ИСПЫТАНИЕ НА ВЕТРОУСТОЙЧИВОСТЬ
Ветроустойчивостью называют способность аппаратуры привоздействия ветра сохранять свои характеристики в пределах норм, установленных в стандартах, ТУ или ПИ.
Согласно ГОСТ 22261–76 для 4 – 7-й групп в ТУ допускается устанавливать требования по ветроустойчивости. Испытания средств измерений 4 – 7-й групп на ветроустойчивость проводят следующим образом:
− после измерений в нормальных условиях характеристик, установленных для испытаний данного вида в стандартах и (или), ТУ, средство измерений выключают и устанавливают в рабочем положении в аэродинамической трубе или под вентиляционной установкой, обеспечивающих воздушный лоток со скоростью не менее 30 м/с;
− изделие включают и обдувают его воздушным потоком под разными углами (через 45°) по 5…10 мин в каждом положении (в направлении наибольшей парусности продолжительность обдува должна быть 20 мин);
− при воздействии воздушного потока проверяют требуемые характеристики;
− прекращают подачу воздуха и выключают средство измерений;
− изделие второй раз обдувают воздушным потоком со скоростью не менее 50 м/спод углами через 45° по 5…10 мин в каждом положении (в направлении наибольшей парусности продолжительность обдува должна быть 20 мин);
− после пребывания в нормальных условиях применения в течение времени, установленного в стандартах или ТУ, средство измерений включают и по истечении времени установления рабочего режима проверяют требуемые характеристики.
|
|
В том случае, когда ветер является существенно воздействующим фактором на изделие, при его разработке и испытании необходимо рассматривать характеристики ветра по ГОСТ 24728–81. Характеристики ветра распределяются по четырем широтным зонам и представительным пунктам с экстремальными сильными и слабыми ветрами в каждой широтной зоне и рассчитываются по геопотенциальным высотам (ГОСТ 4401–81).
ИСПЫТАНИЕ НА ГЕРМЕТИЧНОСТЬ
Герметичностью называют способность оболочки (корпуса), отдельных ее элементов и соединений препятствовать газовому или жидкостному обмену между средами, разделенными этой оболочкой. Испытания на герметичность проводят для определения степени герметичности изделия или его частей, узлов и блоков.
Требования к степени герметичности должны быть определены при разработке конструкции. Степень герметичности должна характеризоваться потоком газа, расходом или наличием истечения жидкости, падением давления за единицу времени, размером пятна и тому подобными величинами, приведенными к рабочим условиям по ГОСТ 24054–80 и ГОСТ 20.57.406–81. Метод испытаний на герметичность выбирают в зависимости от назначения изделия, его конструктивно-технологических особенностей, требований к степени герметичности, а также экономических характеристик испытаний.
|
|
Испытания на герметичность включают в технологический процесс изготовления изделия таким образом, чтобы предшествующие технологические операции не приводили к случайному перекрытию течей. При невозможности исключить опасность случайного перекрытия течей в технологическом процессе необходимо предусмотреть операции, обеспечивающие освобождение течей от закупорки. Метод или программа испытаний на герметичность указаны в стандартах, ТУ или ПИ на изделия конкретного вида.
В зависимости от рода пробного вещества методы испытаний на герметичность подразделяются на две группы: газовые и жидкостные.
К газовой группе относятся следующие методы испытаний: разноактивный, манометрический, массоспектрометрический, галогенный, пузырьковый, ультразвуковой, катодометрический, химический, инфракрасный, параметрический.
К жидкостной группе относятся следующие методы: гидростатический, люминесцентный (цветной), электрический параметрический.
Реализация указанных методов возможна следующими способами: компрессионным, камерным, вакуумным, капиллярным, обдува, щупа, обмыливания, нагревания, внешней опрессовки, опрессовки замкнутых оболочек и в камере.
|
|
Классификация наиболее распространенных методов испытаний на герметичность и их общая характеристика приведены в справочном прил. 2 ГОСТ 24054–80. Метод должен обеспечивать проведение испытаний в условиях отвечающих требованиям действующей НТД по технике безопасности и промышленной санитарии.
