АВТОМАТИЗАЦИЯ ЗАГРУЗКИ И РАЗГРУЗКИ.
Автоматизация загрузки и разгрузки в общем комплексе задач по автоматизации технологических процессов является одной из наиболее сложных, что вызвано разнообразием процессов, а также форм и размеров заготовок (деталей). Иногда конструкция заготовок (деталей) такова, что автоматизировать загрузку вообще невозможно. Основное назначение автоматизации загрузки (питания) металлорежущих станков – превращение станков в полуавтоматы и автоматы и повышение коэффициента их использования, облегчение труда рабочих, создание лучших возможностей применения многостаночного обслуживания и в итоге – значительное повышение производительности труда и снижение себестоимости изготовляемых деталей.
Автоматическим загрузочно-разгрузочным устройством (АЗРУ) называется комплекс механизмов, обеспечивающих автоматическое перемещение заготовок в нужный момент времени с данного места хранения в рабочую зону станка и после завершения операции обработки удаление обработанной детали (полуфабриката) в заданное место хранения или транспортирования.
Назначение и виды загрузочных устройств
В зависимости от конструктивного выполнения загрузочно-разгрузочные устройства представляют собой:
– конструктивные узлы самой рабочей машины;
– самостоятельные независимые узлы;
– приспособления.
Загрузочно-разгрузочные устройства относятся к группе вспомогательных механизмов, так как сами не участвуют в собственно технологическом процессе обработки (сборки), т.е. в процессе изменения состояния предмета труда.
|
|
В зависимости от типа используемых заготовок различают два способа загрузки или питания: непрерывный и прерывистый или порционный.
При непрерывном способе питания заготовка подается на заданный шаг и от нее отделяется очередная порция материала или обрабатываемая деталь. При прерывистом или порционном способе питания осуществляется подача отдельных порций или штучных заготовок.
При первом способе материал, загружаемый в машину, обеспечивает непрерывную работу в течение нескольких операций и представляет единое целое. К этому способу относятся подача из бунтов (мотков) проволоки, ленты, проката профильного сечения или подача пруткового либо листового материала.
При порционном способе или поштучном питании осуществляется подача заготовок не связанных друг с другом. Для этого споcоба заготовки могут быть сориентированными предварительно в пространстве (магазинное питание) или могут быть расположены “навалом” (бункерное питание). Задача автоматического загрузочного устройства в этом случае состоит в том, чтобы каждый раз захватить заготовку и подать ее в рабочую зону в строго ориентированном положении.
|
|
2.2. АВТОМАТИЧЕСКИЕ УСТРОЙСТВА ДЛЯ НЕПРЕРЫВНОГО СПОСОБА ПИТАНИЯ
По способу привода эти устройства могут выполняться:
–с независимым (самостоятельным) приводом;
–приводимыми от рабочего органа машины.
Независимый привод делает загрузочное устройство самостоятельным механизмом, освобождает рабочие органы от дополнительной нагрузки, что особенно важно при выполнении деликатных или высокоточных работ. Привод от рабочего органа упрощает само устройство и, в ряде случаев, значительно упрощает синхронизацию и управление работой загрузочного устройства.
Рис. 2.1 – Блок-схема машины с независимым приводом
Блок-схема рабочей машины с автоматическим загрузочным устройством, имеющим независимый привод, представлена на рис. 2.1.
Здесь привод автоматического загрузочного устройства (АЗУ) осуществляется от своего двигателя Д1, а рабочих органов РО – от двигателя Д2. Для преобразования движений служат в каждой ветви редукторы Р, которые управляются исполнительным механизмом (ИМ). Синхронизация и выработка команд управления осуществляются системой автоматического управления САУ всего комплекса.
|
|
Блок-схема рабочей машины с автоматическим загрузочным устройством, имеющим привод от рабочего органа, может быть представлена рис. 2.2.
Здесь все механизмы работают от одного двигателя Д, который через редуктор Р сообщает движение рабочему органу машины РО. Последний сообщает движение собственно автоматическому загрузочному устройству АЗУ, осуществляющему подачу материала в рабочую зону станка. Синхронизация движений, включение и выключение РО и АЗУ, а иногда и общего двигателя Д, производятся исполнительным механизмом ИМ, управляемым системой автоматического управления САУ, содержащей программу управления и получающей информацию от АЗУ и РО. Уже из самой блок-схемы видно, что такое загрузочное устройство проще, чем предыдущее, содержит меньше узлов, а, следовательно, и более надежно. Однако оно создает дополнительную нагрузку на рабочий орган станка, что не всегда допустимо по условиям точности и характеру работы рабочей машины. Кроме того, ремонт и наладку такого загрузочного устройства необходимо производить совместно с рабочей машиной, что также не всегда удобно и рационально.
