность выпускает фотоэлементы следуюших типов: ЦГ — цезиевый газонаполненный; СЦВ — сурьмяно-цезиевый, вакуумный; ЦВ — цезиевый, вакуумный.
Фотоэлементы с внешним фотоэффектом обладают высокой чувствительностью и высокой температурной стабильностью. Для них характерна линейная зависимость фототока от светового потока. К числу недостатков рассмотренных фотоэлементов, которые ограничивают их применение в автоматических системах управления, относятся: необходимость в повышенном напряжении питания; хрупкость стеклянного баллона; старение и утомляемость, т. е. снижение чувствительности при сильной освещенности. Фотоэлементы с внутренним фотоэффектом (фоторезисторы) чувствительнее элементов первого типа, использующих фотоэффект со свободной поверхности металла. Фотоэлементы с внутренним фотоэффектом не нуждаются во вспомогательной энергии, и им может быть придана весьма разнообразная и очень удобная форма. Недостатками их являются: подверженность влиянию окружающей температуры, утомляемость и высокая инерционность. Последнее ограничивает применение фотоэлементов с внутренним фотоэффектом при частоте прерывания светового потока в несколько десятков герц.
Фоторезисторы (рис. 3.11, б) представляют собой стеклянную пластинку 1 с нанесенным тонким слоем селена или сернистых соединений различных металлов (таллия, висмута, кадмия, свинца). К пластине прикреплены электроды 2. имеющие контакт с полупроводниковым слоем. Размеры фоторезисторов очень невелики. При подаче к электродам напряжения через фоторезистор будет протекать ток, значение которого пропорционально освещенности. Зависимость тока от освещения имеет нелинейную величину. Однако чувствительность фоторезисторов в сотни раз превышает чувствительность вакуумных элементов, что позволяет их использовать в автоматических устройствах без усилителей.
У вентильных преобразователей свободные электроны, изменяя свою энергию под действием светового потока, остаются в веществе. В промышленности получили наибольшее распространение селеновые и меднозакисные фотоэлементы.
Селеновый фотоэлемент (рис. 3.11, в) имеет четыре рабочих слоя. Первый слой образован тонкой пленкой золота 1, далее идут запирающий слой 2, селеновый слой 3 и стальная подкладка 4. Запирающий слой, обладая детекторным свойством, пропускает электроны, выделившиеся из пленки золота, и препятствуют прохождению электронов противоположного направления. Таким образом, световой поток, проходя через пленку золота, создает вентильный фотоэффект, т. е. электроны из освещенного слоя переходят в неосвещенный. Это приводит к возникновению разности потенциалов Uвых. Фотоэлектрические преобразователи просты по устройству и достаточно надежны в работе, однако они более инерционны.
1. Азбель В.О. и др. Гибкое автоматическое производство . – Л.: «Машиностроение», 1983. – 376 с.
2. Бауман В.А., Быховский И.И. Вибрационные машины и процессы в строительстве. – М.: Высшая школа, 1977. – 255 с.
3. Белоусов А.П. и др. Автоматизация процессов в машиностроении. – М.: «Высш. школа», 1973. – 456 с.
4. Блехман И.И., Джанелидзе Г.Ю. Вибрационное перемещение. – М.: Наука, 1964. – 410 с.
5. Бовсуновский Я.И., Свечников Л.В. Механизация и автоматизация контрольных операций в машиностроении и приборострении. – М.-К.: Машгиз, 1961. 318 с.
6. Бочков В.М., Сілін Р.І. Обладнання автоматизованого виробництва. – Львів: Видавництво Державного університету “Львівська політехніка”, 2000. – 380 с.
7. Буда Я.Я. и др. Автоматизация процессов машиностроения. – М.: «Высшая школа», 1991. – 480 с.
8. Владзиевский А.П. Автоматические линии в машиностроении. Кн. І. – М.: Машгиз, 1958. – 430 с.
9. Владзиевский А.П., Белоусов А.П. Основы автоматизации производства в машиностроении. – М.: «Высшая школа», 1974. – 352 с.
10. Волчкевич Л.И. и др. Автоматы и автоматические линии. Ч.1 – М.: Высшая школа, 1976. – 230 с.
Дата добавления: 2018-06-27; просмотров: 713; Мы поможем в написании вашей работы! |
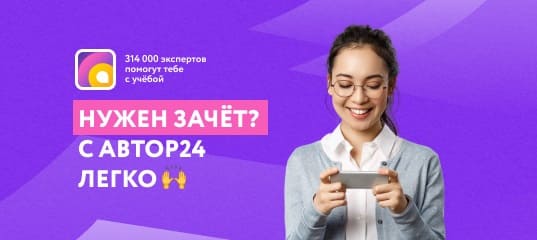
Мы поможем в написании ваших работ!