Испытания герметичности изделий и средств измерений проводят одним из следующих методов (ГОСТ 5197–70, ГОСТ 20.57.406–81, ГОСТ 24054–80 и Публикации МЭК 68-2–17):
− проверка по обнаружению утечки жидкости (гидростатический метод);
− проверка по обнаружению утечки газа масс-спектрометром, в том числе изделий, имеющих свободные внутренние объемы изделий, представляющих собой герметичные перегородки уплотнения (массо-спектро-метрический, химический методы);
− проверка по проникновению жидкости и газа (параметрический метод);
− проверка по обнаружению утечки газа, в том числе путем обнаружения утечки воздуха или другого газа из внутренних областей изделия при погружении его в жидкость с пониженным давлением и при повышенной температуре (пузырьковый, катодометрический методы);
|
|
− проверка по обнаружению, утечки воздуха, подаваемого на изделие под давлением (манометрический метод);
− проверка путем проникновения паров влаги (влажностный метод).
Подготовка изделия к испытаниям на герметичность предусматривает устранение последствий случайного перекрытия течей после хранения, транспортирования и операций, предшествующих испытаниям. Для испытаний на герметичность необходимо использовать оборудование укомплектованное специальными присоединительными и установочными деталями и калиброванными течами в соответствии с ТУ на изделия конкретного вида.
Испытание на герметичность изделий вакуумным способом пузырькового метода проводят следующим образом. Изделие погружают в ванну с индикаторной жидкостью, находящуюся внутри барокамеры, которая должна обеспечивать испытательный режим. Количество жидкости в ванне должно быть достаточным, чтобы исследуемая поверхность была погружена на глубину не менее 50 мм. Температура испытательной жидкости 15…35 °С, кинематическая вязкость 25 сСт при 20 °С. Давление в камере снижают до 0,1…1,0 кПа.
Изделие считают выдержавшим испытание, если пузырьки газа не выделяются.
Испытание на герметичность изделий камерным способом манометрического метода проводят следующим образом. Изделие (или партию изделий) помещают в камеру, заполняют ее пробным газом под давлением и выдерживают в течение определенного времени, устанавливаемого в стандартах, ТУ или ПИ. До заполнения камеры гелием допускается снижение давления до 0,1 кПа и выдерживание в течение 30 мин при этом давлении.
Изделия извлекают из камеры и выдерживают в течение 20 мин в условиях, обеспечивающих удаление гелия, адсорбированного внешними поверхностями. Затем изделия помещают в камеру, соединенную с масс-спектрометром, и измеряют скорость утечки гелия. Измеренное значение сравнивают со значением скорости утечки гелия, указанной в стандартах и ТУ или ПИ на изделие.
Изделия считают выдержавшими испытание, если скорость утечки гелия меньше или равна значению, указанному в стандартах и ТУ или ПИ на изделие.
МЕХАНИЧЕСКИЕ ИСПЫТАНИЯ
Механические испытания позволяют определить свойства материала, в том числе те, что влияют на его прочность. Это необходимо для того, чтобы обеспечить качество изготовленных из этого материала изделий. При выборе материала производителя интересует уменьшение себестоимости изделия, поэтому он ищет баланс между потенциальным уменьшением прочности и материалоемкостью. Механические испытания прочности материала дают такую возможность. Для механических испытаний используются различные установки, проверяющие реакцию различных материалов на такие механические воздействия, как: отвердение, реакцию на «изгиб и разгиб», «растяжение и сжатие», перегиб, сдвиг и т.д. Для исследования характеристик излома и вязкой составляющей используются копры разных принципов действия: вертикальные, горизонтальные и маятниковые.
Механические испытания в зависимости от характера изменения и времени действия нагрузки разделяют на статические испытания (на растяжение, сжатие, изгиб, кручение, твердость), динамические испытания (на ударный изгиб), усталостные испытания (при повторно-переменном приложении нагрузки). Отдельную группу составляют длительные механические испытания (на ползучесть, длительную прочность и др.).