Рис. 2.2 – Блок-схема АЗУ с приводом от рабочего органа машины
|
|
По способу захвата подаваемого материала автоматические загрузочно-разгрузочные устройства непрерывного питания делятся на:
1) крючковые;
2) клещевые или цанговые;
3) валиковые (валковые) или роликовые.
Крючковые подающие устройства используются обычно для подачи ленточного или листового материала, осуществляя захват материала за технологические или рабочие отверстия или выступы, получаемые в процессе обработки (чаще вырубки).
На рис. 2.3 приводится сечение загрузочного устройства с подачей материала приводным клиновым устройством. При движении клина рабочего органа 3 вниз его скос через ролик 2 перемещает каретку 1 влево. Тогда крючок 4 поворачивается и его зуб перемещает материал влево. При движении клина вверх пружина 5 перемещает каретку 1 вправо, крючок 4 поворачивается, его зуб выходит из зацепления и скользит по материалу, подготавливая следующий шаг. Затем процесс повторяется. Могут быть различные модификации этих устройств, но всегда имеется захват (жесткая фиксация) по выступам или отверстиям и возвратно-поступательное или качательное движение подающего механизма. Иногда для повышения точности подачи и быстродействия используются грейферные механизмы, имеющие более сложную траекторию движения, но принцип захвата и транспортирования остает-ся прежним.
Крючковые подачи просты по конструкции, дешевы в изготовлении и могут быть легко установ-лены на любом кривошип-ном или эксцентриковом прессе с числом ходов до 200 в минуту. Однако для их работы требуются технологические отверстия или выступы, а подавае-мый материал должен быть непрерывным, что приводит к повышению расхода материала. В связи с этим применение этого способа ограничено.
Клещевые или цанговые подающие устройства характеризуются захватом и перемещением материала за счет сил трения при возвратно-поступательном движении механизма подачи. Поскольку передача движения осуществляется за счет сил трения, то сила трения в первом приближении определяется как Fтр = Nf, где N – сила нормального давления, а f – коэффициент трения. Тогда, изменяя силу нормального давления, обеспечивают одностороннюю подачу материала (зачастую с перехватом). Зажим материала для его перемещения может осуществляться рычажным, клиновым, шариковым или роликовым устройствами. В качестве примера на рис. 2.4 показана конструкция односторонней клещевой подачи с захватом подаваемой полосы или ленты роликами.
Валиковые (валковые) или роликовые автоматические загрузочные устройства осуществляют подачу в рабочую зону периодическим вращением валиков или роликов. При этом передача движения (захват) может быть за счет сил трения (фрикционная передача) либо захватом за отверстия или выступы, получаемые до захватного органа или в процессе осуществления захвата. Схема роликовой подачи приведена на рис. 2.5.
Рис. 2.5 – Роликовая подача
По способу действия на подаваемый материал автоматические загрузочно-разгрузочные устройства с непрерывным способом питания могут быть (см. рис. 2.6):
– тянущими (рис. 2.6, а);
– подающими (рис. 2.6, б);
– тянуще-подающими (рис. 2.6, в).
|
2.3. АВТОМАТИЧЕСКИЕ УСТРОЙСТВА ДЛЯ
ПОШТУЧНОГО СПОСОБА ПИТАНИЯ
Автоматические загрузочно-разгрузочные устройства непрерывного питания довольно просты, однако они применимы далеко не во всех случаях, т.к. заготовки здесь далеки от оптимальных форм и размеров, что приводит к увеличению отходов и снижению производительности труда. Стремление сблизить формы и размеры заготовок и изготавливаемых деталей приводит к необходимости загрузки штучными (отдельными) заготовками рабочих машин. Количество используемых в машиностроении типоразмеров заготовок огромно, что значительно усложняет создание и эксплуатацию автоматических загрузочно-разгрузочных устройств. В большинстве случаев подаваемые в рабочую зону заготовки должны быть ориентированными в пространстве, тогда как разгрузка осуществляется для уже ориентированных деталей. В связи с этим, большее значение имеет создание автоматических загрузочных устройств.
Автоматические загрузочные приспособления для штучных изделий появились довольно давно. Первоначально загрузочные устройства нашли применение в огнестрельном автоматическом оружии для подачи патронов, затем на пуговичных, патронных, конфетных фабриках, где продукция производится в массовых количествах.
Автоматические устройства для поштучного способа питания позволяют подавать в рабочую зону машины заготовки не связанные друг с другом, поштучно. Все разнообразие таких устройств может быть, прежде всего, разделено на два типа:
1) устройства магазинного питания;
2) устройства бункерного питания.