Традиционные методики испытания механических свойств материалов проводятся, как правило, при комнатных или умеренно отрицательных (до –30…–40 °С) температурах. На примере нескольких методик механических испытаний (испытания на усталость и ударный изгиб) покажем принципиальную возможность адаптации традиционных (без существенных модификаций) методик испытаний механических свойств к условиям низких температур.
ИСПЫТАНИЕ НА СЖАТИЕ
Испытание на сжатие, при котором изучают поведение материалов при одноосном сжатии, можно рассматривать как обратное испытанию на растяжение. Оно имеет наибольшее значение для строительных материалов таких, как натуральный камень, кирпич, бетон, древесина и т.д.
Оно находит также применение для металлических и полимерных материалов, например для материалов,используемых в подшипниковой промышленности.
При испытании на сжатие образец с поперечным сечением А0 подвергают сжатию и измеряют при этом соответствующую нагрузку F.
Если трещина не образуется, испытание проводят до общего относительного сжатия 50 %.
При испытании дерева поперек волокна и других деформируемых строительных материалов испытания прекращают уже после достижения 10 % относительного укорочения.
Предел текучести при сжатии, соответствующий пределу текучести при растяжении, равен
σdF = FF / А0 , H/мм2 (21.48)
где FF – нагрузка, под действием которой на кривой напряжение – относительное укорочение при сжатии при одновременном появлении заметного остаточного укорочения появляется первое отклонение от прямолинейного хода.
Если кривая напряжение – относительное укорочение при сжатии монотонна, то в качестве предела текучести при сжатии определяют условный предел текучести. Условным пределом упругости считают условное напряжение, соответствующее относительному укорочению при сжатии 0,01 %.
Если образец при сжатии разрушается без видимой трещины, относительное укорочение при сжатии определить нельзя. Бочкообразную выпуклость образца (рис. 29), образующуюся при испытании на сжатие, нельзя сравнивать с соответствующим сужением при испытании на растяжение.
Рис. 30. Схема расположения образца при испытании на сжатие
Бочкообразность при сжатии возникает из-за трения между опорными поверхностями на машине и поверхностями сжимаемого образца. Трение препятствует поперечной деформации на торцах сжимаемого образца нарушаетодноосность напряженного состояния при сжатии. Так как ограничение деформации может распространяться конусообразно по середины образца, пластическая деформация при сжатии по существу ограничена областью, лежащей за пределами этого конуса.
Для испытания на сжатие применяют или те же испытательные машины, что и на растяжение, или специальные прессы (например, для испытаний строительных материалов). Находят применение механические прессы с механическим приводом при нагрузке до 105 Н и с гидравлическим приводом до 108 Н. Плиты, применяемые для передачи давления на образец, должны быть ровными, полированными и более твердыми, чем испытуемый материал. Плита, которую в начале испытания кладут на образец, должна быть установлена с помощью шарового вкладыша таким образом, чтобы она могла в некоторых пределах качаться во все стороны для выравнивания (рис. 30) перекосов и небольших отклонений поверхностей образца от параллельности. Диаметр применяемых цилиндрических образцов зависит от размеров имеющихся материалов и обычно составляет 10… 30 мм.
Для грубых измерений используют нормальный образец с высотой, равной диаметру. При тонких измерениях следует применять длинные образцы с L0 = (2,5…3) d0 . Более длинные образцы не применяют из-за опасности продольного изгиба.
При испытании длинных образцов расчетную длину выбирают на половину диаметра меньше, чем высота. Металлические образцы должны быть со всех сторон обточены или отшлифованы. Важно, чтобы торцы были точно параллельны и перпендикулярны оси образца. Для испытаний строительных материалов обычно используют образцы кубической формы.
Трубы и хрупкие материалы (гончарные изделия, глина) испытывают на сжатие для оценки их способности противостоять нагрузке в вертикальной плоскости (сплющиванию). При этом труба лежит на основной плите, а приложение нагрузки производят с помощью пуансона
ИСПЫТАНИЕ НА ИЗГИБ
Испытание на изгиб находит применение для исследования сравнительно хрупких материалов, например чугунов с пластинчатым графитом, инструментальной стали или керамики. Для вязких металлических материалов изгибающую нагрузку можно продолжать прикладывать за пределом текучести без разрушения материала.