2.3.1. Устройства магазинного питания
Эти устройства осуществляют автоматическую подачу заготовок предварительно ориентированных и уложенных в магазин вручную. Иногда такие устройства называют полуавтоматическими.
Ручные ориентирование и загрузка в магазин требуют значительных затрат времени, что снижает производительность по сравнению с бункерным питанием. И, тем не менее, магазинные загрузочные устройства применяются в следующих случаях:
1) для деталей сложной формы, автоматическое ориентирование которых трудно осуществимо или не осуществимо вообще;
2) для деталей повышенной взаимосцепляемости из-за трудности их разделения;
3) для деталей, которые могут быть повреждены (хрупкие, высокоточные и т.п.) при засыпке их навалом;
4) при автоматизации загрузки рабочих машин, осуществляющих длительный цикл обработки, когда применение более сложных и более производительных бункерных загрузочных устройств становится нецелесообразным.
В общем случае магазинное загрузочное устройство состоит из следующих основных узлов:
1) накопителя или собственно магазина;
2) отсекателя;
3) питателя;
4) блокирующего механизма;
5) привода загрузочного устройства.
Взаимодействие этих узлов может быть представлено схемой, приведенной на рис. 2.7.
Заготовки или детали из накопителя поступают к отсекателю и затем с помощью питателя подаются в рабочую зону станка или машины. Блокирующий механизм предупреждает нарушение работы загрузочного устройства, воздействуя на магазин, отсекатель или питатель. Движение рабочих органов устройства осуществляется с помощью привода АЗУ.
Накопитель или магазин служит для помещения в него заданного количества ориентированных заготовок и транспортирования их в питатель, а затем и в рабочую зону станка. Количество загружаемых заготовок должно обеспечить бесперебойную работу рабочей машины в течение определенного времени, обуславливаемого технологическим процессом. Обычно это время – 10…30 мин. Таким образом, при выборе размеров и объема накопителя приходится решать задачу о размещении в нем загружаемых заготовок. Заготовки могут помещаться в накопителе:
1)в один ряд;
2)в один слой и несколько рядов;
3)в один штабель;
4)в несколько штабелей и один ряд;
5)в несколько штабелей и рядов.
При выборе размещения заготовок приходится решать альтернативные задачи. Наиболее простой способ – это размещение в один ряд, поскольку здесь упрощается отбор заготовок, их транспортирование, да и сама загрузка. Однако при этом увеличиваются габариты самого магазинного загрузочного устройства, что может потребовать дополнительную производственную площадь.
Рис. 2.7 – Схема взаимодействия узлов магазинного
загрузочного устройства
В зависимости от конфигурации подаваемых заготовок, требований их хранения, условий выдачи заготовки могут располагаться вплотную или вразрядку.
В автоматических загрузочных устройствах заготовки перемещаются под действием силы тяжести, внешней приложенной силы или сил инерции.
Следовательно, можно выделить четыре вида движения, или транспортирования, изделий:
1) самотечное – под действием силы тяжести;
2) принудительное – под действием приложенной внешней силы;
3) вибрационное – под действием инерционных сил;
4) комбинированное – сочетающее вышеназванные виды для использования их различных преимуществ.
2.3.2. Лотки
По форме продольного профиля лотки бывают прямолинейные обычные, прямолинейные роликовые, изогнутые, винтовые (спиральные), зигзагообразные и специальные (змейковые, каскадные и др.).
Схемы таких лотков приводятся на рис. 2.8. При проектировании самотечных лотков следует иметь в виду, что движение заготовок осуществляется под действием составляющей силы земного притяжения и, следовательно, необходим определенный перепад высоты. Вертикальное расположение лотка приводит к быстрому росту его высоты и, таким образом, применимо для довольно мелких заготовок. Вместе с тем, такое расположение приводит к повышенному давлению заготовок друг на друга, что также не всегда допустимо. В связи с этим для самотечных лотков наиболее часто применяют их наклонную установку.
2.4. ВИБРАЦИОННОЕ ПЕРЕМЕЩЕНИЕ
Для хранения и принудительной подачи заготовок, расположенных в один ряд, в последнее время все шире применяют вибрационные лотки-транспортеры, позволяющие работать даже с отрицательным перепадом высот и обеспечивающие высокую надежность подачи без повреждения подаваемых заготовок. Они, конечно, сложнее самотечных лотков, однако, указанные их преимущества: малая энергоемкость, сравнительные простота конструкции и износостойкость – завоевывают им все большее признание.
Принцип вибрационного транспортирования одинаков как для прямолинейных лотков, так и для вибрационных бункерных питателей, которые будут рассмотрены позже.
Под вибрациями обычно понимают колебательное движение поверхности тела сравнительно малой амплитуды и значительной частоты.
Тогда вибрационное перемещение есть движение тела по вибрирующей поверхности под воздействием периодической возмущающей силы сообщаемой этой поверхностью, т.е. движение под воздействием инерционных сил, возникающих в результате вибрационного перемещения рабочей (несущей) поверхности.
2.4.4. Вибрационные лотки-транспортеры
Использование принципов вибрационного транспортирования позволяет создавать прямолинейные лотки для накопления и транспортирования в рабочую зону различных деталей и изделий. Применяемые в машиностроении прямолинейные вибрационные питатели – вибрационные транспортеры по назначению можно разделить на три группы:
1. Вибрационные транспортеры для перемещения сыпучих материалов и заготовок навалом.
2. Вибрационные транспортеры-лотки для перемещения ориентированных заготовок.
3. Вибрационные транспортеры-лотки для подачи заготовок из бункерного питателя в рабочий орган станка.
Вибрационные транспортеры для транспортирования заготовок навалом и перемещения стружки, как правило, имеют большую длину и мощность; рабочий желоб транспортера имеет поперечное сечение, позволяющее перемещать значительные объемы материалов.
Вибрационные транспортеры-лотки для перемещения ориентированных заготовок имеют небольшие габариты в поперечном сечении. К жесткости рабочего органа такого транспортера предъявляются повышенные требования.
Вибрационные лотки, предназначенные для подачи заготовок из бункерного вибропитателя в рабочий орган станка, имеют обычно небольшую длину, и привод их может осуществляться от колеблющейся чаши бункерного питателя, что значительно упрощает конструкцию.
2.5. АВТОМАТИЧЕСКИЕ ЗАГРУЗОЧНЫЕ
УСТРОЙСТВА БУНКЕРНОГО ПИТАНИЯ
Бункерные загрузочные устройства характеризуются тем, что запас заготовок сосредотачивается в емкости (бункере) беспорядочно (навалом). Необходимая ориентация заготовок перед передачей их в накопитель осуществляется специальным механизмом. Передача заготовок из накопителя в рабочую зону станка осуществляется питателем.
Таким образом, бункерное загрузочное устройство представляет собой группу механизмов, принимающих заготовки навалом и выдающих их строго ориентированными в пространстве и во времени.
В общем случае бункерное загрузочное устройство (БЗУ) состоит из следующих основных узлов:
1) собственно бункера (емкости);
2) механизма захвата;
3) механизма ориентации;
4) предохранительного механизма;
5) магазина или накопителя;
6) отсекателя;
7) питателя;
8) привода.
В реальных конструкциях некоторые узлы могут объединяться или отсутствовать вообще.
Как видно из перечисления, по сравнению с автоматическим загрузочным устройством магазинного питания БЗУ имеют часть узлов аналогичных магазинным загрузочным устройствам, часть модифицированных и, наконец, совершенно новых узлов. Так, начиная от предохранительного механизма, узлы и их функциональное назначение те же, что и у магазинных загрузочных устройств. До предохранительного механизма – совершенно новые узлы, а сам предохранительный механизм является определенной модификацией. Это объясняется тем, что, начиная от накопителя, рассматриваемое автоматическое загрузочное устройство имеет дело уже с ориентированными заготовками, а до него – с расположенными в пространстве произвольно.
Узлы механических БЗУ
Бункер– механизм или емкость, в которую загружаемые заготовки помещаются навалом и из которого механизм захвата извлекает заготовки поштучно или порционно.
Наиболее распространенные формы бункеров показаны на рис. 2.38. По конструкции бункера бывают цилиндрическими, коничес-
Рис. 2.38 – Схемы бункеров
кими и ковшеобразными. Их выполняют с одной емкостью для накопления и выборки заготовок (рис. 2.38, а) и с двумя емкостями, соединяемыми одна с другой (рис. 2.38, б). В последнем случае одна емкость, предбункер 1, служит для сосредоточения основного запаса заготовок, а другая емкость, собственно бункер 2, – для выборки заготовок. Заготовки из предбункера в бункер обычно перемещаются постепенно под действием сил тяжести. Иногда предбункер выполняют отдельно, и его можно располагать вертикально.
Первая группа бункеров имеет широкое применение, но обладает рядом недостатков: интенсивное ворошение заготовок в результате воздействия движущегося захватного органа приводит к забоинам и царапинам на поверхностях заготовок; большое накопление заготовок в бункере, а, следовательно, и значительное давление верхних слоев на нижние, затрудняет подготовкузаготовок к захвату и приводит к падению производительности загрузочного устройства.