Особенное значение имеет испытание на изгиб для полимерных материалов, так как для этой группы материалов, согласно их специфическим свойствам, при практическом использовании преобладает изгибающее нагружении.
При изгибе образца с симметричным поперечным сечением, как показано на рис. 31, в одной из наружных зон возникают растягивающие, а в противоположной – сжимающие напряжения. Напряжения увеличиваются по мере удаления в обе стороны от нейтральной оси, так что самые высокие их значения приходятся на наружные зоны. Если напряжения при этом достигают предела текучести, наступает пластическое течение.
1 – пластическая деформация; 2 – упругая деформация; 3 – нейтральная ось
В упругой области напряжения в поперечном сечении образца распределяются по линейному закону.
Характеристики прочности и пластичности при изгибе определяют при двух модификациях этого испытания: трехточечном и четырехточечном изгибе. При трехточечном изгибе (рис. 32, а) наибольший изгибающий момент возникает под влиянием сосредоточенной силы F в середине образца:
Мbmах = FLs/ 4, (21.52)
где Ls– расстояние между опорами.
При этом максимальное напряжение равно
σmах= FLs/ 4W, Н/мм2. (21.53)
Введя F – нагрузку в момент разрушения, получим временное сопротивление при изгибе σbв. В точке приложения нагрузки появляется наибольший упругий прогиб, равный
гдеЕ– модуль упругости.
Так как при испытании полимерных материалов разрушение образцов часто не достигается, определяют предельный прогиб при условии, что величина прогиба в точке приложения силы в 1,5 раза превышает толщину образца.
Прочностной характеристикой, соответствующей этому прогибу, является условное временное сопротивление при изгибе σb1,5. В случае четко выраженного зуба (площадки) текучести определяют условный предел текучести при изгибе σbF. Если отнести абсолютную величину прогиба к расстоянию между опорами Ls, получим относительную стрелу прогиба при изгибе φ:
φ = f 100 / Ls. (21.55)
Кроме того, поведение материала можно охарактеризовать жесткостью, определяемой соотношением между прочностью при изгибе σbВ и величиной стрелы прогиба при разрушении fB.
При четырехточечном изгибе (см. рис. 32, б) действующая на образец нагрузка F приложена в двух местах на расстоянии m от опор. При таком нагружении между точками приложения нагрузки не возникает усилий среза. Изгибающий момент между точками приложения нагрузки постоянен.
В отличие от трехточечного при четырехточечном изгибе вследствие постоянства изгибающего момента между точками приложения нагрузки создаются условия, при которых получаемые результаты испытаний правильно характеризуют материал и не зависят от возможных неоднородностей образца (в частности, структурных) в области максимального изгибающего момента.
Для проведения испытания на изгиб применяют цилиндрические или призматические образцы.
Образцы кладут на гладкие цилиндрические опоры и равномерно нагружают в соответствии с выбранной схемой испытаний с помощью одного или двух пуансонов.
Перед началом испытания точно устанавливают расстояние между опорами (для цилиндрических образцов Ls= 20d0).
ИСПЫТАНИЯ НА РАЗРЫВ.
Одним из самых важных и распространенных механических испытаний металла является испытание на разрыв и удлинение. Оно производится на испытательных разрывных машинах, которые растягивают образец, изготовляемый из испытуемого материала, и одновременно измеряют величину растягивающей силы. Этим способом определяют прочность, упругость и пластичность.
При испытании на разрыв образец зажимается в машине с двух концов при помощи разъемных вкладышей и постепенно растягивается с возрастающим усилием. Сначала образец удлиняется, но после прекращения растягивания и сближения рам он снова принимает прежние размеры, подобно тому, как возвращается к своему прежнему размеру резиновая пластина или пружина, если их немного растянуть, а затем отпустить.