Вторая группа свободна от недостатков бункеров первой группы и может быть рекомендована для загрузочных устройств, требующих обеспечения большой емкости бункера. Однако конструктивно она сложнее.
Механизмы захвата предназначены для выборки находящихся в беспорядочном состоянии заготовок из бункеров. От конструкции захватных органов во многом зависит производительность и надежность работы бункерно-загрузочных устройств.
Захватные органы выполняют в виде крючков, прямоугольных и фигурных вырезов на диске, штырей, труб и т. п. Крючки (рис. 2.39, а) – распространенный захватный и ориентирующий орган в БЗУ. Их обычно делают круглого сечения, а захватную часть (изогнутый конец) с боковых сторон срезают. Такая формаобеспечивает проход крючков в щель, меньшей по размерам, чем диаметр приемной трубки, что предохраняет выпадение заготовок из трубки.
Рис. 2.39 – Разновидности крючковых и штыревых захватных органов
Для выборки небольших колпачков крючки делают заодно с диском (рис. 2.39, б). Захватные органы для цилиндрических колпачков и втулок выполняют с поворотными крючками (рис. 2.39, в), которые захватывают заготовки при тангенциальном расположении крючков 1, а выдают их в лоток при радиальном расположении 2. Такой способ захвата и выдачи упрощает отвод заготовок при переполнении лотка, лишние заготовки падают в бункер.
Для выборки стеклянных заготовок (бусинок диаметром 3,5мм с отверстием 2,5 мм, длиной 2 мм) применяют захватные органы с одним крючком (рис. 2.39, г). На рис. 2.39, д показан захватный орган в виде непрерывного ремня 1, на котором закреплены штыри 2, осуществляющие захват заготовок (например, низких колпачков). Захватный орган в виде кольца с тангенциальным расположением крючков (штырей) показан на рис. 2.39, е. В нижнем положении штыря колпачок надевается на штырь, а в верхнем – спадает в приемную трубку.
Число крючков на диске определяется производительностью, длинойзаготовки и обычно равно 8-16. Захватный орган с тангенциальным расположением штырей на внутренней поверхности кольца имеет 35-70 штырей. Диаметр по крючкам – 350-400 мм, а по штырям – до 700 мм.
Из перечисленных захватных органов наиболее производительными являются захватные органы, имеющие штыри, расположенные тангенциально.
Рис. 2.40 – Разновидности щелевых захватных органов
Для выборки заготовок со шляпками, шайб и т. п. применяют захватные органы, имеющие щель. На рис. 2.40, а показано сечение качающегося сектора, стенки 1 и 2 которого образуют щель. При качательном движении сектора, в нижнем его положении заготовки западают в щель, а в верхнем соскальзывают в лоток. Форму и размеры щели выбирают в зависимости от конфигурации заготовки (рис. 2.40, а, б, в). Применяют также захватные органы в виде доски 1 (рис. 2.40, г), совершающей возвратно-поступательное движение. Верхний торец доски 2 захватывает заготовки 3 в бункере и транспортирует их вверх, где они скатываются и западают в щель лотка 4.
Для выборки заготовок со шляпками также применяют захваты в виде лопастей 1, закрепленных на барабане 2 (рис. 2.40, д). При вращении барабана лопасти захватывают заготовки и транспортируют их вверх, где они перекатываются в лоток 3. Чаще всего лопастные захватные органы применяют для подачи тонкостенных заготовок (гильз).
Производительным способом выборки заготовок со шляпками (до 220 шт/мин) является круговая щель 5 (рис. 2.40, е), образованная дном бункера 4 и вращающимся диском 3, в которую западают заготовки 1, захватываются и транспортируются подпружиненными собачками 2.
В качестве захватного органа часто применяют диски с прямоугольными и профильными вырезами. На рис. 2.41, а показан диск 1 с прямоугольными вырезами 2 для захвата цилиндрических заготовок 3, а на рис. 2.41, б – с профильными вырезами 1 для захвата шайб 2. Диск устанавливают в донной части бункера.
Рис. 2.41 – Механизмы захвата и ориентирования
Захватные органы в виде цилиндрического барабана 1 с профильными вырезами 2 на торце (рис. 2.41, в) применяют для подачи низких колпачков со сферическим донышком 3. Для таких же колпачков применяют диск 1 (см. рис. 2.41, г) с карманчиками 2, расположенными по окружности. Карманчики делают съемными на случай замены при износе.