Свойство тел изменять свои размеры и форму при действии силы и восстанавливать их после прекращения действии силы называется упругостью. Если растягивающая сила увеличивается, то образец растягивается все больше. Наконец, наступит момент, когда после прекращения действия силы и сближения рам машины образец не сможет принять прежних размеров и формы. Тогда говорят, что материал перешел „предел упругости”, т. е. к материалу были приложены силы, вызвавшие его перенапряжение.
При выборе материала для деталей, например для заклепок, листов и др., всегда производят расчет так, чтобы силы, которые будут приложены к материалу во время работы, не перевели его за предел упругости.
Момент достижения предела упругости отметить трудно и поэтому обычно испытание ведут дальше. Когда разрывающая сила возрастет еще на некоторую величину, настанет момент, когда материал „потечет”, т. е. начнет удлиняться без дальнейшего приложения силы. Образец будет растягиваться все больше и больше; наконец, на нем в одном месте образуется сужение, или „шейка”, и он разорвется.
На рисунке а показан образец до разрыва, на рисунке б— после разрыва.
Площадь поперечного сечения образца в месте разрыва меньше площади поперечного сечения до разрыва.
Сила, приложенная для разрыва образца, называется разрывным грузом. Чтобы вычислить силу, приходящуюся на разрыв 1 мм2 образца, силу разрывного груза делит на площадь поперечного сечения испытываемого образца. Это и будет величиной сопротивления разрыву данного материала.
При испытании отмечают также, насколько удлинился образец в момент разрыва и вычисляют это удлинение в процентах.
Чем больше удлинение при одном и том же сопротивлении разрыву, тем пластичнее считается материал, тем лучше он поддается обработке давлением. Пластичностью обычно принято называть способность металла, не разрушаясь, изменять форму под действием нагрузки и сохранить измененную форму после того как нагрузка будет снята.
ИСПЫТАНИЯ НА УСТАЛОСТЬ.
Многие элементы конструктивных узлов и устройств подвижного состава работают с вибрацией. При этом они испытывают многократное действие изменяющихся по величине или величине и направлению напряжений. За свою «жизнь» материал детали должен выдерживать большое число таких перемен или циклов. Например, за время своей работы ось тепловоза испытывает 400 млн. циклов, шатун паровой машины 1 млрд. циклов, вал паровой турбины 15 млн. циклов.
В результате действия циклических напряжений металл «устает», прочность его снижается и наступает разрушение детали. Данное явление называется усталостью, а сопротивление усталости – выносливостью. Разрушение от усталости происходит всегда внезапно вследствие накопления металлом необратимых изменений, которые приводят к возникновению микроскопических трещин – усталости.
Трещины усталости возникают обычно в поверхностных зонах детали. Большое влияние на образование трещин усталости оказывает состояние поверхности. Наличие на поверхности рисок, царапин, выбоин и других дефектов, вызывающих концентрацию напряжений, облегчает образование трещин усталости. Излом детали, разрушившейся от усталости (рис. 2.1), состоит из зоны усталостного разрушения 1 и зоны долома 2. В зоне усталостного разрушения вследствие трения соприкасающихся поверхностей, ограничивающих развивающуюся трещину усталости, возникает гладкая притертая поверхность. В зоне 1 часто наблюдаются концентрические бороздки, похожие на годовые кольца деревьев. Это следы постепенного распространения трещины усталости. Зона долома 2 имеет шероховатую поверхность, характерную для обычного неусталостного разрушения (вязкого или хрупкого). В связи с применением на железнодорожном транспорте сильно нагруженных быстроходных машин явление усталости привлекает к себе особенно пристальное внимание. Сопротивление усталости является важным свойством металлических материалов, используемых на железнодорожном транспорте, в самолетостроении, машиностроении, судостроении и других отраслях. |
Для оценки устойчивости металлических материалов к действию циклических нагрузок испытанию подвергают гладкие образцы или образцы с надрезом (рис. 2.2). Испытания осуществляют на специальных машинах, позволяющих получить повторно-переменные напряжения при изгибе, растяжении, кручении, ударном нагружении. Выбор машины и условий испытания определяется требованиями, предъявляемыми к материалу в зависимости от условий работы детали.