Весьма производительные (до 200 шт/мин) захватные органы в виде зубчатых дисков 1 (рис. 2.41, д). По окружности диска расположены зубцы 2, между которыми располагаются заготовки (высокие и средние колпачки). Вверху бункера происходит отсортировка колпачков: запавшие вверх донышком выпадают из диска, а запавшие донышком вниз передаются в приемный лоток.
Выборку цилиндрических заготовок можно производить с помощью трубки. На рис. 2.41, е показана вращающаяся трубка 1, вмонтированная в донную часть бункера. Трубка имеет палец 3, который при вращении ворошит заготовки 2, вследствие чего они западают в трубку. Захватные трубки могут быть и с возвратно-поступательным движением, в этом случае на верхнем торце трубки делают наклонный срез, способствующий лучшему западанию заготовок в трубку. Производительность таких захватных органов до 40 шт/мин.
Рассмотренные разновидности захватных органов являются наиболее распространенными и могут служить исходной базой при проектировании бункерно-ориентирующих устройств.
Механизм ориентацииосуществляет ориентирование заготовок в пространстве. Процесс ориентирования заготовок лежит в основе построения любого автоматического загрузочного устройства, осуществляющего подачу штучных заготовок в рабочую позицию в строго определенном рабочем положении. Поэтому выбор принципа построения и разработка механизма ориентации является одним из главнейших вопросов проектирования автоматических загрузочных устройств.
Трудность создания механизмов ориентации обусловлена необходимостью соблюдения ряда условий: укладка всех заготовок в требуемом положении, надежность прохождения заготовок в механизме ориентации и выдачи их в лоток, исключение возможных повреждений заготовок в процессе ориентирования, обеспечение требуемой производительности. Несоблюдение одного из этих условий может привести к тому, что механизм ориентации не обеспечит требуемой производительности.
Для разворота заготовок в требуемое положение используют, с одной стороны, особенности формы заготовок (наличие отверстия, паза, бурта, головки) или смещения их центра тяжести относительно оси симметрии, с другой стороны, форму ориентирующего звена (фасонные вырезы, щель и др.). В зависимости от выбора той или иной особенности формы заготовки и формы ориентирующего звена различаются и способы ориентирования. Например, если заготовка имеет отверстие, а ориентирующее звено вид крючка, то такой способ ориентирования называют “надевание заготовки на крючок”.
Если для ориентирования принимают головку заготовки, а ориентирующее звено – сектор со щелью, то такой способ называют “ориентирование щелью”, или “западание в щель”.
Ориентирование заготовок может производиться в один и в два приема. Ориентирование в один прием осуществляется в процессе захвата заготовок. Например, в крючковых загрузочных устройствах заготовка захватывается крючком за отверстие. Следовательно, захват заготовок является в то же время и процессом окончательного ориентирования. Ориентирование в два приема осуществляется раздельно: предварительное, называемое первичным – во время захвата, окончательное, называемое вторичным – при прохождении через вторичный механизм ориентации. Например, в дисковых загрузочных устройствах предварительное ориентирование длинных цилиндрических колпачков производится при западании их в прямоугольные вырезы диска, а окончательное – при транспортировании в верхнем положении специальным механизмом вторичной ориентации.
Окончательное ориентирование заготовок может осуществляться как внутри бункера, так и вне его. При этом вторичное ориентирование может осуществляться в несколько этапов. В многопозиционных загрузочных устройствах механизмы ориентирования встраивают в захватный диск, поэтому заготовки такими захватно-ориентирующими устройствами выдаются из бункера в лоток окончательно ориентированными. В ряде конструкций бункерно-загрузочных устройств предварительное или первичное ориентирование производится внутри бункера, а вторичное – вне бункера. Механизм ориентации в этом случае можно устанавливать в начале, середине или в конце лотка.
Для классификации механизмов ориентирования выделяют шесть основных, наиболее распространенных способов ориентирования:
I – надевание заготовки на крючок;
II – западание заготовки в щель;
III – западание заготовки в фасонный вырез по профилю заготовки;
IV – поворот заготовки на фасонных губках и других опорах;
V – западание заготовки в фасонный вырез по расположению центра тяжести;
VI – западание заготовки в трубку;
Устройства, осуществляющие первичную ориентациюзаготовок, встречаются редко, так как первичная ориентация обеспечивается обычно одновременно с захватом (см. например рис. 2.42).
При выпадании заготовок в приемное окно его ширина ограничивает производительность БЗУ. Иногда для повышения производительности окно расширяют, допуская потерю ориентации заготовок. Выпадающие заготовки попадают на лоток с направляющими лопастями и получают первичную ориентацию в процессе движения. В этом случае лоток с направляющими лопастями будет являться устройством первичной ориентации.
Механизмы,осуществляющие одновременно захват и первичную ориентацию заготовок, могут выполнять первичную ориентацию следующим образом:
1)путем западания заготовок в карман;
2)лотками в виде щелей и трубок;
3)надеванием заготовок на крючок или штырь.
Первичная ориентация западанием в простые карманы применяется в дисковых БЗУ для заготовок типа валиков и дисков (рис. 2.42, в, г, д).
Ориентация лотком в виде трубки (рис.2.42, е) применяется для заготовок типа втулок и валиков в диапазоне: l/d = 0,2…4. При этом трубка может иметь вращательное, возвратно-поступательное и сложное движения.
Ориентация лотком в виде щели (рис. 2.42, ж) применяется в секторных и лопастных БЗУ для заготовок типа диска, пластины, а также в центробежных БЗУ (рис. 2.42, з). Ориентация заготовок надеванием на крючок или штырь применяется для втулок, гильз в крючковых БЗУ (рис. 2.42, и).
|
Рис. 2.42 – Механизмы для захвата и первичной ориентации
Устройства,осуществляющие вторичную ориентацию заготовок, конструктивно весьма разнообразны. Вторичная ориентация может быть произведена: 1) в захватном органе и 2) в отдельном устройстве.
Вторичная ориентация в захватном органе использует особенности геометрической формы заготовок или смещение центра тяжести относительно середины заготовки.
Механизмы,осуществляющие захват и двойную ориентацию одновременно, построены на принципе использования геометрической формы заготовок. Полная ориентация заготовок происходит непосредственно в захватном органе БЗУ. Захват и двойная ориентация происходят следующими способами:
1) по внутренней поверхности заготовки – надеванием на крючок или штырь в штыревых и крючковых БЗУ;
2) по профилю заготовки – западанием в профильный карман в карманчиковых БЗУ;
3) с использованием головок или уступов – западанием в щель в секторных, щелевых и других БЗУ.
Для одного и того же типа заготовок приемлемыми могут оказаться несколько типов БЗУ. При выборе наиболее рациональной конструкции БЗУ первостепенное значение имеет следующее: 1) положение, в котором заготовки должны выходить из лотка; 2) расположение и число оборотов вала, от которого конструктивно просто осуществить привод; 3) характер исполнительного механизма и простота конструкции БЗУ в целом.
2.7. Вибрационные бункерные
загрузочные устройства
Появившиеся сравнительно недавно в машиностроении вибрационные бункерные загрузочные устройства (питатели) являются новой разновидностью автоматических загрузочных устройств и обладают целым рядом преимуществ по сравнению с другими типами БЗУ. Эти устройства сравнительно просты по конструкции. Отсутствие в них движущихся захватно-ориентирующих органов исключает возможность заклинивания заготовок, в связи с этим отпадает необходимость в предохранительных механизмах.
В вибрационных бункерных загрузочных устройствах (ВБЗУ) со спиральным лотком можно предотвратить падение и удары заготовок друг о друга, нарушающие чистоту поверхностей точных деталей, поступающих на сборку и контроль. Постоянная равномерная скорость движения заготовок по лотку создает благоприятные условия для осуществления ориентации сложных заготовок внутри бункера.
В ряде случаев ВБЗУ являются единственно возможным средством автоматизации загрузки заготовок, например, деталей часового и радиотехнического производства, где заготовки весьма малы, обладают малой прочностью и имеют склонность к взаимному сцеплению (например, рубиновые камни, стеклянные, пластмассовые, слюдяные детали и т. п.).
В машиностроительной промышленности заготовки с крупными заусенцами, например, поковки колец подшипников, могут эффективно загружаться в автоматическое оборудование только при помощи ВБЗУ.
Благодаря использованию резонансного принципа работы ВБЗУ для привода их требуется значительно меньшее возмущающее усилие, чем для вибропитателей других конструкций.
Рассмотрим некоторые конструкции вибрационных загрузочных устройств.
2.7.1. Бункерное загрузочное устройство с
многослойными подвесками
На рис. 2.45 показана конструкция ВБЗУ для небольших заготовок.
ВБЗУ состоит из чаши 1, на внутренней цилиндрической поверхности которой имеется спиральный лоток 2. Днище чаши 3 укреплено на трех многослойных подвесках 4, представляющих наборы плоских рессор.
В центре нижнего массивного основания 5 укреплен электромагнит 6, якорь которого 7 крепится к днищу чаши 3. Для виброизоляции бункер расположен на резиновых амортизаторах 8. Регулирование производительности осуществляется изменением тока, подаваемого в электромагнит, которое производится при помощи встроенного реостата 9.
Резонансная настройка питателя может регулироваться путем изменения количества пластин в пакетах многослойных подвесок 4.