Распространенным методом испытания на усталость является изгиб при вращении. Схема испытания на машинах, работающих по методу консольного изгиба, показана на рис. 2.3. Образец 1 закреплен одним концом во вращающемся от электродвигателя 3 патроне испытательной машины. Другой конец образца вращается в подшипнике, к которому подвешен груз 5. При вращении образец под действием подвешенного груза подвергается изгибу. При этом одни и те же внешние волокна будут подвергаться растяжению, а через полуоборот – сжатию и наоборот. Характер изменения напряжений при этом – синусоидальный (рис. 2.4
При испытании образец доводится до разрушения, при этом фиксируется число циклов до разрушения (число циклов регистрируется специальным счетчиком, установленным на машине, который при разрушении образца выключается).
Основной характеристикой, определяемой при испытании на усталость материала, является предел выносливости – наибольшее напряжение, которое может выдержать материал без разрушения при произвольно большом числе перемен (циклов) нагрузки.
Для определения предела выносливости испытывают серию (не менее 10 шт.) одинаковых образцов, изготовленных из одного и того же материала. Первый образец нагружают так, чтобы максимальное напряжение заведомо превышало предел выносливости. Для второго и последующего образцов нагрузку постепенно снижают. Испытания проводят до разрушения образцов и фиксируют число циклов до разрушения. С уменьшением нагрузки число выдержанных циклов до разрушения возрастает.
По результатам испытаний строят кривую Материал выдерживает, не разрушаясь в течение определенного числа Цикловнагружения. Это число циклов называют базой испытания. Для сталей такоечисло циклов условно принято 10, а для цветных металлов и сплавов 20–100 млн.циклов.Результаты усталостных испытаний сильно зависят от состояния поверхности испытуемого образца. Для получения воспроизводимых результатов необходимо при изготовлении образцов обеспечивать высокое качество поверхности, что достигается шлифованием или полированием поверхности. |
Технологические испытания
Технологические испытания:1-испытания на обрабатываемость, 2- испытания на развальцовку, 3-испытания на отбортовку, 4-испытания на изгиб трубы, 5-на гиб с переломом,6-термические испытанияТехнологические испытания имеют целью определить степень пригодности металла к тому или иному виду технологической обработки, а также пригодности его для изготовления различных деталей или изделий, исходя из конкретных условий их работы в механизме или сооружении.
Основными видами таких испытаний являются: проба на загиб в холодном состоянии, проба на незакаливаемость загибом и проба на осадку в холодном состоянии.
Применение одного или нескольких видов перечисленных проб для данной стали зависит от ее назначения.
Испытание на твердость
Проще говоря, твердость - это сопротивление материала постоянному вдавливанию. Важно понимать, что испытание на твердость - эмпирическое, следовательно, твердость нематериальное свойство. Существует несколько типов испытаний на твердость, каждое из которых определяет различную величину твердости для одного и того же материала. Таким образом, твердость зависит от метода испытания, и каждый результат испытания должен иметь лейбл, указывающий использованный метод испытания.
Однако, твердость широко применяется для описания свойств материалов и определения их пригодности к использованию. Все испытания на твердость, описанные в данном разделе, предусматривают использование индентора специальной формы, значительно более твердого, чем образец испытания, который вдавливается в поверхность образца специальным усилием. Для определения величины твердости измеряется глубина проникновения или размер выемки.
Дата добавления: 2018-05-13; просмотров: 1961; Мы поможем в написании вашей работы! |
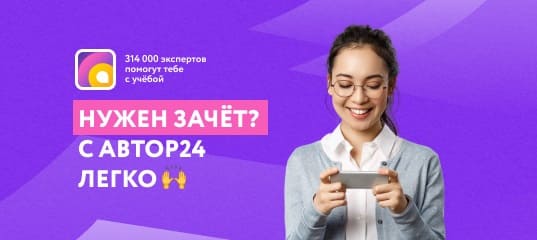
Мы поможем в написании ваших работ!