Рис. 2.45 – ВБЗУ с многослойными подвесками
2.7.2. ВБЗУ с подвеской чаши на цилиндрических стержнях
На рис. 2.46 показана конструкция ВБЗУ с подвеской чаши на цилиндрических стержнях. ВБЗУ состоит из чаши 13, на внутренней цилиндрической поверхности которой выполнена спиральная канавка призматической формы, в которой вмещаются цилиндрические детали в один ряд. Чаша 13 вместе с конусом 12 крепится к днищу 11. Днище ВБЗУ укреплено на трех наклонных цилиндрических пружинных стержнях 2, закрепленных зажимами в верхнем 1 и нижнем 5 башмаках. Стержни расположены таким образом, что проекция их на горизонтальную плоскость перпендикулярна к радиусу в точках крепления их к днищу 11. Для уменьшения габаритов питателя при определенной рабочей длине пружинных стержней 2 крепление их к нижней плите 8 осуществляется зажимами 5 с нижней стороны плиты.
Привод питателя осуществляется от вертикального электромагнитного вибратора 3, установленного в центре плиты 8. Якорь вибратора 14 выполнен из пластин электротехнической стали, пакет которых при помощи планок крепится к основанию якоря.
![]() |
Для изоляции днища бункера от проникновения магнитных силовых линий, которые могут намагничивать подаваемые детали, между основанием якоря и днищем установлена алюминиевая прокладка 15. Сердечник электромагнита состоит из набора Ш-образных пластин 10, изготовленных из электротехнической стали, прикрепляемых к основанию вибратора при помощи планок. На средний выступ набора надевается катушка 9 с обмоткой, через которую пропускается переменный ток.
Вертикальные колебания якоря вибратора за счет изгиба наклонных стержней 2 преобразуются в колебания чаши питателя по винтовой линии. Такое колебательное движение заставляет детали, лежащие на поверхности конуса 12, сползать к спиральной канавке и подыматься по ней вверх.
Для виброизоляции загрузочное устройство установлено на трех витых цилиндрических пружинах 4 сравнительно небольшой жесткости. Устранение чрезмерной подвижности питателя достигается установкой на основании 7 оси 6 с резиновой втулкой, которая входит в отверстие плиты 8 с небольшим зазором. Эта ось, обеспечивая амортизированной системе две степени свободы: перемещение по вертикали и вращение вокруг вертикальной оси, ограничивает возможность остальных перемещений.
Особенностью таких конструкций вибрационных бункерных загрузочных устройств, является применение цилиндрических стержней в качестве упругих подвесок.
Применение цилиндрических стержней вместо плоских пружин вызвано следующими соображениями.
Частота собственных колебаний ВБЗУ должна быть вполне определенной и зависит она от жесткости пружин, на которых подвешена чаша питателя.
Пластинчатые рессорные пружины имеют жесткость, сильно зависящую от направления их изгиба. Поэтому жесткость каждой пружины, закрепленной в системе ВБЗУ, в значительной мере будет зависеть от точности ее установки. Неодинаковая жесткость пружин, на которых подвешивается чаша устройства, нарушает движение заготовок по спиральному лотку и требует дополнительной работы по настройке ВБЗУ.
Круглые цилиндрические стержни имеют одинаковую жесткость в любом радиальном направлении и поэтому менее чувствительны к погрешностям сборки. Расчет их упругих свойств, а, следовательно, и параметров собственных колебаний ВБЗУ прост и точен. Кроме того, цилиндрические стержни допускают устранение погрешностей расчета простым способом регулировки резонансной настройки.
Необходимость регулирования резонансной настройки вызывается тем, что при проектировании вибрационного устройства не всегда удается точно определить массы и моменты инерции частей ВБЗУ из-за их сложной конфигурации. Поэтому частота собственных колебаний системы изготовленного загрузочного устройства может оказаться несколько выше или ниже расчетной. Удаление даже на несколько герц от резонансной области увеличивает требуемое для привода ВБЗУ возмущающее усилие в несколько раз.
Дата добавления: 2018-06-27; просмотров: 3946; Мы поможем в написании вашей работы! |
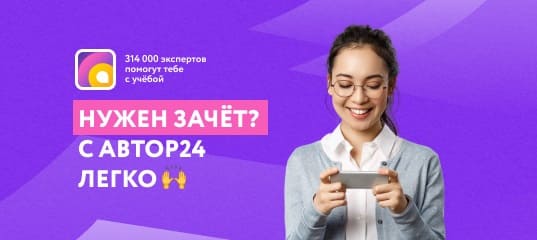
Мы поможем в написании ваших работ!